轴承座的工艺及工装设计.docx
《轴承座的工艺及工装设计.docx》由会员分享,可在线阅读,更多相关《轴承座的工艺及工装设计.docx(23页珍藏版)》请在冰豆网上搜索。
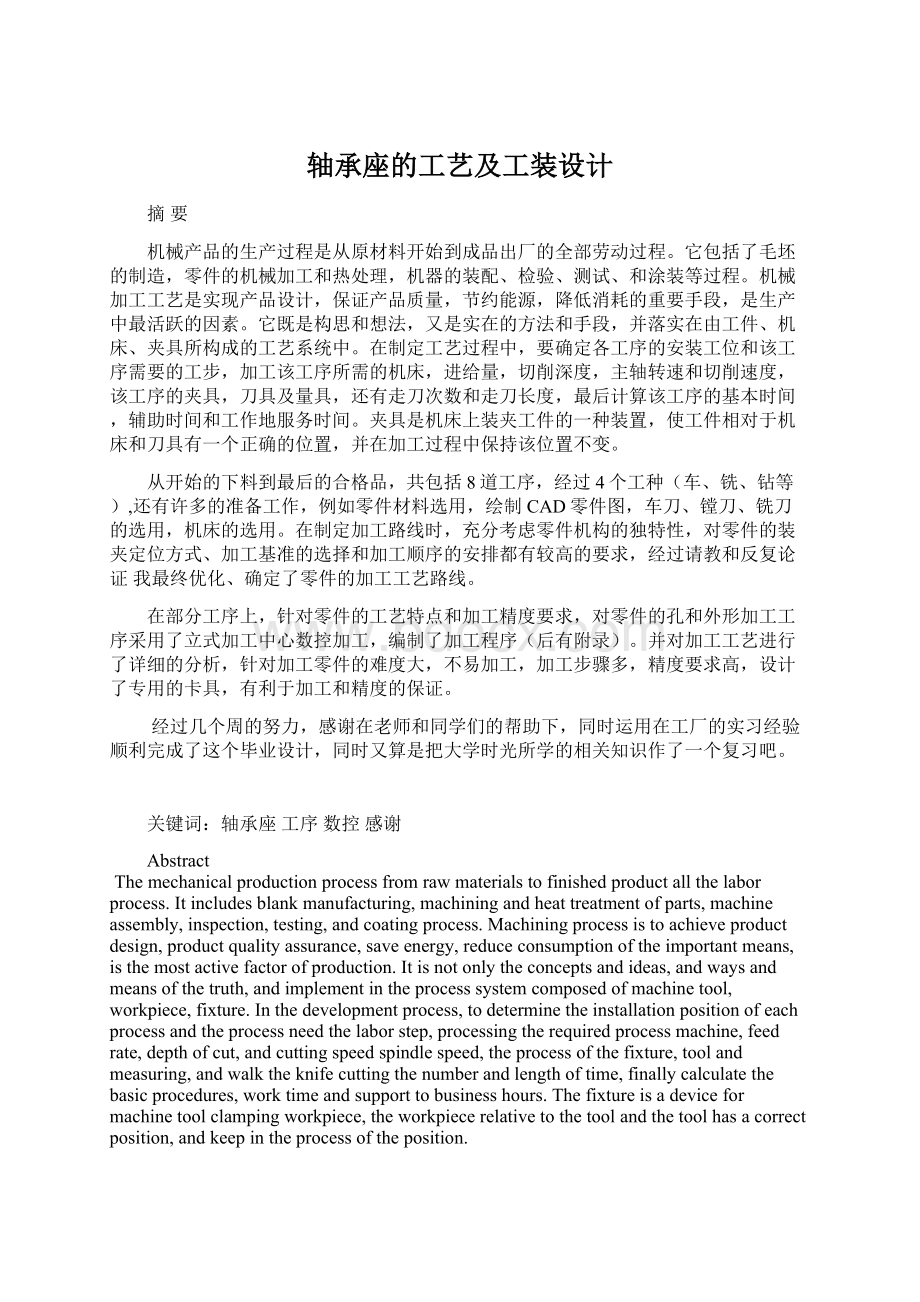
轴承座的工艺及工装设计
摘要
机械产品的生产过程是从原材料开始到成品出厂的全部劳动过程。
它包括了毛坯的制造,零件的机械加工和热处理,机器的装配、检验、测试、和涂装等过程。
机械加工工艺是实现产品设计,保证产品质量,节约能源,降低消耗的重要手段,是生产中最活跃的因素。
它既是构思和想法,又是实在的方法和手段,并落实在由工件、机床、夹具所构成的工艺系统中。
在制定工艺过程中,要确定各工序的安装工位和该工序需要的工步,加工该工序所需的机床,进给量,切削深度,主轴转速和切削速度,该工序的夹具,刀具及量具,还有走刀次数和走刀长度,最后计算该工序的基本时间,辅助时间和工作地服务时间。
夹具是机床上装夹工件的一种装置,使工件相对于机床和刀具有一个正确的位置,并在加工过程中保持该位置不变。
从开始的下料到最后的合格品,共包括8道工序,经过4个工种(车、铣、钻等),还有许多的准备工作,例如零件材料选用,绘制CAD零件图,车刀、镗刀、铣刀的选用,机床的选用。
在制定加工路线时,充分考虑零件机构的独特性,对零件的装夹定位方式、加工基准的选择和加工顺序的安排都有较高的要求,经过请教和反复论证我最终优化、确定了零件的加工工艺路线。
在部分工序上,针对零件的工艺特点和加工精度要求,对零件的孔和外形加工工序采用了立式加工中心数控加工,编制了加工程序(后有附录)。
并对加工工艺进行了详细的分析,针对加工零件的难度大,不易加工,加工步骤多,精度要求高,设计了专用的卡具,有利于加工和精度的保证。
经过几个周的努力,感谢在老师和同学们的帮助下,同时运用在工厂的实习经验顺利完成了这个毕业设计,同时又算是把大学时光所学的相关知识作了一个复习吧。
关键词:
轴承座工序数控感谢
Abstract
Themechanicalproductionprocessfromrawmaterialstofinishedproductallthelaborprocess.Itincludesblankmanufacturing,machiningandheattreatmentofparts,machineassembly,inspection,testing,andcoatingprocess.Machiningprocessistoachieveproductdesign,productqualityassurance,saveenergy,reduceconsumptionoftheimportantmeans,isthemostactivefactorofproduction.Itisnotonlytheconceptsandideas,andwaysandmeansofthetruth,andimplementintheprocesssystemcomposedofmachinetool,workpiece,fixture.Inthedevelopmentprocess,todeterminetheinstallationpositionofeachprocessandtheprocessneedthelaborstep,processingtherequiredprocessmachine,feedrate,depthofcut,andcuttingspeedspindlespeed,theprocessofthefixture,toolandmeasuring,andwalktheknifecuttingthenumberandlengthoftime,finallycalculatethebasicprocedures,worktimeandsupporttobusinesshours.Thefixtureisadeviceformachinetoolclampingworkpiece,theworkpiecerelativetothetoolandthetoolhasacorrectposition,andkeepintheprocessoftheposition.
Fromthebeginningofthenextexpectedqualifiedlast,includingatotalof8processes,after4types(cars,milling,drilling,etc.),therearemanypreparations,suchaspartsmaterialselection,drawingCADpartsdiagram,selectionofturning,boring,millingcutter,machinetoolselection.Inthedevelopmentofprocessingroute,fullyconsidertheuniquenessofpartsofthebody,thepartsoftheclampingandlocatingmethod,machiningdatumselectionandprocessingsequencearrangementhavehigherrequirements,throughtheconsultandrepeateddemonstration,Ifinallyoptimizationprocesstodeterminetheparts.
Inthepartoftheoperation,accordingtotheprocesscharacteristicsofthepartsandmachiningprecisionofparts,andtheshapeoftheholesmachiningprocessusingCNCverticalmachiningcenter,machiningprogram.(aftertheappendix).Andthemachiningprocesswasanalyzedindetail,thepartsoftheprocessingdifficultyisbig,noteasyprocessing,processingsteps,highprecision,isdesignedwithaspecialfixture,toensuretheaccuracyofprocessingand.
Afterafewweeksofhardwork,thankstothehelpoftheteacherandclassmates,alsousedinthefactoryinternshipexperiencesuccessfullycompletedthegraduationdesign,alsoistheknowledgeoftheuniversitytimeforareview.
