压铸模设计 有设计图纸.docx
《压铸模设计 有设计图纸.docx》由会员分享,可在线阅读,更多相关《压铸模设计 有设计图纸.docx(69页珍藏版)》请在冰豆网上搜索。
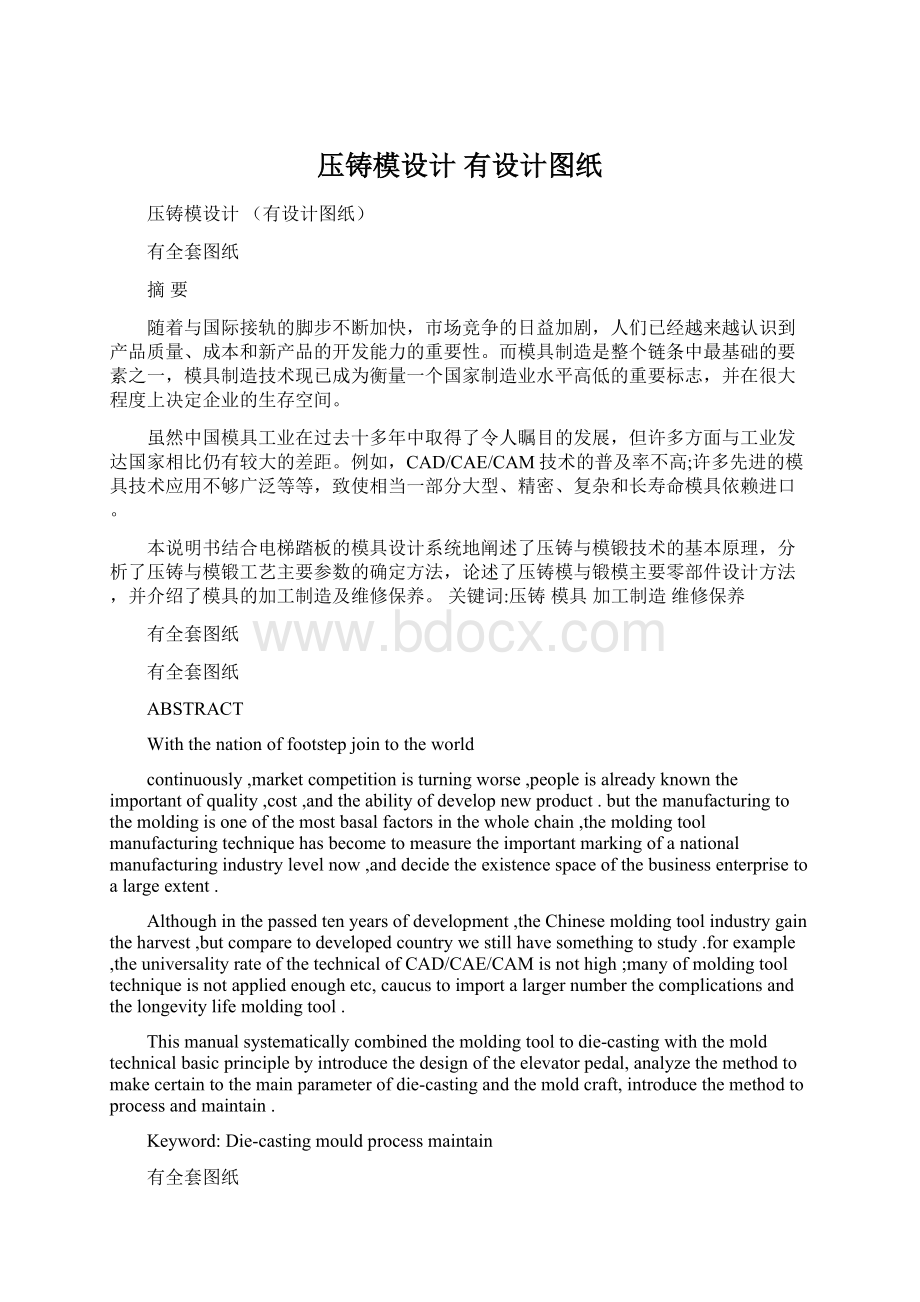
压铸模设计有设计图纸
压铸模设计(有设计图纸)
有全套图纸
摘要
随着与国际接轨的脚步不断加快,市场竞争的日益加剧,人们已经越来越认识到产品质量、成本和新产品的开发能力的重要性。
而模具制造是整个链条中最基础的要素之一,模具制造技术现已成为衡量一个国家制造业水平高低的重要标志,并在很大程度上决定企业的生存空间。
虽然中国模具工业在过去十多年中取得了令人瞩目的发展,但许多方面与工业发达国家相比仍有较大的差距。
例如,CAD/CAE/CAM技术的普及率不高;许多先进的模具技术应用不够广泛等等,致使相当一部分大型、精密、复杂和长寿命模具依赖进口。
本说明书结合电梯踏板的模具设计系统地阐述了压铸与模锻技术的基本原理,分析了压铸与模锻工艺主要参数的确定方法,论述了压铸模与锻模主要零部件设计方法,并介绍了模具的加工制造及维修保养。
关键词:
压铸模具加工制造维修保养
有全套图纸
有全套图纸
ABSTRACT
Withthenationoffootstepjointotheworld
continuously,marketcompetitionisturningworse,peopleisalreadyknowntheimportantofquality,cost,andtheabilityofdevelopnewproduct.butthemanufacturingtothemoldingisoneofthemostbasalfactorsinthewholechain,themoldingtoolmanufacturingtechniquehasbecometomeasuretheimportantmarkingofanationalmanufacturingindustrylevelnow,anddecidetheexistencespaceofthebusinessenterprisetoalargeextent.
Althoughinthepassedtenyearsofdevelopment,theChinesemoldingtoolindustrygaintheharvest,butcomparetodevelopedcountrywestillhavesomethingtostudy.forexample,theuniversalityrateofthetechnicalofCAD/CAE/CAMisnothigh;manyofmoldingtooltechniqueisnotappliedenoughetc,caucustoimportalargernumberthecomplicationsandthelongevitylifemoldingtool.
