钢铁冶金复习题及答案.docx
《钢铁冶金复习题及答案.docx》由会员分享,可在线阅读,更多相关《钢铁冶金复习题及答案.docx(17页珍藏版)》请在冰豆网上搜索。
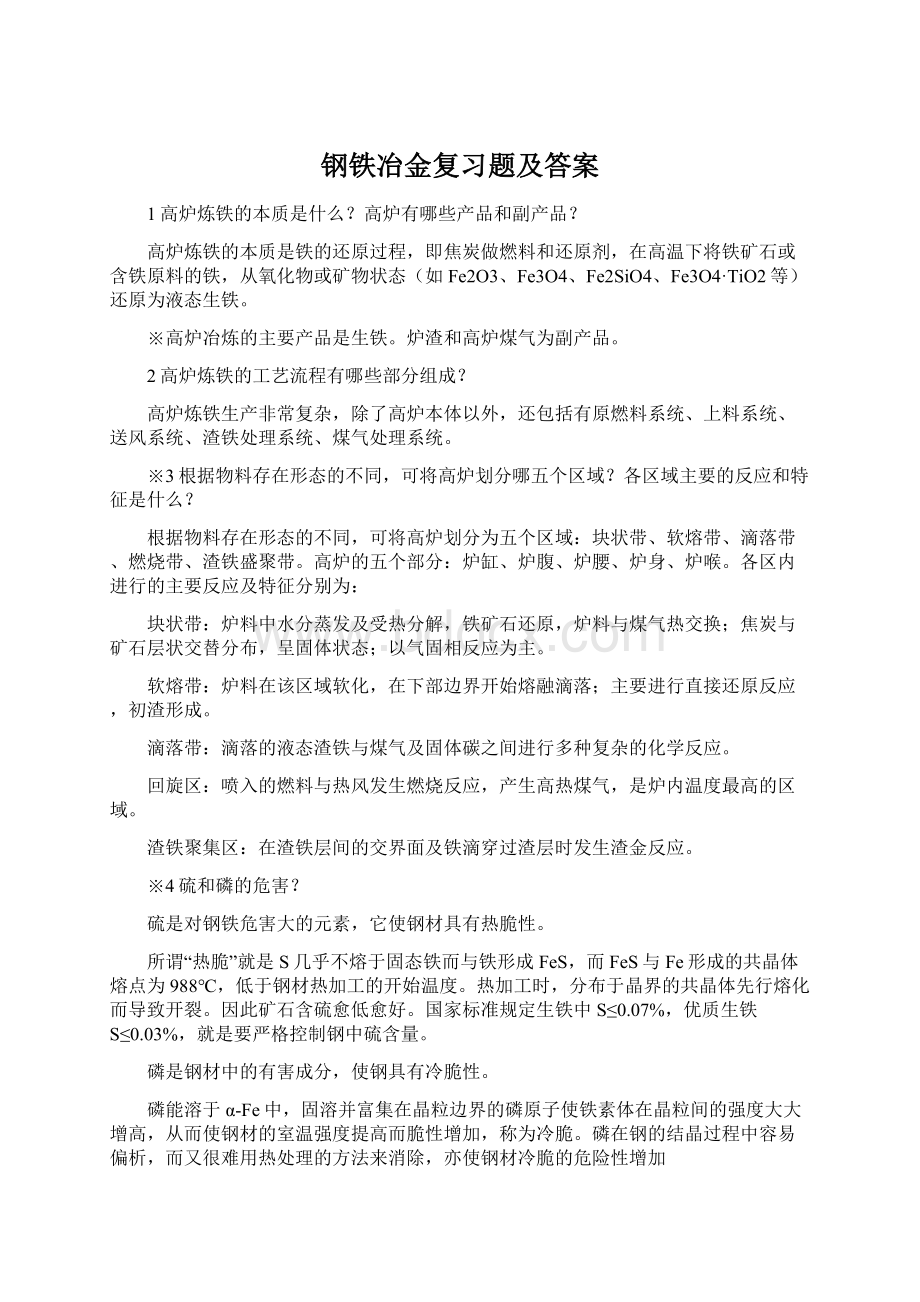
钢铁冶金复习题及答案
1高炉炼铁的本质是什么?
