碳一化工项目建设投资可行性研究报告书.docx
《碳一化工项目建设投资可行性研究报告书.docx》由会员分享,可在线阅读,更多相关《碳一化工项目建设投资可行性研究报告书.docx(62页珍藏版)》请在冰豆网上搜索。
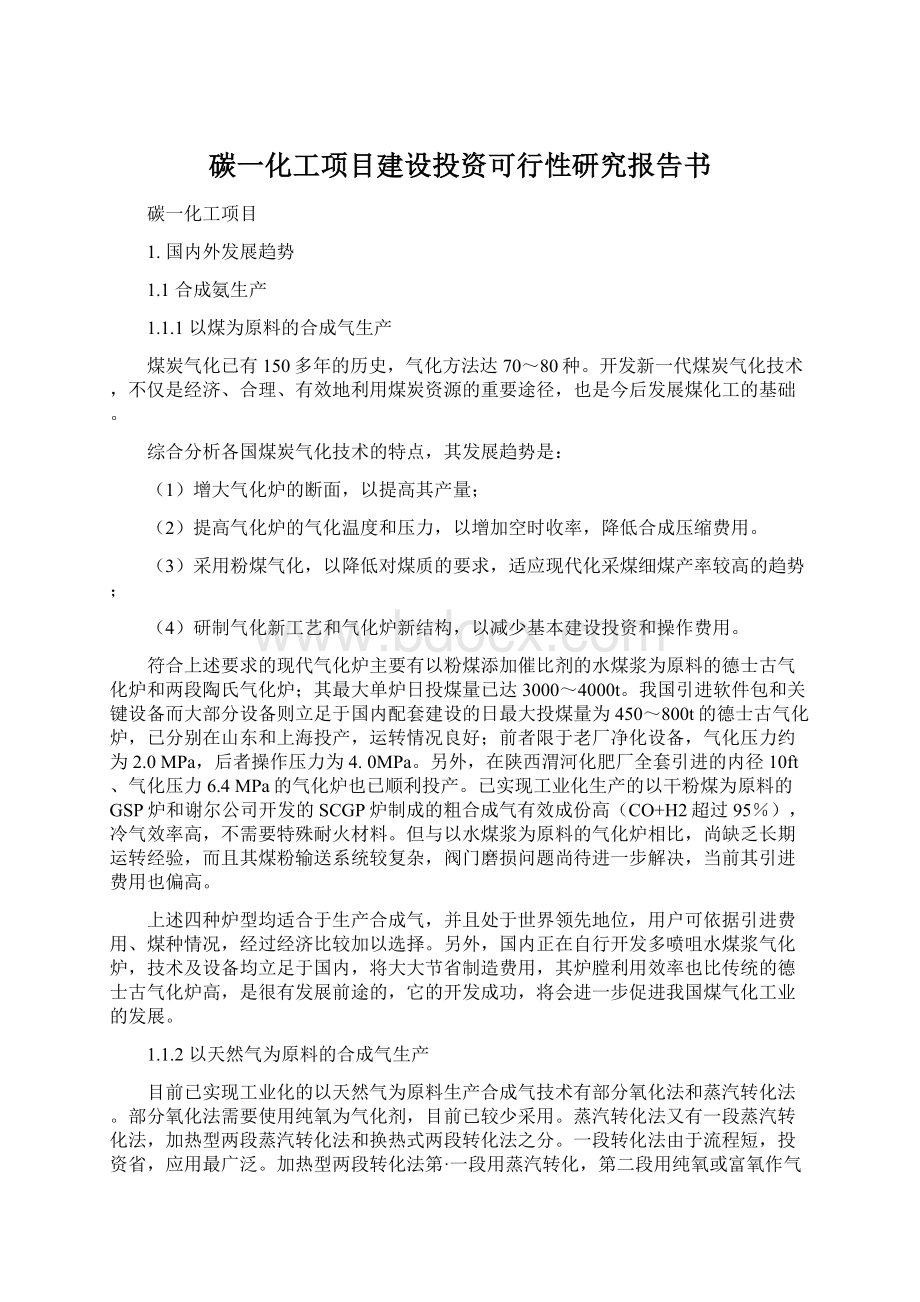
碳一化工项目建设投资可行性研究报告书
碳一化工项目
1.国内外发展趋势
1.1合成氨生产
1.1.1以煤为原料的合成气生产
煤炭气化已有150多年的历史,气化方法达70~80种。
开发新一代煤炭气化技术,不仅是经济、合理、有效地利用煤炭资源的重要途径,也是今后发展煤化工的基础。
综合分析各国煤炭气化技术的特点,其发展趋势是:
(1)增大气化炉的断面,以提高其产量;
(2)提高气化炉的气化温度和压力,以增加空时收率,降低合成压缩费用。
(3)采用粉煤气化,以降低对煤质的要求,适应现代化采煤细煤产率较高的趋势;
(4)研制气化新工艺和气化炉新结构,以减少基本建设投资和操作费用。
符合上述要求的现代气化炉主要有以粉煤添加催比剂的水煤浆为原料的德士古气化炉和两段陶氏气化炉;其最大单炉日投煤量已达3000~4000t。
我国引进软件包和关键设备而大部分设备则立足于国内配套建设的日最大投煤量为450~800t的德士古气化炉,已分别在山东和上海投产,运转情况良好;前者限于老厂净化设备,气化压力约为2.0MPa,后者操作压力为4.0MPa。
另外,在陕西渭河化肥厂全套引进的内径10ft、气化压力6.4MPa的气化炉也已顺利投产。
已实现工业化生产的以干粉煤为原料的GSP炉和谢尔公司开发的SCGP炉制成的粗合成气有效成份高(CO+H2超过95%),冷气效率高,不需要特殊耐火材料。
但与以水煤浆为原料的气化炉相比,尚缺乏长期运转经验,而且其煤粉输送系统较复杂,阀门磨损问题尚待进一步解决,当前其引进费用也偏高。
上述四种炉型均适合于生产合成气,并且处于世界领先地位,用户可依据引进费用、煤种情况,经过经济比较加以选择。
另外,国内正在自行开发多喷咀水煤浆气化炉,技术及设备均立足于国内,将大大节省制造费用,其炉膛利用效率也比传统的德士古气化炉高,是很有发展前途的,它的开发成功,将会进一步促进我国煤气化工业的发展。
1.1.2以天然气为原料的合成气生产
目前已实现工业化的以天然气为原料生产合成气技术有部分氧化法和蒸汽转化法。
部分氧化法需要使用纯氧为气化剂,目前已较少采用。
蒸汽转化法又有一段蒸汽转化法,加热型两段蒸汽转化法和换热式两段转化法之分。
一段转化法由于流程短,投资省,应用最广泛。
加热型两段转化法第·一段用蒸汽转化,第二段用纯氧或富氧作气化剂,但用于制氨时可用空气替代纯氧作气化剂,同时又可减少一段炉的负荷,节省高镍合金钢,故广泛应用于制氨。
换热式两段转化工艺最有发展前途。
其二段转化炉出口高温气体热量供一段炉所需的热量,故可大幅度减少燃料天然气的热用量,存在的问题是副产蒸汽量减少。
