沉镍金工艺培训教材.docx
《沉镍金工艺培训教材.docx》由会员分享,可在线阅读,更多相关《沉镍金工艺培训教材.docx(11页珍藏版)》请在冰豆网上搜索。
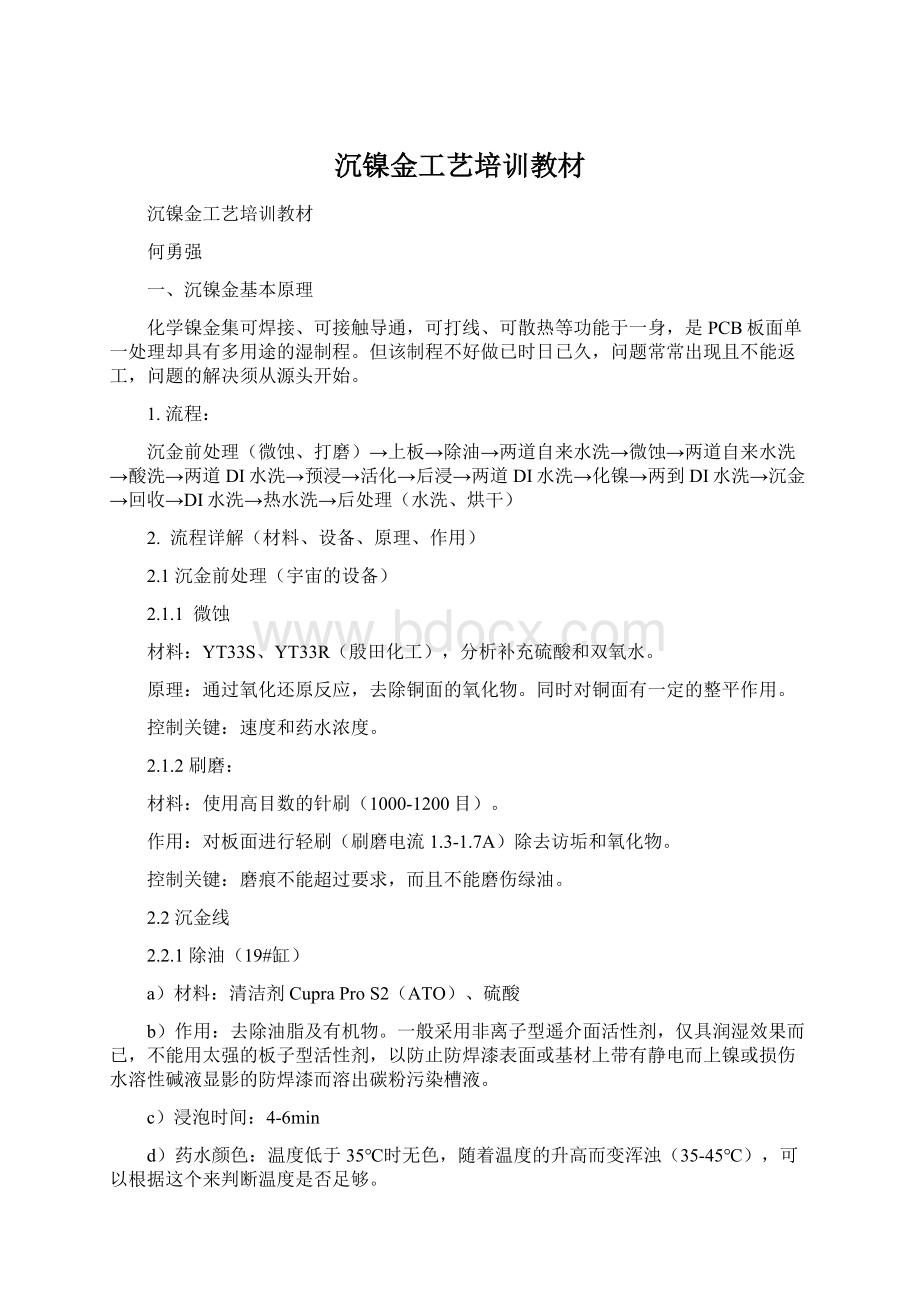
沉镍金工艺培训教材
沉镍金工艺培训教材
何勇强
一、沉镍金基本原理
化学镍金集可焊接、可接触导通,可打线、可散热等功能于一身,是PCB板面单一处理却具有多用途的湿制程。
但该制程不好做已时日已久,问题常常出现且不能返工,问题的解决须从源头开始。
1.流程:
沉金前处理(微蚀、打磨)→上板→除油→两道自来水洗→微蚀→两道自来水洗→酸洗→两道DI水洗→预浸→活化→后浸→两道DI水洗→化镍→两到DI水洗→沉金→回收→DI水洗→热水洗→后处理(水洗、烘干)
2.流程详解(材料、设备、原理、作用)
2.1沉金前处理(宇宙的设备)
2.1.1微蚀
材料:
YT33S、YT33R(殷田化工),分析补充硫酸和双氧水。
原理:
通过氧化还原反应,去除铜面的氧化物。
同时对铜面有一定的整平作用。
控制关键:
速度和药水浓度。
2.1.2刷磨:
材料:
使用高目数的针刷(1000-1200目)。
作用:
对板面进行轻刷(刷磨电流1.3-1.7A)除去访垢和氧化物。
控制关键:
磨痕不能超过要求,而且不能磨伤绿油。
2.2沉金线
2.2.1除油(19#缸)
a)材料:
清洁剂CupraProS2(ATO)、硫酸
b)作用:
去除油脂及有机物。
一般采用非离子型遥介面活性剂,仅具润湿效果而已,不能用太强的板子型活性剂,以防止防焊漆表面或基材上带有静电而上镍或损伤水溶性碱液显影的防焊漆而溶出碳粉污染槽液。
c)浸泡时间:
4-6min
d)药水颜色:
温度低于35℃时无色,随着温度的升高而变浑浊(35-45℃),可以根据这个来判断温度是否足够。
e)控制关键:
浸泡时间和药水温度、药水添加情况。
因为药水只能分析硫酸浓度,与补加硫酸按照1:
2的比例进行补加除油剂。
2.2.2微蚀(22#缸)
a)材料:
过硫酸钠、硫酸
b)作用:
一般蚀铜1-2µm。
化学反应方程式S2O82-+2H++CuO+Cu→2SO42-+2Cu2++H2O,利用氧化还原反应清楚铜表面的氧化物,同时把铜面微粗化,提高镍铜结合力。
如果发现有星点露铜现现象,很可能为感光制程之显影不洁或显影后水洗不净造成。
此时可适当延长微蚀时间除之,但是要保证孔壁厚度。
c)浸泡时间:
≤1.5min
d)药水颜色变化:
开缸无色,随着生产颜色变成深蓝色。
e)控制关键:
铜离子、浸泡时间。
因为浸泡时间过长,孔壁厚度容易不足。
而铜离子过高,微蚀效果变差,而且容易出现薄镀的质量问题。
同时要注意生产线补加NPS的情况,防止局部添加堵塞打气管。
2.2.3酸洗(25#号缸)
a)材料:
硫酸
b)作用:
清洗,去除微蚀中生产的铜盐,防止个别绿油塞油不满的小孔内藏有铜离子导致漏镀或薄镀。
c)浸泡时间:
3-5min
e)控制关键:
浸泡时间和温度。
2.2.4预浸(18#缸)
a)材料:
硫酸
b)作用:
去除前面槽液的污染,保护活化槽,同时保证铜面新鲜。
c)浸泡时间:
3-5min
2.2.5活化(17#缸)
a)材料:
化镍活化剂(ATO)、硫酸
b)作用:
离子钯,通过置换反应,在铜面上置换上一层原子钯,为后续的化镍反应提供催化剂。
化学反应式:
Cu+Pd2+→Pd+Cu2+。
由于铜离子的不断置换出来,当铜离子高(≥2.0g/L)的时候,容易出现漏镀的情况,所以活化的寿命一般为3-4MTO(MTO是MetalTurnOevr的缩写)。
一般活化剂的添加要求为生产每200块板添加1.5L。
c)控制:
温度20-30℃(一般控制25℃),活化Pd浓度为40-60ppm,硫酸50ml/L。
d)浸泡时间:
1.5-2.5min
e)控制关键:
活化缸的杂质和补加的情况。
而且出现吊车故障时,浸泡时间不能超过控制要求。
过了活化的板件必须按正常走后续的流程。
2.2.6后浸(16#缸)
a)材料:
硫酸
b)作用:
清洗板面残留的活化剂,防止出现渗镀,同时形成酸膜保护活化钯面。
去除前面槽液的污染,保护镍缸。
由于原子Pd的活性高,所以在后浸缸浸泡的时间要求为0.5-1min,过长容易出现钝化而出现漏镀。
c)浸泡时间:
0.5-1.0min
2.2.7镍缸(8-13#号缸)
a)材料:
化镍补充剂PartA、化镍补充剂PartB、化镍校正液CNN、氨水。
槽液的配方一般为供应商的机密,主要成份有:
镍盐,还原剂,和多种有机添加剂。
磷含量:
(7-10%)含量低,其抗蚀性,焊锡性都会变差,且镍层表面易钝化,含量高,会影响镍层的质量,增大镍层的内应力,使金镍之间的结合力变差。
Ni2+:
(95%-105%)含量低,影响沉积速率,含量高,槽液稳定性差,活性太强易渗镀和生产镍碎。
有机添加剂:
添加剂主要有络合剂(使Ni2+生成络合物,避免生成氢氧化物或亚磷酸盐沉淀)、加速剂、稳定剂剂。
由于槽液中加有加速剂(多为乳酸),故槽液冷却停用后易发霉。
