微型数控车床设计.docx
《微型数控车床设计.docx》由会员分享,可在线阅读,更多相关《微型数控车床设计.docx(28页珍藏版)》请在冰豆网上搜索。
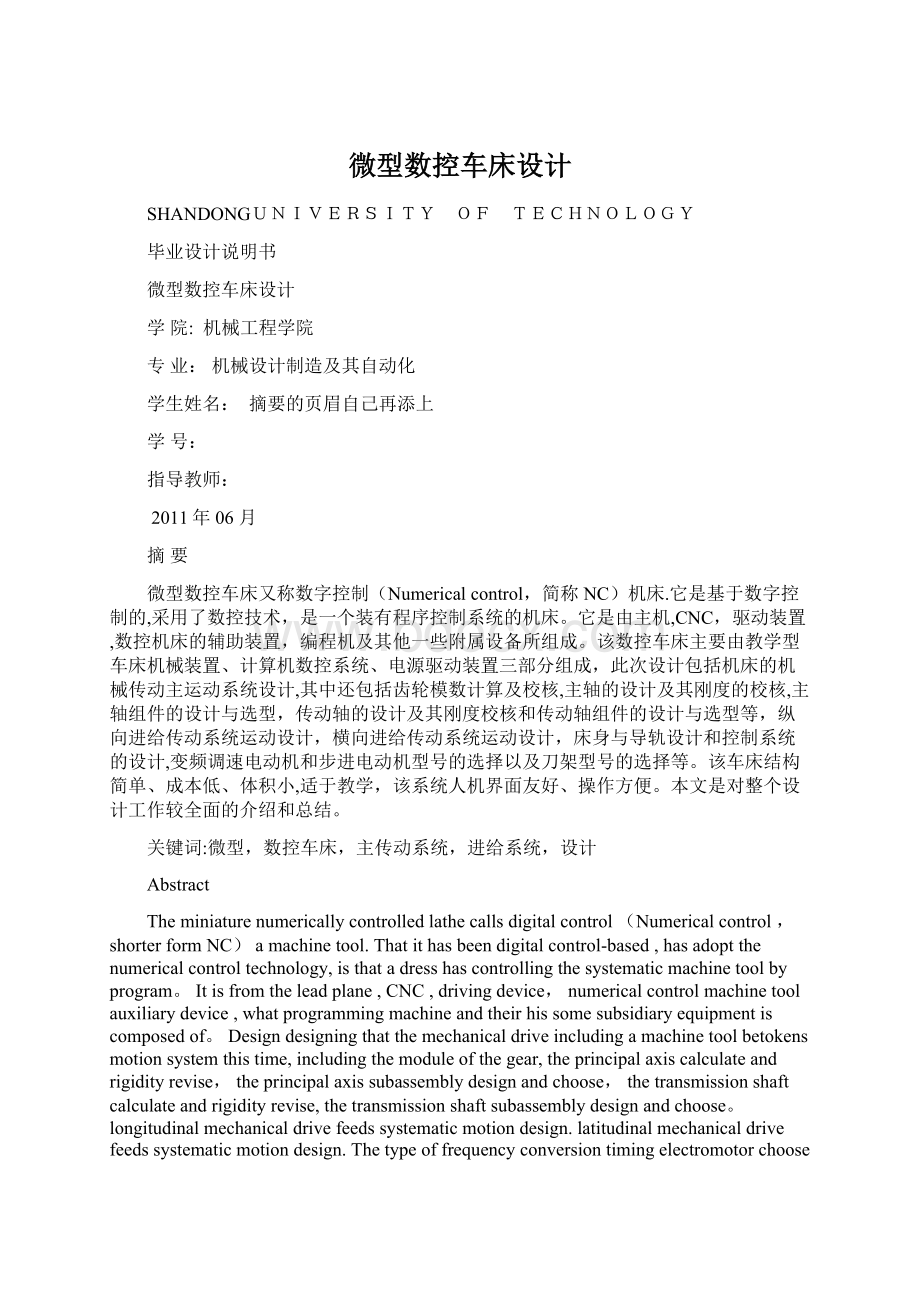
微型数控车床设计
SHANDONGUNIVERSITY OF TECHNOLOGY
毕业设计说明书
微型数控车床设计
学院:
机械工程学院
专业:
机械设计制造及其自动化
学生姓名:
摘要的页眉自己再添上
学号:
指导教师:
2011年06月
摘要
微型数控车床又称数字控制(Numericalcontrol,简称NC)机床.它是基于数字控制的,采用了数控技术,是一个装有程序控制系统的机床。
它是由主机,CNC,驱动装置,数控机床的辅助装置,编程机及其他一些附属设备所组成。
该数控车床主要由教学型车床机械装置、计算机数控系统、电源驱动装置三部分组成,此次设计包括机床的机械传动主运动系统设计,其中还包括齿轮模数计算及校核,主轴的设计及其刚度的校核,主轴组件的设计与选型,传动轴的设计及其刚度校核和传动轴组件的设计与选型等,纵向进给传动系统运动设计,横向进给传动系统运动设计,床身与导轨设计和控制系统的设计,变频调速电动机和步进电动机型号的选择以及刀架型号的选择等。
该车床结构简单、成本低、体积小,适于教学,该系统人机界面友好、操作方便。
本文是对整个设计工作较全面的介绍和总结。
关键词:
微型,数控车床,主传动系统,进给系统,设计
Abstract
Theminiaturenumericallycontrolledlathecallsdigitalcontrol(Numericalcontrol,shorterformNC)amachinetool.Thatithasbeendigitalcontrol-based,hasadoptthenumericalcontroltechnology,isthatadresshascontrollingthesystematicmachinetoolbyprogram。
Itisfromtheleadplane,CNC,drivingdevice,numericalcontrolmachinetoolauxiliarydevice,whatprogrammingmachineandtheirhissomesubsidiaryequipmentiscomposedof。
Designdesigningthatthemechanicaldriveincludingamachinetoolbetokensmotionsystemthistime,includingthemoduleofthegear,theprincipalaxiscalculateandrigidityrevise,theprincipalaxissubassemblydesignandchoose,thetransmissionshaftcalculateandrigidityrevise,thetransmissionshaftsubassemblydesignandchoose。
