手指力学特性测量装置的设计doc.docx
《手指力学特性测量装置的设计doc.docx》由会员分享,可在线阅读,更多相关《手指力学特性测量装置的设计doc.docx(28页珍藏版)》请在冰豆网上搜索。
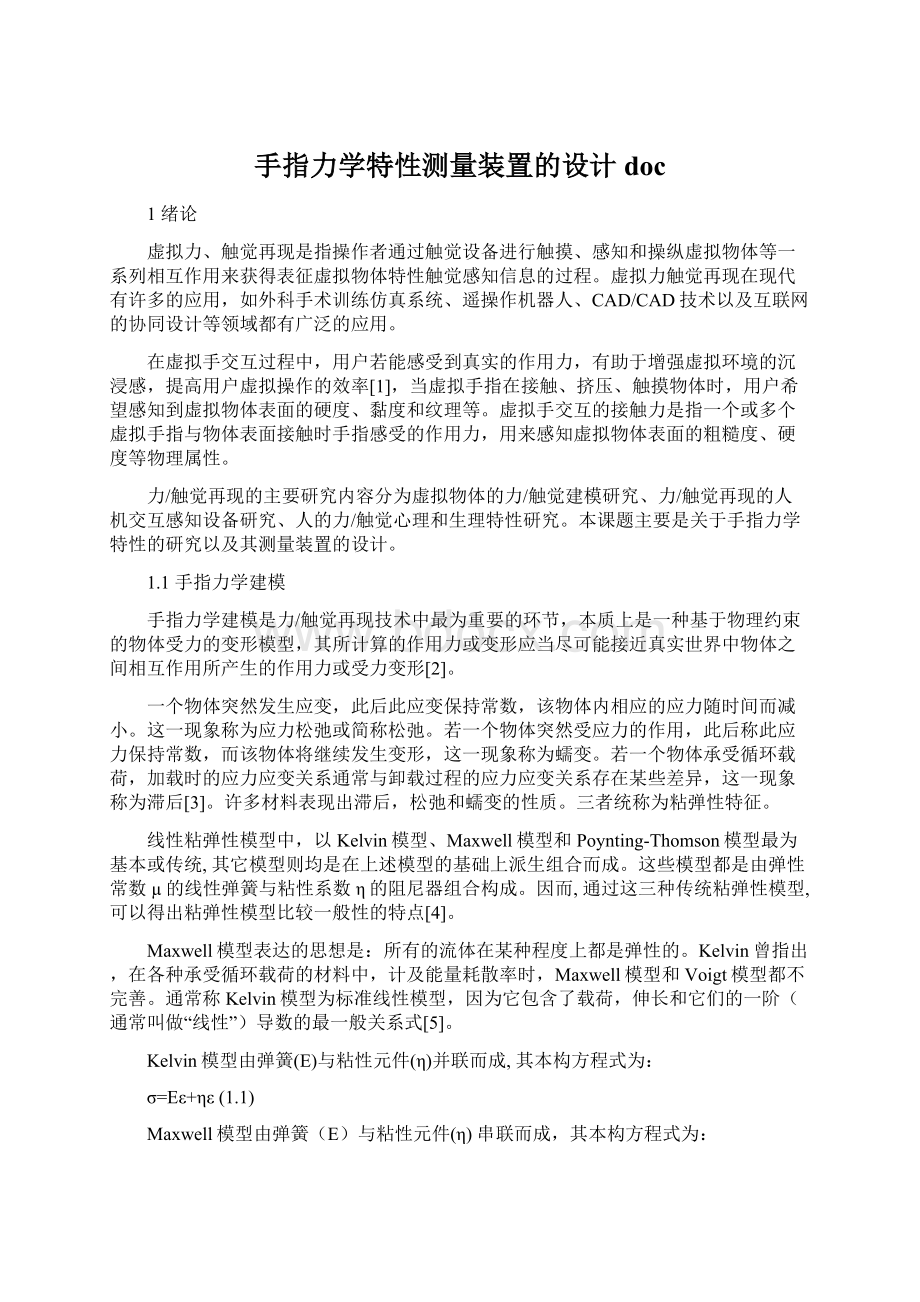
手指力学特性测量装置的设计doc
1绪论
虚拟力、触觉再现是指操作者通过触觉设备进行触摸、感知和操纵虚拟物体等一系列相互作用来获得表征虚拟物体特性触觉感知信息的过程。
虚拟力触觉再现在现代有许多的应用,如外科手术训练仿真系统、遥操作机器人、CAD/CAD技术以及互联网的协同设计等领域都有广泛的应用。
在虚拟手交互过程中,用户若能感受到真实的作用力,有助于增强虚拟环境的沉浸感,提高用户虚拟操作的效率[1],当虚拟手指在接触、挤压、触摸物体时,用户希望感知到虚拟物体表面的硬度、黏度和纹理等。
虚拟手交互的接触力是指一个或多个虚拟手指与物体表面接触时手指感受的作用力,用来感知虚拟物体表面的粗糙度、硬度等物理属性。
力/触觉再现的主要研究内容分为虚拟物体的力/触觉建模研究、力/触觉再现的人机交互感知设备研究、人的力/触觉心理和生理特性研究。
本课题主要是关于手指力学特性的研究以及其测量装置的设计。
1.1手指力学建模
手指力学建模是力/触觉再现技术中最为重要的环节,本质上是一种基于物理约束的物体受力的变形模型,其所计算的作用力或变形应当尽可能接近真实世界中物体之间相互作用所产生的作用力或受力变形[2]。
一个物体突然发生应变,此后此应变保持常数,该物体内相应的应力随时间而减小。
这一现象称为应力松弛或简称松弛。
若一个物体突然受应力的作用,此后称此应力保持常数,而该物体将继续发生变形,这一现象称为蠕变。
若一个物体承受循环载荷,加载时的应力应变关系通常与卸载过程的应力应变关系存在某些差异,这一现象称为滞后[3]。
许多材料表现出滞后,松弛和蠕变的性质。
三者统称为粘弹性特征。
线性粘弹性模型中,以Kelvin模型、Maxwell模型和Poynting-Thomson模型最为基本或传统,其它模型则均是在上述模型的基础上派生组合而成。
这些模型都是由弹性常数µ的线性弹簧与粘性系数η的阻尼器组合构成。
因而,通过这三种传统粘弹性模型,可以得出粘弹性模型比较一般性的特点[4]。
Maxwell模型表达的思想是:
所有的流体在某种程度上都是弹性的。
Kelvin曾指出,在各种承受循环载荷的材料中,计及能量耗散率时,Maxwell模型和Voigt模型都不完善。
通常称Kelvin模型为标准线性模型,因为它包含了载荷,伸长和它们的一阶(通常叫做“线性”)导数的最一般关系式[5]。
Kelvin模型由弹簧(E)与粘性元件(η)并联而成,其本构方程式为:
σ=Eε+ηε(1.1)
Maxwell模型由弹簧(E)与粘性元件(η)串联而成,其本构方程式为:
(1.2)
