年产8万吨异丙苯生产设计毕业设计.docx
《年产8万吨异丙苯生产设计毕业设计.docx》由会员分享,可在线阅读,更多相关《年产8万吨异丙苯生产设计毕业设计.docx(82页珍藏版)》请在冰豆网上搜索。
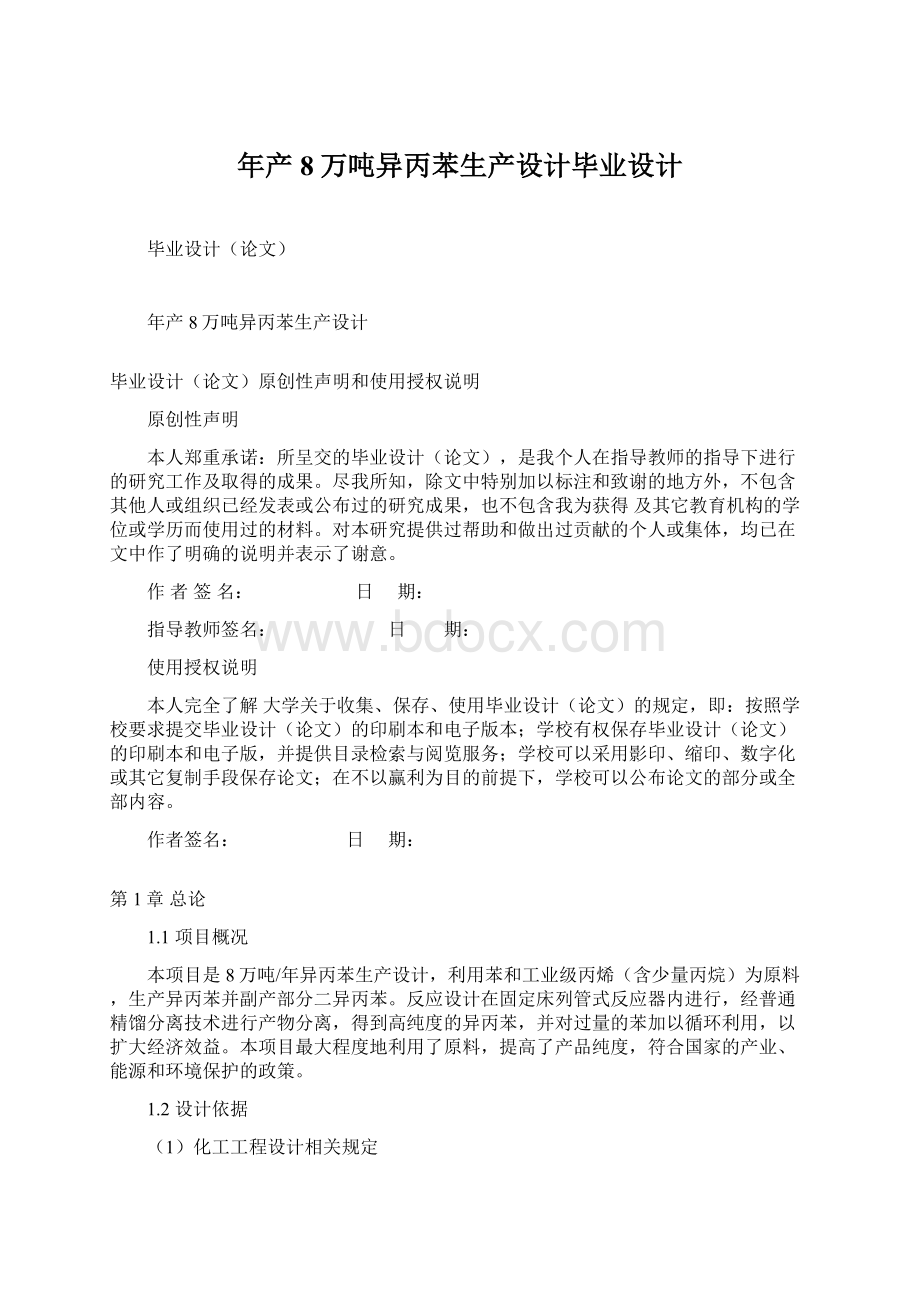
年产8万吨异丙苯生产设计毕业设计
毕业设计(论文)
年产8万吨异丙苯生产设计
毕业设计(论文)原创性声明和使用授权说明
原创性声明
本人郑重承诺:
所呈交的毕业设计(论文),是我个人在指导教师的指导下进行的研究工作及取得的成果。
尽我所知,除文中特别加以标注和致谢的地方外,不包含其他人或组织已经发表或公布过的研究成果,也不包含我为获得及其它教育机构的学位或学历而使用过的材料。
对本研究提供过帮助和做出过贡献的个人或集体,均已在文中作了明确的说明并表示了谢意。
作者签名:
日 期:
指导教师签名:
日 期:
使用授权说明
本人完全了解大学关于收集、保存、使用毕业设计(论文)的规定,即:
按照学校要求提交毕业设计(论文)的印刷本和电子版本;学校有权保存毕业设计(论文)的印刷本和电子版,并提供目录检索与阅览服务;学校可以采用影印、缩印、数字化或其它复制手段保存论文;在不以赢利为目的前提下,学校可以公布论文的部分或全部内容。
作者签名:
日 期:
第1章总论
1.1项目概况
本项目是8万吨/年异丙苯生产设计,利用苯和工业级丙烯(含少量丙烷)为原料,生产异丙苯并副产部分二异丙苯。
反应设计在固定床列管式反应器内进行,经普通精馏分离技术进行产物分离,得到高纯度的异丙苯,并对过量的苯加以循环利用,以扩大经济效益。
本项目最大程度地利用了原料,提高了产品纯度,符合国家的产业、能源和环境保护的政策。
1.2设计依据
(1)化工工程设计相关规定
(2)国家经济、建筑、环保等相关政策
1.3设计原则
本项目本着节约原料和能源、保护环境的前提,生产符合要求的产品并尽可能减少副反应的原则来进行设计,符合国家化工生产的政策。
1.4设计内容
1.4.1基础条件
1、原料及其组成(均为mol%):
(1)工业级丙烯:
纯度≥95%,丙烷≤5%;
(2)苯:
纯度≥99.5%,苯/丙烯=7:
1。
2、产品及其规格:
异丙苯,纯度≥99.5%(m%)。
3、建议工艺条件:
采用UOP法,以磷酸或分子筛作催化剂。
产物主要考虑异丙苯和二异丙苯。
原料中89%的丙烯反应生成异丙苯,3%的丙烯生成二异丙苯。
4、公用工程:
(1)热剂用蒸汽:
根据生产需要选用不同压力级别的蒸汽。
(2)冷剂用循环冷却水:
上水温度可取25℃。
1.4.2设计内容
1、查阅文献,了解设计内容,确定设计基础数据,完成文献综述;
2、生产方案确定及工艺流程设计,绘制工艺原则流程图;
3、主要设备及全装置的物料衡算,列出物料平衡表等表格,绘制PFD;
4、主要设备及全装置的热量衡算(包括热负荷及传热剂用量的计算),列出热量平衡表等表格;
5、主要设备的工艺计算与选型,列出各类设备规格表及设备一览表;
6、确定自控方案,绘制工艺管道及仪表流程图(PID);
7、进行车间及设备布置设计,绘制车间平面布置图及设备平、立面布置图;
8、设计总结,编写初步设计说明书。