高炉有哪些产品和副产品?
高炉炼铁的本质是铁的还原过程,即焦炭做燃料和还原剂,在高温下将铁矿石或含铁原料的铁,从氧化物或矿物状态(如Fe2O3、Fe3O4、Fe2SiO4、Fe3O4·TiO2等)还原为液态生铁。
※高炉冶炼的主要产品是生铁。
炉渣和高炉煤气为副产品。
2高炉炼铁的工艺流程有哪些部分组成?
高炉炼铁生产非常复杂,除了高炉本体以外,还包括有原燃料系统、上料系统、送风系统、渣铁处理系统、煤气处理系统。
※3根据物料存在形态的不同,可将高炉划分哪五个区域?
各区域主要的反应和特征是什么?
根据物料存在形态的不同,可将高炉划分为五个区域:
块状带、软熔带、滴落带、燃烧带、渣铁盛聚带。
高炉的五个部分:
炉缸、炉腹、炉腰、炉身、炉喉。
各区内进行的主要反应及特征分别为:
块状带:
炉料中水分蒸发及受热分解,铁矿石还原,炉料与煤气热交换;焦炭与矿石层状交替分布,呈固体状态;以气固相反应为主。
软熔带:
炉料在该区域软化,在下部边界开始熔融滴落;主要进行直接还原反应,初渣形成。
滴落带:
滴落的液态渣铁与煤气及固体碳之间进行多种复杂的化学反应。
回旋区:
喷入的燃料与热风发生燃烧反应,产生高热煤气,是炉内温度最高的区域。
渣铁聚集区:
在渣铁层间的交界面及铁滴穿过渣层时发生渣金反应。
※4硫和磷的危害?
硫是对钢铁危害大的元素,它使钢材具有热脆性。
所谓“热脆”就是S几乎不熔于固态铁而与铁形成FeS,而FeS与Fe形成的共晶体熔点为988℃,低于钢材热加工的开始温度。
热加工时,分布于晶界的共晶体先行熔化而导致开裂。
因此矿石含硫愈低愈好。
国家标准规定生铁中S≤0.07%,优质生铁S≤0.03%,就是要严格控制钢中硫含量。
磷是钢材中的有害成分,使钢具有冷脆性。
磷能溶于α-Fe中,固溶并富集在晶粒边界的磷原子使铁素体在晶粒间的强度大大增高,从而使钢材的室温强度提高而脆性增加,称为冷脆。
磷在钢的结晶过程中容易偏析,而又很难用热处理的方法来消除,亦使钢材冷脆的危险性增加
※5评价铁矿石的标准有哪些?
铁矿石质量直接影响高炉冶炼效果,必须严格要求。
通常从以下几方面评价:
1.矿石品位2.脉石成分3.有害杂质和有益元素的含量4.矿石的粒度和强度5.铁矿石的还原性6.矿石化学成分的稳定性。
品味提高1%,焦比下降2%,产量增加3%。
※6焦炭在高炉生产中起什么作用,高炉冶炼过程对焦炭质量提出哪些要求?
焦炭是现代高炉冶炼的主要燃料和能源基础,在高炉冶炼过程中具有如下作用:
(1)燃料。
(2)还原剂。
(3)料柱骨架。
(4)生铁渗碳的碳源
高炉对焦炭质量的要求
(1)含碳量高,灰分低。
2)含硫等有害杂质要少。
我国焦炭含硫一般为0.5~1.0%(3)成分稳定。
即要求化学灰分、C、S、H2O等稳定。
(4)挥发分含量适合。
(5)强度高,块度均匀。
7对高炉内衬的基本要求?
对高炉内衬的基本要求如下:
1)各部位内衬与热流强度相适应,以保持在强热流冲击下内衬的稳定性。
2)炉衬的侵蚀和破坏与冶炼条件密切相关,不同位置的耐火材料受侵蚀破坏机理不同,因此要求各部位内衬与侵蚀破损机理相适应,以延缓内衬破损速度。
高炉生产的特点:
高温高压、连续不间断、大规模。
高炉炉衬以陶瓷质材料和炭质材料砌成。
※8生铁和钢的化学成分主要差别在于是什么?