因此,在产量不大或长时间性不用时,每隔1-2天就升温做假镀(拖缸)。
以维持其品质及活性。
b)设备:
镍缸(不锈钢、表明光滑)、自动分析器、自动添加泵、保护电流控制器、循环泵、变频器。
c)原理:
①次磷酸二氢钠的次磷酸根离子水解并氧化成磷酸根,同时放出两个活性氢原子吸附在铜底钯面上。
②镍离子在活化钯面上迅速还原镀出镍金属。
③小部分次磷酸根在催化氢的刺激下,产生磷原子并沉积在镍层中。
④部分次磷酸根在催化环境下,自己也会氧化并生成氢气从镍面上向外冒出。
反应方程式:
H2PO2—+H2O→H++HPO32-+2H(催化剂)
Ni2++2H(催化剂)→Ni+2H+
H2PO2—+H(催化剂)→H2O+OH-+P(副反应)
H2PO2—+H2O→H++HPO32-+H2
d)浸泡时间:
20-25min
e)对于镍缸的稳定性控制,要关注以下几点:
I.每次监督生产镍缸清洗情况,当发现镍缸的使用寿命异常时,重点检查开缸加药的顺序(先加化镍建浴剂、然后再加化镍补充剂A,最后才加氨水。
因为镍非常容易分解,先加PartA会导致部分镍分解生成Ni(OH)2而沉淀下来)、缸壁上镍情况(查清那个地方上镍严重才容易调查原因)、阳极保护的接口和保护套情况等。
II.每天要检查自动分析器,包括管路、分析结果和显示结果、出水是否正常、调整后是否一直加药或不加药等。
每周保养时检查分析器,看是否残留有较多的镍碎、PH探头是否正常等。
(PH探头曾经出现失效导致板件批量报废)
III.镍缸的开缸控制:
新开缸要求分析镍缸成分:
Ni2+浓度为105-108%为正常,次磷酸钠为28-31g/l为正常(不能低于25g/l,否则该缸活性会不足,容易出现颜色不良的问题),PH值4.6-4.7之间(超过说明氨水加入过量,偏小说明氨水加入量少或硝酸没有清洗干净)。
IV.镍缸平时生产控制:
Ni2+浓度控制在98-105%之间;当分析器中的镍碎较多时,分析不准,有时实测会达到110%,所以保养时要清洁,清洁后分析器容易出现不稳定的情况,要求生产关注。
PH值一般控制在4.8-5.0之间,PH探头要求为3个月更换一次,根据目前的保养情况来看,可以使用到半年,但是平时要特别关注,防止出现分析不准,如果没有把握,最好在3个月时更换。
PH值调整时可用10%硫酸或铵水调整,注意:
用铵水和硫酸调整时须缓慢加入且少量多次进行。
V.当镍缸实际分析镍浓度低于90%,要求按开缸比例进行调整,同时对镍缸进行拖缸处理,并查明什么原因造成浓度偏低。
