毕业设计论文.docx
《毕业设计论文.docx》由会员分享,可在线阅读,更多相关《毕业设计论文.docx(19页珍藏版)》请在冰豆网上搜索。
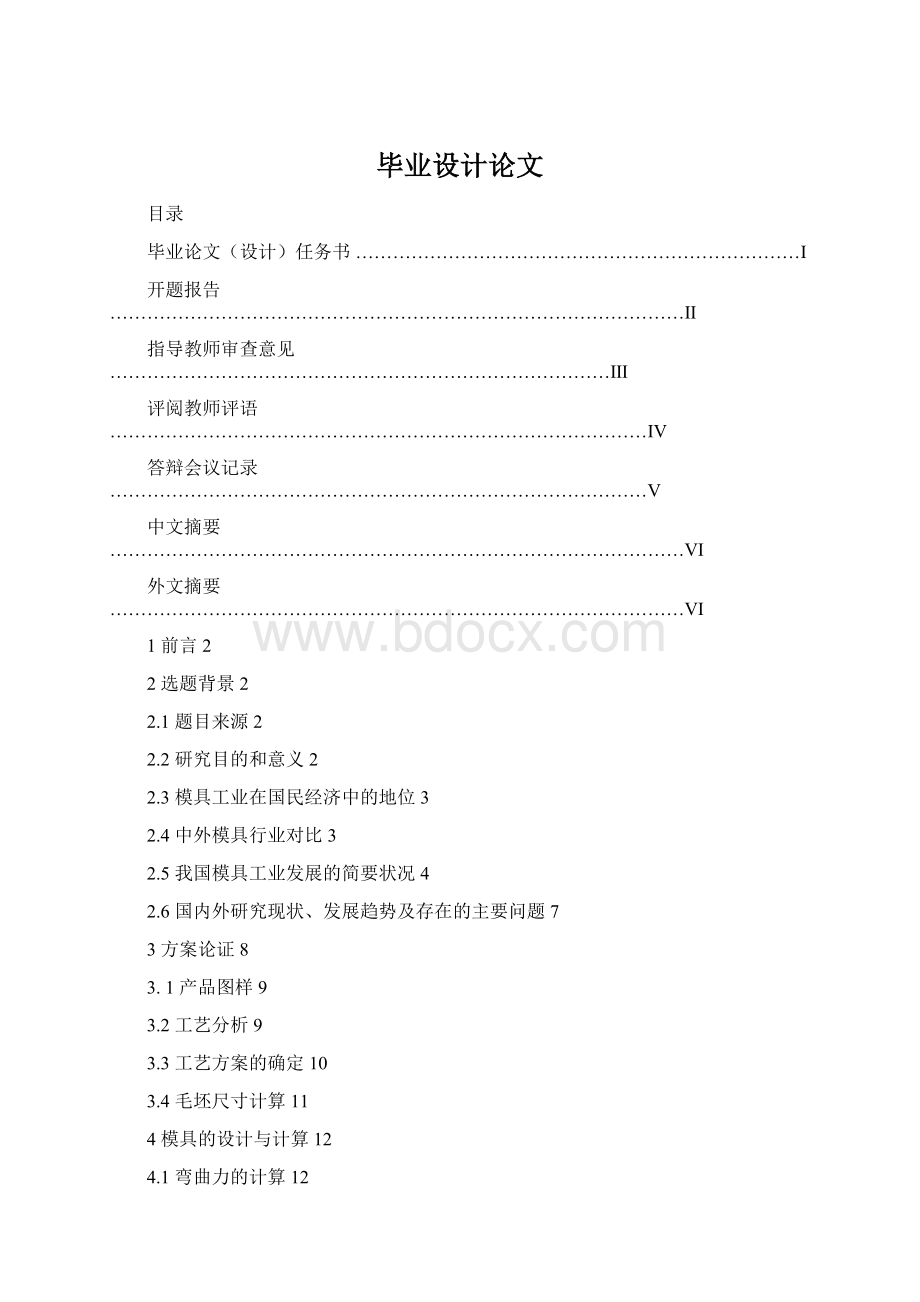
毕业设计论文
目录
毕业论文(设计)任务书………………………………………………………………Ⅰ
开题报告…………………………………………………………………………………Ⅱ
指导教师审查意见………………………………………………………………………Ⅲ
评阅教师评语……………………………………………………………………………Ⅳ
答辩会议记录……………………………………………………………………………Ⅴ
中文摘要…………………………………………………………………………………Ⅵ
外文摘要…………………………………………………………………………………Ⅵ
1前言2
2选题背景2
2.1题目来源2
2.2研究目的和意义2
2.3模具工业在国民经济中的地位3
2.4中外模具行业对比3
2.5我国模具工业发展的简要状况4
2.6国内外研究现状、发展趋势及存在的主要问题7
3方案论证8
3.1产品图样9
3.2工艺分析9
3.3工艺方案的确定10
3.4毛坯尺寸计算11
4模具的设计与计算12
4.1弯曲力的计算12
4.2校正弯曲力的计算12
4.3压力机的选用13
4.4工作零件刃口尺寸计算及模具设计13
4.5弹簧的设计与计算14
4.6其他零件设计列表:
18
5模具材料的选择18
6校核20
7小结20
8参考文献21
9致谢24
管夹弯曲成形级进模设计
学生:
吴巍巍,机械工程学院材料10502
指导教师:
徐小兵,长江大学机械工程学院
1前言
随着人类社会的不断进步,板材成形技术已越来越先进,其成形的方法也越来越多。
目前,常用的技术和方法主要有冲压成形、无模多点成形、无模单点成形、液压成形、电磁成形、激光成形和旋压成形。
其中,冲压成形是使用最广泛的一种,而冲压模具是冲压成形中的一个十分关键的要素。
模具生产的工艺水平及科技含量的高低,已成为衡量一个国家科技与产品制造水平的重要标志,它在很大程度上决定着产品的质量、效益、新产品的开发能力,决定着一个国家制造业的国际竞争力。
作为一个学机械的大学生,我希望将来在模具方面发展,将来为国家的模具事业做出贡献。
2选题背景
2.1题目来源
生产实践
2.2研究目的和意义
系统地温习大学里所学的知识,提高自身的动手能力和设计能力,对所学知识进行强化,为今后的学习和工作打下坚实的基础。
对国内外先进的模具制造与设计技术有一个较深入的了解,使自己所学的与生产实际紧密的结合。
2.3模具工业在国民经济中的地位
模具,是工业生产的基础工艺装备,在电子、汽车、电机、电器、仪表、家电和通讯等产品中,60%~80%的零部件都依靠模具成形,模具质量的高低决定着产品质量的高低,因此,模具被称之为“百业之母”。
模具又是“效益放大器”,用模具生产的最终产品的价值,往往是模具自身价值的几十倍、上百倍。
模具生产的工艺水平及科技含量的高低,已成为衡量一个国家科技与产品制造水平的重要标志,它在很大程度上决定着产品的质量、效益、新产品的开发能力,决定着一个国家制造业的国际竞争力。
