汽车玻璃升降器复合拉深模的设计.docx
《汽车玻璃升降器复合拉深模的设计.docx》由会员分享,可在线阅读,更多相关《汽车玻璃升降器复合拉深模的设计.docx(35页珍藏版)》请在冰豆网上搜索。
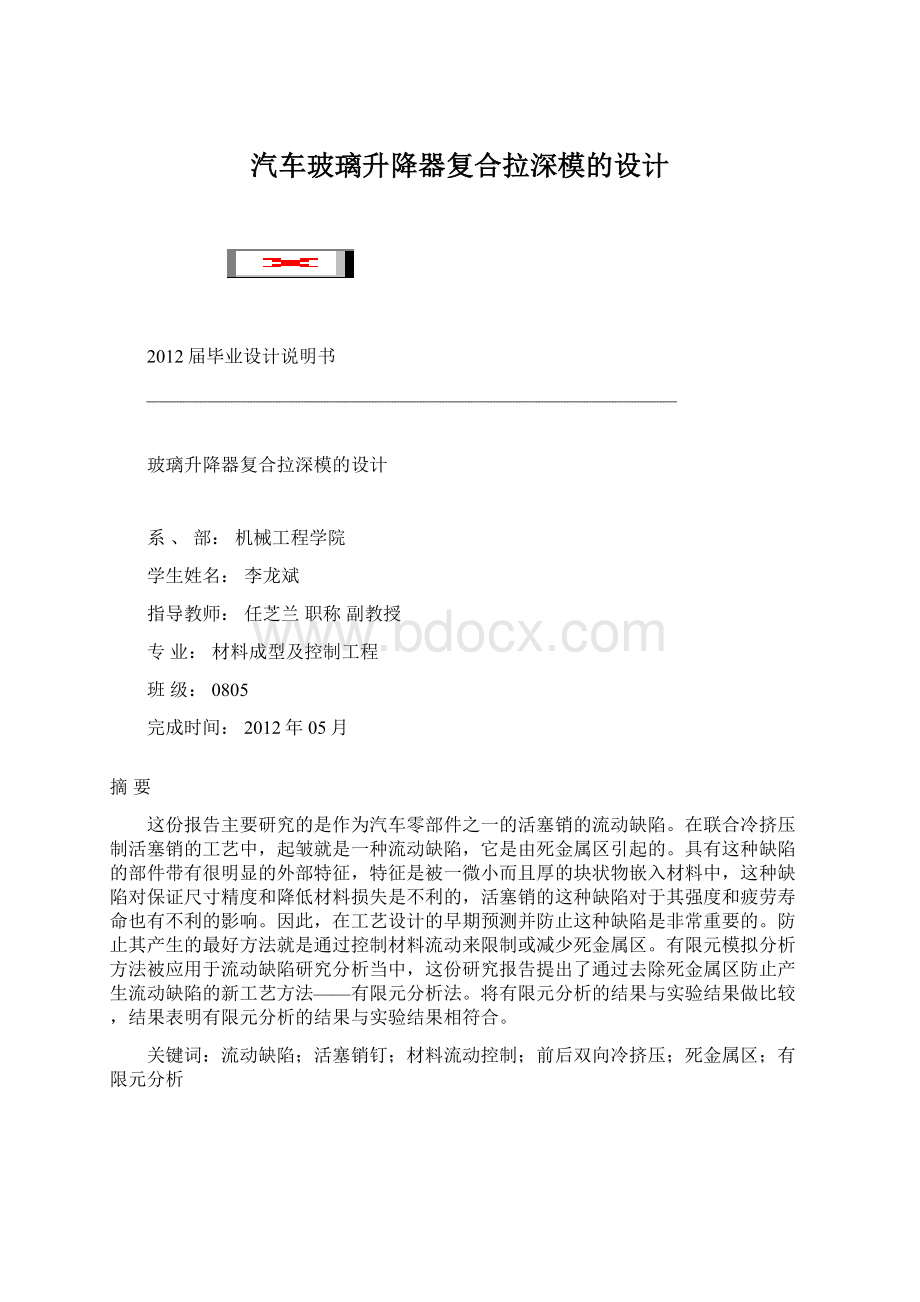
汽车玻璃升降器复合拉深模的设计
2012届毕业设计说明书
玻璃升降器复合拉深模的设计
系、部:
机械工程学院
学生姓名:
李龙斌
指导教师:
任芝兰职称副教授
专业:
材料成型及控制工程
班级:
0805
完成时间:
2012年05月
摘要
这份报告主要研究的是作为汽车零部件之一的活塞销的流动缺陷。
在联合冷挤压制活塞销的工艺中,起皱就是一种流动缺陷,它是由死金属区引起的。
具有这种缺陷的部件带有很明显的外部特征,特征是被一微小而且厚的块状物嵌入材料中,这种缺陷对保证尺寸精度和降低材料损失是不利的,活塞销的这种缺陷对于其强度和疲劳寿命也有不利的影响。
因此,在工艺设计的早期预测并防止这种缺陷是非常重要的。
防止其产生的最好方法就是通过控制材料流动来限制或减少死金属区。
有限元模拟分析方法被应用于流动缺陷研究分析当中,这份研究报告提出了通过去除死金属区防止产生流动缺陷的新工艺方法——有限元分析法。
将有限元分析的结果与实验结果做比较,结果表明有限元分析的结果与实验结果相符合。
关键词:
流动缺陷;活塞销钉;材料流动控制;前后双向冷挤压;死金属区;有限元分析
ABSTRACT
Aflowdefectofapiston-pinforautomobilepartsareinvestigatedinthisstudy.Inthecombinedcoldextrusionofapiston-pin,alappingdefect,whichisakindofflowdefect,appearsbythedeadmetalzone.Thisdefectisevidentinproductswithasmallthicknesstobepiercedandisdetrimentaltodimensionalaccuracyanddecreaseofmaterialloss.Theflowdefectthatoccursinthepiston-pinhasbadeffectsonthestrengthandthefatiguelifeofthepiston-pin.Therefore,itisimportanttopredictandpreventthedefectintheearlystageofprocessdesign.Thebestmethodthatcanpreventtheflowdefectisremovingorreducingdeadmetalzonethroughthecontrolofmaterialflow.Finiteelementsimulationsareappliedtoanalyzetheflowdefect.Thisstudyproposesnewprocesseswhichcanpreventtheflowdefectbyremovingthedeadmetalzone.Thentheresultsarecomparedwiththeresultsofexperimentsforverification.TheseFEsimulationresults
areingoodagreementwiththeexperimentalresults.
©2003ElsevierScienceB.V.Allrightsreserved.
Keywords:
