金属腐蚀理论7.docx
《金属腐蚀理论7.docx》由会员分享,可在线阅读,更多相关《金属腐蚀理论7.docx(19页珍藏版)》请在冰豆网上搜索。
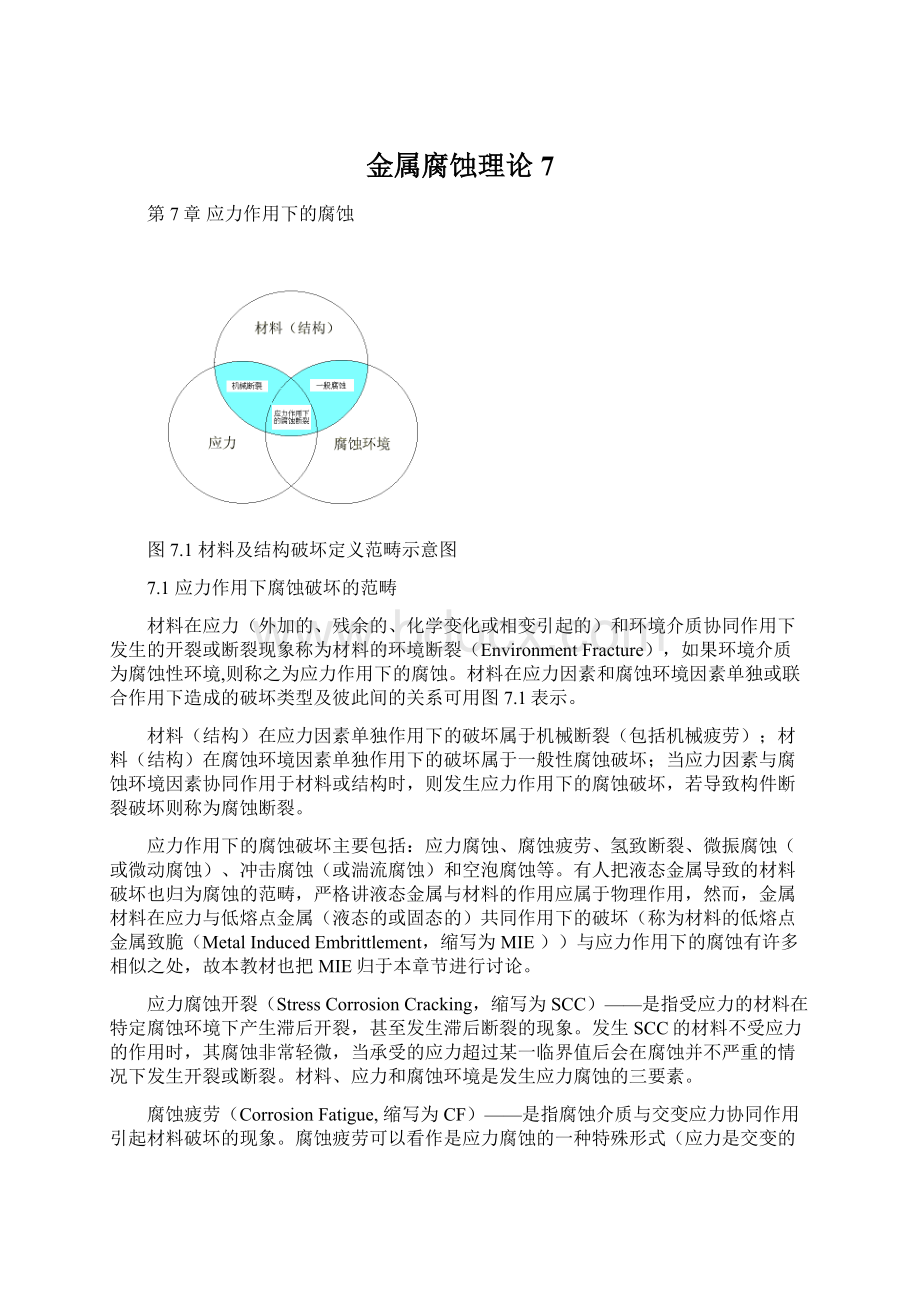
金属腐蚀理论7
第7章应力作用下的腐蚀
图7.1材料及结构破坏定义范畴示意图
7.1应力作用下腐蚀破坏的范畴
材料在应力(外加的、残余的、化学变化或相变引起的)和环境介质协同作用下发生的开裂或断裂现象称为材料的环境断裂(EnvironmentFracture),如果环境介质为腐蚀性环境,则称之为应力作用下的腐蚀。
材料在应力因素和腐蚀环境因素单独或联合作用下造成的破坏类型及彼此间的关系可用图7.1表示。
材料(结构)在应力因素单独作用下的破坏属于机械断裂(包括机械疲劳);材料(结构)在腐蚀环境因素单独作用下的破坏属于一般性腐蚀破坏;当应力因素与腐蚀环境因素协同作用于材料或结构时,则发生应力作用下的腐蚀破坏,若导致构件断裂破坏则称为腐蚀断裂。
应力作用下的腐蚀破坏主要包括:
应力腐蚀、腐蚀疲劳、氢致断裂、微振腐蚀(或微动腐蚀)、冲击腐蚀(或湍流腐蚀)和空泡腐蚀等。
有人把液态金属导致的材料破坏也归为腐蚀的范畴,严格讲液态金属与材料的作用应属于物理作用,然而,金属材料在应力与低熔点金属(液态的或固态的)共同作用下的破坏(称为材料的低熔点金属致脆(MetalInducedEmbrittlement,缩写为MIE))与应力作用下的腐蚀有许多相似之处,故本教材也把MIE归于本章节进行讨论。
应力腐蚀开裂(StressCorrosionCracking,缩写为SCC)——是指受应力的材料在特定腐蚀环境下产生滞后开裂,甚至发生滞后断裂的现象。
发生SCC的材料不受应力的作用时,其腐蚀非常轻微,当承受的应力超过某一临界值后会在腐蚀并不严重的情况下发生开裂或断裂。
材料、应力和腐蚀环境是发生应力腐蚀的三要素。
腐蚀疲劳(CorrosionFatigue,缩写为CF)——是指腐蚀介质与交变应力协同作用引起材料破坏的现象。
腐蚀疲劳可以看作是应力腐蚀的一种特殊形式(应力是交变的);也可看成是特殊环境(腐蚀介质)下的疲劳。
为了突出腐蚀疲劳的特殊性,故应力腐蚀狭义上仅指受静应力或非常缓慢变化应力作用下的腐蚀破坏。
氢脆(HydrogenEmbrittlement,缩写为HE)或氢损伤——是指进入材料内部的氢导致材料性能的退化现象,包括氢压引起的微裂纹(钢中白点、焊接冷裂纹、H2S或酸中浸泡裂纹)、高温高压氢腐蚀、氢化物相或氢致马氏体相变、氢致塑性损失及氢致开裂或断裂。
微动腐蚀(FrettingCorrosion,缩写为FC)——是指在有氧气或其它腐蚀介质存在的条件下,沿着受压载荷而紧密接触的界面上有轻微的振动或微小振幅的往返相对运动,导致在接触面上出现小坑、细槽或裂纹,称之为微动腐蚀。
这种腐蚀现象涉及到二个单元过程:
冷焊、局部断裂和氧化。