Thismanualsystematicallycombinedthemoldingtooltodie-castingwiththemoldtechnicalbasicprinciplebyintroducethedesignoftheelevatorpedal,analyzethemethodtomakecertaintothemainparameterofdie-castingandthemoldcraft,introducethemethodtoprocessandmaintain.
Keyword:
Die-castingmouldprocessmaintain
有全套图纸
有全套图纸
1压铸工艺概
论„„„„„„„„„„„„„„„„„„„„„„„„„„1
1.1压铸生产过程和特
点„„„„„„„„„„„„„„„„„„„„„1
1.1.1压铸生产过
程„„„„„„„„„„„„„„„„„„„„„„1
1.1.2压铸特
点„„„„„„„„„„„„„„„„„„„„„„„1
1.2压铸合金的基本要求和种
类„„„„„„„„„„„„„„„„„„2
1.2.1对压铸合金的基本要
求„„„„„„„„„„„„„„„„„„2
1.2.2压铸合金的种
类„„„„„„„„„„„„„„„„„„„„„2
1.3压铸件的结构工艺
性„„„„„„„„„„„„„„„„„„„„„„4
1.3.1壁
厚„„„„„„„„„„„„„„„„„„„„„„„„„„4
1.3.2铸
孔„„„„„„„„„„„„„„„„„„„„„„„„„„4
1.3.3铸造圆角和脱模斜
有全套图纸
有全套图纸度„„„„„„„„„„„„„„„„„„4
1.3.4螺纹、齿轮和槽
隙„„„„„„„„„„„„„„„„„„„5
1.3.5图案、文字和标
志„„„„„„„„„„„„„„„„„„„6
1.3.6镶嵌
件„„„„„„„„„„„„„„„„„„„„„„„„6
1.4压铸主要工艺参数的选择与调
整„„„„„„„„„„„„„„„„7
1.4.1压
力„„„„„„„„„„„„„„„„„„„„„„„„„„7
1.4.2速
度„„„„„„„„„„„„„„„„„„„„„„„„„„9
1.4.3温度„„„„„„„„„„„„„„„„„„„„„„„„„10
1.4.4时
间„„„„„„„„„„„„„„„„„„„„„„„„„12
1.4.5涂
料„„„„„„„„„„„„„„„„„„„„„„„„„122压铸机„„„„„„„„„„„„„„„„„„„„„„„„„„„„
14
2.1压铸机的种类和工作原
理„„„„„„„„„„„„„„„„„„„14
2.1.1压铸机的型号和种
类„„„„„„„„„„„„„„„„„„„14
2.1.2压铸机结构形式和压铸过
程„„„„„„„„„„„„„„„„13
2.1.3压铸机的主要技术参
数„„„„„„„„„„„„„„„„„18
3踏板的压铸模具设
计„„„„„„„„„„„„„„„„„„„„„„20
有全套图纸
有全套图纸
3.1压铸机的选
用„„„„„„„„„„„„„„„„„„„„„„„20
3.1.1锁模力计
算„„„„„„„„„„„„„„„„„„„„„„20
3.1.2压室容
量„„„„„„„„„„„„„„„„„„„„„„„22
模距3.1.3开
离„„„„„„„„„„„„„„„„„„„„„„„23
