永冠杯作品.docx
《永冠杯作品.docx》由会员分享,可在线阅读,更多相关《永冠杯作品.docx(22页珍藏版)》请在冰豆网上搜索。
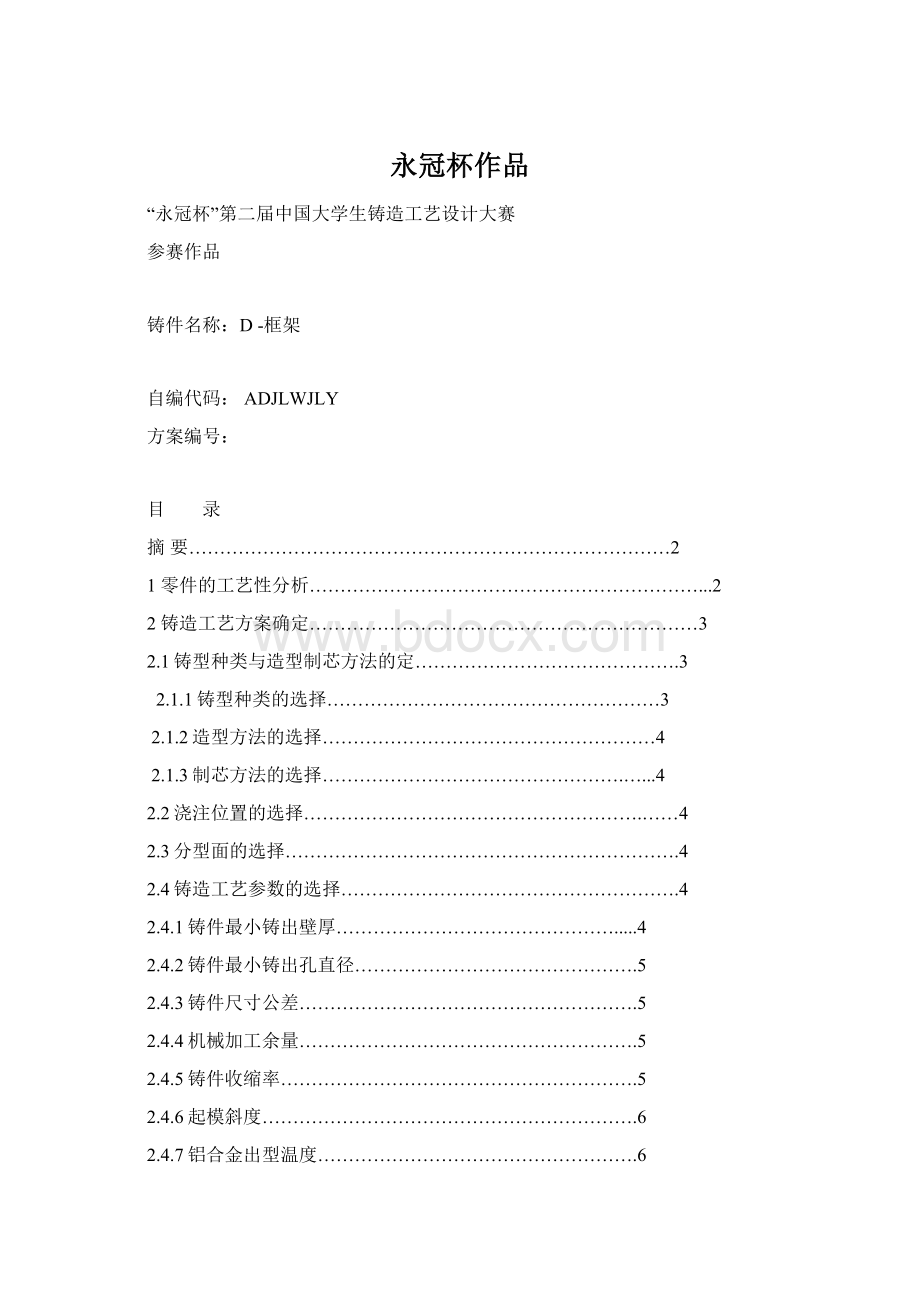
永冠杯作品
“永冠杯”第二届中国大学生铸造工艺设计大赛
参赛作品
铸件名称:
D-框架
自编代码:
ADJLWJLY
方案编号:
目 录
摘要……………………………………………………………………2
1零件的工艺性分析………………………………………………………...2
2铸造工艺方案确定………………………………………………………3
2.1铸型种类与造型制芯方法的定…………………………………….3
2.1.1铸型种类的选择………………………………………………3
2.1.2造型方法的选择………………………………………………4
2.1.3制芯方法的选择………………………………………….…...4
2.2浇注位置的选择……………………………………………….……4
2.3分型面的选择……………………………………………………….4
2.4铸造工艺参数的选择……………………………………………….4
2.4.1铸件最小铸出壁厚……………………………………….....4
2.4.2铸件最小铸出孔直径……………………………………….5
2.4.3铸件尺寸公差……………………………………………….5
2.4.4机械加工余量……………………………………………….5
2.4.5铸件收缩率………………………………………………….5
2.4.6起模斜度…………………………………………………….6
2.4.7铝合金出型温度…………………………………………….6
2.5砂箱尺寸设计……………………………………………………..6
3砂芯的设计与计算……………………………………………………….7
3.1中部圆头砂芯设计………………………………………………..8
3.2两侧砂芯设计……………………………………………………..9
4浇注系统设计…………………………………………………………….9
4.1确定直浇道,横浇道,内浇道,浇口杯的尺寸和个数………..9
4.1.1直浇道的确定…………………………………………........10
4.1.2横浇道的确定………………………………………………11
4.1.3内浇道的确定………………………………………………12
4.1.4浇口杯尺寸确定……………………………………………12
5冒口、冷铁设计…………………………………………………………13
6过滤网的选择…………………………………………………................14
