单件流一个流.docx
《单件流一个流.docx》由会员分享,可在线阅读,更多相关《单件流一个流.docx(15页珍藏版)》请在冰豆网上搜索。
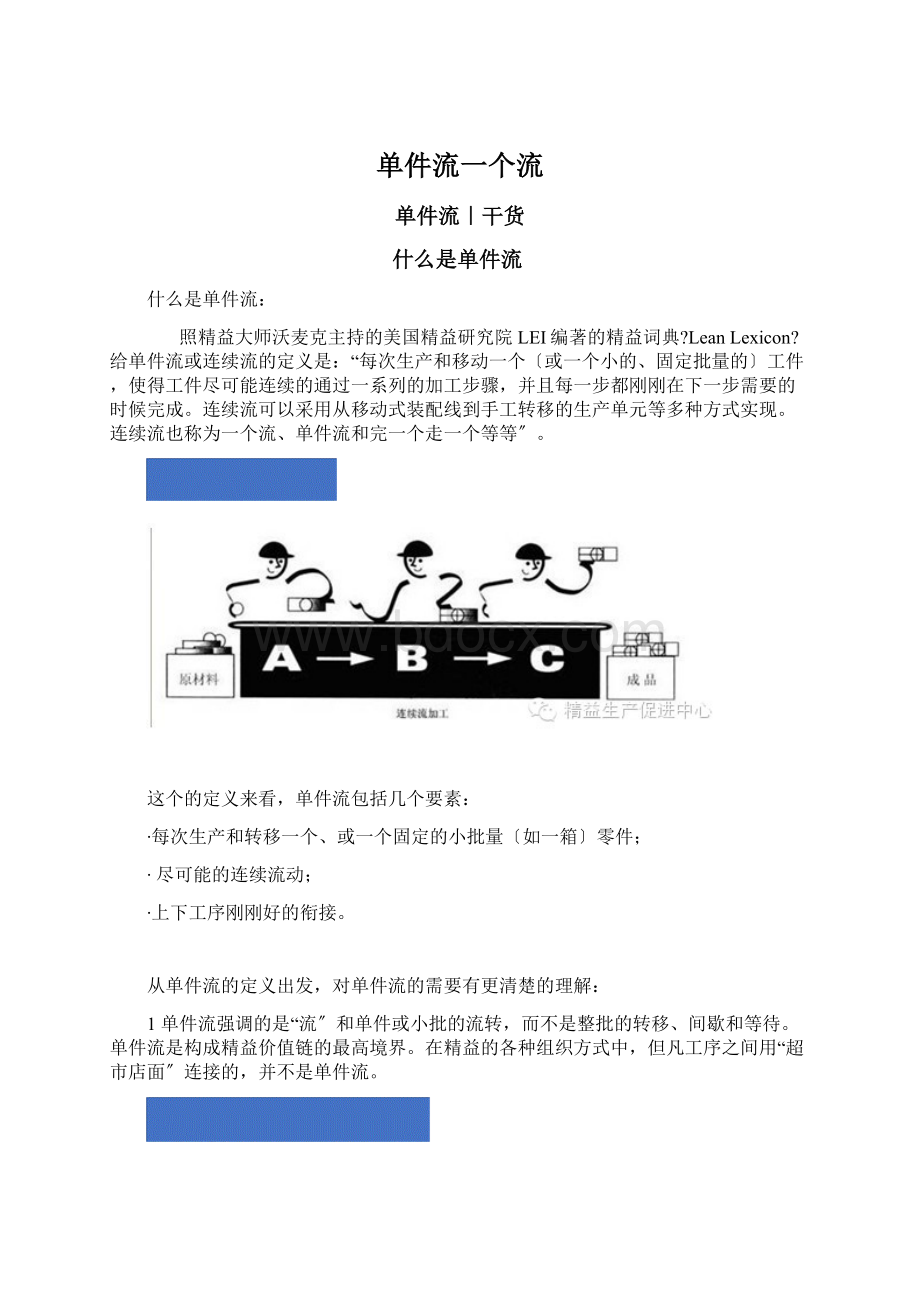
单件流一个流
单件流|干货
什么是单件流
什么是单件流:
照精益大师沃麦克主持的美国精益研究院LEI编著的精益词典?
LeanLexicon?
