实施焦化清洁生产 促进钢铁企业可持续发展.docx
《实施焦化清洁生产 促进钢铁企业可持续发展.docx》由会员分享,可在线阅读,更多相关《实施焦化清洁生产 促进钢铁企业可持续发展.docx(7页珍藏版)》请在冰豆网上搜索。
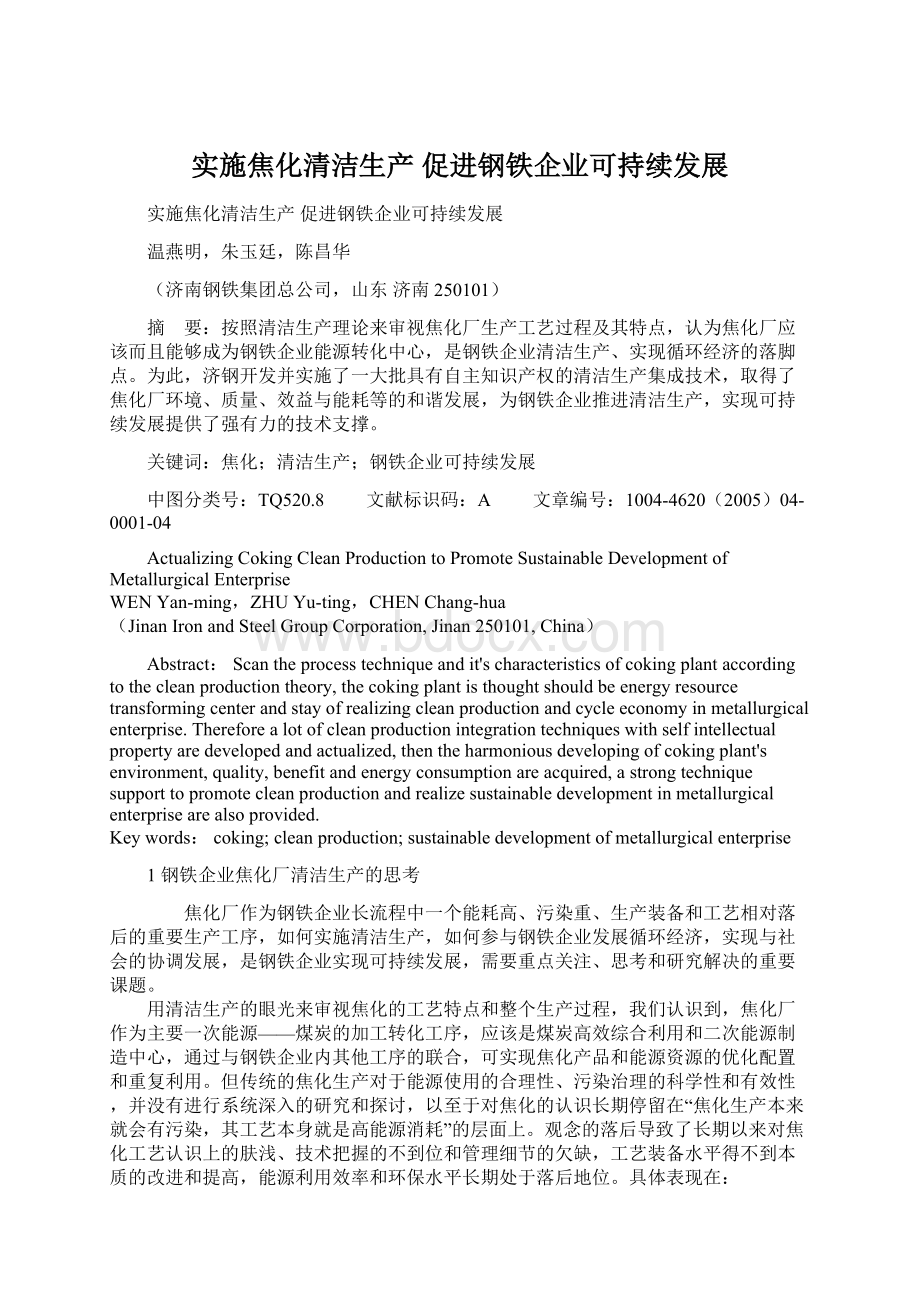
实施焦化清洁生产促进钢铁企业可持续发展
实施焦化清洁生产促进钢铁企业可持续发展
温燕明,朱玉廷,陈昌华
(济南钢铁集团总公司,山东济南250101)
摘 要:
按照清洁生产理论来审视焦化厂生产工艺过程及其特点,认为焦化厂应该而且能够成为钢铁企业能源转化中心,是钢铁企业清洁生产、实现循环经济的落脚点。
为此,济钢开发并实施了一大批具有自主知识产权的清洁生产集成技术,取得了焦化厂环境、质量、效益与能耗等的和谐发展,为钢铁企业推进清洁生产,实现可持续发展提供了强有力的技术支撑。
关键词:
焦化;清洁生产;钢铁企业可持续发展
中图分类号:
TQ520.8 文献标识码:
A 文章编号:
1004-4620(2005)04-0001-04
ActualizingCokingCleanProductiontoPromoteSustainableDevelopmentofMetallurgicalEnterprise
WENYan-ming,ZHUYu-ting,CHENChang-hua
(JinanIronandSteelGroupCorporation,Jinan250101,China)
Abstract:
Scantheprocesstechniqueandit'scharacteristicsofcokingplantaccordingtothecleanproductiontheory,thecokingplantisthoughtshouldbeenergyresourcetransformingcenterandstayofrealizingcleanproductionandcycleeconomyinmetallurgicalenterprise.Thereforealotofcleanproductionintegrationtechniqueswithselfintellectualpropertyaredevelopedandactualized,thentheharmoniousdevelopingofcokingplant'senvironment,quality,benefitandenergyconsumptionareacquired,astrongtechniquesupporttopromotecleanproductionandrealizesustainabledevelopmentinmetallurgicalenterprisearealsoprovided.
Keywords:
coking;cleanproduction;sustainabledevelopmentofmetallurgicalenterprise
1钢铁企业焦化厂清洁生产的思考
焦化厂作为钢铁企业长流程中一个能耗高、污染重、生产装备和工艺相对落后的重要生产工序,如何实施清洁生产,如何参与钢铁企业发展循环经济,实现与社会的协调发展,是钢铁企业实现可持续发展,需要重点关注、思考和研究解决的重要课题。