一般来说,生铁和钢的化学成分主要差别是含碳量。
钢中含碳量最高不超过2.11%。
高炉生铁含碳量在2.5~4.5%范围,铸铁中不超过5.0%。
当铸铁中C>5.0%时,铸铁甚脆,没有实用价值。
9简述现代常用于精选铁矿石的三种方法:
(1)重选
(2)磁选。
(3)浮选
10对烧结矿质量的要求?
对烧结矿质量的要求是:
品位高,强度好,成分稳定,还原性好,粒度均匀,粉末少,碱度适宜,有害杂质少。
11抽风烧结过程大致可分为哪五层?
简述其特点?
抽风烧结过程是将铁矿粉、熔剂和燃料经适当处理,按一定比例加水混合,铺在烧结机上,然后从上部点火,下部抽风,自上而下进行烧结,得到烧结矿。
取一台车剖面分析,抽风烧结过程大致可分为五层(图3-2),即烧结矿层、燃烧层、预热层、干燥层和过湿层。
※12固相反应得机理?
烧结矿的固结主要依靠发展液相来完成。
一方面是上述固相反应形成的低熔点化合物足以在烧结温度下生成液相;同时随着燃料层的移动,温度升高,各种互相接触的矿物又形成一系列的易熔化合物,在燃烧温度下形成新的液相。
机理:
在未生成液相的低温条件下,烧结料中的一些组分就可能在固态下进行反应,生成新的化合物。
固态反应的机理是离子扩散。
相邻颗粒表面电荷相反的离子互相吸引,进行扩散,遂形成新的化合物,使之连接成一整体。
※13烧结与球团的区别?
烧结与球团的区别主要表现在以下几方面:
1).富矿短缺,必须不断扩大贫矿资源的利用,而选矿技术的进步可经济地选出高品位细磨铁精矿,其粒度从-200网目进一步减少到-325网目。
这种过细精矿不益于烧结,透气性不好,影响烧结矿产量和质量的提高,而用球团方法处理却很适宜,因为过细精矿易于成球,粒度愈细,成球性愈好,球团强度愈高。
2.)成品矿的形状不同:
烧结矿是形状不规则的多孔质块矿,而球团矿是形状规则的10~25mm的球球团矿较烧结矿粒度均匀,微气孔多,还原性好,强度高,且易于贮存,有利于强化高炉生产。
3.)适于球团法处理的原料已从磁铁矿扩展到赤铁矿、褐铁矿以及各种含铁粉尘,化工硫酸渣等;从产品来看,不仅能制造常规氧化球团,还可以生产还原球团、金属化球团等;同时球团方法适用于有色金属的回收,有利于开展综合利用。
4)固结成块的机理不同:
烧结矿是靠液相固结的,为了保证烧结矿的强度,要求产生一定数量的液相,因此混合料中必须有燃料,为烧结过程提供热源。
而球团矿主要是依靠矿粉颗粒的高温再结晶固结的,不需要产生液相,热量由焙烧炉内的燃料燃烧提供,混合料中不加燃料
5)生产工艺不同:
烧结料的混合与造球是在混合机内同时进行的,成球不完全,混合料中仍然含有相当数量未成球的小颗粒。
而球团矿生产工艺中必须有专门的造球工序和设备,将全部混合料造成10~25mm的球,小于10mm的小球要筛出重新造球。
※14氧化物还原的一般原理?
哪些物质可以充当还原剂夺取金属氧化物中的氧,决定于它们与氧的化学亲和力。
还原剂与氧的亲和力越大,夺取氧的能力越强,还原能力越强。
C、CO和H2是高炉炼铁适宜的还原剂。
它们由原料带来,兼有热能和化学能的双重职能,焦炭还作为料柱骨架,满足高炉冶炼过程的需要。
15高炉锰还原或冶炼锰铁的基本条件
高炉锰还原或冶炼锰铁的基本条件
(1)足够高的炉缸温度。
(2)提高炉渣碱度Mn回收率增加
(3)正确选择原料。
锰矿石的含Mn量要高,含Fe量和SiO2要低,P、S要特少。
15-1、强化烧结的措施:
混合料预热、加生石灰和消石灰、热风烧结、分层布料和双层烧结。
※16降低生铁含硫量的途径
1.)降低炉料带入的总硫量:
减少入炉原、燃料含硫量,是降低生铁含硫量,获得优质生铁的根本途径和有效措施。
2.)提高煤气带走的硫量3).改善炉渣脱硫性能
※17直接还原和间接还原在高炉冶炼过程中有什么不同作用?
