纱线质量标准.docx
《纱线质量标准.docx》由会员分享,可在线阅读,更多相关《纱线质量标准.docx(34页珍藏版)》请在冰豆网上搜索。
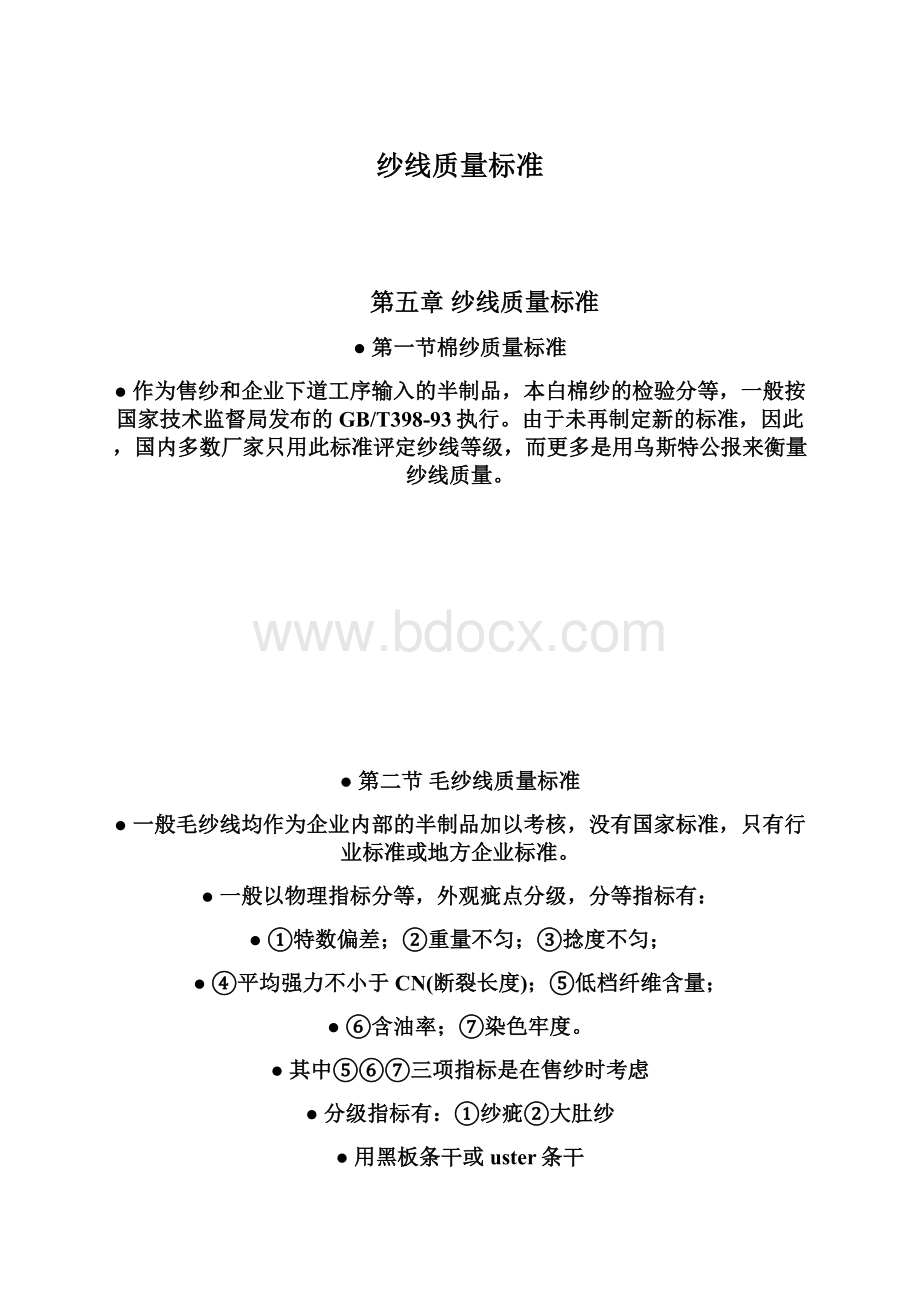
纱线质量标准
第五章纱线质量标准
●第一节棉纱质量标准
●作为售纱和企业下道工序输入的半制品,本白棉纱的检验分等,一般按国家技术监督局发布的GB/T398-93执行。
由于未再制定新的标准,因此,国内多数厂家只用此标准评定纱线等级,而更多是用乌斯特公报来衡量纱线质量。
●第二节毛纱线质量标准
●一般毛纱线均作为企业内部的半制品加以考核,没有国家标准,只有行业标准或地方企业标准。
●一般以物理指标分等,外观疵点分级,分等指标有:
●①特数偏差;②重量不匀;③捻度不匀;
●④平均强力不小于CN(断裂长度);⑤低档纤维含量;
●⑥含油率;⑦染色牢度。
●其中⑤⑥⑦三项指标是在售纱时考虑
●分级指标有:
①纱疵②大肚纱
●用黑板条干或uster条干
●粗纺、精纺参见书上表。
●第三节苎麻纱质量标准
●部颁标准FZ/T32002-92
●•以纱的内在质量:
强力及不匀、重量不匀、重量偏差定等。
●•以纱的外观质量:
条干均匀度、粗细节、麻粒定级。
●•股线:
以单纱强力及不匀、重量偏差定等,以粗节定级。
●数据参见书上表。
第四节绢丝
●质量标准部颁标准FZ/T42002-97桑蚕绢丝指标:
①断裂长度;②支数不匀;③条干不匀;④洁净度;⑤千米疵点数;⑥支数偏差;⑦强力不匀;⑧断裂伸长度;⑨捻度偏差率;⑩捻度不匀率。
其中:
②③⑤对织物外观有影响③④⑤用黑板观察
第五章纱线质量标准
●第一节棉纱质量标准
●作为售纱和企业下道工序输入的半制品,本白棉纱的检验分等,一般按国家技术监督局发布的GB/T398-93执行。
由于未再制定新的标准,因此,国内多数厂家只用此标准评定纱线等级,而更多是用乌斯特公报来衡量纱线质量。
●是全世界纺织工业中纤维、条子、粗纱和纱线进行分类的质量分级的参考指标。
上一期统计公报出版于2007年,2012年将出版新的统计公报。
采用乌斯特统计公报作为比较的标准时,纱的总质量中的特殊疵点和缺陷能很明显地表现出来,从而能迅速转化为生产过程中的改进措施。
USTER公司在世界各地用户和在瑞士的工厂中进行纤维、半制品、细纱的测试,然后进行数据整理分析,每相隔3~5年发表一次试验结果的统计值即USTER统计值。
统计值一般分5%、25%、50%、75%、95%几档,通常认为50%统计值属一般水平;25%及以下属先进水平;75%及以上属较差水平。