7铸件的变质处理和晶粒细化…..………………………………………..14
8造型和模拟…………………………………………………………........14
9结论和参考文献………………………………………………….……16
摘要
本作品为D件---U形框架,材料为铝合金ZL114A,铸件质量为127kg。
铸件外形尺寸为2310mm×520mm×570mm,主要壁厚为12mm,最大壁厚45mm。
本铸件采用手工造型,选择呋喃树脂砂造型和制芯。
采用开放式浇注系统,,浇注比为直浇道:
横浇道:
内浇道=1:
2:
3。
分型面选在上图的X轴方向,浇注位置选在铸件的内侧分型面上。
设有4个内浇道,位置都在铸件的加工面上,呈对称分布。
直浇道为片状直浇道。
铸件上的6根圆柱采用预埋的方式成型,不铸出,利用预埋的轴将砂芯固定,避免了砂芯悬浮在型腔内,解决了砂芯固定和定位问题。
中部圆头砂芯用芯头进行定位。
端部两轴台壁比较厚,设计横浇道末端的集渣槽进行补缩,并加了一个环形冷铁进行局部激冷。
中部凸台设计了一个边冒口补缩。
工艺出品率为69.4%。
采用造型软件UG设计出零件的三维图,将其导入到Pro/E中划分网格,最后在Procast软件中模拟浇注和凝固过程,观察模拟结果,验证工艺方案的合理性。
通过对结果的分析我们可以看到,最终零件成形质量良好,为出现浇不足和大的缩松缩孔缺陷,符合零件的使用要求。
1零件的工艺性分析
本铸件是一个壳形件,材料为铝合金ZL114A,铸件质量为127kg。
铸件外形尺寸为2310mm×520mm×570mm,主要壁厚12mm,最大壁厚45mm。
特征为横向尺寸跨度大,壁薄,且两端凸台和中部环形凸台壁比较厚,框架U形部位有肋板,伸出部分有六根轴,在中部环形凸台内部有四个圆孔需要铸出。
铸件的三维造型如图1-1所示。
图1-1U形框架三维造型图
由于铸件尺寸比较大,壁厚相对于整体尺寸太小,浇注时很容易产生浇不足、缩松、缩孔等缺陷。
而且,伸出部位的两个砂芯的定位和固定比较困难。
针对这些特点和难点,我们在铸造工艺上进行了分析研究。
由于U形框架尺寸比较大,而且壁很薄,我们选用砂型铸造手工造型,为了提高铸件的尺寸精度和表面质量,改善型(芯)砂的溃散性,采用呋喃树脂砂造型和制芯。
我们将浇注位置设成上图右图位置,这样放置有利于安放冒口和砂芯,易实现顺序凝固。
从便于下芯、合箱以及尽量减少分型面数量等方面考虑,我们分型面选在图1-1的X轴方向。
铝合金质轻,热容量小,导热快,温度降低快,极易氧化和吸气[1],因此,我们采用开放式浇注系统,且为中间注入式,为减少冲击,防止吸气和氧化,直浇道做成片状形式,并在直浇道窝与横浇道接口处设置过滤网,既能挡渣,又可以起到缓流的作用。