1.5建设规模及产品方案
本厂以苯和聚合级丙烯为原料,采用UOP法利用固体磷酸为催化剂生产异丙苯[1],年产量为8万吨。
生产出的异丙苯是一种重要的有机化工原料,主要用来生产用途广泛的苯酚和丙酮[2]。
近年来,异丙苯的需求量大幅度增加,本项目可以极大地满足异丙苯的需求量,为社会创造更多的经济效益。
1.6厂址选择
本项目厂址应位于交通便利,各项设施配套完善的工业园区,园区应有合理的布局,齐全的功能,优美的投资环境;园区内产业链优势明显,化工工业之间有良好的联系,如有生产苯或者丙烯等产品的化工厂以及以异丙苯为原料生产其它产品的化工厂等;另外,附近有为工业园区提供科研条件的高校或者研究院等;政府也为人才的引进以及项目的发展提供有力的政策[3]。
1.7能量利用及环境保护
本项目非常注重能量的综合利用以及环境的保护。
在生产过程中,工艺物流之间相互换热,节约大量的冷凝水以及低压蒸汽等公用工程,这在一定程度上节约了电能;反应过程中,排出的气体作为燃料气;从苯塔蒸出的苯作为循环物料;这些都不但节约了成本,也节约了能量,保护了环境;另外,在厂区内绿化工作做得比较好,大大改善了厂区的环境。
1.8存在问题及建议
1.8.1存在问题
在本项目的设计过程中,存在的问题如下:
(1)软件的运用能力不够成熟。
提到设计,除了正确的设计思路,软件肯定是重中之重。
在设计过程中,需要运用大量的设计软件,比如AspenPlus,Cup-tower以及换热网络模拟软件等等。
平时大家对这些软件并不熟悉,在设计过程中,边学软件边进行设计,在一定程度上锻炼了我们的学习能力,但在很大程度上减慢了设计的进度,造成时间的浪费。
(2)参考文献的短缺。
设计过程需要查阅大量的文献,或许是我们查阅文献的能力不够,总感觉“书到用时方恨少”。
这学期我们并没有上过文献查阅课程,可能会存在这方面能力的欠缺。
1.8.2建议
(1)建议学校会在做设计之前的时间在软件方面和文献方面有相关的课程或者训练,这样可以节约时间,更能保证作品质量。
(3)学生自身也应该注意在各方面提高自己,不要只注重专业课程的卷面成绩。
参考文献:
[1]张佩君.合成异丙苯生产现状及技术进展[J].石化技术,2005,12
(2);62-65,68
[2]有机化工工艺学(第四版)
[3]“三井杯”海之涯团队作品之厂址选择原则。
第2章工艺流程设计
2.1生产方案选择
2.1.1产品性质及规格标准
(1)原料及其组成(均为mol%):
工业级丙烯:
纯度≥95%,丙烷≤5%;
苯:
纯度≥99.5%,苯/丙烯=5.2:
1。
(2)产品:
异丙苯,纯度≥99.5%(m%)
2.1.2原料路线确定原则和依据
在化工设计过程中选择技术路线和工艺流程时,必须综合考虑以下三项原则以保证“技术上先进,经济上合理[1]”:
1.先进性。
先进性是指在化工设计过程中技术上的先进程度和经济上的合理可行。
先进性的评价包括基建评价、生产成本、消耗定额以及劳动生产率等方面。
实际生产中,选择的生产方法应达到物料耗损较小、物料循环量较少并易于回收利用、能量消耗较少和有利于环境保护等要求。
2.可靠性。
可靠性主要是指所选择的生产方法和工艺流程是否成熟可靠。
