废液焚烧装置 危废处理 操作手册.docx
《废液焚烧装置 危废处理 操作手册.docx》由会员分享,可在线阅读,更多相关《废液焚烧装置 危废处理 操作手册.docx(40页珍藏版)》请在冰豆网上搜索。
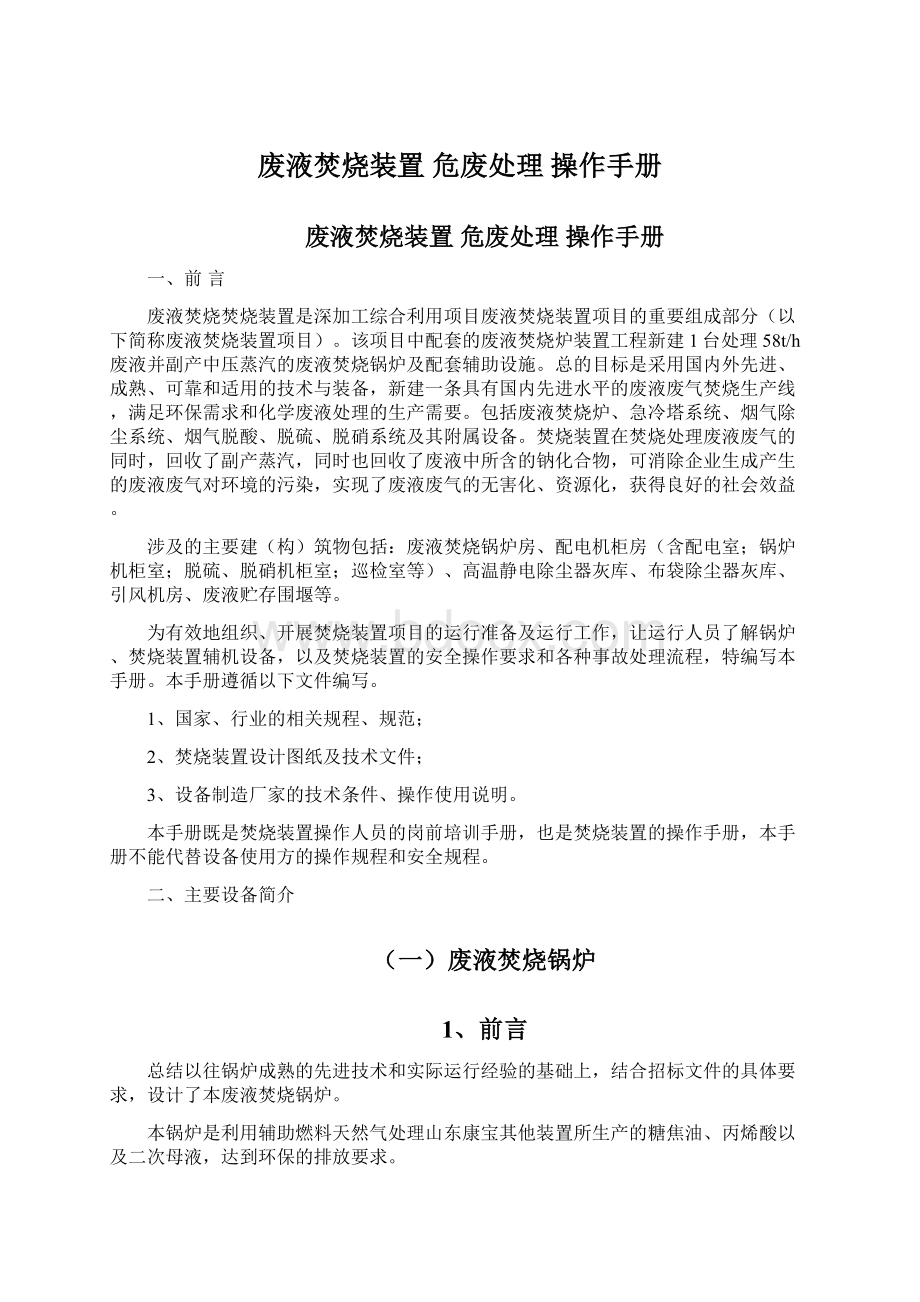
废液焚烧装置危废处理操作手册
废液焚烧装置危废处理操作手册
一、前言
废液焚烧焚烧装置是深加工综合利用项目废液焚烧装置项目的重要组成部分(以下简称废液焚烧装置项目)。
该项目中配套的废液焚烧炉装置工程新建1台处理58t/h废液并副产中压蒸汽的废液焚烧锅炉及配套辅助设施。
总的目标是采用国内外先进、成熟、可靠和适用的技术与装备,新建一条具有国内先进水平的废液废气焚烧生产线,满足环保需求和化学废液处理的生产需要。
包括废液焚烧炉、急冷塔系统、烟气除尘系统、烟气脱酸、脱硫、脱硝系统及其附属设备。
焚烧装置在焚烧处理废液废气的同时,回收了副产蒸汽,同时也回收了废液中所含的钠化合物,可消除企业生成产生的废液废气对环境的污染,实现了废液废气的无害化、资源化,获得良好的社会效益。
涉及的主要建(构)筑物包括:
废液焚烧锅炉房、配电机柜房(含配电室;锅炉机柜室;脱硫、脱硝机柜室;巡检室等)、高温静电除尘器灰库、布袋除尘器灰库、引风机房、废液贮存围堰等。
为有效地组织、开展焚烧装置项目的运行准备及运行工作,让运行人员了解锅炉、焚烧装置辅机设备,以及焚烧装置的安全操作要求和各种事故处理流程,特编写本手册。
本手册遵循以下文件编写。
1、国家、行业的相关规程、规范;
2、焚烧装置设计图纸及技术文件;
3、设备制造厂家的技术条件、操作使用说明。
本手册既是焚烧装置操作人员的岗前培训手册,也是焚烧装置的操作手册,本手册不能代替设备使用方的操作规程和安全规程。
二、主要设备简介
(一)废液焚烧锅炉
1、前言
总结以往锅炉成熟的先进技术和实际运行经验的基础上,结合招标文件的具体要求,设计了本废液焚烧锅炉。
本锅炉是利用辅助燃料天然气处理山东康宝其他装置所生产的糖焦油、丙烯酸以及二次母液,达到环保的排放要求。
本废液焚烧锅炉为单锅筒、自然循环,锅炉具有燃烧稳定,适应负荷变化范围大,连续运行周期长,运行安全可靠,启动迅速,积灰轻,密封性能好,运行操作简便等特点。
2、基本数据
2.1锅炉设计参数
设计处理生物有机液量15.83t/h
锅炉蒸发量58t/h(铭牌)
蒸汽压力3.0MPa(G)
蒸汽温度~233℃
给水温度104℃
锅炉排烟温度~138℃
热风温度100℃
入炉废液浓度60%—70%
设计热效率68%
锅炉出口过量空气系数1.40
锅炉负荷调节范围60~110%
锅炉水压试验水容积55m3
2.2燃料
2.2.1废液(混合废液低温发热量12.1MJ/kg)
废液锅炉设计量:
糖焦油300t/d、丙烯酸60t/d、二次母液20t/d。
