第五章授课54446.docx
《第五章授课54446.docx》由会员分享,可在线阅读,更多相关《第五章授课54446.docx(32页珍藏版)》请在冰豆网上搜索。
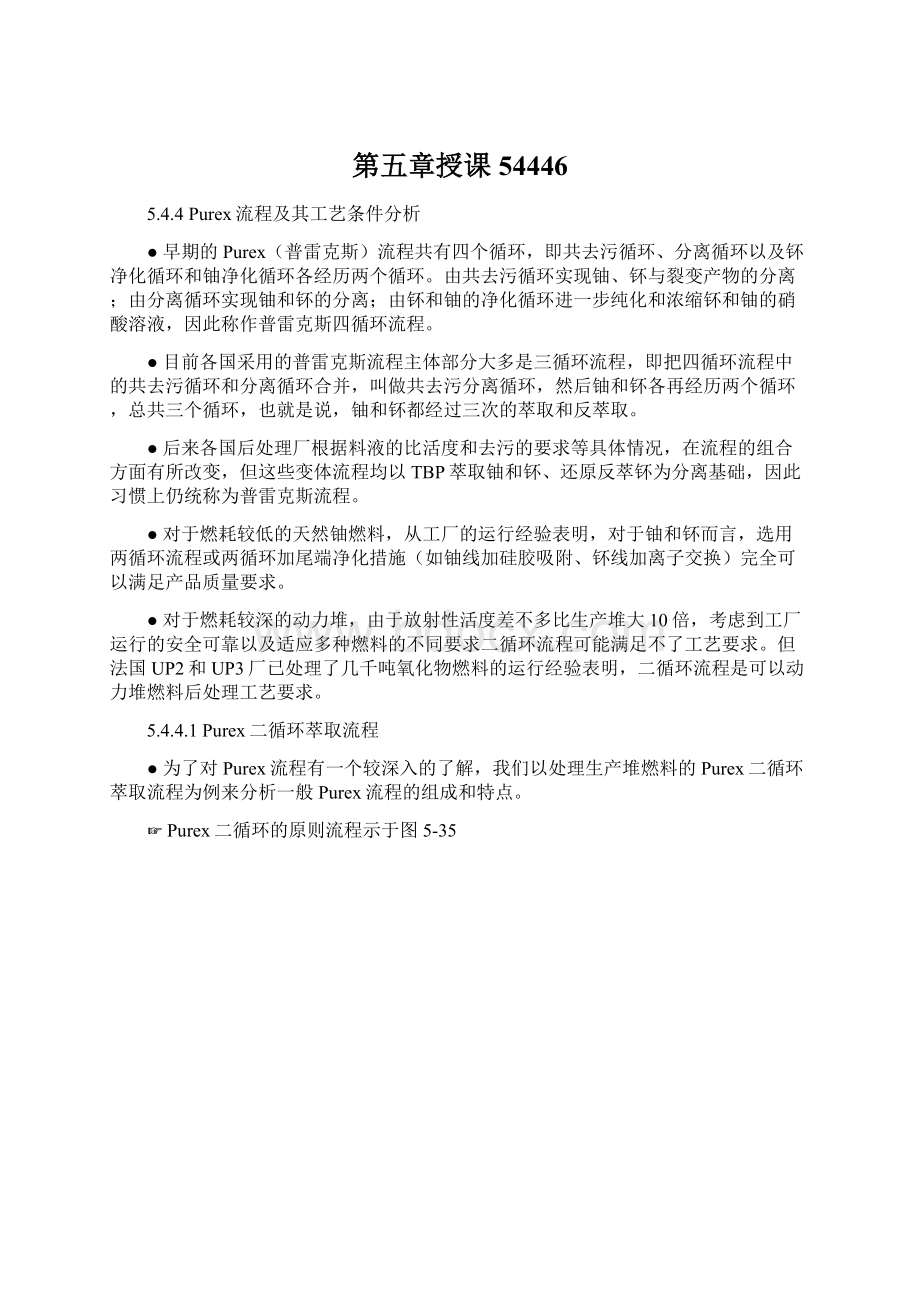
第五章授课54446
5.4.4Purex流程及其工艺条件分析
●早期的Purex(普雷克斯)流程共有四个循环,即共去污循环、分离循环以及钚净化循环和铀净化循环各经历两个循环。
由共去污循环实现铀、钚与裂变产物的分离;由分离循环实现铀和钚的分离;由钚和铀的净化循环进一步纯化和浓缩钚和铀的硝酸溶液,因此称作普雷克斯四循环流程。
●目前各国采用的普雷克斯流程主体部分大多是三循环流程,即把四循环流程中的共去污循环和分离循环合并,叫做共去污分离循环,然后铀和钚各再经历两个循环,总共三个循环,也就是说,铀和钚都经过三次的萃取和反萃取。
●后来各国后处理厂根据料液的比活度和去污的要求等具体情况,在流程的组合方面有所改变,但这些变体流程均以TBP萃取铀和钚、还原反萃钚为分离基础,因此习惯上仍统称为普雷克斯流程。
●对于燃耗较低的天然铀燃料,从工厂的运行经验表明,对于铀和钚而言,选用两循环流程或两循环加尾端净化措施(如铀线加硅胶吸附、钚线加离子交换)完全可以满足产品质量要求。
●对于燃耗较深的动力堆,由于放射性活度差不多比生产堆大10倍,考虑到工厂运行的安全可靠以及适应多种燃料的不同要求二循环流程可能满足不了工艺要求。
但法国UP2和UP3厂已处理了几千吨氧化物燃料的运行经验表明,二循环流程是可以动力堆燃料后处理工艺要求。
5.4.4.1Purex二循环萃取流程
●为了对Purex流程有一个较深入的了解,我们以处理生产堆燃料的Purex二循环萃取流程为例来分析一般Purex流程的组成和特点。
☞Purex二循环的原则流程示于图5-35
●如图5-35所示,Purex二循环流程实际包含了铀、钚共去污分离、铀的净化和钚的净化三个萃取循环。
但对铀、钚而言,各都只经历了两个萃取循环,因而,该流程称Purex二循环流程。
☞共去污分离循环主要由1A、1B、1C三个萃取器组成,它的任务是实现铀、钚与裂片元素的分离以及铀、钚之间的分离。
☞铀的净化循环主要由2D、2E两个萃取器组成,它的主要任务是完成第一循环铀产品液的进一步净化(去除裂片元素及痕量钚、镎)。
☞钚的净化循环也是由两个萃取器(2A、2B)组成,其作用是完成第一循环钚产品液的进一步净化(去除裂片元素和微量铀)与浓缩。
☞在共去污分离循环(第一循环)与铀的净化循环之间设置有1CU产品液流的蒸发浓缩器,以便于对2DF进行调料。
但铀的净化循环有浓流程和稀流程之分,前者需将1CU铀的初产品液进行浓缩,然后再调料;而后者直接将1CU经预处理、调料后便可进料。
☞在共去污分离循环与钚的净化循环之间设有2AF的调料罐,主要任务是调酸和调价(把Pu(III)调到Pu(IV))。
☞每一萃取循环所产生的水相废液(1AW(高放废液),2DW、2AW(中放废液)),均按其放射性水平不同而进入不同的废水处理系统。
☞同样,各循环产生的污溶剂(1CW、2BW、2EW)也按其放射性水平的高低送到不同的污溶剂处理和回收系统。
