轧钢厂扁平材车间质量案例及质量管理学习纪要.docx
《轧钢厂扁平材车间质量案例及质量管理学习纪要.docx》由会员分享,可在线阅读,更多相关《轧钢厂扁平材车间质量案例及质量管理学习纪要.docx(29页珍藏版)》请在冰豆网上搜索。
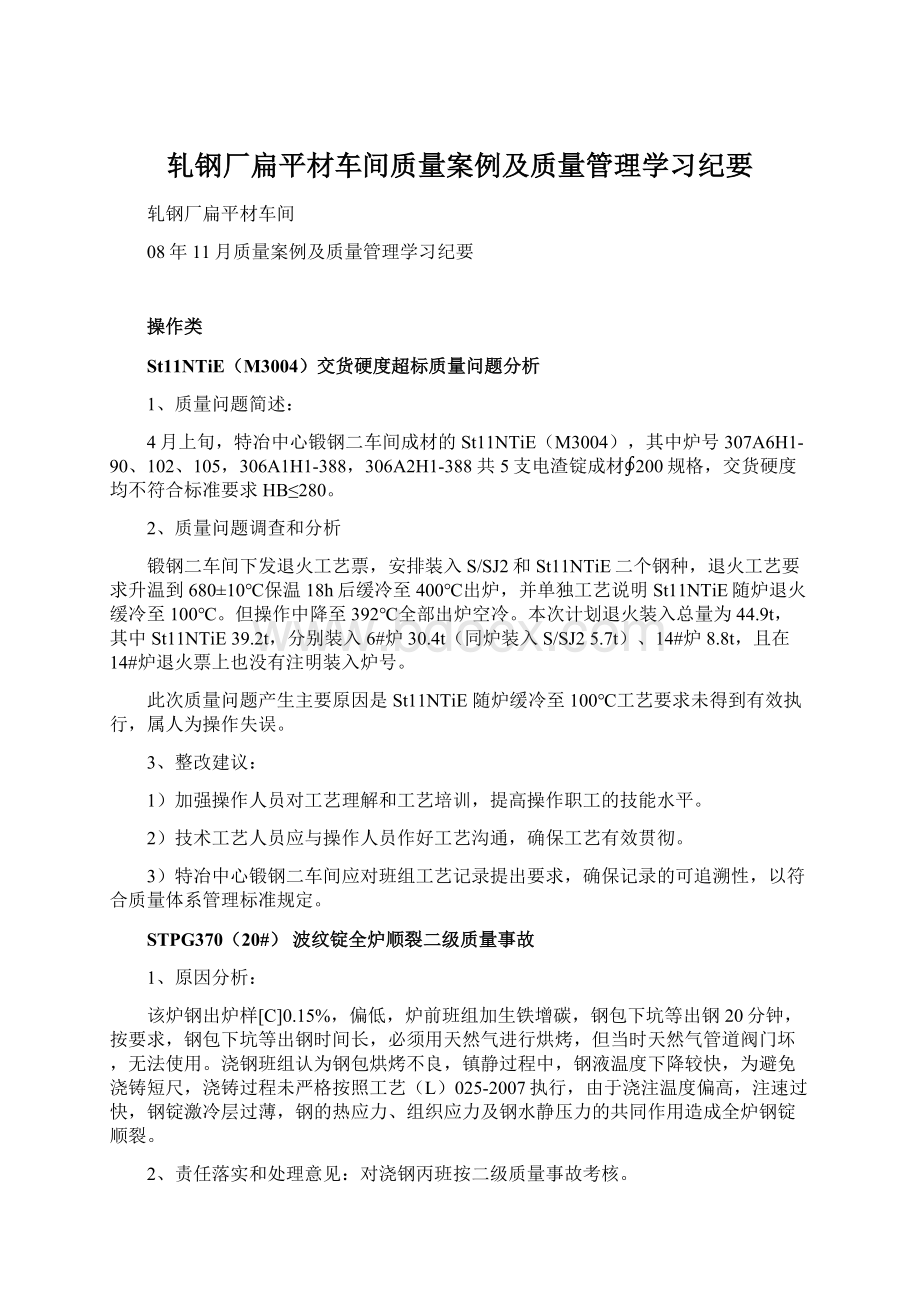
轧钢厂扁平材车间质量案例及质量管理学习纪要
轧钢厂扁平材车间
08年11月质量案例及质量管理学习纪要
操作类
St11NTiE(M3004)交货硬度超标质量问题分析
1、质量问题简述:
4月上旬,特冶中心锻钢二车间成材的St11NTiE(M3004),其中炉号307A6H1-90、102、105,306A1H1-388,306A2H1-388共5支电渣锭成材∮200规格,交货硬度均不符合标准要求HB≤280。
2、质量问题调查和分析
锻钢二车间下发退火工艺票,安排装入S/SJ2和St11NTiE二个钢种,退火工艺要求升温到680±10℃保温18h后缓冷至400℃出炉,并单独工艺说明St11NTiE随炉退火缓冷至100℃。
但操作中降至392℃全部出炉空冷。
本次计划退火装入总量为44.9t,其中St11NTiE39.2t,分别装入6#炉30.4t(同炉装入S/SJ25.7t)、14#炉8.8t,且在14#炉退火票上也没有注明装入炉号。
此次质量问题产生主要原因是St11NTiE随炉缓冷至100℃工艺要求未得到有效执行,属人为操作失误。
3、整改建议:
1)加强操作人员对工艺理解和工艺培训,提高操作职工的技能水平。
2)技术工艺人员应与操作人员作好工艺沟通,确保工艺有效贯彻。
3)特冶中心锻钢二车间应对班组工艺记录提出要求,确保记录的可追溯性,以符合质量体系管理标准规定。
STPG370(20#)波纹锭全炉顺裂二级质量事故
1、原因分析:
该炉钢出炉样[C]0.15%,偏低,炉前班组加生铁增碳,钢包下坑等出钢20分钟,按要求,钢包下坑等出钢时间长,必须用天然气进行烘烤,但当时天然气管道阀门坏,无法使用。
浇钢班组认为钢包烘烤不良,镇静过程中,钢液温度下降较快,为避免浇铸短尺,浇铸过程未严格按照工艺(L)025-2007执行,由于浇注温度偏高,注速过快,钢锭激冷层过薄,钢的热应力、组织应力及钢水静压力的共同作用造成全炉钢锭顺裂。
2、责任落实和处理意见:
对浇钢丙班按二级质量事故考核。
3、整改措施:
1)设备维护人员立即对0#炉的天然气阀门进行处理。
2)浇钢班组必须深刻认识波纹锭浇铸参数的重要性,浇铸过程必须严格按照工艺(L)025-2007执行。
违者按重大违规考核。
3)生产组在生产条件不具备的情况下(如:
天然气不足、保护渣水分超标),不得安排波纹锭的生产。
关于3070-121820Cr模底跑钢案例分析
1、事故概述
炼钢三车间于2007年8月6日冶炼3070-121840Cr技术条件为GB/T3077-1999生产锭型为700*24支,计划产量16.656t。
在浇注第一锭盘过程中,当钢水浇注至锭身4/5时,2#外圈锭模底部突然跑钢,封堵无效;小锭盘挽救两支下渣无法使用,实际浇注700*12支,废700*12支,废品量8.328t。
2、原因分析
事故发生后,含增炼钢站站长与车间相关人员进行了事故讨论分析,并一致认为浇注第一锭盘至锭身4/5时跑钢造成8.328t废品的原因是:
