锅炉原理及设备复习题.docx
《锅炉原理及设备复习题.docx》由会员分享,可在线阅读,更多相关《锅炉原理及设备复习题.docx(34页珍藏版)》请在冰豆网上搜索。
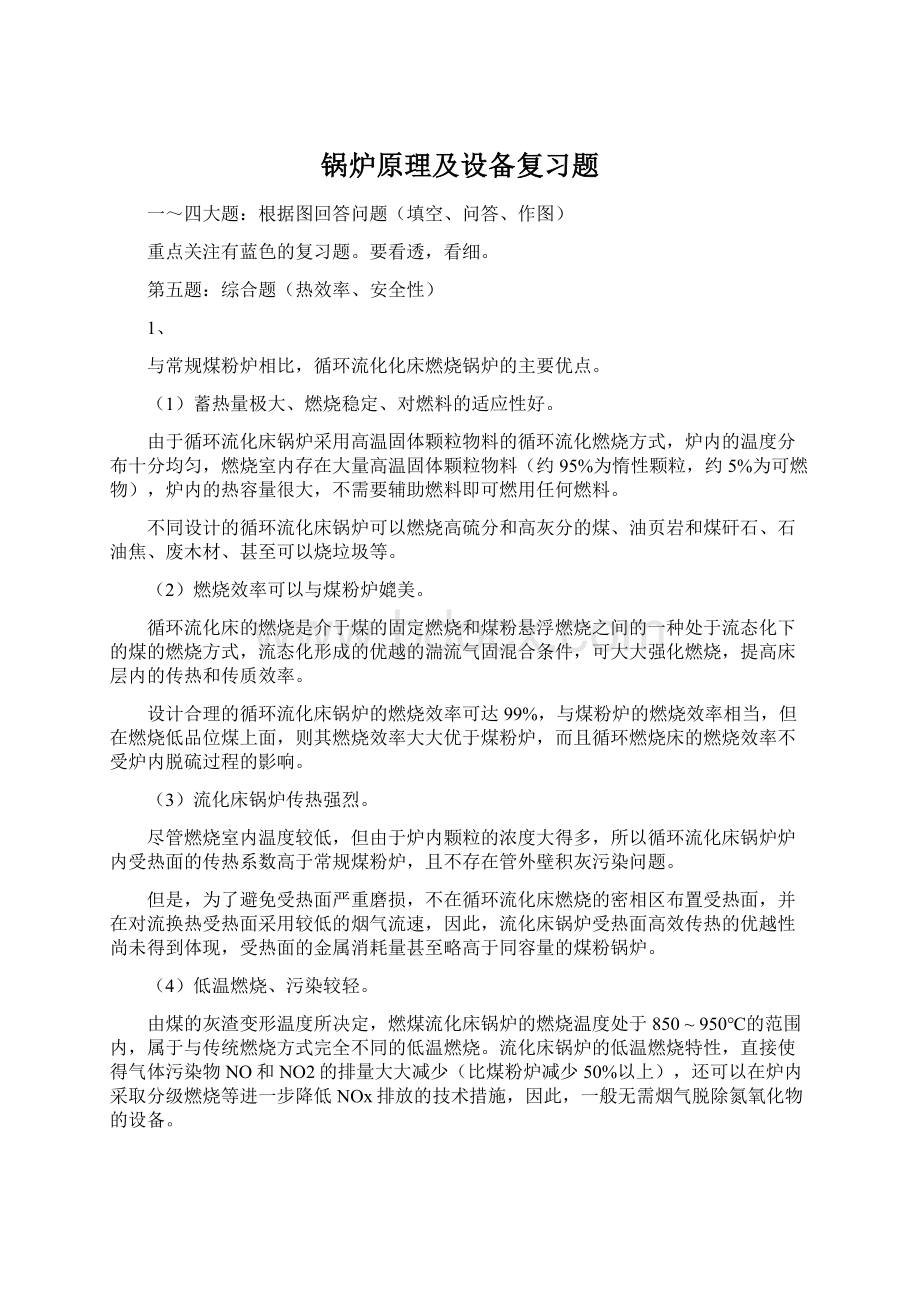
锅炉原理及设备复习题
一~四大题:
根据图回答问题(填空、问答、作图)
重点关注有蓝色的复习题。
要看透,看细。
第五题:
综合题(热效率、安全性)
1、
与常规煤粉炉相比,循环流化化床燃烧锅炉的主要优点。
(1)蓄热量极大、燃烧稳定、对燃料的适应性好。
由于循环流化床锅炉采用高温固体颗粒物料的循环流化燃烧方式,炉内的温度分布十分均匀,燃烧室内存在大量高温固体颗粒物料(约95%为惰性颗粒,约5%为可燃物),炉内的热容量很大,不需要辅助燃料即可燃用任何燃料。
不同设计的循环流化床锅炉可以燃烧高硫分和高灰分的煤、油页岩和煤矸石、石油焦、废木材、甚至可以烧垃圾等。
(2)燃烧效率可以与煤粉炉媲美。
循环流化床的燃烧是介于煤的固定燃烧和煤粉悬浮燃烧之间的一种处于流态化下的煤的燃烧方式,流态化形成的优越的湍流气固混合条件,可大大强化燃烧,提高床层内的传热和传质效率。
设计合理的循环流化床锅炉的燃烧效率可达99%,与煤粉炉的燃烧效率相当,但在燃烧低品位煤上面,则其燃烧效率大大优于煤粉炉,而且循环燃烧床的燃烧效率不受炉内脱硫过程的影响。
(3)流化床锅炉传热强烈。
尽管燃烧室内温度较低,但由于炉内颗粒的浓度大得多,所以循环流化床锅炉炉内受热面的传热系数高于常规煤粉炉,且不存在管外壁积灰污染问题。
但是,为了避免受热面严重磨损,不在循环流化床燃烧的密相区布置受热面,并在对流换热受热面采用较低的烟气流速,因此,流化床锅炉受热面高效传热的优越性尚未得到体现,受热面的金属消耗量甚至略高于同容量的煤粉锅炉。
(4)低温燃烧、污染较轻。
由煤的灰渣变形温度所决定,燃煤流化床锅炉的燃烧温度处于850~950℃的范围内,属于与传统燃烧方式完全不同的低温燃烧。
流化床锅炉的低温燃烧特性,直接使得气体污染物NO和NO2的排量大大减少(比煤粉炉减少50%以上),还可以在炉内采取分级燃烧等进一步降低NOx排放的技术措施,因此,一般无需烟气脱除氮氧化物的设备。
由于流化床内的燃烧温度较低,所以,可以在流化床床层内直接添加石灰石脱硫剂,在燃烧过程中完成有效的脱硫。
与煤粉炉的炉内脱硫过程相比较,流化床内的脱硫剂与烟气中SO2之间的反应环境(反应温度、停留时间和传质等)十分有利于脱硫反应的进行,因此,可以在相对较低的钙硫摩尔比下,得到较高的脱硫效率。
如果与煤粉炉的烟气脱硫方式相比,其设备投资和运行费用远低的多。
此外,脱硫灰渣可以综合利用,不会产生二次污染。
(5)锅炉设备占地面积少。
循环流化床锅炉不需要单独的脱硫脱氮装置,也不需要像煤粉炉的庞大复杂的煤粉制备系统,只需燃煤的简单破碎和筛分,一般不需干燥,因此热风温度仅在200℃左右。