用清洁生产的眼光来审视焦化的工艺特点和整个生产过程,我们认识到,焦化厂作为主要一次能源——煤炭的加工转化工序,应该是煤炭高效综合利用和二次能源制造中心,通过与钢铁企业内其他工序的联合,可实现焦化产品和能源资源的优化配置和重复利用。
但传统的焦化生产对于能源使用的合理性、污染治理的科学性和有效性,并没有进行系统深入的研究和探讨,以至于对焦化的认识长期停留在“焦化生产本来就会有污染,其工艺本身就是高能源消耗”的层面上。
观念的落后导致了长期以来对焦化工艺认识上的肤浅、技术把握的不到位和管理细节的欠缺,工艺装备水平得不到本质的改进和提高,能源利用效率和环保水平长期处于落后地位。
具体表现在:
(1)蒸汽一直是焦化化工生产过程中所依赖的最主要的能源介质,人们并没有认识到它是一种劣质低效的能源。
一方面是其本身传热效率不高;另一方面难以重复利用,变成冷凝水后成为生产污水。
(2)使用中温循环水冷却化工产品,存在循环量大、蒸发量多、化产品的冷却效率低、化产品挥发量大等缺陷,造成能源动力消耗和操作费用高、环境污染大,新水消耗居高不下。
(3)以红焦、荒煤气显热为主的余热大量存在,不但没有很好地回收利用,反而需要耗费更多的冷媒水进行冷却,同时化产系统还存在着频繁的加热与冷却过程,造成了能源的巨大浪费。
(4)以装煤、推焦和筛焦过程为主的扬尘问题,因为对环境保护的认识水平不够高和单纯出于对经济效益的考虑,一直未引起足够的重视。
(5)“三大恶臭气”即:
粗酚分解气、高温沥青烟、蒸氨分缩冷凝气的污染,由于工艺、装备落后,长期得不到良好的解决。
(6)生产过程中产生的焦粉、化产渣、酸焦油等一直被视作废弃物,在浪费资源的同时,也造成了严重的环境污染。
(7)废水外排,不但浪费了资源,还需交纳排污费。
尤其是作为钢铁联合企业内部的焦化厂,没有认真分析废水在全公司范围内可能的使用途径。
(8)落后的浓氨水生产工艺带来了氨资源的浪费和环境的污染。
(9)落后的装备和控制水平导致生产效率低,使资源、能源的浪费和环境污染问题难以有效的解决。
经过以上认真调研和分析,济南钢铁集团总公司(简称济钢)对焦化厂进行了重新认识和定位,并将焦化厂列为实现钢铁企业可持续发展的重点和突破点,形成了焦化厂清洁生产全新观念:
(1)焦化厂应由传统的“供应焦炭、满足钢铁生产的角色”转变为“钢铁企业的能源转化中心”;
(2)焦化厂在钢铁企业中是能源、资源、产品、工艺、技术密集型生产单元,也应是最具潜力、最有条件、最迫切需要发展的环节;
(3)实现焦化生产的高效化、清洁化是实现钢铁企业可持续发展的落脚点;
(4)焦化厂应成为支撑钢铁企业实现可持续发展的基础单位。
2钢铁企业焦化厂清洁生产技术开发与实践
2.1以开发直燃型制冷机技术为突破口,大面积应用低温循环水,实现工业水的高效、低污染综合利用
针对采用中、低温循环水做冷媒存在的不足,济钢采取了以下措施:
一是对焦化循环水系统进行大面积改造,在化产品加工工序中广泛采用低温水用于冷却,使焦化循环水量比原来降低了60%,年可减少循环水蒸发量35.04万t,同时换热速度加快减少了化产品的挥发,解决了大量使用中温水存在的运行成本高、环境污染大的问题;
二是在国内首家研究应用了直燃型制冷技术,制冷机直接以燃烧煤气为热源,能源利用率明显提高,且杜绝了蒸汽生产和输送过程的能源浪费,大大提高了热效率,使制冷机的运行成本明显降低。