Keywords:
BearingblockProcessesNumericalcontrolThank
引言
随着电子及数字技术的飞快发展,计算机与其数字程序在机械制造领域得到了广泛的应用,计算机数字程序自动控制加工机床和加工中心等高精度、高效率的新一代机床正好满足市场竞争和工艺发展的需要。
在轴承座这个传统零件的加工过程中,我们采用新工艺、新思维,在原有经验的基础上有所改进加工出来。
本论文从生产实践的角度出发,对本零件的加工工艺过程进行了分析,本论文共分9的部分,分别是:
零件的工艺性分析、刀具的选择、量具的使用、机床的选择、零点分析和基点计算、数控编程、零件的加工过程。
通过这一步一步的学习真正提高了本人的学习和设计能力,为将来的工作奠定了基础。
针对零件的工艺特点和加工精度要求,对零件的孔及外型面加工工序采用了数控加工,并编制了加工程序,并对数控加工工艺进行了详细的分析,针对加工零件的加工难度大、零件不易装夹,加工步骤多的特点,专门使用了一个专用夹具,以利于零件的加工。
1零件的工艺性分析
1.1零件的材料和结构分析
零件的材料和结构决定了加工方案的选用,了解结构更能理解零件的作用和价值。
1.1.1零件的材料分析
机械工业生产的原材料主要包括:
金属材料和非金属材料。
1.金属材料主要包括:
钢(碳钢、合金钢、结构钢),铸铁(白口、灰口、可锻、球墨、)铜,铝,镁等不锈钢。
非金属材料包括:
塑料、橡胶、尼龙、石蜡、木、电木等。
本零件的材料为铸铁,铸铁是根据碳在铸铁中存在的形式不同来划分的,这大体分为3大类。
2.白口铸铁
碳除微量溶于铁素体外,其余全部以铁素体的形式存在。
其端口银白色,故称白口铸铁。
这种铸铁中含有大量莱氏体,性能硬而脆,难以切削加工,所以很少用于零件加工。
3.灰口铸铁
碳全部或大部分以游离状态的石墨存在于铸铁中,其端口呈灰色,故称灰口铸铁。
它在工业中最常用。
4.麻口铸铁
这种铸铁组织中既有石墨又有莱氏体。
属于白口铸铁和灰口铸铁的过渡部分。
这种铸铁有很多的硬脆性,工业上也很少用。
5.材料的力学性能:
强度和塑性、硬度、冲击韧度、疲劳极限、断裂韧度。
材料的硬度主要包括:
布氏硬度、洛氏硬度、莫氏硬度等。
以洛氏硬度为例:
HRC<32的材料较软HRC32—37一般HRC37—43中等HRC43—48硬HRC>48超硬
我设计的轴承座材料:
HT200,抗拉强度160-220Mpa,能够承受中等载荷如机座、支架、轴承座等零件。
1.1.2零件的结构
一般情况下零件主要分为以下几种结构:
轴、筒类:
传动轴、连接轴等
盘、片类:
飞轮盘、齿圈、轮毂等
机匣类:
传动机匣、机匣壳体、机匣上盖、泵体等
齿轮类:
直齿、斜齿、锥齿轮、齿条、蜗中轮、蜗杆等
本零件其结构特点为:
①属于中、小型盘类零件②回转类,形状结构复杂
加工不易变形,刚性一般。
有四个均匀分布的耳朵圆台。
1.2零件精度和基准的分析:
零件的精度和基准决定零件的可靠性,确保零件的作用和价值
1.2.1零件精度
1.尺寸类型及本零件的尺寸分析包括:
直径、半径、厚度、倒角、 圆弧、圆角等。
本零件的尺寸类型主要有(单位是mm):
1厚度:
50
2直径尺寸:
Φ238Φ138Φ126Φ111Φ75Φ62Φ7.5(四个均布)φ6.5±0.1(三个均布)
3圆弧:
R10,
4角度:
45°
5槽宽:
3.5±0.01
尺寸精度特点:
一般<0.020mm
本零件的尺寸精度包括:
自由公差以及工艺保证尺寸。
2.粗糙度对零件表面的影响:
减小表面粗糙度可提高零件的接触刚度,密封测
量精度。
生产加工中:
大于3.2的是要求粗糙度较低3.2----1.6为一般要求
1.6---0.8为中等要求小于0.8为粗糙度要求较高工件
本零件粗糙度为:
一般1.6,部分3.2属于一般要求
形位公差包括:
平行度、同轴度、垂直度等
本零的形位公差有:
D.B基准的同轴度要求,D.A也有同轴度的要求.靠近B基准的表面还有垂直度的要求。
1.2.2工艺基准:
工艺基准是在工艺过程中采用的基准,根据作用的不同有可分为工序基准、定位基准、测量基准和装配基准。
下面重点介绍一下定位和测量基准。
1.定位基准的选择应遵循以下内容:
A与测量基准重合
B稳定性好
C定位误差小
D控制尺寸和位置
E夹具结构简单
本零件定位基准选择:
由于要与测量基准重合,因此选在工件支撑表面及内孔圆心上。
2.测量基准的选择通常为:
A夹具面
B零件的上端面
C与坐标系重合
D与定位基准重合
本零件的测量基准:
A选择零件圆心为外形、外圆弧及平均分布在零件的四个孔的
测量基准。
B选择工件的底面支撑平面为沟槽深度尺寸的测量基准。
3.支撑面的选择应考虑:
①增加刚性(辅助支撑)②限制自由度
本零件支撑面为:
工件外径上有环形槽的最近底平面
夹紧面的选择原则:
A变形小B使用方便C结构简单
本零件的压紧面为:
工件的上表面
1.2.3加工余量:
1.余量大的先加工
2.加工路线要合理
3.首先看一下什么是工艺加工路线。
加工路线是指制定工艺过程的总体布局,其主要任务是在确定加工面得定位基准和装夹方法后,选择各个加工表面的加工方法和加工方案,确定各个表面的加工顺序以及整个工艺过程中的工序数目和各工序内容。
然后将其所需的辅助、热处理等工序插入到机械加工路线中的适当位置,就得到了机械加工工艺路线。
4.工序的集中与分散
工序集中是指零件的加工集中到少数几个工序中完成,每道工序加工的内容较多,工艺路线短。
其特点是:
可以采用高效机床和工艺加工设备,生产效率高;减少设备的数量以及操作工人和占地面积,节省人力、物力;减少工件的安装次数,有利于保证表面间的位置精度,还能减少工序间的运输量,缩短生产周期;采用的工装设备结构复杂,专业化程度高,成本高,调整维修困难,生产准备工作量大,转换新产品周期长。
工序分散就是指每道工序的加工内容很少,甚至每道工序只含一个工步工艺路线很长,主要特点是:
设备和工艺设备比较简单,便于调整,生产设备工作量少,有易于平衡工序时间,容易适应产品的交换;对工人的技术要求较低;可以采用最合理的切削用量,和减少机动时间;所需设备和工艺装备数目多,操作工人多,占地面积大。
5.基准的选定
基准先行即用作精基准的表面先加工出来,然后以精基准定位面来加工其他的表面。
先粗后精,整个工件的加工应是粗加工在先,半精加工其次,最后安排精加工和光整加工。
先主后次即先安排主要的表面。
先加工那些表面精度、配合精度等较高的表面,在以它们为基准加工其他的表面。
先面后孔即先加工基准面再加工孔,这样加工出来精度就比较高。
本零件刚度一般,加工的路线大致如下:
(1)下料,把中间的内孔都铸出来,还有不加工的凹槽。
因为凹槽是不用加工的,这样可提高效率。
(2)在车削之前对铸件进行热处理消除内应力,这样有利于切削。
(3)用三爪卡盘卡Φ148的内圆粗车Φ114到Φ111.
(4)调头用反装的三爪卡盘卡Φ111的外圆,粗车端面G、F及外圆Φ196。
精车F。
G端面保证15mm。
粗镗内孔Φ149留0.5mm余量。
精镗Φ149到尺寸且保证垂直度。
粗镗、精镗内孔到尺寸Φ62。
倒角。
(5)调头。
有三爪自定心夹盘软爪撑Φ149内圆,粗车外圆Φ138的外圆。
精车外圆Φ138至尺寸及大端面至粗糙度Ra1.6并保证13mm。
粗镗内圆Φ75留余量0.5mm。
精镗Φ75至尺寸及端面并保证22mm满足垂直度要求。
精车阶梯孔保证轴向尺寸13mm。
倒角。
(6)热处理。
(7)用专用卡具在立式加工中心上用Φ20的铣刀铣外形,钻孔、镗孔、攻丝。
(8)去毛刺。
(9)终检。
补充说明一下:
对于铣型面的加工我采用Φ40的端铣刀使这个尺寸一次加工合格。
由于余量较大,所以在加工时应该用较小的mm,因此.在铣削去余量的过程中,其去除余量的进给量,避免损坏刀具。