3.1.4装模尺
寸„„„„„„„„„„„„„„„„„„„„„„„23
3.2浇铸系统和溢流、排气系统的设
计„„„„„„„„„„„„„„„23
3.2.1内浇口的设
计„„„„„„„„„„„„„„„„„„„„„24
3.2.2直浇道的设
计„„„„„„„„„„„„„„„„„„„„„26
3.2.3横浇道的设
计„„„„„„„„„„„„„„„„„„„„„„27
3.2.4溢流槽和排气槽的设
计„„„„„„„„„„„„„„„„„„28
3.2.5动、定模导柱和导套的设计„„„„„„„„„„„„„„„„
29
3.2.6模板的设
计„„„„„„„„„„„„„„„„„„„„„„„30
3.2.7抽芯结构的设
计„„„„„„„„„„„„„„„„„„„„„34
3.2.8推出机构的设
计„„„„„„„„„„„„„„„„„„„„35
3.2.9模具厚度与动模座板行程的核
算„„„„„„„„„„„„„37
4压铸模的技术要求及选材„„„„„„„„„„„„„„„„„„„„
有全套图纸
有全套图纸39
4.l压铸模总装的技术要
求„„„„„„„„„„„„„„„„„„„39
4.1.1压铸模装配图上需注明的技术要求„„„„„„„„„„„„„39
4.1.2压铸模外形和安装部位的技术要
求„„„„„„„„„„„„„40
4.1.3总体装配精度的技术要
求„„„„„„„„„„„„„„„„„41
4.2结构零件的公差与配
合„„„„„„„„„„„„„„„„„„„41
4.2.1结构零件轴与孔朗配合和精
度„„„„„„„„„„„„„„„41
4.2.2滑动零件的配
合„„„„„„„„„„„„„„„„„„„„„41
4.3零件的表面粗糙
度„„„„„„„„„„„„„„„„„„„„„42
4.4压铸模零件的材料选择及热处理要
求„„„„„„„„„„„„„43
4.4.1压铸模所处的工作状况及对模具的影响„„„„„„„„„„„43
4.4.2影响压铸模寿命的因素及提高模具寿命的措施„„„„„„„„44
4.4.3压铸模材料的选择和热处理„„„„„„„„„„„„„„
46模具的加工制造及维修保
养„„„„„„„„„„„„„„„„„47
5.1金属模具的加工制造„„„„„„„„„„„„„„„„„„„„
47
5.1.1金属模县毛坯的获取方
法„„„„„„„„„„„„„„„„„47
5.1.2模样及铸
有全套图纸
有全套图纸
型„„„„„„„„„„„„„„„„„„„„„„„47
5.1.3金属模具的机械加
工„„„„„„„„„„„„„„„„„„„50
5.2模具的快速制
造„„„„„„„„„„„„„„„„„„„„„„„60
5.2.1快速成形技术的原理、主要方法及特
点„„„„„„„„„„„60
5.2.2模具毛坯的快速制造方法„„„„„„„„„„„„„„„„62
5.3铸造模具的维护保
养„„„„„„„„„„„„„„„„„„„„64
5.3.1铸模的预防性维护保养„„„„„„„„„„„„„„„„„64
5.3.2铸模的修复性维
护„„„„„„„„„„„„„„„„„„„65
5.3.3工装模具的清洗技术„„„„„„„„„„„„„„„„„„„68
参考文献„„„„„„„„„„„„„„„„„„„„„„„„71