与蒸汽型制冷机相比,其热效率由32.13%提高到92%,每吨制冷水能耗由4.08kg标煤降到0.823kg标煤。
热效率的提高使焦化工序吨焦能耗降低了12.84kg标煤。
2.2开发无蒸汽蒸氨新工艺,提高能源利用效率,降低了生产成本,解决了蒸氨的环境污染问题
针对传统蒸氨生产中存在的能耗高、效率低、污染大、设备腐蚀严重的问题,济钢研究并移植了多溢流复合型斜孔塔板和以热导油为热媒介质替代蒸汽加热两项核心技术,成功开发出了无蒸汽高效蒸氨新工艺,提高了蒸氨塔的效率。
(1)高效塔板由于具有独特的结构,使蒸氨塔的空速得以提高,消除了旧蒸氨工艺存在的气、液相并流的问题,大大提高了气、液相的接触时间,从而提高了蒸氨塔的传质和传热效率。
(2)用热媒介质代替蒸汽作热源,解决了蒸汽使用效率低、废水量大的问题,大大降低了能源消耗。
(3)蒸氨后的氨在密闭状态下直接送至脱硫系统做碱源,消除了因氨气外逸造成的环境污染。
(4)自主开发高防腐不锈钢复合板,应用于蒸氨装置,大大提高了蒸氨塔寿命,降低了运行成本。
新蒸氨工艺与旧蒸氨工艺比较:
不用蒸汽年少产生污水21.02万t,氨利用率提高78%,热效率提高54.2%,焦化工序吨焦能耗降低22.16kg标煤。
2.3开发自带除尘式装煤车,实现了装煤的低耗高效除尘
针对目前装煤除尘技术的不足,济钢设计、制造了国内第一台集除尘和加煤于一体的车载式干式除尘加煤车。
该新式装煤车除尘采用非燃烧、干式烟尘净化、低阻文丘里脉冲袋式除尘器和预喷涂技术,装煤采用螺旋给料和球面密封导套。
它的投用克服了地面站除尘系统处理大量荒煤气的弊端,提高了除尘效率,也没有水的二次污染问题。
经除尘收集下来的粉尘又掺入装炉煤使用,解决了粉尘外排问题。
与除尘地面站相比,不但达到了相同的除尘效果(烟尘捕集率大于95%、除尘净化率大于99%),而且节省了大量投资,操作方便、运行费用低,不需配备操作人员及额外占地,还实现了粉尘的回收利用。
2.4研究开发了高压水自动清扫炉门新技术,彻底改善炉门部位的荒煤气泄漏,减轻了环境污染
焦炉炉门高压水自动清扫系统通过在上下及两侧设置水压高达65MPa的高压水喷枪,产生高压高速的水流对炉门不锈钢刀边、密封槽以及耐火砖进行全方位、高效率清扫,实现了炉门管理的自动化,提高了炉门的密封质量,杜绝了炉门处外泄烟气对环境造成的污染,降低了操作者的劳动强度。
2.5改进干熄焦工艺,实现焦炭余热的资源化利用
(1)在干熄炉耐火材料砌筑方面,济钢成功研究应用了五段组合式砌炉技术。
该技术针对干熄炉不同部位对耐温、耐压和耐磨要求的不同,研究开发了相应的耐火材料,并采取了不同的组合砌筑方法,大大提高了干熄炉炉体的使用寿命,由设计的0.5年提高到2年,降低了干熄焦的运行成本。
(2)余热锅炉采用自然循环工艺,降低了锅炉的泄漏率,节省了强制循环所用的设备投资和运行费用,提高了锅炉的热效率。
(3)研究应用湿式陶瓷多管除尘专利技术,提高了除尘效率,减少了环境污染。
2.6研究开发湿磨焦粉配煤炼焦新工艺,实现了焦粉低污染、高效益的最佳资源化利用
研究认为,焦粉在水中出现渗淅及水膜现象,强度和耐磨性大幅度降低,据此原理济钢成功开发了焦粉湿磨配煤炼焦新工艺。
其主要流程是利用球磨机将焦粉掺水后进行细磨,细磨后的焦粉通过真空过滤机过滤,达到粒度要求的经沉淀脱水后送至配煤系统,粒度较大的部分重新回到球磨机二次研磨直至合格。