对于外形的加工,由于我所选择的铣刀直径为Φ20,所以尺寸不能大于铣刀直径的一半。
由于上道工序加工余量不是很大,所以我们一刀既可完成加工。
对于均布孔的加工,首先用Φ2.5mm中心钻加工一个4mm深的孔作为钻头的引导,起到定位作用;再用Φ6.5mm的钻头钻13mm深的通孔,钻头的加工余量为直径尺寸为6.5mm深度为4mm;最后选择Φ7mm镗刀加工具有位置度要求的孔其直径方向余量为7mm-6.5mm=0.5mm。
2刀具的选择
2.1刀具材料
刀具是数控加工中重要内容之一,它不仅会影响机床加工效率而且直接影响加工质量,编程时刀具通常考虑到加工工序内容,工件材料等因素。
与传统的加工方法相比数控加工对刀具的要求更高不仅要求精度高,刚度好,耐用度高,而且要求尺寸稳定,安装调整方便,这就要求采用新型优质材料制造数控加工刀具,并优选刀具参数。
我在选择刀具时的标准是:
结合实际情况(包括加工设备的满足、零件的需要),达到预期效果,生产效率最高,损耗最小。
不同的情况不同的对待。
在工业生产加工中主要采用以下几种刀具:
①钢刀:
也叫高速钢刀,可重复使用,成本低、适合加工镁铝等硬度较低的工件。
②硬质合金刀:
材质硬、切削性能好,适合加工中等硬度材料。
③陶瓷:
材质硬,耐磨损,但抗冲击性能差。
④涂层刀:
涂层物主要包括氮化碳、氮化碳+AL2O2+氮化钛。
特点:
耐磨损,抗冲击。
耐高温Vmax=300mm/min。
本零件的加工由于是在数控机床上加工,因此要求精度高、钢度好、耐用度高,而且要求尺寸稳定,安装调整方便刀具。
选择硬质合金刀可以达到较好尺寸精度。
2.2刀具的结构
主要分为:
①整体刀具;②焊接刀具;③机夹刀具(首选)。
本零件的加工应选择的刀具结构为:
中心钻、钻头、铣刀为整体结构。
镗刀首选机夹刀具,镗刀种类:
按主切削刃数量分单刃和双刀,按工件加工表面分内孔和端面,内孔分通孔和盲孔,按刀具结构分固定式,装夹式,可调式。
可调式分微调式和差动式。
具体的有:
盲孔镗刀、通孔镗刀、可转位镗刀、阶台镗刀、人造金刚石镗刀、不锈刚小孔精镗刀、机夹后尾出屑镗刀。
2.3刀具类型
刀具类型主要包括以下几种:
①外径刀(偏刀)②内径刀③切槽刀④螺纹刀。
本道工序加工本工件所选择的立式加工中心上的刀具包括1.D=2.5中心钻。
2.D=6.5钻头.D=7.5的钻头。
3.D=7和8的镗刀。
4.Φ40Φ20的铣刀。
其中,中心钻加工所有的孔防引偏。
¢20铣刀加工R10、R9和R119的圆弧外形。
¢40的铣刀加工外端面的凸台。
加工本工件所考虑刀具的几何参数为:
中心钻:
可选标准型的D=2中心钻。
钻头:
前角可选的大一些。
镗刀:
后角大小保证不与镗孔发生干涉。
¢20铣刀:
半径小于最大的切削量(外形)。
2.4刀具长度的选择
对于刀具长度的选择要考虑到:
①切到最深时,刀架与零件外端面应大于20mm。
②空刀。
加工本工件考虑刀具的长度:
切到最深时,刀架与零件外端面应大于20mm。
2.5几何参数包括以下内容
2.5.1前角
前角r。
前角大,切削层的塑性变形小,切屑摩擦阻力小,切削力和切削热可降低;但前角过大则切削刃和刀头强度降低,散热条件恶化,刀具寿命下降。
前角较小,切屑变形增大,断屑容易。
前角的大小与其他几何参数一样,应依加工要求合理选择。
2.5.2后角、副后角
减小刀具的后刀面或副后刀面与工件之间的摩擦。
但后角过大,会减弱减切削刃强度,并恶化三人条件,使刀具寿命下降。
刃倾角r,1.改变刃倾角的方向和大小,可控制切削的流动方向;2.断续切削时,适当的r可使切削刃逐渐切入和切出工件,缓和冲击,切削平稳;3.负值的人倾角可提高刀尖的抗冲击能力,但过大的负刃倾角会使径向切削力显著增大;4.可增大实际切削前角r。
减小切削变形,使切削轻快;5.可减小切削刃圆角的有效半径,增加锋利性,便于实现微量切削。
2.5.3主偏角
