5S现场管理S现场管理内容.docx
《5S现场管理S现场管理内容.docx》由会员分享,可在线阅读,更多相关《5S现场管理S现场管理内容.docx(23页珍藏版)》请在冰豆网上搜索。
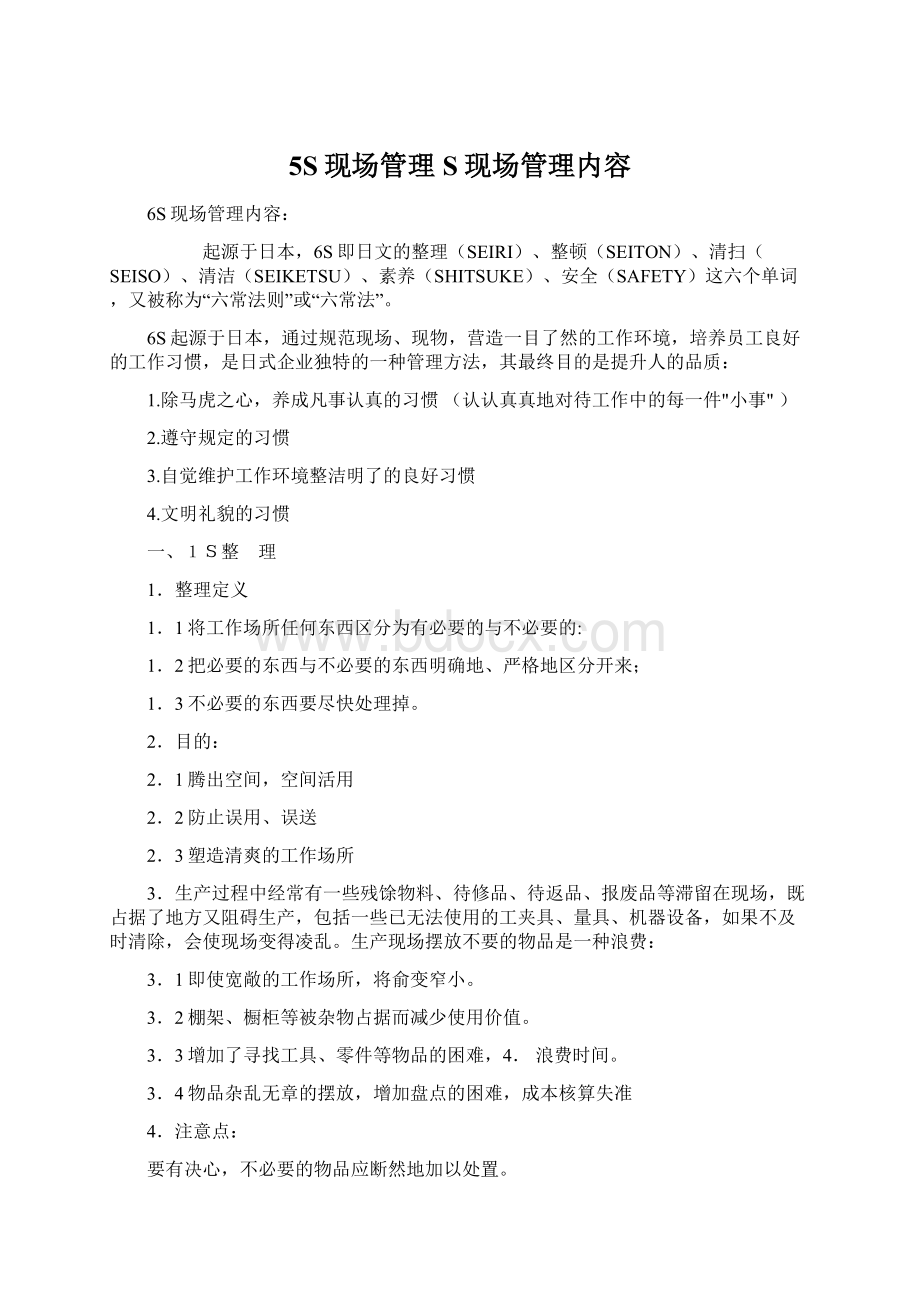
5S现场管理S现场管理内容
6S现场管理内容:
起源于日本,6S即日文的整理(SEIRI)、整顿(SEITON)、清扫(SEISO)、清洁(SEIKETSU)、素养(SHITSUKE)、安全(SAFETY)这六个单词,又被称为“六常法则”或“六常法”。
6S起源于日本,通过规范现场、现物,营造一目了然的工作环境,培养员工良好的工作习惯,是日式企业独特的一种管理方法,其最终目的是提升人的品质:
1.除马虎之心,养成凡事认真的习惯(认认真真地对待工作中的每一件"小事")
2.遵守规定的习惯
3.自觉维护工作环境整洁明了的良好习惯
4.文明礼貌的习惯
一、1S整 理
1.整理定义
1.1将工作场所任何东西区分为有必要的与不必要的:
1.2把必要的东西与不必要的东西明确地、严格地区分开来;
1.3不必要的东西要尽快处理掉。
2.目的:
2.1腾出空间,空间活用
2.2防止误用、误送
2.3塑造清爽的工作场所
3.生产过程中经常有一些残馀物料、待修品、待返品、报废品等滞留在现场,既占据了地方又阻碍生产,包括一些已无法使用的工夹具、量具、机器设备,如果不及时清除,会使现场变得凌乱。
生产现场摆放不要的物品是一种浪费:
3.1即使宽敞的工作场所,将俞变窄小。
3.2棚架、橱柜等被杂物占据而减少使用价值。
3.3增加了寻找工具、零件等物品的困难,4.浪费时间。
3.4物品杂乱无章的摆放,增加盘点的困难,成本核算失准
4.注意点:
要有决心,不必要的物品应断然地加以处置。
5.实施要领:
5.1自己的工作场所(范围)全面检查,包括看得到和看不到的
5.2制定「要」和「不要」的判别基准
5.3将不要物品清除出工作场所
5.4对需要的物品调查使用频度,决定日常用量及放置位置
5.5制订废弃物处理方法
5.6每日自我检查
二、2S整顿
1.整顿定义:
1.1对整理之后留在现场的必要的物品分门别类放置,2.排列整齐。
1.2明确数量,2.并进行有效地标3.识。
2.目的:
2.1工作场所一目了然
2.2整整齐齐的工作环境
2.3消除找寻物品的时间
2.4消除过多的积压物品
3.注意点:
这是提高效率的基础。
4.实施要领:
4.1前一步骤整理的工作要落实
4.2流程布置,确定放置场所
4.3规定放置方法、明确数量
4.4划线定位
4.5场所、物品标识
5.整顿的"3要素":
场所、方法、标识
5.1放置场所:
5.1.1物品的放置场所原则上要100%设定
5.1.2物品的保管要定点、定容、定量
5.1.3生产线附近只能放真正需要的物品
5.2放置方法:
5.2.1易取
5.2.2不超出所规定的范围
5.2.3在放置方法上多下工夫
5.3标识方法:
5.3.1放置场所和物品原则上一对一表示
5.3.2现物的表示和放置场所的表示
5.3.3某些表示方法全公司要统一
5.3.4在表示方法上多下工夫
6.整顿的"3定"原则:
定点、定容、定量
6.1定点:
放在哪里合适
6.2定容:
用什么容器、颜色
6.3定量:
规定合适的数量
三、3S清扫
1.清扫定义:
1.1将工作场所清扫干净。
