浅谈国内大工业硅炉的冶炼操作.docx
《浅谈国内大工业硅炉的冶炼操作.docx》由会员分享,可在线阅读,更多相关《浅谈国内大工业硅炉的冶炼操作.docx(73页珍藏版)》请在冰豆网上搜索。
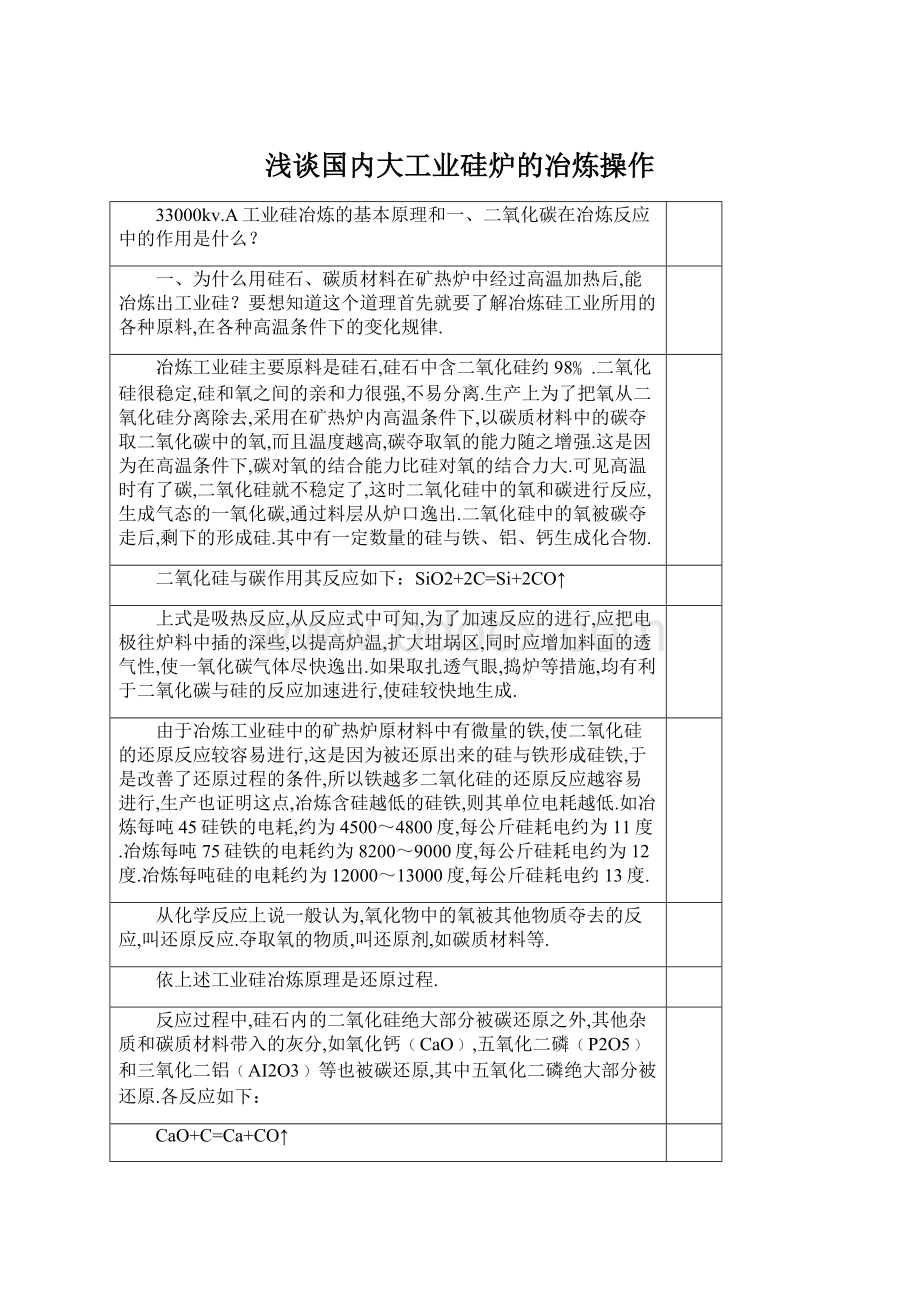
浅谈国内大工业硅炉的冶炼操作
33000kv.A工业硅冶炼的基本原理和一、二氧化碳在冶炼反应中的作用是什么?
