管状零件内孔的表面粗糙度测量装置设计方案.docx
《管状零件内孔的表面粗糙度测量装置设计方案.docx》由会员分享,可在线阅读,更多相关《管状零件内孔的表面粗糙度测量装置设计方案.docx(34页珍藏版)》请在冰豆网上搜索。
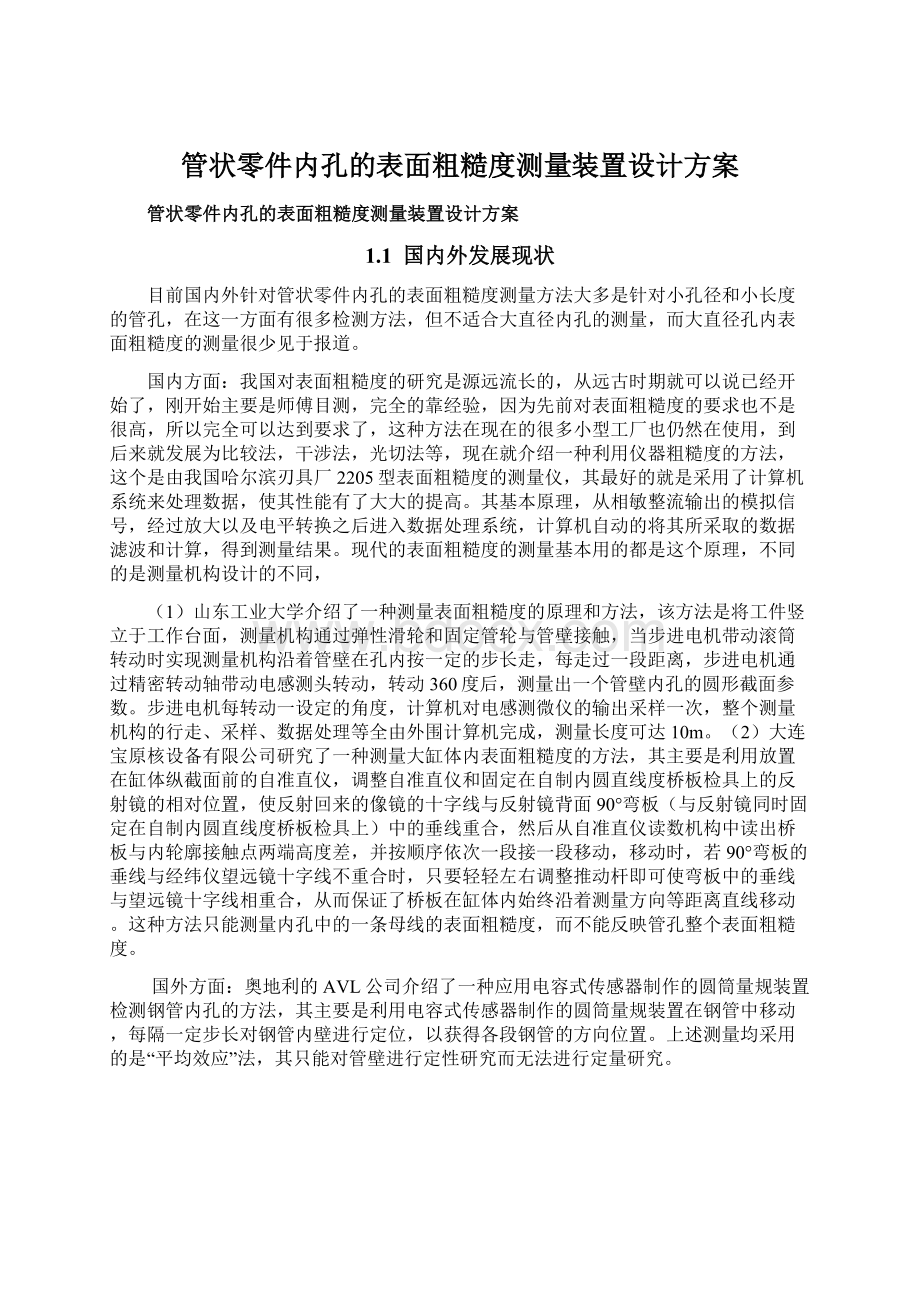
管状零件内孔的表面粗糙度测量装置设计方案
管状零件内孔的表面粗糙度测量装置设计方案
1.1国内外发展现状
目前国内外针对管状零件内孔的表面粗糙度测量方法大多是针对小孔径和小长度的管孔,在这一方面有很多检测方法,但不适合大直径内孔的测量,而大直径孔内表面粗糙度的测量很少见于报道。
国内方面:
我国对表面粗糙度的研究是源远流长的,从远古时期就可以说已经开始了,刚开始主要是师傅目测,完全的靠经验,因为先前对表面粗糙度的要求也不是很高,所以完全可以达到要求了,这种方法在现在的很多小型工厂也仍然在使用,到后来就发展为比较法,干涉法,光切法等,现在就介绍一种利用仪器粗糙度的方法,这个是由我国哈尔滨刃具厂2205型表面粗糙度的测量仪,其最好的就是采用了计算机系统来处理数据,使其性能有了大大的提高。
其基本原理,从相敏整流输出的模拟信号,经过放大以及电平转换之后进入数据处理系统,计算机自动的将其所采取的数据滤波和计算,得到测量结果。
现代的表面粗糙度的测量基本用的都是这个原理,不同的是测量机构设计的不同,
(1)山东工业大学介绍了一种测量表面粗糙度的原理和方法,该方法是将工件竖立于工作台面,测量机构通过弹性滑轮和固定管轮与管壁接触,当步进电机带动滚筒转动时实现测量机构沿着管壁在孔内按一定的步长走,每走过一段距离,步进电机通过精密转动轴带动电感测头转动,转动360度后,测量出一个管壁内孔的圆形截面参数。
步进电机每转动一设定的角度,计算机对电感测微仪的输出采样一次,整个测量机构的行走、采样、数据处理等全由外围计算机完成,测量长度可达10m。
(2)大连宝原核设备有限公司研究了一种测量大缸体内表面粗糙度的方法,其主要是利用放置在缸体纵截面前的自准直仪,调整自准直仪和固定在自制内圆直线度桥板检具上的反射镜的相对位置,使反射回来的像镜的十字线与反射镜背面90°弯板(与反射镜同时固定在自制内圆直线度桥板检具上)中的垂线重合,然后从自准直仪读数机构中读出桥板与内轮廓接触点两端高度差,并按顺序依次一段接一段移动,移动时,若90°弯板的垂线与经纬仪望远镜十字线不重合时,只要轻轻左右调整推动杆即可使弯板中的垂线与望远镜十字线相重合,从而保证了桥板在缸体内始终沿着测量方向等距离直线移动。
这种方法只能测量内孔中的一条母线的表面粗糙度,而不能反映管孔整个表面粗糙度。
国外方面:
奥地利的AVL公司介绍了一种应用电容式传感器制作的圆筒量规装置检测钢管内孔的方法,其主要是利用电容式传感器制作的圆筒量规装置在钢管中移动,每隔一定步长对钢管内壁进行定位,以获得各段钢管的方向位置。
上述测量均采用的是“平均效应”法,其只能对管壁进行定性研究而无法进行定量研究。
1.2发展趋势与展望