longitudinalmechanicaldrivefeedssystematicmotiondesign.latitudinalmechanicaldrivefeedssystematicmotiondesign.Thetypeoffrequencyconversiontimingelectromotorchooseandthetypeofwalkingelectromotorchoose,andthetypeofkniferestchoose.Thispaperismorecompehensiveintroductionandsumming-upforthewholedesignwork。
Keywords:
miniature,numericallycontrolledlathemechanical,drivesystembetokenssystematic,feeddrivesystem,design。
第一章引言
1.1课题的背景
当今世界电子技术迅速发展,微处理器、微型计算机在各技术领域得到了广泛应用,对各领域技术的发展起到了极大的推动作用。
一个较完善的机电一体化系统,应包含以下几个基本要素:
机械本体、动力与驱动部分、执行机构、传感测试部分、控制及信息处理部分。
随着微电子技术的发展,大规模集成电路的集成度越来越高,体积越来越小.数控设备厂采用超大规模集成电路并采用表面安装工艺(SMT),实现了三维立体装配,将整个CNC装置做得很小,以适应机械制造业机电一体化的要求.日本三菱电机株式会社,最近推出的普及型CNCMELDAS50系列及实用型CNCMELDAS520A系列,这两个系列都采用了32位RISC微处理器,实现超小型化的CNC装置,较原来的M310及L3、L3A,体积大为减小(H168mm×W76mm×D135mm),安装面积减小了一半,功能还有所进步。
采用了超薄型显示器(9。
5in的EL及10。
4in的彩色LCD)。
这个系统的微小线段加工能力提升至64m/min,最大快速进给速度为240m/min,其同步攻螺纹精度较M310进步了3倍,主轴定位时间缩短了30%。
德国SIEMENS公司最新推出的SINUMERIK840D主控组件选用386DX或486DX,具有1~4个通道,可实现直线及圆弧插补、螺旋线插补、5轴螺旋线插补及样条插补、圆柱插补等,共可控制32个轴,并有多种校正及补偿功能,体积仅为50mm×316mm×207mm.