废液的元素分析提供的由中国制浆造纸研究院有限公司2019年12月06日出具的《实验分析报告》完整版,摘录其中的表2如下:
表2化工工程废液的检测分析结果
分析项目
糖焦油
丙烯酸
二次母液
pH
4.8
--
--
比重
1.106
--
--
浓度/绝干度(%)
59.45
69.33
59.15
灰分(575℃,%)
2.63
3.50
1.08
N(%)
19.92
0.90
2.46
C(%)
29.14
69.50
56.46
H(%)
8.37
6.06
4.84
S(%)
2.01
1.95
0.27
O(%)
39.18
20.70
35.88
Cl(%)
0.72
0.08
0.02
Fe(%)
0.060
0.017
0.063
Na(%)
0.58
0.78
0.01
K(%)
0.02
0.01
0
高位发热量(MJ/kg)
19.45
26.03
21.45
低位发热量(MJ/kg)
17.46
24.73
20.41
备注
表中百分含量(%)、毫克/千克(mg/kg)和兆焦/千克(MJ/kg)均对废液总固形物计。
在此表中,糖焦油中含有Cl离子并未反映出来,因此需要修正,采用硝酸银滴定法测出的数据如下:
因此,对《实验分析报告》糖焦油的Cl的百分比进行调整(Cl和水分共计40%),考虑分析实验的方法中O含量是推导得出,所以,糖焦油的元素分析按:
C:
17.48;H:
5.02;O:
23.94;N:
11.95;S:
1.21;Cl:
23.72;Na:
0.35;K:
0.012;Fe:
0.036;W:
16.28。
2.2.2辅助燃料:
天然气
低位发热量:
36170KJ/Nm3
高位发热量:
38465KJ/Nm3
密度(mg/Nm3):
0.73143
压力:
200~300KPa
2.3气象地质条件
2.3.6地震烈度
根据《中国地震动参数区划图》(GB18306-2001),本项目所在地区地震动峰值加速度为0.05,对照GB18306-2001表D1,该地区地震基本烈度值为6度。
2.4公用工程规格
2.4.1蒸汽
(1)中压3.0MPaG压力蒸汽
压力MPaG3.0
温度℃233℃
(2)低压0.6~0.8MPaG压力蒸汽
压力MPaG0.6~0.8
温度℃240℃
2.4.2锅炉软化水
本工段自产。
2.4.3蒸汽冷凝液
本废液焚烧装置产生的蒸汽冷凝液收集后通过疏水泵送至除氧器循环利用。
2.4.4生产用水
一次生产用水参数,满足《生活饮用水卫生标准》GB5749-2006。
供水压力≥0.4MPa(G)
供水温度常温
最大流量200m3/h
2.4.5仪表空气及杂用压缩空气
本装置自产。
2.4.6氮气
纯度≥99.5%
供气压力≥0.5MPa(G
温度环境温度
最大流量200Nm3/h,间断使用。
2.4.7电源
高压电:
10kV±5%频率:
50Hz±0.5%三相三线