Poynting-Thomson模型由弹簧(E2)与粘性元件(η)串联后再与弹簧(E1)并联而成,其本构方程式为:
(1.3)
非线性粘弹性模型,就本构方程式的形式而言,类型也较多,这里将写出的是基于近年试验结果提出的可变量本构方程式,该本构方程式构成如下:
(1.4)
(1.5)
1.2.手指力学研究现状
1.2.1国内外研究现状
粘弹性是材料的长期力学行为,同时也是高温等特殊条件下材料的一个重要性能指标[6]。
对粘弹性的研究是建立在适当的模型基础之上,建立和改进模型需要依据实验结果,实际设计需要有关数据与设计参数,因此近年来粘弹性实验研究受到学者们的普遍关注。
近几年来无论从复合材料的细观结构还是宏观角度,国内外学者都对复合材料的粘弹性和相关性能进行了大量卓有成效的研究工作。
从研究方式上讲大体可分为三类:
一是理论研究,建立理论模型,如laws和Mclaughin运用自洽方法导出复合材料的蠕变柔量的表达式;S.Maghous.GJ.Gerus在时间域中运用均匀化方法,得到了粘弹性多层材料的有效松弛模量的表达式;二是蠕变实验研究,如Hashin针对某些碳纤维复合材料界面情况,考虑界面材料剪切行为服从Maxwel模型,利用实验研究了这种粘弹性界面对纤维增强复合材料和颗粒增强复合材料有效性能的影响;三是结合试验数据建立有限元计算模型,进行计算机模拟,如Brock一enbrough等人应用有限元方法考察了纤维的排列方式对复合材料的总体粘弹性和塑性性能的影响[7]。
1.2.2目前主要存在的问题
生命运动是包括机械运动,电磁运动,化学运动等在内的多种运动形式的综合,而以位移为特征的机械运动规律的研究,是力学的本分。
因此,对生命现象的认识,必然涉及很多力学问题,这就是生物力学的主题[8]。
因为生物组织具有粘弹性的特征,因此粘弹性模型在生物力学中特别有用。
在实验室里确定松弛曲线和蠕变曲线十分容易[9]。
若使用合适的实验机,也很容易确定出承受周期力作用的材料的复数模量。
正确选择与实验数据相符合的模型是关键问题。
流体力学和固体力学的数目繁浩的文献,大体上都是以理想方程为根据。
而在生物界,材料的性能一般并不符合这些简单的关系式[10]。
因此,通过材料实验以确定用简化的本构方程式表述生物材料的性能,准确到怎样的程度,就是十分重要的了。
可能除过以下的三个方面外,生物材料的力学特性实验与工业材料的实验在原则上并无差别:
(1)取得生物材料的大试样的可能性极少;
(2)必须严格留意使试样保持活性,并使其尽量保持活体状态;(3)很多生物材料是不均匀的。
由于有这些特点,常常需要特殊的实验方法和设备[11]。
1.3论文研究题目的提出
为了研究人类手指的粘弹性特征,我们需要进行对人类手指的应力测量,由于人类手指的结构复杂,论文的任务是设计出一个可以精确测量人类手指变形和受力的测量装置。
2总体结构设计及传感器选型
2.1测量装置总体结构设计