东西方制造业的差距更多的在于职教基础的差距,实践动手能力的差距,我国数控学员储备60万人,而全国数控人才每年缺口15万人,高级数控技工年薪高达10万,那种20人/台的教学实效性与成材率不匹配的矛盾日益突出。
1.2课题的目的和意义
生产型数控机床作为数控教学实习设备是十分必要的,但在前期教学中使用则耗电大、材料消耗大、安全系数相对较低成为困扰许多院校的大问题。
西方发达国家数控教学前期阶段都是采用小型台式高仿真数控教学机床作为数控编程和操作的实习设备。
目前数控技术课程实训过程中普遍存在以下现实问题:
系统开放性差、操作界面不太理想、教学设备成本高、实验耗材费用高、操作危险性大、学生独立动手机会少、教学效率低、教学质量差等。
因此需要设计一个软硬件结构开放、功能完善、人机界面友好、操作方便的系统,来解决了授课过程中存在的课堂教学难、实验教学难、实训教学难的问题。
第二章微型数控车床主传动系统设计
2。
1主要设计技术指标与参数:
两个坐标方向的工作行程:
X:
30mmZ:
100mm。
加工精度:
0.01mm。
加工材料:
石蜡、肥皂类或铝质类等。
2。
2主传动系统的大分类:
目前,主传动系统大致可分为以下大类。
2.2。
1带有变速齿轮的主传动
如图2—1a)所示,通过少数几对齿轮降速,以满足主轴低速时对扭矩特性的要求。
数控机床在交流或直流电机无级变速的基础上配以齿轮变速,使之成为分段无级变速。
滑移齿轮的移位大都采用液压缸和拨叉或直接由液压缸带动齿轮来实现。
2。
2。
2通过带传动的主传动
如图2-1b)所示,这种传动主要应用在小型数控机床上,由交流电机通过V带直接带动主轴。
这种传动方式可以避免齿轮传动时引起的振动与噪声,但只能适用于低扭矩特性要求的主轴。
2.2。
3调速电机直接驱动的主传动
如图2-1c)所示,这种主传动方式大大简化了主轴箱体与主轴的结构,有效地提高了主轴部件的刚度,但主轴输出扭矩小,电机发热对主轴影响较大。
图2—1主传动型式
本数控车床选用无级变速。
2.3确定合适的切削参数:
本机床加工的工件为代木、石腊,铝等材料,查《金属切削原理》(陈日曜主编)表11—5,选择机床背吃刀量=1mm;进给量f=0。
18mm/r;切削速度v=250m/min.
2.3。
1计算切削力:
由公式查《金属切削原理》(陈日曜主编)表4—1,
得=11N,进给抗力和切深力可按下列比例分别计算:
,计算的=2.75N,=4。
4N。
2。
3.2确定机床的切削功率:
切削功率是力和所消耗的功率之和,因方向没有位移,所以不消耗动力。
于是:
切削功率
式中——纵向切削力(N);
V——切削速度(m/min);
——进给力(N);
-—工件转速(r/s);
f——进给量(mm/r)。
粗略计算切削功率=45。
8w,机床效率取,计算机床电机功率.
由此选用额定功率100w中大交流变频调速电动机,参数如表2-1:
电机型号
出力
电压
频率
极数
额定转速
最高转速
额定电流
额定力矩
启动转矩
带齿轴电机
W
V
Hz
P
r/min
r/min
A
N·m
N·m
Kgf·cm
5RK100GU—AF
100
1ph100
50
4
1000
3000
2。
10
0.90
0。
78
7。
80
表2—1额定功率100w中大交流变频调速电动机参数
2。
4主传动系统的设计计算:
主轴的计算转速:
。
主轴要求的恒功率变速范围:
电动机的恒功率变速范围:
。
该系统至少需要的变速级数、变速组数:
。
取.