一、为什么用硅石、碳质材料在矿热炉中经过高温加热后,能冶炼出工业硅?
要想知道这个道理首先就要了解冶炼硅工业所用的各种原料,在各种高温条件下的变化规律.
冶炼工业硅主要原料是硅石,硅石中含二氧化硅约98﹪.二氧化硅很稳定,硅和氧之间的亲和力很强,不易分离.生产上为了把氧从二氧化硅分离除去,采用在矿热炉内高温条件下,以碳质材料中的碳夺取二氧化碳中的氧,而且温度越高,碳夺取氧的能力随之增强.这是因为在高温条件下,碳对氧的结合能力比硅对氧的结合力大.可见高温时有了碳,二氧化硅就不稳定了,这时二氧化硅中的氧和碳进行反应,生成气态的一氧化碳,通过料层从炉口逸出.二氧化硅中的氧被碳夺走后,剩下的形成硅.其中有一定数量的硅与铁、铝、钙生成化合物.
二氧化硅与碳作用其反应如下:
SiO2+2C=Si+2CO↑
上式是吸热反应,从反应式中可知,为了加速反应的进行,应把电极往炉料中插的深些,以提高炉温,扩大坩埚区,同时应增加料面的透气性,使一氧化碳气体尽快逸出.如果取扎透气眼,捣炉等措施,均有利于二氧化碳与硅的反应加速进行,使硅较快地生成.
由于冶炼工业硅中的矿热炉原材料中有微量的铁,使二氧化硅的还原反应较容易进行,这是因为被还原出来的硅与铁形成硅铁,于是改善了还原过程的条件,所以铁越多二氧化硅的还原反应越容易进行,生产也证明这点,冶炼含硅越低的硅铁,则其单位电耗越低.如冶炼每吨45硅铁的电耗,约为4500~4800度,每公斤硅耗电约为11度.冶炼每吨75硅铁的电耗约为8200~9000度,每公斤硅耗电约为12度.冶炼每吨硅的电耗约为12000~13000度,每公斤硅耗电约13度.
从化学反应上说一般认为,氧化物中的氧被其他物质夺去的反应,叫还原反应.夺取氧的物质,叫还原剂,如碳质材料等.
依上述工业硅冶炼原理是还原过程.
反应过程中,硅石内的二氧化硅绝大部分被碳还原之外,其他杂质和碳质材料带入的灰分,如氧化钙﹙CaO﹚,五氧化二磷﹙P2O5﹚和三氧化二铝﹙AI2O3﹚等也被碳还原,其中五氧化二磷绝大部分被还原.各反应如下:
CaO+C=Ca+CO↑
P2O5+5C=2P+5CO↑
AI2O3+3C=2AI+3CO↑
反应中生成的一氧化碳气体,从炉口逸出,其他生成物如钙、铝和磷等进入硅铁中,因此,要求原料中的杂质尽量少,以保证硅铁的质量.
在冶炼过程中有少部分的二氧化硅,三氧化二铝和氧化钙等未被还原,而形成炉渣.炉渣成分约含SiO2:
30~40﹪;AI2O3:
45~60﹪;CaO:
10~20﹪.此种炉渣熔点约为1600~1700℃.渣量大时,消耗电量增加,同时过粘的炉渣,不易从炉内排除,引起炉况恶化.故要采用较好的原料,以减少渣量,降低单位电耗.
