铝合金搅拌摩擦焊焊缝受力及焊缝成型的关系.docx
《铝合金搅拌摩擦焊焊缝受力及焊缝成型的关系.docx》由会员分享,可在线阅读,更多相关《铝合金搅拌摩擦焊焊缝受力及焊缝成型的关系.docx(23页珍藏版)》请在冰豆网上搜索。
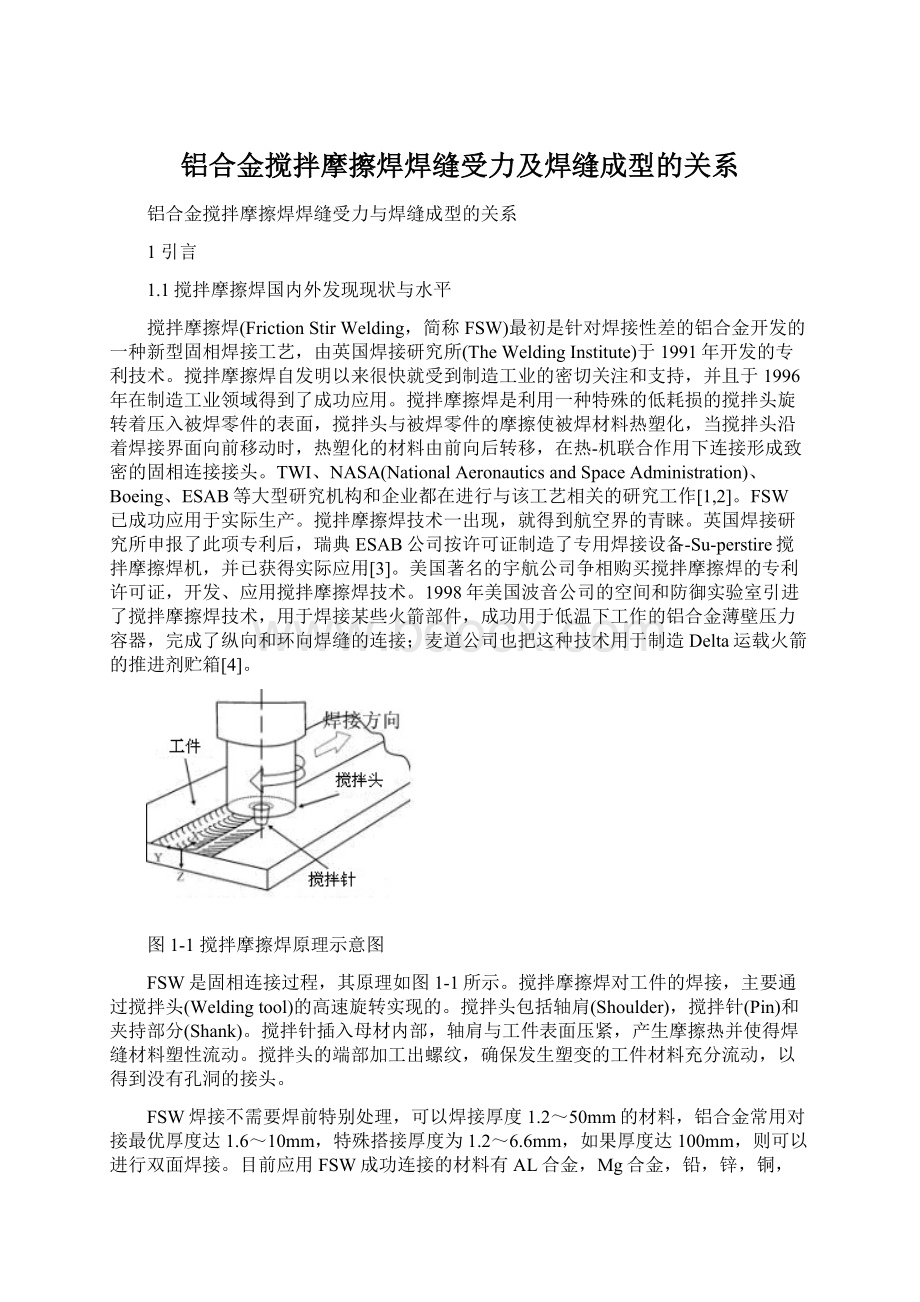
铝合金搅拌摩擦焊焊缝受力及焊缝成型的关系
铝合金搅拌摩擦焊焊缝受力与焊缝成型的关系
1引言
1.1搅拌摩擦焊国内外发现现状与水平
搅拌摩擦焊(FrictionStirWelding,简称FSW)最初是针对焊接性差的铝合金开发的一种新型固相焊接工艺,由英国焊接研究所(TheWeldingInstitute)于1991年开发的专利技术。
搅拌摩擦焊自发明以来很快就受到制造工业的密切关注和支持,并且于1996年在制造工业领域得到了成功应用。
搅拌摩擦焊是利用一种特殊的低耗损的搅拌头旋转着压入被焊零件的表面,搅拌头与被焊零件的摩擦使被焊材料热塑化,当搅拌头沿着焊接界面向前移动时,热塑化的材料由前向后转移,在热-机联合作用下连接形成致密的固相连接接头。
TWI、NASA(NationalAeronauticsandSpaceAdministration)、Boeing、ESAB等大型研究机构和企业都在进行与该工艺相关的研究工作[1,2]。
FSW已成功应用于实际生产。
搅拌摩擦焊技术一出现,就得到航空界的青睐。
英国焊接研究所申报了此项专利后,瑞典ESAB公司按许可证制造了专用焊接设备-Su-perstire搅拌摩擦焊机,并已获得实际应用[3]。
美国著名的宇航公司争相购买搅拌摩擦焊的专利许可证,开发、应用搅拌摩擦焊技术。
1998年美国波音公司的空间和防御实验室引进了搅拌摩擦焊技术,用于焊接某些火箭部件,成功用于低温下工作的铝合金薄壁压力容器,完成了纵向和环向焊缝的连接;麦道公司也把这种技术用于制造Delta运载火箭的推进剂贮箱[4]。
图1-1搅拌摩擦焊原理示意图
FSW是固相连接过程,其原理如图1-1所示。
搅拌摩擦焊对工件的焊接,主要通过搅拌头(Weldingtool)的高速旋转实现的。
搅拌头包括轴肩(Shoulder),搅拌针(Pin)和夹持部分(Shank)。
搅拌针插入母材内部,轴肩与工件表面压紧,产生摩擦热并使得焊缝材料塑性流动。
搅拌头的端部加工出螺纹,确保发生塑变的工件材料充分流动,以得到没有孔洞的接头。
FSW焊接不需要焊前特别处理,可以焊接厚度1.2~50mm的材料,铝合金常用对接最优厚度达1.6~10mm,特殊搭接厚度为1.2~6.6mm,如果厚度达100mm,则可以进行双面焊接。
目前应用FSW成功连接的材料有AL合金,Mg合金,铅,锌,铜,不锈钢,低碳钢等同种或异种材料。
国外许多人进行了铝合金-Ag的FSW焊接研究,对AM50,AM60,AZ31,AZ91镁合金同种和异种材料之间进行了FSW焊接试验,证明可以应用FSW连接镁合金。
FSW不仅对一系列铝合金成功连接,而且也实现了对高熔点材料Ti合金的连接。
TWI于1997年11月报道成功FSW焊接3mm厚的低碳钢,EWI(EdisonWeldingInstitute)于1998年5月报道成功连接6mm软钢,并报道12mm厚12%Cr不锈钢的FSW焊接[6]。