变速箱实际公比:
.
传动的最小传动比:
.
其他传动副的传动比:
。
电动机的最高和最低工作转速分别为:
。
转速图如图2-2所示:
图2-2主传动系统转速图
电动机最高、最低工作转速时所传递的功率分别为:
2.5齿轮的设计计算:
2.5。
1齿轮的设计
该传动系统有一个变速组,两个传动副。
同一变速组,模数相同,不采用变位齿轮,为第一传动副的主、被动齿轮的齿数,为第二传动副的主、被动齿轮的齿数。
m相同,则:
取S=110,得.
确定各个齿轮的尺寸:
选用直齿圆柱轮,取m=2。
5,则分度圆直径:
,各个齿轮的齿顶高:
,各个齿轮的齿根高:
取齿宽系数,则各个齿轮的齿宽为:
2.5.2齿轮的校核:
齿轮齿面接触疲劳强度的校核计算:
(参考《机械设计》高等教育出版社)
一级减速齿轮的校核:
圆周速度
精度等级由表12。
6选8级精度
使用系数由表12.9
动载系数由图12.9
齿间载荷分配系数由表12.10,先求
由此得
齿向载荷分配系数由表12。
11
载荷系数
弹性系数由表12。
12
节点区域系数由图12.16
接触最小安全系数由表12。
14
总工作时间取
应力循环次数由表12.15,估计〈〈,则指数取8.78
原估计应力循环次数正确。
接触寿命系数由图12.18
许用接触应力
==
验算
22.82
<
计算结果表明,齿面接触疲劳强度合适,
齿轮尺寸无需调整。
齿根弯曲疲劳强度验算:
重合度系数=0。
68
齿间载荷分配系数由表12。
10,
齿向载荷分配系数
由图12。
14
载荷系数
齿形系数由图12。
11
弯曲疲劳极限由图12.23C
弯曲最小安全系数由表12。
14
应力循环次数由表12。
15,估计<,则指数取49.91
原估计应力循环次数正确。
弯曲寿命系数由图12。
24
尺寸系数由图12。
25
许用弯曲应力
==
验算
〈
〈
传动无过载,不须作静强度校核。
一级减速齿轮的校核:
圆周速度
精度等级由表12.6选8级精度
使用系数由表12.9
动载系数由图12。
9
齿间载荷分配系数由表12.10,先求
由此得
齿向载荷分配系数由表12.11
载荷系数
弹性系数由表12.12
节点区域系数由图12.16
接触最小安全系数由表12.14
总工作时间取
应力循环次数由表12.15,估计〈<,则指数取8。
78
原估计应力循环次数正确。
接触寿命系数由图12。
18
许用接触应力
==
验算
58.82
<
计算结果表明,齿面接触疲劳强度合适,
齿轮尺寸无需调整。
齿根弯曲疲劳强度验算:
重合度系数=0。
68
齿间载荷分配系数由表12。
10,
齿向载荷分配系数
由图12.14
载荷系数
齿形系数由图12。
11
弯曲疲劳极限由图12.23C
弯曲最小安全系数由表12。
14
应力循环次数由表12。
15,估计<,则指数取49。
91
原估计应力循环次数正确。
弯曲寿命系数由图12.24
尺寸系数由图12。
25
许用弯曲应力
==
<
<
传动无过载,不须作静强度校核.
