各类不锈钢的焊接特点.docx
《各类不锈钢的焊接特点.docx》由会员分享,可在线阅读,更多相关《各类不锈钢的焊接特点.docx(12页珍藏版)》请在冰豆网上搜索。
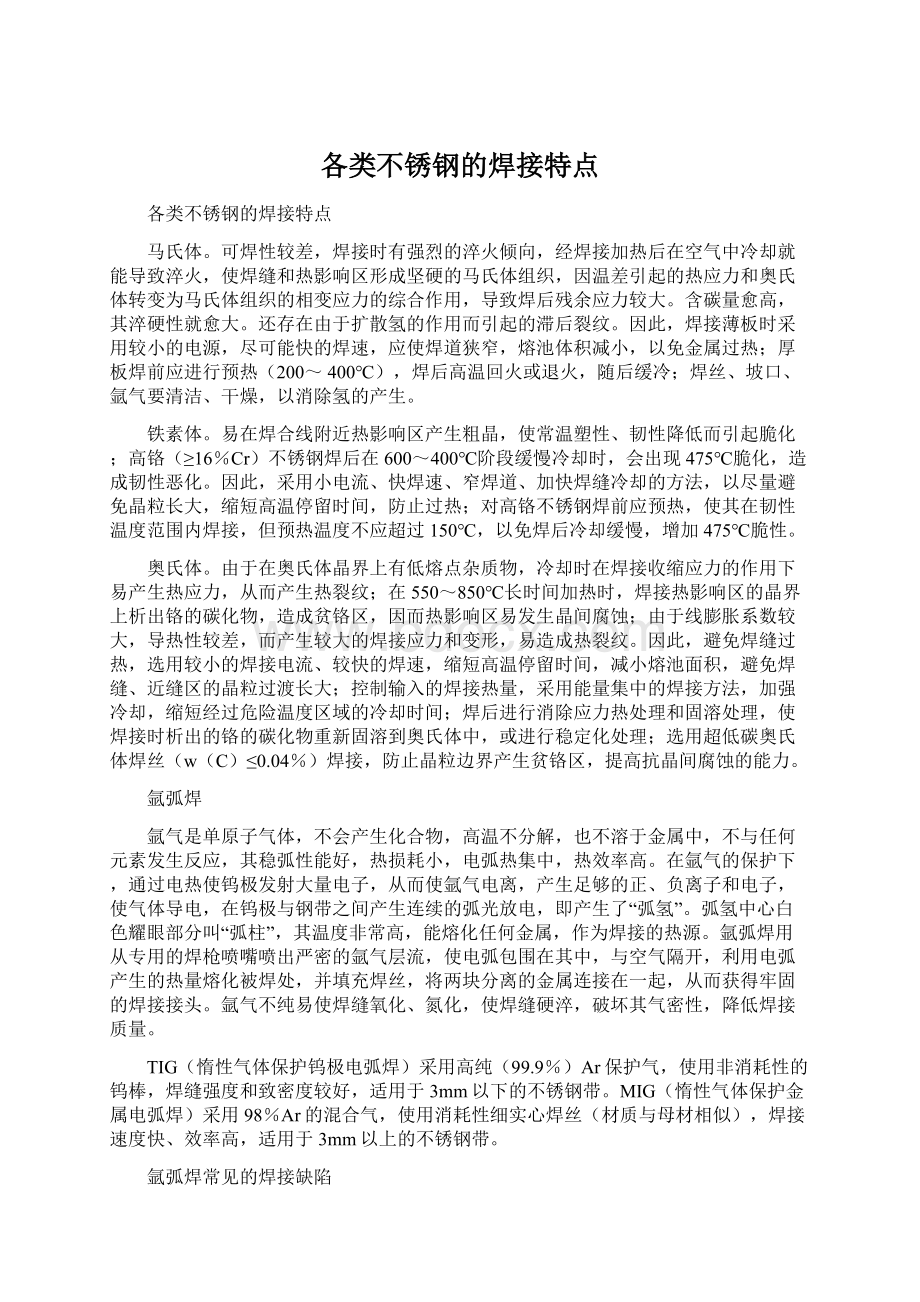
各类不锈钢的焊接特点
各类不锈钢的焊接特点
马氏体。
可焊性较差,焊接时有强烈的淬火倾向,经焊接加热后在空气中冷却就能导致淬火,使焊缝和热影响区形成坚硬的马氏体组织,因温差引起的热应力和奥氏体转变为马氏体组织的相变应力的综合作用,导致焊后残余应力较大。
含碳量愈高,其淬硬性就愈大。
还存在由于扩散氢的作用而引起的滞后裂纹。
因此,焊接薄板时采用较小的电源,尽可能快的焊速,应使焊道狭窄,熔池体积减小,以免金属过热;厚板焊前应进行预热(200~400℃),焊后高温回火或退火,随后缓冷;焊丝、坡口、氩气要清洁、干燥,以消除氢的产生。
铁素体。
易在焊合线附近热影响区产生粗晶,使常温塑性、韧性降低而引起脆化;高铬(≥16%Cr)不锈钢焊后在600~400℃阶段缓慢冷却时,会出现475℃脆化,造成韧性恶化。
因此,采用小电流、快焊速、窄焊道、加快焊缝冷却的方法,以尽量避免晶粒长大,缩短高温停留时间,防止过热;对高铬不锈钢焊前应预热,使其在韧性温度范围内焊接,但预热温度不应超过150℃,以免焊后冷却缓慢,增加475℃脆性。
奥氏体。
由于在奥氏体晶界上有低熔点杂质物,冷却时在焊接收缩应力的作用下易产生热应力,从而产生热裂纹;在550~850℃长时间加热时,焊接热影响区的晶界上析出铬的碳化物,造成贫铬区,因而热影响区易发生晶间腐蚀;由于线膨胀系数较大,导热性较差,而产生较大的焊接应力和变形,易造成热裂纹。
因此,避免焊缝过热,选用较小的焊接电流、较快的焊速,缩短高温停留时间,减小熔池面积,避免焊缝、近缝区的晶粒过渡长大;控制输入的焊接热量,采用能量集中的焊接方法,加强冷却,缩短经过危险温度区域的冷却时间;焊后进行消除应力热处理和固溶处理,使焊接时析出的铬的碳化物重新固溶到奥氏体中,或进行稳定化处理;选用超低碳奥氏体焊丝(w(C)≤0.04%)焊接,防止晶粒边界产生贫铬区,提高抗晶间腐蚀的能力。
氩弧焊
氩气是单原子气体,不会产生化合物,高温不分解,也不溶于金属中,不与任何元素发生反应,其稳弧性能好,热损耗小,电弧热集中,热效率高。
在氩气的保护下,通过电热使钨极发射大量电子,从而使氩气电离,产生足够的正、负离子和电子,使气体导电,在钨极与钢带之间产生连续的弧光放电,即产生了“弧氢”。
弧氢中心白色耀眼部分叫“弧柱”,其温度非常高,能熔化任何金属,作为焊接的热源。
氩弧焊用从专用的焊枪喷嘴喷出严密的氩气层流,使电弧包围在其中,与空气隔开,利用电弧产生的热量熔化被焊处,并填充焊丝,将两块分离的金属连接在一起,从而获得牢固的焊接接头。
氩气不纯易使焊缝氧化、氮化,使焊缝硬淬,破坏其气密性,降低焊接质量。
