干湿法脱硫工艺研究论文.docx
《干湿法脱硫工艺研究论文.docx》由会员分享,可在线阅读,更多相关《干湿法脱硫工艺研究论文.docx(6页珍藏版)》请在冰豆网上搜索。
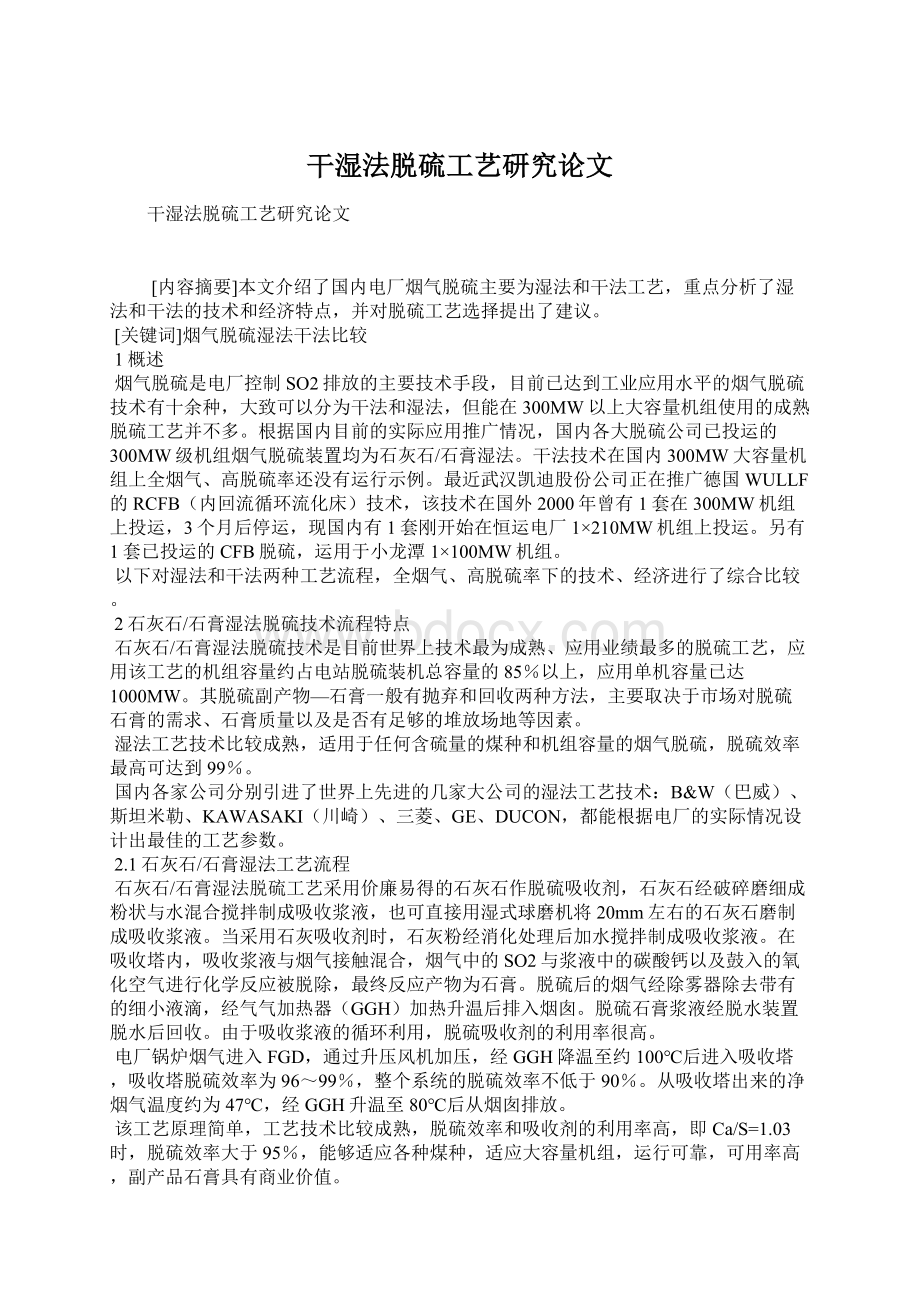
干湿法脱硫工艺研究论文
干湿法脱硫工艺研究论文
[内容摘要]本文介绍了国内电厂烟气脱硫主要为湿法和干法工艺,重点分析了湿法和干法的技术和经济特点,并对脱硫工艺选择提出了建议。
[关键词]烟气脱硫湿法干法比较
1概述
烟气脱硫是电厂控制SO2排放的主要技术手段,目前已达到工业应用水平的烟气脱硫技术有十余种,大致可以分为干法和湿法,但能在300MW以上大容量机组使用的成熟脱硫工艺并不多。
根据国内目前的实际应用推广情况,国内各大脱硫公司已投运的300MW级机组烟气脱硫装置均为石灰石/石膏湿法。
干法技术在国内300MW大容量机组上全烟气、高脱硫率还没有运行示例。
最近武汉凯迪股份公司正在推广德国WULLF的RCFB(内回流循环流化床)技术,该技术在国外2000年曾有1套在300MW机组上投运,3个月后停运,现国内有1套刚开始在恒运电厂1×210MW机组上投运。
另有1套已投运的CFB脱硫,运用于小龙潭1×100MW机组。
以下对湿法和干法两种工艺流程,全烟气、高脱硫率下的技术、经济进行了综合比较。
2石灰石/石膏湿法脱硫技术流程特点
石灰石/石膏湿法脱硫技术是目前世界上技术最为成熟、应用业绩最多的脱硫工艺,应用该工艺的机组容量约占电站脱硫装机总容量的85%以上,应用单机容量已达1000MW。
其脱硫副产物—石膏一般有抛弃和回收两种方法,主要取决于市场对脱硫石膏的需求、石膏质量以及是否有足够的堆放场地等因素。
湿法工艺技术比较成熟,适用于任何含硫量的煤种和机组容量的烟气脱硫,脱硫效率最高可达到99%。
国内各家公司分别引进了世界上先进的几家大公司的湿法工艺技术:
B&W(巴威)、斯坦米勒、KAWASAKI(川崎)、三菱、GE、DUCON,都能根据电厂的实际情况设计出最佳的工艺参数。
2.1石灰石/石膏湿法工艺流程
石灰石/石膏湿法脱硫工艺采用价廉易得的石灰石作脱硫吸收剂,石灰石经破碎磨细成粉状与水混合搅拌制成吸收浆液,也可直接用湿式球磨机将20mm左右的石灰石磨制成吸收浆液。
当采用石灰吸收剂时,石灰粉经消化处理后加水搅拌制成吸收浆液。
在吸收塔内,吸收浆液与烟气接触混合,烟气中的SO2与浆液中的碳酸钙以及鼓入的氧化空气进行化学反应被脱除,最终反应产物为石膏。
脱硫后的烟气经除雾器除去带有的细小液滴,经气气加热器(GGH)加热升温后排入烟囱。
脱硫石膏浆液经脱水装置脱水后回收。
由于吸收浆液的循环利用,脱硫吸收剂的利用率很高。
电厂锅炉烟气进入FGD,通过升压风机加压,经GGH降温至约100℃后进入吸收塔,吸收塔脱硫效率为96~99%,整个系统的脱硫效率不低于90%。
从吸收塔出来的净烟气温度约为47℃,经GGH升温至80℃后从烟囱排放。
该工艺原理简单,工艺技术比较成熟,脱硫效率和吸收剂的利用率高,即Ca/S=1.03时,脱硫效率大于95%,能够适应各种煤种,适应大容量机组,运行可靠,可用率高,副产品石膏具有商业价值。