中温区所进行的还原反应称为间接还原反应,而把高温区所进行的还原反应称为直接还原反应。
间接还原反应除Fe2O3→Fe3O4不可逆外,其它均属可逆反应。
反应进行的方向取决于平衡气相组成,即CO/CO2和H2/H2O的比值。
在高温区的直接还原反应中,H2与CO类似,它的还原产物H2O(气)与CO还原FeO的产物CO2一样,立即与焦炭中的碳素作用,又生成H2和CO去参与还原。
但无论H2还是CO的还原,最终都归结为消耗碳素的直接还原反应。
可见H2和CO在高温直接还原反应的条件下,起着中间媒介的作用,这种作用大大推动了碳素直接还原反应地进行。
因为固态的铁氧化物与焦炭之间的直接反应是很困难的,浸在渣中的焦炭与FeO的直接还原也是有限的,所以消耗碳素的直接还原反应实际上是通过气相的CO和H2来进行的。
高炉下部铁氧化物的直接还原反应的进行取决于碳的气化反应的发展(即气化反应的迟早和速率)。
而碳的气化反应的发展则决定于温度和焦炭本身的反应性。
焦炭反应性愈好,碳的气化反应可提前在较低的温度下进行,则直接还原反应发展的早,进行的快,高炉内直接还原区扩大。
相反,焦炭反应性较差时,碳的气化反应需要在更高的温度下进行,则直接还原反应发展的晚,进行得慢,即直接还原区向高温区收缩。
一般希望适当扩大间接还原区,缩小直接还原区。
因此,使用反应性较差的焦炭反而有利。
18高炉渣按照形成过程分为?
含义是什么?
高炉渣按其形成过程有初渣、中间渣和终渣之分。
初渣是指在高炉的适当温度区域刚开始出现的液相炉渣;中间渣是指在处于滴落过程中成分、温度在不断变化的炉渣终渣是指已经下达炉缸,并周期的从炉内排出的炉渣。
19改善煤气化学能利用的关键是
改善煤气化学能利用的关键是提高CO利用率(ηCO)和H2利用率(ηH2)。
炉顶煤气中CO2愈高,CO愈低,则煤气化学能利用愈好。
反之,CO2愈低,CO愈高,则化学能利用愈差(传质不良)。
20论述高炉节能的主要方向?
高炉节能的主要方向:
1.)降低焦比和燃料比为此,必须用精料,改善高炉操作,提高煤气利用率和采用高压、高风温、富氧、综合喷吹等新技术。
2.)节约高炉煤气,提高鼓风有效利用率改进燃烧器结构,采用合理的燃烧制度,降低高炉煤气含水量和含灰量,提高或保持煤气的温度,均可改善燃烧,提高理论燃烧温度,从而节约煤气用量和节省煤气热值。
3.)加强能源回收,充分利用二次能源序能耗和钢铁生产过程总能耗的一个重要方向。
高炉煤气必须予以充分回收,降低放散率。
热风炉废气余热回收,用来预热助燃风和热炉煤气,或供余热锅炉生产蒸汽。
利用高炉冲渣水采暖。
此外,还可利用高炉冷却水落差发电
21、风口前燃料的燃烧和炉缸工作状态对高炉冶炼过程的重要意义
首先,燃料燃烧是高炉冶炼所需热能和化学能的源泉。
燃料在风口前燃烧,放出大量的热,并产生高温还原性气体(CO、H2),保证了炉料的加热、分解、还原、熔化、造渣等等过程的进行。
其次,燃料燃烧是高炉炉料下降的前导。
风口前焦炭及其他燃料的燃烧和炉料的熔化,产生了空间,为炉料的不断下降创造了基本条件。