在设计砂芯时,考虑到伸出部分悬臂砂芯定位困难,且六根圆柱轴充填比较困难等问题,我们将六根轴采用预埋的方式(轴的材料依然是ZL114),跟砂芯固定在一起,这样既能起到固定砂芯的作用,又避免了轴充填困难的问题。
铸件的两轴台和中间圆环轴台部分壁较厚,容易出现缩松缩孔,因此我们在两轴台外围设置一环形冷铁,并将横浇道末端的集渣槽做成保温冒口形式,而中间圆环轴台部分也设置一个边冒口进行补缩。
由计算机模拟结果可以看出我们设置的冒口起到了很好的补缩效果,没有出现浇不足和大的缩孔缺陷。
2铸造工艺方案的确定
参考相关文献,在考虑了铸造合金的种类、零件的结构与技术要求、生产批量的大小和生产条件等因素后,设计了数种工艺方案。
经过反复运用UG,Pro/E造型化分网格,Procast数值模拟后,确定了一种最优的铸造工艺方案。
应用Procast进行模拟分析的流程如下图所示:
图1-2Procast应用流程
2.1铸型种类与造型制芯方法的选择
2.1.1铸型种类的选择
采用砂型铸造时,选用铸型的原则是:
中小铸件应优先选用湿型;对于湿型不能满足要求时,或大型铸件、有较大水平壁的铸件、造型过程长或需长时间等待浇注的铸件等情况下,则应考虑选用树脂砂型或水玻璃砂型、干型等[2]。
考虑到铝合金铸件收缩率大,氧化比较严重及铸件本身的结构特点,我们选用树脂砂型,用呋喃树脂做粘结剂。
2.1.2造型方法的选择
造型方法可按砂型紧实成形方式分为手工造型和机器造型两大类。
本铸件采用手工造型。
2.1.3制芯方法的选择
采用树脂自硬砂制芯,不用烘干,节省了资源,又缩短了生产周期。
2.2浇注位置的选择
浇注位置是铸造工艺设计中的重要环节,关系到铸件的内在质量、铸件的尺寸精度及造型工艺过程的难易。
浇注位置是指浇注时铸件所在铸型中所处的位置,即铸件那个部位应该在上或下[2]。
通常,确定铸件浇注位置时,很大程度上着眼于控制铸件的凝固,以保证铸件质量。
我们所铸件材料为铝合金,铸造收缩大,铸件横向跨度大,壁厚相对于铸件外形尺寸太小,铸件中空,而且砂芯很难定位。
考虑到以上因素,我们选取图2-1所示的浇注位置,既有利于铸件的顺序凝固和补缩,又方便砂芯的固定和定位。
图2-1零件浇注位置及分型面
2.3分型面的选择
分型面的优劣,在很大程度上影响铸件的尺寸精度、成本和生产率。
分型面确定的是否合理,对于能否简化铸造工艺、降低成本、提高铸件质量等都有直接关系。
通常砂型分型面的选择应与浇注位置尽量一致,以避免合型后还要翻转。
分型面一般设在铸件的最大截面上,以便顺利取出模型。
