QC钢筋绑扎间距控制.docx
《QC钢筋绑扎间距控制.docx》由会员分享,可在线阅读,更多相关《QC钢筋绑扎间距控制.docx(13页珍藏版)》请在冰豆网上搜索。
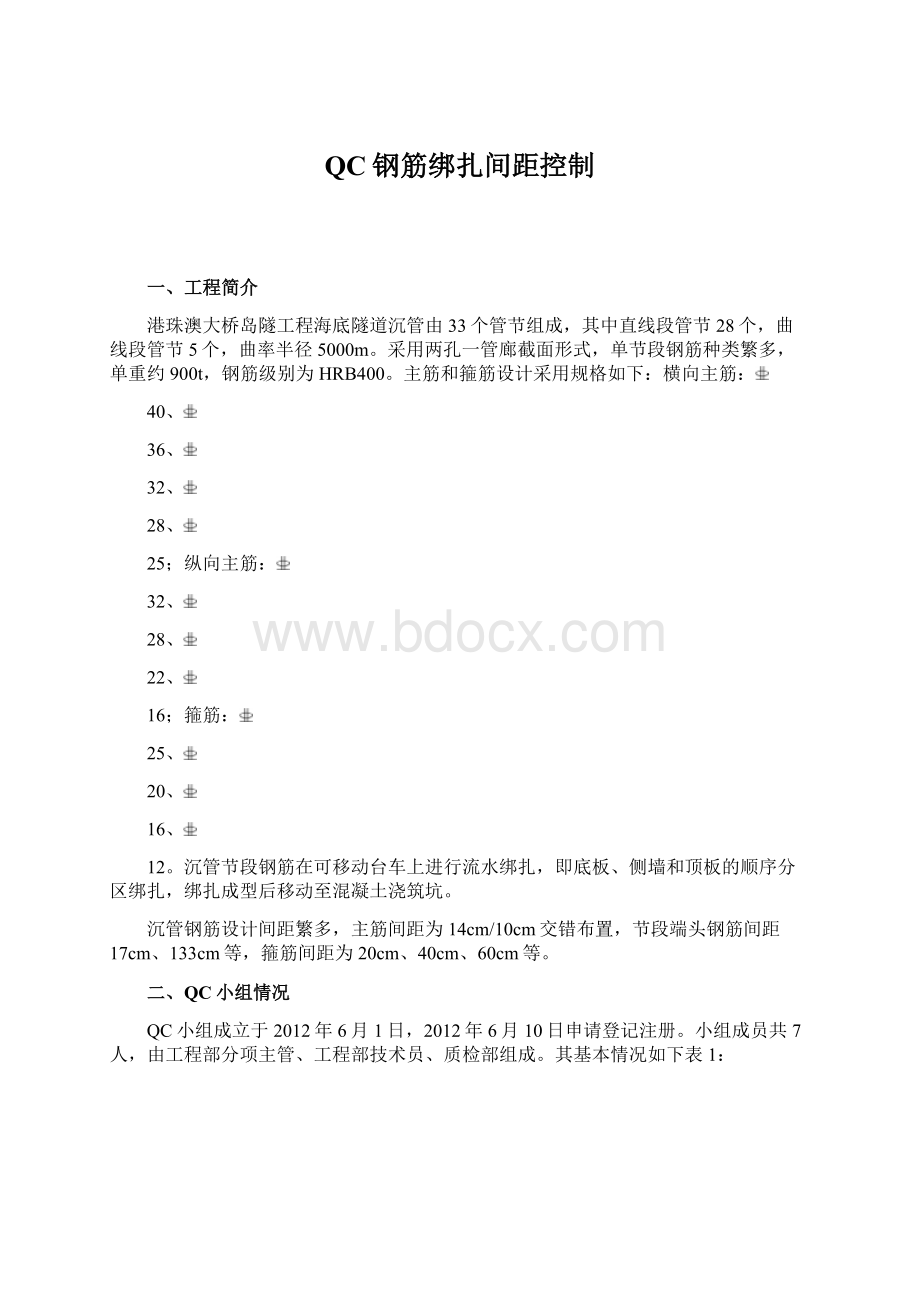
QC钢筋绑扎间距控制
一、工程简介
港珠澳大桥岛隧工程海底隧道沉管由33个管节组成,其中直线段管节28个,曲线段管节5个,曲率半径5000m。
采用两孔一管廊截面形式,单节段钢筋种类繁多,单重约900t,钢筋级别为HRB400。
主筋和箍筋设计采用规格如下:
横向主筋:
40、
36、
32、
28、
25;纵向主筋:
32、
28、
22、
16;箍筋:
25、
20、
16、
12。
沉管节段钢筋在可移动台车上进行流水绑扎,即底板、侧墙和顶板的顺序分区绑扎,绑扎成型后移动至混凝土浇筑坑。
沉管钢筋设计间距繁多,主筋间距为14cm/10cm交错布置,节段端头钢筋间距17cm、133cm等,箍筋间距为20cm、40cm、60cm等。
二、QC小组情况
QC小组成立于2012年6月1日,2012年6月10日申请登记注册。
小组成员共7人,由工程部分项主管、工程部技术员、质检部组成。
其基本情况如下表1:
三、
选题理由
四、现状分析及确定目标
1、现状及主要问题分析
根据沉管足尺模型试验段及E1管节的施工经验,钢筋绑扎间距控制作为最基本的控制项目,但由于钢筋间距数据繁多,误差控制严格,现场实施困难。
通过对两段足尺模型钢筋绑扎质量来看,钢筋间距控制存在较多问题。
钢筋绑扎间距存在的主要问题:
1)底板横向主筋间距(14cm/10cm)
主筋绑扎成等间距
2)底板纵向主筋间距(等间距20cm)
间距为22.5cm,误差+2.5cm,超过允许误差±1cm
3)墙体横向主筋间距(等间距20cm)
间距为16.8cm,误差为-3.2cm,超过允许误差±1cm
4)墙体竖向主筋间距(10cm/14cm)
间距15.8cm,误差+1.8cm,超过允许误差±1cm
钢筋间距作为钢筋绑扎质量控制关键点,对沉管整体受力发挥着极其重要的作用。
通过足尺模型及E1管节施工来看,钢筋绑扎过程中,钢筋间距控制是最简单又是最繁琐的一项任务。
主筋、箍筋及加强钢筋间距过大抑或过小,都会影响沉管预制成品质量评定,与沉管预制总体质量目标不符,需要在钢筋绑扎过程中采取有效措施对间距进行管控。
2、目标确定
为达到沉管预制总体质量目标,铸就120年精品工程,项目部希望通过QC小组对现场钢筋绑扎间距现存的问题进行分析并提出简便有效的解决措施,提高钢筋绑扎质量,全面提高沉管预制总体质量。
根据上述要求,小组确定控制目标如下:
1)技术管理人员熟悉关于钢筋间距控制指标及掌握设计图纸钢筋间距理论数据,并对现场班组长和作业人员进行多次反复交底,提高作业人员质量意识;
