09精密注射成型的关键技术黄步明.docx
《09精密注射成型的关键技术黄步明.docx》由会员分享,可在线阅读,更多相关《09精密注射成型的关键技术黄步明.docx(16页珍藏版)》请在冰豆网上搜索。
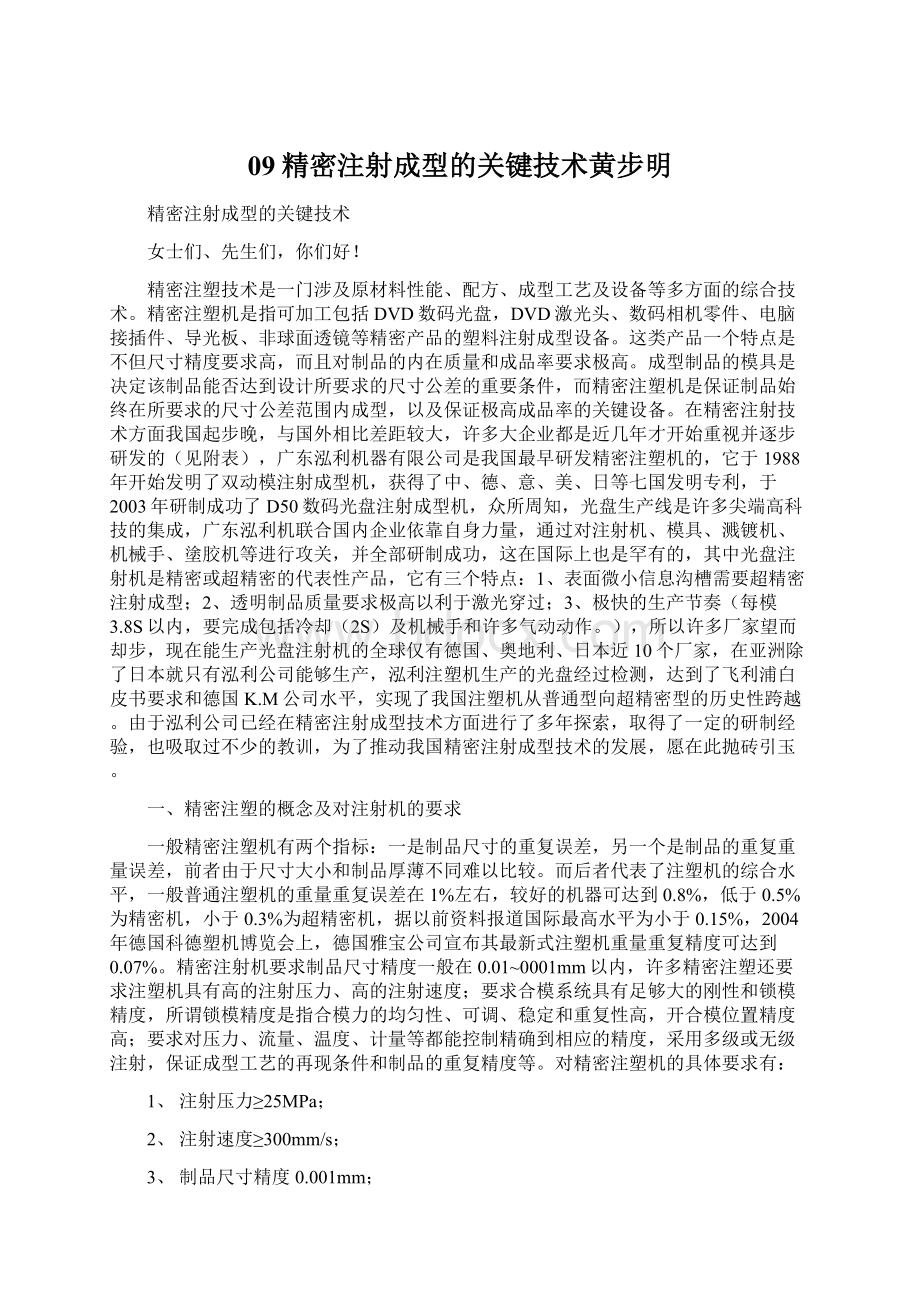
09精密注射成型的关键技术黄步明
精密注射成型的关键技术
女士们、先生们,你们好!