另外,还要考虑原料供给的可靠性,对于一个建设项目,必须保证在其服务期限内有足够的、稳定的原料来源。
3.合理性。
合理性是指在进行化工厂设计时,应该结合我国的国情,从实际情况出发,考虑各种问题,即宏观上的合理性。
2.1.3工艺技术方案比较和选择理由
2.1.3.1异丙苯的生产技术概述
(1)异丙苯传统生产技术
异丙苯的传统生产技术主要有固体磷酸(SPA)法和三氯化铝法两种[2]。
固体磷酸法由UOP公司首先开发成功并实现工业化生产,凯洛格(Kellogg)工程公司对该生产工艺流程进行了改进和完善。
该工艺以硅藻土负载固体磷酸为催化剂,采用固定床反应器,苯和丙烯进行液相反应得到异丙苯和少量的多异丙苯。
反应条件为:
反应温度180-230℃,反应压力3.0-4.1MPa,苯与丙烯的摩尔比为5-7:
1,质量空速为1-2h-1,为保持催化剂的反应活性,需要向反应器中连续注入少量水。
催化剂分层装填,丙烯分段注入。
该工艺流程简单,腐蚀性相对较小,但催化剂无烷基转移功能,所得产品质量较差,苯的回收率相对较低,只有94.7%-96.0%。
三氯化铝法主要有美国科学设计公司(SD公司)开发的SD工艺和日本Monsanto公司开发的Monsanto工艺2种工艺[3]。
SD工艺采用以三氯化铝为主催化剂,HCl、氯乙烷等为助催化剂。
该催化剂既可催化烷基化反应,又可催化烷基转移反应。
该工艺催化剂活性高,反应条件温和,苯收率可以达到约96%,但工艺流程长,设备腐蚀严重,物耗、能耗较高,排放的污水量大。
Monsanto工艺是对SD工艺的一种改进。
该工艺采用三氯化铝络合物为催化剂,能溶解在苯中形成均相体系,反应在均相中进行,更有利于异丙苯的生成。
与SD工艺相比,该工艺所使用催化剂的消耗量减少约80%,副产物(如丁苯等)生成量少,但工艺流程依然很长,腐蚀和污染问题仍没有得到很好的解决。
由于固体磷酸法和三氯化铝法都存在难以彻底解决的设备腐蚀和环境污染问题,因此自20世纪60年代以来,世界各大公司开始转向开发无腐蚀、无污染的以沸石分子筛催化剂为基础的新型催化生产异丙苯新技术。
沸石分子筛催化剂可以再生,没有固体磷酸和三氯化铝工艺废物废液的排出问题,同时可提高苯制异丙苯的选择性、纯度和收率。
异丙苯纯度可以达到99.97%以上,收率为99.7%,每100g多异丙苯的重组分低于0.2kg。
目前,采用沸石分子筛催化剂的工艺技术主要有:
Dow/Kellog工艺、Polimeri工艺、UOP工艺、EniChem工艺、Mobil/Badger工艺以及CD Tech工艺等。
(2)UOP法生产异丙苯技术
UOP公司于20世纪80年代以超稳γ-沸石(USY)开发了第一代异丙苯液相烷基化催化剂[4,5]。
90年代开发了以苯和炼厂级或化学级丙烯为原料的液相固定床多段进料的“Q-Max工艺”技术。
该工艺采用MgAPSO-31沸石催化剂(牌号为QZ-2000),该催化剂孔体积大小适中,具有特殊的三维孔结构,再生性能良好,使用周期为18个月,总寿命超过5年,可以完全再生,各催化剂床层采用相同的催化剂,可同时用于烷基化和烷基转移反应,无专门的烷基化和烷基转移催化剂之分。