正常情况下,渣量控制在不大于硅量的百分之五为宜.以上是硅铁冶炼基本原理,工业硅冶炼的基本反应如下:
SiO2+2C=Si+2CO↑
实际炉内的化学反应比这复杂.实验证明氧化物的还原,是由高价氧化物逐步还原成低价氧化物.二氧化硅的还原,在高温情况下,首先被还原成一氧化硅〔SiO〕,而后再被还原成硅〔Si〕,其顺序是SiO2→SiO→Si冶炼工业硅,在1700~1800℃时,将发生如下反应:
SiO2+C=SiO+CO↑
也就是说二氧化碳硅首先被碳还原成一氧化碳,然后再被还原成硅,其反应式如下:
SiO+C=Si+CO↑
被还原出来的硅,部分的将和二氧化硅作用,又产生一氧化硅,其反应式如下:
SiO2+Si=2SiO↑
从上述的三个反应式中,可以看到一氧化硅对促进冶炼反应的进行是个重要环节.一氧化硅在高温情况下是以气体状态存在,低温时不稳定.因此,一氧化硅在炉内坩埚中是气体,少量的一氧化硅从炉口逸出后,被空气氧化﹙SiO+1∕2O2=SiO2﹚
而成为二氧化硅,冷却后呈灰白色,部分凝结在电极,筒瓦等处.在约为1700℃以上高温时,大部分的一氧化硅挥发到碳质材料的气孔中,广泛地和碳接触并作用,按第二个反应式,还原成硅,少部分的硅在高温区与二氧化硅作用,按最后反应式又生成一氧化硅,然后又和碳进行反应,结果反应连续不断地进行.由此可知,一氧化硅不但是反应的中间产物,同时,它可促进反应加速进行.
由于一氧化硅在高温下是气体,易挥发而损失掉,尤其当塌料或大刺火时,逸出或喷出白色气体多是一氧化硅.因此,要求与时处理"塌料或大刺火〞的现象,否则,将造成一氧化硅的大量损失,减少产量,增高单位耗电.
二、反应中碳化硅的产生和破坏的原因是什么?
冶炼工业硅时在反应中的二氧化硅首先破坏被还原成一氧化硅.部分的一氧化硅气体在上升过程中与料层中碳质材料接触并作用后,较易生成碳化硅.其反应如下:
SiO+2C=SiC+CO↑
冶炼过程中,碳质材料加入量过多时,更易产生碳化硅.其反应式如下:
SiO2+3C=SiC+2CO↑
往往在修炉时于料层内部发现大量碳化硅﹙冷却后呈褐色,稍有光泽并是针状结晶﹚,说明产生碳化硅的反应是存在的,并且是中间产物.
碳化硅SiC的熔点约为2500℃,不易熔化,电阻小,导电性强.因此,炉中积存过多碳化硅,使炉况恶化.例如:
〔虽然碳化硅易产生,但在冶炼硅铁中由于炉料中有钢屑,碳化硅较轻易被铁﹙Fe﹚破坏〕,其反应式如下:
SiC+Fe=FeSi+C
冶炼45硅铁,因炉料中钢屑较多,碳化硅更易破坏,所以,碳化硅对炉况没有影响.碳化硅在高温时,还可被二氧化硅所破坏,其反应式如下:
SiO2+2SiC=3Si+2CO↑
2SiO2+SiC=3SiC+CO↑
较大容量工业硅电炉,因炉温高,碳化硅易被破坏.碳化硅在高温时还可以被一氧化硅破坏,其反应式如下:
SiO+SiC=2Si+CO↑
三、高温下形成的"坩埚〞作用是什么?
什么是坩埚?
坩埚就是每相电极下面的"埚〞型高温区,也就是主要的发言区.