第三,炉缸反应除燃料燃烧外,还包括直接还原、渗碳、渣、铁间脱硫等尚未完成的反应,都集中在炉缸内来最后完成,最终形成生铁和炉渣,自炉缸内排出。
22、软熔带的位置和结构形状如何影响煤气流运动的阻力与煤气流分布
软熔带位置的高低对高炉冶炼的影响是:
顶点位置较高的“∧”形软熔带,由于增加了软熔带中的焦窗数目,减小煤气阻力,有利于强化冶炼,软熔带位置较低,则由于焦窗数目减少,煤气阻力增加,不利于强化,但却扩大了块状带间接还原区,有利于提高煤气利用率。
软熔带宽度和软熔层厚度对煤气阻力的影响是:
当软熔带宽度增加时,由于煤气通过软熔带的横向通道加长,煤气阻力增加;而软熔带厚度增加意味着矿石批重加大,虽因焦窗厚度相应增加使煤气通道的阻力减小,但焦窗数目减少,而且由于扩大矿批后块状带中分布到中心部分的矿石增加,煤气阻力呈增加趋势,从而使总的煤气阻力和总压差可能升高,不利于强化和高炉顶行。
只有适当的焦、矿层厚度才能达到总阻力最小。
这个适宜的厚度是因冶炼条件不同而异的,需通过实践摸索。
※23、炼钢的基本任务是什么?
采用的主要技术手段有哪些?
炼钢的基本任务是脱碳、脱磷、脱硫、脱氧,去除有害气体和非金属夹杂物,提高温度和调整成分。
归纳为:
“四脱”(碳、氧、磷和硫),“二去”(去气和去夹杂),“二调整”(成分和温度)。
采用的主要技术手段为:
供氧,造渣,升温,加脱氧剂和合金化操作。
※24、简述磷和硫对钢产生哪些危害
钢中磷的含量高会引起钢的“冷脆”,即从高温降到0℃以下,钢的塑性和冲击韧性降低,并使钢的焊接性能与冷弯性能变差。
磷是降低钢的表面张力的元素,随着磷含量的增加,钢液的表面张力降低显著,从而降低了钢的抗裂性能。
磷是仅次于硫在钢的连铸坯中偏析度高的元素,而且在铁固熔体中扩散速率很小,因而磷的偏析很难消除,从而严重影响钢的性能,所以脱磷是炼钢过程的重要任务之一。
硫对钢的性能会造成不良影响,钢中硫含量高,会使钢的热加工性能变坏,即造成钢的“热脆”性。
硫还会明显降低钢的焊接性能,引起高温龟裂,并在焊缝中产生气孔和疏松,从而降低焊缝的强度。
硫含量超过0.06%时,会显著恶化钢的耐蚀性。
硫还是连铸坯中偏析最为严重的元素。
25、钢中脱氧的任务包括哪些?
常用的脱氧剂?
根据具体的钢种,将钢中的氧含量降低到所需的水平,以保证钢水在凝固时得到合理的凝固组织结构;
使成品钢中非金属夹杂物含量最少,分布合适,形态适宜,以保证钢的各项性能指标;
得到细晶结构组织。
常用的脱氧剂有Fe-Mn,Fe-Si,Mn-Si,Ca-Si等合金。
26、外来夹杂和内生夹杂指什么?
外来夹杂是指冶炼和浇铸过程中,带入钢液中的炉渣和耐火材料以及钢液被大气氧化所形成的氧化物。
内生夹杂包括
(1)脱氧时的脱氧产物;
(2)钢液温度下降时,硫、氧、氮等杂质元素溶解度下降而以非金属夹杂形式出现的生成物;
(3)凝固过程中因溶解度降低、偏析而发生反应的产物;
(4)固态钢相变溶解度变化生成的产物。
(5)钢中大部分内生夹杂是在脱氧和凝固过程中产生的。
※27、氢和氮对钢产生哪些危害?