Flowdefect;Piston-pin;Materialflowcontrol;Forward–backwardextrusion;Deadmetalzone;FEsimulation
1前言
1.1玻璃升降器的功用及拉深模的设计要求
现在许多轿车门窗玻璃的升降(关闭和开启)已经抛弃了摇把式的手动升降方式,一般都改用按钮式的电动升降方式,即使用电动玻璃升降器来控制,也就是常说的“电动门窗”。
轿车用的电动玻璃升降器多是由电动机、减速器、导绳、导向板、玻璃安装托架等组成。
因导绳的材料或制作工艺方式不同,又分为绳轮式、软轴式和塑料带式三种电动玻璃升降器。
前二种是用钢丝绳做为导绳,后一种是用塑料带做为导绳。
以普遍使用的绳轮式电动玻璃升降器为例,它是由电动机、减速器、钢丝绳、导向板和玻璃安装托架等零部件组成,安装时门窗玻璃固定在玻璃安装托架上,玻璃导向槽与钢丝绳导向板平行。
开启电动机,由电动机带动减速器输出动力,拉动钢丝绳移动玻璃安装托架,迫使门窗玻璃作上升或下降的直线运动。
而塑料带式电动玻璃升降器的导绳采用塑料带,带上有孔,用来移动和定位塑料带,控制门窗玻璃的升降。
电动玻璃升降器结构的关键是电动机和减速器,这两者是组装成一体的,其中电动机采用可逆性永磁直流电动机,电动机内有两组绕向不同的磁场线圈,通过开关的控制可做正转和反转,也就是说可以控制门窗玻璃的上升或下降。
电动机是由双联开关按钮控制,设有升、降、关等三个工作状态,不操纵时开关自动停在“关”的位置上。
操纵电路设有总开关(中央控制)和分开关,两者线路并联。
总开关由驾车者,控制全部门窗玻璃的开闭,而各车门内把手上的分开关由乘员分别控制各个门窗玻璃的开闭,操作十分便利。
电动机的质量直接关系到电动玻璃升降器的正常工作,它一定要具有体积小、重量轻、防护等级高、噪声低、电磁干扰小、运行可靠等特点。
现代轿车已广泛应用微电子技术,电机工作会发射电磁波干扰其它电器件的工作;前几年通用汽车公司一篇售后分析报告显示,近40%的电动玻璃升降器故障是由电动机密封性差引起的。
因此,减少电磁干扰和解决电机密封性问题巳成为近年汽车电机技术的热门话题。
90年代中期以来,电动玻璃升降器的控制机构技术发展很快,电子模块控制形式大量应用于批量装车,并设有安全保护装置。
例如博世公司生产的电动玻璃升降器系统,在电动机中埋植磁环,感应电机转速,在电子模块中埋植霍尔元件,感应电流,并通过电子模块控制对电动机的过流、过压及过热保护,而且当玻璃上升途中遇到人力障碍时会自动识别而反向运行,防止乘员夹伤。
2冲裁工艺设计
2.1冲裁工艺计算
2.1.1工艺力和功的计算
冲裁力是指冲裁过程中的最大抗力,它是合理地选用冲压设备吨位和校检模具强度的重要依据。
影响冲裁力的因素很多,主要有材料的机械性能、厚度、冲裁件周边长度、模具间隙以及刃口锋利程度等。
(1)冲裁力的计算
采用平刃凸模和凹模冲裁时,其冲裁力的计算公式
·····································2.1
式中
——冲裁力;
——冲裁件的周长(mm);
——材料厚度(mm);
——材料的抗剪强度。
如图
(一)所示,工件尺寸为,k=260,L=284,Ra=105,Rb=144,则
查附表1-1,取
,工件厚度
,故
····················2.2
考虑到模具刃口的钝化,凹模和凸模间隙不均匀,材料性能的波动和材料厚度的偏差等因素,实际所需冲裁力还应增加30%,即
则
(2)卸料力和推件力的计算
当冲裁工作完成以后,冲下的工件(或废料)沿径向发生弹性收缩,同时,工件废料还要力图恢复弹性穹弯。
这两种弹性恢复的结果导致工件(或废料)硬塞在凹模内,废料(或工件)箍紧在凸模上。