但从节能的角度来看,这种方法最有竞争能力,是今后大型装置的主要发展方向。
用天然气两段转化制合成气,含氢量高但碳量不足,因此一段转化炉采用副产的二氧化碳作为气化剂来增碳,不仅可改善合成氨的氢碳比,同时减少了工厂二氧化碳的排放,因此也是值得推广的一种工艺技术。
1.2甲醇及含氧化合物的生产
1.2.1甲醇
甲醇是一种重要的基本有机原料,也是C1化学的起始化合物,在基本有机原料中,甲醇仅次于乙烯、丙烯和苯而居第四位。
甲醇合成目前普遍采用帝国化学公司(ICI)和德国鲁奇(Lurqi)的工艺。
由合成气合成甲醇,己有多年的工业化实践,技术上已臻成熟,能量利用效率已接近工艺本身可以达到的最佳化程度。
尽管如此,由于一些固有问题的约束,当前的甲醇合成仍然是一个能耗较高的工艺过程,仍有改进的必要。
这些固有问题主要是:
(1)造气过程能耗高,投资大;
(2)受合成过程热力学的控制,对于甲醇合成从化学平衡来看低温是有利的,但是传统的催化剂需要在较高温度下进行,因此单程转化率低,大量未转化的合成气需要循环,使操作费用相当昂贵;(b甲醇合成过程反应热的移出及利用尚有赖于反应卫程学的问题妥善解决;(4)传统的催化剂对硫过分敏感,增大了合成气脱硫的费用。
为了降低造气费用,国外正在研究甲烷(或天然气)直接氧化制甲醇及甲醛。
加拿大、前苏联、日本都有研究,但均停留在小试阶段,目前尚无法与间接法竞争,估计实现工业化还需经过一段相当长时间的工作。
在甲醇合成反应器和催化剂方面的研究工作也取得了一些突破,较有成效的有:
(1)Dat/t/Makee合成新工艺
这种工艺的特点是使用了耐硫催化剂,采用管式低温合成塔,比传统合成塔大大提高了空速。
(2)浆态合成甲醇反应器
早在70年代中期,美国化学系统公司即开始了浆态相合成甲醇的研究,通过5~8t/d的中试装置,成功地实现了连续运转,已进入了实用化阶段。
该反应器有效地改善了合成过程的传热,使反应基本上在等温下操作,合成原料气通过新设计的环形气体分布器进入反应器,在保持高浓度催化剂浆液悬浮的同时,又保持了紧密的气/液接触,改进了传质。
在温度250℃,5MPa下采用内部换热,无浆液外循环方式,空速11000L/h·kg情况下,出口甲醇浓度为7%~8%,每小时每公斤催化剂的甲醇产率可达到0.96kg。
但浆态操作因催化剂均匀悬浮在液相介质中,其中毒机会是均匀的,因而对原料气杂质含量要求很严格:
总硫含量要求低于0.06X10-6,HCl、Fe(CO)5及Ni(CO)4要求低于0.01X10-6,美国空气液化公司将与达科气化公司合作,在大平原煤气化厂建造一套日产500t的浆态床甲醇合成工业示范装置,项目预算约2.14亿美元。
(3)守固。
固滴流反应器
气固一固滴流流动反应器(gas-solid-solidtrickleflowreactor简称(GSSTFR)是一种新型反应系统。
