挤压模具设计课程设计.docx
《挤压模具设计课程设计.docx》由会员分享,可在线阅读,更多相关《挤压模具设计课程设计.docx(14页珍藏版)》请在冰豆网上搜索。
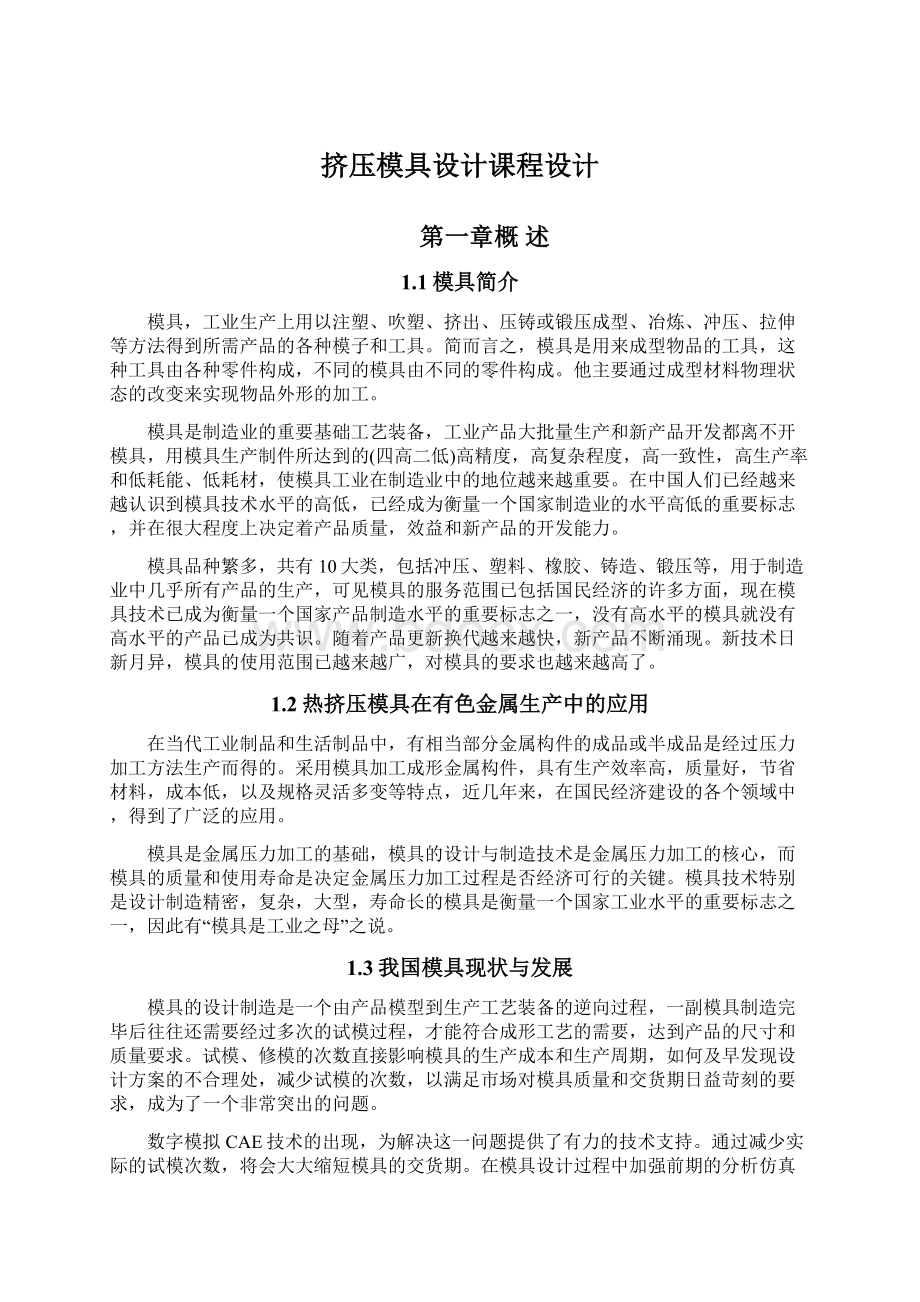
挤压模具设计课程设计
第一章概述
1.1模具简介
模具,工业生产上用以注塑、吹塑、挤出、压铸或锻压成型、冶炼、冲压、拉伸等方法得到所需产品的各种模子和工具。
简而言之,模具是用来成型物品的工具,这种工具由各种零件构成,不同的模具由不同的零件构成。
他主要通过成型材料物理状态的改变来实现物品外形的加工。
模具是制造业的重要基础工艺装备,工业产品大批量生产和新产品开发都离不开模具,用模具生产制件所达到的(四高二低)高精度,高复杂程度,高一致性,高生产率和低耗能、低耗材,使模具工业在制造业中的地位越来越重要。
在中国人们已经越来越认识到模具技术水平的高低,已经成为衡量一个国家制造业的水平高低的重要标志,并在很大程度上决定着产品质量,效益和新产品的开发能力。
模具品种繁多,共有10大类,包括冲压、塑料、橡胶、铸造、锻压等,用于制造业中几乎所有产品的生产,可见模具的服务范围已包括国民经济的许多方面,现在模具技术已成为衡量一个国家产品制造水平的重要标志之一,没有高水平的模具就没有高水平的产品已成为共识。
随着产品更新换代越来越快,新产品不断涌现。
新技术日新月异,模具的使用范围已越来越广,对模具的要求也越来越高了。
1.2热挤压模具在有色金属生产中的应用
在当代工业制品和生活制品中,有相当部分金属构件的成品或半成品是经过压力加工方法生产而得的。
采用模具加工成形金属构件,具有生产效率高,质量好,节省材料,成本低,以及规格灵活多变等特点,近几年来,在国民经济建设的各个领域中,得到了广泛的应用。
模具是金属压力加工的基础,模具的设计与制造技术是金属压力加工的核心,而模具的质量和使用寿命是决定金属压力加工过程是否经济可行的关键。
模具技术特别是设计制造精密,复杂,大型,寿命长的模具是衡量一个国家工业水平的重要标志之一,因此有“模具是工业之母”之说。
1.3我国模具现状与发展
模具的设计制造是一个由产品模型到生产工艺装备的逆向过程,一副模具制造完毕后往往还需要经过多次的试模过程,才能符合成形工艺的需要,达到产品的尺寸和质量要求。
试模、修模的次数直接影响模具的生产成本和生产周期,如何及早发现设计方案的不合理处,减少试模的次数,以满足市场对模具质量和交货期日益苛刻的要求,成为了一个非常突出的问题。
数字模拟CAE技术的出现,为解决这一问题提供了有力的技术支持。
通过减少实际的试模次数,将会大大缩短模具的交货期。
在模具设计过程中加强前期的分析仿真,将会提高成形工艺和模具结构设计的水平,减少试模的工作量,降低模具制造成本,缩短模具新产品的设计制造周期。
我国模具行业现己广泛地采用了CAD/CAM技术,在应用中取得了显著效益。
目前,较有规模的模具企业都已采用了CAD/CAM技术,在模具设计中甩掉了图板,采用CAM技术加工复杂模具型面。
经济实力较强的模具企业已开始应用高速加工机床加工模具。
虽然中国模具工业在过去十多年中取得了令人瞩目的发展,但许多反方面与工业发达国家相比仍有较大差距。
特别在大型,精密,复杂和长寿命模具技术上存在明显差异,这些类型模具的生产能力的不能满足国内需求,因而需要大量从国外口。