该测量装置由力学传感器、步进电机和升降机构等组成。
其结构如图2.1所示。
手指放在下平台上,传感器等测量装置固定在升降机构上,升降机构沿Z方向运动。
测量平台如图2.1所示:
图2.1手指力学测量装置结构图
测量时,将手指放在下平台上,调节好手指与上平台之间的距离,然后通过电机控制平台下压,力传感器即开始对手指所受的力进行测量。
力传感器与配套的控制器相连,控制器通过USB总线或RS232-C总线与PC相连。
测量装置的控制主要是对步进电机的控制。
装置的主体是一个步进电机,步进电机通过联轴器与丝杠相连,步进电机驱动丝杠转动,带动升降机构做Z方向运动。
2.2力传感器的选型
力传感器选用-SBC系列精巧的按钮式微型压力传感器,在这里采用了SBC100型微型压力传感器,该传感器小巧轻便,不锈钢材质,NIST校准证书,具有测量精度高、稳定性能好、温度漂移小、输出对称性好、结构紧凑,规格齐全。
其外型图及硬件条件分别如图2.2及表2.1所示:
图2.2SBC100型微型压力传感器外型图
表2.1SBC100型微型压力传感器硬件条件
量程
0.5、1、2、3、5KG
综合精度
0.05%F·S
灵敏度
1±0.1mV/V
蠕变
±0.05 %F·S/30min
非线性
±0.05%F·S
滞后误差
±0.05%F·S
重复性误差
±0.05%F·S
零点温度系数
±0.05%F·S/10℃
输出温度系数
±0.05%F·S/10℃
输入阻抗
700±15Ω
输出阻抗
650±15Ω
绝缘电阻
≥5000MΩ
供桥电压
建议10VDC(标准信号12V24V)
工作温度范围
-20-+70℃
允许过负荷
150%F·S
密封等级
IP67
材质
合金铝
接口
M6
传感器接线说明
电源正:
红电源负:
绿
输出正:
黄输出负:
白
力传感器尺寸图分别如图2.3所示:
图2.3SBC100型微型压力传感器外型尺寸图
3测量装置机械结构的设计
3.1机械结构的设计
在测量装置的结构设计中,最主要的就是直线运动的设计,其结构图如图3.1所示,步进电机通过联轴器直接驱动丝杠,减少了中间传动环节,可提高精度[12],丝杠螺母副将丝杠转化为螺母的直线运动,带动滑块机构沿导轨做Z轴方向的运动。
图3.1测量装置外型图
3.1.1丝杠螺母副的选择
螺旋传动是利用螺杆和螺母组成的螺旋副来实现传动要求的。
他主要用于将回转运动转化为直线运动或将直线运动转化为回转运动,同时传动运动或动力。
螺旋运动根据螺纹副的摩擦情况,可以分为三类:
滑动螺旋,滚动螺旋和静压螺旋[13]。
滑动螺旋构造简单。
加工方便,易于自锁,但摩擦大,效率低(一般为30%~40%),磨损快。
低速时可能爬行,定位精度和轴向刚度较差。
静压螺旋实际上是采用静压流体润滑的滑动螺旋。
静压螺旋传动效率可达99%,但结构复杂,需要供油系统。
滚珠丝杠传动是滚动螺旋传动的一种。
他具有以下优点:
(1)传动效率高。