它集催化剂的催化作用和吸附剂的吸附作用于同一一反应器,在进行合成反应的同时,进行产品的吸附分离,产品甲醇一经生成,即被吸附剂吸附,使合成反应平衡不断向产品方向转移,从而克服了化学平衡的限制,CO的单程转化率已接近100%,循环操作可以取消。
这项革新很有吸引力,受到了广泛的重视。
GSSTFR系统气相是合成气和甲醇,一个固相是Cu基催化剂,固定在反应器的栅架上,另一个固相是硅铝裂化催化剂,以滴流状态流过催化剂床层,用于吸附反应区域中的甲醇。
为了评价GSSTFR系统的可行性,荷兰Twente工业大学建立了一套微型试验装置,在解决了固体输送和气。
固分离问题、实现连续化后,其经济效果是可观的。
(4)耐硫催化剂
最近日本公害资源研究所开发了一种新的Pd系合成甲醇催化剂,据称无需深度脱硫即可直接用于合成气的甲醇合成。
这种新型催化剂以带状云母作为载体。
它是一种具有层状结构物的矿物,层与层之间有Ni离子,这种矿物具有溶胀性和离子交换性。
这种耐硫催化剂就是通过离子交换法使Pd载入载体中取代Ni离子而制得的。
(5)超临界合成甲醇反应器
为了改变合成甲醇时大量未转化的合成气循环的情况,我国中科院山西煤化所开发了超临界相合成甲醇新工艺。
该技术的特点是在甲醇反应器中添加超临界或亚临界介质,使合成的甲醇连续不断地从气相转移至超临界相,从而克服了传统的合成甲醇尾气大量循环(约为新鲜气的5~8倍)的情况。
在山西太原化肥厂一所作的中试结果证明,在无尾气或新鲜气与尾气循环比为1:
l时,CO转化率达到了90%,甲醇时空产率平均值达到0.46t/h·t催化剂,当放空气能合理利用时具有较好的工业化前景,现该所正与宁夏化肥厂合作进行进一步的开发和放大试验工作。
(6)燃料甲醇
在国家科委支持下,我国从德国引进了三辆以纯甲醇为燃料的汽车,经过长达8年的长期公路运行试验,取得了很好的成果。
公路实际运行实践验证,1.6~1.7t甲醇,相当于1t汽油。
按现行的汽油和甲醇市场价格对比,其经济效益明显,且尾气排放较汽油车大幅度减少,对改善城市环保有较好的效果。
这种环保型汽车的发展,无疑将进一步促进甲醇工业的发展。
1.2.2合成其他含氧化合物
(1)甲醇碳基化制醋酸及醋酥
甲醇碳基化制醋酸及醋酐是近年来C1化学的重大进展,美国和英国均已实现了工业化。
自1982年以来,世界醋酸生产能力中,甲醇碳基合成法已占50%以上。
最近德国赫斯特公司(Hoechst)将含氢的CO鼓泡导人醋酸甲酯和甲醇的混合液中进行碳基化反应,所得醋酐产率可达1766g/gRh-h。
在醋酸甲酯制备方面也取得了进展。
美国联合碳化物公司已将甲醇碳基化制醋酸甲酯和醋酸混合液的反应选择性提高到接近100%。
碳基化主要采用锗络合催化剂,助催化剂为碘化物。
因此,各国都重视锗和碘的回收。
据德国赫斯特公司发表的专利,它可使醋酸甲酯和甲醇碳基化产品液中的总碘量由2X10-6降低至5X10-12以下。