给单件流或连续流的定义是:
“每次生产和移动一个〔或一个小的、固定批量的〕工件,使得工件尽可能连续的通过一系列的加工步骤,并且每一步都刚刚在下一步需要的时候完成。
连续流可以采用从移动式装配线到手工转移的生产单元等多种方式实现。
连续流也称为一个流、单件流和完一个走一个等等〞。
这个的定义来看,单件流包括几个要素:
∙每次生产和转移一个、或一个固定的小批量〔如一箱〕零件;
∙ 尽可能的连续流动;
∙上下工序刚刚好的衔接。
从单件流的定义出发,对单件流的需要有更清楚的理解:
1单件流强调的是“流〞和单件或小批的流转,而不是整批的转移、间歇和等待。
单件流是构成精益价值链的最高境界。
在精益的各种组织方式中,但凡工序之间用“超市店面〞连接的,并不是单件流。
2单件流过程是自动〔由工人自主〕流动,不设置工序间的间歇和人工的控制,零件进入单元后自动周转,直至完工或流出单元;
3在实现单件流时,在同一台设备上加工不同的品种零件的快速换装和快速转移是最根本的条件。
但是连续的流动和各工序之间刚刚好衔接是单件流更本质的特征。
4单件流和按箱或按小批流动是不矛盾的。
实际上,在多数实行JIT生产的企业中,看板拉动的单位都是标准容器〔箱〕。
并且根据企业的产品特点——体积小、数量相对较大,使用一件一件的转移并不方便。
为什么要推行单件流
为什么要推行单件流?
1、缩短生产周期,由于单件流是所有生产人员分制程的同步作业,最大程度的减少了人力资源的浪费,生产效率的提高大大的缩短了生产周期。
2、降低在制品库存:
由于单件流生产形式是后拉式的生产模式,既最后一道工序需要多少,前工序才生产多少,所以它的制造过程中就是每工序同步运作一次即一个成品出车间,如无特殊情况,几乎可到达无库存。
3、节省生产空间:
由于单件流是快速出成品的制程,在生产过程中无需库存任何材料,大大节省了生产空间。
4、减少不良品数量:
单件流的生产模式是以一件为批量,整条流水线同步作业一次即出一件成品,所以能及时发现问题,最大程度的减少了不良品发生的机率。
(编者注:
单件流的好处,由于没有中间在库,一个工序发现NG时机器停止运转,其它工序也跟着停止作业。
这样可以防止大批量的产生不良〕
5、提高生产力:
单件流的精髓是单元同步,每个岗位即为一个单元。
习惯性的同步协调,培养了团队合作的精神、高度团结、高度集中精力的结果大大提高了生产力。
〔编者注:
大批量生产时各工序间有大量库存,掩盖了很多浪费。
实行单件流生产后没有中间在库的掩盖,很多问题点都会浮出水面,问题显现化得以更好的解决问题消除浪费。
〕
实现单件流的条件
实现单件流的根本条件:
一、有形成流的环境:
形成流动的环境可以是移动式装配线、按工序顺序和节拍排列的机床组、柔性制造单元或手工移动的制造单元等。
就像开渠引水一样,没有河道就没有流;也有直接将单件流定义为“在单元环境下的制造零件的方法〞。
可见单元布置对实现单件流的作用。
二、生产条件的稳定性:
设备、工具、人员可用性有保障,不会因为临时故障发生堵塞;〔理想状态是做到自働化〕
三、标准化工作:
作业标准,执行作业的时间、动作都严格按标准行事,没有随机的行为影响整个价值流的流畅;〔制定各类标准,并且严格遵守执行〕
四、按客户同步节拍生产:
生产节拍就是流动的步伐,各个工序或者到达各个站点的步伐不一致就会出现脱节或堵塞;〔每个工段都按客户的订单方案量来安排TT时间,同节拍运行。
〕
五、JIDOKA:
在多品种小批量复杂产品生产中,实现单件流最严重的问题是按需求的配比均衡生产问题。
按照精益生产原那么,生产是由客户需求拉动的,不管怎样流,其目标是满足总装配的配套需求。
从生产的全局看,“单项独进〞是没有用的,最后仍旧是积压和停滞。
在多品种小量生产中,要求在同一条生产线上满足多种零件加工的需要,是“齐头并进〞。
在一条生产线上绝对的齐头并进是做不到的,因此究需要频繁更换加工对象。
复杂产品制造实现单件流的挑战
复杂产品制造实现单件流的挑战
满足上期我们讲的实现单件流的大局部条件要靠长期的精益生产根底的积累,如持续的进行标准化工作、提供全员设备管理创造好的稳定的生产环境,增强质量意识等等。
快速换装在实现单件流中非常重要,在多数工厂中也是个非常困难的问题。
快速换装问题的症结不在于技术,而在于现有规章制度和业务分工对工装改良的认可。
必须突破这些桎梏!
