完整版数控铣中典型零件的设计制造及工艺毕业设计.docx
《完整版数控铣中典型零件的设计制造及工艺毕业设计.docx》由会员分享,可在线阅读,更多相关《完整版数控铣中典型零件的设计制造及工艺毕业设计.docx(32页珍藏版)》请在冰豆网上搜索。
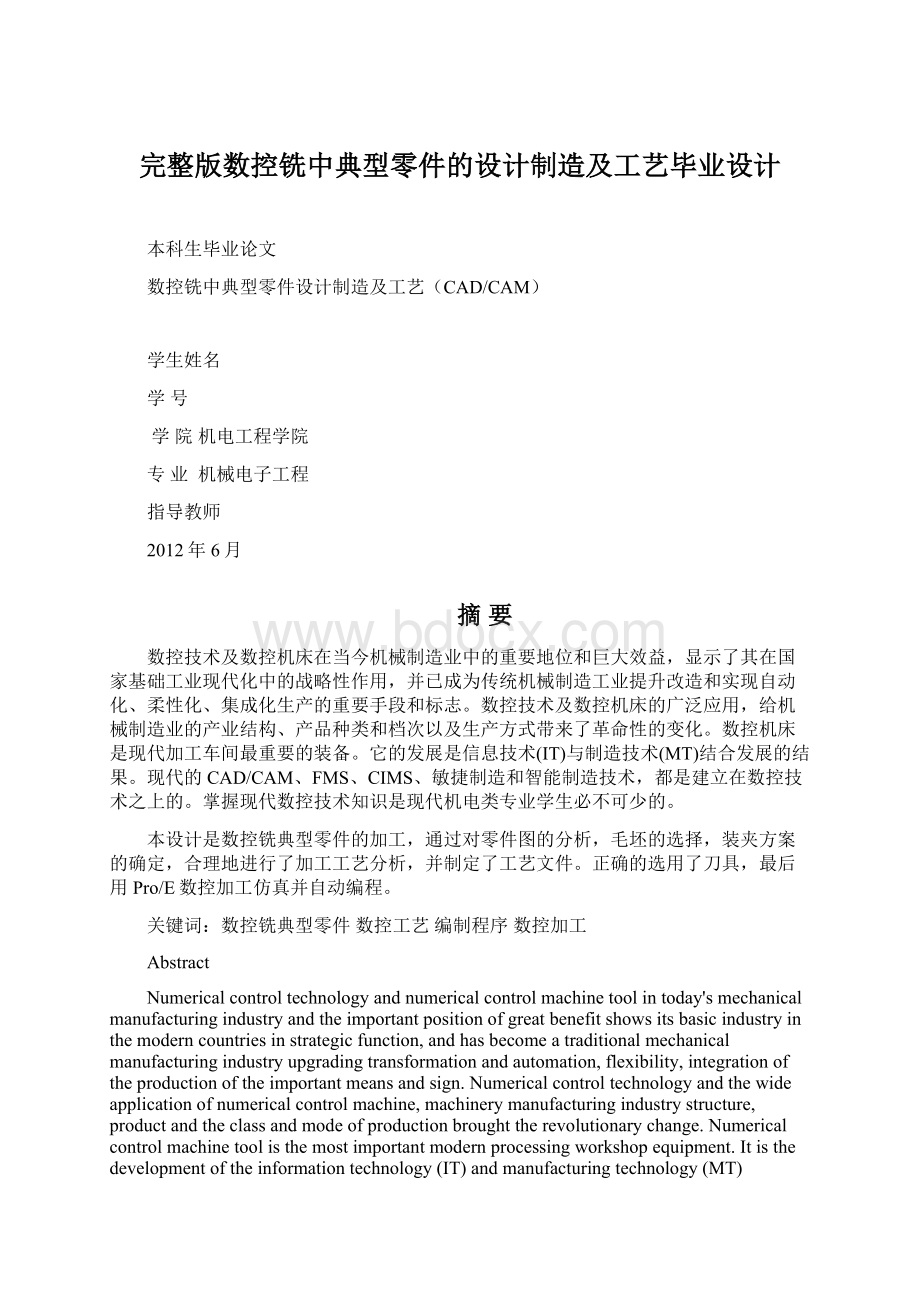
完整版数控铣中典型零件的设计制造及工艺毕业设计
本科生毕业论文
数控铣中典型零件设计制造及工艺(CAD/CAM)
学生姓名
学号
学院机电工程学院
专业机械电子工程
指导教师
2012年6月
摘要
数控技术及数控机床在当今机械制造业中的重要地位和巨大效益,显示了其在国家基础工业现代化中的战略性作用,并已成为传统机械制造工业提升改造和实现自动化、柔性化、集成化生产的重要手段和标志。
数控技术及数控机床的广泛应用,给机械制造业的产业结构、产品种类和档次以及生产方式带来了革命性的变化。
数控机床是现代加工车间最重要的装备。
它的发展是信息技术(IT)与制造技术(MT)结合发展的结果。
现代的CAD/CAM、FMS、CIMS、敏捷制造和智能制造技术,都是建立在数控技术之上的。
掌握现代数控技术知识是现代机电类专业学生必不可少的。
本设计是数控铣典型零件的加工,通过对零件图的分析,毛坯的选择,装夹方案的确定,合理地进行了加工工艺分析,并制定了工艺文件。
正确的选用了刀具,最后用Pro/E数控加工仿真并自动编程。
关键词:
数控铣典型零件数控工艺编制程序数控加工
Abstract
Numericalcontroltechnologyandnumericalcontrolmachinetoolintoday'smechanicalmanufacturingindustryandtheimportantpositionofgreatbenefitshowsitsbasicindustryinthemoderncountriesinstrategicfunction,andhasbecomeatraditionalmechanicalmanufacturingindustryupgradingtransformationandautomation,flexibility,integrationoftheproductionoftheimportantmeansandsign.Numericalcontroltechnologyandthewideapplicationofnumericalcontrolmachine,machinerymanufacturingindustrystructure,productandtheclassandmodeofproductionbroughttherevolutionarychange.Numericalcontrolmachinetoolisthemostimportantmodernprocessingworkshopequipment.Itisthedevelopmentoftheinformationtechnology(IT)andmanufacturingtechnology(MT)combinedwiththeresultofthedevelopmentof.ModernCAD/CAM,FMS,CIMS,agilemanufacturingandintelligentmanufacturetechnology,arebasedinthenumericalcontroltechnologyon.Mastermodernnumericalcontroltechnologyknowledgeismodernmechanicalandelectricalengineeringstudentsindispensable.