由此可知,随着搅拌摩擦焊技术的发展,FSW可以应用于更多的材料的连接。
1.2搅拌摩擦焊接的特点
1)能保持母材的冶金性能,焊接接头力学性能好
铝合金具有密度低、强度比高、刚度比高等优点,但是铝合金熔点较低、导热系数大、比热容大、线膨胀系数大,在采用熔化焊进行焊接时,易产生裂纹、气孔、变形等焊接缺陷。
同时,由于焊接温度较高,其性能会降低,因而限制了铝合金的广泛应用。
由于搅拌摩擦焊是一种固相焊接方法,在焊接铝合金时不会产生与熔化焊有关的焊接缺陷,也不会降低焊接接头的性能,而且,焊缝金属的晶粒结构比母材金属的更细小,焊缝金属的强度超过热影响区金属的强度,没有焊缝金属蒸发产生的合金元属损失,不改变合金的成分,因此接头的力学性能好。
2)焊后变形小、残余应力小
由于搅拌摩擦焊的焊接温度较低,焊接后结构的变形量和残余应力比熔化焊小得多。
同时,由于不存在熔焊过程中接头部位大范围的热塑性变形过程,焊后接头的内应力小、变形小,基本可实现板件的低应力低变形焊接。
3)焊接成本低、效率高
搅拌摩擦焊操作方便,能量利用效率高。
并且在焊前和焊接过程中对环境的污染小,焊前工件无须进行严格的表面清理准备,焊接过程中的摩擦和搅拌可以去除焊件表面的氧化膜,焊接过程中也无烟尘和飞溅。
还可以在有磁场的条件下进行焊接,并适合自动化焊接。
4)适用范围广
由于搅拌摩擦焊没有熔化焊所形成的裂纹,如液化裂纹或结晶裂纹,因此,可以焊接热裂纹敏感的材料;通过对挤压型材进行焊接,可制成大型结构,如船板、框架、平台等;搅拌摩擦焊能实现不同材料的焊接,如铝和银的连接。
搅拌摩擦焊可实现各种位置的焊接,并可实现多种形式的焊接接头,如对接、角接、搭接接头,甚至厚度变化的结构和多层材料的连接。
搅拌摩擦焊由于其焊接原理的限制,存在一些缺陷,主要是:
①被焊接工件必须在垫板上牢固夹紧,以防止被焊穿及在焊接过程中工件松动;②搅拌针退出会在焊缝末段留下一个小孔,在大多数情况下,只能用其它焊接方法填充;③焊接工件没有足够的强度和刚度,或通过夹具不能提高焊缝区的刚度或强度的承载能力,则不适合采用搅拌摩擦焊[5]。
1.3搅拌摩擦焊焊缝组织
典型的搅拌摩擦焊接头宏观组织如图1-2所示(所焊材料为LY12)。
从图中可以看出,焊核位于焊缝中心,内部组织是清晰的洋葱状,由一系列的椭圆组成,焊核可以看得很清楚(但在有些合金中不一定很清楚或根本看不到)。
焊核延伸到焊缝表面,比搅拌针大,比轴肩小,焊核偶尔会延伸到焊件底部。
焊核的外貌取决于搅拌针的形状、焊接参数和被焊材料的强度。
图1-2FSW接头横截面“洋葱环”
通过对搅拌摩擦焊焊接接头的金相分析以及显微硬度分析可以发现,搅拌摩擦焊的焊缝组织可分为A、B、C、D四个区域,如图1-3所示:
A区为母材区(basicmetal,简称BM),无热影响也无热变形;B区为热影响区(heataffectedzone,简称HAZ),该区域的材料因受热循环的影响,热变形影响区(thermomechanicalllyaffectedzone,简TMAZ),该区域材料已经产生了剧烈的塑性变形。