VI.每天注意观察镍缸的反应状态。
当发现镍缸活性偏低时要求生产进行拖缸。
同时可以考虑提高温度和暂时停加PartB的方法。
在活性正常的情况下,镍厚一般在150-230微英寸之间,超过250说明活性太强,要适当调整温度,低于150就说明活性偏低,就要提高温度同时进行拖缸处理。
按照目前的情况来看,刚开缸时,镍厚度一般为180-210之间;使用1MTO以后会有所下降,到2-3MTO基本可以维持在150-180之间,所以要关注镍厚度。
同时可以根据化学方法来测量镍缸的活性(测量镍缸的稳定点):
取1L最佳条件下的槽液,恒温加热并保持82-84度;同时配制滴定液(取30ml活化剂原液到250ml容量瓶配制成30ppmPd液)
VII.每天关注PartA和PartB的添加槽和添加流量,如果偏差大(连续生产超过3-5L)必须调查,有下面几个可能:
有一添加槽里面的药水已经很少(或药水没有完全浸没取样口)会导致两者流量不相等、生产是否在生产过程由于金面颜色不良停用PartB、添加泵是否正常工作、两者流量比例是否正常等。
其实如果是PartA比PartB的耗用量梢大,影响不大。
根据目前的情况来看,PartA比PartB大较好,现在基本控制在1:
1到1.2:
1之间;如果是PartB大的话就要注意板件的颜色情况,要进行拖缸和适当调整两者的流量比例。
VIII.保护阳极:
每次镍缸换缸前都要注意检查阳极保护杠的情况:
接口是否生锈、保护杠是否固定好、下端不能与缸壁接触。
定期对阳极保护的电压和电流进行检测。
IX.镍缸循环:
目前三个镍缸的循环泵都有变频器可以调整流量。
目前一般控制在25-35赫兹之间。
该循环量一般控制在4-6个循环/小时,对改善大铜面方向性的颜色不良有很大的帮助。
2.2.8金缸(4-5#)
a)材料:
浸金补充剂、浸金建浴剂、浸金辅助剂、氰化金钾(含金68.3%)
b)原理:
当PCB板面沉好镍层放入金槽后,其镍面即受到槽液的攻击而溶出镍离子,所抛出的两个电子被金氰离子获得而在镍面上沉积出金层。
反应式:
Ni→Ni2++2e Au(CN)2-+2e→Au+2CN-
由此可知,一个镍原子溶解可获得两个金原子的沉积,又因金层上有许多疏孔,故表面虽已盖满了金层,但仍可让疏孔的镍面溶解而继续镀出金层,只是速度越来越慢而已。
c)设备要求:
由于金缸反应为置换反应,所以要求设备里面不能含有金属的材料,防止带进金属杂质,要求全部使用铁氟龙材料。
沉金金缸中不能使用任何的金属或含金属的材料。
切记!
