常见工业原料的制备.docx
《常见工业原料的制备.docx》由会员分享,可在线阅读,更多相关《常见工业原料的制备.docx(14页珍藏版)》请在冰豆网上搜索。
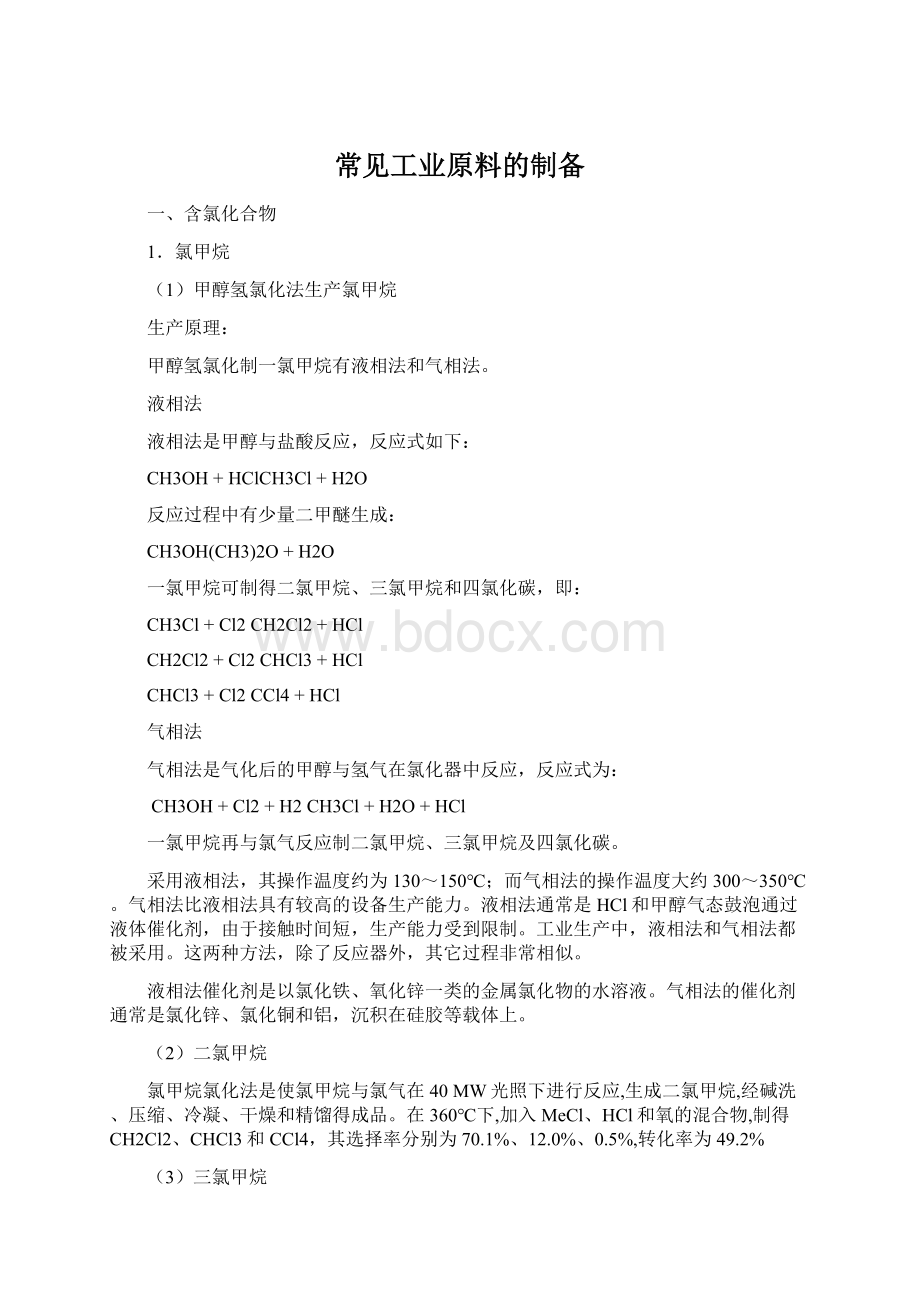
常见工业原料的制备
一、含氯化合物
1.氯甲烷
(1)甲醇氢氯化法生产氯甲烷
生产原理:
甲醇氢氯化制一氯甲烷有液相法和气相法。
液相法
液相法是甲醇与盐酸反应,反应式如下:
CH3OH+HClCH3Cl+H2O
反应过程中有少量二甲醚生成:
CH3OH(CH3)2O+H2O
一氯甲烷可制得二氯甲烷、三氯甲烷和四氯化碳,即:
CH3Cl+Cl2CH2Cl2+HCl
CH2Cl2+Cl2CHCl3+HCl
CHCl3+Cl2CCl4+HCl
气相法
气相法是气化后的甲醇与氢气在氯化器中反应,反应式为:
CH3OH+Cl2+H2CH3Cl+H2O+HCl
一氯甲烷再与氯气反应制二氯甲烷、三氯甲烷及四氯化碳。
采用液相法,其操作温度约为130~150℃;而气相法的操作温度大约300~350℃。
气相法比液相法具有较高的设备生产能力。
液相法通常是HCl和甲醇气态鼓泡通过液体催化剂,由于接触时间短,生产能力受到限制。
工业生产中,液相法和气相法都被采用。
这两种方法,除了反应器外,其它过程非常相似。
液相法催化剂是以氯化铁、氧化锌一类的金属氯化物的水溶液。
气相法的催化剂通常是氯化锌、氯化铜和铝,沉积在硅胶等载体上。
(2)二氯甲烷
氯甲烷氯化法是使氯甲烷与氯气在40MW光照下进行反应,生成二氯甲烷,经碱洗、压缩、冷凝、干燥和精馏得成品。
在360℃下,加入MeCl、HCl和氧的混合物,制得CH2Cl2、CHCl3和CCl4,其选择率分别为70.1%、12.0%、0.5%,转化率为49.2%
(3)三氯甲烷
三氯乙醛法(又称氯油法)是国内常用方法。
该法是以酒精转化为三氯乙醛(氯油)(要求三氯乙醛含量大于70%),然后滴加到装有石灰乳的碱解釜中。
石灰乳含氢氧化钙8%~21%。
碱解釜中氯油在60~65℃下碱解生成氯仿。
然后通过水洗、沉降分离,得到粗氯仿,再精制得到成品
乙醛法也是国内常用的一种生产氯仿的方法。
该法是将原料漂白液和经稀释的乙醛溶液按1.015∶1的比例混合后,进入带搅拌的常压反应器中,在72~80℃发生反应,生成氯仿,经两次冷凝后得到半成品—粗氯仿溶液(含氯仿超过90%)。
该溶液再经水洗处理送入间歇精馏塔精制得到氯仿成品。