从1957年开始,乌斯特公司推出乌斯特统计值,它是用乌斯特仪器将世界各地取样的纱线测试结果的统计值,每隔几年在《乌斯特新闻公报》(USTERNEWSBULLETIN)上发布一次包括棉、毛两大款纱线产品共分五档水平,用统计图的方式表示,横座标为纱的线密度(号数),纵座标为质量指标的数值,采用的是双对数座标。
●一、国内有六项指标
●1单强
●2单强不匀
●3条干:
Uster条干、黑板条干
●4重量不匀率
●5重量偏差
●6纱疵点:
10万米纱疵、黑板条干纱疵
●1、普梳棉纱技术要求(参见书上表)
●2、精梳棉纱技术要求(参见书上表)
●二、Uster的2001公报
●参见书上公报统计。
●第二节毛纱线质量标准
●一般毛纱线均作为企业内部的半制品加以考核,没有国家标准,只有行业标准或地方企业标准。
●一般以物理指标分等,外观疵点分级,分等指标有:
●①特数偏差;②重量不匀;③捻度不匀;
●④平均强力不小于CN(断裂长度);⑤低档纤维含量;
●⑥含油率;⑦染色牢度。
●其中⑤⑥⑦三项指标是在售纱时考虑
●分级指标有:
①纱疵②大肚纱
●用黑板条干或uster条干
●粗纺、精纺参见书上表。
●第三节苎麻纱质量标准
●部颁标准FZ/T32002-92
●•以纱的内在质量:
强力及不匀、重量不匀、重量偏差定等。
●•以纱的外观质量:
条干均匀度、粗细节、麻粒定级。
●•股线:
以单纱强力及不匀、重量偏差定等,以粗节定级。
●数据参见书上表。
●作业:
简述棉毛麻绢纱线质量考核标准的内容。
第六章纱线不匀分析与控制
●纱线质量与织物质量密切相关,均匀度是纱线质量的关键之一。
●1)不匀率的关键点是条干不匀
●2)其次是:
棉结和纱疵
●3)再次是:
强力和支数不匀
第一节纱条不匀特性
●一、纱条不匀内容
●长度方向:
支数、直径(粗细)、强力、捻度等不匀。
●长度及径向:
混合比、纤维分布(长短)、纤维形态(伸直平行度)等不匀。
●分类:
●按纱条不匀的性质:
结构不匀
粗细不匀(重量不匀率和条干不匀率)
●按不匀的形式:
周期性和非周期性不匀
●按产生的原因:
随机不匀和附加不匀
●按所检验的范围:
内不匀
外不匀
总不匀
●粗细不匀与片段长度的大小有关:
●短片段不匀:
纤维长度×(1-10)倍
●中片段不匀:
纤维长度×(10-100)倍
●长片段不匀:
纤维长度×100倍以上
●周期不匀——机械因素造成
●非周期不匀——牵伸波
●结构不匀:
纤维分离度,纤维伸直平行度(弯钩、卷曲、倾斜),某类纤维集聚造成疵点
常用于计算半制品的条干,如萨氏条干
●三、纱条不匀率结构特性
●1、内不匀、外不匀、总不匀
●内不匀¡ª反映某片段内部均匀度变化
●外不匀¡ª几个片段间的不匀率
●总不匀¡ª不分片段为整个纱的不匀率
●C2总=C2内+C2外
●2、纱条不匀与片段长度的关系