。
二沉金出现的质量问题及基本解决办法:
1.沉金颜色不良:
镀层的光亮度(颜色均匀与否)依赖基底表面的粗糙度。
1.1沉金前的影响:
单面开窗的孔边缘有水迹或其他污染,这会造成沉金后明显的发白或水迹状不良。
(可以通过水平微蚀前处理降低影响,但是要注意防止薄镀的出现)。
经过绿油工序,如果显影不好的时候,会有有机杂物附在铜面上,如果微蚀不好无法完全除去会影响。
活化缸钯浓度不足时,由于多层板的内外层存在着电位差(经过微蚀后更突出),阻止镍的附着,从而颜色不良,严重漏镀。
同时要控制好微蚀的铜离子含量。
1.2沉镍:
镍缸活性的影响,同时还有负载、药水的循环情况、温度、震荡等。
我们前处理微蚀使用的药水与OSP一致,对铜面有一定的整平作用,对颜色不良有比较大的帮助,但是由于走前处理容易藏药水而出现薄镀的问题,所以要比较小心。
1.3当在一些大铜面与绿油交接处出现金层发白,而且发白处剥离。
主要原因有:
镍缸循环过快、镍缸活性不足、活化不足、微蚀效果不好、镍缸开缸拖缸不足。
对这些可能的原因进行调查分析并改善。
同时可以试试停用镍缸震荡的办法,应该会有改善。
1.4插脚镀金后再沉金的板件应该注意的问题:
胶迹污染、镀金时药水污染、离金指边小于1mm的焊盘漏镍、颜色不良。
a)对于胶迹污染,根据目前使用的3M胶带来看,应该问题不大,但是如果有出现,可以试走退膜后在微蚀的办法,同时要检查生产是否按要求对胶辊进行清洁,但也不是万能的,所以要具体对待。
b)镀金时药水污染,此问题偶尔发生,所以一定要求生产对于沉金板件在镀金时所贴的蓝胶带和压胶带的情况,避免镀金时渗药水污染。
同时最好要求此类板件尽量采用新领的蓝胶带进行贴板,而且要尽快安排生产,清洗后注意隔板纸的情况,尽量采用比较干净的隔板纸。
c)离金指边小于1mm的焊盘漏镍,此问题一直存在。
主要是由于该焊盘离红胶带很近,而在药水缸中,在红胶带边缘药水容易交换不均匀。
在近段的时间生产时,通过对金缸进行人工震荡,有所改善,但是无法杜绝。
d)颜色不良:
正常情况下提高微蚀效果和镍缸活性。
一般情况下都可以通过前处理来改善。
如果按正常速度没有改善,可以适当降低速度,但要保证孔壁厚度。
而且要注意防止薄镀出现。
从这几次的情况来看,新开的前处理微蚀更容易出现薄镀,更加要注意。
个人认为是在贴蓝胶带和红胶带时桌面要保持清洁。
2.渗镀
渗镀问题在沉金线偶尔发生,分为以下几种情况
a)镍缸活性高造成的渗镀:
拖缸过度、镍缸反缸、自动添加失去平衡(PartA比PartB大)等,这种情况一般可以通过镍厚来判断。
b)吊车故障:
停机造成板件在活化缸、镍缸的浸泡时间过长。
c)生产线正常无法判断的情况(建议切片确认):
曾经出现板件的镍厚正常,但是板件却出现渗镀的情况。
从当时调查的情况来看,各个工艺参数正常,设备正常,但是通过镍缸活性点的检查滴定来看,活性偏高。
但是活性怎么会提高呢,根据后来的观察和调查,可能为:
由于我们B槽为PartB和CNN按1:
1的配比,该添加槽只有50L,当槽内大约剩余10L药水时,生产操作人员会进行配槽,先加入1桶(约25L)CNN后,也就只能再加入15-20L左右的PartB,这样稳定剂会偏小,刚开始生产时可能没问题,当生产时间过长,会导致缸内的稳定剂含量下降,从而导致活性高,出现渗镀。
d)化镍槽前的活化药水(钯离子)被污染(尤其是铁离子或化学镀镍液的滴入)。
调查污染来源。
e)活化药水老化,关注活化缸使用寿命。
f)板子在镀镍磨板时除铜面氧化物时,所用的刷板压力太大,造成铜粉残留蚀铜未净,磨痕来判断。
或基材表面上留有残铜,切片确认。
3.漏镀:
漏镀镍金,发生露铜或跳镀
a)绿油显影不净、显影后水洗不净,或是烘烤过程中,板件放板密度过高和通风效果不良,一般可以通过加强微蚀效果来解决,但难度大。
b)镍槽的添加补充不正常,镍离子不正常。
曾经出现过取样管破进水,自动分析器浓度低,不断补充药水,导致镍浓度达到140%,因为PartA和PartB是同时补加,而PartB中含有稳定剂,过量的稳定剂会导致镍缸活性下降。