ThisdesignisCNCtypicalpartsprocessing,throughtotheanalysisofthedrawing,thechoiceofblank,clampingschemestodeterminethe,thereasonableprocessingtechnologyanalysis,andformulatedtheprocessdocuments.Thecorrectchoosethecuttingtools,withthePro/Encmachiningsimulationandautomaticprogramming.
Keywords:
CNCmillingtypicalparts;numericalcontroltechnology;programming;CNCprocessing
第一章绪论
随着数控技术的发展,数控技术的应用不但给传统制造业带来了革命性的变化,使制造业成为工业化的象征,而且随着数控技术的不断发展和应用领域的扩大,它对国计民生的一些重要行业的发展起着越来越重要的作用。
本课题是对我所学知识的应用,它包括了我在大学四年所学的全部知识,在机电专业上具有代表性,而且提高了我们综合运用各方面知识的能力。
程序的编制到程序的调试,零件的加工运用到了我们四年所学的专业课程:
《工程制图》、《AUTOCAD制图》、《数控技术》、《机械制造技术基础》等。
这将我所学到的理论知识充分运用到了实际加工中,切实做到了理论与实践的有机结合。
1.1数控加工内容的选择
当选择并决定对某个零件进行数控加工后,一般情况下,并非其全部加工内容都适合在数控机床上完成,而往往只是其中的一部分工艺内容适合数控加工。
为了提高生产效率,充分发挥数控的优势,选择哪些最合适、最需要的内容和工序进行数控加工。
一般可按下列原则选择数控加工内容:
(1)普通机床无法加工的内容应作为优先选择内容。
(2)普通机床难加工,质量也难以保证的内容应作为重点选择内容。
(3)普通机床加工效率低,工人手工操作劳动强度大的内容,可以在数控机床尚未加工能力的基础上进行选择。
此外在选择数控加工内容时,还要考虑生产批量、生产周期、工序间周转情况等因素,要尽量合理使用数控机床,达到产品质量、生产率及综合经济效益等指标都明显提高的目的,要防止将数控机床降格为普通机床使用。
由于本次加工零件是单件,形状较为复杂,故本次毕业设计的所有内容都选择在数控机床上加工。
1.2机床的选择
根据图形结构有曲面、轮廓、平面、内腔、椭圆、凹槽等型面,加工内容较复杂,为了避免重复定位带来的误差,减少手工换刀操作,结合我校机床的实际情况。
采用加工中心VDF850进行加工,该机床的X轴的行程850mm,Y轴的行程为510mm,Z轴的行程为510mm,工作台为1000×500mm,主轴中心线至刀库容量为20把,X,Y,Z切削速度0~760mm/min,X,Y,Z快速进给速度为
第二章数控加工工艺性分析
2.1零件毛坯余量的确定
零件在进行数控铣削加工时,由于加工过程的自动化,使用余量的大小,如何装夹等问题在选用毛坯时就要仔细考虑好,否则,如果毛坯不适合数控铣削,加工将很难进行下去,根据经验,列举以下几点:
2.1.1分析毛坯的加工余量
该图的毛坯采用铝合金,且达到要求。
所以图2-1采用206×206×66(mm)的毛坯尺寸进行加工,由于该件是铸造件,须考虑用到砂型误差、收缩量及金属液体流动性差不能充满型腔等造成余量不均匀,此外,毛坯的扭曲变形量的不同地方造成余量不充分,不稳定,因此,要采用数控铣削加工,其加工面均有充分的余量。
2.1.2分析毛坯的变形及余量大小均匀性