TIG(惰性气体保护钨极电弧焊)采用高纯(99.9%)Ar保护气,使用非消耗性的钨棒,焊缝强度和致密度较好,适用于3mm以下的不锈钢带。
MIG(惰性气体保护金属电弧焊)采用98%Ar的混合气,使用消耗性细实心焊丝(材质与母材相似),焊接速度快、效率高,适用于3mm以上的不锈钢带。
氩弧焊常见的焊接缺陷
焊缝不合要求。
因焊接工艺参数选择不当,或操作技术不熟练,导致焊缝高低宽窄不一,焊缝成形不良,背面焊缝下凹。
造成焊缝减弱过多,使焊缝强度不够;焊缝过高,造成应力集中,易形成裂纹。
烧穿。
因焊接电流过大,熔池温度过高,焊丝加入不及时,带钢对接间隙过大,焊接速度过慢等,导致焊缝上出现单个或连续的穿孔。
使焊缝强度减弱,易引起引力集中和裂纹。
未焊透。
因电流过小,操作不熟练,焊接速度太快,对接间隙小,电弧过长或电弧未对准焊缝等,导致焊丝与基体金属未熔合在一起或焊接金属中局部未熔合。
该部位应进行补焊。
裂纹。
液体金属在凝固过程中或略低于固相线温度下,产生沿晶间边界的、断口上有明显氧化色的热裂纹。
在固态时发生相变,或有扩散氢存在,以及冷却时在过大的焊接收缩应力作用下,而生成的具有穿晶性质的、断口发亮、没有氧化色的冷裂纹。
当选择和使用焊丝不当,焊接时高温停留时间过长,造成氧化、过热和晶粒度过度长大,材料本身杂质较多,或材料本身易淬硬时均易产生裂纹。
气孔。
因熔池在高温时能溶解大量的氢,熔池冷凝时溶解氢的能力显著下降,当熔池冷却过快时氢气来不及跑出熔池,即在焊接内部及表面产生单个或密集的圆形空穴,使焊缝金属的有效截面积减小,降低焊缝的强度,造成应力集中。
在焊件、焊丝表面有油污、氧化皮、铁锈,或在潮湿气氛焊接,或氩气纯度低、含杂质较多,或氩气保护气不良以及熔池高温氧化、飞溅等情况下均易产生气孔。
奥氏体不锈钢的焊接
奥氏体不锈钢在焊接过程中的弹、塑性应力和应变量很大,却极少出现冷裂纹。
焊接接头不存在淬火硬化区及晶粒粗大化,故焊缝抗拉强度较高。
主要问题:
焊接变形较大;因其晶界特性和对某些微量杂质(S、P)敏感,易产生热裂纹。
奥氏体不锈钢的焊接特性:
1.碳化铬的形成,降低了焊接接头抗晶间腐蚀能力。
(1)针对焊缝晶间腐蚀和目材上敏化温度区腐蚀,可采用下列措施加以限制:
a.减少目材及焊缝的含碳量,目材中添加稳定化元素Ti、Nb等元素使之优先形成MC,以避免Cr23C6形成。
b.使焊缝形成奥氏体加少量铁素体的双相组织。
焊缝中存在一定数量的铁素体时,可细化晶粒,增加晶粒面积,使晶界单位面积上的碳化铬析出量减少。
铬在铁素体中溶解度较大,Cr23C6优先在铁素体中形成,而不致使奥氏体晶界贫铬;散步在奥氏体之间的铁素体,可防止腐蚀沿晶界向内部扩散。
c.控制在敏化温度区间的停留时间。
调整焊接热循环,尽可能缩短600~1000℃的停留时间,可选择能量密度高的焊接方法(如等离子氩弧焊),选用较小的焊接线能量,焊缝背面通氩气或采用铜垫增加焊接接头的冷却速度,减少起弧、收弧次数以避免重复加热,多层焊时与腐蚀介质的接触面尽可能最后施焊等。