1从现场来看,砌砖时砖尾和衬砖有些偏低,班组检查时也发现过,并处理,但处理效果不是很好。
2尾砖和衬砖两侧的砂子没插紧,砖上面的灰条没末抹均匀。
3下口砖打得有点松。
3、整改措施
1对铸锭班组进行事故通报、教育,对事故人员进行检查,考核。
2通过对本次事故的教训,吸取经验,加强对班组人员的管理和培训,提高班组操作技能。
关于407F3-2017JS45纵裂的三级质量事故分析
1、事故概述
10月23日,407F3-2017JS45CJX-L012-20063.3t×12支因精整时有6支波纹锭纵裂,经现场确认后判废,构成三级质量事故。
经调查,该炉钢是10月19日炼钢3横班冶炼,冶炼设备运行正常。
15:
15开始熔化;17:
49化清,温度1599℃,C:
1.41%(其它成分均满足冶炼要求);18:
40温度1638℃,C:
0.31%、P:
0.015%Cr:
0.17%,由于3#加热炉冶炼T91,造成等工位约1个小时;20:
07~20:
10温度1651℃,出钢;因C含量偏低,包中增C剂6袋。
20:
18~20:
50在3#加热炉冶炼,总体情况正常。
但由于入罐C仍较低(C:
0.31%),加热炉增C粉60kg,增C量较大(达0.09%)。
浇注第二盘时,锭身速度为612秒,偏快(炼钢工艺要求下限为660秒)。
模冷24小时后脱模发现钢锭纵裂6支19.8吨。
2、原因分析:
1)电炉因等加热工位而长时间无法出钢,钢液吸气较为严重;终点碳低,出钢过程和LF精炼过程增碳量大(共计0.18%),对钢液纯净度不利;
2)铸锭浇注二盘锭身注速过快,钢锭激冷层薄,易产生裂纹。
3)由于中碳含量的碳、合结钢表面裂纹倾向大,加上冶炼、浇注过程中关键控制点操作不好,更易产生裂纹。
3、整改措施
10月24日炼钢四车间召开了事故分析会,提出了如下纠正措施:
1)车间横班合理组织生产,避免电炉冶炼后期长时间等工位,减少钢液后期送电吸气;
2)电炉班组加强操作,合理控制终点碳,减少还原期大量增碳;
3)浇钢班组必须严格执行工艺要求,防止注速过快导致钢锭激冷层薄弱。
关于4145H(Ф220)轧制超差事故的报告
1、事故概述
2007年11月中旬,轧钢厂大型材车间生产的Ф220mm的4145H大型材大部分出现钢材尺寸偏小的现象,经统计,本次共生产Ф220mm的4145H大型材10炉共88支约290.4吨钢材,经过测量尺寸全部合格的钢材只有28支,不合格的钢材58支约200吨,另有2支因探伤切头已成短尺未上台测量,其不合格率达到68%。
在尺寸超差的58支中,有55支属于钢材头部1~2.5米范围内局部超差(定尺钢,切除超差部分后无法交货),有3支为整支钢材通根超差。
超差尺寸为Φ214-217mm。
2、调查分析:
1)Ф220mm规格大型材由825初轧机轧制,在轧制时采用夹板盒子进行轧制,如坯料控制不精容易卡钢,通常采取压头子进行轧制,但压头子后坯料头部尺寸偏小易造成钢材头部未充满而尺寸偏小。
因此对轧钢人员轧制技能要求较高。
2)该炉期生产的Ф220mm4145H采用4.6吨锭型,一锭一材。
规程要求:
每炉钢轧第一支锭时必须测量尺寸,符合尺寸公差后方可进行正式生产。