1.2保持工作场所干净、亮丽的环境。
2.目的:
2.1消除赃污,保持职场内干干净净、明明亮亮
2.2稳定品质
2.3减少工业伤害
3.注意点:
3.1责任化
3.2制度化
4.实施要领:
4.1建立清扫责任区(室内、外)
4.2执行例行扫除,清理脏污
4.3调查污染源,予以杜绝或隔离
4.4建立清扫基准,作为规范
四、4S清洁
1.清洁定义
将上面的3S实施的做法制度化、规范化,并贯彻执行及维持结果。
2.目的:
维持上面3S的成果
3.注意点:
制度化,定期检查。
4.实施要领:
4.1落实前面3S工作
4.2制订考评方法
4.3制订奖惩制度,加强执行
4.4高阶主管经常带头巡查,以表重视
五、5S素养
1.素养定义
通过晨会等手段,提高全员文明礼貌水准。
培养每位成员养成良好的习惯,并遵守规则做事。
开展5S容易,但长时间的维持必须靠素养的提升。
2.目的:
2.1培养具有好习惯、遵守规则的员工
2.2提高员工文明礼貌水准
2.3营造团体精神
3.注意点:
长期坚持,才能养成良好的习惯。
4.实施要领:
4.1制订服装、仪容、识别证标准
4.2制订共同遵守的有关规则、规定
4.3制订礼仪守则
4.4教育训练(新进人员强化5S教育、实践
4.5推动各种精神提升活动(晨会、礼貌运动等)
六、6S安全
1.定义
指企业在产品的生产过程中,能够在工作状态、行为、设备及管理等一系列活动中给员工带来即安全又舒适的工作环境。
2.目的
2.1发现安全隐患并予以及时消除
2.2争取有效预防措施
3.注意点
前面“5S”的实施的前提
4.实施要领
4.1采取系统的措施保证人员、场地、物品等安全
4.2系统的建立防伤病、防污、防火、防水、防盗、防损等保安措施
七、6S现场管理法的推行步骤
掌握了6S现场管理法的基础知识,尚不具备推行6S活动的能力。
因推行步骤、方法不当导致事倍功半,甚至中途夭折的事例并不鲜见。
因此,掌握正确的步骤、方法是非常重要的。
1.步骤1:
成立推行组织
1.1推行委员会及推行办公室成立
1.2组织职掌确定
1.3委员的主要工作
1.4编组及责任区划分
建议由企业主要领导出任6S活动推行委员会主任职务,以视对此活动之支持。
具体安排上可由副主任负责活动的全面推行。
2.步骤2:
拟定推行方针及目标
2.1方针制定:
推动6S管理时,制定方针做为导入之指导原则
2.1.1例一:
推行6S管理、塑中集一流形象
2.1.2例二:
告别昨日,挑战自我,塑造捷虹新形象
2.1.3例三:
于细微之处着手,塑造公司新形象
2.1.4例四:
规范现场·现物、提升人的品质
方针的制定要结合企业具体情况,要有号召力。
方针一旦制定,要广为宣传。
目标制定:
2.2先予设定期望之目标,做为活动努力之方向及便于活动过程中之成果检查
2.2.1例一:
第4个月各部门考核90分以上
例二:
有来宾到厂参观,不必事先临时做准备
目标的制定也要同企业的具体情况相结合。
3.步骤3:
拟定工作计划及实施方法
3.1拟定日程计划做为推行及控制之依据
3.2收集资料及借鉴他厂做法
3.3制定6S活动实施办法
3.4制定要与不要的物品区分方法
3.5制定6S活动评比的方法
3.6制定6S活动奖惩办法
4.7其他相关规定(5S时间等)
3.8大的工作一定要有计划,以便大家对整个过程有一个整体的了解。