二氧化硅在较高温度下,粘度比较大,每当捣炉时就会发现很粘稠的炉料,甚至呈玻璃丝状.电极附近的炉料,因距离电极位置不同,高温处即熔化,低温处即粘结.所以,在电极周围自然形成有粘结炉料组成的"埚〞型高温区,即主要
反应区,习惯称为坩埚.坩埚顶和壁是粘稠的熔融状炉料,其组成为粘稠的炉料混合物;已进行部分反应而生成的化合物;硅颗粒;液体合金;碳化硅和三氧化二铝等.坩埚内部是气体空间也就是电弧区.坩埚内的温度约为1800~2000℃以上,能够使化学反应比较充分地进行.冶炼工业硅,当大塌料时,可看到坩埚的部分形状,在电炉修洗炉时,也可看到坩埚的部分轮廓.
坩埚顶和壁的炉料,在高温下不断地反应,生成硅落入熔池内,又不断地加入新炉料.所以,坩埚是主要反应区.坩埚的大小对冶炼有很大的影响.
电极插入炉料较深时,热量损失较少,炉内温度高,坩埚则较大,反应速度较快,产量高,单位电耗低.反之,电极插入炉料浅时,热量损失增加,炉内温度较低,坩埚则较小,反应速度减慢,产量低,单位电耗势必增高
坩埚的大小也可以从料面的透气性来判断,当料面透气性比较均匀时,说明坩埚较大.当料面透气性不好时,炉中的料下沉速度较慢时,则说明坩埚较小.
控制合适的配料比,操作中不偏加料;维护好炉况,使料面保证较低的高度,并保持炉料有良好的透气性等,这样就有较大的坩埚.
供电制度对坩埚的大小也有影响,使用的功率高,则坩埚较大;反之则坩埚较小.
每相电极的坩埚扩大到一定程度时,坩埚间必然互相沟通,出炉时硅水就比较容易全部流出.如因炉温低或炉底上涨等原因,造成坩埚小,甚至使三个坩埚不能连通,这样不但硅水不能全部排出,并对下一炉冶炼造成不利的影响.
四、原料和配料
1.什么样的硅石适于冶炼工业硅?
硅石是冶炼工业硅的基本原料之一.为减少渣量,降低电耗和提高产量,要求硅石中的二氧化硅含量大于99%.硅石中的,三氧化二铝是有害杂质,它的熔点高约为2050℃当炉渣中含有较高的三氧化二铝时,将造成排渣困难.同时硅石中三氧化二铝较多时,易使铝被还原出来而进入硅中,使硅的含铝量增加,影响硅质量.因此,要求硅石中的三氧化二铝不大于0.2%.硅石表面呈现粉红色线条是三氧化二铝存在的象征.三氧化二铝也常存在硅石表面泥土中.为此,硅石入炉之前用水冲洗,以减少冶炼时的渣量.
硅石中的含硫量,由于冶炼过程中硫﹙S﹚和硅﹙Si﹚形成硫化硅,如SiS、SiS2等化合物,这些化合物在高温下易挥发跑掉,因此对硅石含硫量不作要求.
硅石中的氧化钙﹙CaO﹚和氧化镁﹙MgO﹚含量较高,冶炼时就会增加渣量,并侵蚀出铁口,为此要求硅石中氧化钙和氧化镁含量之和小于0.5%.
硅石加入炉内预热时均有不同程度的爆裂,这是因二氧化硅晶格变化时体积膨胀造成的.不同产地的硅石,其爆裂程度不同.受热后爆裂程度较大的硅石,在冶炼时会恶化料面的透气性,造成炉况变坏.因此.要求硅石在高温下,应具有一定热稳定性.
大工业硅矿热炉温度较高,硅石更易早期爆裂,因此要用质量好些硅石.选矿源时要把硅石先做炉内试验,再确定是否能用.小炉子用的硅石,可因地制宜,适当酌情降低质量要求.
对硅石粒度也有要求,粒度过大,反应速度减慢,粒度过小或粉末多,会影响料面的透气性.粉末多的硅石带入泥土也多,使渣量增加.生产证明︰大工业硅矿热炉用的硅石,要求粒度为60~120毫米,其中大于80毫米的要大于50%.