精密注塑技术是一门涉及原材料性能、配方、成型工艺及设备等多方面的综合技术。
精密注塑机是指可加工包括DVD数码光盘,DVD激光头、数码相机零件、电脑接插件、导光板、非球面透镜等精密产品的塑料注射成型设备。
这类产品一个特点是不但尺寸精度要求高,而且对制品的内在质量和成品率要求极高。
成型制品的模具是决定该制品能否达到设计所要求的尺寸公差的重要条件,而精密注塑机是保证制品始终在所要求的尺寸公差范围内成型,以及保证极高成品率的关键设备。
在精密注射技术方面我国起步晚,与国外相比差距较大,许多大企业都是近几年才开始重视并逐步研发的(见附表),广东泓利机器有限公司是我国最早研发精密注塑机的,它于1988年开始发明了双动模注射成型机,获得了中、德、意、美、日等七国发明专利,于2003年研制成功了D50数码光盘注射成型机,众所周知,光盘生产线是许多尖端高科技的集成,广东泓利机联合国内企业依靠自身力量,通过对注射机、模具、溅镀机、机械手、塗胶机等进行攻关,并全部研制成功,这在国际上也是罕有的,其中光盘注射机是精密或超精密的代表性产品,它有三个特点:
1、表面微小信息沟槽需要超精密注射成型;2、透明制品质量要求极高以利于激光穿过;3、极快的生产节奏(每模3.8S以内,要完成包括冷却(2S)及机械手和许多气动动作。
),所以许多厂家望而却步,现在能生产光盘注射机的全球仅有德国、奥地利、日本近10个厂家,在亚洲除了日本就只有泓利公司能够生产,泓利注塑机生产的光盘经过检测,达到了飞利浦白皮书要求和德国K.M公司水平,实现了我国注塑机从普通型向超精密型的历史性跨越。
由于泓利公司已经在精密注射成型技术方面进行了多年探索,取得了一定的研制经验,也吸取过不少的教训,为了推动我国精密注射成型技术的发展,愿在此抛砖引玉。
一、精密注塑的概念及对注射机的要求
一般精密注塑机有两个指标:
一是制品尺寸的重复误差,另一个是制品的重复重量误差,前者由于尺寸大小和制品厚薄不同难以比较。
而后者代表了注塑机的综合水平,一般普通注塑机的重量重复误差在1%左右,较好的机器可达到0.8%,低于0.5%为精密机,小于0.3%为超精密机,据以前资料报道国际最高水平为小于0.15%,2004年德国科德塑机博览会上,德国雅宝公司宣布其最新式注塑机重量重复精度可达到0.07%。
精密注射机要求制品尺寸精度一般在0.01~0001mm以内,许多精密注塑还要求注塑机具有高的注射压力、高的注射速度;要求合模系统具有足够大的刚性和锁模精度,所谓锁模精度是指合模力的均匀性、可调、稳定和重复性高,开合模位置精度高;要求对压力、流量、温度、计量等都能控制精确到相应的精度,采用多级或无级注射,保证成型工艺的再现条件和制品的重复精度等。
对精密注塑机的具体要求有:
1、注射压力≥25MPa;
2、注射速度≥300mm/s;
3、制品尺寸精度0.001mm;
4、制品质量标准差系数(变化率)≤0.1%;
5、开、合模位置精度:
开≤0.03mm,合≤0.01;
6、注射位置精度(保压终止点)≤0.03mm;
7、拉杆受力均衡度≤1%;
8、预塑位置精度≤0.03mm;
9、定、动模板平衡度;A:
锁模力为零时≤0.03mm,B:
锁模力为最大时≤0.005mm;
8、机筒、螺杆温控精度≤±0.5℃。