采用Q-Max工艺投资和操作费用均较低,产品异丙苯中芳烃含量、溴价指数均低于固体磷酸传统工艺,采用固体磷酸催化剂的异丙苯装置仅需要稍加改造就可以。
异丙苯产品纯度的质量分数可以达到99.96%-99.97%,收率接近化学计量值99.7%。
Q-Max工艺技术于1996年8月首次实现工业化生产。
美国JLM化学公司采用Q-Max工艺投运了一套6.6万吨/年异丙苯生产装置。
雪佛龙公司采用Q-Max工艺改造了其在美国得克萨斯州阿瑟港(PortArthur)的固体磷酸法异丙苯生产装置,使生产能力由原来的22.7万吨/年扩增到45.4万吨/年。
陶氏化学公司也采用该工艺对荷兰特纽赞地区的固体磷酸法异丙本苯生产装置进行了改造。
1999年,我国上海高桥石化公司投运的12万吨/年苯酚/丙酮装置中异丙苯生产单元也采用了“Q-Max”工艺,氧化精馏采用凯洛格技术。
UOP法典型的工艺流程包括烷基化反应器、脱丙烷塔、烷基转移反应器、苯塔、异丙苯塔和二异丙苯塔。
该工艺的烷基化采用固定床反应器,催化剂分层装填,新鲜的苯和循环苯加入反应器,丙烯分段注入,完全转化。
产品质量分数可达99.7%,收率接近化学计量值99.7%。
丙烯原料纯度可以是炼厂丙烯级(摩尔分数65%一80%)、化学级和聚合级。
催化剂对普通进料杂质(如水、硫、二氧杂环乙烷和肿等)不敏感。
此后,该公司又推出了商品名为QZ2000的催化剂。
采用该催化剂,允许低苯量循环操作,新建及老装置改造投资和操作费用均较低。
2.1.3.2异丙苯生产技术方案的选择
通过上面的比较我们可以看出:
生产异丙苯具有很大的优越性。
此外,分子筛催化剂又比固体磷酸催化剂具有很大的优越性,因此采用分子筛催化剂用于UOP法生产异丙苯是未来发展之趋势。
但是分子筛催化剂在现阶段实际应用中还不是特别的广泛,所以我们还是依照常规选用固体磷酸催化剂。
因此最终我们确定采用UOP法固体磷酸做催化剂的生产技术方案路线。
2.1.4操作条件的确定
UOP法生产异丙苯是气固相反应,即催化剂为固相——固体磷酸催化剂,原料为气相,因此苯和丙烯在进反应器之前需要经过加热炉加热气化。
在反应过程中,虽然低温有利于异丙苯的选择性,但是低温条件下催化剂的活性低,不于苯的转化率。
高温虽然有利于苯的转化率和反应速率,但是会加剧副反应的发生,同时增加能耗。
苯过量对反应的转化率有利,但增加了后续分离成本。
因此,在反应过程中我们需要综合各方面的因素来确定合适的反应条件。
通常我们主要优化反应器大小和苯的循环量这两个参数,来达到高转换率、高选择性及工艺经济性。
对于反应器,其体积越大,达到相同转化率时所需要的温度就越低,因此可以节省能耗和降低二次反应的发生,但是增大了设备费用。
2.2工艺流程设计
2.2.1反应原理
苯与丙烯烷基化合成异丙苯是典型的付克反应属正碳离子机理。
在催化剂作用下,其反应机理是:
苯与丙烯烷基化,首先生成异丙苯。
在质子酸催化作用下,丙烯被活化成异丙基正碳离子,生成的异丙基正碳离子进攻苯环形成σ-络合物,再经质子离去完成该烷基化反应过程[6]。
沸石作为固体酸催化剂,能催化种类繁多的烃化反应。
另外,沸石具有接近分子直径的均匀孔道系统,该孔道系统可以选择地允许小于孔道直径的反应物分子或产物分子进出沸石内部,在沸石上由于孔道的限制作用,不易生成多异丙基苯。
