铜钛氰废水的治理.docx
《铜钛氰废水的治理.docx》由会员分享,可在线阅读,更多相关《铜钛氰废水的治理.docx(9页珍藏版)》请在冰豆网上搜索。
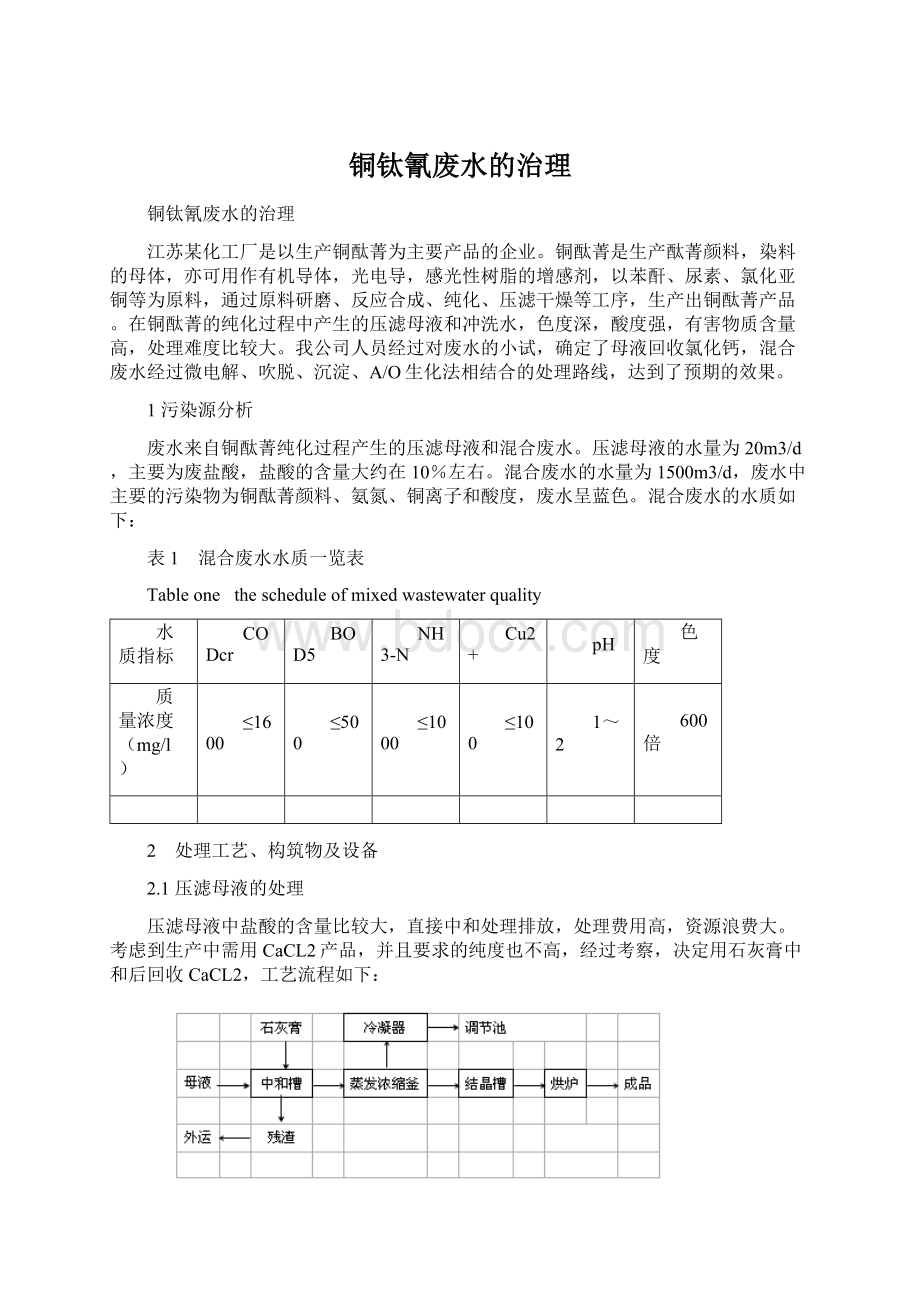
铜钛氰废水的治理
铜钛氰废水的治理
江苏某化工厂是以生产铜酞菁为主要产品的企业。
铜酞菁是生产酞菁颜料,染料的母体,亦可用作有机导体,光电导,感光性树脂的增感剂,以苯酐、尿素、氯化亚铜等为原料,通过原料研磨、反应合成、纯化、压滤干燥等工序,生产出铜酞菁产品。
在铜酞菁的纯化过程中产生的压滤母液和冲洗水,色度深,酸度强,有害物质含量高,处理难度比较大。
我公司人员经过对废水的小试,确定了母液回收氯化钙,混合废水经过微电解、吹脱、沉淀、A/O生化法相结合的处理路线,达到了预期的效果。
1污染源分析
废水来自铜酞菁纯化过程产生的压滤母液和混合废水。
压滤母液的水量为20m3/d,主要为废盐酸,盐酸的含量大约在10%左右。
混合废水的水量为1500m3/d,废水中主要的污染物为铜酞菁颜料、氨氮、铜离子和酸度,废水呈蓝色。
混合废水的水质如下:
表1 混合废水水质一览表
Tableone thescheduleofmixedwastewaterquality
水质指标
CODcr
BOD5
NH3-N
Cu2+
pH
色度
质量浓度(mg/l)
≤1600
≤500
≤1000
≤100
1~2
600倍
2 处理工艺、构筑物及设备
2.1压滤母液的处理
压滤母液中盐酸的含量比较大,直接中和处理排放,处理费用高,资源浪费大。
考虑到生产中需用CaCL2产品,并且要求的纯度也不高,经过考察,决定用石灰膏中和后回收CaCL2,工艺流程如下:
(1)压滤母液经过收集进入中和槽,和投加的石灰膏进行中和反应。
中和槽为钢混结构,有效容积20m3,内设搅拌机2台,提升泵2台。
(2)反应上清液提升进入蒸发浓缩釜,蒸发液经过冷凝后进入调节池,浓缩液进入结晶槽。
浓缩釜采用链排炉加热,为减少煤的用量,采用负压蒸发的方式,余热进入烘炉。
浓缩釜1只,碳钢防腐,有效容积10m3。
(3)结晶槽在烘炉中烘干后,既是成品CaCL2。
2.2混合废水的处理
混合废水中含有铜酞菁颜料、氨氮、铜离子,废水呈强酸性。
处理流程如下:
(1)调节池为钢混结构,花岗岩防腐。
设计HRT=6h,有效容积375m3。
配备化工离心泵2台,不锈钢泵前水箱2只。
(2)铜酞菁颜料的分子结构很稳定,必须将颜料的发色基团氧化后,才能消除其对环境的不良影响,考虑到废水呈酸性,因此利用微电解塔对其进行氧化还原反应,并且也可以置换废水中的铜。
微电解塔内填充铁屑和焦炭,使其分别作为微电池的阴阳两极,电极反应产生的新生态H,能与颜料中的多种组分发生氧化还原反应,破坏废水中的发色物质和发色结构。
微电解塔设计HRT=6h,200%的回流率,铁屑和焦炭的质量比为1:
1。
微电解塔2只,碳钢防腐,配循环泵2台,空压机2台。
(3)废水中的氨氮含量较高,通常的生化处理法对氨氮的降解率只有70%~80%,所以单纯采用生化法处理难以达到理想效果。
