聚合物的流变性能解析.docx
《聚合物的流变性能解析.docx》由会员分享,可在线阅读,更多相关《聚合物的流变性能解析.docx(11页珍藏版)》请在冰豆网上搜索。
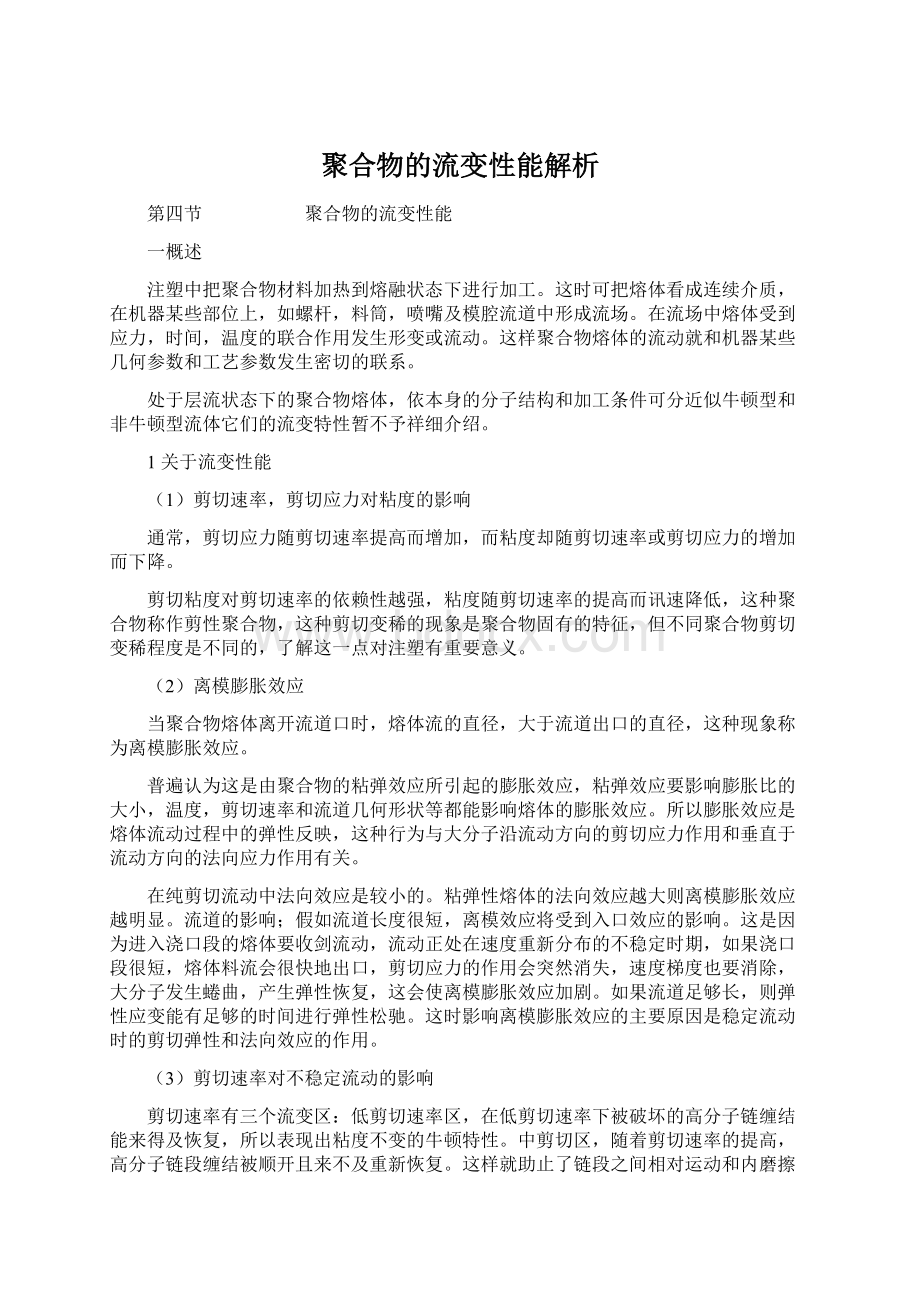
聚合物的流变性能解析
第四节 聚合物的流变性能
一概述
注塑中把聚合物材料加热到熔融状态下进行加工。
这时可把熔体看成连续介质,在机器某些部位上,如螺杆,料筒,喷嘴及模腔流道中形成流场。
在流场中熔体受到应力,时间,温度的联合作用发生形变或流动。
这样聚合物熔体的流动就和机器某些几何参数和工艺参数发生密切的联系。
处于层流状态下的聚合物熔体,依本身的分子结构和加工条件可分近似牛顿型和非牛顿型流体它们的流变特性暂不予祥细介绍。
1关于流变性能
(1)剪切速率,剪切应力对粘度的影响
通常,剪切应力随剪切速率提高而增加,而粘度却随剪切速率或剪切应力的增加而下降。
剪切粘度对剪切速率的依赖性越强,粘度随剪切速率的提高而讯速降低,这种聚合物称作剪性聚合物,这种剪切变稀的现象是聚合物固有的特征,但不同聚合物剪切变稀程度是不同的,了解这一点对注塑有重要意义。
(2)离模膨胀效应
当聚合物熔体离开流道口时,熔体流的直径,大于流道出口的直径,这种现象称为离模膨胀效应。
普遍认为这是由聚合物的粘弹效应所引起的膨胀效应,粘弹效应要影响膨胀比的大小,温度,剪切速率和流道几何形状等都能影响熔体的膨胀效应。
所以膨胀效应是熔体流动过程中的弹性反映,这种行为与大分子沿流动方向的剪切应力作用和垂直于流动方向的法向应力作用有关。
在纯剪切流动中法向效应是较小的。
粘弹性熔体的法向效应越大则离模膨胀效应越明显。
流道的影响;假如流道长度很短,离模效应将受到入口效应的影响。
这是因为进入浇口段的熔体要收剑流动,流动正处在速度重新分布的不稳定时期,如果浇口段很短,熔体料流会很快地出口,剪切应力的作用会突然消失,速度梯度也要消除,大分子发生蜷曲,产生弹性恢复,这会使离模膨胀效应加剧。
如果流道足够长,则弹性应变能有足够的时间进行弹性松驰。
这时影响离模膨胀效应的主要原因是稳定流动时的剪切弹性和法向效应的作用。
(3)剪切速率对不稳定流动的影响
剪切速率有三个流变区:
低剪切速率区,在低剪切速率下被破坏的高分子链缠结能来得及恢复,所以表现出粘度不变的牛顿特性。
中剪切区,随着剪切速率的提高,高分子链段缠结被顺开且来不及重新恢复。
这样就助止了链段之间相对运动和内磨擦的减小。
可使熔体粘度降低二至三个数量级,产生了剪切稀化作用。
在高剪切区,当剪切速率很高粘度可降至最小,并且难以维持恒定,大分子链段缠结在高剪切下已全部被拉直,表现出牛顿流体的性质。
如果剪切速率再提高,出现不稳定流动,这种不稳定流动形成弹性湍流熔体出现波纹,破裂现象是熔体不稳定的重要标志。
当剪切速率达到弹性湍流时,熔体不仅不会继续变稀,反而会变稠。
这是因为熔体发生破裂。