另一方面,由于循环流化床锅炉没有像煤粉炉那样的精心设计和布置数十台煤粉燃烧器,而是采用简单的机械(或气力)输送方式将煤直接送入流化床的密相区内,还因为密相区内固体颗粒混合十分强烈和均匀,通常只需很少量的给煤口即可。
因此,给煤管道较煤粉炉的煤粉管道数量少且布置简单,从而能节约电厂布置场地,为循环流化床锅炉大型化创造了有利条件。
(6)负荷变化范围大,调节性能好。
循环流化床锅炉具有较大的负荷变化范围,一般为100%~25%,而且具有较大的负荷升降速度,变化速率约为每分钟5%。
1)循环流化床锅炉水循环的安全性
对煤粉炉来说,炉内存在明显的火焰中心,热负荷分布不均匀,炉内热负荷最高处与容易产生传热恶化的受热管段相吻合。
另外,根据在锅炉较高负荷下的沿炉膛高度的热负荷分布设计的水循环系统,在锅炉低负荷时,由于火焰中心变化,热负荷中心也发生较大的变化,因此,易引起水循环故障。
譬如,工质发生停滞或倒流,甚至出现爆管等事故。
循环流化床锅炉炉内不存在火焰中心,温度和热负荷分布较煤粉炉分布均匀的多,无论锅炉负荷如何变化,炉内温度始终保持均匀且变化不大,因此,炉膛壁面的热负荷分布均匀,这种热负荷分布不随锅炉负荷而明显变化的特点使得循环流化床锅炉具有可靠的水循环性能,这对锅炉水循环及金属的安全性十分有利,可适应较煤粉炉大得多的负荷调节范围。
2)循环流化床锅炉的汽温特性。
由于对流受热面的出口汽温随热负荷变化的特点,煤粉炉在低负荷运行时,过热汽温和再热汽温常难以达到满负荷时的额定汽温。
但是,对循环流化床锅炉来说,由于燃烧温度较低,炉膛出口的烟气焓不足以使过热汽温和再热汽温达到额定温度值,因此,在设计时考虑了炉膛尾部受热面的合理布置和吸热量的分配,部分过热器和再热器受热面必须布置在固体颗粒循环回路中。
这部分受热面不仅具有较好的换热特性,而且,可以在负荷变化时通过改变循环物料的浓度来控制蒸发、过热和再热吸热量,因此,循环流化床锅炉具有优于煤粉炉的汽温控制手段,保证了在很大的负荷变化范围内维持额定的蒸汽温度。
3)循环流化床锅炉的燃烧特性。
循环流化床锅炉燃烧系统中的燃料存有量很少,其优越的燃烧稳定性是不言而喻的,所以可以适应很低负荷下的稳定燃烧。
而且,由于床温在很大负荷范围内总保持一定,基本不存在负荷变化时加热或冷却炉内物料的过程,因此,当要求负荷变化时,在维持床温不变的条件下,采用改变燃煤量、送风量、飞灰循环量和床层厚度等手段,来实现负荷调节。
(7)流化床燃烧的灰渣可以综合利用。
低温燃烧和添加脱硫剂使炉渣和飞灰具有与煤粉炉不同的物理和化学特性,流化床锅炉灰渣未经高温熔融过程,灰渣活性好,可燃物含量低,且含有无水石膏,有利于做水泥掺合料或其他建筑材料。
2、
循环流化床燃烧锅炉的构成。
(1)燃烧室
•燃烧室下部区域为循环流化床的密相区,颗粒浓度较大,是燃料发生着火和燃烧的主要区域,此区域的壁面上敷设耐磨耐热材料,底部为布风板,并设置循环飞灰返料口、给煤口、排渣口等