滚珠丝杠传递系统的效率高达90%~98%,为传统的滑动丝杠系统的2~4倍,所以能以较小的转矩获得较大的推力。
(2)运动平稳。
滚珠丝杠传动系统为点接触滚动运动,工作中摩擦阻力小,灵敏度高,启动是无颤动。
低速时无爬行现象,因此可精密的控制微量进给。
(3)高精度。
滚珠丝杠传动系统中温升较小,并可预紧消除轴向间隙和对丝杠进行预拉伸以补偿热伸长。
因此可以获得较高的定位精度和重复定位精度。
(4)高耐用性。
刚球滚动接触处均经硬化(HRC58~63)处理,并经精密磨削,运动过程属纯滚动,小队磨损甚微,故具有较高的使用寿命和精度保持性。
(5)高可靠性。
与其他传动机械,液压传动相比,滚珠丝杠传动系统故障率很低,维修保养也较简单,只需进行一般的润滑和防尘,还可在许多特殊场合下工作。
滚珠丝杠螺母副是数控机床中回转运动转换为直线运动常用的传动装置。
它以滚珠的滚动代替丝杆螺母副中的滑动,摩擦力小,具有良好的性能。
它的特点有:
(1)传动效率高:
机械效率可高达92%~98%。
(2)摩擦力小:
主要是用滚珠的滚动代替了普通丝杆螺母副的滑动。
(3)轴向间隙可消除:
也是由于滚珠的作用,提高了系统的刚性。
经预紧后可消除间隙。
(4)使用寿命长、制造成本高:
主要采用优质合金材料,表面经热处理后获得高的硬度。
除此之外,目前很多厂家的滚珠丝杠产品已形成系列且规格齐全,方便选用。
鉴于此,我选择滚珠丝杠来构建平台。
丝杠的相关计算如下:
(1)确定滚珠丝杠副的导程:
(3.1)
式中:
——滚珠丝杠副的导程,单位为mm
——工作台最大移动速度,单位为mm/min
——电机最大转速,单位为r/min
——电机至丝杠的传动比
假设工作台最大移动速度为20mm/s,即1200mm/min。
初步选择步距角为
的步进电机,这一系列的步进电机工作频率在1000pps~3000pps之间,取3000pps。
则电机最大转速
=450r/min(3.2)
(3.3)
查阅优励聂夫滚珠丝杠尺寸标准,选取丝杠导程为4mm。
(2)丝杠螺母副的预紧
常见的消除间隙和预紧的方法有以下三种结构形式。
1)垫片消隙式。
采用垫片式消隙和预紧的结构原理,用螺钉连接滚珠丝杠两个螺母的凸缘,在凸缘间加垫片。
调整垫片的厚度使螺母产生轴向位移,以达到消隙和产生预紧力的目的。
这种结构的特点是结构简单,可靠性好,刚度高,装卸方便。
但调整费时,很难在一次修磨中调整完成,除非更换不同厚度的垫片,故仅适用与一般精度的数控机床。
2)螺纹消隙式。
这种结构简单可靠,工作可靠,调整方便,故应用较多。
但调整精度较差,预紧力不能准确控制。
3)齿差消隙式。
这种调整方式的结构较为复杂,尺寸较大,但调整精确可靠,不会松动。
故目前在数控机床上应用较广。
滚珠丝杠副的轴向间隙,是指在无负载情况下的原始轴向间隙,和在负载作用下由于滚珠与滚道型面接触点的弹性变形,而引起螺母轴向位移量的总和。