根据轧钢操作原始记录,在实际操作中也做到了尺寸测量,但钢材的尺寸检查不到位,在卡量钢材时仍按通常操作方式只卡量钢材中部(尺寸符合要求),而未对易出现尺寸超差的钢材头部未进行卡量,因此错误地认为整支钢、整炉钢尺寸合格,造成连续出现钢材头部尺寸超差而未有一个操作工人发现此问题。
3)操作工操作时随意性太强,对压下指针数和坯料开坯尺寸控制不准确,造成部分钢材通根尺寸超差。
综上所述,产生此次质量事故的原因主要是人为因素:
1)轧钢工在825初轧机轧制Ф220mm以上大规格大型材的操作技能有所欠缺。
2)对钢材尺寸控制不严、尺寸测量不到位。
3)轧钢操作工责任心不强,操作随意性太强。
特别是对4145H这样的重点品种更应该加强生产过程的质量控制。
3、纠正预防措施:
1)提高轧钢工的质量意识,使其认识到产品质量的重要性。
多利用班前会、班组学习会进行质量分析和讨论,以便于提高和改进产品质量。
2)加强轧钢工的工作责任心,在工作中要做到勤观察、勤测量。
对Ф220规格大型材要改进测量方式,对钢材的头、中、尾三点都要进行卡量,并要对钢材进行取样测量以保证钢材的公差尺寸符合要求。
3)提高轧钢工的操作技能,改进轧制方法以保证轧制尺寸。
4)对Ф220规格的夹板盒子进行调整和改进,并将坯料和大型材的夹板盒子分开管理,保证轧材的尺寸精度。
5)加强质量信息的沟通,出现质量问题要及时、准确向相关部门反映,以保证质量问题得到及时解决。
4、事故责任及考核
1)产生此次质量事故主要是轧钢操作工责任心不强,质量意识淡薄,对钢材尺寸控制不严和检测不到位所造成的。
2)质保部考核轧钢厂10000元,并责成轧钢厂对责任单位进行质量考核。
关于40Mn2纵裂质量事故分析
2008年2月13日,冶炼炉号为4083-33(F2-57)的40Mn2发生纵裂8支×3.5t,合计28吨的三级质量事故。
一、冶炼情况:
该炉钢2月13日早班一横班09:
35装料,09:
40送电熔化,11:
20熔清取样,11:
53测温1587℃,11:
57取2样,11:
58进入氧化,12:
24温度达到1649℃出钢;电炉冶炼时间共计175分钟。
脱碳量为0.39%。
12:
35入罐,测温为1530℃,13:
12调电Mn550Kg、Fe-Si30Kg,13:
50测温1586℃喂Al线80m,静吹Ar至14:
10温度1570℃吊包,镇静380秒开包浇注。
二、原因分析:
1、该炉钢计划为S50Cr,由于化清C低(0.71%)请示值班后决定改炼40Mn2。
由于氧化时间较短(26分钟),炉前综合氧化操作做的不太好,熔池沸腾不均匀。
虽然保证了脱碳量,但去气去夹杂的效果不太好。
2、加热炉操作人员对本钢种也未引起足够重视,吊包温度偏高(1570℃),后期浇铸操作不易控制,导致热应力较大,从而产生裂纹。
以上两点是造成本次三级质量事故的主要原因。
由于40Mn2裂纹倾向较大,必须精细操作才能有效防止裂纹问题的发生。
三、纠正预防措施:
1、炉前切实做好综合氧化操作,避免单管吹氧。
氧化末期要保证一定的纯沸腾时间,达到充分去气去夹杂。
2、吊包温度和镇静时间控制合理。
3、对于冶炼中碳碳、合结钢,操作上不能大意,严格按规程执行。
4、裂纹倾向较大的钢种,不能红送的要及时下坑。
1Cr11Mo1NiWVNbN电极棒成份Ni高
1、事故概述
特冶车间07年12月27日真空感应炉生产的电极棒1Cr11Mo1NiWVNbNT07M4-243冶炼过程时,炉中分析结果Ni分别为0.32%、0.40%,Ni成份偏低,标准要求Ni:
0.40-0.70%,炉前操作人员计算后补加了11kgNi(专题人员未在现场),因未考虑到出炉前需加入的Ni-Mg(Ni含量约70%左右)中Ni的含量,最终造成成品Ni:
0.80%,超出上限,后经联系用户同意让步下流。
2、原因分析
事情发生后,经特冶车间联系相关人员召开事故讨论会,一致认为造成1Cr11Mo1NiWVNbN电极棒成品Ni高的因素为:
1)查铁票配料无错误,炉中冶炼时怀疑因坩埚壁的吸收造成Ni含量偏低,炉前操作人员补加Ni时按6300kg钢水量进行计算补加11kg,而实际装入量为5300kg;
2)计算配入量时,未考虑9.353kg的Ni-Mg合金料中Ni对本炉钢的影响,未将Ni含量计算进去;
3)值班专题人员不在现场,炉前冶炼出现异常时,联系不上。
3、整改措施
1)加强班组人员的责任心教育,炉前补加合金料时,应谨慎考虑,周全计算,应有专人负责(如班长)检查核对,防止出错;
2)对冶炼中使用的其它合金料的成份含量造成的影响因考虑周全,防止出类似事故;
3)重点产品冶炼时,值班专题人员要在现场。
质量小知识一:
质量管理体系基础知识――有关合格(符合)的术语
1合格(符合)conformity
满足要求
注:
该定义与ISO/IEC指南2是一致的,但用词上有差异,其目的是为了符合GB/T19000的概念。
注2:
术语“conformance”是同义的,但不赞成使用。
2不合格(不符合)nonconformity
未满足要求
3缺陷defect
未满足与预期或规定用途有关的要求
注1:
区分缺陷和不合格的概念是重要的,这是因为其中有法律内涵,特别是与产品责任问题有关。
因此,术语“缺陷”应慎用。
注2:
顾客希望的预期用途可能受供方信息的内容的影响,如所提供的操作或维护说明。
4预防措施preventiveaction
为消除潜在不合格或其他潜在不期望情况的原因所采取的措施
注1:
一个潜在不合格可以有若干个原因。
注2:
采取预防措施是为了防止发生,而采取纠正措施是为了防止再发生。
5纠正措施correctiveaction
为消除已发现的不合格或其他不期望情况的原因所采取的措施
注1:
一个不合格可以有若干个原因。
注2:
采取纠正措施是为了防止再发生,而采取预防措施为了防止发生。
注3:
纠正和纠正措施是有区别的。
6纠正correction
为消除已发现的不合格所采取的措施
注1:
纠正可连同纠正措施一起实施。
注2:
返工或降级可作为纠正的示例。
7返工rework
为使不合格产品符合要求而对其所采取的措施
8降级regrade
为使不合格产品符合不同于原有的要求而对其等级的改变
9返修repair
为使不合格产品满足预期用途而对其所采取的措施
注1:
返修包括对以前是合格的产品,为重新使用所采取的修复措施,如作为维修的一部分。
注2:
返修与返工不同,返修可影响或改变不合格产品的某些部分。
10报废scrap
为避免不合格产品原有的预期用途而对其采取的措施
示例:
回收、销毁。
注:
对不合格服务的情况,是通过终止服务来避免其使用。
11让步concession
对使用或放行不符合规定要求的产品的许可
注:
让步通常仅限于在商定的时间或数量内,对含有不合格特性的产品的交付。
12偏离许可deviationpermit