根据“十一五”模具行业发展的任务与目标,我国模具行业要努力解决发展中存在的诸如总量供不应求、产品结构不够合理、工艺装备水平低、配套性不好、利用率低、技术人才严重不足、专业化程度低、高档产品市场缺席等问题,使我国模具行业向大型、精密、复杂、高效、长寿命和多功能方向发展,在良好的市场环境中稳步前进。
1.4我国模具发展所面临的问题
目前我国大部分模具企业应用CAD技术还限于二维绘图,数控加工在模具制造中所占的比例仍然较低,与国外先进水平相比,还有较大差距。
CAE在我国模具行业的应用还刚起步,只有为数不多的企业才购买了少量的商品化CAE软件,处于尝试应用、积累经验的过程中。
归纳起来,我国模具CAD/CAE/CAM技术的应用和开发上还存在以下问题:
1)大多数企业CAD的应用还处于计算机绘图阶段,还未开始三维模具设计,致使CAD的效能尚未得到充分发挥,模具设计制造过程中的信息集成受到影响。
2)从总体上讲,模具企业应用CAE还处于初级阶段,只有少部分的企业开始应用CAE,应用面还需进一步扩大,应用水平还有待提高。
3)高水平的CAD/CAE/CAM应用人员,特别是CAE应用人员缺乏,影响了(CAD/CAE/CAM技术的应用效果。
培养大量的CAD/CAE/CAM应用人才,是模具企业普遍面临的问题。
4)模具CAD/CAM系统的二次开发跟不上,利用通用软件解决专业问题,普遍存在效率不高的问题:
5)匡为模具CAD/CAE/CAM技术处于向产业化、商品化过渡的时期,不少自主开发的模具CAD/CAE/CAM系统商品化程度不够高,功能和稳定性方面与匡外先进软件相比还有差距。
“十一五”期间,中国模具业市场份额将达1200亿元。
虽然目前模具产业具有广阔的市场空间,但是受外资垄断挤压产业利润空间以及内资企业自身存在种种问题的困扰,产业投资风险陡然上升。
第二章模孔布置
2.1模孔位置的排列
采用多孔棒材模时,金属流动要比单孔模均匀,故可减少中心缩尾形成的几率。
但是,如果模孔排列不当,会使挤出的制品长短不齐,增加几何废料,恶化表面质量;如果模孔靠近挤压筒边缘,也会使制品表面产生起皮、分层等缺陷。
此外,多模孔过于靠近挤压筒边缘时由于内侧金属供应量大、流动速度快,而外侧由于金属供应量不足,流动速度慢,会造成制品出现外侧裂纹;当模孔太靠近挤压筒中心时,外侧金属供应量大于内侧,则制品易出现内侧裂纹。
图2-1所示,表示了模孔分布对制品长度的影响,从而了解模孔位置布置的重要性,故应将多孔模模孔的理论重心均匀地分布在距模具中心和挤压边缘有适当距离的同心圆周上。
多模孔的同心圆直径D心与挤压筒直径Dt之间的关系可以按以下经验公式来确定:
D心=
(2-1)
式中:
D心多孔模模孔断面中心分布的同心圆直径;
Dt挤压筒内径;
n模孔数目(n2);
经验系数,一般取2.5~2.8;n值较大时取下限,挤压筒内径大时取上限,一般取2.6。
根据上式,取=2.51,计算,D心=
。
D心通过上式求出后,还必须考虑节约模具钢材和工模具规格的系列化及互换性(如模垫、导路的通用性等),再对D心进行必要的调整。
为了延长模具的使用寿命,模孔离模具外径圆周的距离和模孔之间的距离都应保持一定的数值,这个数值与挤压机的大小有关。