预紧是为了消除滚珠丝杠副的轴向间隙并提高其刚度,最终是为了达到定位精度的需要。
预紧的方法有很多种,最普遍和常用的是双螺母结构,在两个螺母之间配有垫片来达到预紧。
双螺母预紧方式如图所示,在一根丝杠上装两个螺母,通过垫片对其施加一定的预紧力Fa0.使滚珠与滚道接触处产生一定的预变形,这样,滚珠丝杠副不论在哪一个方向承受轴向力,只有轴向力的大小在一定范围内,滚珠丝杠螺母副间都不会出现轴向间隙。
还有一种预紧是在单螺母和丝杠间通过控制中径,并调节增大刚球直径,从而实现预紧目的。
四点接触预紧方式如图3.2与图3.3所示。
图3.2双螺母预紧
图3.3四点接触式预紧方式
本测量装置选用双螺母预紧方式。
查优励聂夫滚珠丝杠尺寸标准,导程4mm,底径9.5mm的丝杠,其额定动载荷Ca为4380N。
根据下面公式可计算预紧载荷Fao:
(3.4)
其中ζ为预紧系数,其值可查表3.1
表3.1预紧系数表
载荷类型
轻载荷
中载荷
重载荷
0.05
0.07
0.1
本装置中的丝杠承受轻载荷,故取ζ=0.05,则得预紧载荷
Fao=0.05*4380=219N(3.5)
丝杠结构图如图3.4所示:
图3.4丝杠结构图
3.1.2滚珠丝杠的支承方式选择
滚珠丝杠的支承方式主要有四种:
(1)两端固定。
这种支承方式适用于高转速,高精度的情况,其结构如图3.5所示:
图3.5两端固定方式
(2)一端固定,一端支承。
适用于中等转速,高精度的情况,其结构如图3.6所示:
图3.6一端固定,一端支承方式
(3)两端支承。
适用于中等转速,中等精度的情况,其结构如图3.7所示:
图3.7两端支承方式
(4)一端固定,一端自由。
适用于低转速,中精度,短轴丝杠,其结构如图3.8所示:
图3.8一端固定,一端自由方式
本文选择两端固定的支承方式。
固定端具体结构如图3.9所示:
图3.9固定端剖视图
3.1.3轴承的选择
与滑动轴承比较,滚动轴承有下列优点:
(1)摩擦系数小,启动力矩小,效率高(与混合润滑滑动轴承比较)。
(2)径向游隙小,还可用预紧方法消除游隙,因此运转精度高。
(3)轴向尺寸(宽度)较小,可使机器的轴向尺寸紧凑。
(4)某些滚动轴承能同时承受径向与轴向载荷,因此可使机器结构简化,紧凑。
(5)润滑简单,耗油量少,便于密封,易于维护。
(6)为标准件,互换性好,易于选用与更换,且成本较低。
各种结构类型轴承由于不同的结构特性,可适应于不同的使用条件,设计人员可根据自己的需要进行选择。
通常选择轴承类型时应综合考虑下列各主要因素:
(1)载荷情况:
载荷是选择轴承最主要的依据,通常应根据载荷的大小、方向和性质选择轴承。
(2)载荷大小:
一般情况下,滚子轴承由于是线接触,承载能力大,适于承受较大载荷;球轴承由于是点接触,承载能力小,适用于轻、中等载荷。
各种轴承载荷能力一般以额定载荷比表示。
(3)载荷方向:
纯径向力作用,宜选用深沟球轴承、圆柱滚子轴承或滚针轴承,也可考虑选用调心轴承。