低压电:
380V50HZ三相四线
220V50HZ单相+N
仪表电源:
220V50HZ单相+N
电压选择:
电动机≥200kw采用10kv交流。
电动机<200kw采用380v交流。
2.4.8天然气
压力:
0.1-0.2MPa(G)
温度:
常温
最大流量:
2000Nm3/h
2.4.9 氨水
浓度:
20%
最大用量:
750kg/h(其中SNCR脱硝450kg/h,SCR脱硝300kg/h)
2.4.10循环冷却水
供水压力≥0.4MPa(G),
供水温度32℃
最大流量2800m3/h
2.4.11 30%NaOH碱液
浓度:
30%
最大用量:
2500kg/h
2.4.12活性炭
吸附力:
≥12ml/0.1g
最大用量:
100kg/h
2.4.13废水
生产废水输送至界区外一米。
3.锅炉设计
3.1锅炉设计说明
本废液焚烧炉额定蒸发量为58t/h。
锅炉型号:
WGZ58/3.0-1型。
该锅炉焚烧主要处理有机液,辅助燃料为天然气。
天然气在起炉过程投入,正式运行可根据实际情况投入。
本焚烧炉为露天布置,设屋顶雨棚。
该炉系单锅筒、自然循环锅炉,锅炉外形尺寸为14750×14800×42800,钢架顶部标高+42800,汽包标高为+39720mm,炉膛尺寸为4800×4800,炉底标高+5500。
锅炉采用全悬吊结构,整台锅炉悬吊于炉顶板梁上,它可自由地向下膨胀。
锅炉设计采用全密封结构,整个炉膛由Φ60×5(20)无缝钢管与扁钢焊成全膜式结构,管子节距为80mm,炉膛上部设置有水冷屏,其后依次布置沸腾管屏、急冷塔。
正常运行时,锅炉给水采用软化水。
经锅炉给水泵将水送至省煤器,流经省煤器后进入锅筒,再沿下降管到水冷壁下集箱在炉膛内吸热形成汽水混合物回至锅筒汽水分离,所产饱和蒸汽送入管网。
本设备设计处理的有机废液分别由不同罐区或者生产装置处的加压泵、风机通过管廊送至锅炉炉前,保证至炉前的压力,再由炉前系统送入炉内。
锅炉设置有5层燃烧器,最下和最上两层设置为天然气燃烧器,糖焦油、丙烯酸二次母液组合设置在中间三层,一次风与燃料一起送入炉内,二次风布置在5层燃烧器上部作为补燃风保证燃料充分燃烧。
废液在炉内采取悬浮干燥燃烧,废液喷枪采用压缩空气雾化,四角切圆布置形式。
由于雾化粒度较细,因此废液进入炉内与高温烟气接触,很快干燥与燃烧,一部分细微的颗粒燃烧后的灰分随烟气至锅炉尾部沉积或被布袋除尘器布袋过滤而被除下来,一部分融化成熔融盐通过后墙的溜槽流出。
3.2给水质量标准
给水采用界区地下水经软水装置软化后进入除氧器进入锅炉。
软化水水质满足GB/T1576-2018《工业锅炉水质》。
3.3锅炉结构
炉膛和水冷系统
炉膛为正方形,由膜式水冷壁构成,水冷炉膛具有寿命长,密封性能好的特点。