•燃烧室上部为稀相区,颗粒浓度较小,壁面上主要布置水冷壁受热面,也可布置过热蒸汽受热面,通常炉膛上部空间布置悬挂式的屏式受热面
(2)布风板
•布风板位于炉膛燃烧室的底部,实际上是一个其上布置有一定数量和型式的布风风帽的燃烧室底板,它将其下部的风室和炉膛分开。
•一方面起到将固体颗粒限制在炉膛布风板上,并对固体颗粒(床料)起支撑作用;另一方面,保证一次风穿过布风板进入炉膛达到对颗粒均匀流化。
•为了满足均匀、良好流化,布风板必须具有足够的阻力压降,一般占烟风系统总压降的30%左右
•在大容量循环流化床锅炉中,为防止布风板过热,均采用水冷布风板,风帽则固定在水冷壁之间的鳍片上,还将整个风室设计成水冷结构,使其可以减少用于水冷风箱和布风板之间的高温膨胀节和厚重的耐火层,同时有利于实现床下点火和锅炉的快速启动。
(3)飞灰分离器
•飞灰分离器是保证循环流化床燃煤锅炉固体颗粒物料可靠循环的关键部件之一,布置在炉膛出口的烟气通道上
•工作温度接近炉膛温度
•将炉膛出口烟气流携带的固体颗粒(灰粒、未燃尽焦炭颗粒和未完全反应的脱硫吸收剂颗粒等)中的95%以上分离下来,再通过返料器送回炉膛进行循环燃烧
•分离器的性能直接影响到炉内燃烧、脱硫与传热,循环流化床锅炉分离器的主要作用在于保证床内物料的正常循环,而不在于降低烟气中的飞灰浓度
•目前,最典型,应用最广,性能也最可靠的是旋风式分离器,一台锅炉通常采用两台或四台分离器。
旋风分离器使含灰气流在筒内快速旋转,固体颗粒在离心力和惯性力的作用下,逐渐贴近壁面并向下呈螺旋运动,被分离下来。
烟气和无法分离下来的细小颗粒由中心筒排出,送入尾部对流受热面。
(4)飞灰回送装置
•返料器的主要作用是将分离下来的灰由压力较低的分离器出口输送到压力较高的燃烧室,并防止燃烧室的烟气反窜进入分离器
•由于返料器所处理的飞灰颗粒均处于较高的温度(一般为850℃左右),所以,无法采用任何机械式的输送装置。
目前,均采用基于气固两相输送原理的返料装置。
典型的返料器相当于一小型鼓泡流化床,固体颗粒由分离器料腿(立管)进入返料器,返料风将固体颗粒流化并经返料管缢流进入炉膛。
由于分离器分离下来的固体颗粒的不断补充,从而构成了固体颗粒的循环回路。
•
在循环流化床锅炉中,物料循环量是设计和运行控制中的一个十分重要的参数,通常用循环倍率来描述物料循环量,其定义为
。
由于颗粒的循环,使未燃尽颗粒处于循环燃烧中,因此,随着循环倍率增加,会使燃烧效率增加。
但另一方面,由于参与循环的颗粒物料量增加,系统的动力消耗也随之增加。
(5)外部流化床热交换器
•外置热交换器的主要作用是控制床温,但并非循环流化床锅炉的必备部件
•将返料器中一部分循环颗粒分流进入一内置受热面的低速流化床中,冷却
后的循环颗粒再经过返料器送回炉膛。
•根据有无外置式流化床换热器所设计的循环流化床锅炉已经在制造领域形