。
一、做到按单件流动起来很不容易,但是做到按配套的品种均衡的流动更不容易。
要害有两个障碍:
单件流的系统设计:
单件或单件流是构成精益价值链的最高境界。
在复杂零件的制造过程往往因为工艺的多样化而难以实现全线的单件流,一般都是分段实现的,在两个单件流之间有超市或其它精益组织形式作为缓冲。
单件流作为零件族价值链的一局部,它的设计必定是与整个零件族的流程设计捆绑在一起的。
设计价值流的最有效的方法是是价值流图VSM。
1.怎样创造流动的渠道:
构建面向零件族的制造单元问题:
2.怎样才能实现均衡投产的问题。
对于复杂产品制造企业其难度在于:
a.毛坯供给的不均衡,形不成均衡的价值流,成为实现单件流的最大障碍;
b.传统的大批量生产的观念,不适应控制节拍的生产,“早投多投〞的做法根深蒂固,总是要出来干扰新的生产秩序。
二、面对这些困难,在复杂产品制造企业实现怎样的单件流就是各需要讨论的问题。
单件流我们可以分三个阶段推行
1可以先回避真正全线流动的效果,实现局部工序间的快速流动即可;这样可以获得快速换装的成果;
2实现局部某些工序之间的单件流;
3整个价值流全线的精益生产。
编者注:
可参考我们分享的:
【精益学堂】丰田秘籍:
JIT推进步骤〔点—线—面—链〕
实现单件流不是目的:
精益大师JimWomack在给精益企业研究所各地成员的一封信中指出,批评了将孤立使用精益工具而无视改变企业组织或转变现有的管理方式的倾向。
他写到:
“企业管理人员总是在用遍所有简单但不管用的方法后,才会慢慢领悟虽然困难但却有效的方法。
〞他认为,就是因为这种对精益工具的低层次应用,十五年过去了,离打造出第二个丰田,仍有相当的距离,更不用说第三个、第四个或者第五个。
JimWomack在这里提出了一个新的名词:
精益管理leanmanagement。
他提倡在进一步实施精益工具之前,必须对精益管理做更多的思考。
让精益运动与精益管理的根本原那么接轨。
他提出的精益管理仍旧是从整个价值流和整个企业的全局出发为客户创造更多的价值。
而与精益管理挂钩的具体方法,仍旧是价值流图和价值流分析。
三、所以,复杂制造企业想要将单件流〔也是一种精益工具〕真正付诸实现,必须闯过以下几道关:
1.制造单元的组织关
2.克服过量投产的思想关
3.标准化工作和生产设施稳定性的根底关,
4.快速换装的技术关,
5.均衡投入的领导关。
其中和信息技术手段的结合尤为重要
精益生产单件流导入六步骤
导入精益生产单件流分为以下六个步骤:
1、分析价值流及P/Q〔P表示品质,Q表示各种数量〕,确定重点改善流程区间和典型产品
首先从价值流分析,发现企业流程上重点浪费的流程段,之后再以P/Q选择典型产品,同时确定典型产品的工艺特性是否适合单元生产,从而选择对改善企业流程具有冲击力的主力产品进行调查。
2、现状调查、立即改善
现状调查包括品种、数量、效率、品质等生产绩效数据,更重要的是浪费数据,还包括已有结果的数据和作业标准、设备点检基准等关键要素的数据。
其中浪费严重可以立即改善的工程,要马上执行改善,如工具现状的最优化改善、生产周期核心的同步化改善以及均衡化改善〔包括平衡生产线改善〕等。
3、设备改革与工程设计
进行单元生产线的设备改善与工程设计,为能实现流水线的改善方案做工程准备。
4、作业改革设定标准作业
根据步骤1和步骤3的现状得到的时间数据与工程设计当中的布局图,做出标准作业组合表。
5、多能工训练
根据步骤4进行生产线内的标准多能工作业训练。
6、实施单元生产线
把原来传送带中的物品、设备、工具全部转移为U形布局〔撤销传送带〕,等单元生产线生产稳定后,再进行以简易自动化为中心来提高生产效率和品质的改善精益活动,最后再提高单元生产线的水平,根据同步化均衡化的生产原那么,彻底消除浪费,从而提高整个生产线的生产效率。