d.焊后进行固溶处理或稳定化退火(850~900℃)保温后空冷,以使碳化物充分析出,并使铬加速扩散)。
(2)焊接接头的刀状腐蚀。
只发生在含有稳定剂Ti、Nb的奥氏体不锈钢的焊接接头中。
其腐蚀部位在热影响区的过热区,沿熔合线发展,开始宽度仅3~5个晶粒,逐步扩大至1.0~1.5mm。
高温敏化(超过1200℃)使TiC、NbC溶入固溶体,由于碳的扩散能力较强,在冷却过程中将偏聚在晶界形成过饱和状态,而Ti、Nb则因扩散能力低而留于晶体内。
当焊接接头在敏化温度区间再次加热时,过饱和碳将在晶间以Cr23C6形式析出。
为此,可采取如下预防措施:
a.降低含碳量。
对于含有稳定化元素的不锈钢,含碳量不应超过0.06%。
b.采用合理的焊接工艺。
选择较小的焊接线能量,以减少过热区在高温停留时间,注意避免在焊接过程中产生“中温敏化”效果。
双面焊时,与腐蚀介质接触的焊缝应最后施焊(这是大直径厚壁焊管内焊在外焊之后进行的原因所在),如不能实施则应调整焊接规范及焊缝形状,尽量避免与腐蚀介质接触的过热区再次受到敏化加热。
c.焊后热处理。
焊后进行固溶或稳定化处理。
2.应力腐蚀开裂。
可采用下列措施防止应力腐蚀开裂的发生:
a.正确选择材料及合理调整焊缝成分。
高纯铬-镍奥氏体不锈钢、高硅铬-镍奥氏体不锈钢、铁素体-奥氏体不锈钢、高铬铁素体不锈钢等具有较好的抗应力腐蚀性能,焊缝金属为奥氏体-铁素体双相钢组织时抗应力腐蚀性良好。
b.消除或减小残余应力。
进行焊后消除应力热处理,采用抛光、喷丸和锤击等机械方法降低表面残余应力。
c.合理的结构设计。
设备和容器中与腐蚀介质的接触面不能有缝隙,尽可能采用对接接头,结构设计中注意不产生热流集中而引起的局部过热或腐蚀液滞留而局部浓缩等措施,以避免产生较大的应力集中。
3.焊接热裂纹(焊缝结晶裂纹、热影响区液化裂纹)。
热裂纹敏感性主要取决于材料的化学成分、组织与性能。
Ni易与S、P等杂质形成低熔点化合物或共晶,硼、硅等的偏析,将促使产生热裂纹。
焊缝易形成方向性强的粗大柱状晶组织,有利于有害杂质和元素的偏析,从而促使形成连续的晶间液膜,提高了热裂纹的敏感性。
若焊接不均匀加热,则易形成较大的拉应力,促进焊接热裂纹的产生。
防止措施:
a.严格控制有害杂质S、P的含量。
b.调整焊缝金属的组织。
双相组织焊缝具有良好的抗裂性能,焊缝中的δ相可细化晶粒,消除单相奥氏体的方向性,减少有害杂质在晶界的偏析,且δ相能溶解较多的S、P,并能降低界面能,组织晶间液膜的形成。
c.调整焊缝金属合金成分。
在单相奥氏体钢中适当增加Mn、C、N的含量,加入少量的铈、镐、钽等微量元素(可细化焊缝组织、净化晶界),可减少热裂纹敏感性。
d.工艺措施。
尽量减小溶池过热,以防止形成粗大的柱状晶,采用小线能量及小截面焊道。
25-20型奥氏体钢易出现液化裂纹。
可通过严格限制母材的杂质含量及晶粒度,采用高能量密度的焊接方法、小线能量和提高接头的冷却速度等措施,以减小母材过热和避免近缝区晶粒的粗化。