成对应的两大流派,各自具有不同的特点。
(6)底渣排放处理系统
•在循环流化床的燃烧过程中,必须定期排出一些不适合于构成床料的灰渣和杂质,以保证正常的流化状态。
同时对应于锅炉的不同运行工况,也必须维持一定量的床内物料量,防止床压过大,多余的物料也必须及时排出。
•与煤粉炉相比,循环流化床锅炉的底渣量占锅炉总灰量的比例在50%以上,再加之脱硫所形成的额外排渣,因此,灰渣的排放量比煤粉炉要大得多。
•与炉膛内的温度相同的高温灰渣经排渣管直接通入冷渣器。
经底渣冷却器出口放出的灰渣温度约为150℃以下,再送入灰渣场。
•目前,国内采用较多的冷渣器采取风(烟)水联合灰渣冷却的方式,具有热量回收、灰渣分选、细颗粒回炉等功能。
•由于正常运行的循环流化床锅炉排出的底渣均为颗粒物料状,其颗粒粒径处于可以良好流化的范围,因此,目前采用的底渣冷却器大都是基于鼓泡流化床热交换器的原理,在鼓泡流化床壁面上或床层内布置传热效率很高的受热面,用高温灰渣的热量来加热锅炉给水,流化气体在保证正常流化的同时也作为灰渣的冷却介质,水和气体同时起到冷却灰渣和回收灰渣热量的作用。
(7)点火系统
•循环流化床锅炉的点火操作是将静止的、常温状态下的固体物料转变为流化状态下正常燃烧的一个动态过程,这一过程比煤粉炉或层燃炉的启动点火要困难得多,其难度主要在于床温的控制。
•大容量的循环流化床锅炉的点火均采用床下风道燃烧器,通常在炉膛水冷风室下部风室前一次风道内布置有两台风道点火器,将通入布风板下的一次风加热到900℃左右,使高温烟气通过布风板,流过并迅速加热颗粒物料床层。
•还常辅助以床上点火油枪。
(8)辅助系统
3、制粉系统安全运行的措施。
(1)应严格控制磨煤机的出口工质温度
(2)严格控制磨煤机的出口煤粉水分
(3)对高挥发分的煤应控制煤粉的细度
(4)输粉管道中应保持足够的流速,防止煤粉离析
4、煤粉细度R200为30%表示的意思。
用孔径200um的筛子过筛,留在筛面上的煤粉占总煤粉的比例为30%
5、目前国内煤的可磨性系数和煤的磨损指数的表示。
煤的可磨性系数采用哈德罗夫(Hardgrove)法测定的哈氏可磨性系数,煤的磨损指数采用冲刷磨损指数
6、钢球筒式磨煤机的工作原理。
•电动机经过减速箱带动筒体旋转,将筒体内的钢球提升到一定高度后落下将煤击碎,并通过钢球和护甲之间的挤压、研磨和碾压将原煤磨成煤粉
•进入筒体的热空气一边干燥煤粉,一般将煤粉带出磨煤机
7、
影响钢球筒式磨煤机工作的主要因素。
(1)磨煤机的筒体转速。
筒体最佳工作转速下,钢球有最大提升高度,磨煤出力最大,分离效果较好。
(2)护甲。
护甲的形状对钢球的提升高度有较大的影响,随着护甲的磨损,磨煤机出力会逐渐降低,磨煤电耗逐渐增加。
(3)钢球充满系数。