2.2石灰石/石膏湿法脱硫技术主要技术特点及指标
2.2.1脱硫效率高,一般不低于90%,最高可以达到99%。
2.2.2脱硫剂利用率高,达90%以上。
Ca/S比低,只有1.01~1.05,国内现正在实施的的几个工程均不大于1.03。
2.2.3吸收塔采用各种先进技术设计,不仅解决了脱硫塔内的堵塞、腐蚀问题,而且改善了气液传质条件,从而提高了塔内脱硫效率,减少了浆液循环量,有效降低了浆液循环泵的功耗。
目前脱硫岛电耗一般为机组装机容量的1~1.5%。
2.2.4喷淋空塔内烟气入口采用向下斜切式入口,烟气由下自上流动,延长了气体分布路径,不仅有利于气体分布均匀,而且由于气体的翻腾形成了湍流,更有利于气液的传质传热。
2.2.5采用计算机模拟设计,优化脱硫塔及塔内构件如喷嘴等的布置,优化浆液浓度、Ca/S比、浆液流量等运行指标,可以保证脱硫塔内烟气流动和浆液喷淋均匀,以最小的消耗取得最好的脱硫效果。
2.2.6根据烟气含硫量,采用不同层数(2~4层)的浆液喷淋层,确保取得最佳的脱硫效果。
2.2.7塔内设置氧化空气分布系统,采用塔内强制氧化,氧化效果好。
2.2.8喷淋层采用交叉联箱布置,使喷淋管道布置更合理,降低了吸收塔高度。
2.2.9采用机械搅拌。
2.2.10废物得到良好的处理,其中废渣变成了优质石膏,完全可以取代高品位的天然石膏。
废水采用回用技术,可以达到零排放。
2.2.11稳定性高,适应性强,可靠性99%以上。
2.2.12应用多、运行经验丰富。
3干法RCFB脱硫工艺脱硫技术流程特点
干法有LIFAC(炉内喷钙尾部增湿活化)、CFB(循环流化床)等工艺,在国家有关部门的技术指南、火电厂设计规程上均限于在中小机组或老机组上实施。
CFB最早由德国鲁奇(LURGI)公司开发,目前已达到工业应用的CFB法工艺有三种:
LURGI公司的CFB、德国WULFF公司的RCFB(内回流式烟气循环流化床)、丹麦FLS公司的GSA(气体悬浮吸收),国内分别由龙净环保、凯迪电力、龙源环保等公司引进,目前多在中小机组上运用,其中只有WULFF公司的RCFB技术向300MW机组上推广,所以本文中作比较的干法仅指RCFB。
3.1RCFB的发展历史
循环流化床(CFB)的发展历史其实很长。
循环流化床CFB烟气净化工艺的实验室技术研究开发工作开始于1968/1969年,1970~1972年CFB烟气净化工艺在德国电解铝厂获得应用,烟气流量为15,000m3/h。
1985~1987年,首台CFB烟气脱硫示范装置在德国一家燃褐煤电站得到应用,处理烟气量为40万m3/h(相当于30万机组气量的四分之一),采用消石灰为脱硫剂。
在此基础上,各公司分别又开发出了上述新一代CFB脱硫工艺(第三代)。
3.2RCFB脱硫工艺流程
RCFB工艺主要采用干态的消石灰粉作为吸收剂,由锅炉排出的烟气从流化床的底部进入,经过吸收塔底部的文丘里装置,烟气速度加快,并与很细的吸收剂粉末相混合。
同时通过RCFB下部的喷水,使烟气温度降低到70~90℃。
在此条件下,吸收剂与烟气中的二氧化硫反应,生成亚硫酸钙和硫酸钙,经脱硫后带有大量固体的烟气由吸收塔的上部排出,排出的烟气进入除尘器中,大部分烟气中的固体颗粒都被分离出来,被分离出来的颗粒经过再循环系统大部分返回到吸收塔。