就铝合金而言,再结晶区域和TMAZ之间通常有明显的界限,但在其它没有热致相变的材料中,如在纯钛、β钛合金、奥氏体不锈钢和铜中,似乎TMAZ整体已再结晶化,产生了无应变再结晶,这可能使HAZ/TMAZ的边界难以精确划分;D区为焊核(dynamicallyrecrystallizedzone,简称DXZ),焊核是最接近轴肩的区域,组织结构通常有较大的变化[11-13]。
图1-3搅拌摩擦焊焊缝区域示意图
在焊接接头的热影响区中,除了腐蚀反应比母材快一些外,其金相组织与母材没有多大区别。
对于时效强化或加工硬化的合金,从焊接区传导来的热量使热影响区过时效或位错密度下降,使焊后接头热影响区的硬度下降。
1.4搅拌摩擦焊金属流动性以及动态软化过程
金属材料的力学性能和物理性能都与材料中的位错密度有关,金属经历塑性变形时,位错密度发生变化,材料性能将相应发生变化,动态再结晶是材料在高温变形条件下,晶粒重新形核并长大,形成新的低位错密度晶粒的过程。
该过程宏观表现是材料的变形抗力减小。
焊接时被焊材料必须保持较高温度和较高的变形速率。
这两点对于保证材料发生充分的动态软化非常关键,这直接影响接头的性能[14]。
软化的金属通过两个过程进行流动:
(1)搅拌针前进侧前部的材料被刮擦掉后,随着搅拌针旋转和行进,经历了螺旋式运动形式,并在螺纹的冲击下下降,同时在螺纹的逆向冲击下上升。
经过一周或数周的旋转,这些材料脱落下来形成焊缝的迹线;
(2)来自于搅拌针后退侧材料的挤出过程,挤出的材料填充进前进侧材料脱落后所留下的空腔。
并且认为两个过程各自形成的材料性能差异较大,因而焊缝的性能与每个过程在整个过程。
当搅拌针插入待焊件,轴肩与待焊件相接触后,两者之间发生摩擦产生热量。
此时建立起温度场[15-17]。
如图1-4所示,由于金属分别处于不同位置,所以受到的热的影响和变形情况不同,从而在物理性质以及力学性能上都会发生不同的变化。
这时靠近搅拌针的A层发生了软化,而B层的物理性能变化却不大,而B层金属由于没有达到足够的温度,因此金属只能发生冷变形。
图1-4搅拌摩擦焊过程中金属动态软化示意图
1.5影响搅拌摩擦焊的因素
1)搅拌头的材料尺寸与形状
搅拌摩擦焊中所使用的搅拌头主要由两部分组成:
轴肩和搅拌针。
搅拌头是搅拌摩擦焊接过程中的关键,最优搅拌头是搅拌摩擦焊获得高质量接头的前提。
搅拌头主要由轴肩和搅拌针两部分构成,其几何形貌和尺寸不仅决定着焊接过程的热输入方式,还影响焊接过程中搅拌头附近塑性软化材料的流动形式,对于给定板厚的材料来说,焊接质量和效率主要取决于搅拌头的形貌和几何设计。
因而设计合理的搅拌头是提高焊接质量、获得高性能接头的前提和关键。
目前国内外所研究出的搅拌头形式主要有:
柱形搅拌针、锥形螺纹搅拌针和三槽锥形螺纹搅拌针、偏心圆搅拌针和偏心圆螺纹搅拌、非对称搅拌针、外开螺纹搅拌针、用于搭接的两级搅拌针、可伸缩式搅拌针等[13]。
从国外某些文献上采用的搅拌针的形状是标准英制螺纹,但很多文献上提到的是特殊结构的搅拌针,但出于保密的原因,迄今为止未见详细报道。
搅拌针的材料通常采用合金工具钢。
搅拌头轴肩的直径通常是搅拌针直径的3倍左右,轴肩直径过小,摩擦热不足以塑化材料,轴肩直径过大,可能使轴肩下面的被焊材料达到或超过熔点,不利于焊接强度的提高,并且会引起焊缝表面的不平整[9]。
试验结果表明,搅拌针的直径为焊件厚度的0.9~1.1倍时,焊缝质量较好。