●①有限长度的不匀为内不匀CV(L)表示内不匀CV(L)值随L↑而增高,开始时快,随后逐渐减慢,L在1m以上时为稳定值,接近纱条CV(∞)的总不匀。
¡②纱条的外不匀CB(L)
¡CB(L)与L的函数关系则是随L↑而减少
¡L→0时CB(L)→CB(0)
¡[CV(L)]2+[CB(L)]2=[CV(∞)]2=[CB(0)]2
●CV值,Uster一般200米以上则认为总不匀。
●CB(L)→0的变化率→称为变异长度曲线。
●它的变化程度反映产品的不匀好坏,变化率斜率大说明产品好
●3、纱条不匀组成
●①理想纱条随机不匀(CV1%)
●由于纤维完全随机排列于纱条中,纤维也会形成片段内不匀称随机不匀。
当纤维数n→∞,在某截面出现的概率为0,泊松分布。
●随机不匀与截面根数多少有关。
●②附加不匀CV2%
●机械波,牵伸波
●纱条
●随着牵伸次数的增加,附加不匀产生叠加,使纱条粗细呈现复合波。
附加不匀的大小,可以表征纺纱工艺的完善程度。
●纱条不匀与纺纱支数有关:
高支纱不匀较高。
●不匀率指数I,表示纱条均匀度达到的理想程度和纺纱工艺过程的完善性。
●二、纱线不匀的测试
●1、测长切断称重法
●棉卷条子粗纱细纱均可用此法
●片段1m5m10m100m
●2、目测—黑板条干
●根据标样评定,可观察片段不匀的程度和内容:
●阴影、云斑、粗细节、竹节、毛羽。
●3、电容式均匀度试验仪Uster可测纱线不匀,粗细节,结粒数。
测试的基本原理:
●1)检测头—电容极板内纤维量转为电量的变化
●2)基本原理:
电极中有纤维通过,可看作两串联电容组合。
●(3)测试方法
●①常使η保持在0.1~0.2之间。
为了保证η很小,实际上根据不同纱条,设档不同宽度极槽使用。
●测条子:
1,2,3档20mm
●测粗纱:
4,5档15mm
●测细纱:
6,7,8档8mm
●细纱为8mm片段长度之间的不匀值
●②在恒温恒湿下进行:
20±2℃,相对湿度65±3%
●③测试速度
●条子:
8米/分细纱:
50~200米/分
●由条干曲线的波长分析疵病部位(Y311型条干分析仪)
第二节提高条干均匀度
●一、重要性
¡1、条干不匀:
一般为2.5~5cm短片段不匀
¡严重的条干不匀形成粗节、细节、棉结、纱疵
¡2、条干不匀重要性
¡1)影响外观;
¡布面:
平整度、纹路
¡条影雨状白条影黑条影
细节粗节+15%粗节+10%
¡2)影响纱线强力;
¡3)影响细纱断头及后道断头;
¡4)影响捻度不匀;
●5)条干是技术与管理水平的综合反应。
●二、影响条干的综合因素
●1、原料对条干的影响
●
(1)长度:
长度与牵伸区长度相适应,并要求纤维长度整齐度好,短绒率低。
整齐度差,牵伸时,往往对短纤维难以控制,而使条干变差。
●棉纺:
配棉长度差异2-4mm