分析毛坯加工中与加工后的变形程度,考虑是否采用预防性措施和补救性措施,是对零件加工变形的一个重要保证。
如对于厚铝合金板,经淬火时效后很容易在加工中与加工后变形。
这时最好采用经预拉伸处理的淬火板坯,对于毛坯的余量大小及均匀性,主要是考虑在加工时要不要分层切削,分几层切削。
自动编程时,尤其重要。
2.2零件图的分析
2.2.1零件图的完整性与正确性分析
由于加工程序是以准确的坐标点来编制,零件的视图应足够、正确及表达清楚,并符合国家标准,尺寸及有关技术要求应标注齐全,图2-1中有圆弧相切,几何元素之间的关系较明确。
2.2.2零件技术要求分析
零件的技术要求主要指尺寸精度、形状精度、位置精度、表面粗糙度及热处理等。
这些要求在保证零件使用性能的前提下应经济合理。
过高的精度和表面粗糙度要求会使工艺过程复杂,加工困难,成本提高。
图2-1中要求最高尺寸公差为0.03mm,该零件最高精度等级为IT8级,被测表面与基准表面之间的平行度公差为0.002mm,表面粗糙度值全部为Ra1.6或Ra3.2,数控铣削加工经粗、精加工可达到IT9-IT7级,表面粗糙度可达到Ra3.2-Ra1.6,故比较容易加工,但加工时如果装夹不当极容易产生振荡,如果定位不好可能会导致表面粗糙度值增加,加工精度难以保证。
图2-1数控铣典型零件图
2.2.3尺寸标注方法分析
零件图上的尺寸标注方法有局部分散标注法、集中标注法和坐标标注法等。
对在数控机床上加工的零件,零件图上的尺寸在加工精度能够保证使用性能的前提下,可不必用局部分散标注,应采用集中标注或以同一基准标注,即标注坐标尺寸,这样,既便于编程又有利于设计基准、工艺基准与编程原点的统一。
图5-1中的尺寸标注采用的是同一基准标注,达到了要求。
2.2.4零件的结构工艺性分析
(1)分析零件的变形情况,保证获得要求的加工精度,虽然数控机床加工精度很高,但对一些特殊情况,就应工艺上充分重视这一问题,应当考虑采取一些必要的工艺措施进行预防。
该零件的材料是属于铸铝类零件,属于不易变形的零件,能够满足要求,对该零件可以进行退火处理等措施来减少或消除变形的影响。
(2)尽量统一零件轮廓内圆弧的有关尺寸。
若工件的被加工轮廓高度低,转接圆弧半径大,可以采用较大直径的铣刀来加工,且加工其底板面时,进给次数也相应减少,表面加工质量也会好一些,因此工艺性能较好;反之,数控铣削工艺性较差,一般来说,当R<0.2H(H为被加工轮廓面的最大高度值),这种工艺性较差。
根据图2-1,当铣U型槽时采用直径10mm键槽铣刀时,则R5mm,
即:
5>0.2×5
故:
工艺性较好
综上所述,在一个零件上,这种内腔圆弧半径数值上的工艺性显得相当重要,零件的外形、内腔最好采用统一的几何类型或尺寸,这样可以减少换刀次数,一般来说,即使不能要求完全统一,但也要力求将数值相近的圆弧半径分组靠拢,达到局部统一,以尽量减少铣刀的规格与换刀次数,并避免因频繁换刀而增加了零件加工面上的接刀阶差,降低表面质量。
2.2.5数控加工的定位基准
加工中定位基准的确定应注意以下几点:
(1)应采用统一的基准定位,数控加工工艺特别强调定位加工,若无统一的基准定位会因工件重新安装产生的定位误差而导致加工后的两个面上的轮廓位置及尺寸不协调现象,因此为保证两次装夹加工后其相对位置的准确性,应采用统一的基准定位。
(2)统一的基准可以是工件上已有表面,也可以是辅助基准,工件上最好有合适的孔作为定位基准,若没有,应专门设置工艺孔作为定位基准,称之为辅助基准,工件上如没有合适的辅助基准位置,可考虑采用在毛坯上增加工艺凸台,制出工艺孔或在后续加工工序要加工掉的余量上设置工艺孔,在完成定位加工后再去除的方法。