因此,沸石分子筛催化剂具有很高的苯烷基化生成异丙苯的选择性和很低的烯烃歧聚反应特性。
本设计采用UOP法生产异丙苯的工艺,采用固体磷酸做催化剂。
主反应:
副反应:
(少量)
这个反应同时伴有副反应,副反应虽然反应的量很少,但是还是很影响异丙苯产物的收率。
物性数据和反应方程式如下表2-1所示:
表2-1反应系统中组分的物性参数
组分
分子量
沸点(℃)
标准生成含kcal/mol
苯
78.1136
80.09
30.9544282
丙烯
42.0806
-47.69
14.8442725
异丙苯
120.194
152.41
32.9368491
二异丙基苯
162.275
210.5
35.3023789
2.2.2装置工艺原则流程图
异丙苯的生产主要包括原料的预处理、反应部分以及产物分离部分。
流程简图如下图2-1所示:
图2-1异丙苯生产装置原则流程图
(1)原料的预处理:
固体磷酸催化剂对原料中水分的要求严格,催化剂中游离酸的含量是通过控制进料水分含量来实现的(200~250ppm),因此要严格控制水分含量,此外,原料中的硫、氨、碱性有机物能引起催化剂中毒,亦应严格控制。
(2)反应部分:
UOP法采用塔式固定床反应器,原料苯和丙烯都为液相进料,但也有气相存在,出口则为气液混合物,反应温度控制在350℃左右,反应压力为2.0~5.0MPa,在工艺条件中控制原料的配比很重要,对UPO工艺来说,不仅要控制苯和丙烯的比(mol),还要控制作为稀释剂加入的丙烷和丙烯的比(称为烷烯比)。
苯和丙烯的比(mol)控制在(2—7):
1,苯的大量过量是为了减少二异丙苯的生成(在UOP法中二异丙苯不能反烃化),其另一个作用是丙烯得到充分的稀释,减少丙烯的自聚反应。
烷烯比控制在(8-10):
1左右,加入丙烷可以稀释丙烯,减少自聚反应,丙烯自聚不仅降低丙烯选择性,也影响异丙苯的质量(丙烯二聚体与异丙苯沸点相近,很难分离)。
同时自聚物可以沉积在催化剂上,降低催化剂的寿命,加入丙烷的另一个作用保证脱丙烷塔的正常运行,而且丙烷蒸出时带出的大量的苯可以减轻塔的负荷。
在反应中:
催化剂颗粒密度:
p(cat)=2000kg/m^3,空隙比e=0.50,固定管到管壁的传热系数:
h=65W/m^2*K
(3)产物分离部分及循环系统:
在异丙苯的合成过程中,由于苯的大大过量和作为稀释剂丙烷的存在,反应器出口有大量未反应的原料和稀释剂,还有生成的少量多烃化物。
因此必须对反应产物进行分离。
在本设计中,首先用一个闪蒸罐将产物中水、丙烷和未反应的丙烯分离出来,其应用价值不大,故作为燃料气。
未反应的苯及产物进入苯塔进行分离,塔顶回收的未反应的苯打循环重新进入反应器进行反应,塔底流出的多烷基化合物和异丙苯最后进入异丙苯精馏塔进行精馏分离出异丙苯,要求异丙苯的纯度达到99.5%以上。
由表2-1我们可以看出丙烯、苯、异丙苯及二异丙苯的沸点是依次增大,并且相邻组分的沸点相差加大,因此可以用普通精馏的方法进行分离。
如图2-2所示,为产物分离部分简单示意图。
图2-2产物分离流程示意图
2.2.3工艺流程简述
图2-3工艺流程示意图