氢在固态钢中溶解度很小,在钢水凝固和冷却过程中,氢会和CO、N2等气体一起析出,形成皮下气泡中心缩孔、疏松、造成白点和发纹。
钢热加工过程中,钢中含有氢气的气孔会沿加工方向被拉长形成发裂,进而引起钢材的强度、塑性、冲击韧性的降低,即发生“氢脆”现象。
钢中的氮是以氮化物的形式存在,它对钢质量的影响体现出双重性。
氮含量高的钢种长时间放置,将会变脆,这一现象称为“老化”或“时效”。
原因是钢中氮化物的析出速度很慢,逐渐改变着钢的性能。
低碳钢产生的脆性比磷还严重。
钢中氮含量高时,在250-4500C温度范围,其表面发蓝,钢的强度升高,冲击韧性降低,称之为“蓝脆”。
氮含量增加,钢的焊接性能变坏。
※28、钢的分类?
(1)按化学成分分类
按是否加入合金元素可钢分为把碳素钢和合金钢两大类。
按炼钢炉设备不同可分为转炉钢、电炉钢、平炉钢。
其中电炉钢包括电弧炉钢、感应炉钢、电渣钢、电子束熔炼及有关的真空熔炼钢等。
按脱氧程度不同可分为沸腾钢(不经脱氧或微弱脱氧)、镇静钢(脱氧充分)和半镇静钢(脱氧不完全,介于镇静钢和沸腾钢之间)。
按质量水平不同可分为普通钢、优质钢和高级优质钢。
(2)按用途分类分为三大类:
结构钢,工具钢,特殊性能钢
29、实际生产中为什么要将[Mn]/[S]比作为一个指标进行控制?
冶炼一般钢种时要求将[Mn]控制在0.4%-0.8%。
在实际生产中还将[Mn]/[S]比作为一个指标进行控制,[Mn]/[S]对钢的热塑性影响很大。
从低碳钢高温下的拉伸实验发现提高[Mn]/[S]比可以提高钢的热延展性。
一般[Mn]/[S]≥7时不产生热脆。
30、影响钢液物理性质的因素
(1)钢的密度温度升高,钢液密度降低,原因在于原子间距增大。
(2)钢的熔点(3)钢液的黏度(4)液的表面张力钢液的表面张力是随着温度的升高而增大(5)钢钢的导热能力
影响钢导热系数的因素主要有钢液的成分、组织、温度、非金属夹杂物含量以及钢中晶粒的细化程度等。
31、熔渣在炼钢中的作用体现在哪些方面?
熔渣在炼钢过程不利作用表现在哪些方面?
去除铁水和钢水中的磷、硫等有害元素,同时能将铁和其他有用元素的损失控制最低;
保护钢液不过度氧化、不吸收有害气体、保温、减少有益元素烧损;
防止热量散失,以保证钢的冶炼温度;
吸收钢液中上浮的夹杂物及反应产物
侵蚀耐火材料,降低炉衬寿命,特别是低碱度熔渣对炉衬的侵蚀更为严重;
熔渣中夹带小颗粒金属及未被还原的金属氧化物,降低了金属的回收率。
32、炼钢熔渣的来源?
炼钢过程有目的加入的造渣材料,如石灰、石灰石、萤石、硅石、铁矾土及火砖块。
钢铁材料中Si、Mn、P、Fe等元素的氧化产物。
冶炼过程被侵蚀的炉衬耐火材料。
※※33、熔渣的碱度的定义?
熔渣中碱性氧化物浓度总和与酸性氧化物浓度总和之比称之为熔渣碱度,常用符号R表示。
34、什么是熔渣的氧化性,在炼钢过程中熔渣的氧化性是如何体现的?