大多数金属表面都有一层氧化膜,某些微小凸起部分的氧化膜在高压应力的摩擦下局部破裂,暴露出的新鲜金属表面或者重新氧化,或者发生冷焊,接触面的相对位移使氧化膜或冷焊区局部破裂,这些基本过程循环进行就产生了微动腐蚀,其结果一是导致以磨损为主的破坏(FrettingWear,微动磨损),二是导致以裂纹萌生和扩展为主的疲劳断裂破坏(FrettingFatigue,微动疲劳),具体破坏形式依赖于工况条件。
冲击腐蚀(ImpingementAttack)——是指金属表面与腐蚀流体之间由于高速相对运动而引起的金属破坏现象。
冲击腐蚀时,金属的腐蚀产物因受高速流体的冲刷而离开金属表面,从而使新鲜的金属表面与腐蚀介质直接接触,加速了腐蚀破坏。
空泡腐蚀(Cavitation)——是指由于水轮机叶片、船舰推进器等在高速转动时所引起的流体压力分布不均匀,在低压区的某些金属表面形成流体的空泡,随后这类空泡破裂,产生高压冲击波(压力可达40MPa),加速构件表面破坏的现象。
空泡破裂产生的冲击波可产生如下三种效应:
使软的金属表面发生高速形变;使韧性差的金属表面层剥落;损坏金属表面的保护膜,促进腐蚀。
应力作用下的腐蚀导致的工程结构破坏危害到航空、航天、能源、国防、石油、化工、海洋开采、船舶、交通、建筑等诸多行业,造成了巨大的经济损失和灾难性后果,这方面的例子不胜枚举,仅以航空领域为例,就曾造成了众多起灾难性事故:
1980年11月,我国一架直升机由于1号桨叶大梁因腐蚀疲劳折断而导致飞机空中解体。
1982年9月17日,日航的一架DC—8客机在上海虹桥机场着陆时,突然冲出了跑道,飞机损坏,乘客受重伤。
事故分析的原因是飞机内一个高压气瓶内壁存在应力腐蚀裂纹,飞机刹车操纵时气瓶突然爆破,破坏了液压系统,使全部刹车失灵。
1985年8月,日航一架747客机由于机身增压舱端框应力腐蚀断裂而坠毁,机上524人全部遇难。
1988年4月28日美国一架波音737-200客机在夏威夷上空因机身蒙皮发生应力腐蚀和腐蚀疲劳等破坏,造成机体上部大面积蒙皮和结构飞掉,一名空中小姐被吸出机身,多名机上人员受重伤。
因此,研究材料、机械设备和结构在应力作用下腐蚀破坏的特征、规律、机理和破坏分析与诊断方法,在此基础上提出和实施合理而有效的预防技术措施,对于确保机械设备的安全性和可靠性意义重大。
7.2应力腐蚀开裂
人们较早对应力腐蚀破坏的认识可追溯到19世纪后期黄铜弹壳的“季裂”现象,即黄铜弹壳在夏季季风期贮存过程中,因潮湿空气中含有腐蚀性氨离子和弹壳制造过程中引入的残余应力联合作用导致弹壳的应力腐蚀开裂破坏。
同一时期还发现了黄铜冷凝管的应力腐蚀开裂和蒸汽锅炉的“碱脆”现象(锅炉中碱性水环境与应力联合作用引起的应力腐蚀)。
应力腐蚀开裂在力学、环境、材料、断裂形态学等方面表现出一些独特的性质。
7.2.1应力腐蚀的特征
7.2.1.1力学特性