二、结构特点
下面从注射机的注射装置、合模装置等方面来分析如何实现以上技术要求。
(一)、注射装置
注射装置是精密注塑成型的关键部件,主要作用是为精密注射成型提供塑化均一的熔融物料。
同时,要求其塑化部件的塑化能力强,均化程度高,注射速度高,注射压力高,螺杆的驱动扭矩大,可实现无级调速。
物料的塑化均一是精密注塑成型的基本条件,塑化均一包括物料的熔融速率、混炼温度的稳定性、染色剂的颜色分散性等。
要实现塑化均一,最重要的一环是塑化装置中的螺杆结构和形式。
要求螺杆具有高的剪切能力,以得到高的熔融速度;具有低温塑化能力,以得到高的混炼温度的稳定性;具有在背压低的情况下,高速旋转塑化能力,以得到高的染色剂的颜色分散性。
作为注射装置中最关键的零部件,注塑螺杆的结构和工作特性对物料的塑化过程有着十分重要的影响,它直接影响到注塑机整机的生产效率和制品的质量。
由于各种塑料的性能差异大,为了适应不同性能的塑料加工的要求,将注塑螺杆设计成不同的结构形式。
就塑化能力和功率消耗而言,专用螺杆的性能更为优越。
精密注塑的螺杆主要有分流型螺杆、屏障型螺杆、分离型螺杆变流道型螺杆和减压螺杆等。
精密注塑要求高的注射压力,一般的注塑机的注射压力为147~177MPa,精密注塑机的注射压力为216~243MPa,有些精密注塑机超高压力已达到243~392MPa。
采用高的注射压力是由于以下原因:
1.精密注塑制品的高精度和高质量要求高的注射压力。
注射压力对制品的成型收缩率有明显的影响,当注射压力提高到392Mpa时,制品的成型收缩率几乎为零,而这时精密制品的精度只受模具精度和环境的影响。
由于注射压力的提高,成型材料的压缩性会增加,比容减小;另外,由于制品密度的增加,线性膨胀系数的减小,使得收缩率进一步减小,从而使整个收缩率降低,提高制品的精度。
2.生产流长比更大的制品需要高的注射压力。
精密注塑机可以注塑更薄的制品,薄注塑无论对节约成型材料或缩小精密制品的体积都有很大的好处。
但是,提高注射压力会导致制品内应力的增加,不同注射压力下的制品会出现不同的应力条纹,压力越高应力条纹会越多。
因此必须精确控制精密注塑机的注射压力。
目前,精密注塑成型也朝着高速注射的方向发展。
提高注射速度不仅可以注塑形状复杂的制品,而且对提高制品的尺寸公差起重要作用。
高速注塑成型具有以下几个优点:
1、易于实现超薄壁成型。
注射速度高使得成型材料在极高剪切速率下流动,材料产生剪切热而使粘度降低,同时,材料与流道的低温壁面接触固化时通常形成一个较薄的皮层,使得充模过程中的熔体能保持较长时间的高温,从而使材料的粘度保持在较低的水平,流动性好,可以成型形状复杂、较薄的制品。
2、成型制品具有相当好的外观。
高速注塑,熔体的粘度较低,制品的温度梯度较小,各部分承受的压力较为均匀,所以制品表面的流纹和熔合线较暗,不明显。
3、可成型流动性较差的工程塑料制品。
轻薄短小化是塑料制品的发展方向,对应于薄壁化、轻量化的高速注塑成型技术的开发将变得越来越重要。
可见,高压、高速注射是精密注塑成型的必备条件,高压、高速注射对控制系统提出了更高的要求。
近年来,在精密注塑机方面有采用液压伺服驱动及电伺服电动机驱动两种。
由于采用伺服电机控制螺杆的塑化计量精度较高,转速也较稳定,还可以多级调节。