模具是制造业的一种基本工艺装备,它的作用是控制和限制材料(固态或液态)的流动,使之形成所需要的形体。
用模具制造零件以其效率高,产品质量好,材料消耗低,生产成本低而广泛应用于制造业中。
模具工业是国民经济的基础工业,是国际上公认的关键工业。
模具生产技术水平的高低是衡量一个国家产品制造水平高低的重要标志,它在很大程度上决定着产品的质量,效益和新产品的开发能力。
振兴和发展我国的模具工业,正日益受到人们的关注。
早在1989年3月中国政府颁布的《关于当前产业政策要点的决定》中,将模具列为机械工业技术改造序列的第一位。
模具工业既是高新技术产业的一个组成部分,又是高新技术产业化的重要领域。
模具在机械,电子,轻工,汽车,纺织,航空,航天等工业领域里,日益成为使用最广泛的主要工艺装备,它承担了这些工业领域中60%~90%的产品的零件,组件和部件的生产加工。
模具制造的重要性主要体现在市场的需求上,仅以汽车,摩托车行业的模具市场为例。
汽车,摩托车行业是模具最大的市场,在工业发达的国家,这一市场占整个模具市场一半左右。
汽车工业是我国国民经济五大支柱产业之一,汽车工业重点是发展零部件,经济型轿车和重型汽车,汽车模具作为发展重点,已在汽车工业产业政策中得到了明确。
汽车基本车型不断增加,2005年将达到170种。
一个型号的汽车所需模具达几千副,价值上亿元。
为了适应市场的需求,汽车将不断换型,汽车换型时约有80%的模具需要更换。
中国摩托车产量位居世界第一,据统计,中国摩托车共有14种排量80多个车型,1000多个型号。
单辆摩托车约有零件2000种,共计5000多个,其中一半以上需要模具生产。
一个型号的摩托车生产需1000副模具,总价值为1000多万元。
其他行业,如电子及通讯,家电,建筑等,也存在巨大的模具市场。
目前世界模具市场供不应求,模具的主要出口国是美国,日本,法国,瑞士等国家。
中国模具出口数量极少,但中国模具钳工技术水平高,劳动成本低,只要配备一些先进的数控制模设备,提高模具加工质量,缩短生产周期,沟通外贸渠道,模具出口将会有很大发展。
研究和发展模具技术,提高模具技术水平,对于促进国民经济的发展有着特别重要的意义。
2.3中外模具行业对比
预计到2018年,中国将一跃成为全球最大的模具制造业基地之一,据相关研究部门调查得知,欧洲模具设计和生产的时间要分别比中国快44%和61%左右,但中国模具设计和生产的成本却只有欧洲同行的91%,因为中国的劳动力成本低廉,对部分国外客户有着很强的吸引力。
同时,欧洲及世界各国之间的模具竞争也相应加剧,像德国近两年半内的模具整体价格就下降了25%左右。
据统计,前些年全球58%的模具是由德国等西欧国家生产,中国等亚洲国家的比例只占到1%,但今后东欧国家的模具将会有较大幅度的增长,而亚洲国家的生产比例将提高至22%左右。
鉴于中国廉价劳动力成本的优势和整体经济持续快速发展的良好势头,中国模具发展的前景将十分广阔。
但这并不意味着中国发展的一切都是那么的理想和完美。
因为中国的市场过早地陷入了价格战的误区,还缺乏自主创新的能力,没有相应地建立起诚信可靠的市场体系,特别是有65%的欧洲客户觉得中国模具的价格虽低但质量不好。