熔渣的氧化性也称熔渣的氧化能力,熔渣的氧化性决定了脱磷、脱碳以及夹杂物的去除等
熔渣氧化性在炼钢过程中的作用体现在对熔渣自身、对钢水和对炼钢操作工艺影响三个方面。
影响化渣速度,渣中FeO能促进石灰溶解,加速化渣,改善炼钢反应动力学条件,加速传质过程;影响熔渣粘度,渣中Fe2O3和碱性氧化物反应生成铁酸盐,降低熔渣熔点和粘度,避免炼钢渣“返干”;影响熔渣向熔池传氧。
影响钢水含氧量[O],低碳钢水含氧量明显受熔渣氧化性的影响,当钢水含碳量相同时,熔渣氧化性强,则钢水含氧量高;影响钢水脱磷,熔渣氧化性强,有利于脱磷。
影响铁合金收得率,氧化性强,降低铁合金收得率;影响炉衬寿命,熔渣氧化性强,炉衬寿命降低;影响金属收得率,熔渣氧化性越强,金属收得率越低。
35、硅和锰的氧化和还原反应的影响因素有哪些?
硅的氧化和还原反应的影响因素有温度、炉渣成分、金属液成分和炉气氧分压。
温度低有利于硅的氧化;
炉渣中降低SiO2的成分含量如增加CaO、FeO含量,有利于硅的氧化,炉渣氧化能力越强,越有利硅的氧化;
金属液中增加硅元素含量,有利于硅的氧化;
炉气氧分压越高,越有利于硅的氧化。
与硅的氧化和还原一样,影响锰的氧化和还原反应的因素有
温度炉渣成分金属液成分炉气氧分压。
温度低有利于锰的氧化;
炉渣碱度高,使(MnO)的活度提高炉渣氧化性强,则有利于锰的氧化;
能增加Mn元素活度的元素,其含量增加,有利于锰的氧化;
炉气氧分压越高,越有利于锰的氧化。
36、钢液中残锰有何作用?
防止钢水的过氧化,或避免钢水中含过多的过剩氧,以提高脱氧合金的收得率,降低钢中氧化物夹杂;
◆可作为钢液温度高低的标态,炉温高有利于(MnO)的还原,残锰含量高;
◆能确定脱氧后钢水的含锰量达到所炼钢种的规格,并节约Fe-Mn用量。
*※37、炼钢过程的碳氧反应的作用是什么?
加大钢—渣界面,加速反应的进行;均匀熔池中成分和温度;有利于熔渣的形成;有利于非金属夹杂的上浮和有害气体的排出;放热升温。
※38、脱磷的条件?
脱磷的条件:
高碱度、高氧化铁含量(氧化性)、良好流动性熔渣、充分的熔池搅动、适当的温度和大渣量。
脱硫的条件:
高温、高碱度、低(FeO)、好流动性。
39、脱氧的方式?
按脱氧原理分:
脱氧方法有三种,即沉淀脱氧法,扩散脱氧法和真空脱氧法。
※39-1、炼钢常用脱氧剂:
铝、硅、锰。
先加锰再加硅后加铝
※40、炼钢用原材料有哪些?
炼钢原料分为金属料,非金属料和气体。
金属料:
铁水、废钢、合金钢
非金属料:
造渣剂(石灰、萤石、铁矿石)、冷却剂(废钢、铁矿石、氧化铁、烧结矿、球团矿)、增碳剂和燃料(焦炭、石墨籽、煤块、重油)
氧化剂:
氧气、铁矿石、氧化铁皮
41、转炉炼钢对铁水成分和温度有何要求?
对铁水要求有:
(1)成分;铁水中的硅含量为0.30%-0.60%为宜锰的含量为0.20%-0.80%。
磷(P)。
磷对一般钢种来说是有害元素,因此要求铁水磷含量越低越好,一般要求铁水[P]≤0.20%。
硫(S)。
除了含硫易切削以外,绝大多数钢种要求去除硫这一有害元素。
我国炼钢技术规程要求入炉铁水的硫含量不超过0.05%。
(2)带渣量;进入转炉的铁水要求带渣量不得超过0.5%。
(3)温度铁水温度是铁水含物理量多少的标志,铁水物理热得占转炉热收入的50%。
应努力保证入炉铁水的温度,保证炉内热源充足和成渣迅速。
我国炼钢规定入炉铁水温度应大于1250℃,并且要相对稳定。
42、什么是合成造渣剂?
它有何作用?