●以下以混合澄清槽为例,分别介绍Purex二循环中每个萃取器的作用及其工艺过程。
1.共去污分离循环
●共去污分离循环的安全稳定运行是整个工厂生产过程的关键之一。
它的运行好坏直接影响着最终产品的质量,金属的收率,以及整个厂房的辐射安全,对生产起着决定性作用。
这是因为:
1)稳定运行的延续时间,生产负荷,由1A槽控制;
2)铀线、钚线采用几个循环运行,在很大程度上取决于1A槽的净化效果;
3)有机溶剂的质量及再生效果,以及对萃取过程的影响主要表现在1A槽;
4)1A槽界面污物和放射性积累,以及开停车过程中的放射性后移问题最突出;
5)237Np的回收率的高低和对镎的去污好坏在很大程度上取决于1A槽的控制;
6)1AW中的金属流失量,占全流程总流失量的30%左右。
(1)1A萃取槽(共去污槽)
●在1A萃取槽中,主要实现铀、钚与裂片元素间最大限度的分离。
镎随工艺条件的不同,可能与铀、钚一起进入有机相,也可能与裂片元素一道留在萃余液中。
●为了提高去污效果,1A槽通常采用分馏萃取的操作方式。
☞乏燃料经过去壳、溶芯、过滤、调价等首端过程制成的1AF水相料液从1A槽的中部引入,并与从槽的水相出口一端进入的有机相1AX逆流接触(该接触段为1A槽的萃取段),在合适的工艺条件下,U(Ⅵ)、Pu(Ⅳ)在萃取段几乎全部被萃入有机相,而分配系数很小的大部分裂片元素则留在水相萃余液1AW中。
萃余液送往高放废液处理系统进行处理。
☞从萃取段出来的负荷有机相进入槽的洗涤段(洗涤剂入口级至料液入口的后一级)并与1AS洗涤剂逆流接触,以洗涤被TBP夹带或萃取的微量裂片元素,部分被洗涤剂洗下的铀、钚随洗涤液一起进入萃取段,以回收在洗涤段转入水相的少量铀和钚。
☞铀、钚的产品液流1AP进入1B槽。
(2)1B萃取槽(铀、钚分离槽)
●在1B槽中完成铀、钚间的分离。
●同1A槽相仿,1B槽也采用分馏萃取操作方式。
☞1AP由1B槽的中部引入,并与自槽子有机相出口端引入的还原反萃剂1BX逆流接触(此接触段叫钚反萃取段),还原剂将Pu(IV)还原为Pu(III)。
由于Pu(III)的分配系数很低而几乎完全转入水相,绝大部分铀此时仍留在有机相中,从而实现了铀与钚的分离,但少量铀也同时进入水相。
☞为了提高钚中去铀的效果,从槽子的水相出口端引入补充萃取剂1BS(即含一定硝酸浓度的30%TBP-煤油)使其与从钚反萃取段流出的水相逆流接触(该接触段称为铀的补充萃取段),被反萃取进入水相的少量铀大部分铀重新转入有机相,而这一有机相与1AP一起从1B槽右端流出进入下一个反萃工序。
☞水相反萃取液1BP去钚净化循环进一步纯化钚。
☞有机相液流1BU进入1C槽去反萃取铀。
(3)1C反萃取槽(铀反萃取槽)
●在1C槽中实现铀的反萃取。
●该槽采用简单的逆流操作方式,
☞来自1B槽的含铀有机相(1BU)在槽内与稀酸反萃取剂(1CX,通常为0.01mol/lHNO3的水溶液)逆流接触。
由于在这种条件下铀的分配系数很低,因而可定量地将U(Ⅵ)反萃取到水相中。
☞铀的水相反萃取液1CU经蒸发浓缩后送铀净化循环进一步纯化铀;
☞污溶剂1CW经溶剂洗涤系统处理后循环使用(即成为1AX)。
2.铀净化循环
(1)2D萃取槽(铀萃取槽)
