IPC9701A 表面贴装锡焊件性能测试方法与鉴定要求.docx
《IPC9701A 表面贴装锡焊件性能测试方法与鉴定要求.docx》由会员分享,可在线阅读,更多相关《IPC9701A 表面贴装锡焊件性能测试方法与鉴定要求.docx(30页珍藏版)》请在冰豆网上搜索。
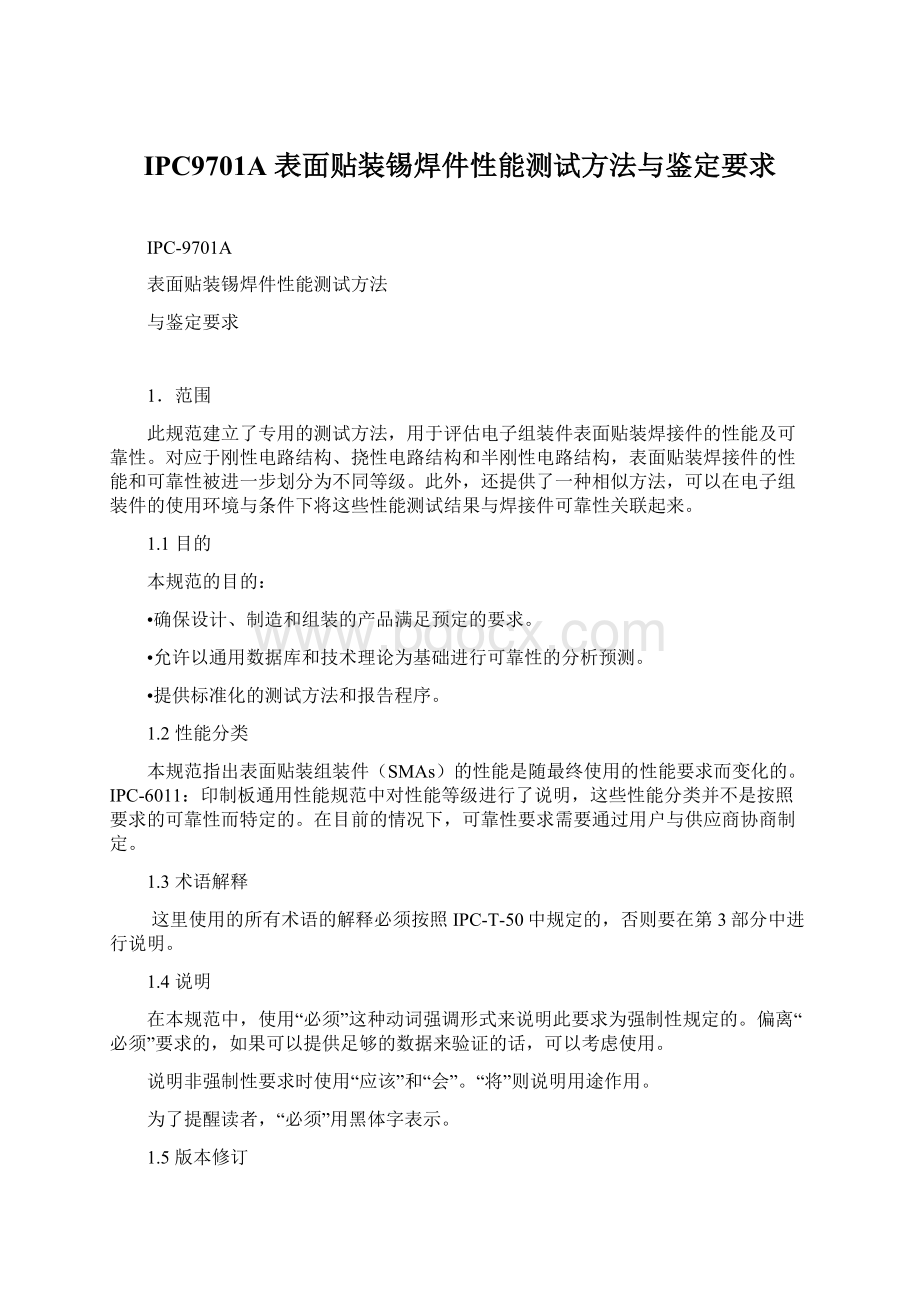
IPC9701A表面贴装锡焊件性能测试方法与鉴定要求
IPC-9701A
表面贴装锡焊件性能测试方法
与鉴定要求
1.范围
此规范建立了专用的测试方法,用于评估电子组装件表面贴装焊接件的性能及可靠性。
对应于刚性电路结构、挠性电路结构和半刚性电路结构,表面贴装焊接件的性能和可靠性被进一步划分为不同等级。
此外,还提供了一种相似方法,可以在电子组装件的使用环境与条件下将这些性能测试结果与焊接件可靠性关联起来。
1.1目的
本规范的目的:
•确保设计、制造和组装的产品满足预定的要求。
•允许以通用数据库和技术理论为基础进行可靠性的分析预测。
•提供标准化的测试方法和报告程序。
1.2性能分类
本规范指出表面贴装组装件(SMAs)的性能是随最终使用的性能要求而变化的。
IPC-6011:
印制板通用性能规范中对性能等级进行了说明,这些性能分类并不是按照要求的可靠性而特定的。
在目前的情况下,可靠性要求需要通过用户与供应商协商制定。
1.3术语解释
这里使用的所有术语的解释必须按照IPC-T-50中规定的,否则要在第3部分中进行说明。
1.4说明
在本规范中,使用“必须”这种动词强调形式来说明此要求为强制性规定的。
偏离“必须”要求的,如果可以提供足够的数据来验证的话,可以考虑使用。
说明非强制性要求时使用“应该”和“会”。
“将”则说明用途作用。
为了提醒读者,“必须”用黑体字表示。
1.5版本修订
对IPC-9701做了些改变,包括附录B——建立了无铅焊点的热循环要求准则。
附录B还为目前的IPC-9701提供了有关使用无铅锡焊工艺时的补充要求。
2.适用的文件资料
下面是适用的文献标准以及这些文件的后续版本和修订部分,都属于本规范的内容。
下列文件标准分为IPC、联合工业标准、ITRI、EIA和其他。
2.1IPC
IPC-T-50电子电路互连及封装的名词术语与定义
IPC-D-279可靠的表面贴装技术印制板组装件的设计指南
IPC-TM-650试验方法手册
2.1.1手动微切片法
2.4.1镀层附着力
2.4.8覆金属箔板的剥离强度
2.4.21.1表面贴装焊接区的粘结强度(垂直拉伸方法)
2.4.22弯曲与扭转
2.4.36金属化孔的模拟返工
2.4.41.2热膨胀系数,应变计法
2.5.7印制线路材料的介质耐电压,
2.6.5多层印制线路板的物理(机械)震动试验
2.6.7.2热冲击-刚性印制板
2.6.8镀通孔的热应力冲击
2.6.9刚性印制电路板振动试验
IPC-SM-785表面贴装锡焊件加速可靠性试验指南
IPC-S-816SMT工艺指南与检验单
IPC-7711/21维修与返工指南
IPC-9252无载印制板电气检测指南与要求
IPC-9501电子元器件的PWB组装工艺模拟评估
IPC-9502电子元器件的PWB组装锡焊工艺指南