综上,图2-1中采用增加工艺凸台,铣两个夹持面作为基准,可以一次性装夹而加工完所要加工的表面,没有重复定位,故能保证基准统一。
如图2-2:
图2-2装夹及定位基准示意
2.3定位基准及装夹方案分析
2.3.1定位基准的选择
根据零件图及加工要求选择设备为加工中心VDF850,同普通机床一样在加工中心上加工时装夹仍应遵守六点定位原则:
(1)尽量选择零件上的设计基准作为定位基准。
(2)当零件的定位基准与设计基准不能重合且加工面与其设计基准又不能在一次安装内同时加工时,应认真分析装配图纸,确定该零件设计基准的设计功能,通过尺寸链的计算,严格规定定位基准与设计基准间的公差范围,确保加工精度。
(3)一次装夹能够完成全部关键精度部分的加工。
(4)定位基准的选择要保证完成尽可能多的加工内容。
(5)批量加工时,零件定位基准应尽可能与建立工作坐标系的对刀基准重合。
(6)必须多次安装时应遵从基准统一原则。
综上所述,我选择设计基准作为定位基准,一次装夹保证其精度,并且遵循基准统一原则。
2.3.2数控铣床夹具的确定
数控铣床夹具的选择应考虑以下几点:
(1)夹紧机构或其他元件不得影响进给,加工部位要敞开。
(2)为保持零件的安装方位与机床坐标系及编程坐标系方向的一致性,夹具应能保证在机床上实现定向安装。
(3)夹具的刚性和稳定性要好。
(4)装夹方便辅助时间应尽量短。
(5)夹具的结构应力求简单。
(6)减少更换夹具的准备—结束时间。
(7)减少夹具在机床上的使用误差。
经上综合分析,结合我校实际,该零件的装夹可选用平口虎钳及垫片和垫块作为辅助夹紧装置加工所需内容。
根据零件图分析,该零件可采取如下工艺措施:
以夹持面和两个侧面定位选用虎钳装夹,如图2-2所示。
安排粗、精加工,采用小直径铣刀铣夹持面以减小切削变形。
装夹夹持面加工上面,完成加工内容,最后翻面夹凸台面,将夹持面铣掉。
由于毛坯为铝合金在装夹时勿过于紧以免发生变形造成加工精度的误差。
2.4刀具的选择
刀具的合理选择和使用,对提高数控加工效率、降低生产成本、缩短交货期及加快新产品开发等方面有十分重要的作用。
国外有资料表明,刀具费用一般占制造成本2.5%-4%,但它却直接影响占制造成本20%的机床费用和38%的人工费用。
如果进给速度和切削速度提高15%-20%,则可降低制造成本10%-15%。
这说明使用好的刀具会增加成本,但效率提高则会使机床费用和人工费用有很大的降低,这正是工业发达国家制造业所采用的加工策略之一。
应根据机床的加工能力、工件材料的性质、加工工序、切削用量以及其他相关因素正确选择刀具及刀柄。
刀具材料切削性能的影响也非常重要:
例如切削低硬材料时可以使用高速刚刀具,而切削高硬度的材料时就必需用硬质合金刀具如表2-1所示。
表2-1刀具材料特性和用途
材料
主要特性
用途
优点
高速刚
比工具刚硬
低速或不连续切削
刀具寿命长、加工的表面较平滑
硬质合金
耐磨损、耐热
可锻铸铁、碳钢、合金钢、不锈钢、铝合金的精加工
寿命比一般工具钢高10-20倍
刀具选择的总原则是:
安装调整方便,刚性好,耐用度和精度高。
在满足加工要求的前提下,尽量选择较短的刀柄,以提高刀具加工的刚性,结合我校实际,采用高速钢刀具加工。
2.4.1刀具尺寸选择
刀具尺寸选择包括直径尺寸和长度尺寸:
(1)直径尺寸:
根据零件图样不同,选用的刀具尺寸不一样,因图而异。
选取的原则是:
在刀具能够满足加工前提下,尽量选取直径大的刀具,铣削刀具都是成型刀具且标准,在同时可根据选取刀具的直径提取刀具各异的刀具。
(2)长度尺寸:
在加工中心上,刀具长度一般是指主轴端面到刀尖距离,包括刀柄和刃具。
选取的原则是:
在满足各个部分加工要求的前提下,尽量减小刀具长度,以提高工艺系统的刚性,制造工艺和编程时,一般不必准确的确定刀具的长度,只需初步估算出刀具长度范围。