2)提出有效简便的操作方法控制钢筋间距;
3)钢筋间距合格率达到90%以上;
五、原因分析
根据足尺模型及E1管节施工及已有的数据资料,多次探讨和现场调研,认真分析问题,并召集相关人员分析讨论,得出钢筋绑扎间距难以控制,间距不符合要求的主要原因。
具体确认情况见表2:
钢筋绑扎间距不符合设计要求的要因确认表表2
序号
类别
原因
确认方法
确认分析
确认人
确认
结果
1
人员
技能水平较差,质量意识不高
现场检查
钢筋绑扎作业人员熟练掌握钢筋安装及绑扎要点,作业班组长进行现场监控,工程技术人员根据设计图纸指导钢筋绑扎。
刘鹏
是
2
作业人员不固定,更换频繁
现场检查
固定钢筋绑扎熟练的作业人员,各绑扎区固定作业班组。
张文森
刘鹏
是
3
材料
钢筋转运导致钢筋弯曲变形
现场检查
钢筋弯曲变形导致绑扎完成后局部位置间距不合格,严格按照钢筋起吊作业方法转运钢筋原材及半成品,并在堆放区域放置平顺
陈科
是
4
施工方法
钢筋铺设流程不合理,间距不合格处不能整改
现场观察
将钢筋绑扎流程形成文字,张贴在展板上,并对作业人员进行详细交底,现场技术人员跟踪指导施工
刘鹏
申昌洲
季亮
是
5
主筋太重,放置不到位或固定不牢靠
现场观察
采用简便设备对特殊位置较重的钢筋进行安装,并通过定位卡槽或定位钢筋固定牢靠
欧志枫
季亮
是
6
机械
桥吊故障
现场检查
防止起重指挥信号不明确而导致钢筋原材或半成品被拉弯
申昌洲
是
7
顶推设备故障
现场检查
加强维修保养,做好一备一用
季亮
是
8
滑移轨道不平顺
现场检查
经常检查,对不平顺处打磨并涂抹润滑剂
欧志枫
是
六、制定对策
针对8条主要原因,小组讨论并确定对策及责任人如下:
对策表表3
序号
要因
对策
目标
措施
责任人
1
技能水平较差,职责分工不清晰,人员更换频繁
做好交底、培训,开展质量展板教育和班前会讲评,固定作业人员
熟练掌握钢筋绑扎技术,提高作业人员质量意识
对所有作业人员组织正式技术交底,在现场质量展板上张贴钢筋绑扎间距设计值及验收标准
张文森
刘鹏
2
钢筋原材及半成品局部弯曲
对起重指挥进行交底,要求起重指令明确
确保钢筋无弯曲,顺直
配置专职司索工,钢筋吊点选择准确,放置处确保钢筋平顺
季亮
陈科
3
钢筋铺设顺序不合理
根据施工方案,严格按照施工流程实施
铺设下一层钢筋,确保上一层钢筋间距合格
对作业人员做好技术交底,现场技术人员实时监控
刘鹏
季亮
4
主筋放置不到位,固定不牢靠
采用轻便设备及卡槽固定钢筋
确保钢筋安装完成后位置不变动
采用滑轮,制作小型起重机安装钢筋,定做卡槽或定位钢筋
刘鹏
季亮
申昌洲
5
顶推设备故障
注重保养,顶推时,设备调试人员随时待命
杜绝设备不正常运作