产品实现前,偏离原规定要求的许可
注:
偏离许可通常是限定的产品数量或期限内并针对特定的用途。
13放行release
对进入一个过程的下一个阶段的许可。
注:
在英语中,就计算机软件而论,术语“release”通常是指软件本身的版本。
管理类
09SiVL和3Cr13混钢的调查分析
1、混钢事故简述:
在2007年5月16日中班和5月17日夜班,轧钢厂扁平材车间轧制一批钢:
07E-3413407F1-16009SiVL成品规格8×450mm。
在一些钢轧制为成品后,在热剪剪切时发现切口不正常,并有碎断现象。
对于此异常情况车间马上通知停止轧制。
在2007年5月17日早班,经轧钢厂大型材车间火花工初步鉴别是铬不锈系列钢。
2、调查分析:
1)轧钢厂扁平材车间的轧制生产情况:
此批钢的坯料是由轧钢厂大型材车间开坯,坯料号为0705-4145,共转运60块坯料到扁平材车间,重量29.84吨。
扁平材车间已经轧制11块坯料,在发现异常停轧,其余未轧制钢坯大部分进了缓冷坑,另有10多块放在车间料场。
查看这些未轧制的钢坯,在钢坯的端部有407F1-160标识,钢坯也都未进行扒皮处理(09SiVL钢坯一般不需要扒皮,而铬不锈系列钢坯需要全扒皮处理)。
查询结论:
从钢坯的端部有正确的炉号标识,同时钢坯也都未扒皮处理来看,扁平材车间未产生混钢,混钢应该是在前面车间产生。
2)炼钢四车间的红送情况及轧钢厂大型材车间的均热和轧制生产情况:
由于火花工在轧钢厂扁平材车间的初步鉴别是铬不锈系列钢,通过查询,有一炉3Cr13(炉号407F3-795)和该炉钢(407F1-16009SiVL)同时装车红送到大型材车间,因此对于这两炉钢的装车红送、装炉和出炉轧制情况作了重点查询分析。
①炼钢四车间装车红送情况:
这两炉钢都是在2007年5月12日浇铸和装车,同一时间发运的。
407F3-7953Cr13:
浇铸完时间是:
15:
31,共浇铸3.5t锭11支和2.2t锭1支;拔帽口时间:
17:
50;实际装车支数:
12支;装完车时间:
19:
00;火车拖出时间:
19:
40;红送车号为:
2405。
407F1-16009SiVL:
浇铸完时间是:
15:
54,共浇铸3.5t锭11支;拔帽口时间:
18:
12;实际装车支数:
11支;装完车时间:
19:
30;火车拖出时间:
19:
40;红送车号为:
2404。
②轧钢厂大型材车间接收钢锭和进均热炉以及轧制情况:
大型材车间接收这两炉钢红送钢锭的登记时间都是2007年5月12日21:
00。
407F3-7953Cr13:
大型材车间配的生产卡号是0705-4144,3.5t锭11支和2.2t锭1支,共12支锭全部装于均热炉1#坑,于2007年5月12日21:
15装炉,加热4h,于2007年5月13日1:
15~2:
05轧制,其0705-4144卡号又分4个分号:
0705-4144轧制100×420mm,共轧35支坯,重量21.14吨,用锭3.5t×7支;0705-4144A轧制80×370mm,共轧4支坯,重量1.79吨,用锭2.2t×1支;0705-4144B轧制80×470mm,共轧12支坯,重量6.04吨,用锭3.5t×2支;0705-4144C轧制80×420mm,共轧14支坯,重量6.04吨,用锭3.5t×2支;