表面粗糙度误差在测量技术是保证零件质量和提高生产率的重要手段,在机械加工中扮演着十分重要的角色.随着计算机测控技术的发展,出现了以单片机、工业控制机和PLC为控制实体的全新的机电一体化测量仪器与在线测量系统。
当然在测量技术还有许多问题亟待解决.如高准确度传感器的研制,测量策略和数据处理策略的优化等,对大型长类零件的测量更是存在一定的问题.随着这些问题的解决,测量技术会有更光明的应用前景。
当前,几何量的趋势是向大量程、高分辨率、动态、自动化、多功能等方向发展.具体的说有以下四点:
(1)提高测长仪器的分辨率,这是提高其相对计量准确度的必要前提;
(2)应用光电和电视技术,光电显微镜最初用于几何量的镜态测量,后来研制成功光点显微镜,显已制成动静两用的光电显微镜;
(3)发展新的光干涉与光信息处理技术;
(4)微处理机用几何量计量仪器,不仅是采集和处理数据,而正在向实时控制和人工智能方向发展,使几何量计量朝着动态、自动、综合、多参数和多功能方向发展,例如坐标计量机。
1.3形状误差测量的定义和方法
1.3.1形状误差的定义
形状误差是指被测实际要素对其理想要素的变动量。
形状误差包括直线度误差、平面度误差、表面粗糙度误差、圆弧度误差、线轮廓度误差和面轮廓度误差。
1.3.2形状误差测量
对形状误差进行测量是认识工件形状质量状况的基本手段。
通过测量,应达到以下两个目的,第一是判断所测量工件是否符合给定的精度要求,即判别其是否合格;第二是根据测量结果,分析和寻找产生形状误差的原因,以便改进有关设计和工艺,使工件的加工精度不断提高。
对测量过程和测量结果的两个方面的要求,一是精确要求,即测量结果必须达到一定的可信度;二是经济性要求,即在保证测量结果精确的前提下,应是测量过程简单、经济、所花代价最小。
要想使形状误差的测量达到上述目的,并符合上述要求,则必须在测量的过程中完成如下任务:
第一,根据工件的精度要求选择相应的测量方法,以满足精确性和经济性要求;第二,按照选定的方法对被测要素进行测量,获得观测数据。
在可能的情况下,直接根据观测数据判断工件是否合格,如不能直接判断,则按照一定的评定方法对观测数据进行数据处理,以评定出形状误差的大小。
1.3.3形状误差的评定方法
在评定被测实际要素的形状误差时,首先应确定其理想要素的位置,因为理想要素的位置不同,所得形状误差值也不同。
国家标准规定,在确定理想要素的位置时,应符合最小条件。
所谓最小条件,使被测实际要素对其理想要素的最大变动量为最小。
但在实际测量评定时,人们从精确性、经济性等不同的角度出发,除采用符合最小条件的最小包容区域法外,还是用了其它几种评定方法,如最小二乘法,粘切法和简易法等。
1.3.3.1最小包容区域法
最小包容区域法(图1-1)是按最小条件来确定理想要素位置的,即用两个等距的理想要素包容被测量实际要素,并使两理想要素之间的最小距离为最小。
这时理想要素的位置符合最小条件,两理想要素之间的距离使用最小包容区域法评定出的形状误差。
即误差
(1—1)
M---仪器放大倍数。
图1-1最小包容区域法
1.3.3.2最小二乘法
在最小二乘法中,理想要素的位置是这样确定的,即使被测实际要素上各点到理想要素的距离的平方和为最小。