●2D槽的作用和操作方式与1A槽基本一致。
☞1CU经蒸发浓缩和调料后制成的2DF料液由2D槽中部进入,与萃取剂2DX逆流接触把铀萃入有机相。
☞萃取液再与从槽子有机相出口端引入的洗涤剂2DS逆流接触,进一步除去锆、铌、钌等裂片元素。
☞萃余液2DW经蒸发浓缩后可送元件溶解器作溶芯用硝酸,也可返回1A槽作1AS洗涤液或者送中放废水处理系统。
☞萃取液(负铀有机相)2DU去2E槽。
(2)2E槽反萃取槽(铀反萃取槽)
●2E槽的作用和操作方式与1C槽相似。
☞用稀酸反萃取液2EX反萃取铀。
☞所得的水相产品液2EU去铀的最终纯化和转化系统进一步处理;
☞污溶剂洗涤后循环使用(即成为2DX)。
3.钚净化循环
(1)2A萃取槽(钚萃取槽)
●2A槽的操作方式与1A槽相同,但萃取对象主要是钚。
☞由共去污分离循环来的稀钚溶液1BP经调价和调酸后制成的2AF料液从槽的中部引入,与从槽的一端进入的萃取剂2AX逆流接触以萃取钚,料液中含少量铀也同时被萃取到有机相中去。
☞萃取液再与从槽子另一端引入的洗涤剂2AS逆流接触,进一步洗去锆、铌、钌等裂片元素。
☞萃取液2AP(负钚有机相)去2B槽进行进一步铀钚分离,
☞萃余液2AW送中放废水处理系统。
(2)2B槽反萃取槽(钚反萃取槽)
●2B槽的作用和操作方式与1B槽类似,主要任务是完成钚的反萃取并进一步去除钚中的微量铀,附带还有浓缩钚的作用。
☞反萃取剂2BX可以采用稀酸或还原反萃取剂。
☞采用还原反萃取时,为了提高钚、铀的分离效果,从槽子的水相出口端引入补充萃取剂2BS,使其与反萃取液逆流接触,将被反萃取到水相中的少量铀再萃取到有机相中(作污溶剂处理)。
☞所得水相产品液2BP去钚的最终纯化和转化工序,
☞污溶剂2BW去溶剂洗涤系统处理或作1B槽的补充萃取剂1BS。
5.4.4.2Purex二循环流程的工艺条件分析
如前所述,在Purex二循环流程中,共有三个溶剂萃取循环(共去污分离循环、铀净化循环和钚净化循环)、七个萃取器(1A、1B、1C、2A、2B、2D、2E)。
下面我们按铀、钚共去污,铀、钚分离,铀反萃取,铀净化及钚净化等五个环节来分析整个流程的工艺条件。
1.铀、钚共去污的工艺条件
●如图5-35所示,铀、钚共去污是在1A萃取器中进行的。
●1A萃取器是Purex二循环流程中的关键性操作单元,它对铀、钚的去污和收率,对镎的走向和溶剂的辐射降解程度都起着决定性的作用。
●由此可见,确定铀、钚共去污的最优工艺条件是很重要的。
但实践表明要作到这点并不容易,因为各种工艺条件对于保证铀、钚的收率和提高净化系数往往是互相矛盾的。
☞比如提高溶剂相中的铀饱和度,有利于改善去污,但不利于提高铀、钚的回收率。
☞此外,对于不同裂片元素的去污方面也存在着矛盾:
如前所述,高温、高酸条件有利于对钌的去污,而低温、低酸条件则有利于对锆、铌的去污。
☞因此在确定工艺条件参数时,必须根据体系的具体情况,对收率与净化的矛盾,锆、钌去污以及锝的诸多的共萃造成难以去污的矛盾加以综合考虑。
(1)1AF中铀的浓度
●1AF料液中铀的浓度高,可以提高萃取器的处理能力;在流比和TBP浓度一定时,可以提高铀的饱和度,有利于裂片元素的去污。
☞但是料液的铀浓度太高时,粘度、密度都增大,流动性不好,影响操作。
