机械制造课程设计说明书主离合器分离叉加工工艺及M10底孔φ11孔工序工装设计.docx
《机械制造课程设计说明书主离合器分离叉加工工艺及M10底孔φ11孔工序工装设计.docx》由会员分享,可在线阅读,更多相关《机械制造课程设计说明书主离合器分离叉加工工艺及M10底孔φ11孔工序工装设计.docx(30页珍藏版)》请在冰豆网上搜索。
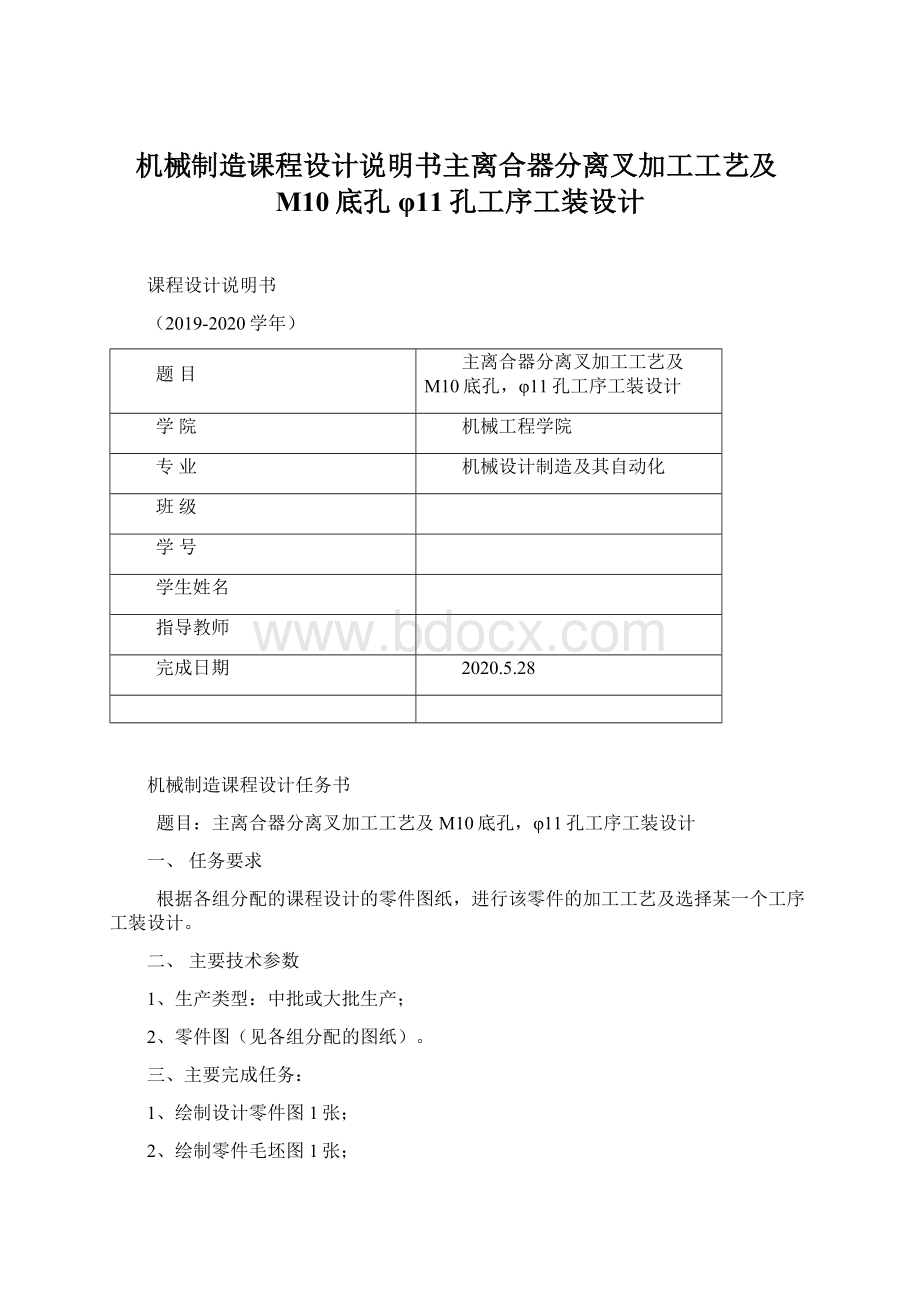
机械制造课程设计说明书主离合器分离叉加工工艺及M10底孔φ11孔工序工装设计
课程设计说明书
(2019-2020学年)
题目
主离合器分离叉加工工艺及M10底孔,φ11孔工序工装设计
学院
机械工程学院
专业
机械设计制造及其自动化
班级
学号
学生姓名
指导教师
完成日期
2020.5.28
机械制造课程设计任务书
题目:
主离合器分离叉加工工艺及M10底孔,φ11孔工序工装设计
一、任务要求
根据各组分配的课程设计的零件图纸,进行该零件的加工工艺及选择某一个工序工装设计。
二、主要技术参数
1、生产类型:
中批或大批生产;
2、零件图(见各组分配的图纸)。
三、主要完成任务:
1、绘制设计零件图1张;
2、绘制零件毛坯图1张;
3、编制零件机械加工工艺1套,绘制综合工艺卡片图样1张;
4、设计某一工序专用夹具(总体结构三维造型,二维工程装配图1张,夹具体零件图1张)
5、编写设计说明书1份(内容包括工艺规程编制、夹具设计)。
四、提交成果
1、相关图纸一套;(电子文档和打印稿各一份)
要求:
符合国家相关规范。
2、课程设计说明书一本。
(电子文档和打印稿各一份)
要求:
内容完整,图表完备,条理清晰,分析有据,计算精确。
五、时间按排
序号
项目内容
参考时间(天)
1
任务布置;查阅相关课题机械制造工艺文献资料;理解设计任务;
1
2
零件图工艺分析,绘制加工零件图;
2
3
绘制零件毛坯图、完成工艺路线编制;
2
4
编制工艺规程,并进行相关计算及某一工序的加工仿真;
5
5
设计、绘制工序夹具二维装配图及三维造型
4
6
设计绘制夹具零件图
2
7
撰写设计说明书
2
8
设计展示与答辩
1
9
设计与说明书完善
2
合计
21
六、注意事项
1、集中时按时进入设计室,注意公共卫生,按学校要求做好防疫;
2、集中时不准用笔在桌子等设施上乱写乱画,否则按零分计;
3、注意安全。
4、按照时间安排的每个节点完成任务,按教师指定时间线上线下答疑、检查。
1零件工艺分析及生产类型的确定
图1-1主离合器分离叉零件图
1.1零件的作用
该零件主要用于离合器和减速器中,起拔动作用,需要承受弯曲应力和冲击载荷的作用,因此该零件应该具有足够的强度,刚度和韧性。
其中φ25的孔用于与轴的联接。
其重要功用是使用两个叉拨动离合器,重要工作表面为φ25孔和其上部键槽,以及叉子内表面,因此这几个部分的精度需要保障。