项目责任者清楚自己及其他担当者的工作是什么及何时要完成,相互配合造就一种团队作战精神。
4.步骤4:
教育
4.1每个部门对全员进行教育
4.26S现场管理法的内容及目的 4.36S现场管理法的实施方法
4.46S现场管理法的评比方法 4.5新进员工的6S现场管理法训练
教育是非常重要,让员工了解6S活动能给工作及自己带来好处从而主动地去做,与被别人强迫着去做其效果是完全不同的。
教育形式要多样化,讲课、放录像、观摩他厂案例或样板区域、学习推行手册等方式均可视情况加以使用。
5.步骤5:
活动前的宣传造势
5.16S活动要全员重视、参与才能取得良好的效果
5.2最高主管发表宣言(晨会、内部报刊等)
5.3海报、内部报刊宣传
5.4宣传栏
6.步骤6:
实施
6.1前期作业准备
6.1.1方法说明会 6.1.2道具准备
6.2工厂"洗澡"运动(全体上下彻底大扫除)
6.3建立地面划线及物品标识标准
6.4“3定”、“3要素”展开
6.5定点摄影
6.6做成“6S日常确认表”及实施
6.7红牌作战
7.步骤7:
活动评比办法确定
7.1加权系数:
7.1.1困难系数、人数系数、面积系数、教养系数
7.2考核评分法
8.步骤8:
查核
8.1现场查核
8.26S问题点质疑、解答
8.3举办各种活动及比赛(如征文活动等)
9.步骤9:
评比及奖惩
依6S活动竞赛办法进行评比,公布成绩),实施奖惩。
10.步骤10:
检讨与修正
10.1各责任部门依缺点项目进行改善,不断提高。
10.1.1QC手法 10.1.2IE手法
10.2在6S活动中,适当的导入QC手法、IE手法是很有必要的,能使6S活动推行得更加顺利、更有成效。
11.步骤11:
纳入定期管理活动中
11.1标准化、制度化的完善
11.2实施各种6S现场管理法强化月活动:
需要强调的一点是,企业因其背景、架构、企业文化、人员素质的不同,推行时可能会有各种不同的问题出现,推行办要根据实施过程中所遇到的具体问题,采取可行的对策,才能取得满意的效果。
八、6S现场管理法实施要点
1.整理:
正确的价值意识---「使用价值」,而不是「原购买价值」
2.整顿:
正确的方法---「3.3要素、3定」4.+整顿的技术
5.清扫:
责任化---明确岗位6S责任
6.清洁:
制度化及考核---6S时间;稽查、竞争、奖罚
7.素养:
长期化---晨会、礼仪守则
九、6S现场管理法与其他管理活动的关系
1.6S是现场管理的基础,是TPM(全面生产管理)的前提,是TQM(全面品质管理)的第一步,也是ISO9000有效推行的保证。
2.6S现场管理法能够营造一种"人人积极参与,事事遵守标准"的良好氛围。
有了这种氛围,推行ISO、TQM、及TPM就更容易获得员工的支持和配合,有利于调动员工的积极性,形成强大的推动力。
3.实施ISO、TQM、TPM等活动的效果是隐蔽的、长期性的,一时难以看到显著的效果。
而6S活动的效果是立竿见影。
如果在推行ISO、TQM、TPM等活动的过程中导入6S,可以通过在短期内获得显著效果来增强企业员工的信心。
4.6S是现场管理的基础,6S水平的高低,代表着管理者对现场管理认识的高低,这又决定了现场管理水平的高低,而现场管理水平的高低,制约着ISO、TPM、TQM活动能否顺利、有效地推行。
通过6S活动,从现场管理着手改进企业"体质",则能起到事半功倍的效果。
6S管理实施办法