搅拌针的直径过大时,焊接区断面面积增大,热影响区变宽,同时搅拌针向前移动时阻力增大;搅拌针的尺寸过小时,焊接区热塑性金属的流动性差;搅拌针向前移动时所产生的侧向挤压力减小,不利于形成致密的焊缝组织。
搅拌针的长度与焊缝的背面成形有关。
搅拌针过短,背面焊不透;搅拌针过长,则背面易过热,导致成形较差。
搅拌针长度的选取与其直径有关。
当搅拌针的直径较大时,其长度可以略短。
2)搅拌头旋转速度
搅拌头转速是影响摩擦搅拌焊热源的主要因素之一,由此可知,当搅拌头的旋转速度较低时,摩擦热不够,不足以形成热塑性流动层,其结果是不能实现固相连接,在焊缝中形成了孔洞。
随着转速的提高,摩擦热源增大,热塑性流动层由上而下逐渐增大,使得焊缝中的孔洞逐渐减小,当转速上升到一定值时,孔洞消失,形成致密的焊缝。
但转速过高时,会使搅拌针周围以及轴肩下面的材料温度达到或超过熔点,无法形成固相连接。
3)焊接速度
在搅拌摩擦焊过程中,焊接速度是影响焊缝成型的重要因素。
当焊接速度过小时,搅拌头所产生的热量使焊接温度过高,焊核区金属温度将接近金属熔点,会使金属因过热而出现疏松,同时焊缝表面将凹凸不平。
当焊接速度过大时,搅拌摩擦焊所产生的热量不足以使搅拌头周围的金属达到塑化状态,不能形成好的焊缝,在内部会出现孔洞。
同时,搅拌摩擦焊焊接速度与焊缝受力也有关。
搅拌头与被焊金属之间的作用力在搅拌头转速一定的情况下随着焊速的提高而增大。
4)焊缝受力
搅拌摩擦焊与普通电弧焊的焊缝受力有很多不同之处。
普通电弧焊焊缝受力主要来自电弧力,磁场力以及熔池自身的重力,而搅拌摩擦焊其焊缝受力主要是垂直与焊接方向的轴向力,焊接进给阻力及焊缝夹持部分与轴肩部分不同心度产生的偏心搅动力,如图1-5所示。
搅拌头与工件有倾角,焊缝所受到的轴向力并不垂直于焊缝表面,由于搅拌头倾角较小,本文忽略搅拌头倾角的因素,把焊缝所受轴向力看作是垂直与焊缝表面的。
可见搅拌摩擦焊焊件与焊机受力都比普通弧焊要高的多。
图1-5搅拌摩擦焊焊缝受力分析
搅拌头与被焊工件表面之间的接触状态对焊缝的成形也有较大的影响,目前在搅拌摩擦焊中轴向力是搅拌针及轴肩与工件接触而形成的。
当轴向压力不足时,表面热塑性金属“上浮”,溢出焊接表面,焊缝在冷却后会由于金属的“上浮”而形成孔洞。
当轴向压力过大时,轴肩与焊件表面摩擦力增大,摩擦热将使轴肩发生“粘头”现象,使焊缝表面出现飞边、毛刺等缺陷[7]。
对于焊缝进给力对焊接接头的影响,国内也有这方面的研究。
试验中所使用的是自行研制的搅拌摩擦焊机。
焊接过程中,搅拌头在水平方向上保持静止不动,由工作台相对搅拌头向焊接反方向运动来完成焊接过程。
通过在焊接过程中对驱动水平工作台运动的电机的工作电流和工作电压进行测量,来计算焊接时搅拌针与被焊金属之间的作用力。
根据
可以分别计算出电机在空载下和焊接过程中负载下的输入功率。
这部分能量要经过电机、减速器以及丝杠,最终传递到工作台。
在能量的传递过程中,各级传递机构都要损耗掉一部分能量。
由于这些损耗无法精确测量,因此先测得空载时电机的输入功率Pk,再测得电机负载时的功率Pf,那么电机对工作台的输出功率为:
根据
,可以求得图2中的力F:
式中:
为水平工作台的运动速度即焊接速度。
通过计算可以得到如下结论:
当搅拌头旋转速度相同时,电机的输入功率随着焊接速度的增大而增大,从而使力F随之增大;而当焊接速度不变时,电机的功率和F则随着旋转速度的增大而减小,这是当搅拌头旋转速度相同时,焊接速度越大,搅拌头在被焊板材同一位置停留的时间就越短,搅拌头与板材摩擦产生很少的热量,金属不能达到一个较好的软化状态。
在这种情况下,焊接过程中金属对搅拌针的阻力较大,从而导致工作台相对运动所需要的力也比较大。
反之,当焊接速度相同时,旋转速度越大,搅拌头在同一位置产生的热量就越多,金属可以达到一个较好的软化状态,工作台相对运动所需的力也就比较小。
在搅拌摩擦焊中,搅拌针与被焊板材之间的作用力通过产热和塑性金属流动两个方面影响着整个焊接过程。
搅拌针与被焊金属之间的作用力在焊速一定的情况下随着搅拌头转速的提高而减小,在搅拌头转速一定的情况下随着焊速的增大而增大[19-20]。
同样,对于搅拌摩擦焊焊缝所受的轴向力,国内也有相关的研究。
采用基于固体力学的有限元方法研究搅拌摩擦焊接过程中,不同过程参数情况下焊缝的受力情况。
研究发现,搅拌摩擦焊接过程中焊缝上应力的最大值发生在焊缝前进方向上焊缝与焊缝中心线接触点的附近,且vonMises应力的最大值随焊缝平移速度的增加而增加。
搅拌头前方焊缝的接触压力较大,后方接触压力较小,后退侧的接触力较前进侧大。
搅拌头的不停旋转决定搅拌头受到交变载荷作用,导致疲劳成为搅拌头破坏的原因之一。
焊缝中心线附近的等效塑性应变和结构纹理呈现洋葱状结构。
随着搅拌摩擦焊接技术的日益发展,越来越多的研究机构与企业投身于研究搅拌摩擦焊焊机的设计与制造方面。
由于设计焊机经常会涉及到机器受力的问题,如果不知道焊接时焊机的具体受力情况,很难进行选材与设计,焊机强度和刚度设计指标低会影响机床使用寿命,甚至不能用于生产,反之,浪费材料,能源,经济效益差。
因此,测量焊缝受力的情况也是设计搅拌摩擦焊机的一个很重要的环节。
同样,搅拌摩擦焊焊缝受力是影响焊缝成型的一个重要因素,对焊缝受力进行精确测量,并研究其与焊缝成型的关系,是提高搅拌摩擦焊焊接质量的一个重要手段。
国内外对搅拌摩擦焊焊缝受力的研究,目前大多数都是通过数值模拟的方法,很少在实际过程中采集数据,本课题是设计测力装置直接采集搅拌摩擦焊接过程中的实际数据,比较切合实际生产状况,对提高焊缝质量有很大的实际意义。
2测量轴向力装置的设计及工艺试验
2.1测力装置的设计
2.1.1测量仪器的选择
选用的测量仪器必须满足以下要求。
首先,为了模拟实际的焊接状况,测量仪器必须在焊缝的任何一个位置都能测量出其受力情况,数据在焊缝任何位置都必须准确。
其次,仪器能时时测量并有数据输出,并能直观的反映出来。
根据以上要求选用2台NS-TH12称重传感器如图2-1所示,使用钢板将他们搭成焊接平台,可以在上面进行实际的搅拌摩擦焊工艺实验。
NS-TH12称重传感器测量精度为0.5%,并且有数据输出,可以通过电脑时时观察焊缝受力的曲线图,还能生成图表,满足实验要求。
表2-1所示为NS-TH12称重传感器的各项指标。
图2-1NS-TH12称重传感器
表2-1NS-TH12称重传感器主要技术指标
技术参数
单位
技术指标
额定载荷
t
1、5、10、15、20、30
额定输出
mV/V
>1.5
综合精度
%F.S