从凸模上将工件(或废料)卸下来的力叫卸料力。
从凹模内顺着冲裁方向将工件(或废料)推出的力叫推料力。
很显然,这些力在选择压力机的吨位和设计模具时必须加以考虑。
影响这些力的因素很多,主要有:
材料的力学性能和厚度、工件形状和尺寸、模具间隙、排样的搭边大小及润滑情况等。
由于这些因素的影响规律很复杂,难以准确计算。
生产中常采用下列公式
······································2.3
······································2.4
式中
——分别是卸料力、推件力(N)
——分别是卸料力系数、推件力系数
——冲裁力(N)
——同时梗塞在凹模内的工件数
参见表2-13,
取0.027,
取0.05,
取为8mm,
,则
(3)冲裁功的计算
选择冲裁设备时,除了要计算冲裁力,使压力机的公称压力大于冲裁力以外,还要进行冲裁功的验算,使压力机的每次行程功不超过额定的数值,以保证其电极不过载,飞轮转速不致下降太多。
平端刃口的冲裁功按下式计算
··································2.5
式中
——冲裁功(n.m)
——材料厚度(mm)
——冲裁力(N)
——系数,一般取为0.63
则
2.1.2压力机的选择
冲压设备选择是冲压工艺过程设计的一项重要内容,它直接关系到设备的安全和使用的合理,同时也关系到冲压工艺过程的顺利完成及产品质量、零件精度、生产效率、模具寿命、材料的性能与规格、成本的高低等一系列重要的问题。
(1)设备类型的选择
设备类型的选择要依据冲压件的生产批量、零件尺寸的大小、工艺方法与性质及冲压件的尺寸、形状等要求来进行,除此之外,还应考虑到设备的精度与刚度以及生产现场的实际可能。
压力机的刚度是由床身刚度、传动刚度和导向刚度三部分组成。
如果刚度较差,负载终了和卸载时模具间隙会发生很大的变化,影响冲压件的精度和模具寿命。
综合考虑以上各因素后参照表7-3[2]和表7-4[2],并结合工厂现有设备情况,此冲模选用开式双柱可倾压力机。
(2)设备规格的选择
在选定设备类型后,进一步根据冲压件的大小、模具尺寸及变形力来确定设备规格。
冲裁时,压力机必须大于或等于冲裁各工艺力的总和,本工件冲裁模采用弹压卸料装置和下出件的模具,故
为了提高设备的工作刚度、冲压零件的精度及延长设备的寿命,要求设备容量留有40~30%的余,并结合工厂现有设备情况选用吨位为100t的压力机,型号为
J23-100开式双柱可倾压力机。
2.2模具总体设计
总体设计的任务包括:
(1)模具类型的确定;
(2)操作方式、进料方式的确定;
(3)定位、联接等型式的确定;
(4)模具压力中心的确定;
(5)模具闭合高度的初定。
2.2.1模具类型的确定
根据冲压件的形状、尺寸、精度要求等确定模具类型。
根据4.1节的计算,落料件的形状(如图所示),是有四段圆弧组成的椭圆形件,形状比较简单,呈中心轴对称,尺寸精度要求也不高为IT13级,因此可以考虑选用简单模。
2.2.2操作方式的确定
虽然该冲压件是进行大批量生产的,但考虑到工厂的现有生产条件,为了降低产品的生产成本,而且落料件的尺寸精度要求不高,所以采用手工操作方式或半自动操作方式。
2.2.3定位、联接型式的确定
为了保证模具正常安全工作,模具中的定位和联接件一定要可靠。
(1)模板
在上下模板上安装全部模具零件,构成模具的总体和传递压力。
模板不仅应该具有足够的强度,而且还要有足够的刚度。
本模具将上模板与凸模、凸模固定板及垫板等装配成一体,用四个螺钉紧固构成模具的上部分;下模板则与凹模等组成模具的下模不分。
此外上下模两部分还分别各对称低用两个圆柱销销紧,以防转动和错位。