(4)温度对粘度的影响
粘度依赖于温度的机理是分子链和“自由体积”与温度之间存在着关联。
当在玻璃化温度以下时,自由体积保持恒定,体积随温度增长而大分子链开始振动。
当温度超过玻璃化温度时,大链段开始移动,链段之间的自由体积增加,链段与链段之间作用力减小,粘度下降。
不同的聚合物粘度对温度的敏感性有所不同。
(5)压力对粘度的影响
聚合物熔体在注塑时,无论是预塑阶段,还是注射阶段,熔体都要经受内部静压力和外部动压力的联合作用。
保压补料阶段聚合物一般要经受1500~2000kgf/cm2压力作用,精密成型可高达4000kgf/cm2,在如此高的压力下,分子链段间的自由体积要受到压缩。
由于分子链间自由体积减小,大分子链段的靠近使分子间作用力加强即表现粘度提高。
在加工温度一定时,聚合物熔体的压缩性比一般液体的压缩性要大,对粘度影响也较大。
由于聚合物的压缩率不同,所以粘度对压力的敏感性也不同;压缩率大的敏感性大。
聚合物也由于压力提高会使粘度增加,能起到和降低熔体温度一样的等效作用。
(6)分子量对粘度的影响
一般情况下粘度随分子量增加而增加,由于分子量增加使分子链段加度,分子链重心移动越慢,链段间的相对们移抵消机会越多,分子链的柔性加大缠结点增多,链的解脱和滑移困难。
使流动过程助力增大,需要的时间和能量也增加。
由于分子量增加引起聚合物流动降低,使注塑困难,因此常在高分子量的聚合物中加入一些低分子物质,如增塑剂等,来降低聚合物的分子量,以达到减小粘度,改善加工性能。
第三章制品成型机理
第一节 结晶效应
1结晶概念
聚合物的超分子结构对注塑条件及制品性能的影响非常明显。
聚合物按其超分子结构可分为结晶型和非结晶型,结晶型聚合物的分子链呈有规则的排列,而非结晶态聚合物的分子链呈不规则的无定型的排列。
不同形态表现出不同的工艺性质误物理—机械性质。
一般结晶型聚合物具有耐热性和较高的机械强度,而非结晶型则相反。
分子结构简单,对称性高的聚合物都能生成结晶,如PE等,分子链节虽然大,但分子间的作用力很强也能生成结晶,如POM,PA等。
分子链刚性大的聚合物不易生成结晶,如PC,PSU,PPO等。
评定聚合物结晶形态的标准是晶体形状,大小及结晶度。
2聚合物结晶度对制品性能的影响
(1)密度.结晶度高说明多数分子链已排列成有序而紧密的结构,分子间作用力强,所以密度随结晶度提高而加大,如70%结晶度的PP,其密度为0.896,当结晶度增至95%时则密度增至o.903。
(2)拉伸强度结晶度高,拉伸强度高。
如结晶度70%的聚丙烯其拉伸强度为27.5mpa,当结晶度增至95%时,则拉伸强度可提高到42mpa。
(3)冲击强度冲击强度随结晶度提高而减小,如70%结晶度的聚丙烯,其缺口冲击强度15.2kgf-cm/cm2,当结晶度95%时,冲击强度减小到4.86kgf-cm/cm2。
(4)热性能结晶度增加有助于提高软化温度和热变形温度。