根据经验公式:
=A-B-N+L++
公式中:
—刀具长度
A—主轴端面至工作台中心最大距离
B—主轴在Z向的最大行程
N—加工表面距工作台中心距离
L—工件的加工深度尺寸
—刀具切出工件长度(以加工表面取2-5mm,毛坯表面取5-8mm)
刀具长度示意图如图2-3
图2-3刀具长度示意图
2.4.2刀具卡片的制定
对图2-1的刀具设计卡片如表2-2
表2-2数控加工刀具卡片
代号
零件名称
数控铣典型零件
零件图号
序号
刀具号
刀具
加工表面
备注
规格名称
数量
刀长/mm
刀柄型号
1
T01
25铣刀
2
50
BT40
粗铣上端面内腔,下斜面
2
T02
12铰刀
1
50
BT40
精铣上端面内腔
3
T03
25球铣刀
1
50
BT40
抛物面
4
T04
12球铣刀
1
50
BT40
抛物面
5
T05
8铰刀
1
50
BT40
抛物面
6
T06
12中心钻
1
50
BT40
钻25孔
7
T07
12钻头
2
50
BT40
钻25、12孔
8
T08
25扩孔钻
1
50
BT40
钻25孔
9
T09
12立铣刀
1
50
BT40
侧面椭圆槽
10
T10
8中心钻
1
50
BT40
钻12孔
编制
审核
批准
年月日
共页
第页
2.5切削用量选择
切削用量包括切削速度(主轴转速n)、背吃刀量和进给量f(或进给速度)其确定原则与普通机械加工相似,对于不同的加工方法,需要选择不同的切削用量,并编入程序单内。
选择切削用量的基本原则是:
粗加工时,一般以提高生产率为主,但也应考虑经济性和加工成本;半精加工和精加工时,应在保证质量的前提下,兼顾切削效率、经济性和加工成本。
具体数值应根据机床说明书,参考的切削用量手册,并结合经验而定。
2.5.1确定背吃刀量
主要根据机床、夹具、刀具和工件的刚度来决定,在刚度允许的情况下,应尽可能使背吃刀量等于加工余量,应以最少进给次数切除这一加工余量,最好一次切净余量,以提高生产效率,为了保证加工精度和表面粗糙度,一般都要留一点余量最后精加工,在数控机床上,精加工余量可小于普通机床,铣型腔=2.5mm,铣孔=2.5mm,铣外轮廓=2.5mm,铣抛物面=2.5mm。
2.5.2确定主轴转速
主要根据允许的切削速度(m/min)选取
n=(2-1)
其中-切削速度
D-工件或刀具的直径(mm)
由于每把刀计算方式相同,现选取12的立铣刀为例说明其计算过程。
D=12mm
根据切削原理可知,切削速度的高低主要取决于被加工零件的精度、材料、刀具的材料和刀具耐用度等因素,可参考表2-3选取。
表2-3铣削时切削速度
工件材料
硬度/HBS
切削速度/(m/min)
高速钢铣刀
硬质合金铣刀
钢
<225
18~42
66~150
225~325
12~36
54~120
325~425
6~21
36~75
铸铁
<190
21~36
66~150
190~260
9~18
45~90
160~320
4.5~10
21~30
铝
70~120
100~200
200~400
黄铜
53~56
20~50
100~180
从理论上讲,的值越大越好,因为这不仅可以提高生产率,而且可以避免生成积屑瘤的临界速度,获得较低的表面粗糙度值。
但实际上由于机床、刀具等的限制,综合考虑:
取粗铣时=100m/min
精铣时=150m/min
代入5-1式中:
==
=2653.93r/min=3980.8r/min
计算的主轴转速n要根据机床有的或接近的转速选取
取=2500r/min=4000r/min
同理计算10键槽铣刀:
取=2000r/min=3000r/min
2.5.3进给速度
