炉外精炼工艺的研究.docx
《炉外精炼工艺的研究.docx》由会员分享,可在线阅读,更多相关《炉外精炼工艺的研究.docx(14页珍藏版)》请在冰豆网上搜索。
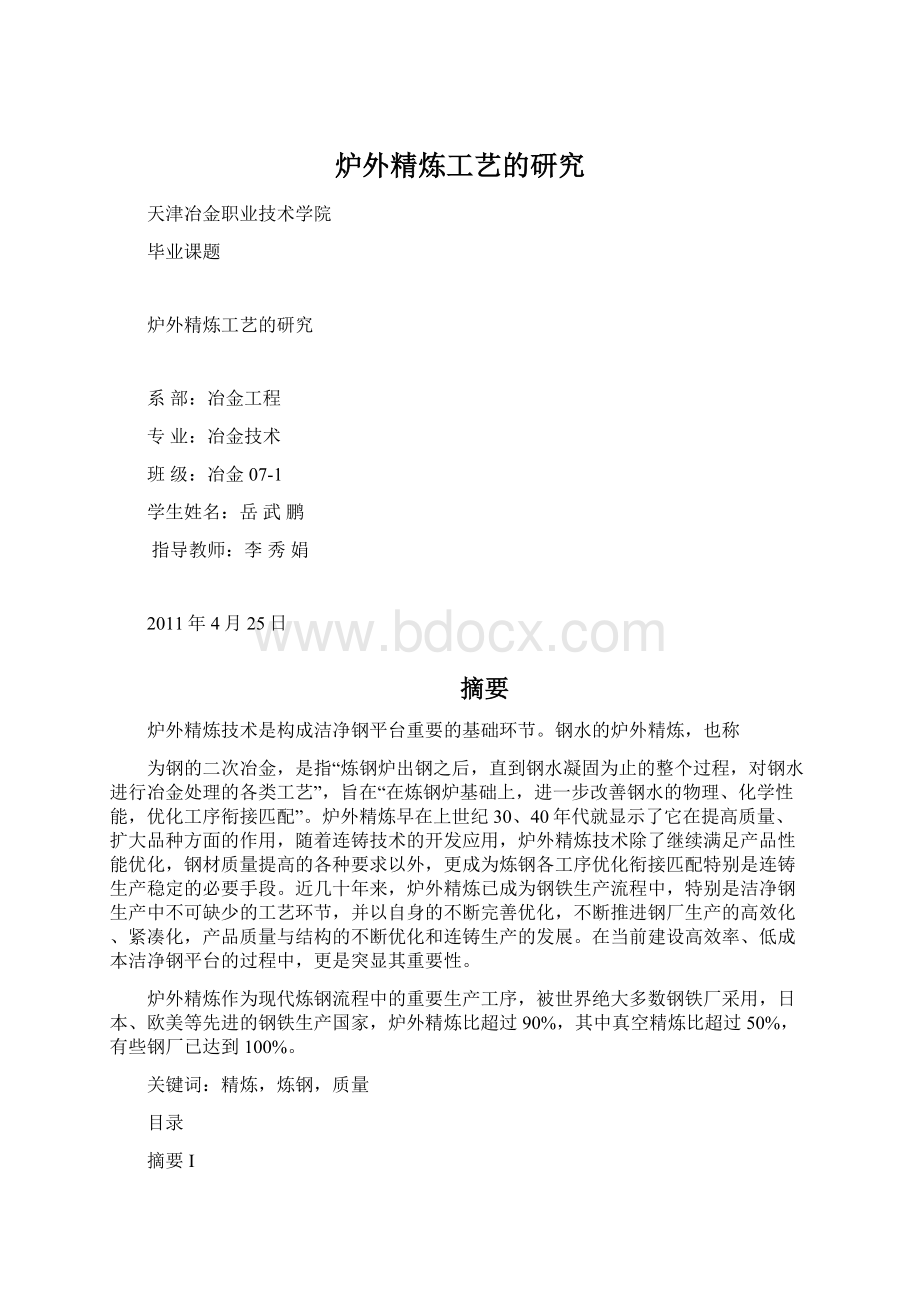
炉外精炼工艺的研究
天津冶金职业技术学院
毕业课题
炉外精炼工艺的研究
系部:
冶金工程
专业:
冶金技术
班级:
冶金07-1
学生姓名:
岳武鹏
指导教师:
李秀娟
2011年4月25日
摘要
炉外精炼技术是构成洁净钢平台重要的基础环节。
钢水的炉外精炼,也称
为钢的二次冶金,是指“炼钢炉出钢之后,直到钢水凝固为止的整个过程,对钢水进行冶金处理的各类工艺”,旨在“在炼钢炉基础上,进一步改善钢水的物理、化学性能,优化工序衔接匹配”。
炉外精炼早在上世纪30、40年代就显示了它在提高质量、扩大品种方面的作用,随着连铸技术的开发应用,炉外精炼技术除了继续满足产品性能优化,钢材质量提高的各种要求以外,更成为炼钢各工序优化衔接匹配特别是连铸生产稳定的必要手段。
近几十年来,炉外精炼已成为钢铁生产流程中,特别是洁净钢生产中不可缺少的工艺环节,并以自身的不断完善优化,不断推进钢厂生产的高效化、紧凑化,产品质量与结构的不断优化和连铸生产的发展。
在当前建设高效率、低成本洁净钢平台的过程中,更是突显其重要性。
炉外精炼作为现代炼钢流程中的重要生产工序,被世界绝大多数钢铁厂采用,日本、欧美等先进的钢铁生产国家,炉外精炼比超过90%,其中真空精炼比超过50%,有些钢厂已达到100%。
关键词:
精炼,炼钢,质量
目录
摘要I
1炉外精炼的冶金功能1
1.1炉外精炼的冶金特点1
1.2炉外精炼的冶金功能2
2国内外炉外精炼技术发展特点3
3攀钢炉外精炼技术现状4
3.1钢包吹氩精炼4
3.2LF炉精炼5
3.3RH精炼7
4存在的主要问题11
4.1炉外精炼功能与产品结构优化的要求尚不协调11
4.2对精炼的功能解析、理解与合理利用还不够深透11
4.3对炉外精炼技术的经济性认识不够深入11
4.4精炼相关技术还有待提高11
5改进思路12
5.1进一步提高钢水真空精炼比12
5.2进一步提高炉外精炼工艺技术,实现高效化12
5.3重视具有重要功能的吹氩、喂线、合成渣洗精炼技术规范与优化12
5.4实现炉外精炼工艺的自动控制12
5.5重视专线化生产的推广应用13
5.6重视中间包冶金技术的开发13
参考文献14
1炉外精炼的冶金功能