本法工艺流程简单,属废物利用,产品质量高,主成分氯仿含量超过99.78%;但三废治理困难。
(4)四氯甲烷
甲烷热氯化法是甲烷与氯气混合,在400~430℃下发生热氯化反应,制得粗品和副产盐酸,粗品经中和、干燥、蒸馏提纯得成品。
副产物除盐酸外,还有三氯甲烷、四氯乙烯和六氯乙烷。
甲醇液相光氯化法生产一氯甲烷后可将一氯甲烷气化后与氯气按一定比例进入氯化反应器,在光照作用下,反应生成氯化液(含四氯化碳97%),氯化液经中和处理后进行精馏,得到成品四氯化碳。
本反应可在较低温度和压力下进行(70~80℃、0.1MPa),副反应小,转化率高。
同时由于整个生产过程基本在一个闭合循环下进行,故生产连续性较强,控制水平较高。
但反应速度慢,生产强度低,只适宜小规模生产。
2.三氯乙烯
乙烯氧氯化法是较先进的工艺,由于采用了氧氯化反应,避免了大量氯化氢的产生,在金属氯化物催化剂下,氯气与乙烯生成1,2-二氯乙焼,在反应温度365°C件下,以二氯乙焼、氯气、氧气或氯化氧为原料,在流化床反应器内反应。
改变TCE与四氯乙烯的联产比可对氯气-二氯乙烧进料比进行调节。
其反应式为:
C2H4+Cl2→C2H4Cl2
8C2H4Cl2+6Cl2+7O2→4C2HCl3+4C2Cl4+4H2O
目前国内新增三氯乙烯的企业大部分采用气相催化法法脱氯化氢工艺,其生产的主要原料为乙炔和氯气,但是反应体系不稳定。
3.四氯乙烯
乙烯一步液相氯化
本法是乙烯一步液相氯化。
将来自电解槽的氯气进行干燥和压缩,然后引进氯气吸收器中,在此被氯乙烷所吸收。
将吸收氯气的氯乙烷从反应器底部加人,再将乙烯以气态形式通入反应器在反应器中,氯加到乙烯中,通过加成法(在8个压力下)制得氯乙烷。
在净化系统中将氯乙烷分馏成低拂点组份、四氯乙烷和五氯乙烷,再将低沸点组份循环到反应器中。
然后将四氯乙烷五氯乙烷的混合液输送到一个单一型管式裂解反应器中,反应压力约为8个大气压,温度在如。
在400-500℃进行热裂解。
从裂解器出来的反应气体进人冷凝器后分离出氯化氢和冷凝液,再把冷凝液蒸馏进行精制,这样就得到了纯的四氯乙烯和三氯乙烯,加人一定的稳定剂后就可供用户使用。
4.氯乙酸
乙酸催化氯化法是目前国内外生产氯乙酸最主要的方法。
它又可分为间歇式生产工艺和连续化生产工艺两种。
乙酸催化氯化法按所用催化剂的不同可以分为硫磺法和乙酸酐法。
一般来说,硫磺法是属于间歇式生产工艺,而乙酸酐法是属于连续化生产工艺(也可以是间歇式的)。