对于49MN以下的挤压机,这个距离可取15~50mm;对于大型挤压机,应加大到30~80mm,参照表2-1所列经验数据,取25mm。
表2-1模孔间最小距离
挤压筒直径
80~95
115~130
150~200
220~280
300~500
最小距离
15
20
25
30
50
挤压制品断面尺寸与模具断面尺寸的大小有因果相存的关系,挤压制品的断面尺寸的大小又同挤压力和挤压模具工作断面尺寸密切相关。
挤压制品的断面尺寸越大,所需要的挤压力就越大,因而挤压模具工作端面的尺寸也就要相应增大。
参照表2-2,取挤压制品的外接圆至挤压筒内壁的最小距离25mm。
表2-2挤压制品的外接圆至挤压筒内壁的最小距离
挤压筒直径
80~95
115~130
150~200
220~280
300~500
挤压制品外接圆至挤压筒之间的最小距离
15
20
25
30
50
在本课程设计中,
挤压筒所允许外接圆直径Dw=(0.80~0.85)Dt=160~170,取160mm
模具外径D=(1.25~1.45)Dw=200~232
经验算,满足上述两个要求
2.2挤压比计算
在挤压生产中,金属的变形量大小常用挤压比或加工率()来表示。
挤压比是指挤压成形前锭坯充满挤压筒时的断面积与挤成形后制品断面积总和之比值,以表示:
(2-2)
式中:
Dt¾挤压筒直径;
dk¾棒材直径;
n¾同时挤压制品的根数或模孔数。
带入数据算得=278,
查表2-3,值偏大,在铜及其合金中取材,黄铜,同时温度范围650~840°C
表2-3热挤压各种金属材料时的工艺参数值(部分)
金属材料
挤压温度°C
挤压比λ
流出速度m/s
单位挤压力
铜及其合金
纯铜
820~910
10~400
0.10~5.0
300~650
α+β黄铜、青铜
650~840
10~(300~400)
0.10~3.3
200~500
含10~13%Ni白铜
700~780
10~(150~200)
0.10~1.67
600~800
含20~30Ni白铜
980~1000
-
0.10~(0.4~0.6)
500~850
第三章
模具尺寸设计
3.1模孔尺寸的确定
模孔尺寸的确定主要考虑挤压制品的金属成分、断面形状、尺寸偏差、各部位几何形状特点和型材的冷却收缩量、张力矫直时的断面收缩量等因素的综合影响来进行设计或计算确定。
若用A表示模孔长度,则用以下算式对棒材模进行计算:
A=A0(1+k)(3-1)
式中:
A0¾棒材断面的名义尺寸,圆棒A0为直径;
k¾模孔裕量系数,见表2-1。
由表3-1查得,黄铜,k=1.0~1.2,取k=1.0,则A0=6mm,A=6´(1+1.0%)mm=6.06mm。
取A=6mm
表3-1不同金属模孔裕量系数k/%
金属种类
孔裕量系数k
紫铜
1.5
黄铜
1.0~1.2
青铜
1.7
L1~L7,LF2,LF3,LF21,LD2,LD31等
1.0~1.2
LF5,LY11,LY12,LD5,LD8,LC4等
0.7~1.0
MB1,MB2,MB15
1.0~1.2
高镁合金
1.0~1.2
3.2模孔工作带长度的确定
棒材模的工作带长度是决定棒材尺寸精度和表面质量的基本参数。
工作带过长,容易在其表面粘结金属,使制品表面出现部分毛刺、麻面等缺陷;工作带过短,不能稳定地控制棒材,常易出现椭圆等缺陷,同时,由于工作带易磨损,致使模具寿命缩短。