2。
6主轴组件设计
2.6。
1主轴组件基本要求
主轴组件是机床主要部件之一。
它的性能对整机的性能有很大的影响.主轴直接承受切削力,转速范围又很大,所以对主轴组件的主要性能特提出如下要求:
旋转精度主轴的旋转精度是指装配后,在无载荷低速转动的条件下,主轴安装工件或刀具部件的定心表面(如该次设计的数控车床主轴轴端的定心短锥采用7:
24锥孔)的径向和轴向跳动。
旋转精度取决于的主要件如主轴、轴承、壳体、孔等的制造,装配和调整精度.工件转速下的旋转精度还取决于主轴的转速、轴承的性能,润滑剂和主轴组件的平衡。
刚度主要反映机床或部件抵抗外载荷的能力。
影响刚度的因素很多,如主轴的尺寸和形状,滚动轴承的型号、数量、预紧和配置形式,前后支撑的跨距和主轴的前悬伸,传动件的布置方式等。
数控机床即要完成粗加工,又要完成精加工,因此对其主轴组件的刚度应提出更高的要求。
温升将引起热变形使主轴伸长,轴承间隙的变化,降低了加工的精度;温升也会降低润滑剂的粘度,恶化润滑条件。
因此,对高精度机床应研究如何减少主轴组件的发热,如何控温等。
可靠性数控机床是高度自动化的机床,所以必须保证工作可靠性,可喜的地方是这方面的研究正在发展.
精度保持性对数控机床的主轴组件必须有足够的耐磨性,以便长期保持精度。
2。
6.2主轴的设计计算:
1初选主轴直径:
主轴直径直接影响主轴部件的刚度,直径越粗,刚度越高,但同时与之相配的轴承等零件的尺寸也越大.故设计之初,只能根据统计资料选择主轴直径。
查阅资料初选主轴前轴颈直径=45mm,后轴直径=30mm。
主轴内孔用来通过棒料,用于通过刀具夹紧装置固定刀具以及传动气动或液压卡盘等。
主轴孔径越大,可通过的棒料直径就越大,机床的使用范围就越宽,同时主轴部件也越轻。
主轴孔径大小主要受主轴刚度的制约。
当主轴的孔径与主轴直径之比小于0。
3时,空心主轴的刚度几乎与实心主轴的刚度相当;为0。
5时,空心主轴的刚度为实心主轴刚度的90%;大于0.7时,空心主轴的刚度急剧下降。
主轴内孔直径选20mm,计算.计算的=0.7,对刚度影响不大。
2主轴悬伸量的确定:
主轴悬伸量是指主轴前支撑径向支反力的作用点到主轴前端面之间的距离,它对主轴组件刚度影响较大,根据分析和试验,缩短悬伸量可以显著提高主轴组件的刚度和抗振性.因此在满足结构要求的条件下,尽量缩短悬伸量a。
初选悬伸量a=41mm。
3主轴跨距及总长的确定:
合理布置各个零件的配合,确定主轴的跨距为266。
5mm,主轴总长314.5m.
4主轴材料选用
主轴选用45钢,调质22~28HRC,局部高频淬硬50~55HRC。
5主轴强度的校核:
计算齿轮受力
齿轮转速
所受转矩4200
所受圆周力
所受径向力
所受法向力
画出主轴受力图如图2—3:
图2—3主轴受力图
计算支撑反力:
水平面反力
垂直面反力
水平面受力图如图2-4:
图2-4主轴水平面受力图
垂直面受力图如图2—5:
图2—5主轴垂直面受力图
画轴的弯矩图:
水平面弯矩图如图2-6:
图2-6主轴水平面弯矩图
垂直面弯矩图如图2-7:
图2—7主轴垂直面弯矩图
合成弯矩图如图2-8:
图2-8主轴合成弯矩图
画轴的转矩图
受转矩
转矩图如图2-9:
图2-9主轴转矩图如图
许用应力
许用应力值用插入法由表16。
3查的
校核轴径
轴径〈35mm
主轴的强度符合要求。
2。
6.3主轴组件的组成和轴承选型
1主轴组件
包括主轴、轴承、传动件和相应的紧固件.主轴组件的构造,主要是支撑部分的构造。
主轴端部是标准的;传动件如齿轮、带轮等与一般机械零件相同。
因此,研究主轴组件,主要是研究主轴的支撑部分.