而且当镍缸自动补充不正常后,生产的板件颜色会非常差,而且状态无法调整到正常状态,所以必须关注自动补加的情况。
c)镍缸有绿油污染,此问题目前无法验证,不过当有大量板件绿油剥离或更换绿油品种时要注意。
d)活化不足:
活化温度温度不足、活化铜离子高、活化浓度低,或从活化出来后在空中或水中停留时间过长。
e)镍缸活性不足:
长时间生产面积小的板件、开始生产前拖缸不足、生产过程中试板多而且没加拖缸板,导致活性不断下降而出现漏镀。
对这些问题,在平时要注意检查并监督。
f)生产多层板而且又是半塞油或塞不足的板件时,由于电位差的缘故,容易出现跳镀,严重漏镀。
在本工序的改善的方法有:
降低微蚀缸的铜离子、提高酸洗缸温度和浸泡时间、提高活化温度、提高活化浓度、延长活化时间、提高镍缸活性,开震荡。
其实最好的方法是绿油工序提高塞油的质量。
4.镀层剥离
4.1化学镍层与底铜结合力不好
对这类情况,我们的思路要把解决问题重点放在镍缸前的流程和来料板面的情况。
a)铜表面有绿油或绿油残膜,遇到这种情况,板件一般要返工。
b)铜面氧化物清除不足,也就有可能是除油、微蚀或前处理的打磨效果不好。
c)化学镀镍前处理经微蚀或活化后因水洗太久而钝化。
4.2金层与镍层间的结合力不好
a)金液中铜离子高(通常不可超过5ppm)或过多有机杂质高。
b)化镍后沉金前水洗时间太长或水质不好、水洗不足产生细菌多等造成镍表面钝化。
c)镍缸有机污染高。
主要药水分解或绿油所析出的物质。
5.生产线一般在放假后注意的问题:
因为我们的镍缸药水中包含有加速剂,而加速剂一般为乳酸,停用后时间过长容易发霉,所以一般时间超过两天都要升温假镀。
6.磷含量问题:
如果磷含量高,金镍的结合力会变差,如果磷含量低,可焊性变差,所以控制镍缸的反应状态和次磷酸钠的含量。
7.停机造成的金镍厚超标,因金层上有许多疏孔,故表面虽已盖满了金层,但仍可让疏孔的镍面溶解而继续镀出金层,只是速度越来越慢而已,从而导致镍受腐蚀,所以金厚超过5微英寸的板件必须隔离确认。
8.镍槽不锈钢槽壁的保护装置呈现电流太高的现象:
a)镍槽温度太高或PH值太高、循环不足导致局部药水温度过高、活化液被带入镍槽内,反应过快。
b)缸壁硝酸洗缸钝化处理不足
c)镍补充药水添加太快,PartB与CNN的比例不一,或PartA比PartB添加比例高,导致稳定剂含量太低
d)吊蓝上的镍金碎片落入镍缸中
e)保护装置不正常(保护阳极缸粗糙、接口生锈、电线接口面积小、连线距离过长)
总的来说,沉金线所产生的问题的原因是多方面,上面所列只是一些常见的质量问题的原因和解决方法。
在沉金生产线的控制中,一个问题的出现,它的原因是多方面的,不要局限于上述的原因,要学会不断更新自己的想法,对所有的原因都要抱着怀疑的态度。
上面所写只是我个人和前人的一些看法,希望能起到抛砖引玉的效果。
三、沉金程序编写说明
3.1程序编码(代表)命令
沉金自动控制系统有它自己的电脑流程语言,每一个语句可以分为指令(包括动作指令、逻辑指令)和数据A、数据B,用户可以根据工艺要求为吊车设计一个吊车流程图(时序图),在命令信号的基础上,吊车会按照指令周期的自动运行。
3.1.1通俗说法:
指令代表
1→→→→→→→→→→→吊车吊起飞巴并把飞巴移动到具体位置
2→→→→→→→→→→→→吊车平移到具体位置
4→→→→→→→→→→→→吊车停留(停止运行)
5→→→→→→→→→→→→以下步骤循环
6→→→→→→→→→→→→吊车等待
7→→→→→→→→→→→→验证吊车运行情况
8→→→→→→→→→→→→确认“7”并取消
9→→→→→→→→→→→→结束程序
10→→→→→→→→→→→→程序开始吊车位置
3.1.2详细说明:
编程序的画面有四列,
第一列为地址(ADDRESS):
表示吊车1、2程序开始的位置。
第二列为指令(INST):
指令代码。
第三列为数据A(DateA)