如结晶度为70%的聚丙烯,载荷下的热变形温度为125度,而结晶度95%时侧为151度。
刚度是注塑制品脱模条件之一,较高的结晶度会减少制品在模内的冷却周期。
结晶度会给低温带来脆弱性,如结晶度分别为55%,85%,95%的等规聚丙烯其脆化温度分别为0度,10度,20度。
(5)翘曲结晶度提高会使体积减小,收缩加大,结晶型材料比非结晶型材料更易翘曲,这是因为制品在模内冷却时,由于温度上的差异引起结晶度的差异,使密度不均,收缩不等,导致产生较高的内应力而引起翘曲,并使耐应力龟裂能力降低。
(6)光泽度结晶度提高会增加制品的致密性。
使制品表面光泽度提高,但由于球晶的存在会引起光波的散射,而使透明度降低。
3影响结晶度的因素
(1)温度及冷却速度结晶有一个热历程,必然与温度有关,当聚合物熔体温度高于熔融温度时大分子链的热运动显著增加,到大于分子的内聚力时,分子就难以形成有序排列而不易结晶;当温度过低时,分子链段动能很低,甚至处于冻结状态,也不易结晶。
所以结晶的温度范围是在玻璃化温度和熔融温度之间。
在高温区(接近熔融温度),晶核不稳定,单位时间成核数量少,而在低温区(接近玻璃化温度)自由能低,结晶时间长,结晶速度慢,不能为成核创造条件。
这样在熔融温度和玻璃化温度之间存在一个最高的结晶速度和相应的结晶温度。
温度是聚合物结晶过程最敏感性因素,温度相差1度,则结晶速度可能相差很多倍。
聚合物从熔点温度以上降到玻璃化温度以下,这一过程的速度称冷却速度,它是决定晶核存在或生长的条件。
注塑时,冷却速度决定于熔体温度和模具温度之差,称过冷度。
根据过冷度可分以下三区。
a等温冷却区,当模具温度接近于最大结晶速度温度时,这时过冷度小,冷却速度慢,结晶几乎在静态等温条件下进行,这时分子链自由能大,晶核不易生成,结晶缓慢,冷却周期加长,形成较大的球晶。
b快速冷却区,当模具温度低于结晶温度时过冷度增大,冷却速度很快结晶在非等温条件下进行,大分子链段来不及折叠形成晶片,这时高分子松驰过程滞后于温度变化的速度,于是分子链在骤冷下形成体积松散的来不及结晶的无定型区。
例如:
当模具型腔表面温度过低时,制品表层就会出现这种情况,而在制品心部由于温度梯度的关系,过冷度小,冷却速度慢就形成了具有微晶结构的结晶区。
c中速成冷却区,如果把冷却模温控制在熔体最大结晶速度温度与玻璃化温度之间,这时接近表层的区域最早生成结晶,由于模具温度较高,有利于制品内部晶核生成和球晶长大。
结晶的也比较完整。
在这一温度区来选择模温对成型制品是有利的,因为这时结晶速率常数大,模温较低,制品易脱模,具注塑周期短。
例如:
PETP。
建议模温控制在(140~190度),PA6,PA66,模温控制在(70~120度),PP模温控制在(30~80)这有助于结晶能力提高在注塑中模温的选择应能使结晶度尽可能达到最接近于平衡位置。
过低过高都会使制品结构不稳定,在后期会发生结晶过程在温度升高时而发生变化,引起制品结构的变化。