减小主偏角,可减小切削厚度和切削刃单位长度上的负荷;同时由于主切削刃工作长度增大,刀尖角增大,刀具寿命可提高;但主偏角过小会使径向切削力增大,容易引起切削振动。
副偏角K`r,1.可减小副切削刃不工作部分与工件已加工表面之间的摩擦;但副偏角过大,会使刀尖角减小,工件表面的残留面积也增加,刀具的散热条件恶化,表面粗糙度增大。
2.5.4副偏角
副切削刃的工作长度增大,对工件已加工表面的修光作用加强,有利于减小工件表面粗糙度;但过小的副偏角会使径向切削力增大,在工艺系统刚性不足时容易引起切削振动。
加工钢件用负前角,增加钢性。
加工镁、铝等硬度较低的工件适用较大前角。
特别注意后角,镗孔时不应发生干涉。
主偏角:
左右偏刀选93°(让3°增加钢性)副偏角:
切槽加工不干涉,增加加工范围。
2.6刀具半径
R0.4,R0.8,R1,R1.2,R1.6零件与刀具半径相同时,选一致的避免多切。
所选
择的刀尖半径为:
中心钻D=2.5钻头D=6.5钻头D=7.5镗刀D=7镗刀D=8+0.075丝锥D=M8
3量具的使用
3.1测量方法
根据测量精度的不同选择不同的量具进行测量。
0.05以上的可用卡尺测量,0.05以下的使用千分尺。
选择的量具其测量误差占公差的20%以下。
本零件的尺寸要求包括:
3-Ф6.5,Ф62,Ф138。
这里特别讲一下圆柱孔的测量方法:
(1)用内卡钳测量圆柱孔。
这种方法适用性较广,是工厂常用的一种方法。
(2)用极限塞规测量圆柱孔。
极限塞规有通端(孔的最小极限尺寸)组成。
(3)用自制量棒测量大孔。
测量大孔时,还可根据工件的装夹情况和尺寸大小。
(4)用游标卡尺测量圆柱孔。
(5)用内径百分尺测量圆柱孔。
当工件批量较小,而孔的尺寸精度较高时,可使用内径百分尺寸。
(6)用内径百分表测量圆柱孔。
3.2量具类型
通用和专用量具及设备
3.2.1通用
卡尺、千分尺(公法线、螺纹)、内径表(百分表、千分表)、R规、角度尺、测量平台、挂架、块规、塞尺等。
3.2.2专用
塞规、卡板、卡钳等。
3.2.3设备
三坐标测量机、齿轮检查仪、工具显微镜等
3.3量具范围
0-25mm、25mm-50mm、50mm-75mm……1000mm-1500mm。
3.4量具精度
0.001mm、0.02mm、0.05mm、0.1mm。
本零件加工后的尺寸精度测量时考虑到零件的外形结构比较复杂,使用通用量具无法测出全部尺寸,因此选择了使用通用量具与测量设备相结合的方法来完成。
通用量具:
卡尺测量6Xφ6.5孔。
专用设备:
三坐标测量机测量全部外形尺寸及工艺保证尺寸。
4机床选择
4.1机床型号的选择
通过对该零件的分析,了解到该零件是一种小型盘类零件,而且该零件有三组等距孔,在加工中容易产生位置度超差,从而影响该零件的质量。
为此,对该零件进行了仔细的工艺分析。
合理的安排工序、选择合适的加工设备就显得很重要。
总体来说,该零件的精度要求比较高,体积小,重量一般,属于高精度要求。
产品形状尺寸中,要求比较严格的有三个等距孔Φ6.5±0.1,并保证位置度Φ0.1以上是我们所分析认为比较重要的尺寸要求。
要确保他们的合格,还必须选择合适的设备。
要求其加工精度必须能满足零件图纸所要求的精度。
数控机床的种类繁多,不同类型的机床其使用范围也有一定的局限性。
只有在一定的工作条件下加工一定的工件才能达到最佳的效果。
因此,确定选购对象之前,应首先要明确准备加工的对象,每一种加工机床都有其最佳加工的典型零件,如卧式加工中心适用于加工箱体、泵体、壳体等。
而立式加工中心适用于加工箱盖和平面凸轮等单面加工零件,要加工的轴承座为盘类零件而回转类零件,所以选择立式机床,这样即方便装夹,也可以提高工件精度。
通过对现有机床的分析,以及该零件自身特点的加工工艺要求,我最后选择了FANC立式数控加工中心。
4.2机床特点
本机床是一种具有自动换刀装置,三轴控制,全功能精密立式加工中心机床,可以进行强力切削。
机床在高速移动时振动小,低速移动时无爬行,并