按这个原则确定了理想要素的位置后,离开理想要素两侧的被测实际要素上两最远点到理想要素的距离之和即为用最小二乘法评定出的形状误差。
即误差
或
(1—2)
M---仪器放大倍数。
图1-2最小二乘法
1.3.3.3贴切法
(1)粘切法是以粘切要素作为理想要素对形状误差进行评定的一种方法。
粘切要素有以下几种。
(2)贴切直线贴切直线是在零件外表面与实际线相切的某一理想直线。
在规定范围内,它与实际直线之间的最大距离应为最小。
(3)贴切平面贴切平面实在零件外表面与实际表面相切的某一理想平面,在规定范围内,它与实际表面的最大距离应为最小。
(4)贴切圆对于外圆表面,贴切圆是指与实际圆外接且直径为最小的理想圆;对于内圆表面使之与实际圆内切且直径为最大的理想圆。
(5)贴切圆柱面对于外圆柱面,贴切圆柱面是与实际外圆柱表面外接且直径为最小的理想圆柱面;对于内圆柱面,贴切圆柱面始于实际内圆柱表面内切且直径为最大的理想圆柱面。
贴切圆柱面与实际圆柱面之间的最大距离为用贴切法评定出的圆柱度误差。
1.3.3.4简易法
简易法是在生产实践中总结出来并广泛使用的一种方法,它的特点是能简便、快速地确定理想要素的位置。
对不同的评定对象,有不同的简易评定方法。
如评定直线度误差时可采用二端点连线法,即以被测直线首尾两点的连线作为理想直线的位置;评定平面误差时,可采用三点法和对角线法确定理想平面的位置等等。
简易法一般用于评定精度要求不很高的场合。
图1-3简易法
用不同的评定方法评定形状误差时,由于理想要素位置不同,评定出的形状误差值也不同。
当由于采用不同的评定方法导致对被测零件的合格与否发生争论时,应按最小包容区域法进行仲裁。
本设计中采用最小二乘法比较合适。
1.4大直径筒体内孔表面粗糙度误差测量装置的设计
本次设计的是对内圆截面尺寸精度要求比较高的零件的测量,都应以表面粗糙度来控制,本测量装置建立被测量件固定在工作台上,在工作台上有支架,支架上有一轴,轴上安装有位移传感器的测头进行测量。
对本次的测量装置初步设计了二个测量表面粗糙度的方案:
(1)方案一:
将工件固定在圆形工作台上,工作台上安装有可以自动升缩式的支架(如图a),通过支架的升缩可以将安装在其上的测量装置放入工件筒内,然后在相关电动力作用下工作台旋转从而使工件旋转和上下移动,测量部分固定不动,测量部分对内壁进行测量,再将相关数据输送给计算机进行数据处理以完成测量。
(2)方案二:
将工件固定在工作台上(如图b),电机直接将测量装置放入工件筒内,待到达测量位置时,启动固定测量装置的支撑系统,然后再启动测量机构进行表面粗糙度测量,数据则通过测量机构上的传感器将数据传给计算机进行数据处理以完成测量工作。
ab
图1-4方案图
若采用方案一,由于是杆的升缩,所以对较长的工件安装不方便,而且设计制造比较麻烦,同时由于是工作台的旋转带动工件旋转进行测量使得测量部分和工件同心较困难,测量误差较大;对于方案二,这种装置使用较方便,三脚定位保证了同心度从而使测量精度高,设计制造也比较容易。
2总体方案设计
2.1本设计方案
通过上面的分析和研究,本设计在满足测量精度的前提下,从测量的简易性,经济性角度出发,拟定出两个方案,并且进行了分析比较。