磨煤出力和电耗不随钢球充满系数值成正比,是因为紧贴筒壁的钢球磨煤的能力大,随着钢球充满系数的增加,内层的钢球的数量增加,而其磨煤的能力却下降,因此磨煤出力与钢球充满系数的0.6次方成正比;内层钢球载荷的重心接近筒体中心,其惯性矩的增加比钢球量的增加要慢些,使得电功率与钢球充满系数的0.9次方成正比。
(4)磨煤机的筒体通风量。
通风量过大时,虽然煤粉分布均匀,磨煤出力增加,但磨煤机出口粗粉量也增加,回粉量增加,磨煤电耗增加,制粉系统的经济性下降;通风量过小时,筒内原煤大多集中在磨煤机入口端,磨煤机出口煤粉量下降,而且多为细粉,磨煤出力降低;在保证磨煤出力和煤粉细度的条件下,使磨煤电耗和通风电耗最小的通风量,称为最佳通风量。
8、磨煤机的磨煤出力和干燥出力。
磨煤出力指单位时间内,在保证煤粉细度的条件下磨制的原煤量;干燥出力指单位时间内,将原煤从最初的收到基水分干燥到煤粉水分的原煤量。
9、单进单出球磨机的优点和缺点。
(1)煤种适应性广,几乎可以磨制各种煤
(2)单机容量大,适用于大容量的锅炉机组
(3)对煤中的杂物不敏感,工作的可靠性高
(4)单台设备金属消耗量大,工作电耗相对较大,只适应于带基本负荷
(5)工作中噪声大,煤粉的均匀性较差
10、双进双出球磨机的优点和缺点。
1可以磨制坚硬、腐蚀性强的煤,煤种适应性强
2对煤中的杂物不敏感,工作的可靠性高,可用率高,事故率仅为1%
3磨煤机维护费用低,维护简便
4两端进煤和两端出粉使筒体的利用率高,比相同容积的磨煤机占地少、
出力大、电耗低、噪声小、适用于大容量机组
5负荷变化时反应速度快,当负荷的变化率超过20%/min时,自然滞留
时间仅为10s左右
6运行时磨煤机中的储粉量大,低负荷时通过减小磨煤风量增加旁路
风量可以保持风粉比不变,出力稳定。
7负荷变化时,既可以全磨运行,也可以半磨运行,并可以磨制混合
物料,灵活性高
11、
影响中速磨煤机工作的主要因素。
(1)转速。
转速过高,煤的离心力大,煤还未磨碎就通过研磨件,大颗粒煤
造成通风阻力、粗粉量以及磨煤通风电耗增加。
转速过低时,磨制好的煤粉不能及时被热风带走,细粉量增加,磨煤电耗增加。
转速的确定应以磨煤效果好、磨煤电耗低和研磨部件寿命长为原则。
对大容量磨煤机,为了降低磨煤电耗,减轻磨煤部件的磨损,磨煤机的转速有降低的趋势。
(2)通风量。
通风量的大小直接影响煤粉细度、磨煤出力和石子煤的排出量。
在运行中允许通风量从最低的不发生煤粉沉积的通风量至最大通风量之间随磨煤机的出力而改变,并始终保持风煤比不变。
风煤比与磨煤出力成线性关系。
(3)风环气流速度。
应保证研磨区有良好的空气动力特性,应能将大部分煤粒托起,但只将少量煤粉带入分离器,其余大部分煤粒返回研磨区并在研磨区部件周围形成一定厚度的循环煤层,以便保证足够的磨煤出力,减少石子煤的排放量。
风环流速值过高,则煤粉变粗,通风电耗增加;风速过低,则煤粉变细,磨煤出力降低,石子煤排放量增加。
风环气流值应合理,可以通过控制风环间隙实现。
(4)研磨压力。