平时加强顶推设备保养,顶推过程中,设备一旦发生故障,进行调试,防止钢筋笼变形及钢筋间距变形
刘鹏
申昌洲
6
滑移轨道不平顺,摩擦系数大
加强轨道及滑移方钢保养
顶推顺畅,钢筋笼无晃动
顶推钢筋笼前,检查轨道有无障碍物及不平顺的地方,同时涂抹黄油和液压油混合物
季亮
欧志枫
七、实施对策及效果
实施一:
1、钢筋绑扎前,分别对绑扎不同部位钢筋笼的班组进行交底;
2、在现场质量展板上张贴钢筋绑扎技术要求、及钢筋间距技术指标;
3、每天早上召开班前会,反复强调钢筋绑扎关键点,加强作业人员质量意识。
实施效果:
截至E1管节预制完成,底板、墙体、顶板钢筋绑扎区各个班组的作业人员已掌握绑扎要点,钢筋间距设计值及钢筋间距验收标准。
班前会讲评、交底
实施二:
1、加工区划分钢筋加工、原材料存放、半成品堆放区域,制作专门平台进行存放,防止原材和半成品发生变形;
2、原材料及半成品转移时先由司索工了解材料重量选择吊点,作业人员按照选好的吊点进行挂钢丝绳。
实施效果:
钢筋原材和半成品堆放区域进行分块,采用槽钢制作堆放平台,钢筋堆放后顺直,整齐。
选择正确的吊点,在转运过程中,不存在两端或中间变形的情况;
钢筋原材堆放顺直半成品堆放整齐且无变形情况
实施三:
现场已购买简便的起重设备进行,钢筋安装到位,且线条顺直;采购卡槽,对底板、墙体和顶板横向主筋进行定位,纵向主筋和两端头特殊间距钢筋在安装前,预先按照图纸钢筋间距放点,在安装中拉线,保证钢筋线条顺直且间距误差在设计允许范围内。
实施效果:
底板、顶板横向主筋采用卡槽定位中隔墙钢筋制作定位钢筋
侧墙横向主筋定位卡
底板横向主筋间距合格
纵向钢筋、箍筋及端头处钢筋预先放点纵向主筋拉线调整间距
实施四:
滑移轨道及方钢进行定期打磨保养,并在顶推前涂抹黄油和液压油混合物,顶推过程中顺畅,钢筋笼无晃动,确保钢筋间距无变动。
实施效果:
滑移轨道、方钢打磨保养
实施效果:
1.加强了现场技术人员对设计图纸理解,对钢筋绑扎工艺流程更加熟悉,同时作业人员钢筋绑扎技术熟练,质量意识有所提高,整个钢筋笼绑扎质量均有大幅提高;
2.横向主筋、纵向主筋以及端头特殊位置钢筋间距合格率均控制在90%以上,随着作业人员的技术熟练,每个施工步骤所耗时间均减少1/3;
3.顶推设备故障减少、方钢及滑移轨道平顺,顶推时间减少1/4,且顶推完成后钢筋间距均无变化,保证了整个钢筋笼质量;
4.对钢筋绑扎及间距控制施工工艺进行总结,编制技术论文。
八、总结与体会
1.通过此次QC活动,项目部从技术管理人员及具体操作人员的专业技术得到很大提高,钢筋绑扎质量意识产生较大的突破;
2.整个QC小组活动期间,经过组员们的共同努力,解决了沉管钢筋种类和间距设计数据繁多的问题,对沉管受力提供保障,为后续沉管钢筋绑扎质量和效率的提升奠定基础。