(1)应力性质——通常认为应力腐蚀只有在拉应力条件下才能发生,这种应力可以是外加应力,或是加工(铸造、锻造、轧制、挤压、机加工、焊接等)、热处理、表面处理、磨削、装配等过程中引入的残余应力,也可以是腐蚀产物的楔入作用而引起的扩张应力。
如304L不锈钢退火酸洗后在42%MgCl2沸腾溶液中放置3个月后,发现断面上有穿晶型应力腐蚀裂纹,这是因为点蚀坑中的固体腐蚀产物比容大,能起到楔子的作用,从而产生横向张应力。
据统计80%的应力腐蚀事故起源于残余应力,因此设备破坏分析中一定要注重对残余应力的分析。
应当指出,近年来有的研究结果表明宏观压应力在某些情况下也可以产生应力腐蚀裂纹,其原因有两种可能:
一是当应力腐蚀开裂以裂纹尖端的金属阳极溶解为控制过程时,由于压应力同样能够引起金属产生滑移变形,故SCC仍可发生;另一种情况是:
虽然结构或试样所受宏观应力为压应力,但微观上局部仍为张应力。
SCC是一种低应力(应力水平通常为材料屈服强度的50~90%)脆性断裂,断裂前无大的塑性变形,常常导致无先兆的灾难性事故。
(2)存在临界应力——应力腐蚀开裂是一种与时间有关的滞后破坏,材料所受应力愈小,断裂时间tF愈长,当应力小于某一临界值后,tF趋于无穷,此应力值称为应力腐蚀的临界应力(σscc),对于存在预裂纹的试样或构件则存在一临界应力强度因子(KISCC)。
不同的材料——环境体系的σscc或KISCC可能有很大的差异,如在室温3.5%NaCl水溶液中,用于制备飞机起落架的30CrMnSiNi2A超高强度钢的KISCC只有17MPa·m
,而用于制备飞机发动机压气机叶片和盘的TC4(Ti6Al4V)钛合金的KISCC高达60MPa·m
,但后者的屈服强度σs只有前者的64%。
图7.2低碳钢在碳酸钠溶液中应力腐蚀敏感性随应变速率的变化
(3)应变速率的作用——应变速率对应力腐蚀的发生与发展有重要的影响。
研究表明材料的应力腐蚀敏感性(以塑性损失率Iϕ=(ϕ空白-ϕSCC)/ϕ空白)常表现出图7.2所示的规律,即当应变速率
大于某一临界值
2后,其塑性损失不明显,表明应力腐蚀敏感性较低(因高应变速率时,断裂时间太短,应力腐蚀裂纹来不及形核就发生机械过载断裂);当应变速率
小于某一临界值
1后,其塑性损失也不明显,同样表明应力腐蚀敏感性较低(原因是应变速率过低,拉伸使金属表面膜破裂的速率低于新鲜金属重新形成钝化膜的速率,这时新鲜金属来不及溶解又被膜覆盖,因此不发生应力腐蚀开裂)。
具有这种应力腐蚀规律的体系其SCC机理属于阳极溶解型。
7.2.1.2环境特性
(1)特定的材料——环境介质组合
对每一种金属材料,只有在特定的介质中才能发生应力腐蚀,如表7.1所示。
正因为如此,有人以环境特点命名一些金属材料的应力腐蚀。
如锅炉钢在碱性溶液中的“碱脆”、低碳钢
表7.1产生应力腐蚀的特定材料——环境介质体系
材料
介质
断裂形式
低碳钢
高强度钢
奥氏体不锈钢
铝合金
钛与钛合金
镁和镁合金
铜和铜合金
镍和镍合金
锆和锆合金