98.00kmol/h纯度≥99.5%原料苯在25℃、1atm下液相进料(物流1),与未反应的循环苯(物流10)进行混合后预热后温度达到74.1℃、1atm,苯的总量(物流2)为511.009kmol/h,另外循环物料中还含有少量的未反应的丙烯及丙烷和反应产物异丙苯及二异丙苯。
总流量为593.0kmol/h物流2经过进料泵进行加压后压力由1atm上升至25atm,流量组成不变,温度变为75.7℃。
然后物流3与25℃、25atm下98kmol/h工业级丙烯(物流4)进入混合器中进行充分混合,从混合器中流出的物流5的状态是液相,温度为71.1℃,压力为25atm,总流量为691.0kmol/h。
然后进入加热炉进行加热气化,从加热炉出来的物流6的温度达到360℃,此时苯的总量为511.009kmol/h,丙烯的总量为97.098kmol/h,苯和丙烯比为5.26:
1,然后进入固定床反应器进行反应,反应过程中反应器温度为360℃,反应压力为25atm,丙烯的反应转化率为92%,其中86%的丙烯生成了异丙苯,6%的丙烯生成了二异丙苯。
从反应器出口流出的物流7的温度为350℃、压力为25.331atm,相态为气相,其进入冷凝器进行冷凝冷却,从而使物流8温度降至90℃、压力降至1.750atm,此时为气液两相共存。
物流8进入闪蒸罐进行闪蒸,闪蒸罐的操作温度为90℃,压力为1.73atm,通过闪蒸,可以把物流中的绝大多数轻组分丙烯丙烷以及少量的苯和产物给闪蒸出来,由于闪蒸器实用价值不大,我们通常将其作为燃料气进行燃烧放空。
从闪蒸罐底部流出的物流9组分中含有大量为反应的苯,我们需要将其打循环加以利用,因此进入苯塔进行分离。
从苯塔塔顶流出的物料10的温度为82.6℃、压力为1.75atm,总循环量为495kmol/h,其中大部分为苯,还有少量的丙烷、丙烯、异丙苯及二异丙苯。
从苯塔塔底流出的物流11温度为177.4℃、压力为1.8atm,总流量为85.926kmol/h,主要含有异丙苯,所以需进异丙苯塔进行分离精制以便达到所需要的产品纯度。
经过异丙苯塔精制后的得到的物流12温度为152℃,压力为1atm,异丙苯总流量为83kmol/h,即9976kg/h,纯度为100%,满足了生产要求。
塔底分离出的物流13温度为208.9℃,压力为1atm,主要为副产物二异丙苯。
参考文献:
[1]陈声宗主编.化工设计[M].第二版.北京:
化学工业出版社,2008.5
[2]张佩君.合成异丙苯生产现状及技术进展[J].石化技术,2005,12
(2);62-65,68
[3]魏文德.有机化工原料大全(下卷).第2版.北京:
化学工业出版社,1999.113-138
[4]U0PInc.Diseretemolecularsieveanduseinaromatic-olefinalkylation.USA,US5434326.1995
[5]U0PInc.Modifiedzeolitebeta,Processesforpreparationandusethereof.USA,US5522984.1996
[6]温朗友,闵恩泽,庞桂赐等.悬浮床催化精馏新工艺合成异丙苯[J].化工学报,2000,51
(1):
115-119.