五.什么样的碳质材料适于冶炼工业硅?
冶炼工业硅石油焦、煤是主要原料,它是冶炼硅的还原剂,所以要求碳质材料内的固定碳的含量越高越好,要大于84﹪,同时要求碳质材料灰分要低.因碳质材料灰分含量高时,渣量增加,由于灰分内含60﹪左右的三氧化二铝﹙AI2O3﹚,造成炉渣粘不易排除.此外,灰分高的碳质材料加入炉内易使料面烧结,影响透气性.因此,要求碳质材料灰分含量应低于2.5﹪.
碳质材料中的碳大部分是以固定碳形式存在,但也有少部分的碳是以碳氢化合物﹙通常称为挥发分﹚形式存在.这部分碳氢化合物在高温下即挥发跑掉,所以要碳质材料的挥发分含量不大于26-38﹪.
除对碳质材料有化学成分要求外,对其物理性能也有要求.碳质材料高温下电阻越大,电极插入炉料越深,有助于提高炉温,从而扩大坩埚.碳质材料的气孔率大,不但电阻大,表面积也大,增加了化学反应面积,加速了化学反应的速度.
碳质材料的粒度对冶炼有很大影响.粒度过大时,炉料电阻减小,电极不易深插入炉料,造成炉温低和坩埚小,冶炼不正常.粒度过小或粉末多,则烧损较大,易使炉况变粘,影响料面的透气性.因此,碳质材料要有一定的使用粒度.大硅铁电炉所用碳质材料粒度以小于8-25毫米为宜.
对碳质材料物理性能要求不做具体规定.可根据生产实践,来选择较合适的碳质材料.
目前,我国冶炼硅用的石油焦、煤,多是筛下的小颗粒.
六、为什用小颗粒可使电极较深地插入炉料?
冶炼工业硅所用的碳质材料,很重要的是希望它在高温下的电阻大,可使电极较深地插入炉料内,有利于提高炉温和扩大坩埚区.碳质材料电阻大为什么使电极插入炉料较深?
这是因为电阻大,通过的电流必然减少,为保持负荷就要增加电流,于是向下移动电极,增加插入深度,从而使电极插入较深的炉料中.
不同粒度碳质材料的电阻变化原因如下:
1.电流通过碳质材料,因这块碳质材料中间无缝隙,电流受的阻力很小,说明这块碳质材料的比电阻较小.
2.把这块碳质材料分为两块,因中间有缝隙,电流通过时略有阻力,说明这时碳质材料的比电阻有所增加.
可见,碳质材料的粒度越小,它的电阻就越大.反之,碳质材料粒度越大,电阻则越小.原因是:
粒度小表面积就大,接触电阻增大,所以粒度小的碳质材料电阻大.反之,粒度大表面积减少,接触电阻变小,因此,力度大的碳质材料电阻小.
由于粒度小的碳质材料电阻大,所以用小粒碳质材料做还原剂时可使电极较深的插入炉料中,这样有利于提高炉温,从而扩大坩埚,加速冶炼化学反应的进行,提高产量,降低单位电耗.
七、冶炼工业硅为什么可用部分粘结煤?
冶炼工业硅的还原剂多数用粘结煤.粘结煤在炼焦过程中焦化温度约为1100~1300℃而形成的焦炭,所以也称冶金焦为高温焦或全焦.焦化温度约600~800℃而形成的焦炭称为低温焦或半焦.煤气焦就是低温焦的一种,所谓煤气焦就是生产煤气时的副产品.
煤气焦和冶金焦性质比较如下:
1.电阻
粒度10~15毫米的各种焦炭,比电阻与温度之间关系,根据实际测定如图4所示.煤气焦的电阻大于冶金焦,即使在较高的温度时,它的电阻仍大于冶金焦的电阻.电阻大时煤气焦的重要的优点.实践证明,冶炼工业硅时使用部分煤气焦,电极可较深的插入炉料中,从而降低电耗.