☞此外,料液铀浓度的提高还受到硝酸铀酰结晶温度的限制。
比如,当HNO3浓度为1mol/L、铀浓度为2.11mol/L时,UO2(NO3)2的结晶温度仅为18℃
●
●图示曲线表明,UO2(NO3)2的结晶温度与溶液中UO2(NO3)2浓度有复杂的关系。
☞当UO2(NO3)2浓度一定时,先随HNO3浓度的增加,结晶温度下降,出现最小值后上升,并在某一HNO3浓度时出现结晶温度的最大值。
☞而且,所有结晶温度的最小值和最大值都随UO2(NO3)2浓度的增加,向低酸方向移动。
硝酸铀酰-硝酸溶液的结晶温度与硝酸和硝酸铀酰浓度的关系示于图5-36。
●一般在处理天然铀或低浓铀(<3%235U)燃料元件时,常采用1.8mol/l(428g(U)/l)的料液浓度,
●而目前处理动力堆氧化物燃料时则采用1-1.3mol/l(225-300g/l)。
●对于处理浓缩铀燃料元件,由于临界安全的考虑,对1AF中铀浓度有一定的限制。
(2)1AF及1AS中的硝酸浓度
●从图5-29可看出,HNO3浓度对DZr、DNb与DRu的影响正好相反。
高的HNO3浓度有利于Ru的净化,低的HNO3浓度对除去Zr、Nb有利。
●实践表明,为了兼顾对锆、铌、和对钌的去污,1AF及1AS中的HNO3浓度有两种合适的组合方式,
☞即高酸进料、低酸洗涤或低酸进料、高酸洗涤。
☞鉴于钌被萃入溶剂相后,洗涤较为困难,故高酸(3mol/lHNO3)进料可提高钌的净化系数。
低酸(1mol/lHNO3)洗涤对锆、铌也有一定的净化效果。
☞但这种组合方式也有其缺点,一方面由于硝酸铀酰的结晶温度随酸度的增高而下降(低酸度范围内),故高酸进料必然造成料液铀浓度减小,进而减小了设备的生产能力。
另一方面高酸进料还提高了1AW中的硝酸浓度,增加了高放废液处理的困难。
☞反之,低酸(0.5-1mol/lHNO3)进料、高酸(2-3mol/lHNO3)洗涤方式的优缺点正好与前一种酸度组合方式相反。
●对于处理天然铀或低浓铀燃料元件,锆、铌在裂片元素中占较大比例,共去污的主要矛盾是锆、铌的去除,两种酸度组合方式均可获得较好的效果。
☞但采用低酸进料、高酸洗涤方式更为有利,故目前生产上大都采用这一方式。
●对于燃耗深、冷却时间短的动力堆燃料元件,钌在裂片元素中的相对含量较高,一般采用高酸进料、高酸洗涤的方式。
●表5-19列出了几组不同酸度组合的净化系数的实验数据。
表5-19料液和洗涤酸度对去污的影响
1AF:
铀浓度,mol/l(g/l)
1.27(302.26)
0.6(142.8)
1.24(295.12)
1.61(383.18)
HNO3浓度mol/l
3.0
0.8
3.0
2.2
相对流量
100
100
100
100
1AX:
TBP浓度,%
20
30
20
30
相对流量
450
157
450
400
1AS:
HNO3浓度,mol/l
1.5
3.0
3.0
2.5
相对流量
55
56
50
60
铀饱和度(ξ),%
78.4
72.2
76.5
76
净化系数DF
Zr-Nb
300-400
800~1000
80-120
50-80
Ru
~600
150-200
300