因此我们选用上图的X轴方向为分型面。
2.4铸造工艺参数
2.4.1铸件最小铸出壁厚
合金液的流动性、铸件的轮廓尺寸和铸造方法,决定了合金液的冲型能力。
为了避免铸件浇不到和冷隔等缺陷,应要求铸件壁厚不小于最小壁厚。
对于砂型铸造各类铸造合金铸件的最小壁厚可参考表2-1[3]。
表2-1砂型铸件最小壁厚(单位:
mm)
铸件轮廓尺寸
铸件材质
铸钢
灰铸铁
球墨铸铁
可锻铸铁
铝合金
镁合金
铜合金
≤200×200
8
≈6
6
5
3
—
3~5
﹥200×200~500×500
10~12
6~10
12
8
4
3
6~8
﹥500×500
15~20
15~20
—
—
6
—
—
该铝合金铸件轮廓尺寸>500×500,所以铸件最小壁厚为6毫米。
对铸件图纸分析可知,铸件的壁厚为12毫米,满足最小壁厚要求。
2.4.2铸件最小铸出孔
通常零件图样上较大的孔应铸出,从节约金属和机械加工工时的原则出发,较小的孔或槽,或者铸件厚壁处不宜铸出,直接用机械加工成孔反而方便,因此,对铸件孔的大小有一定要求,根据零件材质和壁厚查表可知[3],我们研究的铸件最小铸出孔直径为20mm。
2.4.3铸件尺寸公差
铸件尺寸公差是指铸件公称尺寸的两个允许极限尺寸之差。
在这两个允许极限尺寸之内,铸件可满足机械加工,装配和使用要求。
查表1-9[3]可得:
轻金属合金砂型铸造机器造型和壳型的公差等级为7~9级,取8级,铸件基本尺寸为1600~2500mm,可得到铸件尺寸公差为3.8mm。
2.4.4机械加工余量
GB/T6414-1999《铸件尺寸公差与机械加工余量》中规定,机械加工余量值应根据最终机械加工后成品零件的最大轮廓尺寸和相应的尺寸范围选取。
查表知[3],铸件机械加工余量可取4.5mm。
2.4.5铸造收缩率
铸造收缩率又称铸件线收缩率,用模样与铸件的长度差初一模样长度的百分比表示[4]:
式中L1---------模样工作面尺寸;
L2---------铸件尺寸。
为获取尺寸精确的铸件,必须选择适宜的铸造收缩率,查表的铝硅合金自由收缩率为1.0~2.0%,取1.0%。
2.4.6起模斜度
模样的起模斜度应不致使铸件超出尺寸公差,取1º。
2.4.7铝合金出型温度
非铁合金铸件浇注后的出型温度见表1-3[3]。
表2-2非铁合金铸件的出型温度
名称
铸造工艺性
出型温度/℃
铝合金铸件
热烈倾向性小,如Al-Si系合金
250~300
热裂倾向性大,如Al-Cu系合金
150~200
铜合金铸件
热脆性小,如铝青铜
450~500
热脆性大,如锡青铜
250~300
由此可知铝合金的出型温度为250~300℃.