1.目的
为了有效开展6S管理活动,调动全体员工参与与现场的改善的积极性和创造性,以及对现场实施6S管理的监督,确保现场6S能持之以恒的运行。
2.适用范围
公司所有人员
3.工作职责
3.16S推动小组负责本公司6S管理的培训教育、推进、监督、评定及奖惩工作。
3.2各部门领导、车间主任及班组长负责本部门6S的管理工作。
3.3全体员工参与6S实施活动。
4.工作程序
4.16S的检查标准及考核办法
4.1.16S检查标准及考核办法(车间)
序号
检查项目
检查内容
评分
1
地面标识
地面通道没有标识,每处
-1
地面通道标识不明确,每处
-1
地面涂层有人为损坏,每外扣责任部门
-1
2
工位器具
工位器具上有灰尘、油污、垃圾等,每个扣相关部门
-1
工位器具上存放的零件与工位器具不符合,每个
-1
现场有工位器具损坏没有及时报修(或负责修理部门没及时给予修理),每个扣相应责任部门
-2
工位器具上存放的零件没按存放要求存放,每个扣相应责任部门
-1
工位器具摆放乱,每处
-1
3
零件
零件有工位器具不放,而直接放于地面,每个
-2
非工位上的零件的检验状态无标识,每种
-1
工位上的不合格件无明显标识,每处
-2
生产车间现场的不合格件在3日内没有处理(若相关部门没有及时办理手续,则扣相关部门),每种
-2
零件掉地上无人拾起,每处扣
-3
4
工作角
班组园地内的桌椅不清洁,每处
-1
工作角内物品摆放乱,每处
-1
工作角内的物品损坏没有及时修理,每件
-2
班组园地使用的桌椅放于工作角之外的地方,每处
-1
5
目视板
班组无目视板,每少1块
-2
目视板表面脏(如灰尘、污垢、擦拭不干净),每处
-2
目视板损坏,每块
-2
目视板牌面乱,塑料袋破损,未更换,每处
-1
目视板有栏目,但内容空白,每处
-2
目视板牌面过时和信息过时,每处
-1
目视板未定置或未放于规定位置,每块
-1
6
工具箱
工具箱不清洁,每个
-1
工具箱上或下放有杂物,每个
-1
工具箱内没有物品清单或物单不符,每个
-1
箱中物品摆乱,取用不便,每个
-1
工具箱损坏没有及时修理,每个
-2
7
厂房内
空间
窗台、窗户玻璃脏(灰尘、蛛网等),每处
-1
厂房墙壁、立柱上有乱贴、乱画或陈旧标语痕迹,每处
-2
厂房四壁有积灰,每处
-1
厂房内有漏雨或渗水(没及时报修扣专业厂,相关部门未及时处理,扣相关部门),每处
-3
厂房内物流通道、安全通道上有阻塞物,每处
-2
8
现场区划
定置线内无定置物,每处
-1
现在没有设置不同状态件存放区域或区域无标识、标识不明确,每处
-2
现场存放的件与区域标识不一致,每处
-2
9
垃圾及
清运
工位上的包装垃圾没有放于指定的垃圾箱,每处
-1
垃圾箱(桶)内垃圾外溢,每处
-2
垃圾箱没有放于规定的位置
-1
工业垃圾和生活垃圾混放的,每处
-1
10
工艺文件
有过期的或者不必要的文件,每件
-2
文件没有按规定的位置摆放,每件
-1
文件摆放混乱、不整齐的,每处
-1
文件不清洁,有灰尘、脏污的,每件
-1
文件撕裂和损坏的,每件
-2
11
设备
设备有损坏或松动的且没有及时维修的,每处
-2
设备没有按规定位置存放的,每件
-1
设备污脏,每件
-1
设备上放有杂物,每件
-1
12
工作台
工作台不清洁,有积尘、油污的,每张
-1
工作台没按规定位置摆放的,每张