200
γ
1500
~1000
200-400
160-200
β-
2500
2000
500-1000
500
组合方式
高酸进料
低酸洗涤
低酸进料
高酸洗涤
高酸进料
高酸洗涤
中酸进料
中酸洗涤
●在实际生产过程中,为了提高净化系数,可以适当降低进料液酸度或洗涤液酸度。
但必须防止因酸度降低而引起金属在1AW中流失量的增大。
降低洗涤液的酸度将使铀、钚的内循环量增加,还会引起设备生产能力的降低,甚至会导致1B槽的钚中去铀分离系数的降低。
(3)1AX中的TBP浓度
●TBP浓度的选择主要取决于所处理的对象,因而其选择要考虑对体系的临界安全、生产能力和水力学性能等三个方面的影响。
☞一般来说,提高溶剂相中的TBP浓度总是有利于提高生产能力,但TBP浓度增大将会相应的增大有机相的粘度和密度,使溶剂的流动和澄清分相的性能变坏。
因此在实践中确定萃取体系的TBP浓度时,要根据处理对象的特点和上述三个方面综合考虑。
☞对于高浓铀燃料元件,为了保证临界安全,TBP浓度通常取3-15%,
☞对于天然铀或低浓铀燃料元件,TBP浓度取值在20-40%范围内选择,
多数采用30%TBP。
(4)有机相中的铀饱和度(ξU)
●如前所述,铀饱和度对铀、钚的收率和裂片元素的净化有相反的影响,是1A萃取器的重要控制参数。
☞许多工艺条件对收率和净化的影响都是通过对铀饱和度的影响来实现的。
☞为了兼顾收率和净化两个方面,一般ξU值取60-80%。
(5)流比(1AF∶1AX∶1AS的流量比)
●在单位时间内两相流量之比,通常称为流比。
☞流比的变化将直接影响有机相的铀饱和度。
显然,流比(1AX/1AF)增大,铀饱和度下降。
☞但是,若将流比(1AX/1AS)减小,则对裂片元素的去污有利,当然也会相应增加1AW高放废液量。
☞若料液铀浓度定为1.8mol/l,溶剂相TBP浓度为30%,铀饱和度为71.6%,则相比通常采取为1AF∶1AX∶1AS=1∶4.75∶(0.75-0.55)。
(6)温度
●由于TBP萃取铀、钚的过程是一个放热反应过程。
因而温度也是1A萃取器的重要操作参数。
☞如前所述,温度对铀、钚和裂片元素萃取的影响是各不相同的,
☞在Purex溶剂萃取体系中,一般DU(VI)、DRu随温度升高而下降,DZr、DNb、DPu(IV)随温度增高而增大。
☞此外,提高温度还能降低两相粘度,有利于澄清分相;但温度过高会使溶剂降解加剧。
☞综合考虑上述各种因素,生产实践中一般将洗涤段加热到40℃左右,而在萃取段则采取一定的冷却降温措施。
2.铀、钚分离的工艺条件
●铀、钚分离是在1B萃取器中进行的,其分离原理是TBP对不同价态的钚具有不同的萃取能力。
☞比如,当HNO3浓度为0.5mol/l时,Pu(Ⅳ)在19%TBP-煤油中的分配系数是0.8,而Pu(Ⅲ)的分配系数仅为0.008。
☞所以在1B萃取器中,加入适当的还原剂或采用电解还原方法,把1AP中的Pu(Ⅳ)还原成Pu(Ⅲ)便可将钚定量反萃取到水相,而U(Ⅵ)此时仍保留在1AP溶剂相中,从而实现铀与钚的分离。
☞因此,还原反萃剂的选择,其浓度的确定,以及各种干扰因素的排除等是实现铀、钚分离的关键。
☞从图5-14可看出,三价钚的萃取能力比四价或六价钚要小得多。