国外主要采用先进的醋酐催化氯化工艺路线,该法具有产品质量高且易于连续化生产的特点。
不过目前我国氯乙酸的生产也主要是用此种方法,该法中醋酐既是催化剂,也可作原料参与反应,产物中没有催化剂残留,因此产品纯度高、质量好,且催化效率高,乙酸和醋酐合计转化率有时甚至高达98%以上,三废量少、生产能力大、成本低、市场竞争能力强。
5.氯乙酰氯
据文献报道,氯乙酰氯有10余种合成路线,目前工业化或具有工业前景的合成氯乙酰氯的工艺主要有4种:
氯乙酸氯化法、乙酸氯化法、(双)乙烯酮氯化法、氯乙酸光气法。
通常使用氯化剂有氯、三氯化磷、亚硫酰氯、光气等。
其中氯乙酸氯化法是应用最早、目前应用最广的一种,工艺过程较为简单,缺点是生产周期长,
收率80%~95%。
由于催化剂中使用了硫、磷,产品中有时含有微量的硫、磷,其收率、产品纯度、环境保护等方面不尽人意。
目前国内80%以上的装置采用落后的氯乙酸三氯化磷氯化法。
乙烯酮法:
(双)乙烯酮法由美国Monsanto公司开发,已在美国Monsanto公司、Dow化学公司实现了工业化生产。
该法具有工艺技术先进、流程设计合理、产品纯度高、收率高、三废少等优点。
二、含氮化合物
1.甲胺
甲胺生产主要采用甲醇和氨气气相催化反应技术,在加压和高温下,甲醇和氨气在催化剂的作用下合成得到粗甲胺,然后经蒸馏分离,得到一甲胺、二甲胺和三甲胺,日本日东化学公司采用双反应系统成套工艺及新型催化剂,可使二甲胺选择性达到60%,但催化剂在抑制三甲胺合成的同时也抑制了三甲胺的转化,反应生成的三甲胺很难转化为一甲胺和二甲胺。
因此,在装填催化剂的第一反应器增设了装填平衡型催化剂的第二反应器,进行一甲胺和三甲胺的歧化反应,以期进一步提高二甲胺产率。
通过上述双反应器与分离系统的组合,最终可以得到一甲胺、二甲胺和三甲胺物质的量比为7∶86∶7的甲胺产品。
2.乙胺
二氯乙烷法:
二氯乙烷法是通过将原料二氯乙烷和氨水或液氨在高温、高压下直接反应生成乙二胺,一般无需使用催化剂。
但反应生成的乙二胺碱性强于无机氨,会进一步与二氯乙烷反应形成多乙烯多胺系列副产品一般工业生产反应结束后用碱中和反应液,可得到混合游离胺,但副产大量氯化钠和水。
同时稀碱液带入的水会对被分离物系产生稀释作用,乙二胺和水又会形成恒沸物,大量水存在加大了后处理难度。
该反应易生成副产物,所以提高产品选择性,并采用高效分离工艺是该技术开发的关键。
ClCH2CH2Cl+2NH3→NH2CH2CH2NH2+2HCl