膜式水冷壁由Φ60×5(20G/GB/T5310-2017)管子和扁钢制成,炉膛四周水冷壁均焊有销钉,工地安装时在此区域敷设刚玉耐磨可塑料炉衬(δ=60),以保持高温区,利于废液的干燥和稳定燃烧。
在锅炉后墙的水冷壁底部设一个溜渣口。
炉膛出口有烟室,使烟气温度降至850℃左右,不使受热面挂壁。
对于带酸性气体的废液炉,水冷壁管子采用碳钢材料敷以刚玉耐磨可塑料或中质耐酸浇注料,能够保证废液锅炉的安全稳定运行。
沿炉膛高度设置有足够数量和强度的刚性梁,使炉膛具有足够的抗外爆和内爆能力,防爆压力不低于8.7kPa。
炉膛留有一定数量和大小的开孔,以满足风道、燃烧器、观察、吹灰和维修以及各种仪表开孔等需要,并便于通过各楼层平台进行操作。
炉膛各开孔采用合理的密封结构,特别地,在看火孔、吹灰孔和检查门等位置采用空气密封的措施保证锅炉密封性。
锅筒及汽水分离装置
锅筒内径为Φ1500mm,用壁厚为30mm的Q345R钢板卷制而成,通过锅筒吊架悬吊在炉顶构架上。
锅筒内采用水下孔板及顶部百叶窗两级汽水分离装置,能可靠的将汽水混合物分离,保证良好的蒸汽品质。
为防止运行中锅筒满水,锅筒内装有紧急放水管。
锅筒内还设连续排污和加药管,保证炉水品质。
水冷屏
本炉采用人字形水冷屏,布置在炉膛上部。
沿炉膛宽度方向布置14片水冷屏,节距为320mm,以防止屏间积灰搭桥,堵塞烟气通道。
每片屏由Φ60×5mm的管子组成,节距为S=80mm,此结构为膜式壁大间距结构,有利减轻此区积灰。
沸腾管屏
为了保证有足够的蒸发受热面,在水冷屏之后布置了一级蒸发受热面,即沸腾管屏。
沸腾管屏沿炉膛宽度方向布置多片,共25片。
用Φ42×4的20G管子与扁钢焊制成膜式结构,此结构有利减轻此区积灰,同时可有效降低烟气温度。
低温省煤器
低温省煤器采用蛇形管结构,管子规格:
Φ32×3(20G),在锅筒与给水管路之间,设置一根Φ57X3.5再循环管供锅炉启动时用。
转向室
转向室作为沸腾管屏与急冷塔的连接结构。
燃烧装置
燃烧装置主要包括废液喷枪、天然气燃烧器及风道,且预留有活性炭喷口,在炉膛下部布置四只天然气助燃燃烧器(配火检)。
助燃燃料在炉内悬浮燃烧,废液入炉雾化后吸收炉内的高温热蒸发,有机可燃物在高温下燃烧。
锅炉采用一、二次风配置,风温约为60℃。
本项目处理的废液采用焚烧炉负压燃烧,而且选取α≥1.2的过量空气系数,提供足够的氧气使其燃烧完全,同时我们采用分级供风方式,减少氮氧化物的生成;其次有较高的炉膛高度,并且在炉膛内部炉壁四周敷设绝热炉衬,以提高该区域的温度水平,使烟气在炉内停留时间≥2s,保证废液中有机物分解燃尽。
在废液喷枪上部设置有第二级天然气燃烧器,可通过燃烧天然气进一步燃烧未燃尽的CO。
锅炉构架
锅炉构架采用全钢架结构,构架由炉顶钢架、柱、梁、水平支撑及垂直支撑构成一个立体桁架体系。
桁架由主柱与付柱组成,主柱主要用来传递垂直荷重,副柱主要用来通过水平支撑保证主框架的稳定性,而垂直支撑主要布置在付柱平面内,其作用除传递水平力外,还保证柱的稳定性,致使锅炉构架完全能承受地震力、风力及锅炉导向力的作用。