采用伺服电机带动滚珠丝杆驱动螺杆进行注射时,由于滚珠丝杆负载大,高速旋转造成磨损也较严重。
因此,一般全电动式精密注塑机的注射速度不大于500mm/s。
在注射时用伺服电机起动速度比一般的液压式快,但如果液压式精密注塑机的液压系统采用蓄能器时,将比伺服电机启动更快,伺服电机对注射速率及位置的控制都较准确,但进入保压时由于伺服电机不能在不旋转的情况下提供大的扭矩,所以只能间断地旋转,靠测量螺杆前面物料压力进行补压。
这样,一方面滚珠丝杆容易磨损,另一方面也较为耗能,压力也不稳定,另外,要将伺服电机的旋转运动变成注射的直线运动,注塑压力很大,磨损也较大,对于这一点,许多厂家还没有很好地解决办法。
(二)、锁模装置
1.精密注塑成型对锁模装置的要求
①.对于精密注塑而言,注射压力高,有的高达415MPa,这就要求精密注塑机的锁模结构具有足够的刚性和锁模力,但不是锁模力越高越好,它要求锁模力可以控制、稳定、重复性高,它还要求有高的开、合模精度,主要是开、合模终止点的位置精度和模板的平衡度等,它涉及锁模结构、拉杆、动定模板和合模构件的尺寸、材料、热处理方式以及机加工精度和装配精度等。
②.对低压模具保护以及合模力的大小要精确控制。
一般精密注塑成型所需的模具价格十分昂贵,锁模装置应尽量减少对模具的损害;合模力的大小直接影响模具的变形程度,从而影响制品的精度。
这要求动模板和定模板都要具有足够的刚性,对于精密注塑成型,一般要求动定模板与模具接触面的变形≤0.1mm,甚至更小。
③.合模机构的工作效率要高,开合模速度要快(一般达到40m/min左右)。
为了达到这个目的,要求合模结构更加合理,在满足结构刚性的条件下,尽量减少运动部件及其质量,减少运动惯性,有利于实现高速开合模,降低能耗。
2.锁模结构一般有:
传统肘杆式、传统单缸充压式、四缸直锁二板式以及全电动式。
⑴.肘杆式锁模结构(如图1所示)的优点是:
速度快、能耗低、液压系统简单、成本低。
缺点是:
a.结构复杂、易磨损、开合模精度差。
图1肘杆式锁模结构
b.加工精度要求极高,在成型过程中无法保证L2与L4、L3与L5、L1与L6相等,使得模板受力不均,不能成型精密产品。
c.需要复杂的调模结构和润滑系统、开合模行程短,而且销轴等磨损后造成的受力不均,会加速机器损坏,例如:
销轴和拉杆断裂、模板开裂、调模螺母咬死等。
⑵.传统单缸充压式
传统单缸充液式(如图2所示)的优点是:
开合模精度高、模板受力均衡、不需调模、不需加油润滑、磨损较少、开合模行程长。
图2单缸充液式锁模结构
缺点是:
容易内泄造成升压时间长、爬行、甚至让模、速度慢、漏油、能耗高、容易造成液压冲击、液压系统复杂、成本高、大油缸加工困难。
⑶.四缸直锁二板式
图3是泓利公司研发并投入批量生产的四缸直锁二板式锁模结构的结构简图。
如图所示,四缸直锁二板式锁模结构的四根锁模活塞杆穿过动模板,并固定在定模板和后支架上,活塞固定在活塞杆上,四个油缸套在活塞杆上并固定在动模板上,两个移模油缸安装在动模板与后支架之间,移模油缸使动模板作开合模动作,高压油一起进入四个油缸完成高压锁模动作。
四缸直锁二板式锁模结构的性能分析:
图3四缸直锁二板式锁模结构