纯轴向载荷作用,选用推力球轴承或推力滚子轴承。
径向载荷和轴向载荷联合作用时,一般选用角接触球轴承或圆锥滚子轴承,这两种轴承随接触角。
增大承受轴向载荷能力提高。
若径向载荷较大而轴向载荷较小时,也可选用深沟球轴承和内、外圈都有挡边的圆柱滚子轴承。
若轴向载荷较大而径向载荷较小时,可选用推力角接触球轴承、推力圆锥滚子轴承。
(4)载荷性质:
有冲击载荷时,宜选用滚子轴承。
(5)高速性能:
一般摩擦力矩小、发热量小的轴承高速性能好。
球轴承比滚子轴承有较高的极限转速,故高速时应优先考虑选用球轴承。
径向载荷小时,选用深沟球轴承:
径向载荷大时,选用圆柱滚子轴承。
对联合载荷,载荷小时,选用角接触球轴承;载荷大时,选用圆锥滚子轴承或圆柱滚子轴承与角接触球轴承组合。
在相同内径时,外径越小,滚动体越轻越小,运转时滚动体作用在外圈上的离心力也越小,因此更适于较高转速下工作。
保持架的材料与结构对轴承转速影响很大。
实体保持架比冲压保持架允许的转速高。
高速重载的轴承需验算其极限转速。
(6)轴向游动性能:
一般机械工作时,因机械摩擦或工作介质的关系而使轴发热,从而有热胀冷缩产生。
在选择轴承结构类型时,应使其轴有铀向游动的可能性。
因此,常在轴的某一端选用一内圈或一外圈无挡边的圆柱滚子轴承或滚针轴承,以适应由于热胀冷缩而引起轴的伸长或缩短。
(7)调心性能:
当轴两端轴承孔同轴性差(制造误差或安装误差所致)或轴的刚度小,变形较大,以及多支点轴,均要求轴承调心性好,这时应选用调心球轴承或调心滚子轴承。
(8)允许的空间:
在机械设计中,一般都是先确定轴的尺寸,然后根据轴的尺寸来确定轴承的尺寸。
(9)安装与拆卸方便:
对于轴承使用寿命一般都难以等同主机使用寿命,在实际使用中轴承作为易损件要经常装拆。
因此,在选用轴承结构类型时应要求装拆方便。
可分离型的角接触球轴承、圆柱滚子轴承。
圆锥滚子轴承、推力轴承和内圈为锥孔、带紧定套或退卸套的调心滚子轴承、调心球轴承等均具有装拆方便性能。
除上述因素外,还应考虑轴承的工作环境温度、轴承密封及对摩擦力矩、振动、噪声等的特殊要求。
滚动轴承广泛应用于中速,中载和一般工作条件下运转的机械设备中。
仪器精密轴承多为微型深沟球轴承。
本测量装置要求精度较高,且所用轴承主要承受径向载荷,故选用深沟球轴承。
查《机械设计手册》,根据GB/T276-1994,选择内径为8的60000型深沟球轴承,轴承代号为628。
轴承结构图如图3.10所示:
图3.10轴承结构图
3.1.4导轨的选择
导轨主要是用来保证各运动部件的相对位置和和相对运动精度,以及用来承受载荷(包括工作台、滑板部件的重量)[14]。
依定位原理,在结构设计时必须限制运动件的5个自由度,而仅保留其按规定方向移动的自由度[15]。
对导轨的基本要求为:
方向精度——运动件沿规定方向做直线运动的准确程度,它取决于导轨本身的直线度;