(2)熔体应力作用,熔体压力的提高,剪切作用的加强都会加速结晶过程。
这是由于应力作用会使链段沿受力方向而取向,形成有序区,容易诱导出许多晶胚,使用权晶核数量增加,生成结晶时间缩短,加速了结晶作用。
压力加大还会影响球晶的尺寸和形状,低压下容易生成大而完整的球晶,高压下容易生成小而不规则的球晶。
球晶大小和形状除与大小有关还与力的形式有关。
在均匀剪切作用下易生成均匀的微晶结构,在直接的压力作用下易生成直径小而不均匀的球晶。
螺杆式注塑机加工时,由于熔体受到很大的剪切力作用,大球晶被粉碎成微细的晶核,形成均匀微晶。
而塞式注塑机相反。
球晶的生成和发展与注塑工艺及设备条件有关。
用温度和剪切速率都能控制结晶能力。
在高剪切速率下得到的PP制品冷却后具有高结晶度的结构,而且PP受剪切作用生成球晶的时间比无剪切作用在静态熔体中生成球晶的时间要减少一半。
对结晶型聚合物来说,结晶和取向作用密切相关,因此结晶和剪切应力也就发生联系;剪切作用将通过取向和结晶两方面的途径来影响熔体的粘度。
从而也就影响了熔体在喷嘴,流道,浇口,型腔中的流动。
根据聚合物取向作用可提前结晶的道貌岸然理,在注塑中提高注射压力和注射速率而降低熔体粘度的办法为结晶创造条件。
当然,应以熔体不发生破裂为限。
在注塑模具中发生结晶过程的重要特点是它的非等温性。
熔体进入模具时,接近表面层先生成小球晶,而内层生成大的球晶;浇口附近温度高,受热时间长结晶度高,而远离浇口处因冷却快,结晶度低,所以造成制品性能上的不均匀性。
第二节 取向效应
1取向机理
聚合物在加工过程中,在力的作用下,流动的大分子链段一定会取向,取向的性质和程度根据取向条件有很大的区别。
按熔体中大分子受力的形式误作用的性质可分为剪切应力作用下的“流动取向”和受拉伸作用下的“拉伸取向”。
按取向结构单元的取向方向,可分单轴和双轴或平面取向。
按熔体温场的稳定性可分等温和非等温流动取向。
也可分结晶和非结晶取向。
聚合物熔体在模腔中的流动是注塑的主要流动过程,熔体在型腔中取向过程,将直接影响制品的质量。
欲理解注塑制品在型腔中成型的机理需了解无定型聚合物的取向机理。
充模时,无定型聚合物熔体是沿型壁流动,熔体流入型腔首先同模壁接触霰成来不及取向的冻结层外壳。
而新料沿着不断增长地凝固层内壁向前流动。
推动波前峰向前移动。
靠近凝固层的分子链,一端被固定凝固层上,而另一端被邻层的分子链沿着流动方向而取向。
由于靠近凝固层助力最大,速度最小;而中心外流动助力最小,速度最大,这样在垂直于流动方向上形成速度梯度;凝固层处的速度梯度最大,中心处的速度梯度最小,因此靠近凝固层的熔体流受剪切作用最强,取向程度最大,而在靠近中心层剪切作用最小,取向也最小,形成小取向层区。
2取向对制品性能的影响
由于非结晶型聚合物的取向是大分子链在应力作用方向上的取向,所以在取向方向的力学性质明显增加,而垂直于取向方向的力学性质却又明显地降低;在取向方向的拉伸强度,断裂伸长率,随取向度增加而提高。