1.2结构特点
图1-2主离合器分离叉部分图
主离合器分离叉上部有两个叉子并有肋板辅助,下部是一个圆孔并且圆孔的下部开了一个贯通槽。
另外下部左边有一个M10的螺孔,右边有一个φ11的定位槽。
1.3结构工艺性
从零件图上可以看出,标有表面粗糙度的表面有φ25内控,φ25上部和下部的槽,和叉子的两端面和内表面。
图1-3主离合器分离叉部分图
图1-4主离合器分离叉部分图
其中表面粗糙度要求最高的是φ25孔和其下部的槽表面以及叉子的两侧面,为Ra3.2。
该零件硬度要求在170-241HBW,可以通过HT200材料铸造获得。
1.4关键表面的技术要求
加工表面
尺寸偏差/mm
公差/mm及精度
表面粗糙度/um
形态公差/mm
φ25孔
0.13IT11
Ra3.2
两φ25孔同轴度φ0.03
φ25孔上槽侧面
0.145IT12
Ra6.3
键槽对φ25公共轴线的对称度为0.05
φ25孔上槽地面
0.13IT11
Ra6.3
φ25孔下槽侧面
4.5
0IT11
Ra3.2
叉内表面
0.11IT11
Ra3.2
叉端面
0.18IT12
Ra3.2
表1-1关键表面技术要求
由上可知,加工精度最高的是φ25孔,叉头内表面和两侧面。
其中,φ25孔的精度通过扩就可以满足,而叉头内表面可以通过粗铣-半精铣的加工路线满足。
1.5审查工艺性
分析分离叉零件可知,该零件除了φ25孔与下部键槽和叉部内表面和端面外,其余表面加工精度较低,通过铣削,钻削的一次加工就可以达到加工要求。
主要表面加工精度也不是很高,在正常生产条件下可以采用较经济的方法保质保量的加工出来。
由此可见,该零件的工艺性很好。
1.6生产类型
中批生产
2确定毛坯,绘制毛坯简图
2.1选择毛坯
由该零件的功用可知,该零件需要有较强的强度和刚度,为了既能满足要求,价格又相对低廉,因此选择铸铁材料HT200,因此可以确定毛坯的制造形式为铸造。
由于该分离叉为中批量生产,查[2]表5-2可知,应选择砂型铸造机器造型,铸铁件的公差等级为CT9级。
2.2确定加工余量及毛坯尺寸
该分离叉材料为HT200,采用砂型铸造机器造型,且为中批生产。
已确定铸件尺寸公差为CT9级。
由[2]表5-3选择加工余量为H级。
根据机械加工后铸件的最大轮廓尺寸,由[2]表5-4查的各加工表面的加工余量,见下表(单位:
mm):
加工表面
单边余量
双边余量
备注
φ25孔
2
4
基本尺寸取孔轴向长度72mm
叉口两侧平面
1.7
3.4
基本尺寸为叉厚度72mm
叉口槽内表面
1.7
3.4
基本尺寸为叉厚度72mm
表2-1表面加工余量
加工表面的毛坯尺寸只需要将零件尺寸加上查取的相应加工余量即可,毛坯尺寸如下表(单位:
mm):
零件尺寸
单边加工余量
毛坯尺寸
φ25
2
φ21
16
1.7
19.4
14
1.7
10.6