我国在这方面也取得了小试成果。
我国开发的固载化催化剂可以基本解决铐的流失问题。
(2)草酸及乙二醇
CO通过氧化偶联制草酸,也是一项新技术。
甲醇与亚硝酸(N2O3)反应生成亚硝酸甲酯,在Pd催化剂上实现氧化偶联,得到草酸甲酯,经水解后生成草酸;氧化产品中的NO再氧化成N2O3,循环使用。
这一过程实际并不消耗甲醇和亚硝酸,只是CO与O2和H20合成草酸。
若用乙醇代替甲醇,则可生成草酸二乙酯,再加氢即可制得乙二醇,乙醇可循环使用。
这是一条非石油原料合成乙二醇的路线。
日本目前已将合成气制乙二醇列为C1化学技术开发的基本方向之一。
日本工业技术院最近又获得了一项专利,它采用乙酞丙酮基二碳基锗作催化剂,合成气经液相反应制得乙二醇,产率可达17.08mol乙二醇/g原子铑。
我国中科院福建物构所在CO常压催化偶联合成草酸用催化剂的研制方面,进行了原料配比和各种空速条件对催化合成草酸二甲酯的研究,并优选了适宜的反应条件。
改进配制的Pd(2.0%)/a-Al2O3催化剂在常压、140℃、CO/CH3ONO=1.5、空速3000h-l条件下,时空收率达到999g/L·h。
该所并与福建石油化工设计院和福建南靖氨厂合作进行了规模为100t/a的合成氨铜洗回收CO、常压催化合成草酸二甲酯及水解制草酸的中试。
日本国立工业化学实验室开发了一种新的甲醇制乙二醇的工艺。
它采用氧化锗催化剂在常温常压下通过光辐射活化,将甲醇与丙酮的混合液直接合成为乙二醇,据称选择性可达80%。
(3)甲醇碳基化制甲酸甲酯,再水解制甲酸
德国Hu1s公司以甲醇和CO在叔二胺与乙烷作用下进行加压碳基化反应制得甲酸甲酯(HCOOCH3),转化率为80.7%,选择性达99.4%。
同时,该公司还开发了避免甲酸甲酯再酯化而制得无水甲酸甲酯的新工艺。
(4)合成气制甲基叔丁基醚
采用多组份催化剂,可从合成气制含60%异丁醇和40%甲醇的混合物,异丁醇脱水成异丁烯,从而可完成由合成气直接制取甲基叔丁基醚。
这是一条很值得重视的由天然气(或煤)制取高辛烷值添加剂的技术路线。
(5)气相法合成乙醇
日本乙化学组合有关企业和研究所,目前已完成每日2.2kg的小试,在筛选催化剂的基础上,对以Rh/SiO,为母体的催化剂中添加各种金属对催化剂中Rh进行修饰,发现添加能促进CO解离的金属可提高催化剂活性,添加能促进加氢能力的金属可提高生成乙醇的活性和选择性。
小试证明,采用复合式催化剂时,乙醇选择性可达70%,乙醇时空收率为250g/h。
(6)甲醇制醋酸乙烯
美国哈康(Ha1con)公司曾进行过从甲醇与醋酸出发制取醋酸乙烯的研究开发。
该工艺是首先将醋酸转化成醋酸甲酯,再进一步转化成二醋酸亚乙酯,经热分解后得到醋酸乙烯和醋酸,但距工业化实用阶段尚有一定距离。
1.3合成烃类
1.3.1甲醇裂解制烯烃