●短绒率:
美国标准:
1/2”以下的百分率
中国:
>33mm,19.5mm以下
<33mm,15.6mm以下
棉籽上自然短绒率为9%,轧棉后10-12%
清钢为15%,要求高的在10-13%,
在16%以上时纺纱质量下降
其中10mm以下的对条干影响最大。
所以要增加排除短绒的机会,选棉时应考虑皮辊棉和锯齿棉的不同。
●毛纺
●•梳毛配毛时,长度差异<20%;混毛配毛时,长度<10mm;
•绢纺精绵配绵时,相邻级相配,长度相近。
短纤率<16%;
•麻绢注意超长纤维,超长纤维造成纤维同时被前后罗拉握持而造成牵伸不匀。
●
(2)细度:
纤维细度影响纱条截面中纤维根数。
●纱线截面根数:
●由根数分布引起的不匀:
●n增加,成纱条干均匀度好,所以当纺高支纱时,由于成纱中纤维根数少,应选用纤维细度细的,可提高成纱条干均匀度。
同时要求纤维细度不匀率小,以提高不匀率。
●配棉时,要求纤维细度差异500-800公支;
●配毛时,要求直径<2μm;
●配麻时,按细度;
●配绢时,不考虑。
(3)其他纤维性质
●成熟度、卷曲、导电、摩擦系数
●2、半制品结构及条干均匀度
●结构:
指短纤维率、纤维整齐度、分离度、平行伸直度、棉结杂质。
●纤维分离度:
当纤维分离度不良时,纤维束内部联系力大,牵伸时,易成束运动而影响条干。
纤维分离度不良时,短绒、杂质去除不好,同时纤维牵伸平行度就差,这些均影响条干均匀。
●纤维平行顺直度:
当纤维平行顺直度差时,①其有效长度短,在牵伸区中的游离时间长;②纤维不伸直易相互缠结,而易集束运动;③由于不伸直在牵伸时,运动规律受影响。
因而导致条干不匀,即牵伸波严重。
●清棉:
在减少纤维损伤的情况下提高棉块的开松度和混合均匀度,贯彻多包抓取、精细抓棉、大容积混合、增加自由打击、减少握持打击、梳打结合、以梳为主,做到棉卷纵横均匀度良好。
●梳棉:
采用高速度、强分梳、良转移的工艺原则。
●如适当提高锡林速度,保证刺辊锡林速比,增加附加分梳元件,采用新型针布,加强除杂除尘吸风,提高棉网清晰度,以改善生条质量。
●并条:
针对生条纤维结构较乱、前弯钩较多,着重改善纤维的伸直平行度,减少弯钩纤维在并条形成棉结的机会,选用适宜的牵伸工艺,保持良好的机械状态,以提高并条棉条的条干均匀度。
●粗纱:
保证喂入须条的良好结构状态和条干均匀度不受破坏,选用先进的牵伸型式、合理的牵伸工艺、保持良好的机械状态。
●3、细纱牵伸工艺
●条干不匀主要指短片段不匀,因此细纱上加强控制就更显重要、直接、有效
●棉纺:
●1)采用先进的牵伸型式:
四种现代牵伸装置
●2)喂入纱条特数与成纱条干的关系:
●α1=α0E+X(E-1),
●牵伸倍数↑附加不匀越大。