1压铸工艺概论
压力铸造是将熔融合金在高压、高速条件下充型,并在高压下冷却凝成形的精密铸造方法,简称比铸。
在压铸生产中,压铸合金、压铸模和压铸机是最基本的三大要素,而压铸生产就是将此三大要素加以组合、调整和正确实施的过程。
1.1压铸生产过程和特点
1.1.1压铸生产过程
压铸生产过程包括压铸模在压铸机上的安装与调整、对模具必要部位喷涂涂料、模具预热、安放镶嵌件、闭模、将熔融合金舀取倒入压室、压射(高
有全套图纸
有全套图纸
压高速)成型、铸件冷却后脱模和压铸件清理等过程。
1.1.2压铸特点
由于压铸时熔融合金在高压高速下充型,冷却速度快,因此有如下优点:
1(压铸件尺寸精度高压铸件尺寸精度一般可达IT11~IT13,最高可达
RRam3.2~0.4,IT9,表面粗糙度可达。
因此,压铸件可不经机械加工或个u
别表面只需少量机械加工就可直接使用,既提高了金属利用率,又节省了机械加工工时。
2(压铸件组织致密、硬度和强度较高由于熔融合金在压铸模内冷却迅速,同时又在高压下结晶,因此在压铸件上靠近表面的一层金属晶粒较细,组织致密,表面硬度和强度较高,但伸长率较低。
3(可生产薄壁、形状复杂和轮廓清晰的铸件锌合金压铸件最小壁厚可为0.3mm,铸孔孔径最小值可达0.7mm,螺纹的最小螺距能达0(75mm。
同时,也可以压铸清晰的文字、图案和符号等。
4(可采用镶铸法简化装配和制造工艺将事先准备好的与浇注金属不同材料零件,放入压铸模中规定部位,压铸后零件被固定在压铸件中,这种压铸方法称为镶铸法(又称嵌铸法)。
它既可满足特定部位的使用要求,又可简化装配和制造工艺。
5(生产效率高,易实现机械化和自动化生产—般冷压室压铸机每小时可压铸75~80次,热压室压铸机平均每小时可压铸370~870次,当采用“一模多腔”时,产量还可以成倍增加。
尤其是压铸过程是在压铸机上实现的,故易实现生产过程的机械化和自动化。
尽管压铸生产有上述优点,但也存在以下缺点:
1(压铸件易出现气孔和缩松由于充型时间短,金属液在压铸模内凝固速度快,因此,型腔中的气体很难完全排出,补缩也困难,致使铸件容易产生气孔和缩松,铸件壁越厚越严重,故压铸件壁厚一般在4.5~6mm以下。
有气孔的铸件在热处理时,气孔内气体在高温下膨胀会使铸件表面鼓泡,所以这种压铸件不能进行热处理。
2(对内凹复杂的铸件压铸较困难内凹复杂的铸件所需模具结构复杂,且出件脱模也困难。
3(高熔点合金压铸时,模具寿命低,影响了压铸生产的扩大应用。
4(不宜小批量生产由于压铸模结构复杂,制造成本高且准备周期长,因此只适应于定型产品的大量生产。
有全套图纸
有全套图纸
1.2压铸合金的基本要求和种类
1.2.1对压铸合金的基本要求
为了满足压铸件的使用要求,保证压铸件质量,对压铸合金提出如下要求:
(1)密度小,导电和导热性好;
(2)强度和硬度高,塑性好;
(3)性能稳定,耐磨和抗腐蚀性好;
(4)熔点低,不易吸气和氧化;
(5)收缩率小,产生热裂、冷裂和变形的倾向小。
(6)流动性好,结晶温度范围小,产生气孔缩松的倾向小。
1.2.2压铸合金的种类
压铸用合金可分为铸造铁合金和非铁合金两大类。