奥氏体焊缝中δ-铁素体的影响
不希望有δ-铁素体的理由
希望有少量δ-铁素体的理由
希望有较多δ-铁素体的理由
a.要求焊缝无磁性,FN=0
b.特殊的腐蚀条件,FN<0.5
c.在特低温度下使用,FN<0.5
d.在高温下使用,FN<0.5
a.抗热裂性能好,FN=5~15
b.在-100~400℃下工作,FN<5~15
c.无特殊化学腐蚀,FN<5~15
a.对抗应力腐蚀有较高的要求,FN=30~75
b.对强度要求较高,FN=30~75
c.对混合组织起一定抵消作用,FN=15~25
超过上述限值的影响
超过上述限值的影响
超过上述限值的影响
a.有磁性
b.选择性腐蚀
c.丧失韧性
d.有析出相
a.FN<5,会出现热裂纹
b.FN>15,丧失韧性
c.FN>15,相析出
d.FN>15,选择性腐蚀
a.FN<30,会降低抗应力腐蚀能力
b.FN>75,韧性降低
c.FN<30,强度下降
d.FN<15,由于组织混合之后出现热裂倾向
4.焊接接头的脆化。
热强钢应保证焊接接头的塑性,防止高温脆化;低温用钢要求具有良好的低温韧性,防止焊接接头发生低温脆断。
18-8型钢焊缝为双相组织时,其拉伸强度、屈服强度与塑性略低于母材,但韧性比母材低得多,故应使焊缝为单向奥氏体组织。
奥氏体焊缝中含有较多的铁素体化元素或较多的δ相时,高温条件下由于δ→σ转变,引起σ相脆化,焊缝的塑、韧性均显著下降,故焊缝中的δ相应小于5%。
当25-20钢焊缝中Cr与Si含量偏上限时,则易沿晶界析出σ相,引起焊接接头脆化,故应适当减少铁素体形成元素,采用较小的线能量,提高冷却速度。
对于已经出现σ相的焊缝,可将焊接接头加热至1050~1100℃,保温1小时后水冷,进行固溶处理,以使σ相重新溶入奥氏体。
5.焊接变形较大。
因导热率低、膨胀系数大,故焊接变形较大,可采用夹具防止变形。
奥氏体不锈钢的焊接方法和焊接材料:
奥氏体不锈钢可用钨极氩弧焊(TIG)、熔化极氩弧焊(MIG)、等离子氩弧焊(PAW)及埋弧焊(SAW)等方法进行焊接。
奥氏体不锈钢因其熔点低、导热系数小、电阻系数大,故焊接电流较小。
应采用窄焊缝、窄焊道,减少高温停留时间,防止碳化物析出,减少焊缝收缩应力,降低热裂纹敏感性。
焊材选择。
焊材成分尤其是Cr、Ni合金元素要高于母材。
采用含有少量(4~12%)铁素体的焊接材料,以保证焊缝良好的抗裂(冷裂、热裂、应力腐蚀开裂)性能。
焊缝中不允许或不可能存在铁素体相时,焊材应选用含Mo、Mn等合金元素的焊接材料。
焊材中的C、S、P、Si、Nb应尽可能低,Nb在纯奥氏体焊缝中会引起凝固裂纹,但焊缝中有少量铁素体可有效避免。
焊后需进行稳定化或消除应力处理的焊接结构,通常选用含Nb的焊接材料。
埋弧焊用于焊接中板,Cr、Ni的烧损可通过焊剂和焊丝中合金元素的过渡得到补充;由于熔深大,应注意防止焊缝中心区热裂纹的产生和热影响区耐腐蚀性的降低;应注意选择较细的焊丝和较小的焊接线能量,焊丝需低Si、S、P。