构架除承受本体荷重外,还承受锅炉范围内各汽水管道、烟风道及运转层平台的荷重。
本体荷重通过吊杆悬吊在顶板上。
平台扶梯、炉墙及外护板
锅炉主平台布置在锅炉四周,凡有门孔、测量孔、吹灰器、阀门、燃烧器处均有操作维护平台,主要扶梯集中在两侧布置,平台宽1000mm,扶梯宽度800mm,倾角45º,平台及扶梯均采用刚性良好的防滑格栅平台,平台扶梯具有足够的强度和刚性,平台允许活荷载2.2KN/m2,检修平台允许活荷载4.0KN/m2。
平台及扶梯踏板采用具有良好防腐性能的热浸锌格栅结构。
在炉体膜式结构外采用敷管炉墙,其厚度为200mm。
炉顶及炉体外墙采用轻型对人体健康无害的保温材料。
锅炉保温材料外层护板由0.7mm厚的铝合金板包覆,管道外保温材料则由0.5mm厚的铝合金板包覆。
锅炉范围内管道及门孔
锅炉范围内管道是从给水操作台起到锅筒饱和蒸汽阀为止的管道阀门、测量仪表等。
给水操作台共有两根并联管道,在60-110%负荷时用主管道进行调节。
旁路可作启动、进上水、升火及事故状态下的调节。
锅炉炉膛部分、沸腾管屏灰斗及尾部省煤器部分均设置若干检查门,便于检修和清灰。
检查门、看火孔均采用热风(空气)进行正压密封,保证了锅炉烟气不会外漏。
管道最低处装有疏水阀门,最高处装有排气阀门。
锅筒上装有安全阀、压力表、各种水位表,以及自用蒸汽管,加药管和紧急放水管等。
焚烧炉系统还设有定期排污、连续排污、加药、排气、取样、吹灰等管路,并配有相应的阀门。
为了保证锅炉安全运行,锅炉的汽包上有足够数量的安全阀,其要求符合《电力工业锅炉压力容器监察规程》的规范要求。
保温、防腐
敷管炉墙的设计并提供保温金属构件。
按国家行业规定,提供锅炉范围内的保温、防腐的设计制造。
所有易被踩踏的保温应有良好的防护措施。
焚烧炉界区内保温用镀锌薄钢板包覆,外表面温度要求不超过50℃,平台防腐刷漆需要按照腐蚀性工况来设计并制作。
吹灰器
为保持受热面的清洁,保证锅炉连续稳定运行,在水冷屏、蒸发管屏区域布置了11台吹灰器。
吹灰采用程序控制进行。
吹灰器有效吹灰行程为4.8m。
吹灰前应先疏水,再吹灰,以防止管内凝结水入炉使烟尘结块堵塞烟气通道,影响锅炉的正常运行。
3.4锅炉的安全
为安全起见,在炉膛水冷壁后墙与侧墙交界处设置薄弱环节,以便一旦发生炉膛爆炸时,可将此薄弱环节撑开,使爆炸气体由此薄弱环节排出,其目的是将爆炸造成的损失减至最小程度。
锅筒上设有2支安全阀,2支安全阀的排放量大于锅炉的额定蒸发量。
3.5主要配套辅机
序号
设备名称
设备参数
电机功率(kw)
1
鼓风机
风量:
84000m3/h,出口风压:
4000Pa,电压:
10kV
200
2
引风机
风量:
160000m3/h,进口风压:
11100Pa,电压:
10kV
850
3
给水泵
流量:
72m3/h,扬程:
450m,电压:
10kV
160
3.6锅炉仪表
该型号锅炉的计量、检测、控制仪表的配置满足《锅炉仪表配置要求》。
锅炉本体以及尾部相连接烟风道预留能效测试、控制计量孔(点),用于检测、记录锅炉运行状况。
锅炉本体范围内监测项目包括:
给水温度、压力;蒸汽温度、压力(见238F-24-0汽水系统流程图);炉膛出口烟气温度、压力,各级对流受热面进出口烟气温度、压力;排烟温度(见238F-9锅炉烟风系统测点布置图)。
3.7其它
1、钢材消耗量:
锅炉本体耗钢量280(吨);钢结构耗钢量380(吨);
2、锅炉受热面布置合理,辐射受热面1085m2,对流受热面1100m2。
3、锅炉耗电量(含工艺段):
~2050Kw。
3.8汽水系统描述
给水由Φ133管子经给水操纵台送至省煤器下集箱,经省煤器管加热后上升到省煤器出口集箱,再用4根Φ89管子引出至锅筒。
锅筒的饱和水由4根Φ273、2根Φ219下降管将水引出,其中2根进入前、后、左、右侧墙水冷壁,在水冷壁上集箱由Φ133的管子引出至锅筒,2根引入水冷屏,其余2根下降管则进入沸腾管屏,经沸腾管屏出口集箱引到锅筒。
汽水混合物进入锅筒,由水下孔板对汽水进行一次分离后,在锅筒顶部的百叶窗进行二次汽水分离。
从锅筒出来的饱和蒸汽送入厂区蒸汽管网。
3.9灰渣的收集
从炉底熔融物溜槽流出的熔融物经过渡溜槽、双轴冷却器冷却成固态灰渣,由水冷刮板输送机收集在渣仓,沸腾管屏灰斗、急冷塔的灰通过刮板机与布袋除尘器收集的灰一起收集。
。
3.10烟风系统
锅炉配风采用一、二、三次风系统。
一次风、二次风、三次风均为经空气加热器加热到100℃后进入炉膛。
一次风由四周送入炉膛,二次风、三次风由四角送入炉膛,与由废液喷枪喷入炉膛的废液一起燃烧产生高温烟气,烟气逐级经过炉膛、水冷屏、沸腾管屏、急冷塔、活性炭喷射装置、布袋除尘、湿法脱酸、湿法脱硫、蒸汽-烟气换热器、低温SCR、低温省煤器后把烟气冷却至135℃,从锅炉尾部排出,经引风机排入烟囱。
(二)急冷塔系统(详见供货商提供操作手册)
(三)活性炭喷射系统(详见供货商提供操作手册)
(四)布袋除尘系统(详见供货商提供操作手册)
(五)降膜吸收(HCL)系统(详见供货商提供操作手册)
(六)湿法脱硫系统(详见供货商提供操作手册)
(七)低温脱硝系统(详见供货商提供操作手册)
(八)废液炉主要辅助设备
(九)电气
电气设备清单及说明。
(十)自控仪表、DCS系统
采用现场一次表+DCS式组成方式。
DCS系统采用HPZ240工作站;组态软件采用先进的ECS-700来完成系统组态和编程;网络结构采用工业以太网,具备高速稳定的性能。
废液焚烧锅炉热力系统及废液焚烧工艺系统的温度、压力、液位、流量等参数普遍进行显示及相应调节,便于实现计算机远程操作控制;对锅筒水位计、溜槽熔物流动情况采用工业电视系统。
