博士课题论证报告新版.docx
《博士课题论证报告新版.docx》由会员分享,可在线阅读,更多相关《博士课题论证报告新版.docx(15页珍藏版)》请在冰豆网上搜索。
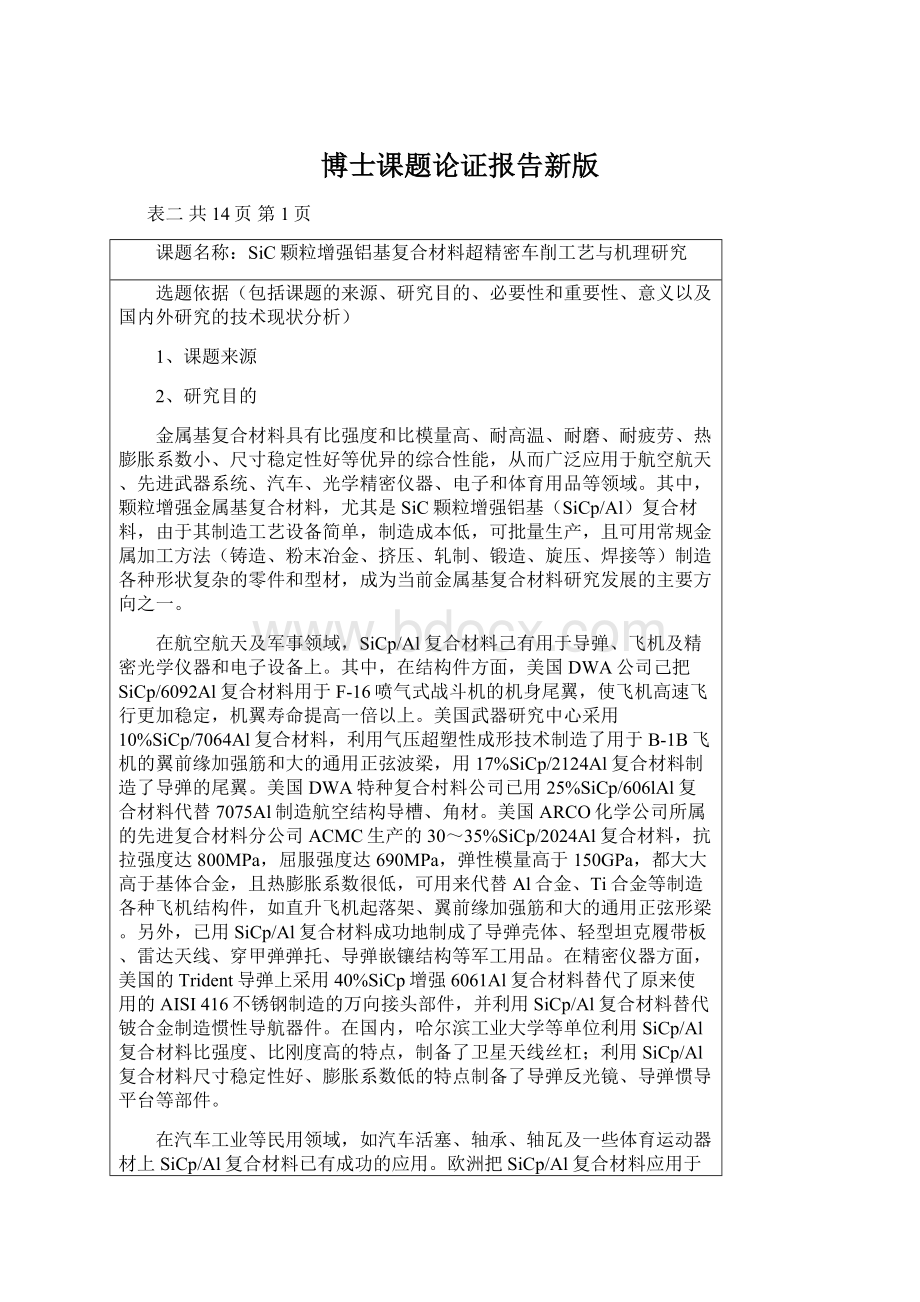
博士课题论证报告新版
表二共14页第1页
课题名称:
SiC颗粒增强铝基复合材料超精密车削工艺与机理研究
选题依据(包括课题的来源、研究目的、必要性和重要性、意义以及国内外研究的技术现状分析)
1、课题来源
2、研究目的
金属基复合材料具有比强度和比模量高、耐高温、耐磨、耐疲劳、热膨胀系数小、尺寸稳定性好等优异的综合性能,从而广泛应用于航空航天、先进武器系统、汽车、光学精密仪器、电子和体育用品等领域。
其中,颗粒增强金属基复合材料,尤其是SiC颗粒增强铝基(SiCp/Al)复合材料,由于其制造工艺设备简单,制造成本低,可批量生产,且可用常规金属加工方法(铸造、粉末冶金、挤压、轧制、锻造、旋压、焊接等)制造各种形状复杂的零件和型材,成为当前金属基复合材料研究发展的主要方向之一。
在航空航天及军事领域,SiCp/Al复合材料己有用于导弹、飞机及精密光学仪器和电子设备上。
其中,在结构件方面,美国DWA公司己把SiCp/6092Al复合材料用于F-16喷气式战斗机的机身尾翼,使飞机高速飞行更加稳定,机翼寿命提高一倍以上。
美国武器研究中心采用10%SiCp/7064Al复合材料,利用气压超塑性成形技术制造了用于B-1B飞机的翼前缘加强筋和大的通用正弦波梁,用17%SiCp/2124Al复合材料制造了导弹的尾翼。
美国DWA特种复合村料公司已用25%SiCp/606lAl复合材料代替7075Al制造航空结构导槽、角材。
美国ARCO化学公司所属的先进复合材料分公司ACMC生产的30~35%SiCp/2024Al复合材料,抗拉强度达800MPa,屈服强度达690MPa,弹性模量高于150GPa,都大大高于基体合金,且热膨胀系数很低,可用来代替Al合金、Ti合金等制造各种飞机结构件,如直升飞机起落架、翼前缘加强筋和大的通用正弦形梁。
另外,已用SiCp/Al复合材料成功地制成了导弹壳体、轻型坦克履带板、雷达天线、穿甲弹弹托、导弹嵌镶结构等军工用品。
在精密仪器方面,美国的Trident导弹上采用40%SiCp增强6061Al复合材料替代了原来使用的AISI416不锈钢制造的万向接头部件,并利用SiCp/Al复合材料替代铍合金制造惯性导航器件。
在国内,哈尔滨工业大学等单位利用SiCp/Al复合材料比强度、比刚度高的特点,制备了卫星天线丝杠;利用SiCp/Al复合材料尺寸稳定性好、膨胀系数低的特点制备了导弹反光镜、导弹惯导平台等部件。
在汽车工业等民用领域,如汽车活塞、轴承、轴瓦及一些体育运动器材上SiCp/Al复合材料已有成功的应用。
欧洲把SiCp/Al复合材料应用于火车刹车块,德国城市铁路快车上己经成功地用SiCp/Al复合材料取代原来的铸钢制造刹车盘。
美国曾用SiCp/Al复合材料制造赛车和摩托车的刹车片,并用20%SiCp/6061Al复合材料制造参赛帆船的桅杆和浮筒等部件。
美国DuralCan公司已用SiCp/Al复合材料成功地制造了汽车制动盘、汽车发动机活塞和齿轮箱等汽车零件。
与铸铁制动盘相比,SiCp/Al制动盘重量减轻40~60%,耐磨性能优良,噪音明显减小,而且摩擦散热快。