2.化学成分
粘结煤中含固定碳较低,灰分较高,从化学性质上来说它不如冶金焦好.这是因粘结煤的焦化温度较低造成的.粘结煤的含碳量低,用它做还原剂时加入量应多些,同时由于粘结煤中灰分高,冶炼时渣量也增加,另一方面也由于粘结煤中含碳较低和它的机械强度较差.在冶炼中往往在坩埚中和下部有缺碳现象.可见,冶炼工业硅全部用粘结煤做还原剂,炉况不易维护.
3.气孔率和反应能力
粘结煤的气孔率比冶金焦的气孔率大40~60﹪,这样不但使粘结煤的电阻大,同时也扩大反应接触面,另一方面粘结煤的反应能力也较高,均有利反应速度加快进行.
上述粘结煤有气孔率高、电阻大和成本低的优点,但它又有含碳较低、灰分高和机械强度差的弱点.所以冶炼时不宜全部使用粘结煤,可与石油焦搭配使用.实践经验证明搭配30~40﹪的粘结煤和石油焦共同使用其效果较好,单位电耗有所降低.
八、为什么可以使用少量的碳化硅
有些单位为降低单位电耗,在冶炼工业硅时加入少量的碳化硅﹙SiC﹚,这样可节约部分电能.这里指的"碳化硅〞,并不是一种特定的原料,而是制造石墨电极时石墨化炉的保温废料.它含有大量的碳化硅,因此,习惯这种废料叫"碳化硅〞.它的成分如下:
SiC2:
5~40%;SiO2:
20%;C25%;其余为Al2O3和CaO等.为什么冶炼时加入少量的"碳化硅〞可以降低电耗.
冶炼工业硅时,二氧化硅被还原是吸收大量热能的反应,因此要在很高的温度﹙约1800~1900℃﹚下,才能使这一反应激烈进行,因此要消耗大量的电能.当炉料中加入部分碳化硅时,它和炉料中的铁在炉内发生如下反应:
SiC+Fe=FeSi+C
这个反应是吸热反应,它吸收的热量和反应温度,要比二氧化硅还原时所需的热量和温度要低.所以炉料中加入部分碳化硅,可以降低电耗.
冶炼工业硅因炉料中铁含量很少,硅石数量较多,碳化硅的破坏反应,将主要按下式进行:
2SiO2+SiC=3SiO+CO↑
SiO+SiC=2Si+CO↑
这两个反应都约在1800℃以上的高温下进行,并且因有气态的SiO参加反应.而因气态的SiO较易挥发,因此,破坏碳化硅的反应,不易较安全地进行.可见冶炼工业硅铁时,碳化硅的利用率低.
碳化硅的熔点高,导电性强,冶炼时加入强化硅后,电极不易稳定,炉况不好掌握,并且碳化硅粉末多,影响料面的透气性,有时刺火较严重.为此,冶炼时不易加入过多的碳化硅,而所用的碳化硅应精选,以减少粉末.
经验证明,冶炼45硅铁时,每批料﹙硅石按300公斤算﹚,可加50~70公斤碳化硅;冶炼工业硅时,每批料加入2~5公斤较为合适.
九、如何计算碳质材料的加入量?
由工业硅冶炼原理可知,用碳质材料中的碳,还原硅石中的SiO2而生成硅.因此,粘结煤加入量直接影响到SiO2能否充分还原和炉况是否正常.所以碳质材料加入量是重要的.
在计算前要说明以下几个问题:
硅因炉内各个区域冶炼温度有所不同,故计算时碳的过剩量和硅的回收率也不同.硅冶炼温度较低;碳和的硅冶炼温度较高,碳和硅的损失较大,所以碳的过剩量按10%计算,硅的回收率按92%计算.
2.原子量﹑分子量的计算
根据化学元素周期表可知Si原子量为28,C原子量为12,﹙O﹚氧原子量为16.所以SiO2的分子量是28+16×2=60.