①.由于此结构的拉杆中部受力,封闭力线短,受力零件少,有效提高了锁模刚性,减少疲劳破坏。
②.移模油缸与锁模油缸分开,有效解决了锁模力与移模速度的矛盾,同时解决了直压式锁模结构存在的问题:
a.运动中力的平衡;b.由于锁模油缸大,要解决升压时间长和卸压冲击的问题;c.充压阀的内泄漏;d.四根活塞杆的磨损及漏油。
图4四缸直锁二板式锁模力变化示意图
③.锁模力通过电脑准确设定,而且可以从锁模油缸中的压力传感器直接将信号传给电脑,不受环境温度等因素的影响,重复精度高。
四缸直锁二板式的锁模力可以随注射压力(如图4中曲线1)的升高而升高1.5倍,锁模力(如图4中曲线2)与胀模力同步变化,并且维持平衡状态,避免模具因长时间受高压而导致疲劳破坏,同时有利于提高制品的精度。
图中曲线3表示肘杆式锁模结构的变化线,在整个充模过程中,锁模力一直保持最大值,这易造成模具的疲劳破坏。
当注射结束后锁模力随之下降至系统压力在冷却过程中则保持一定的低压力。
图5全电动式锁模结构
④.锁模力随注射压力反馈控制,在注射保压完毕时锁模力降至原来的30%,在开模前逐步降至零,有效取消制品的内应力,避免了开模时产生震动,保证制品的光洁度。
⑷.全电动式
全电动式锁模结构仍采用肘杆式合模结构(见图5),不同的是其开合模动作是由伺服电机代替原来的移模油缸进行驱动,其余的模厚调整及顶针也由伺服电机驱动。
因此,开合模位置精度高,锁模力控制较普通肘杆式准。
全电动式锁模系统的主要优缺点
目前的全电动式精密注塑机的锁模系统是伺服电机取代原来的油缸推动肘杆作开合模运动。
这使原来肘杆式结构所存在的问题继续存在,如加工精度要求高,易磨损,调模难等;但有些方面得到一定的改善,由于使用伺服电机,可以使肘杆在不同的角度停下来,有利于锁模力的改变,并可进行压缩成型。
而且由于没有油压惯性的影响,所以噪音较低,控制精度较高,不过,它也带来一些新的问题:
1)由于用伺服电机带动滚珠丝杆,因此滚珠丝杆的磨损会导致精度的下降。
2)如果机器的制造装配精度不高或模具安装平面不平行,那么在滚珠丝杆上就会出现一个附加的径向力,加速滚珠丝杆的磨损。
3)如果肘杆未完全撑直就开始注射,当成型面积较大的制品时就有很大的轴向力作用于滚珠丝杆及伺服电机的轴上,超载时就有可能导致它们的损坏。
三、关键技术要求及控制
(一)锁模力的控制
锁模力的控制精度影响了制品的尺寸精度,对于全液压式而言,其锁模力
可以由锁模油缸中的压力设定,所以可调并准确,其精确度主要取决于压力传感器的精度和压力控制阀的精度。
伺服电机驱动合模装置,由于合模力也是由机构变形获得的,但因为驱服电机可实现精确的位置控制,相当于控制了终止角α1,而α0也可以很准确,所以也比较准确,肘杆式的锁模力是很难调节的,不准确而且易随环境而变化。
(见表一)
单缸充液式
肘杆式
全电动式
四缸直锁二板式
锁模油缸压力经压力传感器直接将信号传给电脑,不受环境因素等影响
1.靠整个系统发生刚性变形产生锁模力,调模机构影响锁模力,最终无法测量2.初始α0只有3.5°~5°终止角>0°初始角越大,终止角越小,锁模力越大。
且无法保证两边肘杆的初始角和终止角相同
同肘杆式
同传统液压式
表一、锁模力形成方式比较
(二)拉杆受力均衡性控制