双轴取向的制品其力学性质具有各异性并与两个方向拉伸倍数有关。
双轴取向改变了单轴取向的力学性质。
在通常注塑条件下,注塑制品在流动方向上的拉伸强度大约是垂直方向的确良1~2.9倍,而冲击强度为1~10倍,说明垂直于流动方向上的冲击强度降低很多。
注塑制品的玻璃化转变温度随取向度提高而上升。
有的随取向度高和结晶度的提高,其聚合物的玻璃化温度值可升高~25度。
由于在制品中存在有一定的高弹形秋,一定温度下已取向的分子链段要产生松驰作用:
非结晶型聚合物的分子链要重新蜷曲,结晶率与取向度成正比。
所以收缩程度是取向程度的反映。
线膨胀系数也将随取向度而变化;在垂直于流动方向线膨胀系数比取向方向约大3倍。
取向后的大分子被拉长,分子之间的作用力增加,发生“应力硬化”现象,表现了注塑制品模量提高的现象。
“冻结取向”越大,则越容易发生应力松驰,制品收缩也越大。
所以制品收缩反映了取向的程度。
3影响制品取向的因素
在注塑加工中,聚合物熔体的取向过程可分两个阶段进行。
第一阶段是充模阶段,这时流动的特点是:
熔体压力低,剪切速率大,模壁处的物料在快速冷却条件丐进行。
这一阶段聚合物熔体的粘度主要是温度和剪切速率的函数。
第二阶段是保压阶段。
其特点是剪切速率低,压力高,温度逐渐下降。
聚合物熔体的粘度主要依赖于温度和注射压力,但对取向影响主要是熔体加工温度。
对结晶影响主要是模具温度。
取向即与剪切或拉伸作用有关,也与大分子链的自由能有关。
根据这种机理,控制取向的条件有以下因素。
(1)物料温度和模具温度增高都会使取向效自学成才降低。
因为熔体升高时粘度会降低。
如果熔体加工温度高它和凝固温度之间的温度域加宽,松驰时间加长,容易解取向。
非结晶型聚合物的松驰时间是从加工温度降至玻璃化温度的时间,而对结晶型聚合物是加工温度至熔化温度的时间,由于熔点温度高于玻璃化温度,显然非结晶型聚合物松驰时间要长于结晶型聚合物。
因此加工结晶型聚合物冷却速度大,松驰过程短。
容易产生冻结取向。
而非结晶型聚合物冷却速度慢,松驰过程长容易解取向,取向效果将减小。
(2)注射压力增加可提高熔体的剪切自学成才力和剪切速率,有助于加速高分子的取向效应。
因此,注射压力与保压压力的提高都会使结晶与取向作用加强,制品的密度将随保压压力的升高而讯速增长。
(3)浇口封闭时间会影响取向效应。
如果熔体流动停止后,大分子的热运动仍较强烈,会使已取向的单元又发生松驰,产生解取向的效应。
采用大的浇口由于冷却得慢,封闭时间延长,熔体流动时间延长增加了取向效果,尤其在浇口处的取向更为明显,所以直浇口比点浇口更容易维持取向效应。
(4)模具温度较低时,冻结取向效应提高。
而解取向作用减小。
(5)关于充模速度对制品取向的影响。
快速充模会引起表面部位的高度取向,但内部取向小,因为在一定温度条件下,快速充模会维持其制品心部在较高的温度下冷却,使冷却时间加长,高分子松驰时间延长使解取向能力加强,所以心部取向程度反而比表层的小。