3.根据原料化学分析结果和实际工作经验采取:
﹙1﹚计算冶炼工业硅的碳质材料加入量
为计算方便,以100公斤硅石为基础,计算碳质材料加入量.
100公斤硅石中含SiO2为:
100×98%=98公斤
硅铁冶炼反应式:
SiO2+2C=Si+2CO
SiO2和2C分子量:
28+2×16=602×12=24
90公斤SiO2纯碳量为:
24/60×98=39.2公斤
我们所用的是含碳84%的碳质材料,将39.2公斤的纯碳换算为碳质材料,则为:
100/84×39.2=46.6公斤
冶炼工业硅,碳质材料烧损约10%,所以碳质材料的加入量为:
46.6×100/90=51.7公斤≡52公斤
碳质材料中含水量约为5%~15%.经验证明碳质材料含量每增加1%时,要相应增加0.6公斤碳质材料.若碳质材料含水量按5%计算,焦炭实际加入量则为:
52+52×5%×0.6≈54公斤
将上述和计算式化简,冶炼工业硅时,100公斤石的碳质材料加入量则为:
100×SiO2×24/60×C%×0.90=碳质材料加入量<公斤>
式中SiO2-硅中的二氧化硅含量%
C%-碳质材料中的固定碳含量%
0.9-碳的利用率<因碳烧损10%>;
24和60-分别为2个碳和二氧化硅的分子量.
用简化式计算出的碳质材料加入量,并非实际需要量,而要根据碳质材料含量有所增加.
9.碳质材料加入量与哪些因素有关?
上述碳质材料加入量的计算,只根据原料的化学成分和一些实际经验而得出的.但碳质材料的实际加入量,往往不准确、所用二次电压与工业硅矿热炉的容量有关,并且和电极的极心圆直径的大小有关.
理论计算出的碳质材料加入量是主要根据,但还要按下述具体情况进行调整.
1.炉况变化时要调整碳质材料的加入量.炉况发粘时,应适当增加碳质材料加入量.炉况碳过剩应适当减少碳质材料加入量.
2.电极插入炉料较浅时,可适当减少碳质材料加入量.
4.同一炉子,冶炼时用二次电压较高时,碳质材料的加入量应适当少些.
5.同容量的矿热炉,其电极间的极心圆直径较大时,碳质材料加入量应多些,极心圆直径较小时,碳质材料加入量应少些.
6.如何配料,为什么大料批不好?
配料是冶炼工业硅的第一道工序,是一项很重要的工作配料时要注意以下几点:
1.称量准确,各种材料必须按规定的数量进行称量,误差要小.如果称量不准,炉况不易掌握,甚至可能出废品.因此,配料工作要细心,还要经常检查称量工具的准确度,发现问题应与时调整或修理.
2.要按规定的是顺序进行配料,以使炉料均匀混合.碳质材料的堆比重约0.5~0.6硅石的堆比重约为1.5~1.6,原料堆比重相差很大.为了炉料混合均匀,配料顺序为碳质材料、硅石、木片.采用这样的配料方法,炉料由料管下降后,能较均匀混合.炉料混合均匀与否对冶炼有很大影响.为使炉料混合均匀,每次只准量一批料,每个料斗存料为得超过二批料.
为什么大料批不好?
料批的大小是以批料中硅石数量为准.目前冶炼工业硅时,一般每批料中有200公斤硅石或300公斤硅石.前者叫小料批,后者叫大料批.
从炉料混合均匀角度来说,料批越小混合得越均匀,料批越大炉料越难混合均匀.因此,要尽量采用小料批,以使炉料混合均匀,但是,小批量为配料为配料操作带来一定困难.
以下是较大容量的工业硅电炉,冶炼工业硅,料批大小不同时的单位电耗示例:
料批大,电耗较高,料批小,则电耗较低,故采用小料批较好.
十、硅铁冶炼工艺
.冶炼工业硅如何加料?