与Al合金活塞相比,
SiCp/Al复合材料汽车活塞具有高的耐磨性,良好的耐高温性能和抗咬合性能,而且热膨胀系数小,导热性较好。
用SiCp/Al复合材料制成的汽车齿轮箱的强度和耐磨性均明显高于Al合金齿轮箱。
美国DWA公司采用SiCp/Al复合材料制造的摩托车活塞耐磨性极佳,装有该活塞的摩托车参加了一年内的100次越野赛,复合村料活塞无明显磨损。
另外,SiCpAl复合材料还适合制作汽车驱动轴、连杆、摇臂等汽车零件。
在电子器件、精密仪器和光学仪器方面,利用SiCp/Al复合材料热膨胀系数和密度低,导热性能良好等优点,已用来制造电子器材的封装材料、散热片等电子器件。
美国亚利桑那大学研制了一种超轻型空间望远镜,采用SiCp增强铝基复合材料制造支承和副镜,不仅大大减轻了重量,通过控制SiC的含量还可使得复合材料的膨胀系数与反射涂层相匹配,并在很大的温度范围内均能保证理想的尺寸稳定性。
此外,现已用SiCp/Al复合材料制造出了惯性导航系统的精密零件、旋转扫描镜、红外观测镜、激光镜、激光陀螺仪、反射镜、镜子底座和光学仪器托架等精密仪器和光学仪器。
虽然SiCp/Al复合材料的应用范围广泛,应用前景开阔,但这种复合材料的一些特点也给它的切削加工带来了很大的困难和挑战。
由于增强相SiC颗粒的加入,该复合材料变得硬而脆,坚硬的SiC(硬度约为HV2700-3500)对刀具会造成严重的磨粒磨损,硬度比增强相低的传统刀具如高速钢和硬质合金在很多情况下都无法适用,特别是对粗加工以及大体积分数的SiCp/Al复合材料切削加工,刀具在数秒至数分钟内即宣告失效。
对于该材料的传统机械切削加工,各种刀具在较大速度范围内都容易产生积屑瘤,积屑瘤不但改变了刀具实际前角,它在切削工程中不断生成和脱落还会造成切削振动,对加工过程的稳定性和加工表面质量产生很大影响。
该材料的已加工表面缺陷和加工所致损伤较严重,如SiC颗粒的破碎、拔出、转动留下的孔洞、微裂纹等缺陷;破碎和松动脱落的SiC颗粒在刀具后刀面的推动下,在已加工表面滑动耕犁,严重损坏已加工表面质量。
在切削这种材料时,刀-屑接触长度短,切削力大,在切削力和切削热的作用下,已加工表面会产生显著的加工硬化现象,甚至使铝合金基体局部熔化;由切削热、材料塑性变形和弹性恢复会产生较大的残余应力;随机分布的SiC颗粒在切削中易引起振动,对表面粗糙度和零件形状精度造成较大影响。
另外,切削该材料时冷却液的使用往往会增加刀具的磨损。
近20年来,人们对SiCp/Al复合材料的车削加工进行了广泛和深入的研究,尝试过的刀具有:
高速钢(涂层和未涂层)、硬质合金(涂层和未涂层)、陶瓷刀具、CBN、CVD、PCD和SPDT等。
结果表明,高速钢和硬质合金刀具一般不适和该材料的切削加工;陶瓷刀具由于和铝的亲和力大,也不适合该材料的切削加工;CBN刀具切削该材料时粘结磨损和磨粒磨损都比较严重,且刀具材料昂贵;PCD在切削SiC颗粒增强铝基复合材料时,具有理想的刀具耐用度,但昂贵的加工成本和加工所致表面/次表面损伤这些问题一直没有得到很好的解决。
天然金刚石SPDT是一种各向异性的单晶体,硬度非常高(HV10000),耐磨性极好,刀具刃口可做得极为锋利,可长时间地切削较硬的物质而保持刃口尺寸的稳定性,加工变质层极小,并且还具有摩擦系数比较小(0.10~0.40)的特点,从而非常适合该材料的超精密切削加工。