并且生化法对污水氨氮浓度有一定要求,质量浓度在1000 mg/L以上时会使微生物中毒,进而影响生化系统的去除效率。
因此,必须采用一种切实可行的预处理方法,先去除部分氨氮,使废水中的氨氮浓度降至140mg/L以下,再采用生化处理方法去除残留氨氮,以达到最终去除氨氮的目的。
因此对70%的废水先采用吹脱的方法,使氨氮含量降低,再和剩余废水一起进入生化处理系统。
吹脱时先将废水的pH值调到10,然后鼓气吹脱,气水比为2500:
1。
本设计采用穿流式筛板吹脱池,池内筛板孔径6 mm,筛板间距300 mm。
水自上向下喷淋,穿过筛孔流下,空气则自下向上流动,控制空塔的气流速度达到2.0m/s。
吹脱池1座,钢混结构,配备离心风机2台,喷淋泵2台。
(4)吹脱后的废水和剩余废水混合后进入反应池,此时废水的pH值在9左右,可以生成Fe(OH)3沉淀,因为铜离子能使生物酶失去活性,对生物氧化系统有毒性效应,为彻底去除废水中的铜,加入硫化钠,以生成硫化铜沉淀。
反应池和初沉池合建,1座,钢混结构。
反应池HRT=30min,初沉池HRT=2h,池内安装φ80的玻璃钢斜管。
(5)沉淀上清液进入A/O生化系统,A/O法对废水中的有机物和氨氮有很高的去除率。
因废水中含有的有毒物质和大分子有机物,容易造成活性污泥的膨胀,因此在好氧生化处理前采用水解酸化作为生化预处理工艺。
许多研究表明,在通常的生物处理前加一级水解酸化预处理可以明显提高其对污染物的去除效果。
其目的有二个:
第一需要降解大分子物质;第二提高微生物的活性,抵抗有毒有害物质侵害,防止污泥膨胀和微生物的流失。
生物硝化脱氮是一个两阶段的生物反应过程,第一过程为硝化过程,分两部进行,首先NH4-N在亚硝化菌的作用下生成NO2-,其后NO2-再在硝化菌的作用下氧化生成NO3-。
第二过程为反硝化过程,是完成生物脱氮的最后一步,NO3--N在反硝化菌的作用下,以有机碳为碳源和能源,以硝酸盐作为电子受体,将硝酸盐还原为气态氮。
生化处理系统运行中,控制废水温度在22~28℃,pH为7.5~8.0,为硝化菌和反硝化菌提供适宜的环境。
控制缺氧池溶解氧浓度低于0.5 mg/L,HRT=6h;好氧池溶解氧浓度2.5~3.0 mg/L,HRT=14h;MLSS=3000mg/l;回流率100%。
采用双伞形散流曝气器,SSR-200罗茨风机2台。
(6)生化处理废水经过活性碳吸附过滤后达标排放。
活性炭过滤池1座,HRT=1h,内置活性炭3吨,蒸汽再生。
3 运行情况
工程由2000年1月份进入调试运行。
母液回收由于已有成功的经验,经过1个月的调试,基本运行正常,产出的CaCL2纯度在85%左右,满足生产需要,经济效益明显。
生化池的启动采用接种的方法,共接种污水处理厂脱水生化污泥20吨,大粪水50吨。
经过闷曝5天后,出现了草履虫、大口钟虫等原生动物,活性污泥已恢复。
开始少量进水,进水量为10m3/h,每天进水10h,并定量投加面粉和磷酸钙。
20天后,生化池污泥的SV在20%左右,镜检原生动物活跃,出水水质指标较好。
此时加大进水量,24小时连续运行,20天后,生化池CODcr的去除率达到70%左右,SV在30%左右,生物相以钟虫、累枝虫、圆筒盖虫和楯纤虫等为主,生化系统启动成功。