铸造铁合金又分为铸铁和铸钢两类。
铸铁类如灰铸铁、可按铸铁和球墨铸铁等;铸钢类如碳钢、不锈钢和各种合金钢等。
由于上述合金熔点高、易氧化和开裂,且模具寿命低,因此铁合金铸件的压铸生产还不普遍。
铸造非铁合金又分低熔点合金和高熔点合金。
低熔点合金如铅合金、锡合金和锌合金等,高熔点合金如铝合金、镁合金和铜合金等。
非铁合金压铸件中比例最大的是铝合金,其次为锌合金、铜合金和镁合金,常见压铸锌合金、铝合金、镁合金的化学成分和力学性能可参考表1-1、表1-2、表1-3。
有全套图纸
有全套图纸
有全套图纸
有全套图纸
1.3压铸件的结构工艺性
压铸件的结构工艺性好,可以简化模具结构,保证压铸件质量,降低成本,提高经济效益。
否则,不仅模具结构复杂,且质量无法保证,甚至造成生产困难。
压铸件的结构工艺性主要包括如下内容:
1.3.1壁厚
实践证明,压铸件壁厚超过某一值时,其强度和致密性随壁厚的增加而下降,这是因为厚壁铸件易产生气孔和缩松等缺陷。
因此在保证强度和刚度的条件下,铸件应尽可能减小其壁厚,通常工艺条件下以不超过4.5mm为宜。
在壁厚相差较大时,应尽可能使各截面的壁厚均匀,在较厚部分可采用减薄壁厚增设加强肋的方法,如图1—l所示(以防铸件产生外表面凹陷、内部缩松和裂纹等缺陷。
铸件有镶嵌件时,镣嵌件周围金属层厚度为(1(5—3(5)mm(以提高金属基体与镶嵌件的包紧力。
由于工艺出案的影响,压铸件壁厚也不能太小,以免产生浇不足和冷隔现象。
最小壁厚可参考表1-4选取。
1.3.2铸孔
有全套图纸
有全套图纸
压铸法的最大优点之一就是能压铸出较小的孔,但必须考虑到压铸合金在冷却过程中向铸件中心逐渐收缩时,对型芯会产生很大的包紧力,因此为防止型芯变形和断裂、考虑抽芯方便等,对铸孔的孔径、孔深和孔与孔之间的距离应加以限制。
一般孔径不小于2.0mm,孔深不大于孔径的4—8倍,孔间距在10mm以上。
1.3.3铸造圆角和脱模斜度
在压铸件壁与壁连接处,都应设计成圆角(它不仅有利于金属流动,便于成型,减小涡流,而且可以防止在尖角处产生应力集中,有利于保证铸件质量。
对模具来说,可以消除尖角处应力集中而延长寿命。
通常,铸造圆角半径最小值可取相邻两壁厚之和的0.5~1.0倍。
为便于压铸件脱模,防止表面划伤,延长模具寿命,压铸件应有合理的脱模斜度。
脱模斜度与铸件壁厚、合金种类等有关。
铸件壁厚越厚。
合金对型芯的包紧力也越大,脱模斜度就越大。
收缩率越大,熔点越高,脱模斜度也越大。
此外,铸件内表面或孔比外表面的脱模斜度要大。
一般脱模斜度取
为。
20~1.0:
1.3.4螺纹、齿轮和槽隙
压铸外螺纹时,需留有(0(2—0(3)mm的加工余量;内螺纹虽可铸出,但必需考虑螺纹旋出装置的复杂性,故一般先铸出底孔,再由机械加工成内螺纹。
螺纹长度不宜过长,因收缩时,长度方向有较人的积累误差。
压铸齿轮的最小模数m=0.3~1.5,对精度要求高的齿轮,齿面应留有(0.2~0.3)mm的加工余量。
槽宽、槽深原则上可参考铸孔,但不能太大。
通常槽宽最小值为(1.0~1.5)mm,槽深最大值为(10~12)mm。
1.3.5图案、文字和标志