2.5砂箱尺寸
由于我们所铸的零件尺寸比较大,而且壁薄,横向跨度大,因此我们在一个砂箱中铸一个铸件。
按铸件及模样平均轮廓尺寸得[2]:
a=110mm,b=140mm。
(如图2-2所示)
所以,沙箱尺寸为:
长=2310+110x2=2530≈2550mm
高=520+140x2=800mm
宽取1600mm
图2-2沙箱尺寸(中部长方形代表铸件轮廓)
验算:
根据压力角验算高度是否满足充型要求。
验算公式为:
Hm≥Ltana
Hm——最小剩余压力头;L——直浇道中心到铸件最高且最远点的水平投影距离;a——压力角。
其中
Hm=148mmL=1150mma=7º
Hm≥Ltana=1150*tan7º=141mm
所以沙箱高度符合要求。
3.砂芯的设计与计算
砂芯主要靠芯头固定在砂型上,对于垂直砂芯,为了保证其轴线垂直,牢固地固定在砂型上,必须有足够的芯头尺寸,对于水平芯头,必须有足够的芯头长度,以承受砂芯的重力和金属液的浮力。
根据我们所研究的铸件的特点可知:
采用水平分型,其两边的异形长方体砂芯跨度很大,而且悬浮在砂型上,因此必须采用加芯撑的方法保证砂芯安放及定位要求,另外,铸件上的轴经研究可以采用预埋的方法,有利于简化铸造工艺,且预埋的棒料有助于砂芯的定位。
根据铸件的结构,本铸件使用三个砂芯。
具体分布为:
中部圆头砂芯3#,两侧分别采用1#、2#悬臂砂芯形成内腔。
由于1#、2#砂芯较长,须用芯撑。
中部圆头砂芯依靠两个芯头定位,砂芯下部设计成如图3-1所示的形状,以防止砂芯绕轴线旋转。
两侧悬臂砂芯悬浮在砂型内的,所以采用预埋的方法,将砂芯与三根圆柱棒做在一起,这样既可以起到固定砂型的作用,而且可以使砂芯精确定位,在砂芯的上下表面各加入一些芯撑,下面的芯撑起支撑的作用,上面的芯撑可以防止砂芯上浮。
两侧砂芯细且长,刚度不容易保证,因此我们在砂芯内加入芯骨以提高砂芯的刚度。
图3-1砂芯示意图
由于铸件的分型面与铸件自身的对称面重合,属于水平面。
因此,本铸件芯头采用水平芯尖。
具体尺寸设计如下所述。
3.1中部圆头砂芯设计
中部圆头砂芯示意图如下:
图3-2中部圆头砂芯示意图
查表1-34[3]水平芯头长度、表1-35[3]水平芯头顶面与芯座的间隙、表1-36[3]芯头斜度和芯头与芯座间隙得。
1)小头部分
根据铸件形状芯头部分,D=153mm
L=180mm+4.5mm=184.5mm
查表1-34,1-35得
l1=50~60mm,取60mm;
间隙:
S=1.0mm;
l2=0.6l1=36mm;
斜度:
а=3º
砂芯角度а1=7º
2)大头部分
根据该侧芯头部分,D=430mm
L=180mm
查表1-35,1-36得
L1=80~100mm,取100mm;
间隙:
S=1.0mm;
L2=0.6l1=60mm;斜度:
а=2º30'
3.2两侧砂芯设计
示意图如下:
图3-3两侧砂芯示意图
两侧砂芯芯头形状根据铸件结构,设计为方形芯头。
根据芯头部分,L=540mm
D=
=
mm=163mm
查表
取L3=80mm;
间隙:
S=1.5mm;
斜度:
а=5º
砂芯角度а1=2º
4浇注系统设计
树脂砂造型,浇注系统应遵循的原则是:
快(大流量)、稳(防止飞溅和紊流)、顺(金属液流动方向有利于气、渣排出)、封闭、保证压头[7]。
铝合金质轻,热容量小,导热快,温度降低快,极易氧化和吸气,且氧化物的密度与铝液相近,混入铝液中的氧化物很难浮起,易引起夹杂,凝固件收缩率大,易产生缩孔和缩松,因此,对浇注系统的要求是:
快速,平稳充型,不产生飞溅,冲击和涡流,有强的挡渣能力和有利于顺序凝固[3]。
根据合金特性,铝合金铸件采用开放式浇注系统,分型面中间注入式。
为了较少冲击,防止吸气,直浇道采用片状形式,并采用带过滤网的缓流式浇注系统。
设置了4道内浇道,两侧各2道,呈对称分布。
4.1确定直浇道,横浇道,内浇道,浇口杯的尺寸和个数
铝合金铸件浇注系统中的最小截面积,通常为直浇道下端的端面面积,由奥赞公式可得:
(cm2)
式中GL——浇注重量,包括浇冒口在内,取2倍铸件质量;
K——流量系数,取0.04~0.07,铸型阻力大时取下限,这里取0.04;
Hp————平均压力头,单位为cm;
(H0为内浇道至浇口杯液面的高度,根据前面砂箱高度取400mm,单位为cm;c为浇注位置铸件总高度即铸件型腔高度;P为内浇道上的铸件高度,单位为cm)。
t为浇注时间,t=δ
铸件质量
G=ρV=47526215.02
×2.7×103kg=127.37kg
浇注质量
GL=2
×G=254.74kg
平均压力头
Hp=400-
=360mm
经验系数S取值3.6,参看表2-58[3]。
则
浇注时间
t=3.6
=22.82s
将铝合金的浇注质量、流量系浇注时间及平均压力头带入奥赞公式,求得铝合金铸件浇注系统直浇道最小截面积的计算式为
=14.7cm2
根据表5-39[6]铝合金铸件的直浇道面积在5~20(cm2)之间,取直浇道面积S直=15cm2
根据表2-62[6]浇注系统各组元常用截面积比可知,铝合金大型铸件的各浇道比直浇道
As:
ΣAru:
ΣAg=1:
(2~5):
(2~6)
本铸件取
As:
ΣAru:
ΣAg=1:
2:
3
4.1.1直浇道的确定
片状直浇道的形式如下图所示:
图4-1片状直浇道示意图
参看片状直浇道尺寸,表2-61[2]
由直浇道的截面积
As=15cm2,取
As=16cm2组数据,片状部分
a=25mm,b=8mm,s=25mm,n=8.