本测量装置的结构简图2-1
图2-1装置结构简图
测量原理:
事先依次给计算机输入筒体内孔被测位置数;电机运转顺序号等相关参数,然后计算机会按照事先的约定依次控制电机1运动,将测量装置送入被测件内,为了防止装置摆动,在其上设计了三个平衡撑脚,当测量装置放到合适的位置时1号电机停止工作,与此同时2号步进电机被启动带动撑脚运动,使得三个撑脚各相差1200同时向外伸出将测量装置固定到了被测筒体内表面上;随后计算机将启动测量机构电机3使传感器测头与被测件接触,当传感器测头与被测件一旦接触,传感器立刻将此信息反馈给计算机,使计算机就会立即停止,测量前的准备工作就绪。
计算机再次给电动机传出命令使传感器在电动机的带动下上下移动,数据采集器就会将所得数据采集后送入计算机,再由计算机处理并进行误差分析后得出测筒体被孔的表面粗糙度误差了。
起动电机2将撑脚收位后,用同样方法可测多个截面的表面粗糙度误差值。
2.2撑脚的设计
本设计中,撑脚的主要功能是固定,将测量部分固定在筒体内,以便测头在测量部分固定的情况下进行旋转测量.即在Y工作台上装有被测件的夹具,将筒体固定在夹具上。
测量前,有电动机带动旋转轴将测量部分送入筒体内某一位置,进行固定。
测头部分和旋转轴之间是通过绳子连接的。
固定是通过三个撑脚进行固定的。
固定过程中,撑脚先是在测头部分内部,撑脚上安装有齿条。
电动机端部安装有齿轮.在电动机作用下,齿轮带动齿条进行运动使撑脚向外伸出。
同时在撑脚端部安装有传感器,当碰到壁时在传感器反馈到电机,电机立即停止运转。
固定后,测杆在电机的作用下伸出,当测头碰到壁时在传感器反馈到电机,电机立即停止.再启动测头旋转电机,带动测头进行旋转,完成测量。
在测量完成对管内壁的一个圆截面的测量之后,由齿轮齿条装置将撑脚缩入.旋转轴将测头部分送到另一个位置,可以测量下一个内圆截面。
送入位置由旋转轴电机控制,给定一个脉冲,即送入一定深度,如此连续测量。
最后将测量结果由计算机数据采集系统进行分析处理。
撑脚端部通常设计成掌形,且为了控制其和内壁接触即停止,通常安装传感器.其结构初步设计为图2-2。
图2-2撑脚
其设计材料为45钢,左边的直径为7的孔被安放传感器的,轴上的孔是起齿条固定作用的.该撑脚具有刚性好,比较传统,易于制造等优点。
2.3齿条的设计
撑脚上的齿条设计:
通常在机械设计中,齿条的作用是它和齿轮一起作用将通常的旋转运动转变为直线运动.当然在本设计中,它的主要功能也是这个作用。
在设计时,齿条通常可以设计成整体型和合成型。
整体型时齿条是一个整体,中间开个孔或槽,安装在相关零件上。
合成型通常是将齿条分成几个部分,在安装时,将它们拼在一起,进行固定即可。
一般来说,合成型虽成本高一点,但在安装上比较方便。
在本设计中也比较适合选用合成型,如一段长度不够还可以另外再添加。
通过构思,其初步结构设计为图2-3。
图2-3撑脚上的齿条
该零件所选用的材料为45钢,它是由左右两半构成,在安装时将轴夹在中间,左右两半合成在一起,由螺栓固定。
传感器测杆上的齿条的设计:
传感器测杆上的齿条的设计思路和撑脚上的类似.所选用的也是合成型,材料为45钢。