如纺出细纱特数不变,喂入纱条特数越大,所需牵伸倍数越大、则附加不匀越大。
●3)细纱特数与成纱条干的关系
●细纱特数小,纱线截面纤维根数少,成纱条干不匀大。
●4)细纱后区工艺
●第一类工艺:
机织纱1.25~1.50,
●针织纱1.02~1.15
●第二类工艺:
1.50~1.80
●第一类工艺条干均匀度好,普遍采用。
●采用两大两小工艺:
粗纱捻系数大,细纱后区隔距大,粗纱牵伸小,细纱后区牵伸小。
●5)罗拉握持距
¡R=LP(纤维品质长度)+K(牵伸力系数)
¡在牵伸力与握持力平衡的条件下,R偏小掌握有利于对纤维的控制,罗拉要有适当的加压。
缩短前牵伸区浮游区长度并适当加重前钳口压力,有利于改善成纱条干。
●6)机械状态
¡罗拉的偏心,胶辊不圆整,弹性不匀等均会造成握持钳口偏移或速度变化,而使纤维变速不规律,产生机械波。
●7)车间温湿度
¡车间温湿度影响纤维摩擦性能,导电性能等
●8)操作接头、清洁工作。
第三节降低细纱重不匀
●一、影响
¡重量不匀是长片段不匀,它影响到:
¡1布面;2细纱重量偏差;3细纱强力不匀。
●二、措施
¡棉卷→细纱经100多万倍牵伸
¡细纱重不匀>100m片段才能反映出来
¡要降低细纱重量不匀率,主要是控制细纱之前各工序的不匀
●棉纺:
¡1、提高棉卷均匀度
●控制棉卷重量不匀率(±1%)、重量偏差(±1~1.5%)(开清棉工序)
●注意:
¡1)提高机器运转率在85%以上,保证定量供应
¡2)控制棉箱内储棉高度和密度
¡影响均匀混合和开松。
棉高度占棉箱2/3~3/4,化纤1/2,棉箱中棉量波动少,密度均匀。
¡3)天平调节装置动作正确、灵敏
¡4)尘笼气流:
影响棉卷横向均匀度
¡要求尘笼气流均匀,不产生涡流,不跑偏,不翻滚,上下集棉比7:
3。
¡5)防粘卷措施
●2、降低梳理生条重量不匀率<4%
●1)统一落棉:
落棉均匀,台间差异<0.5%;
●2)统一工艺,机械状态良好;
●3)换卷与生头:
防接头不良;
●4)张力牵伸合理;
●5)控制车间湿度,防止棉卷粘卷,棉网破洞、破边;
●6)采用清钢联(自调匀整)。
●3、控制熟条重量偏差和不匀——关键工序。
●控制熟条偏差1%,(粗支<2.5%)
●1)轻重条搭配;
●2)每台每眼一个班试验3次,及时更换牵伸牙。
●4、控制粗纱重不匀
●粗纱、细纱不能降低前边的重量不匀率,只能做到不恶化或少恶化
●主要控制张力。
(前后排,锭间,大中小纱)
●张力差异→伸长差异<1.5
●5、细纱
●1)定设备:
同品种使用同一机型
●2)加强巡回;
●3)加强设备维修
●6、自调匀整装置的应用
●清钢并上已普遍使用。
●作业:
●论述从原料到纺纱各工序如何改善条干和重不匀。
●纱线不匀包括哪些考核指标,它们之间的关系如何?