(1)还原反萃剂的选择
●还原剂的选择首先应具有足够的还原能力和较高的选择性。
☞为了达到铀、钚分离的目的,在1B萃取器中,铀必须处于U(Ⅵ),钚必须还原为Pu(Ⅲ)。
☞因而从标准电位来讲(热力学),凡氧化-还原电对的E°,介于E°[U(Ⅵ)-U(Ⅳ)]与E°[Pu(Ⅳ)-Pu(Ⅲ)]之间的还原剂都可以选择性地将Pu(Ⅳ)还原为Pu(Ⅲ)。
☞如Fe2+、U(Ⅳ)及羟胺等均可作为钚的还原反萃剂:
UO22++4H++2e-↔U4++2H2OE°=0.334V
H2O+N2O+6H++4e-↔2NH3OH+E°=0.496V
Fe3++e-↔Fe2+E°=0.771V
Pu4++e-↔Pu3+E°=0.916V
☞当Fe2+作为Pu4+的还原剂时:
Pu4++Fe2+→Pu3++Fe3+
☞当NH2OH·HNO3作为Pu4+的还原剂时:
2(NH3OH)++4Pu4+→4Pu3++N2O+H2O+6H+
2(NH3OH)++2Pu4+→2Pu3++N2+2H2O+4H+
☞当U4+作为Pu4+的还原剂时:
2Pu4++U4++2H2O→2Pu3++UO2++4H+
☞但作为1B萃取器中Pu(Ⅳ)的还原反萃剂,除从热力学上满足上述氧化-还原电位的要求外,就其动力学还应具有还原速度快;在体系中不引入严重影响工艺过程(如对铀、钚产生沉淀、络合等)和腐蚀设备的离子;还原反萃剂本身在工艺过程中稳定性好;容易制备;价格低廉等特点。
☞目前广泛使用的含Fe2+及U(Ⅳ)的还原反萃剂基本上能满足上述要求。
但对Fe2+而言,由于引入了金属离子和反应后生成的具有腐蚀性的离子,从而逐渐被U(Ⅳ)所取代;而在钚线纯化循环,则广泛使用的是硝酸羟胺。
(2)支持还原剂(稳定剂)的使用
●在HNO3溶解铀芯及体系中HNO3的辐射分解过程中均可产生HNO2,在溶解液的调节钚和镎的价态时,还需用NO2-来稳定Pu(Ⅳ)或Np(Ⅴ),因而使水相液流中总有NO2-存在。
☞虽然因HNO2的正常分解,在体系中只能保持很低浓度的NO2-;
☞但由于TBP能以很高的分配系数萃取HNO2,形成HNO2·TBP溶剂化物,而由1AP液流带入1B萃取器。
●尽管NO2-在1B萃取器中的浓度很小,但其破坏作用是相当大的。
☞由于它对还原反萃取剂(Fe2+或U(Ⅳ))按下式产生严重的破坏作用:
Fe2++HNO2+H+→Fe3++H2O+NO↑
U4++2HNO2→UO22++2H++NO↑
2NO+HNO3+H2O→3HNO2
上述反应的最终结果是产生更多的HNO2,造成破坏性反应的恶性循环。
☞此外,HNO2对Pu(Ⅲ)氧化为Pu(Ⅳ)还起催化氧化作用。
这是因为在HNO3体系中,由于硝酸根的氧化作用,要使钚保持三价状态是困难的:
3Pu3++4H++NO3-→3Pu4++NO+2H2O
虽然硝酸根的氧化作用的速度较慢,但反应是自催化的,因为形成的NO会产生HNO2,从而大大地增加其氧化速度。
另一方面,由于体系中存在HNO2,而直接导致Pu(Ⅲ)氧化:
Pu3++NO2-+2H+→Pu4++NO+H2O
☞所有这些妨碍Pu(Ⅳ)还原的因素综合作用的结果,将造成钚的内循环甚至积累,严重时可以完全破坏铀、钚分离过程。