但基于SPDT技术的该材料的超精密切削加工技术这一重要领域,长久以来一直没有得到重视,国内外相关报道极少。
早在20世纪50年代末,由于航天等尖端技术发展的需要,美国首先发展了金刚石刀具的超精密切削技术,称为“SPDT技术”(singlePointDiamondTurning),并发展了相应的空气轴承主轴的超精密机床,用于加工激光核聚变反射镜、战术导弹及载人飞船用球面非球面大型零件等等。
SiC颗粒增强铝基复合材料的常规机械切削加工就如此困难,对它进行超精密切削加工就更是一项具有高难度和高技术含量的挑战。
然而超精密加工既是一种高代价、高投入的工艺技术,又是高增值、高回报的工艺技术,世界工业先进国家都把它放在国家尖端技术和经济振兴的重要位置,所以我们有必要对这种性能优异、应用前景广泛的复合材料进行超精密切削加工研究。
这项工作对发展我国的航空航天事业和促进我国国防建设具有重大意义,对促进该材料在汽车工业和民用等领域的发展和应用也具有积极的经济效益和社会效益。
我们将针对具有高比刚度、高导热及低膨胀系数的SiCp/Al复合材料的特殊机械物理性能,系统研究不同体分比和尺寸的该材料应用于典型零件的超精密车削的相关工艺和技术。
这对大幅度提高我国兵器材料强韧化水平而又不增加其重量和成本,实现武器轻量化和提高其性能有着重要意义。
3、课题研究的依据和必要性
近年来,SiC颗粒增强铝基复合材料(SiCp/Al)由于具有比强度和比模量高、耐高温、耐磨、耐疲劳、热膨胀系数小、尺寸稳定性好等优异的综合性能,而显示出在航空航天、先进武器系统、汽车、光学精密仪器、电子和体育用品等众多领域都有很好的应用前景。
SiCp/Al制造工艺设备简单,制造成本低,可批量生产,且可用常规金属加工方法制造各种形状复杂的零件和型材,成为当前金属基复合材料研究发展和应用的主要方向之一。
现阶段,随着兵器材料技术的不断发展,对材料的要求日益提高。
单一的金属材料尤其是轻金属材料的性能,不能满足武器装备的高性能要求。
因此,必须研究与使用金属基复合材料,大幅度提高武器装备的强韧化水平而又不增加重量和成本,这对于实现武器轻量化和提高其性能有着重要意义。
利用SiCp/Al复合材料比强度、比刚度高的特点,可制备卫星天线丝杠;利用SiCp/Al复合材料尺寸稳定性好、膨胀系数低的特点可制备导弹反光镜、导弹惯导平台等部件。
此外,现已用SiCp/Al复合材料制造出了惯性导航系统的精密零件、旋转扫描镜、红外观测镜、激光镜、激光陀螺仪、反射镜、镜子底座和光学仪器托架等精密仪器和光学仪器。
SiC颗粒增强铝基复合材料在上述这些领域的应用,无不关系着精密和超精密加工技术。
超精密加工是发展尖端技术产品不可缺少的关键性加工手段,不管是军事工业,还是民用工业都需要这种先进的加工技术。
目前,基于SPDT技术的超精密加工主要用于不含铁的强度较弱的塑性或脆性材料,如铜、铝、硅、锗、无氧铜、无电解镍、硫化锌、砷化镓、KDP晶体和塑料等。
而SPDT技术应用于SiC颗粒增强铝基复合材料的超精密加工,迄今为止国内外还未见相关的详细报道。
利用SPDT技术对这种材料进行超精密加工时,会遇到很多困难和挑战。