耐热不锈钢焊缝中铁素体含量应不大于5%。
Cr、Ni含量大于20%的奥氏体不锈钢,需选用高Mn(6~8%)焊丝,焊剂选用碱性或中性焊剂,以防止向焊缝中增Si,以提高其抗裂性能。
奥氏体不锈钢专用焊剂增Si极少,可向焊缝过渡合金,补偿合金元素的烧损,以满足焊缝性能和化学成分的要求。
打磨砂轮片仅能专用于打磨不锈钢,所用的钢丝刷及清除焊渣的工具皆由不锈钢制成,表面不允许暴露在火焰加工处。
短弧焊接,用实芯焊丝作熔化极焊接不锈钢时,保护气体不宜含CO2;而药芯焊丝由于有渣保护,不会因CO2而增加焊缝的含碳量。
不预热。
层间温度应严格控制,要≤150℃。
小焊接线能量。
反面成型的气体保护焊,焊根侧必须用还原气或纯氢保护。
母材熔化量应控制在整个焊缝面面积的35%以下。
含Ti、Nb奥氏体不锈钢建议用超低碳不含稳定剂的填充材料。
因收缩变形大,故在夹紧装置与定位焊上皆应加强。
不允许在工件坡口处有电弧擦伤母材的痕迹。
为确保焊接接头的耐腐蚀性,其表面应呈光亮状,残渣、焊缝的颜色等可通过石英砂轮打磨、酸洗、抛丸、刷洗或抛光去除。
修复焊接前,也应酸洗坡口表面。
应加快焊缝冷却速度。
铁素体不锈钢的焊接
铁素体不锈钢在高温下可能会或根本不出现少量的奥氏体组织,故在焊接热循环作用下可能或根本不出现马氏体组织,焊接后不会出现强度显著下降或淬火硬化问题。
因此,焊接接头的室温强度不是焊接的主要问题;由于热膨胀系数低,故焊接热裂纹和冷裂纹也不是主要矛盾。
但焊接接头的塑、韧性降低,即发生脆化,以及耐腐蚀性必须重视。
铁素体不锈钢的焊接特性
铁素体不锈钢热膨胀系数小,S、P等杂质在铁素体中溶解度大,Si、Nb等是铁素体形成元素,故焊缝结晶时不易形成低熔点共晶,热裂倾向小;焊接热影响区超过临界温度区域形成马氏体的数量极少,故脆硬倾向很小。
由Cr及Al、Nb、Mo、Ti等添加元素来防止在焊接受热过程中形成奥氏体,故在焊后冷却过程中不会出现奥氏体向马氏体转变的脆硬现象。
但焊接热所形成的热影响区近缝带,由于高温而促成铁素体晶粒粗大,明显降低了接头韧性,且无法通过热处理加以改善。
因同质焊缝及热影响区在焊接过程中C、N化合物析出和晶粒长大的作用,导致铁素体不锈钢焊接接头脆化。
由于C、N在铁素体不锈钢中的溶解度极低,在950℃以后迅速析出,故同质焊材的焊缝和热影响区在焊后冷却过程中会析出C、N化合物,引起脆化,提高晶间腐蚀敏感性。
铁素体不锈钢在热影响区产生晶间腐蚀的部位更接近熔合线。
Cr在铁素体不锈钢中的扩散速度远比在奥氏体不锈钢中的快,只需700~900℃范围内短时间保温即可使Cr向贫铬区扩散,恢复焊接接头的耐腐蚀性能。
铁素体不锈钢的焊接方法
焊接材料。
要求焊缝金属与母材有相同的导电、导磁及力学性能和表面色泽时应使用同材质的焊材,但其熔敷金属韧性太低,添加的Al与Ti等铁素体形成元素难以有效过渡到熔池中去,故该类焊材的应用受到一定限制。
采用奥氏体焊接材料或镍基合金,可提高焊接接头的韧性,免除焊前预热和焊后热处理。