第七章成纱强力
●一、对后道的影响
●纱强影响纺纱工序顺利进行,影响织造顺利及织物强力。
●二、纱强的组成:
●P=Q+F
●Q:
全部断裂纤维所构成的部分强力
●F:
全部滑脱纤维所构成的部分强力
●提高纱线强力应从这两方面入手,即选用强力高的纤维;另一方面,提高纤维抱合性,增加纤维的接触面积。
●三、影响单纱强力因素
●1原料性状
●1)长度↑,纤维间接触机会增加,抱合力增加从而减少滑脱,当长度达到一定值时,再增加长度,强力提高不明显。
●棉16mm以下短绒↑:
浮游纤维↑,粗细节↑,条干恶化,强力不匀↑,强力↓
●2)细度
●A当N纱一定时,纤维细,根数多,接触面积大,纤维细,断裂长度长,所以F、Q增加纱强增加。
●B纤维细→柔软,内外转移机会多→纤维间联系力大
●C纤维细→天然卷曲多→纤维间联系力大
●3)断裂长度:
长,纱强增加。
●4)成熟度
¡成熟度增大,纤维强力增加,但细度低,一般选用成熟度适中的纤维。
纺细特纱时,着重考虑纤维细度,成熟度可稍差,由于根数多,纤维间抱合力增大,成纱强力反而不低,而纺中粗特纱时,着重考虑成熟度。
5)其他因素
●车间温湿度↑→吸湿横截面↑,延伸性↑,纤维柔软,抱合力↑。
●2纺纱工艺
¡1)开清、梳理工序
¡工艺参数配置要利于开松、梳理,增加纤维分离度,排除杂质和短绒,同时要减少纤维损伤;棉卷结构良好;梳理应“紧隔距强分梳”,加强梳理,减少损伤和短绒。
¡开清参数:
打手速度、打手与罗拉与尘棒PT、尘棒间PT、打手型式等
●梳理参数:
刺辊n、分离工艺长度、除尘刀位置、锡林与盖板PT、盖板速度。
●2)并条、粗纱
●提高纤维平行顺直度,提高条干均匀度。
●粗纱适当提高温湿度,使回潮率在7%,一定回潮率有利牵伸,加强对纤维运动的控制,降低粗纱不匀。
●3)细纱工艺对成纱强力的影响
●细纱工艺配置要有利于条干,条干不匀↑,强力↓。
●细纱捻度
●①临界捻度
●捻度↑:
●a纤维间的联系力
●加强,滑脱减少,
●增加了纤维断裂根数,强力↑
●b纱轴向承受的有效分力减少,强力↓
●c内外层β不同,纤维应力分布不同。
使纤维断裂的不同时性加剧
●dβ↑,纤维受张力↑,应力↑,使可承受的拉力↓,强力↓。
●故存在临界捻度。
●②捻不匀
¡捻不匀↑,强力差异大
¡故锭速要小→捻不匀↓,强力不匀↓
③前罗拉输出的须条结构要有良好的紧密度。
¡即牵伸区选用合适的集合器,使前罗拉输出须条紧密。
●④纺纱张力适当,可使纤维伸直、纱条紧密。
●1.简述强力的构成及其对后道的影响。
●2.论述从原料到纺纱各工序影响成纱强力的因素。
第八章成纱结粒和毛羽
●短纤维——棉纺:
●一、影响:
●1、纱、布外观,印、染色差;
●2、条干不匀:
粗节内棉结占18%;
●3、断头:
由于强力和张力突变。
●二、分类:
¡1、杂质:
破籽屑、尘土、不孕籽屑、软籽表皮、带纤维籽屑、僵片。
¡2、棉结—纤维相互扭结而成的小棉团。
¡有:
松棉结—结构松散周围有长纤。
¡紧棉结—短绒扭结染后色浅。
¡状态棉结—短纤或纤维包含僵片等杂质。
¡3、白星:
死纤维形成。
●4、毛羽:
纤维头端、短绒、飞花、纤维扩散形成。
●三、测试
¡1、棉结(白星)杂质,可用黑板目测计数和Uster仪器检测。
●2、毛羽检测
●目:
目测
●显微镜
●光:
光电计数
●重:
烧毛失重
●四、减少棉结杂质
●1原棉性质
●1)原棉本身杂质、不孕籽、棉籽、破籽。
●2)成熟度
●①成熟度与细度、短绒率、僵棉呈负相关;而细度、短绒率、僵棉与棉结杂质呈正相关。
●②成熟度正常,抗弯、抗压、抗打击性能好,成纱棉结杂质少。
成熟度系数一般选1.5~1.6以上。
●3)短绒
●①不易伸直平行、易扩散粘附
●②短纤维难控制,梳理中易绕
●③大部分是较脆弱的未成熟纤维
●4)轧棉质量
●•锯齿棉:
纤维损伤大,棉结索丝多,含杂少。
●•皮辊棉:
纤维损伤小,但无排杂装置,僵棉、软籽表皮多,棉结少,含杂多。
●2、纺纱工序
¡1)棉结的产生和排除
¡棉结的排除、形成和分裂贯穿在整个工序中。
¡从原料到清棉,结杂、短绒增加,到梳棉,排除多于产生数,经并条和粗纱,棉结杂质:
粒数↑,粒重↓。
¡①牵伸增加棉结,由于纤维间磨擦所致。
¡②梳棉是控制棉结、杂质、短绒的关键工序:
●刺—给棉板,锡—盖板,锡—道夫:
易形成棉结和分裂棉结,原大变小,原松变紧。
●2)清钢合理分工
●①粘附力较大的带纤维籽屑,粘结纤维的杂质,应在梳棉上清除。
●②原棉含杂3%,则棉卷应含杂1∼1.5%
●清棉:
落棉率与原棉含杂率的比率为80∼110%;
落棉含杂率在50∼68%;
除杂效率50∼60%。
●梳棉:
总落棉率3∼4%
后车肚落棉对棉卷含杂的比为120∼220%
落棉含杂40%以上
除杂效率:
刺辊50∼60%
盖板5∼10%
吸尘10%
●3)提高分梳质量
●①喂入棉卷结构良好
●②紧隔距强分梳
●③减少搓转
●④增加分梳件
●⑤除尘刀:
低刀(落杂大、)大角度(回收)。
●4)精梳工序—除杂最有效的工序
●5)温湿度:
清棉60%,棉卷回潮6.5~7%,梳棉55~60%,生条回潮率6.5%。
●6)并条部分提高纤维平行顺直。
●五、减少白星
●死纤维棉结,它的形成和防止与棉结相同。
●六、减少毛羽
●1.种类:
通常以2mm以上计(以纱干为主体)分顺向、倒向、两向、浮游毛羽。
●2.形成:
●①纤维弯钩、短绒;
●②牵伸过程中纤维扩散;
●③气圈离心力;
●④加捻部件不清洁;
●⑤飞花。
●3.控制:
¡①减少原料中的短绒量;
¡②精梳落棉↑毛羽↓;
¡③提高粗纱捻系数;
¡④进行集束,防止扩散;
¡⑤钢领钢丝圈,特别是钢丝圈:
重量、截面形状、圈形、通道、交叉缺口。
●长纤维¡ª¡ª毛麻绢纺
●一、减少毛麻绢成纱的结粒
●1、毛粒的成因和控制
●1)原料在预处理过程中产生毡并,初加工工艺要适当防止湿热状态下的毡缩
●2)梳毛条中毛粒过多
●主要是:
净毛含油多、土杂多、隔距不当、针布不锋利、回潮大、速比不当、操车周期过长。
●3)针梳条毛粒过多
●主要是:
针板不良、缺针、断针、清洁机构工作不良、毛条通道不洁。
●4)精梳条毛粒过多
●a、毛网正面毛粒多
●喂入过大、厚薄不匀、园梳梳理不良、隔距过大、始梳位置不当、小毛刷过高、拔取隔距不符工艺要求、喂给长度过长。
●b、毛网反面毛粒多
●顶梳位置过高、产生拉毛、顶梳不洁、缺针或抬起过早。
●必须从原料开始,各道严格把关。
●2、麻粒成因与控制
●1)成因
●①与纤维的机械物理性质有关:
●纤维愈长、细,则易于弯曲形成麻粒。
●②梳理过程中纤维断时,由于急弹性而产生回缩卷曲形成麻粒。
●③喂入量过大、隔距过大、针布不锐利、缺针、断针、纤维绕锡林,在针面间搓转,产生麻粒。
●④回潮过高,易于缠结,易绕锡林,降低梳理效率。
●⑤工艺参数不当,清洁工作不力,易生麻粒。
●⑥针、并、精梳条,麻粒过多,与毛粒成因一样。
●2)麻粒控制
●针对性地在原料、加油、回潮、各道设备状态,清洁工作,操作程序方面加强管理。
●3、绵粒的成因与控制
●1)绵粒成因:
即
●①原料本身存在
●②精练过熟
●③纤维细长易缠结形成绵粒
●④梳理工艺不当
●2)绵粒控制
●减少绵粒,从原料抓起。
●对原料状态、加油水、回潮率应严格控制;
●各道工艺设计,设备状态,操作规范,清洁工作加强管理。
特别应加强精梳及烧毛工序,清除绵粒的作用。
●论述从原料到纺纱如何减少成纱的棉结杂质。
布面疵点
●直至现在为止,国际间还没有任何认可布料检定标准,但西欧和美国等地均有其常用十分制评法、四分制评法以控制处理布料疵点,这两个是最常用的制度。
●l)十分制评法
此检定标准适用于任何纤维成份、封度和组