NaOH,CO—CO2—H2O,硝酸及碳酸盐溶液
水介质,氯化物,含痕量水的有机溶剂,HCN溶液
沸腾盐溶液,高温纯水,含Cl-水溶液,合Na+的盐溶液,连多硫酸,H2S溶液,H2SO4十CuSO4溶液,苛性碱溶液
湿空气,含Cl-的水溶液,高纯水,有机溶剂
水溶液,有机溶剂,热盐,发烟硝酸,N2O4
湿空气,高纯水,KCl+K2CrO4溶液
含NH4+溶液或蒸气,NaNO2,醋酸钠,酒石酸钾,甲酸钠等水溶液
高温水,热盐溶液,卤素化合物,HCl,H2S+CO2+C1,NaOH
水溶液(含FeCl3,CuCl2,硝酸,卤素化合物),热盐溶液,甲醇(含I-,Br-,C1-),CCl4,CHCl3,卤素蒸气
晶间/穿晶
晶间/解理
穿晶/晶间
晶间
晶间/穿晶
晶间/穿晶
晶间/穿晶
晶间/穿晶
晶间/穿晶
在硝酸盐溶液中“硝脆”、奥氏体不锈钢在含有Cl-离子溶液中的“氯脆”、黄铜在带有氨气氛中“氨脆”、奥氏体不锈钢在含有连多硫酸溶液中的“硫脆”、高强度钢在酸性或中性NaCl水介质中的“氢脆”。
发生SCC的体系,金属表面的均匀腐蚀倾向小(低于0.125~0.250mm/a),具有一定的钝化能力,以发生局部腐蚀为特点。
(2)
图7.3合金的应力腐蚀断裂电位区(阴影)
特定的电位范围
材料与特定介质的偶合是导致SCC的必要条件可以从电化学的角度找到原因,即金属材料SCC往往发生在电化学极化曲线的活化——阴极保护过渡区、钝化——活化过渡区或钝化——过钝化过渡区(如图7.3所示)。
在这种条件下,表面膜处于不稳定状态,局部易出现活化的点蚀核心,而大部分区域处于钝化状态,从而构成大阴极——小阳极电化学腐蚀结构,为局部应力腐蚀裂纹萌生提供了必要的条件,而特定的材料——环境介质组合正是使材料的自腐蚀电位处于上述“钝化——活化过渡区或钝化——过钝化过渡区”,材料的SCC敏感电位范围除与介质的类型和浓度有关外,还受环境温度的影响(如图7.4所示),温度愈高,其SCC敏感的电位范围愈大。
根据SCC在阳极极化曲线上的特定电位范围特点,既可理解已发现的应力腐蚀断裂系统,也可通过介质的选择和电位的控制,发现和理解新的应力腐蚀断裂系统,达到预测和控制SCC的目的。
(3)局部环境与整体环境间的差异
图7.5铁的裂纹内pH值及电位
图7.4低碳钢在3.5%NaCl溶液中外加电位与断裂寿命的关系
应力腐蚀与点蚀、缝隙腐蚀的发展过程有一个共同点——即均以“闭塞电池”机制为推动力。
根据前面关于点蚀、缝隙腐蚀的讨论知,裂纹或缝隙闭塞区的局部化学环境与整体溶液的化学环境之间存在很大的差别。
测试结果表明在模拟海水环境的3.5%NaCl(pH=5)水溶液中,铁、铝、钛合金和奥氏体不锈钢裂纹尖端的pH值分别约为4、3.5、2和0.7,即裂尖为局部酸性,为阳极溶解提供了条件。
Cl-离子浓度的测量结果表明,裂纹内较外部提高10倍左右。