一种比较理想的解决方法是,加强中欧双方的合作,由欧洲国家出订单和图纸,中国模具企业具体负责完成设计及加工制作,并在此过程中不断学习欧洲先进的技术及管理理念,加快工业化的改造,努力提高企业自身的核心优势和竞争力。
如在提高客户满意度方面,企业除了在价格低廉上做文章外,更重要的是要求交货时间短,产品质量好,诚信度高,尽可能让他们了解产品的研发、设计及生产的全过程企业要明确自己的主攻方向,加强相互之间的合作,及时有效地对客户的需求作出反应。
2.4我国模具工业发展的简要状况
一是已进入模具生产大国之列,但还不是模具强国。
进入新世纪以来,我国模具销售额以年平均20%左右的速度增长,2006年模具销售额达到720亿元人民币,居日本、美国之后第三位;模具出口突破了10亿美元。
我国模具生产厂、点达到了约3万家,从业人员近100万人。
这些都说明我国模具工业有了相当的规模。
但是,我国现在每年还要从境外进口20多亿美元的模具,这些大都是国内尚不能生产的高中档模具。
国内中高档模具的自配率只占50%左右;大型、精密、复杂、长寿命等技术含量较高的模具只占到模具总量的30%左右。
我国模具行业全员劳动生产率还较低,平均只有15万元/人·年左右;我国模具商品化率还只有50%多(发达国家达70%以上);模具标准件使用覆盖率也较低,只有50%左右;模具生产专业化水平还较低。
这些都说明我国的模具工业还不够强大,我国还不是模具强国。
二是模具产品水平有了很大提高,但差距还很大。
近些年来,中国模具的设计和制造水平有了很大提高,CAD/CAE/CAM等计算机辅助技术、高速加工技术、热流道技术、气辅技术、逆向工程等新技术得到广泛应用。
现在,中国已能生产精度达到2微米的多工位级进模,寿命可达3亿冲次以上。
个别企业生产的多工位级进模已可在2000次/分的高速冲床上使用,精度可达1微米。
在大型塑料模具方面,中国已能生产43英寸大屏幕彩电和65英寸背投式电视的塑壳模具、10公斤大容量洗衣机全套塑料件模具以及汽车保险杠、整体仪表板等塑料模具等。
在精密塑料模具方面,中国已能生产照相机和手机塑料件模具、多型腔小模数齿轮模具及精度达5微米的7800腔塑封模具等。
在大型精密复杂压铸模方面,国内已能生产自动扶梯整体踏板压铸模、汽车后桥齿轮箱压铸模以及汽车发动机壳体的铸造模具等。
在汽车覆盖件模具方面,国内已能生产中档新型轿车的覆盖件模具。
子午线轮胎活络模具、铝合金和塑料门窗异型材挤出成形模、精铸或树脂快速成形拉延模等,也已达到相当高的水平,制造出来的模具可与进口模具媲美。
我国生产的最大模具单套重量已超过100吨。
但是,我国模具的制造从总体上看,产品还只是以中低档为主,中高档模具很多还要依赖进口;企业虽然重视推广应用新技术,但这些新技术应用的水平还不够高。
三是模具骨干企业队伍已经形成,但还不够壮大。
经过十多年的快速发展,我国模具企业骨干队伍已经形成。
它们一般都有较好的生产装备,生产都达到了一定的规模,技术水平较高,产品水平也达到了一定的高度,而且产品有了自己的特点。
在各个模具行业骨干企业队伍中也涌现出了本行业的龙头企业。
2006年中国模具工业协会对各行业的50家模具企业授予第一批“重点骨干模具企业”称号。
中国模具骨干企业队伍目前还在成长之中,各方面都有待进一步提高,技术待进步,管理待加强,产品有待更加适应市场的需求。