乙醇胺法:
乙醇胺(MEA)法早先由BASF公司开发成功并实现工业化,该方法又分为氨化还原工艺和缩合工艺,均属清洁生产工艺。
氨化还原工艺以乙醇胺和氨气为原料,反应在氢气流中进行,乙醇胺先脱氢生成醛,再与氨进行脱水反应,主要采用的还原氨化催化剂有VIIIB族、IB族金属或金属氧化物等活性组分
缩合工艺过程采用乙醇胺和氨为原料发生脱水缩合反应,相比其他工艺哌嗪产率较高,该工艺无需临氢,压力相对较低,
主要采用固体酸缩合催化剂,如Lewis酸、质子酸、杂多酸以及分子筛等,催化剂可以再生。
3.乙醇胺
由环氧乙烷和氨水在30~40℃下、70.1~304kPa下缩合而成,其为单、二、三乙醇胺的混合液,在90~120℃下脱水、浓缩,然后于精馏塔中减压蒸馏,截取168~174℃馏分而得。
4.乙腈
1.醋酸氨化法
以醋酸、氨为原料,在三氧化二铝催化剂作用下,在360-420℃温度下,进行反应,一步合成乙腈,反应液经吸水和精馏即得成品。
2.由乙酰胺与五氧化二磷脱水而得。
5.丙烯酸铵
催化水合法
丙烯腈与水在铜系催化剂的作用下,于70~120℃、0.4MPa压力下进行液相水合反应。
CH2=CH-CN+H2O─→CH2=CHCONH2
反应后滤去催化剂,回收未反应的丙烯腈,丙烯酰胺水溶液经浓缩、冷却得丙烯酰胺结晶。
该法工艺流程简单,丙烯酰胺的选择性和收率可高达98%以上。
生化法
生物法制取丙烯酰胺。
系将丙烯腈、原料水和固定化生物催化剂调配成水合溶液.催化反应后分离出废催化剂就可得到丙烯酰胺产品其特点是:
在常温常压下反应.设备简单,操作安全。
生化法技术最早由日本日东化学公司于1985年实现工业化生产。
规模为4000t/a1991年已达1.4万t/a规模。
三、含氧化合物
1.乙烯直接氧化法制环氧乙烷(EO)
主反应与副反应:
主反应:
C2H4+O2→C2H4O选择性氧化
平行副反应:
C2H4+3O2→2CO2+2H2O(g)串联副反应:
C2H4O+2O2→2CO2+3H2O(g)催化剂:
1.工业上使用银催化剂2.由活性组分银、载体和助催化剂组成
影响因素:
空速,反应压力,原料配比,致稳气,原料气纯度产率:
62%
产品纯度》99%
2.环氧乙烷水合制备乙二醇
直接水合工艺是将环氧乙烷和水按l:
(20~25)(摩尔比)配成混合水溶液,在管式反应器中于190~220℃、1.0~2.5MPa条件下反应。
环氧乙烷的转化率接近100%,EG的选择性约89%~90%.