如坚硬的SiC颗粒增强相会对金刚石刀具会造成严重的磨粒磨损;SiC颗粒的破碎、拔出、转动会在已加工表面留下的孔洞、微裂纹等缺陷;破碎和松动脱落的SiC颗粒在刀具后刀面的推动下,在已加工表面滑动耕犁,会严重损坏已加工表面质量;在切削力和切削热的作用下,已加工表面会产生加工硬化现象;由切削热、材料塑性变形和弹性恢复会产生较大的残余应力;随机分布的SiC颗粒在切削中易引起振动,对表面粗糙度和零件形状精度会造成较大影响。
另外,切削该材料时冷却液的使用往往会增加刀具的磨损。
对SiC颗粒增强铝基复合材料进行超精密切削加工是一项具有高难度和高技术含量的挑战,然而超精密加工既是一种高代价、高投入的工艺技术,又是高增值、高回报的工艺技术,我们有必要对这种性能优异、应用前景广泛的复合材料的超精密加工技术进行系统、深入的研究。
这项工作对发展我国的航空航天事业和促进我国国防建设具有重大意义,对促进该材料在汽车工业和民用等领域的发展和应用也具有积极的经济效益和社会效益。
4、国内外研究的技术现状
迄今为止,对SiC颗粒增强铝基复合材料,国内外的研究人员使用过的传统的切削方式有:
车、铣、刨、磨、钻、铰等;非传统方法有:
放电加工、激光/等离子切割、电化学加工、高压水切割、磨料流加工等。
各种加工方法所获得的加工表面都显著地不同于其它普通均质材料加工表面,该材料的已加工表面包含大量的加工所致缺陷,如SiC颗粒的破碎、拔出、转动留下的孔洞、微裂纹,加工硬化和残余应力等。
传统的切削加工中尝试过的刀具有:
高速钢(涂层和未涂层)、硬质合金(涂层和未涂层)、陶瓷刀具、CBN、CVD、PCD和SPDT等。
但绝大多数研究者都是在常规方式、常规精度下对该材料进行切削加工研究,且仅仅对不同体分比、尺寸的SiC颗粒和不同基体合金的该种材料进行加工性研究,或仅对一种或几种刀具的切削性能进行研究,研究内容主要涉及刀具磨损、切削力、温度、表面粗糙度、表面/次表面损伤等,而对SiC颗粒增强铝基复合材料的变形和去除机理、界面性质对材料切削加工的影响涉及较少或没有深入研究。
有关方面文献都没有提供系统的切削加工工艺参数,对该材料的变形机制、切削机理、切屑及加工表面形成机制进行没有作深入、系统的研究。
而对于SiC颗粒增强铝基复合材料的超精密车削加工,可获得的资料更是屈指可数,可以说在这方面的研究基本上还是空白。
1993年,国内哈尔滨工业大学的袁哲俊、耿林等对20%SiCw/6061Al晶须增强复合材料的SPDT超精加工进行了研究,对铸态和拉伸态的该材料,分别获得了Ra0.010μm和Ra0.062μm的表面粗糙度。
2002年,哈尔滨工业大学的韩荣第、王大镇等人使用PCD刀具,对20%SiCw/LD2晶须增强复合材料进行了超精车削加工研究,他们获得了Ra0.012μm的表面粗糙度。
2002年,中国香港理工大学的C.F.Cheung、K.C.Chan等人利用SPDT技术,对体积分数分别为15%和20%的SiCw/6061Al进行了外圆车削,并和SiCp/6061Al、Al6061基体作了比较。
据他们报道,对15%SiCw/6061Al、15%SiCp/6061Al和20%SiCw/6061Al这3种材料,分别获得了Ra=14.3-16.3nm、Ra=20-24.4nm和Ra=18.7-20.2nm的表面粗糙度。
由此可见,国内现有的可获的几篇文献大都是对SiC晶须增强铝基复合材料的超精密加工的研究,对SiC颗粒增强铝基复合材料的超精密加工的研究只有零星的报道。