它也是由左右两半构成,在安装时将轴夹在中间,左右两半合成在一起,由螺栓固定。
其结构初步设计与撑脚上的齿条设计一致。
2.4齿轮的设计
撑脚上的齿轮设计:
齿轮的作用是改变运动状态即传递动力,改变运动方向,边速等。
本设计中齿轮的作用是其和齿条作用将旋转运动变为直线运动。
经分析和思考其结构初步设计为下图2-5:
图2-5撑脚上的齿轮
其设计的材料为45钢,法向模数为2,齿数为15,分度圆直径为30,齿宽为15,直齿圆柱齿轮。
传感器测杆上的齿轮的设计:
传感器测杆上的齿条的设计思路和撑脚上的类似。
其设计的材料为45钢,法向模数为1,齿数为16,分度圆直径为16,齿宽为8,直齿圆柱齿轮。
其结构与撑脚上的齿轮一致。
2.5测量部分位置升降的设计
本次设计当中,测量机构是该装置的核心,其精度要求较高它应具有上下移动的功能。
为此我设计了本次测量机构,它是由最前段的传感器和悬臂,立臂等组成。
最前端的传感器可直接与被测元件接触,悬臂是将最前端的传感器支撑和固定,并且与立臂连接,实现测量机构上下的移动。
2.6滚轮部分的设计
在本设计中滚轮部分的作用是起将测量部分导入筒体内部的作用。
根据要求和分析,其结构初步设计为图2-7。
图2-7滚轮部分
左边的轴和右边的筒的材料均为45钢,它们是靠弹簧焊接在两边而联结起来的。
左边通过螺栓安装有滚子,导入时滚子可以滚动.当滚子受到壁压时弹簧压缩,腔内空气从小孔排出,轴部分进入筒。
2.7支架的设计
本设计中,支架的主要功能是支承,安装撑脚,滚轮部分,传感器旋转轴以及电机等零件,同时保证传感器旋转轴完成旋转运动。
经过分析,其初步设计结构如图2-8所示。
图2-8支架
支架的材料为铸铁,是通过铸造后再进行加工而得到的。
其结构尺寸如图上标注。
3电动机的选择与计算
3.1步进电机的概述
由于所设计的装置是开环控制系统,一般采用功率步进电动机,可直接驱动工作台由于反应式步进电机控制功率小,效率高,造价低,转子为永磁式,因而无力磁时也具有保持力。
根据本次设计转速较低的需要选用反应式步进电机。
当电动机绕组接收到一个脉冲时就转过一个相应的角度,即步距角.其角位移量和输入的脉冲数严格成正比,不会引起误差累积,在时间上与输入脉冲同步,只要控制输入脉冲的数量,频率和电动机绕组的相序,即可获得所需转角的转速和转动方向,由式
(3—1)
可知,反应式步进电机的转速值取决于脉冲频率,转子齿数和拍数,而与电压负载,温度等因素无关。
当步进电机的通电方式选定后,其转速只与输入脉冲频率成正比。
改变脉冲频率就可以改变速度,故可进行无级调速,调速范围很宽.同时,步进电机具有自锁能力,当控制点脉冲停止输入,而让最后一个脉冲控制的绕组继续通入直流时,则电动机可保持在固定的位置上,这样,步进电机可实现停车时转子定位。
步进电机转子齿数Z和定子相数(或运行拍数)越多,则步距角越小,控制越精确。
3.2步进电机的现状和发展趋势
3.2.1步进电机的现状