焊接工艺。
焊接材料与母材的化学成分相同时,须采取措施:
焊前预热温度100~200℃,以使被焊材料处于韧性较好的状态和降低焊接接头的应力;随着铬含量的提高,预热温度也应相应提高。
焊后对焊接接头进行750~800℃退火处理,使过饱和C和N完全析出,使铬充分补充到贫铬区,以恢复其耐蚀性及改善焊接接头塑性;退火后应快冷,以防止475℃脆性产生。
采用小的热输入进行施焊,以减少高温脆化和475℃脆性的影响。
若选用奥氏体不锈钢焊接材料,可免除焊前预热和焊后热处理;不含稳定元素的铁素体不锈钢焊接接头,其热影响区的粗晶脆化和晶间腐蚀问题不会因填充材料的改变而变化。
奥氏体或奥氏体-铁素体焊缝金属基本上与铁素体不锈钢母材等强度;但在某些腐蚀介质中,该种异质焊接接头的耐腐蚀性可能低于同质接头。
极低碳高铬铁素体不锈钢薄板焊前可不预热,焊后也无需热处理,但焊缝金属中C加N的含量不高于母材金属含量。
焊接技巧。
焊接材料不得污染;采用小焊接能量、较快的焊接速度等窄焊道焊接;使焊丝受热末端始终处于保护气体中;采用熔化极氩弧焊(MIG)、等离子氩弧焊(PAW)等先进焊接技术;熄弧后继续通保护气体,直至冷却充分;用高纯氩气保护焊接熔池;焊缝背面应采用惰性保护气体;采用水冷铜板,以减少过热,增加冷却速度。
奥氏体-铁素体(双相)不锈钢的焊接
现代超低碳含氮双相不锈钢,钢中的足够的氮可促进焊接接头热影响区在高温下形成的单相铁素体冷却时,发生逆转变并形成足够的奥氏体,故焊接若影响区的塑、韧性较好,且抗应力腐蚀、点腐蚀的性能优良。
其铁素体含量不应超过50%,以防止焊接时热影响区中铁素体过分长大和缩小形成单相铁素体组织的范围。
双相不锈钢冷轧退火时需快速冷却通过980~700℃的温度范围,以防止焊接过程中形成有害的σ相、χ相和碳氮化合物,保证热影响区的力学性能和耐腐蚀性能。
由于焊缝金属凝固和随后的冷却速度很快,焊缝若采用与母材相同的化学成分时,则在高温形成单相铁素体组织,来不及像母材那样在1050~1100℃保温并水淬处理,发生部分铁素体转变为奥氏体的过程。
故焊材的镍含量要高于母材。
焊缝在焊后自然冷却条件下,由于相对于母材熔池体积很小,冷却速度很快,熔化的金属焊缝沿热传导方向,向焊缝中心呈柱状、树枝状结晶,发生合金元素的偏析,组织不稳定,在随后的冷却过程中,易发生组织转变和析出金属间相。
在正常的焊接参数和焊后自然冷却条件下,配套的焊材的焊缝金属可以达到要求的相比例(FN=30~
70%);但采用较小的焊接热输入或焊缝截面厚,焊后冷却速度较快,焊缝中铁素体的转变来不及充分进行,则焊缝中的铁素体可能会超过70%;若热输入过大或填充的焊接材料较少,则可能加大母材的(熔化)稀释作用,从而降低焊缝金属的镍含量,使焊缝中的铁素体含量增高。
若焊缝的铁素体含量较高,可采取固溶(1050~1100℃)处理,使焊缝金属的相比例较为理想。
可用钨极氩弧焊(TIG)、熔化极氩弧焊(MIG)、等离子氩弧焊(PAW)及埋弧焊(SAW)等方法进行焊接。