对于肘杆式而言,要保证四条拉杆受力是很困难的,唯一办法是在装配中使拉杆两端受力点一致,一段需要测量拉杆的应变进行调整,这是很困难的,而且随着外部环境变化,也会改变,如调模螺再松动等,见表二
单缸充液式
肘杆式
全电动式
四缸直锁二板式
夹紧模具用上图方式,后模板、拉杆乃至整个系统均受力变形,刚性差
同单缸充液式
同肘杆式
类似于4根螺栓将模具夹紧,受力零件少,刚性好
表二、拉杆受力均衡性控制的比较
(三)、模具受力均衡性比较
在相同锁模力下、不同锁模结构所形成的作用在模具上四个角上的力是不同,这是形成制品尺寸误差的最主要原因,见表三:
单缸充液式
肘杆式
全电动式
四缸直锁二板式
锁模力作用在动模板的中心,其反作用力作用再定模板的四个角上。
1.四条拉杆受力可能因受力长度不同而不均匀。
2.制品投影面积型心必须与机器中心重合,否则制品厚薄不均。
A=B1+B2+B3+B4;B1≠B2≠B3≠B4≠A/4
如图,锁模力通过机铰作用在动模板的两个边缘上,反作用力B作用在定模板的四个角上1.四条拉杆受力不均,B1≠B2≠B3≠B4;2.A1≠B1+B3,A2≠B2+B4;3.动模板的变形大于定模板的变形
4.B≠1/2A
同肘杆式
1.A作用在动模板的四个角上。
2.A1=A2=A3=A4,A1=B1,A=B
3.B1=B2=B3=B4。
表三、模具受力均衡性比较
(四)、模具自适应夹紧形成分析及锁模力控制
模板平行度对于开合模很重要,它主要影响模具启闭过程的顺畅性和平稳性,对精密模具的保护起了很大的作用,它是合模装置加工精度和装配精度的综合性指标,但对夹紧模具及精密成型帮助不大;相反,对精密成型影响大的是,高压锁模时,模具的夹紧方式及受力均匀性,对肘杆式而言,它主要是靠位置将模具闭合,所以,其锁模力是间接的,而全液压式(特别是四缸直锁二板式)则可以自动调节位置自适应。
(见表四)
单缸充液式
肘杆式
全电动式
四缸直锁二板式
同四缸直锁二板式
L1与L2由于各种原因,是绝对不可能相等的。
即使模具的精度做得很好,但模板不平行,肘杆长短不一及销轴磨损等原因,也会导致模具闭合不好而出现制品误差,出现飞边,假如加大锁模力,模具即产生变形,飞边解决了,但制品精度无法保证,而且会降低模具寿命。
同肘杆式
若模具有适量平行度误差, 如图所示,则模具刚合上时,F1、F5实际上是未能完全抵销的,F1会继续往前压,直至模具合严,结构在间隙范围内会有适度的摆动,实现自适应。
表四、模具自适应性分析
(五)四种锁模结构在低压护模方面的比较(见表五)
单缸充液式
肘杆式
全电动式
四缸直锁二板式
会产生虹吸现象,动模板在负压下反弹
其低压保护区与力的放大区非常接近,要实现低压护模的区域锁模力变化较大,即使我们在试模时设定了理想的状态,但往往由于系统惯性,肘杆长短不一等综合因素,在实际生产中是无法实现的,在模具即将夹紧时,如果夹到浇口料、嵌件等异物,必然对模具造成较大的损害。
同肘杆式,但通过伺服电机可较好的控制
不存在力的放大区,低压护模区的大小可以通过电脑给定,没有系统液压式结构内泄漏及吸真空造成的爬行现象,有效实现低压护模,甚至用一条棉线即可进行监测
从表中可以看到,四缸直锁二板式的低压护模效果最好,全电动式由于可以控制肘杆的停止位置,也就可以得到很好的护模效果,单缸充液式要消除油中的水份及气泡,减少爬行,这些对精度成型都很重要。