为了应付未来的石油危机,各国对甲醇裂解制烯烃的研究工作已进行了多年。
主要研究方向是抑制生成甲烷和高级烷烃的选择性,提高烯烃选择性。
美国飞马(Mobil)公司开发成功了ZSM-34沸石催化剂,甲醇转化为烯烃的选择性达到80%。
德国BASF公司在日产It的中试中发现钙沸石具有良好的性能,在500~550℃下甲醇转化率为100%,乙烯加丙烯的选择性大于60%。
日本用磷酸钙改性HZSM-5沸石,在600C下甲醇转化率为95%~100%,乙烯十丙烯的选择性达到了67.5%。
我国中科院大连化物所在甲醇裂解制烯烃的科研工作方面居世界领先地位,从日产5kg模式试验获得了优良的效果,甲醇转化率为100%,对烯烃的选择性达到85%~90%,乙烯十丙烯的选择性达到了70%~80%。
每吨烯烃消耗甲醇2.73t(理论消耗量为2.3t),每吨乙烯十丙烯的甲醇消耗约为3t。
据有关文献报道,通过对轻石脑油和甲醇转化制乙烯的经济比较,可初步得出如下结论:
(1)天然气经甲醇制乙烯,其总投资要比传统的石脑油路线增加约84%。
(2)当轻质石脑油价格为200美元/t时,相应的天然气价格为3.6美分/m3此时两条路线的产品乙烯价值相当。
(3)以天然气为原料经甲醇生产乙烯,其工厂成本较低。
当天然气价格为8美分/m3时,若欲使乙烯的工厂成本与轻石脑油为原料的相当,则轻石脑油的价格相应应为162美元/t。
1.3.2合成气制烯烃
目前,合成气制烯烃已成为费托合成化学中新的研究方向之一,一些研究结果已显示出明显的工业化前景。
据报道,有的研究已取得了低碳烯烃收率接近70g/m3合成气的结果。
前景尽管是诱人的,但离实际工业化尚有一定距离,由合成气制取低碳烯烃,还有一些在转化过程中的核心科学问题有待解决:
一是在CO加氢合成烃类反应中,如何抑制甲烷的生成(低碳烯烃的合成反应需在高温下进行,而温度升高,甲烷生成量也随之增加);二是经典的费托合成反应产物受Schulz一Flozy(F一y)分布规律的限制。
为了解决这些问题,一些科研单位在改进催化剂方面作了大量研究工作,发现采用碱改性ZSM担载Fe-MnO催化剂,其烯烃的选择性达到了50%以上。
1.3.3甲烷氧化偶联制乙烯
甲烷通过合成气转化,在能量利用上是很不经济的。
将甲烷直接氧化脱氢生成乙烯,摆脱造气工序,无疑具有巨大的经济效益。
这一方向近年来一直受到国内外的重视。
美国阿尔科(Arco)公司开发的催化剂在700~800℃,600~10000h-1)空速下,获得甲烷转化率25%,烃类选择性75%,其中乙烯选择性50%,催化剂寿命大于半年,完成了年产35万t乙烯装置的模拟设计,初步测算需投资1.6亿美元,预计乙烯成本可低于现行石脑油制乙烷的成本。
肯达Eindhoren大学使用Twente大学研究的LiCO3/MgO催化剂完成了反应器设计。
该设计在海牙召开的美国化学工程师欧洲年会上被认为是最有前途的。
荷兰科学家提出了两种方案:
方案一甲烷转化率30%,C2烃选择性为80%;方案二甲烷转化率50%,C2烃选择性50%。
以1989年1月价格为计算基准,方案一投资1.7亿美元,方案二投资2.07亿美元。
而采用传统的石脑油裂解工艺,投资则高达4.7亿美元。
预计乙烯的成本为450~550美元/t,均低于石脑油裂解制乙烯的成本。
我国兰州物化所通过3年多的工作,也取得了可喜的进展,有的催化剂(碱金属/过渡金属复合氧化物)甲烷转化率达到25%~35%,对C2+的选择性为70%~80%。
国家计委科技司已把甲烷氧化偶联制乙烯的研究工作列为科技攻关重点项目。
1.4合成液体燃料
合成液体燃料主要有间接法和直接法两大类。
间接法是先制取合成气再进一步合成油品;直接法是在高压下进行煤的直接加氢液化。
国外一些化工公司对合成液体燃料进行了评价和经济分析,结论是当油价每桶在25~30美元时,合成液体燃料方具有工业化价值。
1.4.1合成气制汽油
国外合成气制汽油已经工业化的技术有费托(F一T)合成工艺和甲醇制汽油(MTG)工艺。
前者在南非已建成了三个大厂,合成汽油产量已达350万t/a,并副产乙烯453卜山后者系美国飞马公司(Mobil)的技术,新西兰采用该技术已建成了年产50万、无铅汽油的工厂。
正在开发的工艺有美国飞马公司的两段改良费托合成和丹麦托普索公司的Tigas工艺。
托普索公司分析了MTG法的不足之处,将一段催化剂改为合成含氧化物复合催化剂,然后使用HZSM-5分子筛将含氧化物转化成汽油,已建设了规模为每小时处理合成气400m’的小型中试装置。
中试工厂加工了2.0X106m3合成气,共生产了280t烃类,其中汽油为205t相当干每m3合成气生产140g烃类,其中汽油为103g。
日本新能源组合在四日市建成了合成气制汽油(AMSTG)中试装置,规模为日产汽油1桶。
试验证明,每立方米合成气可生产汽油105~150g。
此外,荷兰壳牌公司开发了SMDS工艺,用一氧化碳加氧合成高分子石蜡烃,再加氢异构化成为发动机燃料,其柴油模试产品分布为:
15%石脑油,25%煤油,60%柴油。
我国山西煤化所对两段改良费托合成也做了大量科研开发工作,已完成了模试,并分别在山西代县和晋城两个化肥厂进行了中试和工业试验。
前者设计能力为汽油100t/a,后者为年产80号汽油2000t。
阶段试验结果表明,每标准立方米CO+H2的C5+矿产率接近100g。
工业试验由于采用了不成熟的常温甲醇洗脱硫,造成甲醇降解,消耗过高,未能长期进柴行下去,但试验证明,其一段铁系反应器和二段分子筛反应器设计是成功的,为下一步工业放大创造了条件。
所生产的汽油马达法辛烷值大于80。
此后煤化所又对一段催化剂进行了筛选,制成了超细粒子铁锰催化剂,通过低碳烯烃制汽油。
该工艺融合了Tigas和MFTI艺的优点,可以在较低压力和高CO转化率下实现一、二段反应在等压下操作。