三、检查、试验及调整
(一)工作程序
1、凡需进行试验、单机试运行的设备、管系、系统安装完毕后,经自检,监理复检,项目部代表认可方进行试验及试运行。
2、所有试验项目,试运行设备均应编写试运方案,明确试验目的及方法。
3、按照试验、试运行应具备的条件进行检查,记录试车条件检查结果,经有关方面签字后开始试车。
4、试车过程中,按规定进行检查、记录,填写试车检查记录。
5、试车过程中出现故障及缺陷,由安装单位或供货厂家按照设备技术文件进行处理,并重新填写试车检查记录。
6、试车后确认不符合技术要求的设备(武锅供货),由武锅负责整改,直至提供新设备;设备性能不能满足工程项目要求的设备,由甲方与武锅协商解决。
(二)废液炉及工艺管道检查
1、废液炉检查
1.1炉内检查:
包括锅筒、受热面、集箱、炉膛及烟道内部的检查,此项检查大部分已结合安装验收工作进行。
对经检查封闭的锅筒人孔应确认没有打开过;炉膛内应无杂物;炉底刚玉(高铝质)涂料完整;受热面管子上无其它附着物;仪表和取样管不应有堵塞或破裂现象,其管线不影响炉体膨胀;燃烧装置、吹灰器应完整,位置正确;烟道、风道完整、密封;灰斗应已清理干净,无其它杂物。
1.2 炉外检查:
各人孔门、看火孔、检查门、清渣门应完整并正常开闭;保温层应完整无脱落现象;调节档板操作灵活,开度指示应与实际相符合,并将档板调整至启动位置,如鼓风机、引风机出口档板应开启,进口档板应关闭等;水位计完整、清洁,显示清晰正确;操作盘各仪表、信号装置、指示灯、开关等完整良好(此检查与电气、自控专业人员配合进行)
1.3 汽水系统检查:
对汽水阀门、空气阀、排污阀、事故放水阀、取样阀、安全阀、再循环阀、反冲洗阀进行检查,应完整、动作灵活,手轮开启方向与指示相符;电动门应进行试验,调整其开度满足使用要求,确认其电气和机械部分完整可靠;膨胀指示器是否完整,并校对其指示为零位;汽水系统管道如主蒸汽管、给水管、排污管等管道上不需要的堵板已经拆除。
S1.4平台、楼梯、通道上的不需要附加物及临时设施已拆除,无其它杂物、清洁干净,通行顺畅,安全可靠,照明设施完整。
2、工艺系统管道
2.1按工艺系统管道设计,对天然气、糖焦油、丙烯酸、二次母液、中低压蒸汽、冷却水、清水、污水、循环冷却水、氨水、氨气等系统检查,确认其管道管件如法兰、阀门、测量控制装置、支吊架等均已完整安装,且进口端、出口端已完善接入设备或相应接口管道,符合设计要求。
2.2管道阀门完整,动作灵活,手轮开启方向正确,电动装置已调试合格。
2.3 精度较高的测量及控制装置,如流量孔板应取出,待系统管道冲洗、试运完毕后再行恢复规定的安装状态。
3、管道冲洗试运
3.1试运转的目的
3.1.1对整个工艺系统管道及槽罐进行冲洗,清除焊渣和其它污物,为进入生产介质作准备;
3.1.2检查考核系统的严密性,检查有无泄漏,暴露设计、制造、安装过程中的缺陷和不足;