上下模架均采用标准模架,是用HT200铸造而成。
(2)模柄
模具的上部分通过模柄固定在冲床滑块上。
模柄的结构形式很多,常见的结构形式有带凸缘模柄、压入式模柄、旋入式模柄、浮动式模柄等等。
本模具选用压入式模柄,通过压配合和附加的销钉与模板固定联接以防转动与松动。
模柄材料选用优质碳素钢中的45号钢。
(3)凸模固定板与垫板
用凸模固定板将凸模联接固定在模板的正确位置上。
凸模固定板有圆形和矩形两种,考虑到模具的总体结构这里选用凸模固定板。
固定板与凸模采用过渡配合,压装后将凸模尾部与固定板一起磨平。
凸模固定板用45号钢加工。
(4)坯料的定位和定向
见2.3节。
2.2.4模具压力中心的确定
根据图
(1)所示的落料件可知,落料件形状呈轴对称,其压力中心即为工件的几何中心,因此不需要进行模具压力中心的计算。
批量大时,冲压工序应尽可能组合在一起,用复合模具;小批量生产用单工序简单模。
由于离合器冲压成形需要的多道工序完成,因此选择合理的成形工艺方案十分重要,考虑到生产批量大,应在生产合格零件的基础上尽量提高生产效率,降低生产成本。
要提高生产成本,应该尽量选择合理的工艺方案,选择复合能复合的工序,但复合程度太高,模具的结构复杂,安装调试困难,模具成本高,同时可能降低模具的强度,缩短模具寿命。
根据零件形状确定冲压工序类型和选择工序顺序,冲压该零件需要的基本工序有冲孔、成型、修边。
工序的组合方案及比较
方案一:
1)落料;
2)拉深;
3)成型。
方案二:
1)落料与拉深复合;
2)成型。
方案三:
1)落料;
2)拉深与成型复合。
方案四:
1)落料、拉深与成型复合。
方案一:
复合程度较低,模具结构简单,安装、调试容易,但生产道次多,效率低,不适合大批量生产。
故很少使用。
方案二:
将落料与拉深进行复合,工序少,生产效率较高,但模具结构较复杂,安装、调试难于控制,同时模具强度较低。
方案三:
将拉深与成型复合
方案四:
复合程度最高,模具结构复杂,安装调试困难,模具成本提高,同时可能降低模具的强度,缩短模具的寿命。
根据以上四个冲压工艺方案的比较,四种冲压工艺方案各有其优点和缺点,为了提高生产率,保证模具结构简单,冲压件尺寸稳定、精度高,故在此设计中选择方案四进行冲制。
3.1.4落料尺寸的计算
由于板料在扎压或退火时所产生的聚合组织而使材料引起残存的方向性,反映到拉深过程中,就使桶形拉深件的口部形成明显的突耳。
此外,如果板料本身的金属结构组织不均匀、模具间隙不均匀、润滑的不均匀等等,也都会引起冲件口高低不齐的现象,因此就必需在拉深厚的零件口部和外缘进行修边处理。
这样在计算毛坯尺寸的时候就必需加上修边余量然后再进行毛坯的展开尺寸计算。
根据零件的尺寸取修边余量的值为4.6mm。
查表5—7,《冲压工艺与模具设计实用技术》
在拉深时,虽然拉深件的各部分厚度要求发生一些变化,但如果采用适当的工艺措施,则其厚度的变化量还是并不太大。
在设计工艺过程时,可以不考虑毛坯厚
度的变化。
毛坯尺寸按公式
…………………………………………………3.1
所以
mm
3.2确定排样方案
3.2.1确定排样、裁板方案
冲裁件在板料、条料或带料上的布置方法称为排样。
排样是否合理,直接影响到材料的利用率、零件质量、生产率、模具结构与寿命及生产操作方式与安全。
因此,在冲压工艺和模具设计中,排样是一项极为重要的、技术性很强的工作。
加工此零件为大批大量生产,冲压件的材料费用约占总成本的60%~80%之多。
因此,材料利用率每提高1%,则可以使冲件的成本降低0.4%~0.5%。
在冲压工作中,节约金属和减少废料具有非常重要的意义,特别是在大批量的生产中,较好的确定冲件的形状尺寸和合理的排样的降低成本的有效措施之一。