运动的灵便型和平稳性——主要取决于导轨中的摩擦力和导轨表面的几何形状误差;
对温度变化的不敏感性——当温度变化时导轨仍能正常工作,即不“卡死”又不晃动;
耐磨性——导轨在长时间使用后不降低精度。
它主要取决于相配材料、导轨表面粗糙度及表面硬化;
结构工艺性——导轨应在保证仪器工作性能的条件下,结构简单、加工方便、装修简易、造价低。
按摩擦性质分,导轨可分为滑动摩擦导轨、滚动摩擦导轨和弹性摩擦导轨。
滑动导轨是支承件和运动件直接接触的导轨,优点是结构简单、制造容易且接触刚度大。
缺点是摩擦阻力大,磨损快。
滑动摩擦导轨按承导面形状可分为两类:
圆柱面滑动摩擦导轨和棱柱面滑动摩擦导轨。
圆柱面滑动摩擦导轨的承导面是圆柱面。
它的主要优点是承导面的加工和检验比较简单,易于达到较高的精度。
单一的圆柱面导轨运动件除可沿其轴线做直线运动外,还可绕其轴线运动,但这种转动必须消除。
通常情况下多采用双圆柱形式,它既能保证定位的要求。
又同时能保证较好的承载能力。
考虑到圆柱导轨工艺性较好且本测量装置负载较轻,本装置选用双圆柱导轨形式。
3.1.5联轴器的选择
联轴器的选择主要考虑所需传递轴转速的高低、载荷的大小、被联接两部件的安装精度等、回转的平稳性、价格等,参考各类联轴器的特性,选择一种合用的联轴器类型。
具体选择时可考虑以下几点:
(1)由于制造、安装、受载变形和温度变化等原因,当安装调整后,难以保持两轴严格精确对中。
存在一定程度的x、y方向位移和偏斜角C1。
当径向位移较大时,可选滑块联轴器,角位移较大或相交两轴的联接可选用万向联轴器等。
当工作过程中两轴产生较大的附加相对位移时,应选用挠性联轴器。
(2)联轴器的工作转速高低和引起的离心力大小。
对于高速传动轴,应选用平衡精度高的联轴器,例如膜片联轴器等,而不宜选用存在偏心的滑块联轴器等。
(3)所需传递的转矩大小和性质以及对缓冲振动功能的要求。
例如,对大功率的重载传动,可选用齿式联轴器。
对严重冲击载荷或要求消除轴系扭转振动的传动,可选用轮胎式联轴器等。
绝大多数联轴器均已标准化或规格化(见有关手册)。
设计者的任务是选用,而不是设计。
选用联轴器的基本步骤如下:
选择联轴器的类型:
根据传递载荷的大小,轴转速的高低,被联接两部件的安装精度等,参考各类联轴器特性,选择一种合用的联轴器类型。
具体选择时可考虑以下几点:
(1)所需传递的转矩大小和性质以及对缓冲减振功能的要求。
例如,对大功率的重载传动,可选用齿式联轴器;对严重冲击载荷或要求消除轴系扭转振动的传动,可选用轮胎式联轴器等具有高弹性的联轴器。
(2)联轴器的工作转速高低和引起的离心力大小。
对于高速传动轴,应选用平衡精度高的联轴器,例如膜片联轴器等,而不宜选用存在偏心的滑块联轴器等。
(3)两轴相对位移的大小和方向。
当安装调整后,难以保持两轴严格精确对中,或工作过程中两轴将产生较大的附加相对位移时,应选用挠性联轴器。