3.1.3进一步考核相关辅机性能。
3.2试运转前应具备下列条件
3.2.1相关辅机已经过单机试运转,确认已满足使用要求,无遗留问题;
3.2.2所有与系统有关的管网全部安装完善(包括与其它车间的管线碰头全部完毕),且各支吊架全部完善;
3.2.3 相关电气控制系统及仪表监控全部完善,随时可投入使用;
3.2.4车间的排水系统应畅通;
3.2.5加热系统蒸汽管道保温应完善,外来蒸汽管路能提供汽源;
3.2.6所有容器内杂物均清理完毕。
3.3试运的步骤
向各容器内注水冲洗干净后,封闭人孔门。
对系统管路确定排放点(一般在输入、出设备如泵前后的管道进行解裂),拆卸连接用紧固件,便于冲洗时排出污水及杂质,待冲洗及水质澄清后,恢复原有连接。
启动各系统泵、搅拌装置以及其它辅机,在整个系统内循环冲洗,冲洗完毕后,停机排放污水,清除残留杂物,处理遗留问题,准备进入生产介质。
3.4注意事项
3.4.1 泵起动时应保证进入泵内的水质澄清无杂质;
3.4.2所有泵类起动时应遵循下列原则;
3.4.2.1 离心泵起动时出口阀门全闭,进口阀门全开;
3.4.2.2 柱塞泵起动时进出口阀门全开;
3.4.3 两台离心泵并联运行时,如要停其中一台泵,应将这台泵的出口阀关掉,再停车,避免反车;
3.4.4发现异常应及时停车检查,待故障排除无疑后,才能再次启动;
3.4.5所有参加试运行人员,应服从统一指挥,并相互协调好各个环节,不得随意启动和停止各种设备,防止发生意外;
3.4.6所有蒸汽加热系统应在热状态下进行一次予紧。
3.5试运转的系统
1、溜槽冷却循环水系统试运
清水高位水槽循环水槽循环水泵换热器
溜槽循环水槽
2、废液系统试运
清水废液总管废液加热器炉前废液循环管废液总管
3、密封水系统
清水各密封水冷却水用点密封水回收槽密封水回收泵密封水回收母管
4、蒸汽系统试运
外网蒸汽检查汽密性各用汽点贯通各疏水装置
4、废液炉工作压力水压试验
本次水压试验是烘、煮炉及整体试运行前对废液炉承压部件的一次常规检查。
此前在锅炉本体及管路系统组装完毕后,已按《电建规》的规定对废液炉进行超压试验,因此本次水压试验只进行工作压力(以汽包工作压力3.0MPa为试验压力)试验,重点检查未参加废液炉整体水压试验(超压试验)的部位和虽参加过超压试验又重新拆卸过的管件、人孔等部位。
4.1试验水源及试压泵
水压试验后,废液炉将进入烘、煮炉阶段,因此,试验水源为运行用软化水,以便将试验余水作为煮炉用水;不重新接入新的水泵,以锅炉给水泵作为试压泵,废液炉用给水泵上水至空气阀放水后,关闭给水操作台正常进水及辅助进水管路阀门,缓慢开启试验进水管路阀门,进行水压试验。
4.2人员配备
本系统给水泵开启及停止由控制室操作。
现场配操作人员4名,其中1名负责操作台阀门开、关,1名监视汽包压力表,1名监视给水压力表,1名负责阀门检查及关闭,