-1
工作台上物品摆放混乱,每张
-1
工作台上放有杂物,每张
-1
13
工装
工装的使用和保存方法不正确的,每件
-1
工装没有放在指定的位置,每件
-1
工装不清洁或有脏痕的,每件
-1
工装有损坏没有及时修理的,每件
-2
工装上放有杂物,每件
-1
14
照明
照明设备污脏,每处
-1
照明设备损坏没有及时修理(根据具体扣相应责任单位),每处
-2
15
水电气等各种线管
使用过程中,有污脏的,每处
-1
有跑、冒、滴、漏等损坏或连接松动的,每处
-2
16
生活卫生设施
卫生间不清洁、有异味,每处
-1
洗手池不清洁、有异味、污垢等,每处
-1
卫生间内有杂物,每处
-1
清洁用具没有放于指定的位置,每处
-2
17
人员素养
员工现场打闹,举止不文明的,吸烟的,每人次
-2
员工说脏话,语言不文明,每人次
-1
违反工艺,野蛮操作的,每人次
-3
没有按规定佩戴劳保用品的,每人次
-1
4.1.26S检查标4.1.3准及考核办法(办公室)
序号
检查项目
检查内容
评分
1
办公室
办公室无有标识,每处
-2
有非必需品,每件
-3
2
办公桌
文件、资料放置凌乱,并正确放在文件框内,每件
-3
文件夹上必有标识,并正确放在文件框内,每件
-5
抽屉内物品摆放杂乱,每次
-3
私人物品应分开、整齐摆放一处,每
-3
3
台下、地面
除清洁用具处不得放置任何物品,每处
-3
地面保持干净,无垃圾、无污迹及纸屑等,每处
-3
垃圾筒内垃圾及时清理,每次
-3
4
办公椅
办公椅、办公桌应保持干净、无污迹、灰尘,每处
-3
人离开办公桌后,办公椅应推到桌下,且应紧挨办公桌平行放置,每次
-3
椅背上不允许摆放衣服和其它物品,每次
-3
5
文件柜
应保持柜面干净、无灰尘,每次
-3
柜外应有标识,每处
-3
柜内文件(或物品)摆放整齐,并分类摆放,每处
-3
柜内不得摆放非必需品,每件
-3
文件夹上要标识,每件
-3
6
人员素质
按规定穿工作服,佩带员工证,每人
-5
工作服扣子必须全部扣上,掉了必须补上并保持干净,每人
-3
工作态度要良好,每次
-4
不乱扔烟头、果皮,不随地吐痰,每个
-3
7
门、窗等
保持门、窗干净、无灰尘、无蜘蛛网,每处
-3
人走后(或无人时)应关闭门、窗,每次
-5
8
电脑、复印机等
应保持干净,无灰尘、无污迹,每次
-3
电脑线应整齐,不得凌乱,每次
-3
9
电话,
传真等
应保持干净,电话线不得凌乱,每次
-3
10
其它电器
无人时须关闭电源,每次
-5
饮水机保持干净,每次
-3
坏了及时维修(或申报维修),每次
-5
4.1.36S检查标准及考核办法(仓库)
序号
检查项目
检查内容
评分
1
地面标识
地面通道没有标识,每处
-2
地面通道标识不明确,每处
-1
地面涂层有人为损坏,每外扣责任部门
-2
2
工位器具
工位器具上有灰尘、油污、垃圾等,每个扣相关部门
-2
工位器具上存放的零件与工位器具不符合,每个
-2
现场有工位器具损坏没有及时报修(或负责修理部门没及时给予修理),每个扣相应责任部门
-2
工位器具上存放的零件没按存放要求存放,每个扣相应责任部门
-2
工位器具摆放乱,每处
-2
3
物资
物资没有按规定定置摆放,每处
-2
不合格物资无明显标识,每处
-1
物资没有标识或标识不明确,每处
-2
物资摆放混乱,每处
-2