3.乙二醛的制备
(1)乙二醇气相催化氧化法
(CH2OH)2+O2→(CHO)2+2H2O
由乙二醇氧化制取乙二醛的工艺可分为液相法和气相法两种,液相法虽然工艺简单,反应温度和压力要求不高,但必须使用贵金属钯或铂作催化剂,经济上不合算,且收率不高,至今尚未工业化。
气相法是乙二醇在催化剂存在下,用空气或氧气进行气相氧化,制得的产品经离子交换树脂处理,活性炭脱色,浓缩后得到40%的乙二醛,产品中含有6%~8%甲醛。
(2)乙醛硝酸氧化法(国内提倡大力开发)
乙醛在硝酸铜、亚硝酸钠催化作用下,经硝酸氧化合成乙二醛,反应式如下:
3CH3CHO+4HNO3→3CHO-CHO+4NO+5H2O
引发是硝酸氧化乙醛的关键步骤,一般采用先加催化剂,后加乙醛,再滴加硝酸的加料顺序,反应平稳,易于控制。
工业上乙二醛的收率可达70%左右。
反应液在50℃和6.5kPa压力下,浓缩到硝酸浓度为5%时,加入少量乙醛,继续加温2h,以消除残余的硝酸,蒸去挥发性物质,然后通过阴离子树脂交换器除去有机酸,得到含量40%的乙二醛溶液,国外正在研究用氧化硒来代替硝酸作氧化剂,据称氧化选择性较好,收率可达84%,该法目前尚未工业化。
4.环戊烯氧化制备戊二醛
这是早期合成戊二醛的方法,环戊烯与臭氧反应生成臭氧化物,然后经还原分解得到戊二醛,同时伴有醛酸、戊二酸及醋类化合物生成。
反应液中生成的戊二醛需立即处理,否则易被继续氧化成戊二酸。
该方法设备要求高,工艺条件苛刻,臭氧的发生及处理较为复杂,能耗大,反应中间物臭氧化物易发生爆炸,操作危险,因而仅限于实验室制备,未被工业界重视。
80年代以来随着环戊烯资源日趋增多,国内外学者把研究重点转移到对环戊烯氧化法的改进上,并取得了很大进展。
目前有三步氧化法,二步氧化法,一步氧化法
其中三步氧化法戊二醛总收率可达到70%,但由于反应步骤多,并需使用多种催化剂,因而仍缺乏竞争力。
二步氧化法的文献报道较多,但戊二醛收率并没有得到提高。
一步氧化法是近十几年来的研究焦点,所采用的氧化剂有空气,过氧化氢及酮的过氧化物。
一步氧化法:
近年来国内在这方面的研究取得良好进展,米镇涛等人。
采用三氧化钨为催化剂,过氧化氢为氧化剂,B2O3为助催化剂,并采用乙酸丁醋为溶剂,在温度40-50C,反应时间10h催化剂浓度9%的条件下得到了收率为63%的戊二醛。
许新华等人以钨酸为催化剂,叔丁醇为溶剂,在35C反应24h戊二醛收率达80%他们认为戊二醛是通过环氧化物中间体生成的,该中间体除继续氧化为戊二醛外,还能与水和醇生成其它副产物,因此采用不含羟基的溶剂或使用高浓度的过氧化氢水溶液为氧化剂来抑制环氧化物中间体的副反应发生,可提高戊二醛收率。
5.乙烯直接氧化制备乙醛
乙烯直接氧化法又称瓦克法,它是世界上第一个采用均相配位催化剂实现工业化的过程,该法以氯化钯—氯化铜—盐酸—水组成的溶液为催化剂,使乙烯直接氧化为乙醛。
总反应式为:
实际反应按下述两步进行:
乙烯氧化:
CH2=CH2+PdCl2+H2O→CH3CHO+Pd+2HCl
催化剂溶液的氧化再生:
Pd+2CuCl2→PdCl2+2CuCl
6.丁酸的制备
正丁醛氧化法(国内主要生产方法)
正丁醛氧化法生产正丁酸是以正丁醛为原料、氧气或空气作为氧化剂,有无催化剂均可完成的反应。
如果用催化剂则选择过渡金属以及Cu、Ag、Ce、碱金属和碱土金属。