若焊件处于高应变状态或存在导致耐蚀性和塑、韧性降低的有害相变,则应进行固溶处理。
23%Cr无Mo双相不锈钢和22%Cr双相不锈钢的固溶处理温度为1050~1100℃,而25%Cr双相不锈钢和超级双相不锈钢的固溶处理温度为1070~1120℃。
当匹配的焊缝金属的化学成分(Ni=8~10%)高于焊件化学成分时,应选择给定的温度上限。
快速感应后立即水淬。
保温5~30min,以恢复相平衡,包括金属间相(σ和χ相)的溶解。
需控制焊料飞溅物、杂质、氧化物的形成,以防耐点蚀和缝隙腐蚀性能的下降。
焊后应清洗焊缝及周围区域;若不能清洗,则应控制保护气体的含氧量(10×10-6~25×10-6)。
为了加强熔化极气体保护(GMAW)的电弧稳定性及金属渗透性,可在氩气中添加少量CO2。
焊接材料
MIG不锈钢焊丝较高的Si含量,可使电弧燃烧稳定,熔池流动性好,但表面张力大,从而可减少气孔和飞溅的产生。
埋弧焊只能使用Si含量低的焊丝,以防产生热裂纹。
不锈钢实芯焊丝按焊接方法可分为气体保护焊用焊丝和埋弧焊用焊丝(化学成分与母材大致相同,仅铬、镍含量较母材略高,含碳量较母材略低)。
不锈钢药芯焊丝是薄带钢在卷成圆形或异形管的同时,往里填充一定成分的药粉,经拉制而成的一种焊丝,其具有药皮焊条的配方可调性和CO2焊丝连续焊接的优点。
药芯焊丝按保护气体可分为CO2气体保护、混合气体保护和无保护三种;按有无造渣功能分为“药粉造渣型”和“金属造渣型”两种;按造渣性质分为“钛型(酸性)”、“钛钙型”(中性)和“钙型”(酸性)三种。
此外,一些药芯焊丝仅作为输送合金成分的载体,而无工艺性能方面的要求,配以专门的焊剂或保护气体进行焊接或堆焊(埋弧焊或钨极氩弧焊)。
焊接用钨极的要求:
a.钨极的最大许用电流值要高。
若焊接电流超过许用电流,易使钨极末端熔化而落入熔池,这样会改变焊缝金属的化学成分或产生夹钨缺陷;若钨极末端形成熔球,则位于熔球表面的电弧斑点易收外界因素的干扰而游动,使电弧飘荡不稳,并降低保护气体的保护效果。
钨极的最大许用电流同钨极的化学成分与直径、电流种类与电源极性、钨极伸出导电嘴的长度、外伸长度上产生的电阻热和钨极受冷却的条件。
b.钨极的损耗。
钨极损耗对自动焊过程的稳定性和焊缝成型质量有明显影响。
损耗分为正常损耗与异常损耗。
正常损耗是钨极因热蒸发和缓慢氧化等累计的损耗,与钨极的化学成分、采用的电流种类及电源极性等有关。
因氩弧中的阳极温度和发热量比阴极高,故采用直电流反极性使钨极损耗比交电流时高,而用交电流时的钨极损耗又大于直流正极性接法。
异常损耗发生在多次短路引弧或钨极末端与填充焊丝及熔池接触时,钨极末端被熔化金属所玷污,使熔化温度降低所导致的损耗。
c.引弧及稳弧性能。
由钨极的逸出功大小来决定。
逸出功低,则发射电子的能力就强,引弧和稳弧性能就好。
在钨极中加入一些可降低逸出功的元素(钍、铈、镐等)或其氧化物,即能改善电极的使用性能。