物资没有摆放在规定的架、箱、柜等专用器具上,每件
-2
4
工作角
仓库园地内的桌椅不清洁,每处
-1
工作角内物品摆放乱,每处
-2
工作角内的物品损坏没有及时修理,每件
-2
仓库园地使用的桌椅放于工作角之外的地方,每处
-1
5
目视板
仓库无目视板,每少1块
-2
目视板表面脏(如灰尘、污垢、擦拭不干净),每处
-2
目视板损坏,每块
-2
目视板牌面乱,塑料袋破损,未更换,每处
-2
目视板有栏目,但内容空白,每处
-2
目视板牌面过时和信息过时,每处
-2
目视板未定置或未放于规定位置,每块
-2
6
厂房内
空间
窗台、窗户玻璃脏(灰尘、蛛网等),每处
-2
厂房墙壁、立柱上有乱贴、乱画或陈旧标语痕迹,每处
-2
厂房四壁有积灰,每处
-2
厂房内有漏雨或渗水(没及时报修扣专业厂,相关部门未及时处理,扣相关部门),每处
-2
厂房内物流通道、安全通道上有阻塞物,每处
-2
7
现场区划
定置线内无定置物,每处
-1
现在没有设置不同状态件存放区域或区域无标识、标识不明确,每处
-2
现场存放的件与区域标识不一致,每处
-2
8
垃圾及
清运
工位上的包装垃圾没有放于指定的垃圾箱,每处
-1
垃圾箱(桶)内垃圾外溢,每处
-2
垃圾箱没有放于规定的位置
-1
工业垃圾和生活垃圾混放的,每处
-2
9
文件资料
有过期的或者不必要的文件和资料,每件
-2
文件和资料没有按规定的位置摆放,每件
-2
文件和资料摆放混乱、不整齐的,每处
-1
文件和资料不清洁,有灰尘、脏污的,每件
-2
文件和资料撕裂和损坏的,每件
-2
10
工作台
工作台不清洁,有积尘、油污的,每张
-2
工作台没按规定位置摆放的,每张
-2
工作台上物品摆放混乱,每张
-1
工作台上放有杂物,每张
-1
11
照明
照明设备污脏,每处
-1
照明设备损坏没有及时修理(根据具体扣相应责任单位),每处
-2
12
水电气等各种线管
使用过程中,有污脏的,每处
-2
有跑、冒、滴、漏等损坏或连接松动的,每处
-2
13
生活卫
生设施
卫生间不清洁、有异味,每处
-2
洗手池不清洁、有异味、污垢等,每处
-2
卫生间内有杂物,每处
-1
清洁用具没有放于指定的位置,每处
-2
14
人员素养
员工现场打闹,举止不文明的,吸烟的,每人次
-2
员工说脏话,语言不文明,每人次
-2
违反工艺,野蛮操作的,每人次
-2
4.26S的评比办法
4.2.16S推动小组定期或不4.2.2定期到现场进行巡查,4.2.3并按6S检查标4.2.4准进行检查。
4.2.56S推动小组主任委员将检查记录进行统计,4.2.6并将成绩在公司公告栏上进行公布,4.2.7成绩的好坏以相应的颜色标4.2.8识表示:
绿色○:
90分以上 蓝色○:
80~89分
黄色○:
70~79分 红色○:
70分以下
4.2.3评比以月度为单位进行,取第一名,授予“本月度6S最佳单位”锦旗和发放奖金50元,最后一名发给“本月度6S最差单位”警示旗和罚款50元。
4.2.4锦旗、奖金和警示旗于每月度现场改善成果发布会上颁发,所颁锦旗和警示旗于下次现场改善成果发布会前收回,所颁发锦旗和警示旗必须悬挂于指定位置。
4.2.5成绩均未达到80分时,不颁发第一名锦旗,成绩均超过80分以上,不发最后一名警示旗。
4.2.6颁发的奖金作为部门基金,用作部门文化建设或公共活动基金,严禁将奖金平分下发和私分。