在注射温度相同条件下,慢速充模会延长流动时间,实际熔体温度要降低,剪切力要增加。
这时熔体的实际温度与玻璃化温度或熔点的区间要比快速充模区间小,则应力松驰时间也短,所以解取向作用小;另一方面慢速充模熔体的温度比快速充模时来得低些,解取向作用减小,而取向作用会增加。
就制品心部的结构形态而言,快速充模会引起较小的取向,而慢速充模反而会引起大的取向。
综上所述,影响聚合物结晶与取向的因素有以下几个方面:
1温度:
a熔体温度。
b熔体加工过程的温度。
c模具温度。
d聚合物熔点。
e聚合物玻璃化温度。
f熔体最大结晶速率温度。
2时间:
a聚合物加热时间。
b充模时间。
c保压时间。
d浇口封闭时间。
e冷却时间。
3压力:
a充模压力。
b保压压力。
4速度:
a充模速度。
b塑化速度。
第三节内应力
1内应力产生
在注塑制品中,各处局部应力状态是不同的,制品变形程度将决定于应力分布。
如果制品在冷却时。
存在温度梯度,则这类应力会发展,所以这类应力又称为“成型应力”。
注塑制品的内应力包两种:
一种是注塑制品成型应力,另一种是温度应力。
当熔体进入温度较低的模具时,靠近模腔壁的熔体讯速地冷却而固化,于是分子链段被“冻结”。
由于凝固的聚合物层,导热性很差,在制品厚度方向上产生较大的温度梯度。
制品心部凝固相当缓慢,以致于当浇口封闭时,制品中心的熔体单元还未凝固,这时注塑机又无法对冷却收缩进行补料。
这样制品内部收缩作用与硬皮层作用方向是相反的;心部处于静态拉伸而表层则处于静态压缩。
在熔体充模流动时,除了有体积收缩效应引起的应力外。
还有因流道,浇口出口的膨胀效应而引起的应力;前一种效应引起的应力与熔体流动方向有关,后者由于出口膨胀效应将引起在垂直于流动方向应力作用。
2 影响愉应力的工艺因素
(1)向应力的影响在速冷条件下,取向会导致聚合物内应力的形成。
由于聚合物熔体的粘度高,内应力不能很快松驰,影响制品的物理性能和尺寸稳定性。
各参数对取向应力的影响
a熔体温度,熔体温度高,粘度低,剪切应力降低取向度减小;另一方面由于熔体温度高会使应力松驰加快,促使解取向能力加强。
可是在不改变注塑机压力的情况下,模腔压力会增大,强剪切作用又导致取向应力的提高。
b在喷嘴封闭以前,延长保压时间,会导致取向应力增加。
c提高注射压力或保压压力,会增大取向应力,
d模具温度高可保证制品缓慢冷却,起到解取向作用。
e增加制品厚度使取向应力降低,因为厚壁制品冷却时慢,粘度提高慢,应力松驰过程的时间长,所以取向应力小。
(2)对温度应力的影响
如上所述由于在充模时熔体和型壁之间温度梯度很大,先凝固的外层熔体要助止后凝固的内层熔体的收缩,结果在外层产生压应力(收缩应力),内层产生拉应力(取向应力)。
如果充模后又在保压压力的作用下持续较长时间,聚合物熔体又补入模腔中,使模腔压力提高,此压力会改变由于温度不均而产生的内应力。