0.03,0.05
非线性
%F.S
≤±0.03
滞后
%F.S
≤±0.03
重复性
%F.S
≤±0.03
零点输出
%F.S
<±1
零点温度系数
%F.S/℃
≤0.005
工作温度范围
℃
-20~65
绝缘电阻
MΩ
≥5000
供桥电压
VDC
10
允许过载
%F.S
150
备注
可设计成12V或24V供电,0~5V或4~20mA信号输出
2台NS-TH12称重传感器,其中每台的测量范围是5T,整个测量装置的测量范围是10T,约为100KN。
2.1.2测力装置的装配与使用
采用2台NS-TH12称重传感器作为测量设备,并把其设计装配成可用于焊接实验的测力系统。
装配结果如图2-2所示。
根据使用说明书将传感器与其附带的电子仪表和PC机连接,设定好量程,小数点以及输出频率等参数,确保传感器工作正常。
图2-2测力装置图
2.1.3测力装置的标定
使用WDW-50型微机控制电子万能实验机进行标定,实验机最大载荷为50KN,级别为1。
并对垫板焊缝处不同位置的5个点进行测量标定,电子万能实验机施加的标准压力值与测力装置显示值如表2-2所示。
表2-2电子万能实验机施加的标准压力值与测力装置显示值
标准压力值
点1
点2
点3
点4
点5
5(KN)
5.02(KN)
5.05(KN)
5.02(KN)
5.03(KN)
5.04(KN)
10(KN)
10.05(KN)
10.05(KN)
10.04(KN)
10.08(KN)
10.09(KN)
15(KN)
15.08(KN)
15.08(KN)
15.05(KN)
15.11(KN)
15.14(KN)
20(KN)
20.12(KN)
20.12(KN)
20.08(KN)
20.15(KN)
20.17(KN)
25(KN)
25.15(KN)
25.15(KN)
25.18(KN)
25.21(KN)
25.22(KN)
每个点的误差=(平均偏差/满量程)×100%
点与点之间的最大相对误差=(最大偏差/满量程)×100%=0.13%,传感器的偏载能力可以达到实验要求。
假设每个点的平均误差从点1到点5分别表示为W1、W2、W3、W4、W5,则总平均误差W总=(W1+W2+W3+W4+W5)/5=(0.28%+0.3%+0.25%+0.39%+0.44%)/5=0.332%。
2.2实验内容
本课题是研究搅拌摩擦焊焊缝受力与焊缝成型的关系,通过以下的实验方法来观察焊缝受力及焊缝成型的情况:
1)使用相同板厚的材料,改变焊缝轴肩直径,其他焊接参数不变,观察焊缝轴肩直径对焊缝受力的影响,分别选用3种不同板厚的材料及采用相应的焊缝做3组同样的实验,观察焊缝成型状况。
2)选定5mm板厚的铝合金板,用同一搅拌头改变不同的压入量,其他参数不变,进行实验,观察压入量对焊缝受力以及焊缝成型的影响。
具体实验参数如表2-3所示。
表2-3试验参数
试样标号
实验代号
板厚
(mm)
搅拌针直径(mm)
搅拌针长度(mm)
轴肩直径(mm)
焊缝转速(n/min)
焊接速度
(mm/min)
压入量
(mm)
8-1
8-1
8
M8
7.5
20
750
60
0.1
8-2
8-2
8
M8
7.5
24
750
60
0.1
8-3
8-3
8
M8