其它离子(如金属离子、NO-3、SO2-4等)在裂纹内与裂纹外也有明显的差异,这种差异反映在电化学上则是裂纹尖端与裂纹外的电极电位的不同(图7.5所示为Pourbaix对铁在含Cl-的溶液中根据热力学计算的裂纹内pH值和电位的分布),裂纹内部电位较外部电位通常低数十mV到数百mV,即裂尖是局部阳极区。
7.2.1.3材料学特性
(1)材料成分的作用
材料的成分对SCC通常有明显的影响,一般讲,合金比纯金属更易产生SCC,原因是合金元素的加入能够影响材料表面的电化学均匀性和稳定性,可能促进选择性腐蚀(阳极相或阳极成分分布)。
合金成分的变化会影响材料的组织结构,进而影响在特定介质中的电化学行为。
不同的合金元素对材料的SCC有不同的影响,如加入适当的Cr或Al元素可以提高奥氏体不锈钢的SCC抗力,元素Ni对Fe-Ni-Cr合金SCC的影响则呈非单调的变化规律,而C、N、S、P等易于在金属晶界上析出,构成活性通路,促进SCC的发生。
(2)组织结构的作用
材料的微观组织结构对SCC有重要影响,如面心立方的奥似体不锈钢在氯化物溶液中很容易产生SCC,但体心立方的铁素体不锈钢则对该环境有很高的SCC抗力。
因为材料的显微组织结构取决于材料成分、热处理制度,因此显微组织对SCC的影响与材料成分、热处理制度的作用相联系。
如相同成分的碳钢或低合金钢,在H2S—H2O系统中,在抗SCC性能方面显微组织影响按:
铁素体中球状碳化物组织→完全回火后的淬火显微组织→正火和回火后的显微组织→正火后的显微组织→淬火后未回火的马氏体组织顺序递减。
敏化热处理使奥氏体不锈钢晶界Cr贫化,成为SCC的活化通道,因此促进SCC。
粗晶粒比细晶粒对应力腐蚀开裂更敏感,多数金属的SCC开裂时间tF与晶粒直径d有如下的关系:
lgtF=ad
+b
式中a为材料和环境决定的常数,b是由初始力学因素决定的常数。
决定金属材料SCC特性的最重要因素之一是其强度水平,对于高强度钢来说,强度愈高,其SCC敏感性愈大,当屈服强度大于1400MPa时,其SCC敏感性很高,因此在航空、化工等领域为了控制SCC而对钢的强度、硬度提出了专门的要求,如国际上为防止在H2S环境中发生SCC,要求低合金钢的硬度值必须小于洛氏硬度HRC22。
晶粒取向与应力方向的关系也是影响SCC敏感性的一个重要因素,当应力方向与轧制板材中晶粒长轴方向一致时,SCC敏感性低,当二者垂直时,SCC敏感性高。
需要指出的是不仅金属材料存在SCC问题,非金属材料也会发生SCC破坏,如笔者对钠钙玻璃和精细陶瓷的研究结果表明,在自来水中两种材料均可产生SCC破坏。
图7.6三种裂纹方式
7.2.1.3应力腐蚀裂纹扩展特征
SCC的发生与发展可分为裂纹的孕育期和扩展期两个阶段。
SCC的裂纹孕育期的长短取决于SCC三要素——材料性能、环境状况和力学条件,可以从几分钟到几年,甚至几十年。
对于带裂纹试样,依据外加应力与裂纹面的取向关系,有图7.6所示的三类裂纹试样:
Ⅰ型也称为拉开型,Ⅱ型也叫滑开型,Ⅲ型又叫撕开型。
从断裂力学角度为描述裂纹尖端应力、应变的大小而引入应力强度因子的概念,对于Ⅰ型、Ⅱ型、Ⅲ型裂纹,分别有三类应力强度因子
、
和
。
对于Ⅰ型裂纹,
,式中
分别表示远离裂纹的均匀拉应力和裂纹长度,而形状因子Y是与裂纹形状、加载方式以及试样几何有关的量。
从裂纹扩展速率(da/dt)与裂纹尖端的应力场强度因子
的关系,可以将SCC裂纹扩展过程分为图7.7所示的三阶段:
图7.7裂纹扩展速率da/dt与KI之间的关系
第一阶段:
当
>KISCC时,裂纹才以低速率扩展,这时力学因素起主要作用,da/dt随着KI的增大而迅速增加。
KISCC即为临界应力强度因子。
第二阶段:
当
增大到一定数值后,da/dt保持恒定,即裂纹扩展速率不随力学因素变化而改变,原因是化学或电化学因素起主要作用(如裂纹尖端反应物质的传质过程为裂纹扩展的控制步骤)。
第三阶段:
继续增大,力学因素又起着主要作用,当达到机械断裂的裂纹临界应力强度因子KIC时,则在机械力的作用下发生快速失稳断裂。
应力腐蚀裂纹稳定扩展速率(第一、二及第三阶段快速扩展前)一般为10-8~10-4mm/s,它较机械作用下的快速断裂低1010倍(机械快速断裂一般为金属中声速的1/3~1/4),比点蚀等局部腐蚀速率快得多,如高强度钢在海水中SCC的速率比点蚀速率快106倍。
应力腐蚀试样或构件的寿命是孕育期与裂纹稳定扩展时间的总和。
7.2.1.4应力腐蚀破坏的形态学特征
1
(1)SCC的宏观形态特征
断口特征是分析和诊断SCC破坏的重要依据。
应力腐蚀断裂破坏属于脆性损伤,即使延性很好的材料,其SCC宏观形态仍显示明显的脆性断裂特征,即:
断口平直,并与正应力垂直,没有明显的塑性变形,颈缩也不明显(图7.8),裂纹源及扩展区断口表面通常呈黑褐色(钢基)或深灰色(铝基),原因是腐蚀产物覆盖着断口表面,并且离源区越近,腐蚀产物越多,同时断口表面腐蚀状况还与电化学腐蚀条件及SCC机制有关。
应力腐蚀断裂起源于表面,一般为多源,起源处表面,一般存在腐蚀坑,应力腐蚀与机械断裂过渡区断口上常出现放射性花样或人字纹,最后失稳断裂(机械断裂)区为银灰色。
宏观断口上,放射性花样或人字纹收敛方向即SCC裂纹萌生区(裂纹源)。
我们的研究发现应力腐蚀宏观断口的另一个特征是裂纹前沿的形状因应力状态、SCC作用机理不同而有明显的差异,当表层平面应力状态有重要影响或裂纹扩展以氢脆机制为控制过程时,裂纹前沿一般为正舌型(即试件中部较表面裂纹扩展快);当试件平面应变状态条件满足得好或阳极溶解机制起重要作用时,裂纹前沿通常呈倒舌型、M型或平直型(如图7.9)。
图7.940CrMnSiMoVA超高强度钢试样在3.5%NaCl水溶液中的SCC宏观断口
另外,以阳极溶解为SCC机制的宏观裂纹扩展过程中出现二次裂纹——分叉裂纹,其尺寸通常在数百微米到cm量级,有主裂纹和次裂纹之分,主裂纹延伸方向与最大张应力方向垂直。