但在保压时间短,模腔压力又较低的情况下,制品内部仍会保持原来冷却时的应力状态。
如果在制品冷却初期模腔压力不足时,制品的外层会因凝固收缩而形成凹陷;如果在制品已形成冷硬层的后期模腔压力不足时,制品的内层会因收缩而分离,或形成空穴;如果在浇口封闭前维持模腔压力,有利于提高制品密度,消除冷却温度应力,但是在浇口附近会产生较大的应力集中。
由此看来热塑性聚合物在成型时,模内压力越大保压时间越长,有助于温度所产生的收缩应力的减小反之会使压缩应力增大。
3内应力与制品质量的关系
制品中内应力的存在会严重影响制品的力学性质和使用性能;由于制品内应力的存在和分布不均,制品在使用过程中会发生裂纹。
在玻璃化温度以下使用时,常发生不规则的变形或翘曲,还会引起制品表面“泛白”,浑浊,光学性质变坏。
设法降低浇口处温度,增加缓冷时间,有利于改善制品的应力不均,使制品的机械性能均一。
不管对结晶型聚合物还是非结晶型聚合物,拉伸强度都表现出各向异向的特点。
对非结晶型聚合物拉伸强度会因浇口的们置而异;当浇口与充模方向一致时,拉伸强度随熔体温度提高而降低;当浇口与充模方向垂直时,拉伸强度随熔体温度的提高而增加。
由于熔体温度提高导致解取向作用加强,而取向作用减弱使拉伸强度降低。
浇口的方位会通过影响料流的方向来影响取向,又由于非结晶型聚合物比结晶型聚合物的各向异性表现的强烈,所以在垂直于流动方向上的拉伸强度前者比后者大。
低温注射比高温注射有更大的力学各向异性,如注射温度高时,垂直方向与流动方向的强度比为1.7,注射温度低时为2。
由此看来,熔体温度的提高,不论对结晶型聚合物还是非结晶型聚合物都会导致拉伸强度的降低,但机理却不一样;前者是由于通过取向作用降低的影响。
第四章成型故障及其解决方法
第三节 聚丙烯故障的产生原因及排除方法
一欠注
故障分析及排除方法:
1.工艺条件控制不当。
应适当调整。
2.注塑机的注射能力小于塑件重量。
应换用较大规格的注塑机。
3.流道和浇口截面太小。
应适当加大。
4.模腔内熔料的流动距离太长或有薄壁部分。
应设置冷料穴。
5.模具排气不良,模腔内的残留空气导致欠注。
应改善模具的排气系统。
6.原料的流动性能太差。
应换用流动性能较好的树脂。
7.料筒温度太低,注射压力不足或补料的注射时间太短也会引起欠注。
应相应提高有关工艺参数的控制量。
二溢料飞边
故障分析及排除方法:
1.合模力不足。
应换用规格较大的注塑机。
2.模具的销孔或导销磨损严重。
应采用机加工方法进行修复。
3.模具的合模面上有异物杂质。
应进行清除。
4.成型模温或注射压力太高。
应适当降低。
三表面气孔
故障分析及排除方法:
1.厚壁塑件的模具流道及浇口尺寸较小时容易产生表面气孔。
应适当放大流道和浇口尺寸。
2.塑件壁太厚。
在设计时应尽量减少壁厚部分。
3.成型温度太高或注射压力太低都会导致塑件表面产生气孔。
应适当降低成型温度,提高注射压力。