IPC-9504非集成电路元器件组装工艺模拟评估(预处理非集成电路元器件)
2.2联合工业标准
J-STD-001电气和电子组装件的焊接技术要求
J-STD-002元器件引脚、端子、焊片、接线柱及导线可焊性试验
J-STD-003印制板可焊性试验
J-STD-020塑料集成电路表面贴装器件湿度/回流灵敏度分类
2.3国际锡研究机构
ITRIPub#580锡与锡合金的金相学
ITRIPub#708电子元器件焊点冶金学
2.4其它出版物
2.4.1电子工业机构
JESD22-A104-B“温度循环”(2000年7月)
JESD22-B117“BGA焊球剪切”(2000年7月)
2.4.2OEM工作组
SJR-01第2版“焊点可靠性测试标准”(2001年2月)
3.术语、定义及概念
3.1概述
为确保组装到电路板上的表面贴装电子元件焊点的可靠性,要求采用可靠性(DfR)设计步骤(见IP-D-279),在某些情况下通过试验验证使产品适用于特定产品类型和环境。
元器件或组装越复杂,越需要更多的试验来验证可靠性。
在使用过程中,表面贴装焊接件可能会受各种加载条件影响,可能会导致过早失效。
基本的设想就是将焊点适当地润湿,在焊料、元器件底层金属与印制线路(电路)板(PWB/PCB)之间形成良好的金属粘合。
这样就确保不会由于焊点缺陷而造成早期失效。
下列加载情况可能是单独、连续或同时存在,加起来足以引起SMT焊点失效:
a)热膨胀差
b)振动(运输中)
c)在从焊接操作或从恶劣的使用环境中冷却过程中的热冲击(快速的温度变化引起瞬时翘曲差)。
d)恶劣使用条件或意外误操作造成的机械震动(大加速度)。
安装在电路板上的表面贴装器件的可靠性是焊点完整性与器件/印制板互连的函数。
通过焊接互连由PWB施加给封装的热机械加载可能会导致封装其它部位失效。
在插座上进行的元件级测试不能代表(表明)板上零件加载情况。
对于大批CSP结构和高引脚点BGA封装,大量使用非丝焊芯片模互连会增加在板级测试中“未预料的”内部元器件失效的可能性。
为了确保表面贴装电路组装件的焊点在指定使用环境下满足可靠性预期值,通常需要确定某些特定应用的可靠性,即使已经采取了适当的可靠性设计(DfR)方法。
因为焊点的蠕变和应力松弛特性是随时间而变化的,加速试验中的疲劳损伤和疲劳寿命通常与操作使用中的不同,但利用加速试验结果,通过使用正确的加速因子可以得到产品可靠性估算值。
3.2可靠性概念
通过本规范,要掌握可靠性定义、失效机理以及统计的失效分布。
3.2.1可靠性定义
一个产品(表面贴装焊接件)在给定条件下并在规定的时间内完成规定功能而不超出容许失效等级的能力。
3.3失效机理
3.3.1蠕变
根据时间变化的粘塑性变形是施加的应力与温度的函数。
3.3.2应力松弛
根据时间变化的粘塑性变形通过将弹性应变转换成塑性应变来减小应力。
3.3.3焊点的蠕变-疲劳模型
通过基于实验数据的分析模型估算出受周期性蠕变-疲劳影响的焊点的使用寿命。
可以通过Engelmaier-Wild模型(见IPC-D-279附录A-3.1)或其它适合的被验证过的模型来确定可靠性试验结果估算值、产品可靠性和加速因子。
在Engelmaier-Wild焊点疲劳模型中,变量疲劳延性指数用于说明疲劳寿命与周期粘塑性应变能关联曲线的特征斜率。