(2)SCC的微观形态特征
应力腐蚀断口的微观形态与应力腐蚀机理、环境条件、材料性质、电化学状态、力学因素等有重要关系(表7.1)。
从电化学角度可将SCC机理分为阳极溶解型和氢致开裂型。
对氢致开裂型的SCC,如高强度钢在水介质中,其断口形貌和钢的强度σs以及外加应力(或KI)有关,当σs较低,KI较高时,获得韧窝断口,随σs升高或KI降低,可变为准解理、解理或沿晶断口。
对于阳极溶解型的SCC,将获得脆性沿晶、穿晶(解理或准解理)、混合或相间SCC断口。
航空用超高强度钢在含Cl-离子水溶液乃至纯水中都能表现出很高的SCC敏感性,其SCC过程以氢脆机制为主,微观断口以沿晶为主,其特征为冰糖块状沿晶脆性断口形态(图7.10)。
图7.11铝合金应力腐蚀断口上的扇形准解理形貌
图7.1040CrMnSiMoVA超高强度钢在室温蒸馏水中的SCC沿晶断口形貌
面心立方结构的铝合金和奥氏体不锈钢等SCC断口上常常可见到图7.11所示的河流花样或扇形准解理的形貌特征。
材料成分对SCC断口形貌也有重要影响。
如Mo含量对16Cr-15Ni不锈钢SCC断口形貌的影响是随Mo含量的增高,断口由穿晶破坏向晶间断裂模式转变,金属的阳极溶解作用减弱,即Mo增加了不锈钢的耐Cl-离子腐蚀抗力。
SCC断口不仅有宏观上的分叉,而且存在微观上的分叉,当SCC机理为阳极溶解控制时,显微断口呈多分枝特征,但当SCC机理为氢脆控制时,则通常为单一裂纹。
对于Ti3Al+Nb金属间化合物等材料,还会出现沿相间开裂的阳极溶解型SCC形态特征(如图7.12),这既不同于沿晶型开裂,也不同于穿晶型开裂,而是一种独立的SCC开裂方式。
图7.12Ti3Al+Nb在甲醇溶液中的相间SCC断口
另外,当钛合金与高温氯化物、溴化物、碘化物接触时,如果环境中还有氧和水分存在,同样会发生低应力延迟破坏,其破坏形态以沿晶为主,此称为钛合金的热盐应力腐蚀。
钛合金在各类氯化物中热盐应力腐蚀的敏感程度按次序由轻到重排列情况:
材料在受力变形时往往造成其表面膜的局部破坏,此即膜的机械破坏方式。
裂纹的尖端由于应力、应变集中,所以金属表面膜更容易破裂。
晶界缺陷及杂质较多,表面膜往往不完整,裂纹易于沿晶界形核和扩展,导致沿晶应力腐蚀开裂。
用滑移导致膜破裂的机理模型可以圆满地解释穿晶型应力腐蚀的起因(如图7.13)。
(2)溶解:
阳极溶解控制的活性通道腐蚀型应力腐蚀断裂(APC—SCC)的裂纹是通过裂纹尖端的阳极溶解过程而推进的。
裂纹扩展的可能途径有两个,即预先存在活性通道和应变产生的活性通道。
预存活性通道的电化学机理认为,发生SCC需要两个基本条件:
首先是材料中预先存在着对腐蚀敏感的、多少带有连续性的通道,这种通道在特定环境下相对于周围组织是阳极。
其次是要有足够大的、基本上垂直于活性通道的拉应力。
对于第二种可能的途径有一种观点认为,应力的作用不仅是造成膜的破裂,更重要的是使裂尖局部区域迅速屈服,出现很多的化学活性点,或降低了溶解的活化能,即应变造成新的活性溶解途径。