第四列为数据B(DateB),具体说明如下:
指令1:
表示吊车带飞巴上升,滴水0-14、30秒,移动到目的地,把飞巴放下。
参数A为滴水时间,取值为0-15之间(其中1-14表示为1-14秒,而15表示为30秒);参数B为目的槽号。
指令2:
表示吊车不带飞巴,吊臂在下端时平移到目的地。
参数A没有使用,参数B为目的槽号。
指令4:
吊车在当前位置等待0-60秒。
参数A没有使用,参数B为等待时间,值为0-60。
指令5:
循环动作(顺序动作),用来判断和区分飞巴放入相同作用的镍缸或金缸,或从中取出时的循环动作(顺序工作)。
参数A为该循环出现的次数,参数B为在流程中实际执行的次数。
指令6、指令7、指令8:
这三个指令都属于逻辑指令,它的作用为当某一时刻有两部吊车需要进入同一区域时,防止吊车相撞。
参数A没有使用,参数B为标志值,表示为该指令出现的次数。
为了保证同一时间内只准一部吊车进入同一区域(一个或几个缸,称为重叠区),必须设置标志防止一方相撞。
指令6表示进入重叠区,并设置标志。
指令7表示进入重叠区,进行判断,判断目前的吊车是否已经离开重叠区,并设置标志。
指令8表示进入重叠区,判断指令7已经完成,并把标志清零,等待的吊车可以运行。
指令9:
吊车运行的结尾,也是程序一个周期的结束。
这是吊车动作将会暂停,直到所有吊车动作完成和周期时间到后,吊车会开始一个新的程序周期。
参数A和参数B都为0。
指令10:
在一个周期开始的时间使用,表示开始时吊车所在的位置,保证所有的吊车都在各自开始时为同步执行。
参数A没有使用,参数B为起始位置的缸号。
3.2例子说明
程序名:
ONE085E
周期:
710s;沉金时间:
10分钟;沉镍时间:
22分钟;活化时间:
1.8分钟
起始飞巴:
0、1、5、8、9、13、17、23
以ONE085E为例
吊车1(TP1)吊车2(TP2)
INSTAB
1001(吊车1起始位置在1号缸)10023
200(平移到0号缸)1024
1019(吊起飞巴并移动到19号缸放下)701
2017(吊车平移到17号缸)801
11016(吊起飞巴,滴水10秒,移动到16号缸放下)2019
601(设置第一个重叠区标志,防止碰撞)
201(平移到1号缸)4060
100(吊起飞巴并移动到0号缸放下)2016
207(吊车平移到7号缸)1515
4010(吊车停留10秒)2024
702(判断2号吊车运行情况,是否已经离开第二个重叠区)1025
802(判断指令7的情况,取消第二个重叠区标志,吊车可以运行)2015
512(第一个循环,进入相同作用的镍缸,下面两步循环)1014
209(平移到9号缸)602
208(平移到8号缸,第二个周期时的动作)2025
167(吊起飞巴,滴水6秒,移动到7号缸放下)4060
2014(平移到14号缸)1326
522(第二个循环,进入相同作用的镍缸,下面两步循环)4050
159(吊起飞巴,滴水5秒,移动到9号缸放下)1018
158(吊起飞巴,滴水5秒,移动到8号缸放下,第二个周期时的动作)2019
207(平移到7号缸)400
106(吊起飞巴,滴水0秒,移动到6号缸放下)1020
205(平移到5号缸)4060
1153(吊起飞巴,滴水30秒,移动到3号缸放下)1021
206(平移到6号缸)4045
155(吊起飞巴,滴水5秒,移动到5号缸放下)1022
203(平移到3号缸)4025
182(吊起飞巴,滴水8秒,移动到2号缸放下)2018
4060(吊车在原位置停留60秒)11017
131(吊起飞巴,滴水3秒,移动到1号缸放下)2022
900(程序结束)1323
900
左边为吊车1的程序,右边为吊车2的程序。
上面的例子说明的是吊车1的运行情况。
四、结束语
沉金一直以来都是被人认为是比较难控制的生产线,容易出现质量问题,而且无法返工。
沉金培训教材是个人工作经验和资料结合,难免有不对之处,敬请指正。
希望该教材能对大家对沉金生产线有所了解,谢谢!