表五:
锁模结构在低压护模方面的比较
(六)、各种结构开模过程对模具的影响
由于精密制品的模具复杂,制品有些部位壁厚极薄,所以,开模中的震动会导致制品开裂,这也是精密不可忽视的因素。
(见表六)
单缸充液式
肘杆式
全电动式
四缸直锁二板式
同四缸直锁二板式
由于开模前型芯的变形,开模时型芯在锁模力下降时因弹性而复位,这时,锁模力突然释放并开模会产生震动力,加剧型芯等受力零件的损坏,而且制品的内应力很大,塑料表面与金属表面的磨擦加剧,进一步损坏型芯,这是制品为何光洁度较差的原因之一。
一般高压锁模时,终止角α>0,但由于脱模力太大(即系统超载),会出现如图所示虚线的状态(即肘杆没有按正常内翻),这时α〈0,同时因制品飞边进一步加大脱模,这时,要开模是相当困难的,即使能开模,十字头往后拉,但模板必须先往前压,这时塑料已冷却变硬,必然对模具造成损害。
而且会给整个系统增加一个附加力,该附加力是使已经处于受最大锁模力时的拉杆进一步受拉,就有拉断拉杆的危险。
同肘杆式
锁模力随注射压力反馈控制,在注射保压完毕,锁模力降至原来的30%,在开模前逐步降至零,有效消除制品的内应力(用手压弹环的例子可做个比喻,手慢慢放开,弹环不会跳起,但若手突然离开,弹环会立刻跳起来),因此,避免了开模时产生震动,保证制品的光洁度,在出现系统超载时,模板会自动后退,不会对系统和模具产生损害。
表六:
开模过程对模具影响的比较
(七)锁模力与模具寿命及制品精度
许多人有错误的认识,认为精密注塑机需要高的锁模力而且锁模力越高越好,这是错误的,锁模力的大小影响了制品的厚度,所以,锁模力要适当,不能太高,要精确控制,对全电动式而言,它是靠伺服电机进行精度控制的,对四缸直锁二板式,它可通过液压系统进行自动调节,达到自锁,即在开始注射阶段,使用较低锁模力,随着充模趋于结束,注射压力升高,锁模力随之升高,这不但可避免模具长时间承受高压,还可排气,减小制品收缩、提高表面光洁度。
(见表七)
单缸充液式
肘杆式
全电动式
四缸直锁二板式
同四缸直锁二板式
---肘杆式机构的锁模力
-四缸直锁结构的锁模力
---注射压力
模具两边受力不均,使模具两边的变形量不同,会导致定位柱受弯、模腔变形,甚至由于模具局部长期超载而造成模具报废。
锁模力只能凭经验给定,往往作用在模具上的锁模力大大超过制品的实际成型力,既耗能又降低了模具的寿命。
由于自锁原理,模具由注射开始至开模的全过程都受高压,模具寿命大大缩短,如上图虚线所示。
通过伺服电机,锁模力得到调节
模具受力均匀,并以模具分型面为定位,锁模力随注射压力反馈控制,既节能又能有效保护模具。
如右图所示,在注射保压结束后,锁模力随注射压力的降低而降低至原来的30%左右,开模前降至零,大大缩短了模具受高压的时间。
表七:
不同锁模结构对模具寿命的影响
(八)注射速度和注射压力的控制
一般注塑机都有多级注射速度和注射压力可供选择。
事实上,如果注射速度低,行程长,不采用闭环控制还有一定意义;如果注射速度快,行程短(这些正是精度制品的特点),用开环是很难进行多级注射的,所以必须采用闭环控制。