压力过小磨煤出力降低,煤粉变粗。
压力过大,则使研磨件的磨损加剧。
运行中随着研磨件的磨损,磨煤压力减小。
应及时调整保持研磨压力不变。
(5)燃料性质。
燃料的水分较大时,容易压成煤饼,造成磨煤出力降低。
水分较低时,则发生滑动,也会造成磨煤出力下降。
灰分较大时会加速研磨件的磨损,硬质煤也将加速研磨件的磨损,还应考虑可磨性系数和磨损指数的影响。
12、中速磨煤机的特点。
•结构紧凑,单台磨煤机金属消耗量低,占地面积小,初投资小,
•运行中噪声低,电耗低
•空载功率小,运行控制灵敏,能适应锅炉负荷的变化
•煤粉的均匀性好
•结构复杂,运行和检修要求的技术水平高
•对煤种有选择性,对原煤中的杂物较为敏感
•不能空磨启动,需要先向磨煤机中进煤后才能启动磨煤机,防止磨煤机部件发生脆裂
13、高速磨煤机的特点。
•高速磨煤机的结构形式与风机相似,主要由一个工作叶轮和蜗壳组成
•风扇磨煤机本身就是排粉风机,结构非常紧凑,工作过程中磨煤、干燥、粗粉分离和煤粉输送一次完成,具有结构简单、体积小和金属消耗少的优点
•水分较高的强塑性褐煤由于高温介质的进入自动破碎,煤粒表面积增大,干燥过程加快,而且,风扇式磨煤机中的煤粒几乎总是处于悬浮状态,与高温介质的混合十分强烈,干燥能力强,还可以配用高温炉烟作干燥剂。
非常适用于冲刷磨损系数Ke<3.5、水分Mar>35%的软褐煤和木质褐煤
•主要缺点是叶轮、叶片和护板磨损快、检修周期短,经常更换部件使运行费用增加
14、
直吹式制粉系统的特点。
排粉机装在磨煤机或空气预热器之前,整个制粉系统处于送风机的压头之下,在正压下工作。
优点:
(1)煤粉不通过排粉机或送风机,风机叶轮不会发生磨损,可以选用效率较高的高效风机,降低通风电耗;
(2)外界的冷空气不会漏入系统内,锅炉的排烟热损失较小。
缺点:
磨煤机和煤粉管道系统可能向外冒粉,必须布置密封风机对系统进行密封,防止冒出的煤粉污染环境或造成自燃和爆炸等事故。
15、
图中标号所代表的设备名称。
16、图中标号所代表的设备名称。
17、图中标号所代表的设备名称。
18、图中标号所代表的设备名称。
19、中间储仓式制粉系统的工作过程。
给煤机将原煤送入磨煤机,热空气和原煤一同进入磨煤机,热空气一边干燥一边将煤粉带出磨煤机进入粗粉分离器,分离器将不合格的粗粉分离出来送回磨煤机重磨,合格的煤粉进入细粉分离器将煤粉和空气分开,煤粉进入煤粉仓,再根据锅炉燃烧的需要通过给粉机将煤粉送入炉膛燃烧
20、
乏气送风系统。
热风送粉系统。
适用煤种。
制粉系统中分离出的乏气中含有约10%的极细煤粉,若作为一次风和煤粉仓落下的煤粉混合后送入锅炉去燃烧,这种系统称为干燥剂送风或乏气送风系统,适用于挥发分较高的煤;
若将乏气通过燃烧器中的专门喷口直接送入锅炉燃烧时,则乏气称为三次风,而热空气作为一次风输送煤粉。
这种系统称为热风送粉系统,适用于挥发分较低的煤。
21、