液相反应时,催化剂选择金属羧酸盐,气相反应则使用沉淀于硅胶、氧化铝等上的金属氧化物。
直接采用正丁醛氧化法具有工艺路线简单、生产控制方便、原料单一、产品收率高等优点,在工业上得到广泛应用。
7.丙烯氧化法制备丙烯酯
丙烯氧化法有一步法和两步法之分。
(1)一步氧化法的反应为:
(2)两步法的反应为:
第一步,丙烯氧化生成丙烯醛。
第二步,丙烯醛进一步氧化生成丙烯酸。
时至今日,丙烯氧化法是世界上工业合成丙烯酸的主流工艺方法,几乎所有的工业化大型丙烯酸生产装置全部采用丙烯两步氧化法进行生产。
8.季戊四醇的制备
季戊四醇是由甲醛和乙醛在碱性缩合剂存在下反应制得的,同时副产甲酸盐。
用氢氧化钙作为碱性催化剂的季戊四醇生产工艺称之为“钙法”。
“钙法”产品质量较好,原料成本低廉,但该方法操作步骤多,后处理必须增加沉淀和过滤以除去钙离子。
用氢氧化钠作为碱性催化剂的季戊四醇生产工艺称之为“钠法”。
氢氧化钠法的价格虽然较贵,但由于副产物甲酸钠易溶于水,使后处理步骤减少。
混合碱法:
与传统的钠法和钙法相比,混合碱法有如下特点:
(1)以弱碱碳酸盐和碳酸氢盐为催化剂合成季戊四醇,反应条件较为稳定,可减少副反应的发生,对提高季戊四醇的产率有利;
(2)弱碱碳酸盐和碳酸氢盐对设备的腐蚀性较小;(3)该法能将副产物甲酸钠在贵金属催化剂的作用下,通过氧化或水解转化为本反应所需要的碳酸盐和碳酸氢盐,作为下一批反应催化剂,循环使用。
一方面节省了大量的碱,得到高质量高收率的产品,既降低了成本,又有利于提高产量和经济效益;另一方面,该工艺副产物少,无三废产生,是一种可持续发展的绿色工艺,必将产生很好的环境效益,具有良好的发展前景。
9.3,5-二羟基苯甲醇
3,5-二羟基苯甲醇是一种重要的医药中间体和化工中间体,其合成均以3,5—二羟基苯甲酸为起始原料,经过多步反应得到产品,工业化主要有四条路线。
(1)以氢化铝在醚溶液中直接还原得到3,5—二羟基苯甲酸乙酯,用醚连续提取分离产物,该法反应时间过长、收率不高,且生产安全性差;
(2)将3,5—二羟基苯甲酸的羟基硅烷化予以保护,再用氢化锂铝还原,最后脱掉保护基,分离得到产物;
(3)将3,5-二羟基苯甲酸甲酯先苄醚化,然后经氢化铝锂还原,再用5%Pd/C催化剂氢解苄基得到3,5-二羟基苯甲醇;
(4)以3,5—二羟基苯甲酸为原料,经过酯化、酰化、还原等步骤合成。
方法
(2)与(3)需要使用价格昂贵的保护试剂,生产成本比较高,但是产品质量好、中间控制比较容易,是目前国内外最主要的工业化合成路线。
方法(4)使用价格相对较低的酰化试剂,成本相对较低,生产安全性高,目前国内正在开发此路线,该法将是较有前途的工业化生产方法。
目前国外主要生产厂家有德国赫司特公司和日本三井化学公司,生产能力分别为100-200吨/年之间:
国内由南京制药厂独家生产,生产能力约为50吨/年,主要用于自己合成医药,少部分出口。
该产品世界市场需求看好,预计2005年国内外市场需求量约为600吨左右,国外多次来我国寻求该产品,据报道国内清华大学、南京市师范大学等单位对此合成技术进行研究,技术比较成熟,国内可以采取路线2或3建设一套50吨/年的生产装置。
10.二甲基乙酰胺
二甲基乙酰胺又称乙酰二甲胺,是一种强极性非质子化溶剂,广泛应用于石油加工和有机合成工业中,该品工业化合成主要有两条路线。