压铸文字大小一般不小于GB4457(3—84规定的5号字体。
文字凸出高度应大于(0.3~0(5)mm,线条宽度一般为凸出高度的1.5倍,线条间最小距离为0.3mm,脱模斜度为。
图案、文字和标志在压铸件上匀采用10~15:
:
凸体,且避免尖角。
1.3.6镶嵌件
镶嵌件在铸件内必须稳固牢靠,故其铸入部分可采用滚花、切槽、铣扁和压凸等方式,使金属基体包紧。
镶嵌件包紧部分不允许有尖角等,以免铸件发生开裂。
带镶嵌件的压铸件最好不进行热处理,以免镶嵌件松动。
图1—2为镶嵌件在铸件中的固定方法。
有全套图纸
有全套图纸
总之,压铸件的结构应尽可能避免侧凹、深腔以便于脱模,壁厚均匀,减少尖角,消除铸造应力,以确保压铸件质量。
图1—3为压铸件结构修改实例。
图1—3a、b、c的1分别为轮形、矩形、箱形零件壁太厚产生气孔情况;图中的2分别为修改后情况。
图d是把尖角修改为圆角。
因e的修改是为增大脱模料度、图f的2修改后显然比图f的l起模方便,达到简化模具结构的目的。
有全套图纸
有全套图纸
1.4压铸主要工艺参数的选择与调整
压铸生产时熔融合金充型的过程,是许多矛盾着的因素得以统一的过程。
在影响充型的许多因素中,主要是压力、速度、温度和时间等,时间则
有全套图纸
有全套图纸
是有关工艺参数的协调和综合的结果。
因此,只有对这些工艺参数进行正确选择、控制和调整,才能保证在其他条件良好的情况下,生产出合格的压铸件。
1.4.1压力
(一)压射力
压铸机的压射缸内工作液作用于压射冲头使其推动熔融合金充填模具型腔的力,称为压射力。
它反映压铸机功率大小,其计算式为:
12,,FpD4
式中F——压射力(N);
p——压射缸内工作液的压力(MPa)
D——压射缸直径〔mm〕。
(二)比压
比压是指压射冲头作用于熔融合金单位面积上的压力。
其计算式为:
Fp,A
式中p——比压(MPa);
F——压射力(N);
2mmA——压射冲头截面积()。
将填充阶段的比压称填充比压,充型结束时的比压称压射比压。
比压的选择,应根据压铸件的强度、致密性和壁厚等进行。
一般压铸件要求强度越高,致密性越好,比压就越大。
对于薄壁铸件,因充型困难,故填充比压就要人些;对于厚壁铸件,因疑团时间长,故填充比压可小些,但压射比压要大。
值得注意的是,由于比压过高会使模具受到熔融合金的强烈冲刷和增加枯模的可能性,降低模具寿命,且模具易胀开,因此必须合理选择比压。
现压铸机上调整比压的办法有:
调节压射力的大小和更换不同直径的压射冲头。
一般常用比压可参考表I—6选用。
有全套图纸
有全套图纸
(三)胀型力和锁模力
由于压射比压的作用,使正在凝固的熔融合金将压射比压传递给型腔壁面的压力称为胀型力。
胀型力总是力图使模具胀开,铸件在胀型刀作用下易产牛飞边,为避免此现象发生,压铸机的锁摸机构对模具合模后有一个夹紧力。
故在充型过程中,为保证动、定模相互紧密闭合,沿合模方向上施加在模具上的夹紧力,此力称为锁摸力。
锁模力必须大于胀型力在合模方向上的合力,其计算式为:
FKpA,锁
F式中——锁模力(N);锁
p——压射比压(MPa);
A——铸件(包括浇注系统、排气槽、溢流槽)在合模方向垂直面上的