该指数通过实验得到,是时间和温度的函数,不同于用于Coffin-Manson等式(适用于非蠕变金属)中的常量指数。
3.3.4热膨胀差
在操作使用或可靠性试验中的温度变化会导致材料间的热膨胀和收缩差。
热膨胀或收缩是通过材料的热膨胀系数(CTE)确定的。
热膨胀差分为下列两种:
1)“整体的”热膨胀不匹配:
元器件与基板之间的热膨胀不匹配。
2)“局部的”热膨胀不匹配:
焊料本身以及与它连接的材料之间的热膨胀不匹配。
3.4试验参数
注:
所有标有*的定义说明都是摘自JESD22-A104-B。
3.4.1*工作区
在恒温箱内,在规定条件下进行加载温度控制的区域。
3.4.2温度循环范围/振幅
在操作使用或温度循环试验期间的最高温度与最低温度差。
见图3-1、表3-1和表4-1。
图3-1热循环试验条件的温度曲线
(图3-1基于JESD22-A104-B附录A中的图1)
表3-1表面贴装电子元器件的产品分类以及最恶劣使用环境(仅供参考)
产品类型
(常用分类)
温度℃/℉
最恶劣使用环境
存储
操作运行
Tmin℃/℉
Tmax℃/℉
ΔT℃/℉
TDhrs
循环周期/年
标准使用年限
合格的失效危险%(约)
消费装置
-40/85
0/55
0/32
60/140
35/63
12
365
1-3
1
计算机及辅助设备
-40/85
0/55
0/32
60/140
20/36
2
1460
5
0.1
电信
-40/85
-40/85
-40/-40
85/185
35/63
12
365
7-20
0.01
商用飞机
-40/85
-40/85
-55/-67
95/203
20/36
12
365
20
0.001
工业与汽车-乘员舱
-55/150
-40/85
-55/-67
95/203
20/36
&40/72
&60/108
&80/144
12
12
12
12
185
100
60
20
10-15
0.1
军用
(地面与船用)
-40/85
-40/85
-55/-67
95/203
40/72
&60/108
12
12
100
265
10-20
0.1
太空
leo
geo
-40/85
-40/85
-55/-67
95/203
3/5.4
~100/180
1
12
8760
365
5-30
0.001
军用飞机
a
b
c
维修
-55/125
-40/85
-55/-67
125/257
40/72
60/108
80/144
2
2
2
100
100
65
10-20
0.01
&20/36
1
120
汽车
(发动机罩下)
-55/150
-40/125
-55/-67
125/257
60/108
&100/180
&140/252
1
1
2
1000
300
40
10-15
0.1
&=另外的条件1.所有类型的产品可能都会在18℃~260℃[64.4℉~500℉]温度范围下进行操作。
2.Tmin和Tmax分别为操作运行(试验)最低和最高温度,不限定ΔT的最大值。
3.ΔT表示最大温度范围,但不包括功率损耗的影响;功率损耗要计算ΔT;功率损耗可能会使温度循环加速试验相当不准确。
必须注意温度范围ΔT不是Tmin和Tmax之差;ΔT非常小。