国外方面,还未见有利用SPDT技术对SiC颗粒增强铝基复合材料进行超精密加工方面研究的报道,只见有一、两篇关于该种材料超精密磨削的报道,其原因可能是这种材材涉及到航空航天以及军事等敏感领域,故西方工业发达国家对有关这方面的研究信息进行了封锁。
从以上获得的零星数据可以看出,基于SPDT技术的SiC颗粒增强铝基复合材料的超精密加工基本上是可行的,但是我们对这种材料金刚石车削时的切削机理、变形行为以及它们与表面形成的关系还很不明了,对于该材料超精密切削加工工艺的研究尚属空白。
表二共14页第6页
课题研究方案
(包括具体的研究目标、研究内容和拟解决的关键问题;拟采取的研究方法、技术路线、实验方案及可行性分析)
本课题将切削细观力学理论建模、有限元仿真技术和试验有机结合起来,对SiC颗粒增强铝基复合材料超精密车削机理和工艺进行基础性研究,最后在选择合理的刀具几何角度、工艺参数、SiC颗粒体分比、冷却液的基础上,并将机械-工艺系统调整到最佳耦合状态,加工出符合精度要求的SiC颗粒增强铝基复合材料典型零件。
(1)SiC颗粒增强铝基复合材料超精密切削机理研究
SiCp/Al超精密切削细观力学模型的建立及切削过程的有限元仿真
结合弹塑性力学与断裂力学来考虑建立适合SiC颗粒增强铝基复合材料超精密切削的细观力学模型。
选择商业有限元软件MSC.Deform,在大变形、高温和高应变率下,建立工件材料特性与时间和应变率相关的三维斜角切削弹塑性有限元模型,对开始切削到切削稳定阶段(形成稳定切屑)的材料变形、去除机制进行仿真,对切削力、切削温度、应力应变、残余应力在切屑、工件、刀具中的分布规律进行仿真。
SiCp/Al超精密切削机理研究
通过工具显微镜、光学显微镜和SEM观察切屑的形态及其微观组织结构,用AFM对已加工表面的形貌和微观组织结构进行观察研究,研究切削时SiC颗粒增强铝基复合材料中空洞和裂纹的形成原因以及裂纹扩展路径和方式、剪切区变形规律、材料变形和去除机制。
通过观察和测量切削力、切削温度,利用工具显微镜、SEM、XRD、EDX研究刀具磨损模式和机理,用显微硬度计、表面粗糙度测量仪、金相显微镜、XRD、SEM研究已加工表面质量,从而弄清刀具-工件、刀具-切屑的相互作用机制,刀具磨损模式和机理,表面/次表面损伤。
(2)SiC颗粒增强铝基复合材料超精密车削工艺研究
分别选择-5o、0o、5o三个前角值,5o、10o、15o三个后角值,-5o、0o、5o三个刃倾角值,0.4、0.8、1.6mm三个刀尖圆弧半径值,50、200、800nm三个刃口半径值,研究刀具几何角度、刃口半径及形状精度对切屑的几何形状、已加工表面粗糙度和尺寸精度、刀具磨损、已加工表面完整性的影响。
选择体分比分别为5、15、25%,颗粒尺寸分别为15、45、75μm的SiCp/Al,研究颗粒体分比和尺寸对刀具磨损、表面精度和已加工表面完整性的影响。
分别选择v=60、120、240、420m/min,ap=1、3、6、10μm,f=1、3、6、10μm)和不同成分的冷却液,研究切削参数和冷却液成分对刀具磨损、表面精度和已加工表面完整性的影响。
(3)SiC颗粒增强铝基复合材料非球面曲面的超精密车削工艺研究