2mm投影面积(),其中pA项为胀型力的大小;
K——安全系数,一船取1(1—1(3,小铸件取下限,大铸件取上限。
1.4.2速度
(一)压射速度
压射冲头在特定条件下运动的线速度称为照射速度,一般压射速度为(0.3~5)m/s。
压射速度可通过压铸机调节阀无级调速。
(二)充填速度
在压射冲头作用下,熔融合金充型时通过内浇口的线速度称为充填速度。
充填速度偏低,铸件易造成轮廓不清晰;充填速度偏高,型腔中气体排出困难,熔融合金成喷雾状态进入型腔并粘附型壁,降低铸件表面质量或形成内部疏松,且冲刷模具,严重降低模具寿命。
一般压铸件形状复杂、浇注温度低、内浇口较厚和模具导热性好时,充
有全套图纸
有全套图纸
填速度要高些,反之则低些。
实践证明,充填速度在(15—40)m众时可获得优质铸件。
对厚壁或内部质量要求高的铸件,应选择低的充填速度和高的比压,对薄壁或表面质量要求高以及复杂的铸件,应选择高的充填速度和低的比压。
充填速度可参照表1—7选择。
调整充填速度的方法有:
调整压射速度、改变比压和调整内浇口的截面积。
1.4.3温度
(一)浇注温度
浇注温度是指熔融合金从压室进入型腔时的平均温度。
由于压室内的熔融合金温度不便测量,故一般用保温炉内的熔融合金温度表示。
浇注温度过高,合金收缩大,铸件易产生变形和裂纹,铸件晶粒粗大,且易粘模;浇注温度过低,充型困难,铸件易产生冷隔、表面流纹和浇不足等缺陷。
实践证明,在压力较高的条件下,应尽可能采用低的浇注温度,最好使熔融合金呈粘稠的“粥状”时压铸,这样可以减小型腔表面的温度波动和对型腔的冲刷,延长模具寿命,减小气体卷入和产生涡流的可能性,同时也减小了凝固时的体积收缩,减小缩孔缩松倾向。
但对含硅量高的铝合金不宜呈“粥状”压铸,否则会析出大量的游离硅,使加工性能变坏。
各种合金的浇注温度可参考表1—8选取。
值得指出的是,充填速度超大,熔融合金因摩擦作用而升温的数值也越大,当充填速度为40m/s时,铝合金进入型腔时的温度将增加8?
,因此充填速度大时(可适当降低浇注温度,以保证铸件质量。
有全套图纸
有全套图纸
(二)模具温度
模具温度是指模具的工作温度。
压铸模在压铸前要预热到一定温度,预热的作用如下:
(1)避免模具因激热面胀裂。
(2)避免熔融合金因激冷而充型困难或产生冷隔,或因线收缩加大而使铸件开裂。
(3)降低型腔中的气体密度,有利于排气。
但模具温度也不宜太高,否则易造成粘模、铸件顶出变形、模具局部卡死甚至损坏,且会延长开模时间,降低生产串等。
模具预热一般可采用煤气喷烧、喷灯、电热器和感应加热,当模具温度过高时应采用冷却措施,如采用水冷却。
但冷却液应在模具预热以前及时通入,否则,将因激冷而使模具产生裂纹。
模具工作温度按下式计算:
t式中——模具工作温度(?
);模
t——合金浇注温度(?
)o浇
(三)模具的热平衡
在压铸的每—个循环中,单位时间内模具从熔融合金中吸收的热量和传递散发到外界的热量相等时的热平衡就称为模具的热平衡。
对于中小型模具来说,模具吸收的热量总是来不及向外界散发就进入到下一个循环,故须在模具内设置冷却装置调节模具热平衡。
对大型