[8]姜昌泉,孙然功.沸石分子筛催化合成异丙苯工艺研究[J].吉林:
化工科技,2001,9
(1):
35~37
[9]
[10]白桦.异丙苯生产技术新进展及市场前景分析[J].杭州化工,2007·37
(1)
[11]崔小明.异丙苯生产技术进展及市场需求[J].中国石油和化工,2006,(3):
35-39.
第3章物料衡算
3.1物料衡算概述
为了弄清生产过程中原料、成品以及损失的物料数量,必须要进行物料衡算。
物料衡算是设备热量衡算乃至整个工艺设计的基础,一般在以下几种情况下需进行物料衡算。
⑴对某个操作过程作物料衡算;
⑵对已有的设备:
一个设备、一套设备或整个车间作物料衡算;
⑶设计一套新的装置或一个新的车间时,一般均需做出全面的物料衡算。
因此正确的物料衡算结果为正确的设备热量衡算和设备工艺设计提供可靠的保证,在整个设备设计过程中具有重要的意义[5]。
3.1.1物料衡算的计算依据[6]
物料衡算为质量守恒定律的一种表现形式,即
∑GI=∑Go+∑GA
式中,
—输入物料的总和;
—输出物料的总和;
—累计的物料量。
式∑GI=∑Go+∑GA为总物料衡算式。
当过程没有化学反应时,它也适用于物料中任一组分的衡算;但有化学反应时,它适用于任一元素的衡算。
若过程中累积的物料量为零,则该式可简化为
∑GI=∑Go
上式所描述的过程属于定态过程,一般连续不断的流水作业(即连续操作)为定态过程,其特点是在设备的各个不同位置,物料的流速、浓度、温度、压强等参数可各自不相同,但在同一位置上这些参数随不同时间而变。
若过程中有物料累积,则属于非定态过程,一般间歇操作(即分批操作)属于非定态过程,在设备的同一位置上诸参数随时间而变。
式∑GI=∑Go+∑GA或式∑GI=∑Go中各股物料数量可用质量或物质量衡量。
对于液体及处于恒温、恒压下的理想气体还可用体积衡量。
常用质量分率表示溶液或固体混合物的浓度(即组成),对理想混合气体还可用体积分率(或摩尔分率)表示浓度。
3.1.2物料衡算的计算范围和计算基准
作物料衡算时需要确定一个计算范围,即从哪里开始作为进料,从哪里作为出料。
根据实际需要来确定计算范围,可以是某一设备或一套设备。
对分批操作,可从开始加料到最终出料作为计算范围,有时也取整个过程中的某一阶段作为物料衡算的范围。
作物料衡算时也要选定一个计算基准。
例如分批操作可以分批投料量或每昼夜的处理量作为计算基准。
连续生产可以用每小时、每天或每分钟的投料量作为计算基准。
根据需要有时也采用每吨产品或原料作为计算基准,或者用每千摩尔(kmol)的投料量作为计算基准。
基准的选择是跟据物料衡算的目的和计算的方便来考虑决定[7-8]。
3.1.3操作流程
3.2主要设备的物料衡算
流程中主要设备有混合器(2个),反应器,闪蒸罐,苯塔,异丙苯塔。
3.2.1混合器
3.2.1.1混合器1
图3-1混合器1流程图
3.2.1.2混合器2
图3-2混合器2流程图
3.2.2反应器
图3-3反应器流程图
3.2.3闪蒸罐
图3-4闪蒸罐流程图
3.2.4苯塔
图3-5苯塔流程图
3.2.5异丙苯塔
图3-6异丙苯塔流程图
3.3全装置物料衡算
图3-7异丙苯生产流程图
表3.1混合器1的物料平衡表
项目
进料
出料
物流1
物流10
物流2
流率
流率
摩尔
质量
流率
流率
摩尔
质量
流率
流率
摩尔
质量
kmol/hr
kg/hr
分率
分率
kmol/hr
kg/hr
分率
分率
kmol/hr
kg/hr
分率
分率
苯
98.00
7655.14
1.