焊接检验指导书.docx
《焊接检验指导书.docx》由会员分享,可在线阅读,更多相关《焊接检验指导书.docx(16页珍藏版)》请在冰豆网上搜索。
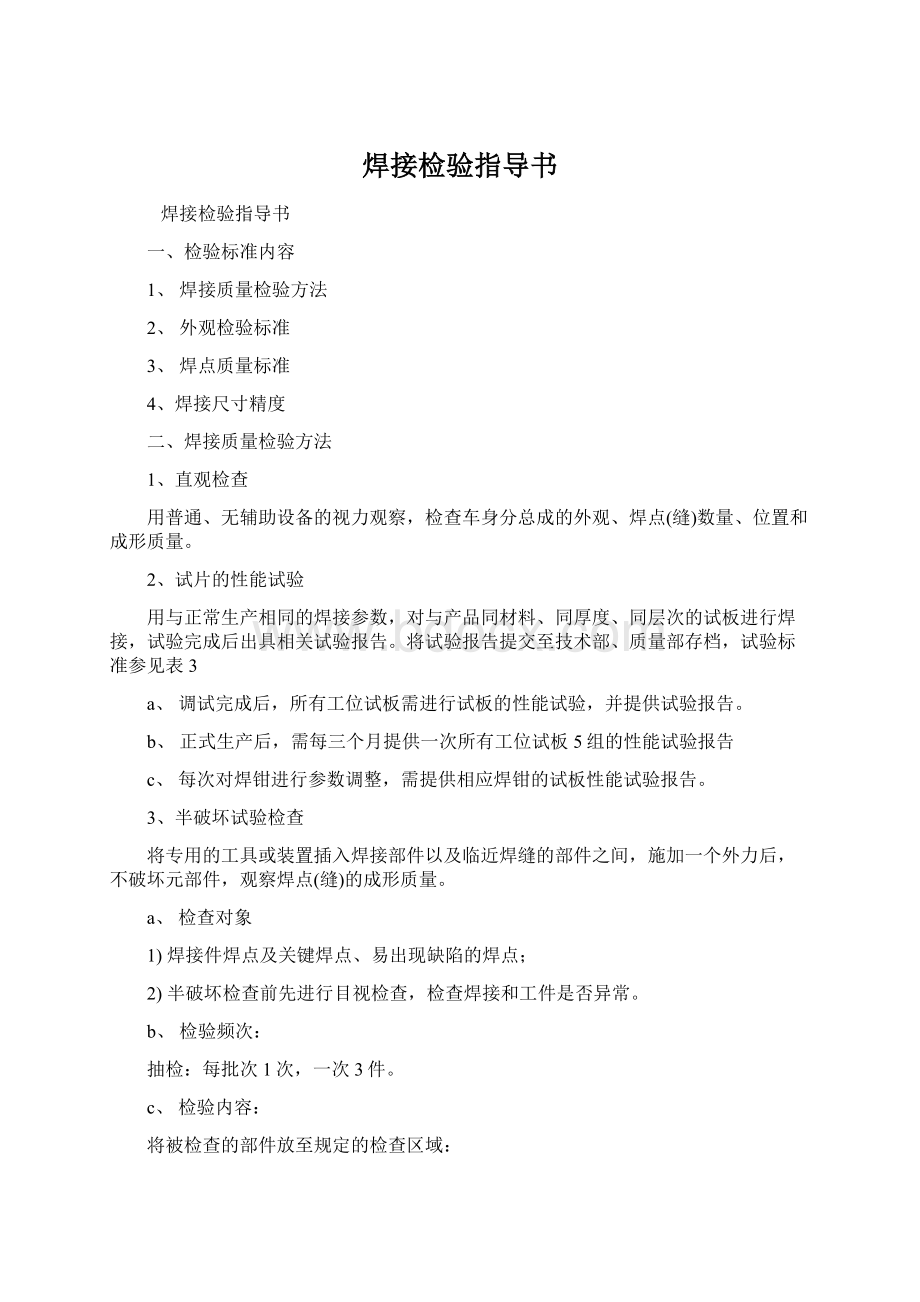
焊接检验指导书
焊接检验指导书
一、检验标准内容
1、焊接质量检验方法
2、外观检验标准
3、焊点质量标准
4、焊接尺寸精度
二、焊接质量检验方法
1、直观检查
用普通、无辅助设备的视力观察,检查车身分总成的外观、焊点(缝)数量、位置和成形质量。
2、试片的性能试验
用与正常生产相同的焊接参数,对与产品同材料、同厚度、同层次的试板进行焊接,试验完成后出具相关试验报告。
将试验报告提交至技术部、质量部存档,试验标准参见表3
a、调试完成后,所有工位试板需进行试板的性能试验,并提供试验报告。
b、正式生产后,需每三个月提供一次所有工位试板5组的性能试验报告
c、每次对焊钳进行参数调整,需提供相应焊钳的试板性能试验报告。
3、半破坏试验检查
将专用的工具或装置插入焊接部件以及临近焊缝的部件之间,施加一个外力后,不破坏元部件,观察焊点(缝)的成形质量。
a、检查对象
1)焊接件焊点及关键焊点、易出现缺陷的焊点;
2)半破坏检查前先进行目视检查,检查焊接和工件是否异常。
b、检验频次:
抽检:
每批次1次,一次3件。
c、检验内容:
将被检查的部件放至规定的检查区域:
1)清点焊点个数;
2)检查焊点位置;
3)检查是否存在不可接受的焊点。
d、检验方法:
对焊缝中具有特征代表性的焊接点进行检验,将专用凿子和锤子进行在离焊点规定处插入一定的深度(与被检查焊点内端齐平),到达要求的尺寸范围后,上下扳动凿子,直到焊接点材料屈服或严重弯曲,检查焊点是否松动。
f、检验注意事项:
1)如果发现有焊点拉长而焊缝无断裂或损坏,应停止检验。
对于两个以上工件之间的焊缝,应在每对相邻工件之间进行检验。
对于两端焊点,必须检验。
2)当进行半破坏检查时应注意:
别让凿子接至焊接部位,这可能会导致衔接部位被切断;
3)当进行半破坏检查时,插入凿子的位置和深度做如下要求:
A=1.0mm~2.0mm(尽量同焊接部位靠近),B=5.0mm以上。
半破坏检查的操作示意图;
4)拔出凿子,用0.5~1镑锤子还原零件。
5)半破坏焊点检查的数量,不少于焊接焊点总量的30%。
g、记录
1)如发现有异常焊点,在相应的焊点上做好异常状态记录,并将结果记录在《检验记录单》,并执行焊接质量问题处理流程
2)缺陷焊点数量超过总数的1%,则焊接质量不合格。
h、修复
1)破坏检查完成后在零件上标出标识,并在规定的区域存放,存放时间为半个工作日,到期后对检查部位加以(修正)点焊补焊后使用;