由于材料的经济利用直接决定于冲压件的制造方法和排样方式,所以在冲压生产中,可以按工件在板料上排样的合理程度即冲制某一工件的有用面积与所用板料的总面积的百分比来作为衡量排样合理性的指标。
同时属于工艺废料的搭边对冲压工艺也有很大的作用。
通常,搭边的作用是为了补充送料是的定位误差,防止由于条料的宽度误差、送料时的步距误差以及送料歪斜误差等原因而冲出残缺的废品,从而确保冲件的切口表面质量,冲制出合格的工件。
同时,搭边还使条料保持有一定的刚度,保证条料的顺利行进,提高了生产率。
这里毛坯直径ø65不算太小,考虑到操作方便,采用单排。
搭边值得大小要合理选取。
根据此零件的尺寸查表19.1—18,《冲压模具设计》取
a=2,a1=1.5
进距s=D+a1
=65+1.5
=66.5mm
条料宽度b=D+2a
=65+2×2
=69mm
板料规格拟选用:
1.5×900×1800
采用纵裁:
裁板条数n1=B/b=900/69=13条余3mm
每条个数n2=(L-a1)/s
=(1800-1.5)/66.5
=27个余3mm
每板总个数n总=n1×n2
=1327
=351个
板的材料利用率η总={[n总
(D2-d2)]/L×B}×100%
=[351×
(652-112)]/900×1800×100%
=69.5%
采用横裁:
条数n1=L/b=1800/69=26条余6mm
每条个数n2=(B-a1)/s
=(900-1.5)/66.5
=13个余34mm
每板总个数n总=n1×n2
=26×13
=338个
板的材料利用率η总=[338×
(652-112)]/900×1800×100%
=66.5%
由此可见,采用纵裁有较高的材料利用率和有较高的剪裁生产率。
计算零件的净重G及材料消耗定额G0
G=A×t×Υ
=
[652-112-3×3.22-(542-502)]×10-2×1.5×10-1×7.85
≈33g
式中Υ为密度,低碳钢取Υ=7.85g/cm3。
[]内第一项为毛坯面积,第二项为底孔废料面积,第三英为三个小孔面积,内为切边废料面积。
G0=(L×B×t×Υ)/351
=(900×10-1×1.5×1800×10-1×10-1×7.85)/351
=54g=0.054Kg
其排样如图3.1所示:
图3.1排样图
3.3计算拉深次数
在考虑拉深的变形程度时,必需保证使毛坯在变形过程中的应力既不超过材料的变形极限,同时还能充分利用材料的塑性。
也就是说,对于每道拉深工序,应在毛坯侧壁强度允许的条件下,采用最大的变形程度,即极限变形程度。
极限拉深系数值可以用理论计算的方法确定。
即使得在传力区的最大拉应力与在危险断面上的抗拉强度相等,便可求出最小拉深系数的理论值,此值即为极限拉
深系数。
但在实际生产过程中,极限拉深系数值一般是在一定的拉深条件下用实验的方法得出的,我们可以通过查表来取值。
该工件拉深一个过程,因此可以计算其拉深系数来确定拉深次数。
其实际拉深系数为:
……………………………………………3.2
材料的相对厚度为
…………………………………3.3
凸缘的相对直径为
…………………………………………3.4
凸缘的相对高度为
…………………………………………3.5
由表5—21,《冲压工艺与模具设计实用手册》可以查出,
表5—22,《冲压工艺与模具设计实用手册》可以查出
8
因为凸缘的相对高度0.2568小于最大相对高度0.58,且实际拉深系数0.58大于最小极限拉深系数0.48,所以拉深过程可以一次拉深成功。
3.4拉深冲压力的计算
由于该零件为轴对称件,故不必进行压力中心的计算。
3.4.1落料过程
(1)落料力
平刃凸模落料力的计算公式为