其中,直浇道窝的尺寸依据直浇道的片状形式,形式如下图所示:
图4-2直浇道窝示意图
4.1.2横浇道的确定
查表5.1-79[4]铝、镁合金铸件的梯形横浇道截面尺寸参考值,如图:
图4-3横浇道截面尺寸示意图(其中b=0.8a,H=1.5a,R=3~5mm)
根据Aru=28cm2,估算得a=47.5mm。
取a=48mm,
则
b=38mm
H=72mm
R取4mm
4.1.3内浇道的确定
查表[4]铝、镁合金铸件的扁平内浇道截面尺寸参考值,如下图所示
图4-4内浇道截面尺寸示意图(其中a=4~6e,b=a-(2~4),R=2~3mm)
依据铸件的实际情况、加工面与非加工面的位置以及浇道设计在加工面上的原则,在对称位置的内浇道尺寸相同的前提下,两侧两组内浇道的实际尺寸不取得相同。
其中
靠近框架铸件中部的内浇道取为
a=75mm
b=68mm
h=20mm
R=3mm;
远离框架铸件中部的内浇道为
a,=40mm
b,=36mm
h=25mm
R,=2mm。
4.1.4浇口杯尺寸确定
由于本铸件为铝合金材料,并且采用了片状直浇道。
所以选取了相对适合的池形浇口杯。
查表5.1-51[4]池形浇口环尺寸,本铸件的质量为127.37kg,铸件质量在(100~200)内,并且片状直浇道在浇口杯上投影呈“一”字排列,因此,在标准浇口杯尺寸的基础上略作改动。
浇口杯示例如下图所示:
图4-5浇口杯尺寸示意图
浇口杯尺寸为:
A=320mmB=150mmH=160mm
a=20mmR=30mmR1=25mm
H1=15mm
片状直浇道与浇口杯之间过渡圆弧,R取7mm。
5冒口、冷铁设计
由于铝合金铸件收缩率比较大,所以必须设置冒口来补缩,且为了保证冒口部分最后冷却,能起到最好的补缩效果,采用保温冒口。
分析知铸件的两端凸台部分比较厚,本应该要设置冒口,但是横浇道末端的集渣包设计为明冒口形式,经Procast模拟后分析发现,可以满足凸台部分补缩的需求,所以这部分就不用设置冒口了。
在铸件的中部环形凸台部分,必须要设置冒口,但是由于凸台环形外围是不加工面,所以我们采用边冒口,设置在圆柱的端部,如图所示:
图5-1冒口的设计
观察procast模拟结果我们发现,在端部凸台部分有比较大的缩松,因此我们在凸台外围设置一个随形冷铁,厚度为30mm。
6.过滤网的选择
铝合金铸件的充型速度很快,这样容易导致铸件的氧化比较严重,因此我们在直浇道窝和横浇道搭接处设置两个玻璃纤维网,网孔尺寸为1.2mm×1.2mm,厚度为0.35mm[1]。
7.铸件的变质处理、晶粒细化及人工时效处理
对于铝硅系合金,变质处理时不可缺少的工序。
其目的是改变共晶硅或初生硅的形貌,从而显著提高合金的力学性能。
本实验采用加入1.5~2%的钠变质剂进行变质处理,并加入自沉细化块进行晶粒细化,并进行人工时效处理。
8.造型和模拟
采用UG软件造型,分别画出零件图,浇注系统,砂芯和沙箱,并将其装配在一起,然后导出CATIAV5格式的文件,导入到Pro/E中划分网格,铸件和浇注系统的网格大小为20mm,砂箱和砂型的网格大小为30mm。