图中标号所代表的设备名称。
22、图中标号所代表的设备名称。
23、过热器和再热器的作用。
过热器的作用就是将饱和蒸汽加热成具有一定温度的过热蒸汽,提高蒸汽的焓值,从而增加蒸汽的做功能力,提高电厂的循环热效率。
另外,在影响过热汽温的因素变化时保证过热汽温正常,并处于允许的波动范围之内。
再热器的作用是将汽轮机高压缸的排汽再一次加热,使其温度与过热汽温相等或相近,然后再送到中、低压缸膨胀做功。
蒸汽再热一方面可以增加蒸汽的做功能力,提高电厂的循环热效率,另一方面也可以降低汽轮机排汽的湿度,提高末级叶片的安全性。
当影响再热汽温的因素变化时,保证再热汽温处于正常的温度波动范围之内。
24、过热器和再热器的工作特点。
概括地说,外部烟温高,内部汽温高,冷却条件差,安全裕度小。
•过热器和再热器外部的烟气温度很高,大约在600~1200℃,越靠近炉膛烟温越高。
•过热器和再热器内部的蒸汽温度也是比较高的,从饱和状态到集汽联箱出口的过热状态,蒸汽温度的变化范围一般在320~540℃。
有时可达560~620℃。
•过热器和再热器管壁的冷却条件比较差。
由于亚临界压力以下的蒸汽密度比水小,特别是再热蒸汽密度更小,这使得在其他条件相同时候,管壁与蒸汽之间的对流放热系数就小,蒸汽对管壁的冷却能力很差。
•为使管壁金属得到有效冷却,避免超温爆管事故,必须提高管内蒸汽的流速。
但是提高流速会增大压降,使蒸汽的做功能力下降,因此过热器和再热器内流速的选取必须综合考虑管壁冷却和压降两个因素。
•由于管外烟温高、管内汽温高、冷却条件差,所以过热器和再热器管壁温度很高,特别是末端部分的壁温最高,往往需要采用抗氧化温度较高的合金钢,甚至不锈钢。
一般情况下为降低锅炉造价,应尽量使用低级别的钢材,设计锅炉时,基本上使各级过热器和再热器金属管子的工作温度都接近允许使用温度,金属的安全裕度很小。
在这种情况下,若在超过其设计工作温度10~20℃下长期运行,会使管子的寿命下降约一半。
因此,在过热器和再热器的运行中应保持汽温稳定,汽温的波动不应超过额定温度的-10~+5℃的范围。
25、
大型锅炉的对流过热器和再热器可分为逆流、顺流,由蛇形管排组成,根据布置方式,可分为垂直式和水平式两种,蛇形管的排列方式有顺列和错列两种,蛇形管可做成单管圈、双管圈和多管圈。
辐射式过热器和再热器布置在炉膛壁面上或炉膛上方,直接吸收炉膛辐射热。
由于炉膛中的辐射传热强度大,可减少金属耗量,同时辐射式受热面具有与对流式受热面相反的汽温特性,有利于改善整个过热器和再热器系统的汽温调节特性,所以辐射式过热器或再热器得到了广泛应用。
对于高参数大容量的锅炉,因其蒸发吸热量所占比例较小,所以应在炉膛内布置足够的辅射式过热器或再热器受热面,以便将炉膛出口烟温降低到合理范围之内。
26、为了防止辐射式过热器和再热器超温爆管事故的发生,可采取的措施。
(1)尽可能将辐射式过热器和再热器布置在热负荷稍低的炉膛上部。