单管试验证明,每标准立方米CO+H,的汽油收率达到了140g,接近世界水平,此过程联产城市煤气或化肥,工业化前景明朗。
为了给实现工业化打好基础,现山西煤化所正在中科院支持下进行万吨级SMFT合成气制汽油的软件包开发工作。
1.4.2煤炭直接液化
煤炭直接液化,尽管前景并不明朗,但发达国家从战略技术储备出发,均投入了较大的人力和物力进行技术开发工作。
美国和德国目前在这方面处于领先地位。
由于煤炭含氢量严重不足,因此需要在高压(20MPa)下进行加氢液化。
液化需要消耗大量氢气,因此制氢的成本在一定程度上决定着煤炭液化在经济上是否可行。
最近中国神华集团煤炭科学研究总院与美国碳氢化合物技术公司(HTI)合作,采用HTI开发的煤炭液化技术进行日处理干煤12000t日产汽油2900t、柴油4170t等产品的预可行性研究工作;其配套所需的纯氢量高达11.5X106m3/d。
该工程投资巨大,按目前的油价,前景尚不明朗。
但从战略需要出发,在当前我国发动机燃料大量进口的严峻形势下,很有必要对煤炭液化进行积极探索,以便为在条件成熟时建设工业规模示范装置打好基础。
国家目前已经不批准用天然气制甲醇项目,而支持用煤制甲醇.甲醇这几年发展很快,是由于以西南化工设计院为代表的主张将甲醇添加到汽油中使用,一般在10%左右,及甲醇汽油,但国家各部委对此争议很大,目前以乙醇汽油占先,并制定了乙醇汽油的国家标准,在河南.安徽等地已经使用了乙醇汽油,主要用成化粮制造乙醇,但是乙醇汽油成本太过,种粮要消耗水.电.化肥.农膜.农药等农资,而且我国粮食本就缺乏,这乙醇汽油推广变为不太可能.80年代到90年代初甲醇汽油在国外发达国家研究比较多,主要是为了应对石油危机,但是甲醇汽油有如下缺点不易克服:
1)汽车尾气由于燃烧不完全有可能甲醛超标,造成环境污染2)甲醇对汽车内的橡胶材质的配件有溶胀性,造成密封不严.3)对汽车加入甲醇汽油时,甲醇本身由于挥发作用,对人体有危害,4)传统不改发动机的汽车,汽油中添加甲醇的量有限.基于以上原因,国家始终没有出台甲醇汽油的国家标准.但是完全烧甲醇的汽车早已经在设计院试用.我觉得最有发展前途的是二甲醚代替柴油,这不仅因为国家发改委刚出台了支持该行业的产业政策,而且二甲醚车用后尾气可以完全达到欧三排放标准,但是该行业也潜伏这风险,由于投资不大,5万吨/年的装置,不算地皮投资,仅需要不到3000万人民币.二甲醚生产分为一步法和二步法,目前国内较多采用二步法,该法灵活性较强,中间有甲醇这个中间产品,以后可以根据市场好坏生产甲醛.醋酸等产品,但工艺路线较长,能耗较高,生产成本高于一步法生产二甲醚,同时由于二甲醚液态产品的性质,决定了二甲醚项目对交通要求较高,受销售半径影响,同时目前二甲醚主要用于液化石油气的代用品,添加量为30%左右,不能过多,否则用户不接受,燃值较液化石油气低,而且由于华白指数的原因,要改燃具.
版主可以给我加点了吧!