棒材模的工作带长度可根据被挤压金属的不同有不同的选择。
挤压紫铜和黄铜时,根据经验值,工作带取8~12mm,这里挤压黄铜,取模孔工作带长度hg=10mm
3.3模具外形尺寸设计
模具的外形尺寸主要是根据挤压机吨位大小和挤压模的强度以及装配模具的相关部件结构等因素来确定,同时应当考虑模具的系列化、标准化,便于使用和管理。
1)模具外径D的设计
为了便于制造和更换,模具外径可标准化与系列化。
模具外径尺寸标准化、系列化的必要性有三个方面:
减少模具设计与制造的工作量,降低产品成本,缩短生产周期,提高生产效率;
通用性大,互换性强,只需要配备几种规格的模支撑和模架,可节约模具钢材,容易备料,便于维修和管理;
标准化有利于提高产品的尺寸精度。
因此,对于一台挤压机来说,模具外径最好根据挤压机配备各种规格的挤压筒,有1~3中规格为宜。
表3-3所示为棒材模具外形尺寸。
因设计条件为在19.6MN挤压机的200mm挤压筒上生产6mm的圆棒线材,所以取模具的外圆直径D1为198mm。
表3-2棒材模具外形标准尺寸
挤压机能力/MN
挤压筒直径/mm
D1/mm
H/mm
7.35
11.76~14.7
19.6
34.3
49
122.5
196
85,95
115,130
170,200
270,320,370
300,360,420,500
420,500,650,800
650,800,1100
113,132
148
198
230,330
270,306,360,420
300,420,570,670,880
570,670,900,1000
16,32
32,50,70
40,60,80
60,80
60,80
60,80,120,150
80,120,150,200
3
3
3
3
6
6,10
10,15
2)模具厚度H
模具厚度H应根据被挤压合金的变形抗力(即挤压力)的大小来考虑。
在保证模具组件(模具、模垫、垫环等)有足够的强度的条件下,模具的厚度应尽量减薄,规格应尽量减少。
但为了安装和调整方便,模具的厚度尺寸应尽量可能系列化,便于管理和使用,一般模具的厚度按下述数值(单位:
mm)选用:
20,25,30,40,50,60,70,80,90,100,110
在挤压机设计时,通常选取单位压力为1000MPa时的挤压筒直径Dt作为基本参数来确定模具的厚度,其关系为:
H=(0.12~0.22)Dt(3-2)
将Dt=200mm带入式中,得到H=24~44mm,考虑标准化及强度等因素,将H放大,取H=80mm。
3.4挤压模结构形式与模具外形锥度
挤压模具的外形结构根据其安装方式的不同可以有不同的结构形式,卧式挤压机上用的挤压模有圆柱形、带正锥和带倒锥三种形式。
带正锥的挤压模在操作时逆着挤压方向放到模支承中,为了便于装卸,锥度不能太小,否则,人工取模困难;但如果锥度过大,则可能出现在模座靠紧挤压筒时,挤压模容易从模支承中脱落出来,故正锥的锥度在130~4范围内选取。
带倒锥的挤压模在操作时顺着挤压方向装入模支承中,其锥度为3~10,一般取6左右,为了便于机械加工挤压模的外形锥度,一般在锥体上有一段长10mm左右的圆柱部分。
由表3-2查得,=3,因此,应选择带正锥的挤压模,如图3-1所示。
3.5模具入口处圆角半径的确定