☞为了抑制HNO2的破坏作用,需往体系中加入支持还原剂。
它能在Pu(Ⅳ)还原反应进行之前,把体系中存在的HNO2破坏掉。
☞支持还原剂与新生成的HNO2反应,于是就破坏了自催化反应链,因而氧化作用受到阻碍。
为此,与NO2-作用时不应再产生NO2-,而它与NO2-的反应速度要超过NO2-与还原反萃剂或Pu(Ⅲ)的反应速度。
●氨基磺酸根(NH2SO3-)是常用的支持还原剂,它通过下列反应可以有效地破坏NO2-:
NH2SO3-+NO2-→N2↑+SO42-+H2O
●肼(N2H4)也可以起支持还原剂的作用,其反应为:
N2H5++NO2-→HN3+2H2O
HN3+NO2-+H+→N2O↑+N2↑+H2O
●用NH2SO3-作支持还原剂,它与NO2-作用产生的SO42-对不锈钢设备有腐蚀作用,对Pu(Ⅳ)有强的络合作用,而且使高放废液玻璃固化时产生黄色能溶于水的第二相,这些都是它的缺点。
●采用N2H5+作支持还原剂时,它与NO2-反应的中间产物叠氮酸(HN3)在一定浓度范围内有爆炸性(在水溶液中NH3浓度约为4.7mol/l时,即可发生爆炸)。
☞在HNO3溶液中,只要N2H4浓度不超过0.2mol/l,其操作便是安全的。
作为支持还原剂,从总体上来说,肼已取代了氨基磺酸。
●在实际生产过程中,为了减少支持还原剂的用量,可以采取加热、喷入压缩空气等预先破坏HNO2的措施。
(3)还原反萃剂的用量和浓度的确定
●实践表明,对于生产堆乏燃料的后处理,Fe(NH2SO3)2和Fe(NO3)2-肼都是很好的还原反萃剂。
●但对于动力堆或快堆乏燃料,由于钚含量高,如果仍用Fe2+作还原剂则会给体系引入大量的铁离子,使后续工序处理更加困难。
☞因此动力堆或快堆乏燃料的处理,大都采用不引入杂质离子的U(Ⅳ)作还原剂或采用电解还原等其它还原反萃方法。
●当用Fe2+作钚的还原剂时,Fe2+的用量对Pu(Ⅳ)的还原反萃率有很大的影响。
钚的流失量随铁钚比Fe2+/Pu(Ⅳ)(mol数比)的降低而增大。
☞在钚浓度较低时(<2.00×10-3mol/l),钚的损失与铁、钚比的关系如表5-20所示。
表5-20钚损失与Fe2+用量的关系
Fe2+/Pu(Ⅳ),mol数比
水相HNO3浓度,mol/l
钚的损失,%
10
0.5
0.1-0.2
2
0.5
0.2
1.5
0.5
0.4-0.5
1.1
0.5
>1.0
☞为保证钚的还原反萃率,Fe2+/Pu(Ⅳ)比可在10/1至40/1之间选择,通常取15/1左右。
☞一般说来在满足钚的还原反萃率前提下,应尽量减少Fe2+的用量,否则会把过多的亚铁离子带入钚线二循环,在2AF调料把Pu(Ⅲ)转化为Pu(Ⅳ)时,便会消耗更多的NO2-,并且还将增加钚净化循环2AW废液中的铁盐含量以及由上述反应产生的SO42-量,给废液的处理和循环复用带来困难。
☞在Fe2+/Pu(Ⅳ)比确定之后,可根据其它工艺要求选定Fe2+的浓度。
在1BX中通常把Fe2+的浓度定为0.03mol/l左右。
●在用U(Ⅳ)作还原剂时,既要保证Pu(Ⅳ)的还原反萃取,又不要造成铀的同位素稀释,一般取U(Ⅳ)/Pu(Ⅳ)比为3-8。
☞由于U(Ⅳ)能被TBP萃取,所以U(Ⅳ)-