完成后,网格导入到Procast中进行模拟。
其中浇注温度为700℃,浇注速度为2.1m/s,铸件和砂型之间的换热系数为500w/㎡k,空冷。
在模拟之前,我们做了很多简化处理:
所有圆角均为画出,因为在proe中画网格时圆角部分会报错;冒口形状用简单的长方体代替腰形,但保证总体积不变;冷铁均为画出,且预埋的六根圆柱棒与砂芯一起,作为砂芯处理。
由于铝合金的出型温度为250~300℃,因此我们冷却到了300℃左右就结束了,这时所得结果与室温下的结果差别不大,缩松缩孔都已经形成。
结果如图所示:
图8-1温度场分布图
图8-2凝固时间图
在Procast模拟结果中,我们还可以看到缩松和缩孔的位置及大小,如图所示:
(a)沿x方向(b)沿y方向(c)沿z方向
图8-3铸件内部的缩松缩孔
观察上面几幅图我们可以看出,铸件的缺陷主要出现在壁厚的端部凸台部位,分析其原因主要是凸台部位壁比较厚,中心部位最后凝固,得不到补缩,造成缩松缩孔。
而且在模拟时我们简化了模拟的条件,未将冷铁加入到砂型中去。
实际的浇注过程中加入冷铁,可以显著减小缩孔的大小和数量。
另外,凸台部位的缩孔不影响铸件的使用性能。
9.结论
(1)采用开放式浇注系统,并使用片状直浇道,减缓充型速度,浇注出来的铝合金铸件质量良好,符合使用要求。
(2)由上图我们可以看到,铸件充型良好,最终冷却没有出现大的浇不足和收缩。
三个冒口起到了很好的补缩效果,由此验证了我们所设计的工艺方案是合理可行的。
(3)将六根轴采用预埋的方式不铸出来,既有利于砂芯的固定和定位,又避免了轴在浇注过程中易收缩产生浇不足的缺陷问题。
(4)对铸件进行数值模拟是方便可行的,能够在减小铸件缺陷的基础上有效的提高铸件的合格率。
参考文献
[1]严青松、余欢、徐志峰等.浇注工艺对金属型铸造ZL114合金性能的影响[J].铸造技术.2009.2.Vol.30No.2
[2]陈琦,彭兆弟.实用铸造手册.[M].北京:
中国电力出版社,2009.
[3]李弘英、赵成志.铸造工艺设计[M].北京:
机械工业出版社,2005.2:
1~310
[4]王文清,李魁盛.铸造工艺学[M].北京:
机械工业出版社,2002.10:
290~305
[5]刘瑞玲、范金辉.铸造实用数据速查手册[M].北京:
机械工业出版社.2006.8
[6]<<砂型铸造及工装设计>>联合编写组编.砂型铸造工艺及工装设计[M].1980年08月第一版
[7]曹瑜强.铸造工艺及设备(第2版)[M].北京:
机械工业出版社.2008.
附图
附图1零件工艺图(.dwg文件)
附图2铸件三维造型图
附图3模拟浇注过程和凝固过程图
附图2铸件三维造型图
三维造型图(红色代表砂芯,黄色代表铸件和浇注系统)
附图3模拟铸件浇注与凝固图
图1充填30%
图2充填60%
图3充填100%
图4开始凝固
图5凝固到300度
图6凝固时间图
图7各节点温度随时间变化曲线(节点间距1000)