焦粉配煤研究与应用,实现了焦粉的无污染闭路循环利用,获得了环境和效益的双丰收。
2.7开发化产废渣粘结剂技术配煤炼焦新工艺技术,实现了焦化三大渣资源化闭路应用
利用化产废渣做粘结剂生产型煤进行配煤炼焦,既解决了化产废渣对环境造成的污染问题,又可使废物变成资源得到利用。
此外,济钢还开发了工业水小半径使用和分区域循环的高效低污染利用技术,实现了工业水外排为零;开发利用焦炉烟道废气分解酚钠盐工艺,解决了硫酸分解工艺废气对环境的污染问题;自主开发单塔脱苯工艺,大大缩短了粗苯生产的工艺流程,降低了设备投资和生产运行成本;实现利用导热油代替蒸汽进行苯精制和精苯生产气相连料技术,大大降低了苯精制的能耗,减少了污水的产生;开发多焦炉集气管压力模糊自动控制技术,实现了集气管压力的稳定控制,解决了因集气管压力波动造成的荒煤气外逸所产生的环境污染问题;研究焦化废水分级处理技术,实现了焦化蒸氨废水用于炼铁冲渣;实施余热采暖技术,年回收余热415.32×108kJ,焦化工序吨焦能耗降低22.52kg标煤等。
另外,引进沥青水下成型技术,消灭了沥青烟对环境的污染;应用焦侧推焦拦焦除尘地面站技术,彻底解决了推焦过程中的扬尘污染问题。
在新上的煤气回收净化系统中,首次把脱硫系统放在鼓风机前(负压区域),实现了煤气净化系统半负压工艺技术的应用,避免了原有工艺中存在的机后高温煤气进脱硫系统前需二次冷却而造成的能源浪费。
3焦化厂清洁生产效果
(1)焦化工序能耗持续大幅降低,从最初的高于202kg标煤降到94kg标煤,如图1所示。
图1 济钢焦化厂历年综合工序能耗趋势图
(2)实现了工业水循环、废水零排放。
吨焦耗新水从以前的20.98m3降至目前的1.23m3,节新水经济效益显著。
如图2所示。
图2 济钢焦化厂吨焦耗水历史趋势图
(3)蒸汽消耗逐年减少,节能效果和环保效益显著。
吨焦耗蒸汽由410kg降至26kg,因化工工序用汽量大大减少,杜绝了由纯净的蒸汽在生产过程中变为废水对环境造成的污染。
如图3所示。
图3 济钢焦化厂历年吨焦耗蒸汽趋势图
(4)工业废气排放量显著降低。
吨焦排放量由以前的2311m3降至1506m3,吨焦SO2、烟尘、粉尘排放量分别由原0.7、0.1、0.17kg降至0.05、0.004、0.08kg。
年回收利用粉尘12775t,废渣3712t。
(5)直接经济效益显著。
焦化清洁生产技术开发与应用后,年经济效益达2.68亿元。
若在全国推广应用,按年产焦炭1.36亿t计,年可创直接经济效益236.6亿元。
(6)焦化区域大气环境得以改善,基本实现了舒适、美丽的现代化花园式工厂的目标。
4用循环经济理念构建焦化生产新流程
随着济钢发展循环经济规划方案的全面启动,今后将按照资源高效利用、能源高效转化、代谢物高效再生的原则,积极开发焦化生产的绿色新工艺,构建焦化厂的反馈式物质循环新流程,吸纳、消化社会废弃物应用于焦化生产,进一步实现物质-能源循环链的延伸和扩展,充分发挥焦化厂“能源转化中心”的功能,向钢铁流程和周边社区提供清洁能源和产品,实现钢铁企业的社会友好型转换。
如图4所示。
图4 焦化厂能源转化示意图
4.1主要思路
(1)从能源的高效利用与转化、资源的高效利用和废弃物的高效再生、服务社会功能的充分发挥方面,开展清洁生产。