工业硅冶炼的基本反应,是利用碳质材料中的碳,将硅石中二氧化硅的硅还原出来的反应.要使这一反应顺利进行,必须有良好的炉况.正确的加料方法,是获得良好炉况、达到高产量低消耗的关键环节之一.因此,加料时应注意以下几点:
1.每批料必须混合均匀后加入炉内,不准偏加料.
大家知道,每批料的配比,是根据硅冶炼的化学反应原理和所用原料的成分,并结合实际情况计算出来的.所以,加入炉内的每批料的组成,必须符合批料的配比.均匀地混合炉料是保证炉内反应正常进行的重要操作条件.如果炉料未经均匀混合或任意选择性的加入炉内,这就是同常所说的"偏加料〞,其结果是在炉内局部区域造成硅石过剩或焦碳过剩,这两种情况都不利于炉内反映顺利进行,而使炉况恶化.可见,炉料混合均匀是十分重要的.
2.炉料要连续地一小批一小批地加入炉内.这样不但易于控制料面的高度,而且可以使加入炉料的组成与其分布比较均匀.
3.必须适当地控制料面的高度.料面高度过高则电极上升,料面过低易塌料,两者都不能充分的利用热量,都会对炉况产生不利的影响.
料面高度控制适当,可使电极较深的插入炉料中,从而提高炉温和扩大坩埚,使炉料可得到充分的预热,促使炉内反应加快进行.
4.加料时要随时观察炉况,如料面透气性与电极动态等,必要时应采取相应的措施进行处理.
5.应使炉料与电极成垂直方向加入,但要防止炉料碰撞电极.这种加料方法,可使料面成为低料面宽锥体的形状,不致引起电极波动.
小容量工业硅矿热炉,因其炉温度较低,熔炼速度较慢,应力求减小热量损失.加料时应注意如下几点:
1.勤加、薄盖.
2.随时注意刺火并在处理火后应与时加料.
3.在保持适当的锥体和料面的前提下,进行焖烧,直到出硅后将炉料捣下去,再重新加料焖烧.
现在,我国工业硅生产的加料方式,大多采用加料机加料.加料时应注意以下几点:
1.少加勤快为宜.不能一次加得过多,以便保持良好的料面透气性.
2.应先从锥体底部往电极根部逐渐地加入炉料.这样可以保持炉料的组成,分布比较均匀,不致使硅石块滚到锥体底部边缘.
3.摆动加料机流槽时,其方向与电极成垂直或平行,两种异向投料方式应当交替进行使用.防止加料机槽碰撞电极.
.为什么不能偏加料?
炉况不正常时出于某种原因,为使电极较深的插入炉料或为了稳定电极,要在电极周围加入较多的硅石;有时炉况不正常,在电极周围加入过多焦炭或过多硅石炉料,这就电偏加料.此种操作方法是错误的,危害极大.
1.加入过多的硅石炉料时,初期电极可能插得深,时间过长就会造成电极周围缺碳,坩埚缩小,电极容易上抬,料面透气性不好并有刺火现象,甚至给不足负荷,炉总值恶化,尤其是当出炉口相电极其出现这种情况,其后果更为严重,出炉操作不容易顺利进行.
2.加入碳质材料过多时,电极易上升,同时其他的部位必有缺碳现象,料面会有烧结,透气性不好,不得炉况正常进行.
3.料在炉内分布不均匀,使化学反应不能充分进行,尤其偏加硅石过多,二氧化硅的还原速度大为减慢.
十一、为什么料面要保持一定的高度?
料面高度对充分利用热量,加速炉内化学反应的进行,有很大影响.
料面高度过高,电极与炉料的接解面积增加,通过的电流增大为保持额定电流,需要提升电极,因此,使电极插入炉料中的深度变浅,高温区上移,坩埚缩小,热量损失增多,化学反应速度减慢;炉底温度低,排渣情况不好,甚至引起炉底上涨,使炉况恶