德国B.L.公司1994年五相混合式步进电动机专利期满后,推出了新的三相混合式步进电动机系列,为定子6极转子50齿结构,配套电流型驱动器,每转步数为200、400、1000、2000、4000、10000和20000,它具有通常的二相和五相步进电动机的分辨率,还可以在此基础上再10细分,分辨率提高10倍,这是一种很好的方案,充分运用了电流型驱动技术的功能,让三相电动机同时具有二相和五相电动机的性能。
⑴在获得小步距角方面,三相电动机比二相电动机要好。
⑵三相电动机的两相励磁最大保持力矩为√3T1(T1为单相励磁转矩),而二相电动机为 √2T1,所以三相电动机的合成力矩大。
⑶三相电动机的转矩波动比二相电动机要小。
⑷三相电动机连续2步用于半步的转矩差比二相电动机的要小。
⑸三相电动机绕组可以星形连接,三个终端驱动,励磁电路晶体管6个; 而二相电动机是8个。
⑹连续运转时,由于三相步进电动机结构原因,磁通和电流的三次谐波被消除了,所以三相电动机的振动力矩比二相电动机的要小。
结论是显而易见的。
另外的结论是HB型电动机更适合于低速大转矩用途;RM型适用于平稳运行以及转速大于1000r/min的用途;而PM型成本低,在低转速时的振动和高转速时的大转矩方面,三相PM型电动机比两相电动机的性能要好。
我国的情况有所不同,直到20世纪80年代,一直是磁阻式步进电动机占统治地位,混合式步进电动机是80年代后期才开始发展,至今仍然是二种结构类型同时并存。
尽管新的混合式步进电动机完全可能替代磁阻式电动机,但磁阻式电动机的整机获得了长期应用,对于它的技术也较为熟悉,特别是典型的混合式步进电动机的步距角(0.9°/1.8°)与典型的磁阻式电动机的步距角(0.75°/1.5°)不一样,用户改变这种产品结构不是很容易的,这就使得两种机型并存的局面难以在较短时间内改变。
这种现状对步进电动机的发展是不利的。
3.2.2步进电机的发展趋势
当前最有发展前景的当属混合式步进电动机,而混合式电动机又向以下四个方向发展:
(1)发展趋势之一,是继续沿着小型化的方向发展。
随着电动机本身应用领域的拓宽以及各类整机的不断小型化,要求与之配套的电动机也必须越来越小,在57、42机座号的电动机应用了多年后,现在其机座号向39、35、30、25方向向下延伸。
瑞士ESCAP公司最近还研制出外径仅10mm的步进电动机。
(2)发展趋势之二,是改圆形电动机为方形电动机。
由于电动机采用方型结构,使得转子有可能设计得比圆形大,因而其力矩体积比将大为提高。
同样机座号的电动机,方形的力矩比圆形的将提高30%~40%。
(3)发展趋势之三,对电动机进行综合设计。
即把转子位置传感器,减速齿轮等和电动机本体综合设计在一起,这样使其能方便地组成一个闭环系统,因而具有更加优越的控制性能。
(4)发展趋势之四,向五相和三相电动机方向发展。
目前广泛应用的二相和四相电动机,其振动和噪声较大,而五相和三相电动机具有优势性。
而就这两种电动机而言,五相电动机的驱动电路比三相电动机复杂,因此三相电动机系统的性能价格比要比五相电动机更好一些。
3.3步进电机的计算和选用
选用步进电机时,必须首先根据机械结构草图计算机械传动装置及负载折算到电机轴上的等效转动惯量.分别计算各种工况下所需的等效转动力矩,在根据步进电机的最大静转矩和启动矩频特性运行矩频特性,选择合适的步进电机.