RCFB的控制系统主要通过三个部分实现:
1.根据反应器进口烟气流量及烟气中原始SO2浓度控制消石灰粉的给料量;
2.反应器出口处的烟气温度直接控制反应器底部的喷水量,使烟温控制在70~90℃范围内。
喷水量的调节方法一般采用回流调节喷嘴,通过调节回流水压来调节喷水量;
3.在运行中调节床内的固/气比。
其调节方法是通过调节分离器和除尘器下所收集的飞灰排灰量,以控制送回反应器的再循环干灰量,从而保证床内必需的固/气比。
3.3RCFB脱硫技术的主要技术特点及指标
3.3.1耗电量在机组容量的0.5~1.0%。
脱硫率80%时,为0.6%左右;脱硫效率大于90%时,塔内物料量增加引起系统阻力的增大而使电耗大幅上升。
3.3.2在塔的顶部区域加装了导流板,在塔内加装了紊流装置。
3.3.3脱硫率>90%,Ca/S为1.2~1.5。
石灰活性必须高且稳定,达到T60标准(软缎石灰,四分钟内水温上升60℃)。
3.3.4塔内平均流速4m/s左右。
10米左右直径的流化床内流场比较复杂。
3.3.5用消石灰作为脱硫剂。
石灰消化后,以消石灰干粉形式送入流化床吸收塔。
喷入足够的水分保证脱硫效果,水分越大脱硫率越高。
3.3.6严格控制床温。
床温偏低时设备有腐蚀,偏高时脱硫效率及脱硫剂利用率下降。
3.3.7塔内的水分要迅速蒸发掉,以保证灰渣干态排出。
3.3.8在煤的含硫量增加或要求提高脱硫效率时,不增加任何设备,仅增加脱硫剂和喷水量。
3.3.9不另设烟气旁路,当FGD停运时,脱硫塔直接作为烟气旁路使用。
3.3.10在中小电站或工业锅炉上应用较多,300MW机组上国内外仅应用了1套并只有短期运行的经验。
3.3.11RCFB脱硫渣的利用
RCFB烟气脱硫技术吸收剂为钙基化合物,脱硫渣中的主要成分为CaSO3等。
但不同电厂的脱硫渣的成份是不一样的,若要有效利用,必须做个案研究。
不包括前除尘器的灰,CaSO3·1/2H2O含量占50±10%,根据德国WULFF公司提供的部分个案研究实例,是可以应用的。
国内的南京下关电厂对LIFAC技术的脱硫渣已作了一些个案研究,恒运电厂正准备和凯迪公司合作,开展脱硫灰利用的研究工作。
4石灰石-石膏湿法与干法RCFB比较
4.1工艺技术比较
4.1.1在300MW以上机组FGD上的应用
干法RCFB:
国外从小机组放大到300MW机组仅有1台,国内还没有300MW机组的实运装置,仅在中小机组或工业锅炉上有实运装置。
从国内引进FGD的经验来看,各个电厂都有一定的实际情况,设计时也必须满足各个电厂的特定情况。
据报道,几家引进CFB的公司在中小机组的示范装置上大多碰到了较严重的问题,经大量长时间调试整改后,有的仍达不到设计要求,有的甚至需更换重要部件,更为严重的机组无法按正常出力运行。
国内唯一的一套RCFB是广州恒运电厂FGD,从运行情况来看,虽然将石灰标准从T60降至T50左右,消化装置仍不能正常运行,目前靠买消石灰维持;除尘器有堵塞等问题,曾造成了电厂停运,但粉尘泄漏较严重;控制系统还不能稳定监测和调控脱硫装置的运行。
石灰石-石膏湿法:
已很成熟,国外有各种条件下机组上的运行经验,国内虽然运行实例不多,但国内公司引进的均为国外先进可靠的技术。
其市场占有率占电站脱硫装机总容量的85%以上,应用单机容量已达1000MW。
国家相关职能部门在组织国内专家充分调研的基础上,提出指导性意见:
在新、扩、改300MW机组FGD上或要求有较高脱硫率时,采用石灰石-石膏湿法技术。
在火电厂设计技术规程中,也作了同样的规定。
现在大部分设备均可以实现国产化,初始投资大幅降低,备品备件的问题也将得到彻底解决。
4.1.2适用煤种
干法RCFB:
据国内各大研究单位的报告及国外的部分应用实例,CFB适用于中、低硫煤。
对高硫煤,较难达到环保要求,且投资与运行费用将大幅上升。
RCFB是否适应高硫煤的大机组,需进一步论证。
石灰石-石膏湿法:
不限。
4.1.3Ca/S比
干法RCFB:
脱硫率>90%时为1.3~1.5。
氧化钙纯度要求≥90%,并要有非常高的活性(T60标准),达不到以上要求时,将影响装置的脱硫率及正常运行。
石灰石-石膏湿法:
1.01~1.05,一般为1.03,纯度达不到要求时,最终仅影响脱硫副产品石膏的质量。
4.1.4脱硫效率
干法RCFB:
稳定运行一般在80%左右,若需要进一步提高,则需降低烟气趋近温差,增加Ca/S和喷水量,但会对下游设备如除尘器、引风机等带来不利影响。
95%的脱硫率对干法技术来讲,已达到高限(国外为90%),当环保要求进一步提高时,改造较困难。
烟气含硫量波动时,因为有大循环灰量,难以灵敏调整控制,脱硫效率难以保证。
石灰石-石膏湿法:
一般可在95%以上稳定运行,对环保要求的适应性强。
烟气含硫量变化时,易于调整控制,脱硫效率较稳定。
4.1.5耗电量
干法RCFB:
机组容量的0.5~1.0%,脱硫效率在80%左右时,为0.6%左右;当脱硫效率>90%时,耗电量上升很快,将达到1%左右。
石灰石-石膏湿法:
机组容量的1.0~1.5%。
.1.6对ESP(电除尘器)的影响
干法RCFB:
初始设计时ESP2负荷很高,进口浓度800g/Nm3(远高于电厂正常电除尘器进口的20~30g/Nm3),ESP2除尘效率将达到99.9875%。
随脱硫率的变化增加Ca/S,ESP2负荷急剧增加,其出口含尘浓度能否达标值得考虑。
环保要求还将进一步提高,在即将实行的《火电厂污染物排放标准》(征求意见稿)中,火电厂最高允许烟尘排放浓度为50mg/Nm3。
当烟气含硫量变化时,为保证脱硫率,或满足环保要求的不断提高而提高脱硫效率,采取以上降低烟气趋近温差,增加喷水量和Ca/S措施时,将导致ESP低温腐蚀,排灰易粘结(塔壁也易于结灰),严重时,将影响装置的正常运行,在中小机组的运行中是普遍存在的问题。
石灰石-石膏湿法:
没有后ESP,无影响。
经脱硫塔洗涤后,烟尘总量减少50~80%左右,FGD出口烟尘浓度小于50mg/Nm3。
4.1.7对机组的影响
干法RCFB:
因故障停电等原因使CFB停运,会导致塔内固态物沉积,重新启动需清理沉积固态物,由于无旁路,当后ESP和回灰系统发生堵塞进行检修时,机组将停运。
石灰石-石膏湿法:
因FGD是独立系统,有旁路,故无影响。
4.1.8对机组负荷的适应性
干法RCFB:
负荷的变化会引起烟气流速的变化,从而影响脱硫反应及装置的运行。
石灰石-石膏湿法:
较好。
4.1.9水
干法RCFB:
石灰消化一般需热水,且水质要求高;无废水排放。
石灰石-石膏湿法:
耗水量相对稍多一点,但水质要求不高,可用水源水;仅有少量废水排放。
4.1.10吸收剂制备
干法RCFB:
需大批量外购符合要求的T60标准的石灰粉,以目前投运电厂的运行情况来看,石灰消化存在诸多问题,如果采购满足要求的消石灰Ca(OH)2将增加业主采购成本。
最大问题是一般较难购买到品质稳定的高活性(T60标准)的石灰粉。
RCFB脱硫效果的保证及装置的运行可靠性完全依赖于石灰的高纯度及高活性。
石灰石-石膏湿法:
可外购石灰石粉或块料,石灰石块料价格便宜,直接购粉则可大幅度降低投资及耗电量,但相应增加了采购成本。
4.1.11排烟温度
干法RCFB:
脱硫率80%左右时为70~90℃,脱硫率提高到95%后要降55~70℃。
石灰石-石膏湿法:
GGH出口一般为大于80℃。
4.1.12副产品输送利用
干法RCFB:
目前仅适宜用于填坑、铺路,应用价值低。
用于其他场合的应用方法还未研究,而且还将是很长一段过程。
灰易产生粘结,既影响输送,也影响装置的运行。
当脱硫渣排入灰场时,将影响粉煤灰的综合利用。
在抛弃过程中需要考虑增设合适的储运设施,同时也增加一定的运输和储存成本。
石灰石-石膏湿法:
脱硫石膏质量优于天然石膏,可综合利用,应用价值较高。
如采用抛弃法,可节省部分投资,输送也不会有问题。
4.1.13占地面积
干法RCFB:
在大容量机组考虑采用1炉1塔时占地较小。
石灰石-石膏湿法:
较大。
4.2经济比较
以下以某电厂2×300MW机组烟气脱硫装置为例,脱硫项目建设期按1年计算,运营期按20年计算,采用总费用法对干、湿法方案进行经济比较,总费用低的方案较优。
从“经济比较成果表”可以看出,湿法脱硫方案的总费用略低于干法脱硫方案。
因此,从经济比较的角度来看,湿法方案优于干法方案。
5结论和建议
5.1结论
综上所述,湿法与干法相比,技术更加成熟,运行经验更加丰富,脱硫剂供应有保证,脱硫副产品利用好,系统供应商较多;经营费用小,初始投资高,总成本费用较低,全系统本厂占地面积较大。
每个电厂有各自的实际情况,在FGD装置设计上也有不同。
方案比选中不仅要考虑干法、湿法的技术因数,还要考虑各种实际存在的问题:
如脱硫剂的供应、废渣的处理、对环境变化的适应、政府的规划等。
目前干法烟尘排放量要大于100mg/Nm3,湿法小于50mg/Nm3,均小于现行环保排放标准200mg/Nm3的要求。
如果环保政策要求进一步提高脱硫效率,降低出口允许烟尘排放浓度,湿法也比较容易调整改造,而干法效率已到高限,难以实施进一步改造。
5.2建议
湿法脱硫工艺是目前世界上应用最多、最为成熟的技术,吸收剂价廉易得、副产物便于利用、煤种适应范围宽,并有较大幅度降低工程造价的可能性。
对大容量机组,从技术的成熟性、可靠性以及环保的高要求考虑,应采用石灰石/石膏湿法。
RCFB工艺脱硫效率较高,建设投资较省,占地面积较少,在能满足高品位石灰供应并妥善处理脱硫灰的条件下,具有较好的发展前景,主要适用于中小机组和老机组的脱硫改造。