……………………………………………………………3.6
依据(P175,《冲压工艺与模具设计实用手册》)
式中P—冲裁力(N)
L—冲件的周边长度(mm)
t—板料厚度(mm)
—材料的抗冲剪强度(MPa)
K—修正系数。
它与冲裁间隙、冲件形状、冲裁速度、板料厚度、润滑情况等多种因素有关。
其影响范围的最小值和最大值在(1.0~1.3)P的范围内,一般
k取为1.25~1.3。
在实际应用中,抗冲剪强度
的值一般取材料抗拉强度
的0.7~0.85。
为便于估算,通常取抗冲剪强度等于该材料抗拉强度
的80%。
即
因此,该冲件的落料力的计算公式为
………………………………………………3.7
(2)卸料力
一般情况下,冲裁件从板料切下以后受弹性变形及收缩影响。
会使落料件梗塞在凹模内,而冲裁后剩下的板料则箍紧在凸模上。
从凸模上将冲件或废料卸下
来所需的力称卸料力。
影响这个力的因素较多,主要有材料力学性能、模具间隙、材料厚度、零件形状尺寸以及润滑情况等。
所以要精确地计算这些力是困难的,一
般用下列经验公式计算:
卸料力
…………………………………………………3.8
式中F——冲裁力(N)
——顶件力及卸料力系数,
其值可查(表19.1—12,《冲压模具设计》)取
为0.04。
因此
3.4.2、拉深过程
(1)拉深力
带凸缘圆筒形零件的拉深力近似计算公式为
………………………………………………3.9
式中
—圆筒形零件的凸模直径(mm)
—系数,查(表5—3,《冲压工艺与模具设计实用手册》)取0.8
—材料的抗拉强度(MPa)
因此
(2)压边力
压边力的大小对拉深件的质量是有一定影响的,如果过大,就要增加拉深力,因而会使制件拉裂,而压边圈的压力过小就会使工件的边壁或凸缘起皱,所以压边圈的压力必须适当。
合适的压边力范围一般应以冲件既不起皱、又使得冲件的侧壁和口部不致产生显著的变薄为原则。
压边力的大小和很多因素有关,所以在实际生产中,可以根据近似的经验公式进行计算。
…………………………………………3.10
依据(P328,《冲压工艺与模具设计实用手册》)
式中D—毛坯直径(mm)
d—冲件的外径(mm)
q—单位压边力(MPa)(表5—20,《冲压工艺与模具设计实用手册》
q的值取2.5。
所以
(3)顶件力
顶件力的计算公式可按下式:
=
……………………………………………3.11
式中
——顶件力(N);
——顶件力系数;查表2-8
=0.06
=
=0.06x132257
=793524
(4)拉深功的计算
拉深所需的功可按下式计算
………………………………………………3.12
依据(P45,《冲压工艺模具学》)
式中
——最大拉深力(N)
h——拉深深度(mm)
W——拉深功(N·m)
C——修正系数,一般取为C=0.6~0.8。
所以
3.4.3成型过程
采用平头凸模对塑性较好的低碳钢板、软铝板进行胀形所能达到的深度h见表2-1《冲压工艺与模具》。
采用刚性凸模对平板毛胚进行胀形时所需的胀形力F按下式估算
胀形力
…………………………………………………3.13
=
式中L--胀形区周边长度
t--板料厚度
K–考虑变形程度大小的系数,一般取K=0.7~1
--板料抗拉强度
拉深力出现在落料力之后,因此最大冲压力出现在冲裁阶段,选用落料拉深成型复合模结构,最大冲压力为:
Fmax=F+F1+F2………………………………………3.14
=299929+11997+79354
=391280N
3.5冲压设备的选择
为安全起见,防止设备的超载,对于冲裁工序,压力机的公称压力P应大于或等于冲裁时总冲压力的1.1~1.3倍。
即:
P≥(1.1~1.3)Fmax…………