在上述研究成果的基础上,利用Nanosys-300非球面超精密复合加工系统,探索出适合SiC颗粒增强铝基复合材料非球面曲面超精密车削加工的工艺路线,最终加工出表面粗糙度Ra=0.01-0.05μm,表面精度0.2-0.6μm的非球面表面。
研究基础
(包括与本项目有关的研究工作积累和已取得的研究工作成绩;课题研究现有的基础和已具备的实验条件,可能遇到的困难或问题和拟解决的途径和措施等)
对于SiC颗粒增强铝基复合材料这种极难加工的材料,其超精密加工不仅要解决形位公差、尺寸精度和表面粗糙度的这些核心问题,而且要获得尽量小的加工所致缺陷和加工变质层,这更是一项高难度的挑战。
对该材料的SPDT超精密加工,不仅要求有高刚度和高精度的超精密加工机床,对刀具系统和工作外环境的要求也非常苛刻。
金刚石刀具的几何角度、刀面的晶面取向、刃口半径大小及其形状精度对超精密加工表面的形成和质量有着决定性的影响,机床工作环境,如温度、湿度、清洁度和振动等对超精密加工表面质量也有着极大的影响。
此外,超精密加工表面质量和结果也和SiC颗粒增强铝基复合材料的物理机械性能和微观组织结构、机床-刀具-工件工艺系统的耦合情况息息相关。
本课题拟对SiC颗粒增强铝基复合材料进行以下几方面开创性、系统性的研究:
SiC颗粒增强铝基复合材料超精密切削机理研究;SiC颗粒增强铝基复合材料超精密车削工艺参数的系统研究;SiC颗粒增强铝基复合材料非球面曲面的超精密车削工艺研究。
2.2.1SiC颗粒增强铝基复合材料超精密切削机理研究
这是本课题的重点,也是难点。
本项研究主要包括以下三个方面:
(1)建立SiC颗粒增强铝基复合材料超精密切削的细观力学模型
由于切削过程中刀具和SiC颗粒之间剧烈的摩擦造成刀具迅速磨损,切屑也有着不可忽略的横向流动,再加上SiC颗粒是具有一定尺寸的三维实体,且在复合材料中有相当的体分比,所以这种材料的剪切变形就不能被看作是在单一的平面内完成的,而是在一个具有一定宽度的区域内完成,剪切角在切削过程中也不是一个定值,故经典的单一剪切面模型和剪切角理论不再适合SiCp/Al的切削分析。
到目前为止还没有在纯理论分析基础上建立该材料的切削模型。
对于连续增强的复合材料(尤其是长纤维增强的聚合物基复合材料)己经有了各种成熟的力学模型,在此基础上也己发展了一些短纤维增强复合材料的力学模型,但是对于颗粒增强的复合材料,其力学模型的建立是极复杂和困难的问题,至今少见有成果报道。
因此,在颗粒增强金属基复合材料的力学行为研究中尚欠缺系统、完整的理论基础。
鉴于颗粒增强材料与未增强材料的根本区别在于前者含有不可塑性变形的硬脆颗粒,且增强颗粒是复合材料受外力作用后行为的控制相,所以应结合弹塑性力学与断裂力学一起来考虑建立复合材料的切削模型。
(2)SiC颗粒增强铝基复合材料超精密切削机理的有限元建模与仿真
由于超精密切削加工难度大、刀具机床费用高,所以完全在试验的基础上进行该材料的超精密切削加工机理研究是不科学的,也是不必要的。
本课题拟采用有限元技术,对该材料的切削过程进行三维建模和仿真,从而了解该材料超精密切削加工时的变形机制和去除机理,切屑和加工表面形成机制,刀具磨损的模式和磨损机理,刀具-工件、刀具-切屑之间的相互作用机制,以及应力应变、温度和残余应力在刀具、切屑、工件中的分布规律。
(3)SiC颗粒增强铝基复合材料超精密切削机理研究
有限元仿真有其局限性和困难,如材料的特殊性,切削过程中的高的局部应变率以及切削区附近产生的温度都对仿真结果的准确性和精确性都有重大影响。