醋酐法
以醋酐为原料与二甲胺反应而得,目前国内主要采用该法生产。
乙酰氯法
由二甲胺与乙酰氯反应而得。
该工艺首先由抚顺化工研究院开发成功,该工艺特点是采用先进的催化反应精馏技术,强化了反应,降低能耗,分离效果和产品收率大大提高,工艺过程简化,与醋酐法相比较,生产成本有所降低。
目前国内二甲基乙酰胺总生产能力约3000吨/年,有十余家企业生产,主要生产企业有上海纪中化工厂、上海新华化工厂、济南高创化工有限公司、苏州寅生化工厂、河北化学工业研究院实验厂等。
目前年产量约2600t年,基本上能够满足国内市场需求,每年有一定数量的进口,尽管目前二甲基乙酰胺生产能力基本能够满足国内需求,但是随着我国石油化工,尤其是合成树脂、丙烯腈纤维和芳烃的生产能力快速增加,国内二甲基乙酰胺的需求将有较大的增长幅度,因此投资建设1000吨/年的二甲基乙酰胺市场前景看好,另外与二甲基乙酰胺生产过程比较相似同系物N,N-二丁基乙酰胺、N,N-二乙基癸酰胺等与该产品生产技术与生产设备也比较相近,因此在开发二甲基乙酰胺的同时,建议同时开发生产这些同系物,可以有效规避投资风险,增加装置的经济效益。
11.乙酰乙酸甲酯
乙酰乙酸甲酯是重要的精细化工原料和溶剂,其工业化主要路线是双乙烯酮酯化法,即由双乙烯酮与甲醇在催化剂存在下进行酯化反应,经过精制后得到产品。
该工艺不仅操作方便、能耗低,而且同一套装置和相同工艺可以生产乙酰乙酸乙酯、乙酰乙酸氯乙酯、乙酰乙酸异丙酯、乙酰乙酸烯丙基酯等系列产品,因此国内外主要采用该路线合成。
目前国内有多家企业生产乙酰乙酸甲酯,因此生产能力难以准确统计,目前国内乙酰乙酸甲酯的生产能力约为1.2万吨/年左右,国内主要生产厂家有南通醋酸化工股份有限公司、上海彭浦化工厂、河北沧州农药化工厂、安徽蚌埠八一化工有限公司、山东青岛农药场、淄博开发区医药化工厂、西安太宝化工有限公司等十余家企业生产,其中南通醋酸化工股份有限公司生产能力最大,达到6000吨/年,其余企业均为数百吨/年,我国乙酰乙酸甲酯生产与国外先进水平差距较大,主要是产品质量较差,国内除少数规模较大企业产品质量有所提高以外,大部分装置不能生产出下游医药、农药和维生素等所需要的99%以上的产品,因此国内每年需要进口大量的高纯度的乙酰乙酸甲酯来满足国内市场需求,2002年进口量高达5000吨左右。
随着科学的进步,乙酰乙酸甲酯的用途不断被开发出来,其许多下游产品都是目前国内非常具有发展前景的精细化工中间体或化学品,下游产品发展异常迅速,因此加快乙酰乙酸甲酯开发与生产非常重要与必要。
建议新建装置规模在3000-5000吨/年为宜。
四.芳香族化合物
1.二氯苯
邻二氯苯制备方法:
1.氯苯副产回收无论是采用苯液相氯化法还是采用苯气相氧氯化法制造氯苯,都联产二氯苯。
按照目前氯苯的工艺控制条件和生产情况,氯苯与二氯苯的比例为30-35:
1,工业上分离邻、对位二氯苯的方法主要有精馏法和结晶法。
2.由邻氯苯胺经重氮化、置换而得将邻氯苯胺及盐酸加入反应锅,于25℃以下混匀。
冷却至0℃,滴入亚硝酸钠溶液,温度维持在0~5℃,至碘化钾淀粉液变蓝色时停止加料,得重氮盐溶液。
在0~5℃下加入氯化亚铜的盐酸溶液中,充分搅拌、混匀,升温至60~70℃℃,反应1h,冷却、静置分层,油层用5%氢氧化钠和水反复洗涤,以无水氯化钙脱水、分馏,收集177~183℃馏分,即得成品。