炉外精炼工艺方法种类繁多,基本上分为真空和非真空精炼两大类,主要包括钢包吹氩精炼工艺(LT、CAS)、LF(钢包炉)精炼工艺、VD真空精炼工艺、RH真空精炼工艺、VOD真空吹氧精炼工艺、AOD氩氧精炼工艺等。
表1.1列出了各种炉外精炼设备的冶金功能比较。
表1.1各种炉外精炼设备的冶金功能比较
精炼工艺
精炼设备
搅拌
升温
合金化
精炼功能
生产调节
脱气
脱碳
渣洗
喷粉
夹杂物处理
非真空处理
CAS
▲
▲
▲
-
-
□
-
△
▲
LF
△
▲
▲
-
-
▲
-
▲
△
真空处理
AOD
▲
▲
△
□
△
△
-
△
□
RH
▲
△
▲
▲
▲
□
▲
△
▲
VD
△
-
▲
▲
□
△
-
△
△
VOD
△
△
▲
▲
▲
△
▲
△
△
▲强 △一般 □较弱 -不具备
1.1炉外精炼的冶金特点
各种炉外精炼设备都具备高效精炼的特点,能满足以下冶金特点:
(1)改善冶金反应的热力学条件。
如脱碳、脱气反应,反应产物为气体,降低气相压力,提高真空度,有利于反应继续进行。
(2)加快传质速度。
对于多数冶金反应,液相传质是反应速度的限制环节,各种精炼设备采用不同的搅拌方式,强化熔池搅拌,加速混匀过程,提高化学反应速度。
(3)增大渣钢反应面积。
各种炉外精炼设备均采用各种搅拌或喷粉工艺,造成钢渣乳化,显著增加渣钢反应面积,提高反应速度。
(4)精确控制反应条件,均匀钢水成分、温度。
各种炉外精炼设备,配备了不同的加热功能,可以精确控制反应条件,使各种冶金反应更趋近平衡。
同时,通过搅拌均匀钢水成分,精确调整成分,实现成分微调。
1.2炉外精炼的冶金功能
炉外精炼设备的冶金功能主要包括:
(1)搅拌功能,均匀钢水成分和温度,保证钢材质量均匀。
(2)提纯精炼功能,通过钢渣反应、真空冶炼以及喷射冶金等方法,去除钢中[S]、[P]、[H]、T[O]等杂质和夹杂物,提高钢水纯净度。
(3)钢水升温和控温功能,对钢水实现成分微调。
(4)生产调节功能,均衡炼钢-连铸生产。
为实现上述冶金功能,一般采用以下精炼方法:
(1)渣洗精炼:
精确控制炉渣成分,通过渣钢反应实现对钢水的提纯精炼,主要用于钢水脱氧、脱硫和去除夹杂物等方面。
(2)真空精炼:
在真空条件下实现钢水的提纯精炼,适用于对钢液脱气、脱碳和用碳脱氧等反应过程。
(3)吹氩搅拌:
通过吹氩,加速熔体内传热、传质过程,达到混匀的效果。
(4)喷射冶金:
通过载气将固体颗粒反应物喷入熔池深处,造成熔池的强烈搅拌并增大反应面积。
固体颗粒上浮过程中发生熔化、溶解,完成固-液反应,显著提高精炼效果。
(5)加热与控温:
为了精确控制反应温度与终点钢水温度,炉外精炼设备采用了各种不同的加热功能,避免精炼过程温降。