2主轴的传动件
可以位于前后支撑之间,也可位于后支撑之后的主轴后悬伸端。
目前传动件位于后悬伸端的越来越多。
这样做,可以实现分离传动和模块化设计。
主轴组件(称为主轴单元)和变速箱还可以作成独立的功能部件,又有专门的工厂集中生产,作为商品出售。
变速箱和主轴可用齿轮副或带传动联结.
主轴支撑分径向和轴向.角接触球轴承兼起径向和推力支撑的作用。
推力支撑应位于前支撑内,原因是数控机床的坐标原点,设定在主轴前端.为了减少热膨胀造成的坐标原点的位移,应尽量缩短坐标原点支推力支撑之间的距离。
3主轴组件的动态特性
平移,主轴作为一个刚体(实际上略有弯曲),在弹性支撑上作平移振动,主轴各点的振动方向一致。
2摇摆,主轴在弹性支座上摇摆,左右振动方向相反。
3弯曲,主轴本身作弯曲振动,主轴中间与两端的振动方向相反,有两个节点。
这两个节点位于支撑点附近。
每个振型都有其固有频率。
每个振型固有频率排列的次序,称为阶。
上述三个振型的固有频率,以平移振型为最低,弯曲振型为最高,三个振型分别为第一、二、三振型,振型和固有频率合成为模态。
可以看出,第一、二阶模态的弹性环节主要是轴承;第三阶则主要是轴承。
当轴的刚度提高时,第一、二阶模态的固有频率也随之提高,但第三阶模态提高不多。
主轴是一个连续体,又无穷个模态。
例如还有主轴的扭矩振动、纵向振动等。
但是,这些模态的固有频率较高,工作是不可能发生共振,所以,只需研究最低几阶模态,可用有限元法或传递矩阵法,借助计算机计算.
通常,主轴组件的固有频率很高,但是,高速主轴,特别是带内装式电动机高速主轴,电动机转子是一个集中质量,将使固有频率下降,有可能发生共振。
改善动态特性,可采取下列措施。
(1)使主轴组件的固有频率避开激振力频率。
通常使固有频率高于激振频率的30%以上。
如果发生共振的那阶模态属于主轴在弹性基础上(轴承)的刚体振动的第一阶(平移)和第二阶(摇摆)模态,则应提高轴承的刚度。
如果属于主轴的弯曲振动,则应提高主轴的刚度,如加粗直径.
(2)增大比尼。
如前所述,降低模态,常是主轴的刚度振动。
这时主轴轴承,特别是前轴承的阻尼对主轴组件的抗震性影响很大。
如果要求得到很大。
如果要求得到很光的加工表面,滚动轴承适当预紧可以增大阻尼,但过大的预紧反而使阻尼减小,故选择预紧时还因考虑阻尼因素.(3)采用消振装置
4主轴轴承
选用角接触球轴承。
这种轴承即可承受径向载荷,又可承受轴向载荷。
这种球轴承为点接触,刚度较低。
为了提高刚度和承载能力,常采用多联组配的办法。
有三种基本组配方式,分别为背对背,面对面和同向组配,背靠背和面对面都能受双向轴向载荷;同向组配只能承受单向轴向载荷。
背对背与面对面相比,支撑点(接触线的交点)间距离前者比后者大,因而能产生一个较大的抗弯力矩,即支撑刚度较大。
运转时,轴承的外圈的散热条件比内圈好,因此,内圈的温度将高于外圈,径向膨胀的结果将使轴承的过盈加大.轴向膨胀对背靠背组配将使过盈减少,于是,可以补偿一部分径向膨胀;而对于面对面组配,将使过盈进一步加大,本车床是微型数控车床载荷不是很大,因此采用一个角接触球轴承即可。
基于上述分析,本车床主轴前端轴颈部轴承选用1个角接触球轴承型号为7009C,后轴颈轴承采用1个角接触球轴承型号为7006C.