中国的煤世界排名第三,现在石油紧张,中国从俄罗斯的输气管道虽已建成,但要真正帮助中国解决问题还是不太可能,现在煤化工项目在兴起中。
煤基烯烃,煤变甲醇,煤气化(代油)合成氨,煤制二甲醚都在大上特上。
但目前投资过热,国家已经出台政策,甲醇100WT/a,其他的也有了限制,国家支持大化工,但不支持能源的浪费,要是有钱,这种是玩不起的,搞点小化工产品差不多。
煤炭炼油从经济上来说是合理的。
目前原油价格都是在75美元一桶左右,而煤炭价格吨煤炭也就100——500元之间。
最优质的煤炭也不过400多元一吨。
世界上有些国家缺乏石油资源,而国家又需要石油资源,他们就采用煤炭炼油技术来满足这一要求,比如说南非,他们采用世界上最先进的煤炭间接液化制造油。
这种技术在二次世界大战时德国就掌握了,技术成熟。
我们国家也在开展煤炭液化炼油技术。
我们国家采用的技术主要是我国自己开发的煤炭直接液化技术,采用煤炭加氢技术。
我国首个煤炭直接液化炼油厂是神华集团公司的,在内蒙古鄂尔多斯市。
国家经过技术经济评价如果原油价格在32美元一桶,则整个煤炭液化炼油厂就可以刚好运转不亏损也不盈利,目前原油价格在75美元一桶,比较一下是由优势的。
在者我们国家缺油,缺气,多煤。
如果采用煤炭炼油可以缓解能源危机同时又可以减少直接燃烧煤炭对环境的污染。
煤化工行业发展空间被打开
上周,2006年山西投资洽谈会胜利闭幕,大会共引资257亿美元,其中煤化工项目就占135亿美元,占总引资额的54.4%,可见,随着国际局势的动荡不安,石油价格很难大幅回落,中国多煤的特征,已经吸引了国内外大批资金的注意,煤化工的题材,已经由广受怀疑的炒作概念转向了得到实业机构认可的实质操作。
缺油富煤是我国客观存在的能源资源结构。
从资源储量分析,我国煤炭储量远远高于石油储量,煤炭可开采年份是原有可开采年份的5倍,可见,在油价高涨、国内能源紧张的形势下,发挥国内资源优势,通过煤生产甲醇、二甲醚作为首选替代燃料,通过煤生产烯烃等石化下游产品具有重大的战略意义。
政策高度支持从政策层面讲,国家已经充分认识到了煤化工的重要性。
在十一五规划纲要中明确指出,要发展煤化工,开发煤基液体燃料,有序推进煤炭液化示范工程建设,促进煤炭深度加工转化,并开发大型煤化工成套设备,煤炭液化和气化、煤制烯烃等设备。
相关各省在其"十一五"发展规划中把煤化工作为重点发展方向。
这将促使煤化工产业进入规范发展的新阶段。
煤化工发展潜力巨大从技术角度讲,随着应用研究的深入,煤化工产品甲醇替代汽油和二甲醚,在替代柴油、液化气方面表现出的成本优势以及在应用性能的改善上得到广泛认同。
随着原油价格的上涨,甲醇替代汽油作为燃料的呼声与日俱增。
因而大量企业开始投入到煤制甲醇的行业中来。
从需求看,甲醇汽油具有巨大的市场需求空间,专家预测,2020年,中国的石油产量在1.7-2.0亿吨,相当于2.09-2.28亿吨甲醇,还不包括甲醇作为上述四种基础原料的其他消耗。
因而,预计2020年,甲醇的市场需求量有望达到3亿吨左右,需求空间广阔。
从利润空间看,工业甲醇的成本在1000元/吨左右,而市场价格在2500元/吨上下,拥有巨大的利润空间,未来甲醇产量和需求量都会大幅提升,利润空间可以维持。
通过研究证明二甲醚(DME)是理想的柴油替代燃料和民用燃料,是一种重要的超清洁能源和环境友好产品,被称为"二十一世纪的燃料"。
根据试验测算,1吨柴油的发热量相当于1.48吨二甲醚的发热量,而1.5吨甲醇大约可以制成1吨二甲醚。
1吨甲醇的成本约在1000元左右,所以煤制二甲醚成本大约2200元左右。
而目前二甲醚的出厂价在40