4.驻留时间TD为每半个温度循环周期内焊点蠕变时间。
3.4.3*样品温度:
Ts
在温度循环期间,通过附着在或嵌入在样品上的热电偶或其它温度测量仪器测量的样品温度。
这种固定热电偶或其它温度测量仪器的方法确保样品总质量达到温度极限和驻留/保温时间的要求。
3.4.4*最高样品温度:
Ts(max)
样品的最高测量温度。
3.4.5最高额定温度:
T(max)
特定试验条件下的最高额定温度就是允许的样品最高温度Ts(max),见表4-1。
3.4.6*最低样品温度:
Ts(min)
样品的最低测量温度。
3.4.7最低额定温度:
T(min)
特定试验条件下的最低额定温度就是允许的样品最低温度Ts(min),见表4-1。
3.4.8平均循环温度Tsj
最高额定温度与最低额定温度的平均值,见附录A的公式4。
3.4.9额定ΔT
给定试验条件下的最高额定温度T(max)与最低额定温度T(min)之差,见表3-1。
3.4.10驻留/保温时间TD
样品温度总时间在每个额定最高温度T(max)和最低温度T(min)规定范围内(见表4-1)。
驻留时间对于加速试验来说特别重要,因为在加速试验过程中蠕变过程实际上不完整。
驻留便于将不完整的蠕变过程对产品使用温度循环产生的影响进行校正,产品使用温度循环时间足够长,可以使蠕变过程在每个循环驻留时间内趋于完整。
3.4.11驻留/保温温度
高于T(max)(循环上限),低于T(min)(循环下限)的温度,见表4-1。
3.4.12循环时间
完成一个完整的温度循环周期所用的时间,见图3-1。
3.4.13*温度缓变率
样品在每个时间单位内温度增加或降低的速率。
温度缓变率应该在温度曲线的直线部分测量,通常是在给定试验条件温度的10%~90%的范围内。
注:
缓变率可能会受载荷的影响,应该通过验证。
3.4.14最大循环应变(变形)范围
在周期性热或机械损伤过程中形成的总应变(变形)范围。
3.4.15最大循环应力范围
在周期性热或机械变形过程中产生的总应力范围。
焊点在发生蠕变的温度范围内,应力和应变范围是彼此独立的(与非蠕变型金属相反,它的应力-应变曲线说明了应力与应变的唯一对应关系),因为每一个温度和应变率都有不同的应力-应变曲线。
模量和产出量是受温度和应变率影响的,连接件结构的复杂性(例如易弯曲的引脚)对焊点的最大应力产生的影响很大。
3.4.16滞后回线
滞后回线可以用图表示出载荷循环过程中焊接件的应力-应变特性。
滞后回线区域说明了每个循环周期的粘塑性应变能,也是衡量每个循环周期疲劳损伤的一个计量单位。
滞后回线大小要根据应变范围、应力范围、循环驻留时间而定,平均循环温度对其影响很小。
3.4.17设计使用寿命
一台设备在规定环境下,完好地完成所有功能所需的操作使用寿命。
3.4.18预计的使用寿命
通过加速试验结果产生的模型(将疲劳循环数与给定容许的累计失效概率建立关联)预测出的使用寿命。
3.4.19早期失效
在环境应力筛选(ESS)试验、老化试验、初始功能试验或在初期使用过程中,主要由于不充分的性能或生产工艺而导致的失效。
3.4.20随机稳定状态失效
是一段有效的操作使用寿命周期——表面上失效随机发生或以低速率发生,与产品复杂性无太大关系。