(2)更注重能源、资源的高效利用,追求企业效益、环境效益、社会效益的和谐统一。
(3)更加重视以自动化水平的提升提高生产效率,实现高效经济,满足循环经济的发展需求。
4.2具体措施
4.2.1“三干”技术的开发
(1)开发以焦炉烟道废气为热源的风选破碎技术与煤调湿相结合的煤热整粒工艺技术,达到焦炭产量提高5%~10%、质量明显改善、吨焦工序能耗降低15.2kg标煤、减少剩余氨水6万t/a的目标。
(2)研究应用处理能力达到150t/h的大型干熄焦技术,更好地回收利用焦炭余热,改善焦炭质量。
(3)以导热油技术的推广应用为主线,开发以热媒油为热源的新型制冷机和太阳能利用等技术,全面实现化产工序无蒸汽生产,并逐步实现生活用能方式的改变,进一步降低焦化工序能耗。
4.2.2上升管余热回收利用发电技术充分利用国际先进的上升管余热回收技术,结合已有的热媒油利用技术,研究开发用热媒油回收上升管荒煤气余热并生产蒸汽用于发电的新技术。
4.2.3化产蒸馏系统推广应用负压蒸馏工艺技术,降低能耗,减少污染。
4.2.4自动化升级改造
实现翻车机无人操作;逐步实现焦炉机车无人操作;实现苯精制系统离线自动操作。
4.2.5开展配煤技术的深入研究,开发弱粘低灰、低硫煤配煤炼焦技术,缓解资源压力,提高产品清洁度,减少对环境的硫污染。
4.2.6研究开发废塑料配煤炼焦技术,实现企业社会友好功能。
5焦化清洁生产推动循环经济模式开发
5.1源于焦化的清洁生产理念,提出钢铁企业循环经济指导思想
蒸汽是劣质低效的传热介质;减少用水就是节能;减少蒸汽使用就是减少污染;污染是放错位置的资源;实施污染资源化治理就是可持续发展。
5.2源于焦化厂清洁生产技术,为钢铁企业实现循环经济提供坚强的技术支撑
第一个大型余热回收项目“干熄焦”的成功实施,拉开了济钢实施“分布式发电”的序幕;第一个实现工业用水闭路,其“小半径循环、分质用水、分区域闭路”的用水模式延伸到了济钢水系统调整中;第一个采用热导油技术,为济钢余热高效回收、余热资源高效利用提供了一种崭新的模式;第一个采用溴化锂制冷技术,推动济钢利用余热蒸汽制冷代替低效高能耗制冷设备成为现实;第一个实现取消蒸汽传热介质,带来济钢高效热能传质开发理念的更新。
5.3源于焦化的资源、能源使用模式,带动钢铁企业工艺结构和能源结构的调整
焦化厂水质技术的开发、管理与运行,推动了济钢用水结构的调整和节约;借鉴焦化厂焦炉蓄热式燃烧技术,实现了济钢加热炉的蓄热化;焦炉改烧低热值煤气,带动了济钢的煤气热值调整和结构调整,为最终实现燃气-蒸汽联合循环发电创造了条件;焦化高盐水用于烧结厂配料,焦化污水用于炼铁厂泡渣,开创了工序间废弃物资源化治理的新模式。
6结语
钢铁企业焦化厂全方位、全过程以循环经济理念实施源头削减、过程控制、末端资源化治理的有益探索,进一步证实焦化厂实现资源高效利用、能源高效转化、代谢物高效再生是可行的、有效的。
通过积极推行焦化厂的清洁生产,我们深刻体会到:
循环经济是知识经济、创新经济、高效经济、清洁经济,是提高企业竞争力的经济,是实现焦化企业可持续发展的必由之路,是当代企业家的历史责任;钢铁企业高效清洁生产的难点在焦化工序,潜力在焦化工序,焦化厂完全可以成为钢铁企业的能源转化中心。
只要转换视角,更新观念,坚持自主清洁生产技术开发,焦化企业清洁生产的目标就一定能实现,钢铁企业循环经济的目标也就一定能够实现。