5角接触球轴承的间隙调整和预紧
主轴轴承的内部间隙,必须能够调整,多数轴承还应在过盈状态下工作,使滚动体和导轨之间有一定的预变形,这就是轴承的预紧。
轴承预紧后,内部无间隙,滚动体从各个方向支撑主轴,有利于提高运动精度。
滚动体的直径不可能绝对相等,滚道也不可能绝对正圆,因而预紧前只有部分滚导体与滚道接触。
预紧后,滚导体和滚道都有一定的变形,参加工作的滚动体将增多,各滚动体的受力将更加均匀.这些都有利提高轴承的精度、刚度和寿命.如主轴产生振动,则由于各个方面都有滚动体支撑,可以提高抗震性.但是,预紧后发热较多,温升较高;且较大的预紧将使寿命下降,故预紧要适量。
角接触球轴承在轴向力的作用下,使内外圈产生轴向错位实现预紧,衡量预紧力大小的是轴向预紧力,简称预紧力F,单位为N。
多联角接触球轴承是根据预紧力组配的。
轴承厂规定了轻预紧、中预紧和重预紧三级预紧.定货时可指定预紧级别。
轴承厂在内圈(背靠背组配)或外圈(面对面组配)的端面根据预紧力磨取.装配时挤紧,便可得到预定的预紧.
6承载能力和寿命
主轴轴承通常载荷相对较轻。
除了这些特殊重载主轴外轴承的承载能力是没有问题的。
主轴轴承的寿命,主要不是取决于疲劳点蚀,而是由于磨损而降低精度.通常,如轴承精度为P4级,经使用磨损后跳动精度降为P5级,这个轴承就认为应该更换了。
虽然还未达到其疲劳寿命,但这种“精度寿命"目前还难以估计。
7主轴轴承的润滑和密封
滚动轴承在接触区的压强很高,在这么高的压强下,接触区产生变形,是一块小面积的接触而不是一条线或一个点的接触:
润滑剂在高压下被压缩,粘度升高了。
因此,才能在滚动体与滚道的接触区,形成一个厚度的油膜,把两者隔开,滚道体与滚道的接触面积很小,所以,滚动轴承所需的润滑剂很少的。
当然,也可用脂润滑,还有用油气润滑的。
滚动轴承能用脂润滑是它的突出优点之一。
脂润滑不需要供油管路和系统,没有漏油问题。
如果脂的选择合适、清洁、密封良好,不是灰尘、油、切削液等进入,寿命是很长的。
一次冲填可用到大修,不许补充,也不要加脂孔。
脂润滑可选用锂基脂,如SKFLGLT2号(常用于球轴承)。
主轴的密封有接触式和非接触式两种。
图2—10非接触式密封
几种非接触密封的形式如图2-10所示.图2-10a)是利用轴承盖与轴的间隙密封,在轴承盖的孔内开槽是为了提高密封效果;这种密封用于工作环境比较清洁的油脂润滑处.图2-10b)是在螺母的外圆上开锯齿形环槽,当油向外流时,靠主轴转动的离心力把油沿斜面甩到端盖的空腔内,油液再流回箱内.图2-10c)是迷宫式密封的结构,在切屑多、灰尘大的工作环境下可获得可靠的密封效果;这种结构适用于油脂或油液润滑的密封.接触式密封主要有油毡圈和耐油橡胶密封圈密封两种。
2。
6。
4传动轴的设计计算
1初选传动轴直径:
传动轴直径越粗,刚度越高,但同时与之相配的轴承等零件的尺寸也越大.根据齿轮内径及相配合轴承的内径大小,初选传动轴前轴颈=10mm,后轴直径=15mm。
2传动轴悬伸量的确定:
传动轴轴悬伸量是指传动轴前支撑径向支反力的作用点到传动轴前端面之间的距离,它对传动轴组件刚度影响较大,根据分析和试验,缩短悬伸量可以显著提高主轴组件的刚度和抗振性。
因此在满足结构要求的条件下,尽量缩短悬伸量a。
初选传动轴悬伸量a=