7.5
26
750
60
0.1
5-1
5-1
5
M5
4.8
18.7
950
60
0.1
5-2
5-2
5
M5
4.8
15.3
950
60
0.1
5-3
5-3
5
M5
4.8
16
950
60
0.1
3-1
3-1
3
M5
2.9
13
950
60
0.1
3-2
3-2
3
M5
2.9
18
950
60
0.1
3-3
3-3
3
M5
2.9
12
950
60
0.1
5-A
5-A
5
M5
4.8
18.7
950
60
0.1
5-B
5-B
5
M5
4.8
18.7
950
60
0.2
5-C
5-C
5
M5
4.8
18.7
950
60
0.3
5-D
5-D
5
M5
4.8
18.7
950
60
0.4
实验材料选用LY12铝合金。
LY12是一种可通过固溶热处理后再进行时效处理强化的硬铝合金。
它的固溶热处理温度范围很窄,处理温度在490~503℃之间,若低于此温度范围,合金元素溶入量少,则降低了时效强化的效果;若超过此温度范围,则容易产生过烧现象[18]。
其化学成分如表2-4所示,力学性能如表2-5所示,用自制的高温合金焊缝和焊接夹具,在用X53K型立式铣床改装的搅拌摩擦焊机上进行焊接,焊缝倾角统一使用2°。
表2-4LY12铝合金的化学成分
Cu
Mg
Mn
Fe
Si
Zn
Ni
Ti
Fe+Si
其它
Al
3.8-4.9
1.2-1.8
0.3-0.9
0.5
0.5
0.3
0.1
0.15
0.5
≤0.15
余量
表2-5LY12铝合金力学性能
σb/MPa
δ/%
HBS
470
17
105
施焊前,将测量仪表连接好并调节好参数,确保仪表与PC机连接正常并能记录数据。
用锉刀去除工件飞边和毛刺,用砂纸打磨平对接试样表面,用丙酮清洗待焊试件的连接处。
把待焊的铝合金板材固定好,先调整焊缝的中心轴线与对接线在同一直线上,保证焊缝的行进方向与两片铝合金板的缝隙平行,焊缝恰好压在缝隙上边,否则会影响到焊缝的焊接质量。
开机待焊缝旋转稳定后,PC机开始记录压力数据,焊缝缓慢插入焊缝,达到预定压入量,开始焊接进给,到达停止焊接位置时,停止进给并保持焊缝在焊缝中停留10-60秒,然后缓慢退出焊缝,停止记录数据并关机。
实验结束后对焊缝外表面成型进行拍照记录,截取部分焊缝作为宏观金相样本,经打磨抛光后在16倍显微镜下观察宏观组织,并拍照记录。
2.3实验结果与分析
2.3.1不同板厚,使用不同轴肩直径搅拌头所焊焊缝的实验结果
图2-3是实验代号8-1,8-2,8-3所焊出的焊缝表面成型情况。
(a)轴肩直径20mm(b)轴肩直径24mm(c)轴肩直径26mm
图2-3实验板厚8mm,不同轴肩直径所焊焊缝的表面成型
图2-4是实验代号8-1,8-2,8-3所焊出的焊缝轴向受力曲线图。
(a)轴肩直径20mm
(b)轴肩直径24mm
(c)轴肩直径26mm
图2-48mm板厚,改变轴肩直径焊出的焊缝轴向受力图
图2-5是实验代号5-1,5-2,所焊出的焊缝表面成型情况。
(a)轴肩直径18.7mm(b)轴肩直径15.3mm
图2-55mm板厚,不同轴肩直径所焊焊缝的表面成型
图2-6是实验代号5-1,5-2,所焊出的焊缝受力曲线图。
(a)轴肩直径