正常运行后,出水指标完全达到国家一级排放标准,各部分的去除率如表2所示。
表2 污染物去除率一览表
Tabletwothescheduleoftheratioofcontaminationwipingoff
指标
原水
微电解塔
吹脱池
初沉池
生化处理
过滤池
出水
去除率
出水
去除率
出水
去除率
出水
去除率
出水
去除率
CODcr
(mg/l)
1600
1300
20%
900
30%
400
55%
120
70%
≤100
≥20%
Cu2+
(mg/l)
100
20
80%
10
50%
1
90%
0.5
50%
≤0.5
≥20%
NH3-N
(mg/l)
1000
800
20%
40
95%
40
/
10
80%
≤15
≥20%
色度
(倍)
600
200
60%
150
25%
60
60%
40
30%
≤50
≥20%
pH
1~2
4~5
/
10
/
9
/
7
/
6~9
≥20%
4技术经济分析
污水处理厂总投资280万元,其中母液回收投资80万元,混合污水处理投资200万元。
每天回收成品CaCL21.5吨,每吨的售价在1200元,则每天的收益为1800元。
污水处理站总装机容量为106.5kw,实用功率为75kw,每天的电费为864元;石灰膏的用量每天4吨,费用为1200元;硫化钠的用量每天30kg,费用为30元;PAM的用量每天1.5kg,费用为30元;煤的耗量每天为4吨,费用为1200元;人工费每天200元。
则除收益外,每天净投入的运行费用为1724元,即1.15元/m3.污水。
5 结论
铜酞菁生产过程中产生的压滤母液和冲洗废水,对压滤母液中和后回收CaCL2,冲洗废水经过微电解、吹脱除氮和除铜后,再进行生化处理,实践证明是可行的。
铜酞菁生产废水的浓度高、毒性大,直接生化处理的难度比较大。
生化处理法对污水氨氮浓度和铜离子浓度都有一定的适应范围,氨氮质量浓度在1000mg/L以上、铜离子质量浓度在5mg/L以上时会使微生物中毒,进而影响生化系统的去除效率。
因此,必须采用一种切实可行的预处理方法,先去除部分氨氮和铜离子,使废水中的氨氮浓度降至140.0mg/L以下、铜离子浓度降至5mg/L以下,再采用生化处理方法,以达到最终达标排放的目的。
铜冶炼含砷污水处理
国内铜冶炼企业在90年代得到了快速发展,冶炼能力的上升加大了对原料铜精砂的需求。
为了生产需要,一些企业降低了对原料的质量要求,特别是原料中砷的含量。
国家有关质量标准规定原料中As<0.3%,但国内有些矿山生产的铜精砂中As含量较高,个别原料中As>1%。
产生的后果是给企业的环境治理带来难度,使某些企业的大气排放和污水排放超标。
本文主要讨论的是水环境的影响。
对铜冶炼企业含砷工业污水的形成以及如何处理达标排放,并确保不造成二次污染,从本人的设计经验及生产实践中,阐述一些认识及看法。
1 含砷工业污水的组成
1.1 污酸
铜精砂中砷一般以铜的硫化物形态存在,主要是以砷黝铜矿(3Cu2S.As2S3)和硫砷铜矿(Cu3AsS4)存在。
含砷矿物在采选过程中基本不溶于水而赋存在铜精砂中。