四流料痕
故障分析及排除方法:
1.熔料及模温太低。
应适当得高料筒和模具温度。
2.注射速度太慢。
应适当加快注射速度。
3.喷嘴孔径太小。
应换用孔径较大的喷嘴。
4.模具内未设置冷料穴。
应增设冷料穴。
五银条丝
故障分析及排除方法:
1.成型原料中水分及易挥发物含量太高。
应对原料进行预干燥处理。
2.模具排气不良。
应增加排气孔,改善模具的排气性能。
3.喷嘴与模具接触不良。
应调整两者的位置及几何尺寸。
4.银条丝总是在一定的部位出现时,应检查对应的模腔表面是否有表面伤痕。
如有表面伤痕的复映现象,应采取机加工方法去除模腔表面伤痕。
5.不同品种的树脂混合时,会产生银条痕。
应防止异种树脂混用。
六熔接痕
故障分析及排除方法:
1.熔料及模具温度太低。
应提高料筒及模具温度。
2.浇口位置设置不合理。
应改变浇口位置。
3.原料中易挥发物含量太高或模具排气不良。
应除去原料内的易挥发物质及改善模具的排气系统。
4.注射速度太慢。
应适当加快。
5.模具内未设置冷料穴。
应增设冷料穴。
6.模腔表面有异物杂质。
应进行清洁处理。
7.浇注系统设计不合理。
应改善浇注系统的充模性能,使熔料在模腔中流动顺畅。
七黑条及烧焦
故障分析及排除方法:
1.注塑机规格太大。
应换用规格较小的注塑机。
2.树脂的流动性能较差。
应使用适量的外部润滑剂。
3.注射压力太高。
应适当降低。
4.模具排气不良。
应改善模具的排气系统,增加乔气孔或采用镶嵌结构,以及适当降低合模力。
5.浇口位置设置不合理。
应改变浇口位置,使模腔内的熔料均匀流动。
八气泡
故障分析及排除方法:
1.浇口及流道尺寸太小。
应适当加大。
2.注射压力太低。
应适当提高。
3.原料内水分含量太高。
应对原料进行预干燥处理。
4.塑件的壁厚变化太大。
应合理设计塑件的形体结构,避免壁厚急变。
九龟裂及白化
故障分析及排除方法:
1.熔料及模具温度太低。
应提高料筒及模具温度。
2.模具的浇注系统结构设计不合理。
应改善模具流道及浇口结构,使熔料在充模时不产生紊流。
3.冷却时间太短。
应适当延长冷却时间。
4.脱模的顶出装置设计不合理。
最好采用气动脱模装置。
5.注射速度和压力太高。
应适当降低。
十弯曲变形
故障分析及排除方法:
1.模具温度太高或冷却不足。
应适当降低模具温度或延长冷却时间,对于细长塑件可采取胎具固定后冷却的方法。
2.冷却不均匀。
应改善模具的冷却系统,保证塑件冷却均匀。
3.浇口选型不合理。
应针对具体情况,选择合理的浇口形式。
一般情况下,可采用多点式浇口。
4.模具偏芯。
应进行检查和校正。
十一脱模不良
故障分析及排除方法:
1.注射速度和压力太高。
应适当降低。
2.模具型腔表面光洁度太差。
应通过研磨及电镀等方法提高其表面光洁度。
3.模具温度及冷却条件控制不当。
当塑件在模芯处粘模时,应提高模具温度和缩短冷却时间;如果塑件在型腔表面处粘模