合成造渣剂是用石灰加入适量的氧化铁皮、萤石、氧化锰或其他氧化物等熔剂,在低温下预制成型。
合成渣剂熔点低、碱度高、成分均匀、粒度小,且在高温下易碎裂,成渣速度快,因而改善了冶金效果,减轻了转炉造渣负荷
43、顶吹氧气转炉炼钢工艺主要包含:
?
顶吹氧气转炉炼钢工艺主要包含:
(1)装料
(2)供氧(3)造渣(4)温度及终点控制(5)脱氧及合金化
44、装料次序?
(1)对使用废钢的转炉,一般先装废钢后装铁水。
先加洁净的轻废钢,再加入中型和重型废钢,以保护炉衬不被大块废钢撞伤,而且过重的废钢最好在兑铁水后装入。
(2)为了防止炉衬过分急冷,装完废钢后,应立即兑入铁水。
炉役末期,以及废钢装入量比较多的转炉也可以先兑铁水,后加废钢。
45、什么是转炉的炉容比?
确定装入量应考虑哪些因素?
装入量指炼一炉钢时铁水和废钢的装入数量,
炉容比:
它是指转炉内自由空间的容积与金属装入量之比(m3/t),通常在0.7-1.0波动,我国转炉炉容比一般0.75。
熔池深度:
合适的熔池深度应大于顶枪氧气射流对熔池的最大穿透深度,以保证生产安全,炉底寿命和冶炼效果。
炉子附属设备:
应与钢包容量、浇注吊车起重能力、转炉倾动力矩大小、连铸机的操作等相适应。
46、供氧制度的含义是什么?
供氧制度的主要内容包括确定合理的喷头结构、供氧强度、氧压和枪位控制。
47、炉料熔化过程基本可分为四个阶段
炉料熔化过程见下图,基本可分为四个阶段(期),即点弧、穿井、主熔化及熔末升温。
48、电炉炼钢氧化期、熔化期和还原期的主要任务
氧化期的主要任务
继续脱磷到要求——脱磷;
脱碳至规格下限——脱碳;
去除气、去夹杂——二去;
提高钢液温度——升温
熔化期的主要任务
将块状的固体炉料快速熔化,并加热到氧化温度;提前造渣,早期去磷;减小钢液吸气及挥发。
还原期的主要任务
脱氧至要求——脱氧;
脱硫至一定值——脱硫;
调整成分——合金化;
调整温度——调温。
其中:
脱氧是核心,温度是条件,造渣是保证
49、合金化操作的总的原则和具体的原则?
合金加入时间总的原则是:
熔点高,不易氧化的元素可早加;熔点低,易氧化的元素晚加。
A)易氧化的元素后加原则
B)比重大的加强搅拌原则:
熔点高的、比重大的铁合金,加入后应加强搅拌。
如钨铁的密度大、熔点高,沉于炉底,其块度应小些。
C)便宜的先加原则:
在许可的条件下,优先使用便宜的高碳铁合金,然后再考虑使用中碳铁合金或低碳铁合金。
D)贵重的控制下限原则:
50、UHP电炉主要优点:
缩短熔化时间,提高生产率;提高电、热效率,降低电耗;易于与炉外精炼,连铸相配合,实现高产、优质、低耗。
51、衡量一座电炉是不是UHP电炉的标准
衡量一座电炉是不是UHP电炉,不仅要看功率的高低,还要看变压器利用率,工艺流程优化否,公害抑制的如何,以及是否高效节能。
52、电炉的热点与冷点的含义
在电炉炉衬的渣线水平面上,距电极最近点叫热点(区),而距电极最远点叫冷点(区)。
53、直流电弧炉的优越性?
石墨电极消耗大幅度降低,可降低50%左右。
原因一是炉顶电极由三根变成一根;二是阳极效应。
降低电能消耗,可节约电能约5%~10%。
原因一是单相,电阻损失少;二是直流损耗低。
对电网的干扰和冲击小,电压闪烁降低了50%左右,这样根据电网条件可省去SVC装置或减小补偿的容量。
炉衬寿命提高,耐材消耗降低,喷补材料可节约30%。
噪音降低10~15dB。
电磁搅拌力强,钢液成分及温度均匀。
54、EBT(偏心底出钢法)电炉的优点?
具体优点如下:
出钢倾动