3.3.1驱动测量部分升降的旋转轴的电机的选择:
3.3.1.1转动惯量计算
初步选择电机型号为75BF型,查技术手册表得所选电机的转子转动惯量为:
JM=0.13。
轴传动算到电机轴上的转动惯量:
J=0.78×0.84×21×10-3=0.0067(3—2)
所以,折算到电机轴上的总转动惯量为:
必须注意在上式中没有考虑电机转子本身的转动惯量,根据实践经验,传动系统的惯量J和转子惯量JM之间有一个惯量匹配的问题,JM/J得笔直不能太小,否则装置的动态特性将主要取决于负载特性,此时不同质量和行程的各坐标的特性将有很大区别.并且很容易受摩察力等干扰的影响,但是JM/J得比值太大,也是很不经济的。
所以,J/JM=0.1367/0.13=1.05<3
3.3.1.2电机力矩的计算
电机负载力矩的各种工况下是不同的,下面分快速上升启动时所需力矩和匀速上升时所需力矩,:
快速下降启动时所需力矩和匀速下降时所需力矩。
经过分析,快速上升启动时所需力矩最大。
快速上升启动时所需力矩:
M起=Mamax+M1(3—3)
M起-起动力矩(N·m)
Mamax-起动时折算到电机轴上的加速力矩(N·m)
M1-载荷折算到电机轴上的力矩(N·m)
用下式计算:
式中:
J∑——传动系用折算到电机轴上的总等效转动惯量(kg.cm2);
ε——电机最大角加速度(rad/s2)
nmax——电机的最大转速(r/min)nmax=vmax/δP×θb/360°
vmax——运动部件的最大快进速度(mm/min)
δP——脉冲当量(mm/步)
θb——步进电机的步距角(°)
ta——运动部件从停止起动加速到最大快进速度所需的时间(s)
三相六拍时λ=Mq/Mjmax=0.866
Mjmax=Mq/λ=2.86/0.866=3.30(3—5)
所以,查文献得75BF003型电机的最大静转矩为0.882,大于所需最大静转矩,可作为初选型号。
经过上述计算以后,通常将最大力矩作为选择步进电机的依据。
因为要保证一定的动态性能,系统时间常数较小,而等效转动惯量有较大,故电机力矩主要是用来产生加速度的,而负载力矩往往小于加速力矩,故常常用起动力矩M起作为选择电机的依据。
3.3.1.3步进电机的选择.
首先根据最大静转矩Mjmax初选电机型号,步进电机的起动转矩Mg和最大静转矩Mjmax如下关系:
如表3-1
表3-1起动转矩Mg和最大静转矩Mjmax
步进电机
相数
三相
四相
五相
六相
拍数
3
6
4
8
5
10
6
12
0.5
0.86
6
0.70
7
0.70
7
0.80
9
0.95
1
0.86
6
0.86
6
上面计算出的空载起动力矩M起应小于Mq
这样初选出来的电机型号并不一定能满足实际工作时的要求.也就是说,尽管最大静转矩Mjmax数值能满足要求,但是并不能保证在快速空载起动和运行时不失步.所以还必须用起动机电一体化课程设计指导书上的矩频特性和运行矩频特性两个重要性能曲线来检查所选步进电机的型号是否满足要求.
3.3.2驱动撑脚运动的电机的选择计算:
等效转动惯量的计算:
初选电机为36BF,则JM=0.08kg·cm2
JΣ=JM+J1+
(3—6)
J1,——齿轮Z1的转动惯量(kg·cm2)
G—齿条部分重量
所以,J1=0.78×10-3×34×1.2=0.075kg·cm2
=
=0.108
JΣ=0.075+0.108=0.183kg·cm2
考虑惯量匹配问题:
J/JMΣ=0.183/0.08=22.29<3
故基本满足匹配。
所以初估nmax=vmax×θb/(δP×360)=2400×1.5/(360×360)=1000r/min(3—7)
ta=30ms
所以,
N·cm(3—8)
查表,步进电机为五相十拍时,λ=Mq/Mjmax
所以最大静力矩为Mjmax=Mq/λ=9.18/0.951=9.65N·m
按此最大静力矩从表查出:
36BF004型最大静转矩为1N·m,大于所需最大静转矩。
3.3.3驱动测杆运动电机的选择:
等效转动惯量的计算:
初选电机为36BF,则J