2)焊点有损坏的,应用CO2焊补焊处理。
如果有缺陷,应按照指定方案修理并重新进行检查或者报废。
注1:
下列焊点不适于进行半破坏检查:
1)凿子无法达到的焊点;
2)外表面,平整度要求较高的焊点(包括铜板焊接)。
4、破坏试验检查
由专业人员用专用的工具或装置插入焊接部件以及临近焊缝的部件之间直到元部件彻底分离,观察焊点(缝)的成形质量。
a、检查对象
焊接件焊点及关键焊点、易出现缺陷的焊点。
b、检验频次:
在正常批量生产过程中,现场加工的所有焊缝应按检验周期(见下表1)进行破坏性检验。
序号
每周生产数量
频次
备注
1
1-500
1次/2000
1次3件
2
501-1500
1次/3000
1次3件
3
1501-3000
1次/3000
1次3件
4
3001-6000
1次/3000
1次3件
5
6001-10000
1次/3000
1次3件
c、检验内容:
破坏检查前先进行目视检查,检查焊接和工件是否异常。
将被检查的部件放至规定的检查区域:
a)清点焊点个数;
b)检查焊点位置;
c)检查是否存在不可接受的焊点。
对焊缝中具有特征代表性的焊接点进行检验,将专用凿子或液压扩力钳对工件进行破检,工件撕裂要求在分离后的任意一个工件上焊接处形成一个圆孔,另一个上形成一个圆凸台,且焊点直径符合表3的规定,见表3。
如果两个工件上孔径小于标准,表示点焊试件不合格。
并将结果记录在《检验记录单》。
d、记录
a)如发现有异常焊点,在相应的焊点上做好异常状态记录,并将结果记录在《检验记录单》,并执行焊接质量问题处理流程。
b)缺陷焊点数量超过总数的1%,则焊接质量不合格。
三、外观检验标准
表2外观检验标准
序号
检查项目
检查方式
检验工具
检验标准
1
表面清洁
目视
不允许有记号笔痕、油污(允许少量浮油)、残胶
不允许有目视可见铁屑、灰尘等异物
2
圆弧,棱线
目视
不允许明显的轮廓不清晰
3
划伤碰伤
目视手感
不允许零件表面明显划伤
4
凸包/凹坑
目视手感
油石
不允许目视可见、手感明显的凸包凹坑
5
麻点群
目视手感
油石
无手感明显的麻点(群)
6
材料缺陷
目视测量
游标卡尺
不允许
7
锈蚀
目视
不允许明显目视可见的锈斑
8
间隙
目视测量
间隙尺
间隙不得超过0.8mm
9
裂纹
目视
不允许
10
错位
目视测量
游标卡尺
不允许明显可见装配错位
11
变形
目视
检具
不允许
12
打磨纹
目视手感
油石
不允许
13
缺胶
目视
按照工艺标准检查,不允许缺胶
14
错焊、漏焊
目视
不允许
15
其它
不允许有影响整车安全性能及明显影响整车外观的缺陷
四、焊点质量标准