在熔炼过程中,铜精砂中的砷由于高温绝大部分进入冶炼烟气中,并以As2O3的形态存在。
而冶炼烟气通过净化、干吸、转化的工艺流程制成硫酸。
制酸工艺采用一转一吸时,烟气中As2O3绝大部分进入制酸尾气中,经尾气处理系统进行处理和回收,使尾气达标排放。
但现有尾气处理工艺存在着处理费用高,且尾气排放难以达标的问题,所以冶炼烟气制酸企业大都通过技术改造尽可能采用两转两吸制酸工艺,使制酸尾气能够达标排放。
而烟气中的As2O3及其它杂质则进入定期抽出的污酸中,再对污酸进行处理,回收其有用金属。
分析一些企业的排出污酸中含砷量一般均达3~10g/L,特殊情况高达20g/L,并含其它有害杂质。
如贵冶和金隆铜业公司的污酸成分,见表1。
表1 污酸成分及杂质含量 g/L
成分
H2SO4
As
F
Cu
Fe
Bi
Cd
贵冶
529.9
5.281
1.181
1.348
0.545
0.410
0.149
金隆
1340.0
1.4
5.900
0.100
13.100
1.2 污水
冶炼企业的工业污水主要来源于电收尘冲洗、硫酸车间地面冲洗水和其它工况点被污染的生产水。
水量大,成分复杂,含有As、Cu、Pb、Zn、Cd等有害金属离子,需进行深度处理后才能达标排放。
有代表性的厂区工业污水成分见表2。
2 含砷污水的处理
2.1 高砷污酸的处理
2.1.1 处理原理
化工企业在硫酸生产中排出污酸一般采用石灰乳多段中和即可达到予期效果,而铜冶炼企业硫酸生产中的污酸由于高砷杂质的存在,必须采用硫化法除砷及铜离子后,再进行中和法处理,才能使工业污水达标排放。
目前国内厂家污酸处理主要采用硫化→中和→氧化工艺或中和→硫化→氧化工艺。
经生产实践验证,取得了满意的效果。
如金隆铜业公司采用的污酸处理工艺见图1
污酸处理流程中各段反应机理分别为
①中和反应生成石膏
CaCO3+H2SO4=CaSO4+H2O+CO2↑
②硫化脱铜
Cu2++S2-=CuS↓
③硫化脱砷
3Na2S+As2O3+3H2O=As2S3↓+6NaOH
2.1.2 影响因素
由于污酸中硫酸含量约在100g/L左右,pH≈0,在中和反应过程中一般控制pH=1.5~3.5,故对后续除砷反应影响甚微。
污酸中砷主要以三价砷的形态存在,即AsO+离子,分析砷的电位—pH图,在硫化去砷反应中,应控制氧化还原电位在-50~+50mv之间,经生产实践证明,在此控制条件下,砷的去除率可达95%,而铜的去除率可达98%以上。
采用分步硫化工艺处理污酸,在处理后的反应液中砷浓度一般低于100mg/L,能够回收污酸中的有用金属,并为污水处理站的达标排放创造了条件。
但硫化工艺设备投资和处理成本较高,处理成本中Na2S的费用约占处理费用的20%~30%,吨酸处理成本约百元左右。
高投入和高成本制约了一些中小型企业对该工艺的运用。
已有资料显示采用电积法处理含砷污酸其成本低于硫化法,目前已形成试验规模,相信能很快在生产中得到运用。
2.2 含砷污水的处理
2.2.1 处理原理
铜冶炼企业均设有污水处理站,处理硫酸车间污水和全厂生产污水。
一般进入厂污水处理站污水的特点是处理量大,成份复杂。