当前,我国制造业的快速发展,特别是受汽车制造业发展的拉动,国内模具市场不断扩大;跨国集团到我国进行模具国际采购不断增加,而且国际上将模具制造逐渐向我国转移的趋势十分明显。
由此展望未来,中国模具工业将会有一个持续快速发展的机遇期。
我们要很好地把握住这个机遇期,使我国模具工业有一个很大的提高。
2.5国内外研究现状、发展趋势及存在的主要问题
根据国内和国际模具市场的发展状况,有关专家预测,未来我国的模具经过行业结构调整后,将呈现十大发展趋势:
一是模具日趋大型化;二是模具的精度将越来越高;三是多功能复合模具将进一步发展;四是热流道模具在塑料模具中的比重将逐渐提高;五是气辅模具及适应高压注射成型等工艺的模具将有较大发展;六是模具标准化和模具标准件的应用将日渐广泛;七是快速经济模具的前景十分广阔;八是压铸模的比例将不断提高,同时对压铸模的寿命和复杂程度也将提出越来越高的要求;九是塑料模具的比例将不断增大;十是模具技术含量将不断提高,中高档模具比例将不断增大,这也是产品结构调整所导致的模具市场未来走势的变化。
虽然中国模具工业在过去十多年中取得了令人瞩目的发展,但许多方面与工业发达国家相比仍有较大的差距。
例如,精密加工设备在模具加工设备中的比重比较低;CAD/CAE/CAM技术的普及率不高;许多先进的模具技术应用不够广泛等等,致使相当一部分大型、精密、复杂和长寿命模具依赖进口。
未来冲压模具制造技术发展趋势:
模具技术的发展应该为适应模具产品“交货期短”、“精度高”、“质量好”、“价格低”的要求服务。
达到这一要求急需发展如下几项:
(1)全面推广CAD/CAM/CAE技术
模具CAD/CAM/CAE技术是模具设计制造的发展方向。
随着微机软件的发展和进步,普及CAD/CAM/CAE技术的条件已基本成熟,各企业将加大CAD/CAM技术培训和技术服务的力度;进一步扩大CAE技术的应用范围。
计算机和网络的发展正使CAD/CAM/CAE技术跨地区、跨企业、跨院所地在整个行业中推广成为可能,实现技术资源的重新整合,使虚拟制造成为可能。
(2)高速铣削加工
国外近年来发展的高速铣削加工,大幅度提高了加工效率,并可获得极高的表面光洁度。
另外,还可加工高硬度模块,还具有温升低、热变形小等优点。
高速铣削加工技术的发展,对汽车、家电行业中大型型腔模具制造注入了新的活力。
目前它已向更高的敏捷化、智能化、集成化方向发展。
(3)模具扫描及数字化系统
高速扫描机和模具扫描系统提供了从模型或实物扫描到加工出期望的模型所需的诸多功能,大大缩短了模具的在研制制造周期。
有些快速扫描系统,可快速安装在已有的数控铣床及加工中心上,实现快速数据采集、自动生成各种不同数控系统的加工程序、不同格式的CAD数据,用于模具制造业的“逆向工程”。
模具扫描系统已在汽车、摩托车、家电等行业得到成功应用,相信在“十五”期间将发挥更大的作用。
(4)电火花铣削加工
电火花铣削加工技术也称为电火花创成加工技术,这是一种替代传统的用成型电极加工型腔的新技术,它是有高速旋转的简单的管状电极作三维或二维轮廓加工(像数控铣一样),因此不再需要制造复杂的成型电极,这显然是电火花成形加工领域的重大发展。
国外已有使用这种技术的机床在模具加工中应用。
预计这一技术将得到发展。