1、点焊:
a、焊点外观质量:
焊点表面呈圆形或椭圆形,焊点数量、位置、尺寸应符合产品图样或工艺文件的要求,焊点目视无裂纹、气孔、脱焊、烧穿、过烧等缺陷;
b、焊点直线度:
焊点直线度之差左右位移量不大于3mm,
c、压痕深度:
不可大于板厚的20%;如果两工件的厚度比大于2:
1,压痕深度可增大到20%~25%,任何压痕要抛光处理;
d、焊透率:
应为30-80%。
e、焊点熔核直径:
工艺规程未注明焊点熔核直径的,根据表2检验,焊点直径误差允许-1~+2mm。
f、焊点强度:
焊点抗剪强度要求见表3;
g、焊点间距/边距:
工艺规程未注明焊点边距和焊点间距的,根据表4检验,焊点须均布,焊点间距之差为±5mm,但不得积累。
当最后一个焊点间距不能满足要求时(间距过大或过小)须进行调节保证焊点均布,间距Ha>3d(d为核心直径)。
h、焊点数量:
符合该工位《焊装标准作业指导书》的要求,工艺文件中规定的某个焊接边的焊点数为5个或者更少时,不允许出现有缺陷焊点或少焊点;工艺文件中规定的某个焊接边的焊点数为6个或者更多时,允许的缺陷焊点数量和多余的焊点数量见下表5。
i、如果一条焊接边允许有两处或者两处以上的缺陷焊点,那么缺陷焊点间应至少有一个好的焊点间隔,才可以看作合格;焊缝末尾的焊点不得有缺陷。
表3焊点熔核直径及焊点抗剪强度要求
序号
板厚(mm)
熔核直径(mm)
抗剪强度(kN/点)
焊透率
1
0.8+0.8
4.5
≥4.0
注:
1、焊透率应为30-80%。
2、二层点焊应按簿板计算。
3、薄板与厚板焊接,按薄板计算,多层点焊分别按现两外层板计算。
2
1.0+1.0
5
≥5.4
3
1.2+1.2
5.5
≥6.8
4
1.5+1.5
6
≥9.3
5
1.6+1.6
6.3
≥10.9
6
1.8+1.8
6.7
≥11.4
7
2.0+2.0
7.1
≥13.7
8
2.5+2.5
7.9
≥17.7
9
3.0+3.0
8.1
≥18.5
表4点焊板厚与焊点位置要求
板厚δ(mm)
最小点距e(mm)
边距b(mm)
备注
0.5
10
>4.5
0.8
12
>5.0
1.0
12
>6.0
1.2
14
>6.5
1.5
14
>7.0
2.0
16
>8.0
2.5
18
>9.0
3.0
20
>10.0
表5有效焊点数量要求
规定的焊点数
有效焊点数Min
实施焊点数MAX
1-5
n
n
6-10
n-1
n+1
11-20
n-2
n+2
21-30
n-3
n+3
31-40
n-4
n+4
41以上
(1-12%)×n
(1+12%)×n
表6点焊缺陷判断
序号
检查项目
图示
检查方式