如布置在炉顶或炉膛上部壁面区域。
(2)将辐射式过热器和辐射式再热器作为低温受热面,以较低温度的蒸汽冷却这些受热面
(3)采用较高的管内工质质量流速,加强对管壁的冷却。
27、
为保证屏式受热面外圈管子工作安全,下图(a)~(d)采取的措施。
外圈两圈管子截短、外圈一圈管子短路、内外圈管子交叉、外圈一圈管子短路而内外管屏交叉。
28、布置包覆过热器的主要目的。
现代大容量锅炉的包覆过热器采用的结构。
为了简化炉墙结构,减轻炉墙的重量,便于采用悬吊结构的敷管炉墙。
现代大容量锅炉的包覆过热器都采用膜式壁结构,这样可以保证锅炉烟道的气密性。
29、分隔屏过热器的作用。
(1)降低了炉膛出口烟温,避免或减轻炉膛出口的结渣。
(2)改善了整个过热器系统的静态汽温特性,当锅炉负荷发生变动时,使过热器系统的出口汽温的变化幅度变小。
(3)切割旋转烟气流,减少气流残余扭转效应,使炉膛出口气流沿水平烟道宽度能分布得比较均匀,有利于降低烟气沿水平烟道宽度方向的烟温偏差。
30、
下图是300MW亚临界压力锅炉的过热器系统,该系统的布置有哪些特点?
•整个过热器系统为辐射一对流组合式系统,由于辐射过热器和对流过热器具有相反的汽温特性,所以使整个过热器系统出口汽温的变化幅度变小,减轻了汽温调节的负担。
•各级(或段)过热器之间用集中大直径管道及三通管道连接,加强了蒸汽的混合,减少了过热器热偏差。
•在后屏出口联箱与末级高温过热器进口联箱之间布置左右交叉连接管,使由后屏过热器出来的蒸汽左右交叉进入末级高温过热器,可以减少过热器左右两侧的热偏差。
•布置两级喷水减温器调节过热蒸汽温度。
在分隔屏进口管道上布置第一级喷水减温器,这一级减温器除调节过热汽温外,还有控制进入分隔屏的蒸汽温度、防止分隔屏和后屏出口管壁超温的作用。
第二级减温器布置在末级高温过热器的进口管道上。
31、
下图是300MW亚临界压力锅炉的再热器系统,该系统的布置特点。
•整个再热器系统为辐射—对流组合系统,所以使整个再热器系统出口汽温随负荷的变化特性比较平稳。
•屏式再热器和末级再热器之间用中间联箱、三通和两根大口径管道相连,并左右交叉,加强了蒸汽的混合,减少了再热器偏差。
•在第一级墙式辐射再热器的进口管道上布置有事故喷水减温装置。
再热汽温的调节是用摆动燃烧器上下倾角的方法完成,汽温调节灵敏度高。
•再热器采用三级布置,与二级布置比较,每级的焓增量降低,使每级再热器出口蒸汽温度偏差减少。
32、过热器和再热器的热偏差。
过热器和再热器的热偏差指过热器和再热器管组中因各根管子的结构尺寸、内部阻力系数和热负荷可能不同而引起的每根管子中的蒸汽焓增不同的现象。
33、引起过热器和再热器并列工作的管子间吸热不均的主要原因。
(1)炉内烟气温度场和速度场客观上是不均匀的。
由于炉膛四周水冷壁的吸热,使得靠近炉壁处的烟气温度总是比炉膛中部的烟气温度要低,同时由于炉壁处的流动阻力