入口圆角半径r选取与金属的强度、挤压温度和制品的断面尺寸、模具结构有关。
根据生产经验,r值可在表3-3所列数值范围内选取。
由于锭坯材料为黄铜,入口处圆角半径r取值范围为2~5mm,则取r=3mm。
模具入口处圆角是指被挤压金属进入工作带时,模具工作端面与工作带表面间形成的拐角r入。
这个角若为尖棱角时,在挤压过程中则易开裂或压秃、压堆,从而改变模孔尺寸,导致难以保证挤压制品的尺寸精度,因此必须采用过渡圆角半径r。
制作入口圆角半径r,
还可以防止低塑性合金在挤压时产生表面裂纹,减小金属在流入模孔时的非接触变形。
但是,圆角增大了接触磨损面积,可能会引起及压力增加。
表3-3模具入口处圆角半径/mm
金属种类
铝合金
紫铜、黄铜
白铜
镍合金
镁合金
钢、钛合金
入口处圆角半径r
0.40~0.75
2~5
4~8
10~15
1~3
3~8
3.6模具出口部位结构及尺寸
模具的出口部分是保证成形制品能顺利通过模具并确保表面质量的重要通道。
模具出口部位又称为模孔空刀,也是指模具出口端尺寸大于模具工作带对应的模孔部分。
模孔空刀既要保证模具工作带强度,又要便于模具的加工制作,同时使制品能顺利导出模孔而不刮伤其表面。
若模具空刀尺寸过大,会大大削弱工作带强度,引起工作带过早变形和压塌,明显降低模具的使用寿命。
因此,对于圆形管、棒挤压模来说,可按以下方式选取:
空刀直径:
d1=d+(3~5)(3-2)
式中:
d模孔直径(即模孔长度)。
由公式(3-1)得d=6.06mm,则d1=6.06+(3~5)mm=9.06~11.06mm,取d1=10mm。
一般情况下,对于模孔形状的挤压模,模孔空刀可选用比模孔边线扩大距离h1可取1.5~2.5mm的形式。
因此模具出口部位结构,如图3-2所示,尺寸为模孔空刀比模孔边线扩大距离h1为1.95mm,空刀直径为10mm。
3.7模具材料的确定
模具的寿命不仅与挤压工艺、模具设计制造工艺过程有关,而且还与模具的材质选择有重要的关系。
对于热挤压模具的材质,必须具备以下条件:
1)具有足够的高温强度。
即模具能承受高温、高压作用,不发生屈服变形和断裂,保证挤压制品获得所需尺寸精度。
2)具有良好的抗磨损性能。
即在高温、强摩擦的挤压条件下,模具材料能抵抗金属制品长时间、高速、激烈的摩擦作用,而不过早出现磨损,尤其对模具工作带表面更显重要。
3)具有足够高的抗疲劳性。
在挤压过程中,模具能承受周期性循环载荷作用而不发生断裂损坏,
因此,模具材料必须具备良好的抗冲击韧性。
4)具有良好的导热性能。
热挤压模具处于高温挤压变形过程中,由变形金属产生的大量变形热及模具与变形金属之间产生的摩擦热,直接传递给模具导致温度升高,为防止模具局部出现“过烧”现象,模具材料应具有良好的导热性能,能向外快速地散发热量。
图3-3模具二维图
5)具有良好的热处理淬透性和可氮化性。
即模具材料在热处理过程中,应保证模具的强度、力学性能均匀
一致。
同时,模具在使用过程中,可多次进行表面氮化
处理,提高模具表面强度的耐磨性。
除此外,模具材料还应具有良好的抗回火稳定性、抗腐蚀性,较低的膨胀系数,良好的工艺制造性能,以及价格的合理性等。
由表3-3,可选取4Cr5MoSiV1作为模具的材料。
4Cr5MoSiV1模具钢,是近年来国内外广泛用于热挤压制品的一种模具材料,其特点是:
具有良好的抗疲劳性能和综合机械力学性能,同时又具有良好的热处理淬透性。
表3-4热挤压模具材料选择(部分)
挤压件材料
模具材料
硬度(HRC)
铜和铜合金
4Cr5MoSiV1
42~44
4Cr3Mo3SiV
5Cr4W2Mo2SiV
3Cr2W8V
4Cr4W4Co4V2Mo
第四章
棒材模强度校核
对于多孔棒材模,需要对模孔之间和模孔与模具外径圆周之间的危险断面进行强度校核。
多孔棒材模的剪切强度计算公式如下:
≤
(4-1)
式中:
Q模具上承受的总压力,一般取Q=0.8P,有时为了安全起见,可取Q=P;
P挤压机的公称压力;
rx各模孔均布的同心圆半径;
d棒材直径;
n多孔模的模孔数;
[]模具材料允许的抗剪切强度,在400℃时,4Cr5MoSiV1钢取[]=(0.5~0.6)b,b由表3-4查得,则[]=(0.5~0.6)1360MPa=680~816MPa,取[]=816MPa;
H模具允许的最小厚度;由下式可得到:
(4-2)
即多孔棒材模具的厚度为:
H≥
(4-3)
表4-1常用挤压工具钢及其机械性能(部分)
牌号
试验温度℃
力学性能
b
MPa
0.2
MPa
%
%
ak
HB
kJ/m2
热处理制度
4Cr5MoSiV1
650
20
400
450
500
550
600
1630
1360
1300
1200
1050
825
1575
1230
1135
1025
855
710
5.5
6
7
9
12
10
45.5
49
52
56
58
67
290
1050℃淬火,625℃在油中回火2小时
根据设计条件及计算,已知P=19.6MN,rx=
,H=80mm,d=6mm,n=4,则有
≤[];
,H≥77.89mm,
因为选取H=80mm,
,故抗弯强度符合要求。
校核通过,设计合理。
第五章
模具实体图
图5-1模具整体图
图5-2模具剖面图
第六章总结
本课程设计为挤压模具设计,在19.6MN挤压机的Φ200mm挤压筒上采用四模孔生产出Φ6mm的圆棒线材。
主要分五个部分,概述部分介绍模具应用于发展,之后依次为模孔布置、模具尺寸设计、强度校核、绘制模具图,最后总结此次课程设计。
通过本课程设计是让我们熟悉所学知识,掌握挤压成形的基本原理;能够综合运用所学知识,发现、提出、分析和解决实际问题;熟练运用有关技术、资料。
课程设计是锻炼实践能力的重要环节,是对我们实际工作能力的具体训练和考察过程。
本课程设计可以帮助我们具体运用和巩固专业课程及相关理论知识,加强我们对专业理论知识的理解和实际运用,通过团队成员的之间的密切配合,加强我们团员之间的合作能力。
通过这次课程设计,使我在原来的理论基础上增加了实战性的知识,同时我也感受到要成为一个模具设计师需要付出很多努力。
本次设计中,图采用CAD画,为准确表达排样图与压力中心坐标图提供了便利。
使我们明白了计算机辅助设计技术和模具在实际生活中的重要性,以后我一定更加努力学习,为将来打下坚固的基础。
这次设计得到张红云、张金标、徐向其、刘建等老师的帮助和辅导,在这里表示衷心的感谢。
参考文献
[1]樊刚.热挤压模具设计与制造基础[M].重庆:
重庆大学出版社,2001
[2]马怀宪.金属塑性加工[M].北京:
北京冶金工业出版社,2012.1
[3]付建军模具制造工艺[M]北京:
机械工业出版社,2004.8