检验工具
检验标准
1
拉痕
目视测量
1、钢板被拉超过紧靠焊点周围的厚度的两倍,就判定该焊点有缺陷。
2、缺陷焊点数不得大于10%
2
扭曲
目视测量
1、母材扭曲变形超过焊接面30度
2、缺陷焊点数不得大于10%
3
咬边
目视
1、焊点不得超过焊接钢板的边缘
2、缺陷焊点数不得大于10%
4
脱离
目视测量
1、脱离的焊点部位不能超过焊点直径的1/3;
2、对于棱角、圆角部位,不容出现脱离正确位置的焊点。
3、缺陷焊点数不得大于10%
5
飞溅(焊接面上焊接液呈毛刺状)
目视测量
1、S=从熔核直径超过2.0mm以上的为不良
2、e=从熔核直径超过5.0mm以上的为不良
3、不允许超过总点数的15%
6
压痕过深
目视测量
1、被电极压的深度为较薄板的70%以下时,但要求钣金的外部压锻为90%以下时判为压痕过深
2、不允许超过总点数的20%
7
焊接痕迹
A:
窄处B:
宽处
目视测量
1、A/B<0.8的情况为不良
2、不允许超过总点数的20%
序号
检查项目
图示
检查方式
检验工具
检验标准
8
焊后
孔洞
目视测量
1、孔洞直径D=1.5mm以上为不良
2、D≤1.5mm的情况下不允许超过总点数的5%
9
虚焊
半破坏试验/破坏试验
扁铲、锤子
1、无熔核或熔核过小,按表3检验
2、缺陷焊点数量超过1%
10
焊穿
目视
缺陷焊点数不得大于10%
11
漏焊
目视
缺陷焊点数不得大于10%
12
开裂
目视
开裂焊点数不得大于1%
13
焊偏
目测
焊偏数≤10%,偏离位置小于等于3mm。
缺陷焊点数不得大于10%
2、凸焊
a、外观质量:
无螺纹损伤、裂纹,允许有轻微飞溅和少量的金属挤出,但不影响螺栓拧入;不允许有漏焊、错焊、未焊透、焊接变形等缺陷。
b、凸焊螺母螺栓抗扭强度应符合要求,若不合格必须重新凸焊,或用CO2保护焊加固;
c、关键零件凸焊螺母不允许有裂纹,一般零件凸焊螺母若有裂纹,允许用CO2保护焊补焊;
d、检验方法说明:
1)螺母螺纹检验法:
选用与工件上凸焊螺母相配的螺纹螺栓,要求不能借用任何工具,直接用手能将螺纹螺栓顺利拧入螺母孔内,则为合格;反之螺纹螺栓或拧入困难,则为不合格。
2)螺栓螺纹检验法:
选用与工件上凸焊螺栓相配的螺纹螺母,要求不能借用任何工具,直接用手能将螺纹螺母顺利拧入螺栓上,则为合格;反之螺纹螺母不或拧入困难,则为不合格。
3)产品强度检验:
将工件固定在工作台上,把扭力扳手上的专用套筒套在螺母及螺栓上,用手扳动扭力扳手。
如工件上螺母及螺栓承受规定的扭力而不脱落,则为合格;如试片上螺母及螺栓承受的扭力未达到要求或达到要求后脱落,则为不合格。
表7螺母凸焊抗扭强度参数:
螺母