(5)提高模具标准化程度
我国模具标准化程度正在不断提高,估计目前我国模具标准件使用覆盖率已达到30%左右。
国外发达国家一般为80%左右。
(6)优质材料及先进表面处理技术
选用优质钢材和应用相应的表面处理技术来提高模具的寿命就显得十分必要。
模具热处理和表面处理是否能充分发挥模具钢材料性能的关键环节。
模具热处理的发展方向是采用真空热处理。
模具表面处理除完善应发展工艺先进的气相沉积(TiN、TiC等)、等离子喷涂等技术。
(7)模具研磨抛光将自动化、智能化
模具表面的质量对模具使用寿命、制件外观质量等方面均有较大的影响,研究自动化、智能化的研磨与抛光方法替代现有手工操作,以提高模具表面质量是重要的发展趋势。
(8)模具自动加工系统的发展
这是我国长远发展的目标。
模具自动加工系统应有多台机床合理组合;配有随行定位夹具或定位盘;有完整的机具、刀具数控库;有完整的数控柔性同步系统;有质量监测控制系统
3方案论证
2.6零件加工工艺分析
2.6.1产品图样
材料厚度t=1㎜,零件材料H62,则零件精度选IT13,冲模制造精度为IT7~IT8,大批量生产
查资料得:
零件材料为H62(硬),屈服强度为420MPa,伸长率为10%
该零件形状复杂,如采用单工序模生产,存在生产效率低,产品质量不稳定等缺陷。
为了保证产品质量,提高生产效率,决定采用多滑块压力机二次弯曲成形,并创建了一条自动化冲压生产线。
2.6.2工艺分析
从图中可知,零件形状复杂,有多处弯曲,成形工序比较多。
依据样件分析,零件原采用多滑块压力机二次弯曲成形,现如采用级进模一次弯曲成形有2处难点:
①无法弯曲内径;②一次弯曲成形难以保证弯曲精度。
如采用级进模二次弯曲,难点在于,弯曲回弹较大,难以保证弯曲精度。
2.6.3工艺方案的确定
零件展开图
设计方案一:
用多滑块压力机二次弯曲加工零件,主要工序有:
切断、凹模上压弯曲、左右弯模弯曲。
(1)进料
(2)切断
(3)凹模上压弯曲
(4)左右弯模弯曲
(5)左右弯模回程
(6)落料
设计方案二
用级进模二次弯曲加工零件,如图,第一次弯曲得到的形状
主要工序有:
(1)进料
(2)切断
(3)凸模下压弯曲
(4)第二次弯曲
(5)落料
分析比较
方案一工序集中,工位数较少,因此模具结构尺寸也教少,多滑块压力机各部分威独立的单一体,使得结构大为简化。
用多工位级进模加工,不仅模具十分复杂,而且模具费用也比多滑块压力机模具高得多。
但是在此方案中,工位过于集中,在一个工位上完成多个工序,使的模具零件相距太近,凹模的壁厚较薄,影响模具寿命。
方案二工位较多,且由于弯曲回弹很大,两次弯曲会使精度难以得到保证。
综合以上所述,选有方案一较为合理。
2.6.4毛坯尺寸计算
最小弯曲半径Rmin=0.3T=0.3
R=20
R>0.5t
R/T=20
sinθ/2=1/10=63.53mm
θ=11.48
ai=2πR(90°-11.48°)/360°=27.4°
L1=[10+π(120+0.5)27.4°/180=19.80mm
第一次弯曲时,毛胚长度
L1=l1+l2+π(r+xt)
=2l1+π(r+xt)
=2×19.80°+π(20+0.5)
=104.00mm
故毛胚长度为104mm
3模具的设计与计算。