主要的加热方法有:
电弧加热、化学加热和脱碳二次燃烧加热。
2国内外炉外精炼技术发展特点
钢水炉外精炼最初主要用于少数高级别钢种的脱气处理,如DH、RH等。
上世纪70年代和80年代,VOD、AOD、RH-OB、VD、LF、TN等不同功能炉外精炼新技术纷纷开发成功,炉外精炼开始大量用于普通钢种。
其后经过多年发展,炉外精炼已发展成为满足钢水洁净度要求、对钢水温度和成分进行精确控制并有效协调炼钢与连铸生产组织,对炼钢生产具有非常重要意义的关键工序环节。
当前炉外精炼技术发展呈现以下特点:
(1)炉外精炼比显著提高,高水平钢厂精炼比达到了100%;
(2)真空精炼比显著提高,日本钢铁企业RH精炼比平均在74%以上,宝钢真空精炼比达到75%;
(3)强调高效、经济、快速和根据产品特点选择精炼工艺;
(4)高水平钢厂开始分钢类建立专业化精炼生产线,精炼效率显著提高,成本大幅度降低。
3攀钢炉外精炼技术现状
攀钢通过不断的技术改造,从1993年建设第一座130tLF炉,1997年建成投产第一套130tRH装置,发展到目前拥有4座130tLF炉,具有钢水加热、成分微调、造渣精炼功能,年处理钢水600万吨能力和3套130tRH真空装置,具有钢水脱气、去除夹杂、成分微调功能,年处理钢水400万吨能力的水平,设备装备水平有了大幅度提高。
3.1钢包吹氩精炼
钢包吹氩精炼有包底透气砖吹氩、上部插入喷管吹氩、加盖吹氩等。
钢包吹氩技术是最普通也是最简单的炉外处理工艺,其主要冶金功能是均匀钢水成分、温度、促进夹杂物上浮,目前在国内外已得到广泛应用。
吹氩搅拌精炼主要靠吹入的氩气泡在钢液内部的上浮对钢水进行搅拌,通常钢包吹氩的气体搅拌强度为0.003~0.01Nm3/t·min。
提高钢包吹氩强度,有利于钢水混匀和夹杂物上浮,而吹氩强度过大,会使钢液面裸露,造成钢液二次氧化。
为获得良好精炼效果必须做到:
(1)能够精确控制Ar流量以控制搅拌强度;
(2)严格控制转炉出钢下渣量;(3)对钢包渣进行还原改质,以防止带入的高FeO含量转炉渣对钢水造成的二次氧化。
攀钢在5座炼钢转炉均配置了1套钢包吹氩精炼装置,转炉出钢后的所有钢水都要经过吹氩处理。
吹氩搅拌强度一般为0.002~0.004Nm3/t·min,搅拌时间为6~12分钟。
国外日、德、韩等国钢厂,大量采用钢包吹氩精炼工艺生产低碳铝镇静钢、热轧带钢、特殊钢等优质钢种。
韩国浦项钢铁公司宣称,其LF炉仅在生产[S]含量低于0.002%的超低硫钢种时采用,其它低硫钢种则主要采用钢包吹氩加顶渣工艺。