在扁平材车间发现混钢后,大型材车间对0705-4144、0705-4144A、0705-4144B、0705-4144C全部打火花检测,结果是0705-4144A的4支坯是3Cr13,其余0705-4144、0705-4144B、0705-4144C都是09SiVL。
407F1-16009SiVL:
大型材车间配的生产卡号是0705-4145,3.5t锭11支,其中10支全部装于均热炉5#坑(另外一支由于脱模脱不掉退回炼钢四车间),于2007年5月12日23:
15装炉,加热3h30min,于2007年5月13日2:
45~3:
15轧制,此炉钢只轧制了一个卡号:
0705-4145轧制80×470mm,共轧60支坯,重量30.2吨,用锭3.5t×10支。
③对于407F1-160那一支因脱模脱不掉退回炼钢四车间的钢锭分析情况:
在扁平材车间发现混钢后,炼钢监督站从退回炼钢四车间的那一支钢锭帽口处取样,经光谱分析该钢的铬成份,分析结果是Cr13型钢的铬成份。
④轧钢厂大型材车间和炼钢四车间的查询分析和结论:
轧钢厂大型材车间对这两炉钢装钢时间是分开的,装钢起始时间间隔2小时,并且一炉装的1#坑,一炉装的5#坑,两炉没有混装,而且两个炉座相隔也较远,不存在装炉时吊错炉座的情况。
对407F3-7953Cr13这一炉轧制的几个卡号打火花检测,只发现1支2.2t锭轧制的4支坯为3Cr13,其余都是09SiVL,因此可知两炉钢除1支2.2t锭型外,其它11支刚好对混。
此外,退回炼钢四车间的1支407F1-160钢锭,经检测也是3Cr13,也证实了在红送车皮上已经混钢了。
3、调查结论:
混钢是炼钢四车间在转运时搞混的。
在装这两炉钢的过程中,刚好遇到天车交接班时间,炼钢四车间在两炉钢都装完11支钢锭后,在吊剩下的1支3Cr13时把这支钢锭吊错车,同时这两炉钢在锭型、支数方面差异也仅仅是这支2.2t的钢锭,因此在填写车号时也根据最后的这支钢锭把两个车的炉号和钢种搞反。
4、纠正和预防措施:
炼钢四车间应对红送钢锭的转运过程加强监控,确保料票相符,特别要加强交接班管理,交接班转运钢锭时应认真核对炉号、钢种和钢锭支数,确保与生产卡片一致,避免类似混错事故的发生。
关于5月初炼钢四车间几起重大违章的分析
1、情况简述:
2007年4月30日~5月10日,炼钢四车间有5炉钢因出完钢将钢水搁置在铸锭跨超过50分钟,被判为重大违章。
搁置时间过长被判为重大违章明细:
日期
钢种
电炉炉号
精炼炉号
出完钢时间
搁置在外时间
出钢时,各精炼工位情况
4月30日
1Cr12Ni2Mo1W1V
4071-473
407V1-582
15:
58
57分钟
V2检修;
F2加热407F2-625,时间为14:
44~17:
12;
F3加热407F3-689,时间为16:
38~18:
05;
V1处理407V1-581。
4月30日
1Cr13
4074-167
407V1-578
2:
26
70分钟
V2检修;
由于4071-469快出钢,F2等该炉入罐;
V1处理407V1-577,时间为0:
05~3:
23。
5月3日
Cr12MoV
4071-491
407V1-604
7:
52
68分钟
V2检修;
F2加热407F2-649,时间为7:
30~10:
15;