如金隆铜业公司和金昌冶炼厂的综合污水水质见表2。
表2 污水水质成分
成分
H2SO4
As
F
Cu
Fe
Zn
Cd
贵治
3920
440
620
300
600
金隆
1314
182.8
86.1
172.6
547
307
0.03
重金属离子,特别是砷离子,给污水处理工艺的选择带来一定的难度。
按照GB8978-1996限定的砷排放浓度为0.5mg/L,在设计选取的工艺指标中,砷离子的总去除率要达到99%,才能使处理水达标排放。
采用简单的石灰乳中和工艺不能保证水质达标排放。
在近几年投产的大型铜冶炼企业和进行技术改造的环境治理企业,对含砷酸性污水处理均采用了石灰乳两段中和加铁盐除砷工艺,经生产实践证明,该工艺是行之有效的,在砷离子达标排放时,其它重金属离子均能达标排放。
该工艺流程见图2
该工艺反应机理分别为:
一段中和反应控制PH=7~8
Ca(OH)2+H2SO4=CaSO4↓+2H2O
2H3AsO3+Ca(OH)2=Ca(AsO2)2↓+4H2O
氧化反应分别使Fe2+氧化成Fe3+,As3+氧化成As5+生成铁盐及亚铁盐。
4Fe(OH)2+O2+2H2O=4Fe(OH)3
2Fe(OH)3+3As2O3=2Fe(AsO2)3↓+3H2O
Fe(OH)3+H3AsO4=F3AsO4+3H2O
Fe(OH)3+H3AsO4=FeAsO3+3H2O
2.2.2 影响因素
①PH影响
二段中和控制PH=10~11,使上述反应中的铁砷盐和钙盐在碱性条件下完全沉淀。
在上述反应中,要保证砷的去除率达到99%,关键在控制二段中和反应的条件,依据有关去砷的试验资料,见图3、图4,但二段中和反应控制PH=9~11时,可使出水中As<0.5mg/L。
②Fe/As的影响
分析不同pH值与铁盐共沉曲线图,当Fe/As>10时,处理出水中的砷<0.5mg/L,在生产中,对不同的含砷酸性水按上述控制参数及反应条件进行调整,都取得了较好的处理效果。
③凝聚剂的影响
在上述反应后添加凝聚剂有助于中和产物的快速沉淀,PAM具有较好的吸附、桥联作用,使铁砷盐及钙盐在浓缩池中能够快速沉淀。
④设备的影响
两段中和加铁盐去除含砷污水处理工艺,处理效果的优劣与工艺装备及测控设施的先进可靠程度有关,关键设备及仪表采用目前国内外的先进产品,能为整个处理工艺的达标运行奠定了可靠的基础。
3 中和渣的处理
脱水后的中和渣主要成分是石膏和铁砷盐,含其它重金属碱式盐(Cu(OH)2,Zn(OH)2等),在目前阶段,回收其中的有用金属难度大,生产成本高。
为了不造成二次污染,必须对中和渣进行妥善处理。
通常采用永久渣场填埋。
4 结论
4.1 铜冶炼企业含砷污水处理采用硫化法和石灰乳两段中和加铁盐除砷工艺,能够达到预期目标,但污酸处理存在着处理成本高的问题,有待于新的处理工艺运用,目前国内已有院校试验电积法处理含砷污酸,其成本低于硫化法,将给企业带来明显的经济效益。
4.2 目前铜冶炼企业含砷工业污水虽然经处理后做到了达标排放,但在处理水返回使用,降低处理成本方面仍有许多工作可做,这些工作与企业体制,管理水平有着明确的联系。
做好这些工作可明显提高企业的经济效益和环境效益。