3.1弯曲力的计算
由于黄铜H62的强度为420MPA
F自=CKB
²/r+t
=(0.7×1.3×8×1)÷(20+1)×420
=145.6N
3.2校正弯曲力的计算
由于A=2(R+t)×B
=336mm²
.F校=PA
=70×336
=23520
顶件力和压料力
F顶和F压可近似取弯曲力的30%-80%
3.3压力机的选用
选择适合的多滑块压力机,及其适当的滑块
3.4工作零件刃口尺寸计算及模具设计
确定工作零件刃口尺寸计算方法时,首先要考虑工作零件的加工方法及模具装配方法。
在多滑块压力机上取常用切断刀,切带料时,由于材料为硬黄铜,故取切刀锲角β为90°
凸模半径(心轴半径)R1/t=20>10,Rp应该考虑回弹后引起的R的变化
R=15.686
凹模半径Rd=Rp+t=16.686
回弹K=1.275
则R=R”/K=20÷1.275=15.686
凹模深度由U型件M=3mm
凹凸模间隙B/H=0.16<2
C=T=1mm
选用合适的滑块,一般情况下,不另外设计芯模。
但是考虑此时受到较大的回弹影响
则有型模直径D=0.9Dt=0.9×400
=36mm
凸凹模工作部分的尺寸于公差
宽度尺寸,标注在外侧,以凹模为基准,选IT7
凹模宽度尺寸为Bd=(B-0.75△)+δd
0
=(8-0.75×0.5)+15
0
凸模单边间隙Bp=Bd-2C
=7.625+15-2
0
=5.625+15
0
3.5弹簧的设计与计算
在冲压模具的设计中,簧是标准件,在冲压模具中常常使用的是螺旋型弹簧和碟型弹簧。
因为碟型弹簧常用在冲压力很大但工作行程较短的情况,所以这里选用圆柱型螺旋弹簧,选用4个弹簧,每个弹簧分到的力为145.6N/4=36.4N。
先初选弹簧。
由《实用模具设计与制造手册》表2-108圆柱螺旋压缩弹簧(GB2089-80)可知材料直径d=4.5mm;弹簧中径32mm;节距t=10.3mm;工作极限负荷
=647N;自由高度
=90mm;有效圈数n=5.5;工作极限负荷下的变形量
=38.5mm;展开长度L=754mm。
(实际的工艺行程
=20,取工作余量
=6)由弹簧特性曲线可知在预紧力647N作用下该弹簧的预紧量10,最大许用压缩量
=38.5mm。
所以
=36mm,弹簧的最大工作压力要小于实际的预紧力,故所选弹簧满足实际要求。
弹簧设计如下表
d
D2
t
Fj
h0
n
hj
L
4.5
32
10.3
547
90
5.5
38.5
754
D2-弹簧中经(mm)、d-材料直径(mm)、t-节距(mm)、Fj-工作极限载荷(N)、hj-工作极限载荷下变形量(mm)、h0-自由高度(mm)、n-有效圈数、L-展开长度(mm)
弹簧的校核选用机械设计手册(软件版).V3.0的弹簧设计功能进行校核,校核结果如下:
材料名称M_Name=油淬火回火硅锰合金弹簧钢丝A类
切变模量G=79000(MPa)
弹性模量E=206000(MPa)
抗拉强度σb=1471(MPa)
许用切应力τb=647.24(MPa)
压并圈取值范围n2'=1~2.5
弹簧基本参数
钢丝直径d=4.5(mm)
弹簧中径D=32.00(mm)
旋绕比C=7.11
曲度系数K=1.21
有效圈数n=5.5
压并圈数n2=2