对于焊接件来说,此过程不可测量,因为可能不存在或失效率很低。
3.4.21损耗失效
损耗就是损伤累积超时过程,在此过程中,由于疲劳或其它损耗机理导致产品消耗恶化而引起失效发生稳定上升。
这是由于焊接件的蠕变疲劳引起的损耗失效,为本规范的论述主题。
3.5统计失效分布的概念
3.5.1统计失效分布
失效,特别是由于损耗引起的失效,不是突然同时发生,但是超时分布。
威伯尔统计分布是最适合用于损耗失效的分布;但有时还可以使用Log-Normal分布。
对于威伯尔分布,需要2个定义参数:
(1)威伯尔斜率(分布范围的一个计量单位);
(2)某些截止值(通常N(63.2%)——威伯尔分布的特征寿命,但有时为N(50%)——平均失效寿命。
在威伯尔分布坐标图上,利用这两个定义参数将测量数据绘制成直线,可以简化数据分析。
3.5.2平均失效寿命N(50%)
一半的样品失效所用的时间。
3.5.3无失效寿命N0
首次失效发生前的时间(或循环数)(此参数用在3参数(3-P)威伯尔统计分布中)。
3.5.4累积失效百分比
在试验过程中,样品i的累积失效百分比通过等式F(i)=i/(n+1)计算,其中i为样品序号。
3.5.5累积失效概率
为了设计需要,规定的可靠性通常是指不超出规定设计寿命的“累积失效概率”。
3.5.6容许的累积失效概率
在使用寿命结束时,允许的最大缺陷/失效百分比。
3.6可靠性试验
3.6.1加速可靠性试验
在比使用寿命短的时间内,加速影响操作使用的损伤机理,从而引起失效的一种试验。
虽然加速试验结果来自较短的循环周期或更恶劣的加载条件,但必须避免使用外来的损伤机理。
可以通过适当的加速因子来估算使用寿命。
3.6.2热循环
要将组装件进行周期性的温度变化试验,温度变化率要足够慢以避免热冲击(通常小于或等于20℃[36℉]/分钟)。
热循环的最高温度应该为低于印制电路板材料的玻璃软化温度Tg温度的25℃[45℉]。
必须注意如果循环温度低于-20℃[-4℉]或高于110℃[230℉]或两种情况都存在(接近共晶(易熔的)锡铅焊料)可能会使焊接件遭受不只一种的损伤机理,这些机理彼此互相加速促进,从而导致早期失效;此外,由于多种损伤机理的混杂,所以在此环境下推断试验结果前必须对各种损伤机理有所了解。
3.6.3热冲击
当组装件遭受温度快速变化(在零件/组装件内引起瞬时温度梯度、翘曲以及应力)时会发生热冲击。
热冲击的温度变化率通常大于20℃[36℉]/分钟。
3.6.4电源循环
对于经常被接通/断开电源的电子器件来说,电源循环试验可能比温度循环试验更能准确地模拟现场使用条件。
3.7其它试验
3.7.1老化试验
对成品进行老化试验,定期的在正常的,有可能是恶劣的但还是仿真的操作环境下进行,不属于加速可靠性试验。
3.7.2环境应力筛选(ESS)
筛选过程利用由环境产生的应力,使组装件中“薄弱的”元器件的应力超限达到失效点,防止这些潜在缺陷在现场使用中出现,引起现场失效。
产生这些应力的环境可能或不可能与产品使用环境条件有关。
一旦出现失效,元器件就会被检测出来并被维修、替换、报废,或为未来产品重新设计。
ESS必须在不损坏“正常的”元器件的情况下进行。
ESS不是加速可靠性试验。
3.7.3高速应力试验(HAST)