间二氯苯制备方法:
(1)间苯二胺与硫酸、亚硝酸钠经重氮化反应,制成重氮盐,再经氯化而成。
(2)间氯苯胺经重氮化、氯化而成。
3.间二硝基苯直接催化氯化法。
对二氯苯制备方法:
(1)苯定向氯化将苯置于氯化反应器中,加苯重量的0.1%-0.6%的硫化锑,通入氯气,控制氯化温度在20℃左右,氯化30-45分钟,加入苯磺酸定向催化剂,然后再通入氯气,当二氯苯晶体析出时,将反应液加热到50-60℃,再缓速通氯气直到反应液增重理论量的95%左右为止,收率70%-75%。
由于苯氯化产物组分较多,工业制备的关键是对二氯苯选择适当的分离,精制方法。
(2)由氯苯生产过程中回收将氯苯精馏塔底物,经真空蒸馏蒸出混合二氯苯,在结晶器中进行结晶而得较纯的对二氯苯。
2.氯苯
直接氯化法:
用苯接氯化制氯苯的方法,是英国于1909年首先进行工业化生产的,并一直沿用至今。
反应式为:
有气相法和液相法两种。
①气相法,反应温度400~500℃,成本高于液相法,故已被淘汰。
②液相法,通常用三氯化铁催化,但在生成氯苯的同时,还伴有多氯苯生成。
氧氯化法:
由德国拉西公司于1932年开发成功。
反应是在275℃和常压下于气相中进行的,催化剂为铜-氧化铝。
为了抑制多氯苯的生成,所用的苯需大大过量。
尽管如此,还会生成5%~8%的二氯苯,而氯化氢被全部用完。
3.对氯甲苯:
重氮化法:
由对甲苯胺经重氮化、置换而得。
将对甲苯胺和盐酸加入反应锅中搅拌加热,至60℃溶解后,冷却至15℃以下,滴加亚硝酸钠溶液。
到达终点后继续搅拌0.5h。
加入氯化亚铜盐酸溶液,在室温搅拌3h。
然后升温至60℃保持0.5h,冷至室温静置分层,弃去酸水层,用水洗至中性,过滤,得对氯甲苯。
直接氯化法:
由甲苯进行芳环氯化制得。
4.硝基氯苯
生产方法:
硝基氯苯的生产主要采用混酸硝化法,共有两种工艺:
等温硝化,绝热硝化。
目前国内几乎全部采用等温硝化法,而国外主流技术为绝热硝化工艺
5.均三甲苯
(1)重溶剂油经分馏得。
(2)可用偏三甲苯的异构化法或丙酮在硫酸催化下脱水合成,纯均三甲苯由丙酮在300~500℃下气相催化脱水制得:
3CH3COCH3→(CH3)3C6H3+3H2O
6.壬基酚
壬基酚的生产包括丙烯齐聚制壬烯和苯酚烷基化制壬基酚两个过程。
常州化工二厂和大庆石油化工厂采用波兰布拉霍夫尼亚有机合成研究院的齐聚工艺,其特点是使用布拉霍夫尼亚有机合成研究院开发的专用含磷催化剂,齐聚反应选择性高,催化剂寿命较长(不少于6个月)。
7.对氨基酚
硝基苯化学还原法:
用活泼金属为还原剂,将硝基苯还原得到对氨基苯酚,
反应40min得到中间体苯肢,再在20%硫酸介质中,82度下经重排反应lh制得对氨基苯酚,硝基苯转化率为72%该方法原料廉价易得,操作方便,工艺流程简单,生产成本低,生产废水经处理后完全达到环保要求的排放标准。
8.苯二酚
(1)邻苯二酚
工业上是通过重氮化邻氨基苯酚后水解,或者在高压釜中水解邻氯苯酚制得,目前大部分邻苯二酚的工业制法为苯酚羟基化法,其过程为苯酚经氧化物(过氧酸、双氧水等)氧化可制得邻、对苯二酚,经分离可得邻苯二酚。
(2)对苯二酚
苯磺酸用发烟硫酸磺化、中和,再经碱熔、酸化、正丁醇萃取、蒸去溶剂后,经