闭环控制必须有高速大容量电脑、高精度位移传感器、伺服阀或伺服电机,其中伺服阀有电子式、喷嘴式、挡板式三种,许多厂家将高速比例阀称为比例伺服阀或伺服阀,但在控制精度上是有差异的,目前也有一些厂家将带反馈比例变量泵称为伺服泵,这种泵价格较低,控制精度比较低,伺服电机有直接驱动和皮带传动两种,虽然直接驱动的精度高些,但带来了一些新的问题。
注射压力的控制关键在保压点的控制。
(九)塑化系统的控制
塑化关系到制品的内在质量,主要是背压的控制以及塑化速度的稳定性等,一般采用开环控制就能达到较好效果。
(十)注射压缩成型
注压成型对许多产品是有利的,在减少气泡、真空泡、减小收缩变型、减小能耗方面有很大作用,全液压式可方便实现注压成型,全电动式也很方便,关键点是注射量的控制要准确。
四、精密注塑机的发展动向
全电动式注塑机有一系列优点,特别是节能和在动作精度上。
但由于目前的全电动式注塑机采用肘杆式锁模,一方面限于机械加工精度,另一方面是肘杆的机械磨损,故全电动式注塑机在开合模精度及使用寿命上是不如全液压式的;另一方面,一些保压时间很长的产品,或者注射速度要求很高的产品,用全电动式也不适合;再次,全电动式寿命低也是限制其使用的原因之一。
而全液压式注塑机要保证精度就必须采用伺服控制,而伺服阀价格昂贵带来成本上升,使带有伺服阀的全液压式注塑机的价格高于全电动式的。
电动/液压式注塑机是一种集液压和伺服电驱动于一体的新型注塑机。
它融合了全液压注塑机高性能的优点和全电动注塑机节能的优点。
电动/液压相结合的复合式注塑机已成为当今精密注塑机发展的新动向。
电液复合式注塑机目前主要有以下几种形式:
(1)计量/塑化采用伺服电机驱动,螺杆的往复运动/注射由液压系统完成,锁模采用液压式机构。
事实上,将液压机中耗能较多的塑化加工由电驱动,塑化加工需要旋转运动,用电驱动很易实现,其效率高、节能。
(2)计量/塑化及注射均采用伺服电机驱动,锁模采用伺服电机和肘杆式机构,液压系统采用带蓄能器及变量泵的增压装置,可达到高速、较高的精度和节能的效果,在加工薄壁制品时有利。
(3)电动/液压复合的锁模机构。
采用两组伺服电机加滚珠丝杠的动模驱动装置,取代原来的一对液压油缸进行开合模动作。
在后模板上装有一个大的锁模油缸,锁模油缸活塞杆的一端固定在动模板上,另一端的外表面有螺纹,并套穿在锁模油缸的中心孔内。
在锁模油缸上有一对剖开螺母,在动模驱动装置的滚珠丝杠上有一组补油油缸,它连接到锁模油缸上。
该装置还设有一组增压驱动装置,由伺服电机、滚珠丝杠
及增压油缸组成,增压油缸通过阀也连接到锁模油缸上。
在合模过程,对开的螺母打开,动模驱动装置作合模动动,补油油缸对锁模油缸充油。
在锁模过程,对开螺母闭合,增压驱动装置动作,对锁模油缸增压。
这种直压式锁模机构,以极少量的油为媒介,利用伺服电机与螺纹所产生的油压力进行中心锁模,位置对准精确度高、启动停止性能好。
其缺点是结构复杂、成本高。
以上介绍了三种电液复合式结构的注塑机。
我们认为电动/液压复合式结构将是未来注塑机采用的主流结构,相信还有更多的复合式结构即将问世。
现代注塑机将朝着高速高效(这次在上海举办的China plas2002展览会上,日本厂家展出了注塑成型周期为0.61秒的注塑机)、节能、网络化、智能化方向发展,而模内装饰、模内装配、多组分注射和水辅注射将获得更快的发展。
广东泓利机器有限公司黄步明