弹簧总圈数n1=7.5
实际刚度k=22.47(N/mm)
要求刚度k'=44.7(N/mm)
实际刚度k=22.47(N/mm)
刚度相对误差δk=49.73(%)
安装变形量f1=8.9(mm)
安装载荷(设计)F1=200(N)
工作变形量f2=28.79(mm)
工作载荷(设计)F2=647(N)
试验变形量fs=38.65(mm)
最小变形比f1/fs=0.23
弹簧特性(安装)Tf1=满足要求
最大变形比f2/fs=0.74
弹簧特性(工作)Tf2=满足要求
最小切应力τmin=216.41(MPa)
最大切应力τmax=700.07(MPa)
切应力特性系数γ=0.31
最大切应力比抗拉强度τmax/σb=0.48
弹簧疲劳强度Tq=满足要求
稳定性要求Tw=满足要求
安全系数S=1.18
强迫机械振动频率γr=0(Hz)
弹簧自振频率γn=284.45(Hz)
是否为减振弹簧JZ=否
承载W=(N)
共振要求Tg=满足要求
自由高度H0=72.63(mm)
安装高度H1=56(mm)
工作高度H2=43.83(mm)
压并高度Hb=33.75(mm)
试验高度Hs=33.98(mm)
节距p=11.98(mm)
螺旋角α=6.794578(度)
3.6其他零件设计列表:
名称
主要尺寸
备注
对角导柱下模座
360×240×35
《中国模具设计大典》
对角导柱上模座
360×240×40
《中国模具设计大典》
导柱
25×130
《中国模具设计大典》
导套
25×85×33
《中国模具设计大典》
凸模垫板
厚度选择t=8mm
《中国模具设计大典》
凹模垫板
厚度选择t=12mm
《中国模具设计大典》
凸模固定板
T=15mm
《中国模具设计大典》
模柄
φ40mm×60mm
《中国模具设计大典》
4模具材料的选择
由于零件尺寸较小,且材料为H62,比较容易成形,因此对模具材料要求不高,本模具在运行的过程中,模具受力较小,所受冲击也较小,加工温度为室温,对温度要求不高,由于零件材料硬度不高,所以对模具材料的硬度要求也不高,根据工作条件分析,模具的失效形式主要是疲劳磨损失效,但考虑到模具的尺寸较小,所以应选择合金钢。
对于模具中的滑块部分,所许硬度不要很高,但是在级进模工作过程中,它要不断的滑动,这就要求它有很高的耐磨性,考虑到经济性和货源的供货问题,决定采用我国自己生产的9Mn2V和高速刚,其中高速钢做滑块部分材料。
9Mn2V钢是我国自行研制的低合金冷作模具钢,它是在碳素工具钢基础上,主要用Mn来合金化以提高钢材的谇透性,同时加入Si或V,以减少锰钢的过热敏感性。
9Mn2V钢油谇时的临界直径为40mm,在170硝盐中谇火的临界直径也有30~40mm。
如果不一定要求模具整体谇透,油谇时尺寸可放宽到60mm左右。
对于有效直径不超过40mm的模具,用170硝盐分级谇火,表面硬度可达到60HRC以上。
9Mn2V的谇火温度范围比较宽,一般推荐780~800度谇火,晶粒都不显著长大,硬度达到最到最大值,变形情况亦最小。
但高于800度谇火时,由于残余奥氏体量增加而致硬度略有下降。
淬火可采用油,硝盐等冷谇。
对截面较大的模具可采用170度碱浴分级谇火;对要求变形小,硬度HRC>60的模具,可先在170~180度的分级淬