表2-2毛坯尺寸
由[2]表5-1查的各铸件加工尺寸公差如下表(单位:
mm):
毛坯尺寸
公差
按“对称“标注
结果
φ21
1.7
±0.85
φ21±0.85
17.4
1.7
±0.85
19.4±0.85
8
1.5
±0.75
10.6±0.75
表2-3铸件尺寸公差
2.3绘制铸造毛坯简图
图2-1毛坯图
3拟定工艺路线
3.1定位基准的选择
3.11精基准的选择
φ25mm孔不但是精度要求最高的孔,而且也是该零件的设计基准,装配基准与测量基准。
为避免由于基准不重合而产生误差,保证加工精度,应选择φ25mm孔为精基准,即遵循“基准重合”的原则,同时选择叉头内表面为精基准。
3.12粗基准的选择
φ25孔为重要表面,加工时要求余量小而均匀,因此应该选择φ25长孔为粗基准。
但是因为此零件精度要求不是太高,此时可以选择φ25孔左端面作为粗基准。
3.2各表面加工方案的确定
1,平面的加工
平面的加工有车,刨,铣,磨,拉等。
对于本零件叉口4个平面来说。
其表面粗糙度要求为3.2,加工精度较高,所以选择半精铣(先粗铣,再半精铣)加工方式以获得所需表面粗糙度。
而对于叉头内表面也可以用半精铣获得加工要求。
2,螺纹加工
2×M10螺纹采用丝锥攻螺纹加工方式。
在攻螺纹工序之前应设置一道倒角工序,或在本工序中先设一道倒角工步,以免折断丝锥,使攻螺纹顺利进行。
3,孔及退刀槽的加工
孔的加工方式有很多,比如钻,扩,镗,拉,磨等。
对于已铸出φ25mm孔的毛坯,可采取在车床上镗孔(粗镗->半精镗)的方式。
原因之一是该零件的结构紧凑,质量也不大,适用于车削加工;原因之二是该零件精度不高,使用车床镗孔较为经济。
而对于φ11mm的孔,可以考虑先钻然后扩的加工方式(或者在毛坯上预铸孔,然后再扩孔也可以满足)。
而扩孔可以考虑使用麻花钻当扩孔钻使用。
由[2]表5-12知,钻孔的公差等级为IT12-IT13,可以满足加工要求,故这里使用锥柄麻花钻进行扩孔。
3.3确定工艺路线
由于本零件是中批生产,其特点是尽量选用通用机床并配以专用夹具。
在安排本零件工艺路线的过程中主要考虑了以下几个方面。
以此提出以下两个工艺路线方案:
方案一:
工序05:
扩2×φ25孔
定位基准:
φ25孔加外表面
工序10:
锪φ25孔两端倒角
定位基准:
锪右边倒角用左边毛坯孔加左端面,锪左边倒角用右边毛坯孔加右端面
工序15:
粗铣四个叉口平面
定位基准:
2×孔φ25及外表面
工序20:
精铣四个叉口平面
定位基准:
φ25孔和外表面
工序25:
粗铣两个叉口槽
定位基准:
2×孔φ25外表面
工序30:
精铣两个叉口槽
定位基准:
φ25孔和外表面
工序35拉键槽
定位基准:
叉头内表面和侧面
工序40:
检验同轴度
工序45:
钻2×M10底孔
定位基准:
2×φ25轴线,叉头内表面
工序50:
攻2×M10螺纹孔