且超精密切削加工是一个及其复杂的过程,刀具-工件-切屑三者的相互作用非常复杂,所以有必要对该材料的超精密加工机理仿真的结果从试验的角度来进行验证和修正。
通过观察试验中的切屑形态及其微观组织结构,已加工表面的形貌和微观组织结构,研究空洞和裂纹的形成原因以及裂纹扩展路径和方式,从而了解材料变形和断裂机制和剪切区变形规律。
通过测量试验工程中的切削力、切削温度、切屑变形系数,观察刀具前、后刀面的磨损方式和磨损区域微观形貌和结构,以及通过对已加工表面形貌、显微硬度、显微组织和残余应力进行测量,来研究刀具-工件、刀具-切屑的相互作用机制。
2.2.2SiC颗粒增强铝基复合材料超精密车削工艺研究
前人在SiC颗粒增强铝基复合材料超精密切削加工工艺方面的研究非常有限,该材料的系统的超精密车削工艺研究尚属空白。
通过有限元仿真和试验手段相结合,研究刀具几何角度,单晶金刚石刀具刀面的晶面取向,增强颗粒的体分比、尺寸、形状及其分布,基体材料及其热处理状态,切削参数和冷却液等对该材料超精密切削加工的影响,主要研究在各种切削条件下的切屑形状、刀具磨损、切削力、温度、表面粗糙度、表面/次表面损伤等。
2.2.3SiC颗粒增强铝基复合材料非球面曲面的超精密车削工艺研究
表二共14页第9页
研究计划和进度
2005.2-2005.6
系统查阅并消化相关文献。
2005.7-2005.9
进一步查阅和消化总结相关文献,对课题的可行性进行论证,并撰写开题报告。
2005.10-2006.6
完成SiC颗粒增强铝基复合材料超精密切削机理和适合工艺参数的研究,并加工出符合精度要求的典型零件。
2006.7-2006.12
针对前阶段试验过程中发现的系列问题,提出改进措施;同时完成博士论文的初稿,查漏补缺,进一步完善研究内容。
2007.1-2007.4
完成博士论文。
效果预测
(包括预期研究成果、研究内容的创新性)
本课题的研究将达到以下效果:
(1)建立适合SiC颗粒增强铝基复合材料超精密切削的细观力学模型,也为其他金属基复合材料的切削机理提供参考。
(2)深入地研究SiC颗粒增强铝基复合材料超精密切削机理,为探求该材料的合理的车削加工工艺路线打下坚实的理论基础。
(3)探索、配备出适于切削SiC颗粒增强铝基复合材料的切削液成分。
(4)提供相应的金属基复合材料超精密车削工艺系统参数。
(5)对机械系统、工艺系统进行调整,实现机械-工艺系统的最佳耦合。
(6)探索出SiC颗粒增强铝基复合材料非球面曲面的超精密车削工艺,同时也为其他类似材料提供工艺上的借鉴。
主要技术指标为:
面型精度:
0.2-0.6um
表面粗糙度:
Ra0.01-0.05um
(7)发表论文3篇以上。
研究经费预算与来源(含支持本课题的项目编号)
项目
预计经费(万元)
经费来源
备注
资料
0.2
原材料
2.0
试验费
1.5
测试费
1.5
杂费
0.2
不可预测费用
0.3
共计
5.7
表二共14页第11页
参考文献(应有50篇以上)
[1]材料加工原理,徐洲,姚寿山,科学出版社,2003年
[2]复合材料力学,R.M.琼斯,朱颐龄等译,上海科学技术出版社,1981年
[3]金属基复合材料的发展及应用,吴利英,高建军,靳武刚,化工新型材料,2002.10,第30卷第10期,pp.32-35