钨极中焊THO,可降低逸出功,故能大大提高阴极发射电子的能力,改善引弧和稳弧性能;可降低对焊机的空载电压值的要求,即引弧电压低;减少阴极发热量,降低电极的损耗,且可增大焊接的许用电流值;但钍具有微量的放射性。
铈钨极在直流小电流焊接时,较钍钨极更易引燃电弧且能减少电极的损耗,放射性剂量也很低。
钨极的磨削。
钨极端部的形状、光洁度及尺寸对焊接许用电流大小、电弧的稳定性和焊缝成型等有直接影响。
若钨极表面粗糙、不同心和尺寸不合适,则产生的电流既不集中又不稳定。
焊接用保护气体
1.氩气(Ar)。
密度比空气大,热导率和比热容比空气小,具有很好的稳弧特性。
用Ar保护进行熔化极焊接时,焊丝金属很容易呈稳定的轴向射流过渡,飞溅极小。
作焊接用保护气体的纯度应达到99.9~99.999%。
因其是分馏液态空气的副产品,故其中的有害杂质是氧、氮及水蒸气。
2.氦气(He)。
氦的电离能较高,故焊接时引弧较困难,电弧引燃特性差,氦弧的电弧电压高,使电弧具有较大的电功率,电弧温度高,传递给焊接的热量较大。
因密度较空气小,故流量要大。
价格昂贵。
3.氢气(H2)。
密度小,热导率大,分解时可吸收大量的分解热,故对电弧有较强的冷却作用。
氩气中加入适量的氢,可增大母材金属的输入热,提高电弧电压及电弧温度,从而提高热功率,增加熔透性且提高焊接速度和生产效率。
氢在弧柱中会吸热分解成氢原子,产生两种相反的作用:
氢原子流到较冷的焊件表面上时,会复合成氢分子而释放出化学能,对焊件起补充加热作用;氢原子在高温时能溶解于液体金属中,其溶解度随温度降低而减少,故液体金属冷却时析出的氢若来不及外逸,则易在焊缝金属中出现气孔、白点等缺陷。
4.CO2(二氧化碳)。
CO2气体纯度要求≥99.5%,含水量≤0.05%。
液态CO2可溶解0.05%的水,多余的水则沉于瓶底。
这些水在焊接过程中随CO2一起挥发并混入CO2中,成为主要的有害杂质。
故需采取措施:
倒置新灌气瓶,开启阀门将沉积在底部的水排出(一般排放2~3次,每次间隔约30min),放水结束后仍将气瓶倒正;因上部的气体含有较多的水分和空气,故使用前先放气2~3min;气路中设置采用硅胶或脱水硫酸铜的干燥器,进一步减少CO2中的水分;当瓶中气压降低到0.1Mpa时不再使用,此时液态CO2已挥发完,气体压力随气体消耗而降低,水分分压相对增大,使焊缝金属产生气孔。
5.混合气体。
混合气体可细化熔滴、减少飞溅、提高电弧稳定性、改善熔深及提高电弧温度。
a.Ar+He。
He的加入量视板厚而定,板越厚加入的He应越多。
该种混合气体可改善熔深及焊缝金属的润湿性。
可用于焊接铁素体不锈钢。
b.Ar+H2。
可用来焊接奥氏体不锈钢、镍及其合金,可抑制和消除镍焊缝金属中的CO气孔。
H2含量须小于6%,焊接双相不锈钢时,H2含量可达10%。
焊接方法
1.TIG(钨极氩弧焊)
钨极氩弧焊借助高熔点的金属钨作为一个电极,工件作为另一个电极,利用氩气(Ar)作为保护气体,并在钨极与工件之间引燃电弧进行焊接。
焊接时