F3配合V1精炼407V1-603(407F3-709),时间为5:
50~9:
10。
5月3日
42CrMo
4075-645
407F3-712
12:
22
53分钟
V2检修;
F2配合V1精炼407V1-605(407F2-651),时间为11:
53~15:
00;
F3加热407F3-711,时间为11:
25~13:
10。
5月10日
H13
4074-197
407V2-536
6:
07
73分钟
F3配合V2精炼407V2-534(407F3-773),时间为5:
45~8:
30;
F2因上除尘设备,早上8:
00~晚上8:
00不炼钢;
V1处理407V1-665,时间为3:
28~7:
16。
2、调查分析:
1)工位紧张:
⑴设备方面:
炼钢四车间在1#炉附近上除尘设备,现场天车调配和冶炼受到影响。
如F2工位因上除尘设备受到影响。
⑵生产安排上:
4月30日6:
20,V2处理完407V2-525便开始停炉检修,直到5月8日才开炉,现场只有F3、F1+V1工位正常。
4月30~5月3日,现场开3台炉子,冶炼钢80余炉,由于产量较高,加上精炼工位较少,导致出钢后等工位的情况较多。
2)由于电炉为保产量,操作抢进度,导致入罐炉外精炼的钢操作负担重、精炼时间久、操作周期长,而电炉出钢后又无法及时入罐,就采取搁置在外的违章处置方式。
由于生产节奏控制不合理,造成恶性循环,严重影响钢的质量,并且影响了生产的连续性。
3、改进措施建议:
由于工位紧张,炼钢四车间已将部分2Cr13以上的Cr不锈钢改为单加热,以缓解工位紧张的压力。
但最根本的措施应为:
⑴在工位紧张的情况下,合理控制生产节奏,提前采取预防措施和准备紧急预案。
⑵提高炉前精细操作意识,保证冶炼质量,为炉外精炼创造良好条件,以有效缩短精炼时间,提高生产的连续性。
G20Cr2Ni4A外事混钢事故分析
1、质量问题简述:
外事反映G20Cr2Ni4A307A52-155中混有2Cr12NiMo1W1V外事混钢的情况。
2、质量问题调查和分析
质保部含增质监总站立即组织各相关车间有关人员对G20Cr2Ni4A生产过程中所涉及的可疑炉号进行了调查分析,排查中发现特冶车间冶炼的2Cr12NiMo1W1V307A6H2-80-4成分异常,取样作化学分析其成份为G20Cr2Ni4A成份规格,并且此炉与外事炉号307A52-155为同一天出罩,经成份对比,确定307A6H2-80-4锭为G20Cr2Ni4A,与外事反馈混钢信息相符合。
原因分析:
①车间因场地有限,缓冷区域仅分为两块,分别为炉座A1-A4和炉座A5-A6两块区域,发生混钢的两炉号为同一区域内存放;
②事故发生日期为春节初一、初二节假日期间,当事人因工作责任心不强,出罩时未及时在钢锭上标写、校对钢种、炉号,致使钢种、炉号标识错误,造成混钢。
3、整改建议:
①电渣钢锭入罩时及时在缓冷罩上书写炉号、钢种,严格核对冶炼记录;
②出罩过程中做到钢锭逐支吊取逐支注明炉号、钢种并严格核对缓冷罩上的炉号、钢种,杜绝钢种、炉号写错。
③车间加强对标识的日常巡查工作,对未及时进行标识或标识不规范等行为进行考核。
一起“特殊”0Cr13Mn成品板材成份不合质量问题分析
1、质量问题概述
2007年6月含增质监总站综合判定组判定0Cr13Mn,炉号405V1-1824、405V1-1454、405V