切削进给速度时切削时单位时间内工件与铣刀沿进给方向的相对位移,单位mm/min。
它与铣刀的转速n、铣刀齿数z及每齿进给量(mm/z)的关系为
=nz(2-2)
每齿进给量的选取主要取决于工件材料的力学性能、刀具材料、工件表面粗糙度值等因素。
工件材料的强度和硬度越高,越小,反之则越大;工件表面粗糙度值越小,就越小;硬质合金铣刀的每齿进给量高于同类高速钢铣刀,可参考表2-4选取
表2-4铣刀每齿进给量
工件材料
每齿进给量/(mm/z)
粗铣
精铣
高速钢铣刀
硬质合金铣刀
高速钢铣刀
硬质合金铣刀
钢
0.10~0.15
0.10~0.25
0.02~0.05
0.10~0.15
铸铁
0.12~0.20
0.15~0.30
铝
0.06~0.20
0.10~0.25
0.05~0.10
0.02~0.05
综合选取:
粗铣=0.06mm/z
精铣=0.03mm/z
铣刀齿数z=3
上面计算出:
=2500r/min=4000r/min
将它们代入式子8-2计算。
粗铣时:
=0.06×3×2500
=450mm/min
精铣时:
=0.03×3×4000
=360mm/min
切削进给速度也可由机床操作者根据被加工工件表面的具体情况进行手动调整,以获得最佳切削状态。
2.6切削液选择
由于在切削加工过程中,被切削层金属的变形、切屑与刀具前面的摩擦和工件与刀具后面的摩擦要产生大量的热——切削热。
大量的切削热被工件吸收9%~30%、切屑吸收50%~80%、刀具吸收4%~10%,其余由周围介质传出,而在钻削时切削热有52%传入麻花钻。
由于热胀冷缩的原理,工件和刀具吸收了一部分的热量,工件和刀具产生变形最终影响加工精度。
如果大量的切削热传入刀具,容易使刀具损坏——造成“烧刀”的现象。
为了提高加工零件的精度和刀具的耐用度及使用寿命,在切削加工过程中必须使用冷却液对工件和刀具进行冷却,以避免造成“烧刀”的现象和零件精度的影响。
通过查询资料知道常用的切削液主要有以下三种,见表2-5
表2-5常用切削液
冷却液名称
主要成份
主要作用
水溶液
水、防锈添加剂
冷却
乳化液
水、油、乳化剂
冷却、润滑、清洗
切削油
矿物油、动植物油、极压添加剂或油性添加剂
润滑
从工件材料考虑,切削铝时不得使用水溶液,考虑到冷却液作用和价格,选择乳化液可以满足要求。
从刀具材料考虑,硬质合金刀具一般采用乳化液作为冷却液,其冷却效果很好。
综合以上的种种分析,采用乳化液作为冷却液效果很好。
它的主要作用:
冷却、润滑、清洗而且还有一定的防锈作用。
2.7起刀、进刀和退刀的工艺问题的处理
2.7.1程序起始点、返回点和切入点(进刀点)切出点(退刀点)的确定
(1)程序起始点
程序起始点是指程序开始时,刀尖(刀位点)的初始停留点,采用G54对刀时为对刀点。
(2)程序返回点
程序返回点是指一把刀程序执行完毕后,刀尖返回后的停留点为换刀点。
(3)切入点(进刀点)
切入点(进刀点)是指在曲面的初始切削位置上,刀具与曲面的接触点。
(4)切出点(退刀点)
切出点(退刀点)是指曲面切削完毕后,刀具与曲面的接触点。
2.7.2程序起始点、返回点和切入点、切出点的方法
(1)起始点、返回点的确定原则
在同一个程序中,起始点和返回点最好应相同,图2-1的程序起始点就是在X0Y0Z100的位置,在加工时,多个程序的设置最好也完全相同。
(2)切入点选择原则
在进刀或切削过程中,要使刀具不受损坏,一般来说,对粗加工而言,选择曲面内的最高角点作为曲面的切入点(初始切削点)。
因为该点的余量较小,进刀时不易损坏刀具。
对精加工而言,选择曲面内某个曲率比较平缓的角点作为曲面的切入点,因为在该点处,刀具所受的弯矩小,不易折断刀具。
总之,要避免将铣刀当钻头用,否则因受力大,排屑不便