这种试验是在温度与湿度结合的加速应力中电偏压情况下模拟与失效机理有关的侵蚀。
HASL可以用于元器件和组装件,但对于焊接件来说不属于加速可靠性试验。
3.7.4机械震动
机械震动就是对系统产生快速的机械能量转换,在系统内部使应力、速度、加速度或位移发生显著变化。
3.7.5振动
交替地与平衡位置相反的方向周期性或随机地运动。
应用载荷通常低于材料的屈服点(弹性)。
3.7.6工艺鉴定
用来验证制造产品的工艺是否满足性能规范的一种特殊试验或一组试验。
3.7.7工艺检验
对工艺进行定期的评估,确保工艺优化或消除工艺偏离。
3.8评估与应用事项
表3-1列出了9种最常见的产品类型的常用存储和操作环境以及最恶劣的使用环境条件。
此表格仅供参考。
3.9焊接件工艺说明
焊料根据特定的使用条件随温度、时间和应力而变化的特性使其在工艺金属中具有独特性。
例如,共晶(易熔的)铅锡焊料在高于20℃[68℉]温度时具有稳定的蠕变和应力松弛,而在低于-20℃[-4℉]温度时具有与其它金属相似的长时间承载能力。
高于20℃[68℉]时,温度越高并/或压力等级越高,焊料的蠕变和压力松弛越快。
设计并确保产品可靠性的第一步就是要对给定的表面贴装焊接技术的可靠性和失效机理有所了解。
为此,需要有通用数据库。
虽然可能会发生基于单超限应力的失效机理,但最常见的可靠性威胁是来自于由疲劳损伤引起的应力松弛。
理想的疲劳失效数据库是根据低加速和高加速的结合试验得到的。
对于接近共晶(易熔的)铅锡焊料来说存在这样的数据库,但对于其它合金,目前不存在这种数据库,特别是对于无铅焊料。
由于这个原因,试验器件在低加速试验中产生的平均失效次数大约比现场使用的实际寿命短10~20次。
高加速试验大约短100~500次。
试验加速度越大,试验结果反映出的现场条件性能越少。
因此,低加速试验应该更能最大程度地模拟预期的现场条件,但通常由于低加速试验所要求的时间和资源问题,使高加速试验成为必要试验。
4.性能测试方法
规范化的加速可靠性测试方法为首选方法,因为其试验数据可以用于形成可靠性基础标准。
IPC-SM-785为加速可靠性测试方法的设计与实行提供技术基础。
特别推荐将本标准与IPC-SM-785一起使用,因为本标准介绍了SMT焊点失效物理机制,也就是导致焊点疲劳的各种机理。
除了用公式说明失效的机理外,本标准还提供了基于实证研究的技术资料,从中可以获得加速测试程序。
IPC-SM-785给出了适当的警告与免责条款。
由于SMT焊点的疲劳寿命远远超出了电子组件设计与研制通常所需的时间,因此加速试验就成为鉴定产品使用寿命的一个必要条件。
IPC-9701为加速寿命试验的设计提供指导方法。
虽然加速寿命试验通常要在用户与供应商之间达成一致,但本标准的使用(按照需要稍作改动)将会使寿命试验规范化。
本标准中的测试方法和要求可能在技术上没做严格要求,但继续使用与数据积累将会形成可靠的数据基础。
4.1总要求
表4-1列出了规定的和推荐参考的试验参数。
规定的参数应该严格遵守,不能有任何偏差。
遵照所有规定的条件可以确保试验和结果通过工业验收;偏离某一特定的规定参数可能会被个别用户接受但最终影响供应商的试验结果通过工业验收。
对于多种参数,建议使用推荐参考的以适应更广泛的工业兼容性和验收。