例如当径向位移较大时,可选滑块联轴器,角位移较大或相交两轴的联接可选用万向联轴器等。
(4)联轴器的可靠性和工作环境。
通常由金属元件制成的不需润滑的联轴器此较可靠;需要润滑的联轴器,其性能易受润滑完善程度的影响,且可能污染环境。
含有橡胶等非金属元件的联轴器对温度、腐蚀性介质及强光等比较敏感,而且容易老化。
(5)联轴器的制造、安装、维护和成本。
在满足便用性能的前提下,应选用装拆方便、维护简单、成本低的联轴器。
例如刚性联轴器不但结构简单,而且装拆方便,可用于低速、刚性大的传动轴。
一般的非金属弹性元件联轴器(例如弹性套柱销联轴器、弹性柱销联轴器、梅花形弹性联轴器等),由于具有良好的综合能力,广泛适用于一般的中、小功率传动。
本测量装置将电机轴与丝杠直接相连,减少了中间传动环节,可提高测量装置的精度。
联轴器是连接两轴或轴和回转件,在传递转矩和运动过程中一同回转而不脱开的一种装置,在传动过程中不改变转动方向和转矩的大小,这是各类联轴器的共性功能。
联轴器连接的两轴,由于制造及安装误差,承载后的变形以及温度变化的影响等,往往不能保证严格的对中,而是存在着某种程度的相对位移,相对位移的基本形式如图3.11所示:
图3.11被连接两轴相对位移基本形式
图中,
(1)表示两轴平行但中心线不在同一直线上,这时产生的偏差称为径向偏差。
(2)表示安装时两轴互成一个角度,这时产生的偏差称为角向偏差。
(3)表示由于机械原因产生的轴间往复微动的偏差,称为轴向偏差。
(4)表示的是前述三种偏差的组合,称为复合偏差。
相对位移的存在,要求在设计联轴器时,要从结构上采取各种不同的措施,使之具有适应一定范围的相对位移的性能。
根据对各种相对位移有无补偿能力(即能否在发生相对位移条件下保持联接的功能),联轴器可分为刚性联轴器(无补偿能力)和挠性联轴器(有补偿能力)两大类。
挠性联轴器又可按是否具有弹性元件分为无弹性元件的挠性联轴器和有弹性元件的挠性联轴器两个类别。
挠性联轴器因其具有挠性,故可在不同程度上补偿两轴间某种相对位移。
挠性联轴器品种多,用量大,是最常用的联轴器。
十字滑块联轴器属于挠性联轴器[16]。
十字滑块联轴器由两个在端面上开有凹槽的半联轴器和一个两面带有凸牙的中间盘组成。
因凸牙可在凹槽中滑动,故可补偿安装及运转时两轴间的相对位移。
十字滑块联轴器结构如图3.12所示:
图3.12十字滑块联轴器结构图
十字滑块联轴器适用于多种场合,如转速计、编码器、丝杠、机床、产业机械等。
其优点是结构简单,使用方便、容易安装、节省时间、尺寸范围广、转动惯量小,便于目测检查,可电气绝缘等。
半联轴器和中间盘之间的滑动能容许大的径向和角向偏差。
联轴器的固定方式有如下几种:
(1)定位螺丝固定:
两个定位螺丝间隔90°对所固定的轴进行锁紧,是一种传统的固定方式。
(2)夹紧螺丝固定:
利用内六角螺栓拧紧的力量,使狭缝收缩,而将轴心紧紧夹持住。
(3)键槽型:
这种类型与定位螺丝固定型