(3)断裂:
应力腐蚀裂纹扩展达到临界尺寸,便会机械力作用下发生失稳快速断裂。
氢致开裂型SCC理论认为,如果阳极金属溶解腐蚀所对应的阴极过程是析氢反应,而且原子氢能扩散进入金属并控制了裂纹的形核与扩展,这一类的应力腐蚀即称为氢致开裂型应力腐蚀,它是氢损伤的一个特例。
氢损伤的具体机制详见下节讨论。
图7.14SCC的阳极溶解型和HE型机理模型
a)阳极溶解型b)氢致开裂型
阳极溶解控制的活性通道腐蚀型SCC(APC—SCC)和阴极析出氢控制的氢脆型SCC(HE—SCC)在微观机制和SCC裂纹形核位置上均有不同,这可通过图7.14加以比较。
图7.14(a)中APC—SCC的裂纹是通过裂纹尖端的阳极溶解过程而推进的。
活性通道可以是合金中原先已经存在的一些连续或准连续的成分不均匀区,也可以是裂纹尖端的前沿因塑性变形而新形成的活性区。
阴极过程除了与阳极过程所产生的电子发生反应外,对SCC裂纹扩展并无其它影响。
图7.14(b)中HE—SCC的裂纹是通过合金在阴极区吸收阴极反应的产物氢原子诱导脆性开裂而推进的。
阳极过程仅为阴极反应提供电子,对裂纹扩展并无直接影响。
在实际构件的SCC事件中,两种机理可能会同时起作用,即为混合型作用机理。
由于电化学保护技术或金属镀层方法对阳极溶解型SCC和氢致开裂型SCC有截然不同的影响,所采取的预防措施也就不同,因此分析和诊断SCC机理属于阳极溶解型还是氢致开裂型是十分重要的。
具体区分两种机理可以综合参考下述方法和途径:
(1)电化学方法:
一般来说,阳极极化可加速阳极溶解型SCC破坏,而减缓氢致开裂型SCC破坏;阴极极化则加速氢脆型SCC过程,而减缓阳极溶解型SCC破坏。
但由于SCC过程的复杂性,上述情况是有例外的,如对高强度钢在水溶液中阳极极化,则加速氢在钢中的渗透,从而促进HE的作用,另外,若阳极极化使局部腐蚀减轻而全面腐蚀加速,同样可缓解SCC过程。
钛合金对HE十分敏感,但是阴极极化可导致裂纹尖端pH值从1.8升至11,析氢减缓,SCC敏感性反而降低。
图7.15阳极溶解型SCC和氢脆型SCC裂纹的显微形貌
(a)阳极溶解型SCC(b)氢脆型SCC
(2)断口特征:
应力腐蚀断口依赖于断裂机理、应力状态、材料强度、氢含量等多种因素。
一般来说,阳极溶解型SCC断口,腐蚀坑明显,起源于表面;而氢致开裂型SCC断口表面可能探测出氢化物,裂纹一般起源于次表面。
同时,阳极溶解型SCC裂纹通常为多分叉特征,而氢致开裂型分支少(如图7.15,图的左边为试件表面)。
解理、准解理、沿晶等是共同的断口特征,但氢致开裂型断口有时可看到较轻微的韧窝特征。
(3)应力状态的作用:
宏观压应力能引起阳极溶解型应力腐蚀开裂,其孕育期较拉应力情况高1~2个数量级,门槛值高3~5倍,但不会引起氢致开裂型的SCC。
(4)裂纹扩展的连续性:
传统认为,