应该遵守推荐参考的参数,除非供应商可以验证他们建议的偏差可以提高特定封装的板级可靠性。
4.2试验器件
试验器件的正确设计与组装是确保获得正确有效数据的关键。
4.2.1元器件说明
表面贴装元器件就是使用传统的回流技术用焊料合金将元器件焊接到一块电路板上。
球栅阵列(BGA),小尺寸封装(SOP)和芯片级封装(CSP)都是一些典型的元器件类型。
表4-1温度循环要求,规定条件下的规定的与推荐参考的试验参数
试验条件
规定条件
温度循环(TC)条件:
TC1
TC2
TC3
TC4
TC5
0℃~+100℃(推荐参考)
-25℃~+100℃
-40℃~+125℃
-55℃~+125℃
-55℃~+100℃
测试时间
热循环次数(NTC)要求:
NTC-A
NTC-B
NTC-C
NTC-D
NTC-E
无论哪种条件,首先:
50%(最好为63.2%)累积失效
(推荐参考测试时间)
或
200次循环
500次循环
1000次循环(推荐TC2,TC3和TC4)
3000次循环
6000次循环(推荐TC1)
低温驻留时间
温度极限(推荐)
10分钟
+0/-10°C(+0/-5°C)[+0/-18°F(+0/-9°F)]
高温驻留时间
温度极限(推荐)
10分钟
+10/-0°C(+5/-0°C)[+18/-0°F(+9/-0°F)]
温度缓变率
≤20°C[36°F]/分钟
所有产品样品的尺寸
33个元器件样品
(32个试验样品,1个样品做横切测量,另外10个样品进行再加工)
印制线路(电路)板(PWB/PCB)厚度
2.35mm[0.093in]
封装/芯片模条件
菊花链结构的芯片模/封装(见表4-2)
试验检测
连续检测(见表4-4,推荐使用事件检测器)
本鉴定要求标准将论述焊点的可靠性以及在其他板级热循环干扰下元器件/印制板之间相互的热机械影响,例如分层、过孔断裂、电介质断裂等等。
本标准规定的默认条件是使用菊花链结构的芯片模以确保在板级温度循环期间焊球可靠性、封装材料以及芯片模级间的互连全部特性化。
表4-2列出了免除菊花链结构芯片模要求的类型。
表4-3列出了免除类的特定参数要求。
机械芯片模(如果允许)应该按照尺寸和芯片模间的互连制造一个实际芯片模但要求包括菊花链线对或活性硅电路。
表4-2菊花链要求
免除类型
规定条件
全部产品特性化(默认)
菊花链结构的芯片模
免除类型A
(见表4-3)
菊花链结构的封装基片与机械芯片模(推荐菊花链结构的芯片模)
陶瓷封装(基板厚>1mm[0.040in],平均模数240-270Gpa)
菊花链结构的封装基片(推荐菊花链结构)
4.2.1.1菊花链结构芯片模/封装
试验器件的元器件封装与芯片模应该能代表产品元器件的特性:
1.规定试验器件的元器件布局、结构和材料必须能代表典型的产品元器件,包括芯片模连接粘合与工艺、填充与工艺、丝焊/倒装芯片等等。
2.试验器件的元器件的芯片模是菊花链结构(如果适合条件)(见表4-2)。
试验器件必须使用能代表产品元器件特性的封装材料和尺寸,并且使用与产品元器件相同的芯片模互连、印制线结构、过孔结构以及层数等与外部引脚/焊球/焊盘连接。
为了减少试验费用,菊花链结构的芯片模应该与产品元器件的最大尺寸芯片模相符。