定位基准:
2×φ25轴线,叉头内表面
工序55:
钻2×φ11孔
定位基准:
2×φ25轴线,叉头内表面
工序60:
切槽
定位基准:
2×φ25孔外表面,叉头内表面,2×φ25孔左右端
工序65:
去毛刺,清洗
工序70:
检验
方案二:
工序05:
扩2×φ25孔
定位基准:
φ25孔加外表面
工序10:
锪φ25孔两端倒角
定位基准:
锪右边倒角用左边毛坯孔加左端面,锪左边倒角用右边毛坯孔加右端面
工序15:
粗铣四个叉口平面
定位基准:
2×φ25及外表面
工序20:
精铣四个叉口平面
定位基准:
φ25孔和外表面
工序25:
粗铣两个叉口槽
定位基准:
2×φ25外表面
工序30:
精铣两个叉口槽
定位基准:
φ25孔和外表面
工序35拉键槽
定位基准:
叉头内表面和侧面
工序40:
检验同轴度
工序45:
切槽
定位基准:
2×φ25孔外表面,叉头内表面,2×φ25孔左右端
工序50:
钻2×M10底孔
定位基准:
2×φ25轴线,叉头内表面
工序55:
攻2×M10螺纹孔
定位基准:
2×φ25轴线,叉头内表面
工序60:
钻2×φ11孔
定位基准:
2×φ25轴线,叉头内表面
工序65:
去毛刺,清洗
工序70:
检验
比较以上两种加工方案,可知不同主要在于切槽和钻φ11孔的顺序,如果先钻孔后切槽,则可能后面切槽的时候会对钻的孔以及M10L螺纹造成破坏,而先切槽再锥螺纹则不会产生这种情况。
因此我们选择方案二作为我们最终的加工工艺路线。
3.4机床设备及工艺装备的选用
1,选择加工设备
选择加工设备即选择机床类型。
由于已经根据零件形状,精度特点,选择了加工方法,因此机床的类型也随之确定。
至于机床的型号,主要取决于现场的设备情况。
因铸铁硬度不是太大,普通机床均能满足要求,所以不用校核机床效率。
结合加工设备要考虑加工精度,初步选定各工序机床如下:
工序05,10扩孔,倒角:
Z35摇臂钻床,主要技术参数见表5-14;
工序15,20,25,30铣平面:
XA5032立式升降台铣床,主要技术参数见[2]表5-14;
工序35拉键槽:
拉床
工序50,55,60钻孔攻螺纹:
Z3025摇臂钻床;
工序65:
铣开:
XA6132卧式铣床,主要技术参数见[2]表5-13;
2,选择夹具
对于成批生产的零件,大多采用专用机床夹具。
在保证质量,操作方便,满足高效的前提下,也可部分采用通用夹具。
本机械加工工艺规程中所有工序均采用了专用机床夹具,需专门设计制造。
3,选择刀具
(1)钻头
从零件要求和加工经济性考虑,采用锥柄麻花钻头(GB1438.1-2008)完成加工工序。
05中采用麻花钻扩孔,由[2]表5-19可知,选用d=25mm的高速钢锥柄麻花钻;对于工序10,采用锪钻进行倒角;工序45中,选用φ11mm的麻花钻钻一个φ11mm的孔;工序50中,由[2]表5-20