德国蒂森-克虏伯公司采用上部插人喷管吹氩搅拌加顶渣工艺,可以生产[S]含量低于0.003%的优质热轧钢板。
国内武钢、马钢等钢厂也采用钢包吹氩加顶渣精炼工艺,大量生产优质低碳铝镇静钢和许多低硫、超低硫钢种。
3.2LF炉精炼
LF精炼炉是70年代初由日本开发成功。
由于采用电弧加热,可以多量造新渣,在渣-钢精炼方面较其它精炼方法具有优势,成为最主要的炉外精炼设备。
LF炉的工艺优点包括:
精炼功能强,适宜生产超低硫、超低氧钢;具有电弧加热功能,热效率高,升温幅度大,温度控制精度高;具备搅拌和合金化功能,易于实现成分精度控制,提高产品的稳定性。
LF炉的精炼工艺主要包括:
(1)加热与温度控制:
LF炉采用电弧加热,用埋弧泡沫技术,对钢水加热效率较高,升温速度可达到3~5℃/min,终点温度的控制精度≤±5℃。
(2)白渣精炼工艺:
LF炉利用白渣进行钢水精炼,实现钢水脱硫、脱氧,生产超低硫钢和低氧钢。
因此,白渣精炼是LF炉工艺操作的核心,也是提高钢水纯净度的重要保证。
(3)合金微调与成分精度控制:
合金微调与成分精度控制技术是保证钢材成分性能稳定的关键技术之一,也是LF炉的重要冶金功能。
实现合金微调与成分精度控制的主要措施是①在线建立快速分析设施,保证分析响应时间≤3min;②精确估算钢水重量和合金收得率;③钢水脱氧良好,实现白渣精炼;④计算机在线准确计算各种合金加入量,保证钢水成分的准确性与稳定性。
攀钢目前拥有4座130tLF炉,具有钢水加热、成分微调、造渣精炼功能,年处理钢水600万吨能力。
表3.1列出了攀钢LF炉工艺参数。
表3.1攀钢LF炉工艺参数
序号
项目
参数
1
钢包公称容量,t
130
2
钢包平均处理钢水量,t
131.5
3
变压器额定容量,kVA
20000
4
变压器二次侧电压,V
219~345
5
变压器二次侧额定电流,A
40947
6
平均加热升温速度,℃/min
2.0~4.5
7
电极分布圆直径,mm
780
9
三相功率不平衡系数,%
≤8
10
精炼能力,万吨
150
攀钢把LF炉作为温度调整和低合金钢生产的主要精炼设备。
攀钢低合金钢采用的生产工艺流程为:
铁水预处理-转炉冶炼-LF精炼—钙处理-连铸。
在低合金钢生产工艺流程中,采用出钢过程加入6~10kg/t的高碱度精炼渣、出钢后加入2kg/t的调渣剂,LF工序再次加入2~3kg/t的高碱度精炼渣,并补加0.3~0.6kg/t铝丸的分步调整方法对钢包渣的组成和氧化性进行控制,同时将精炼后的软吹氩时间延长至5min以上。
通过采取以上工艺措施,攀钢低合金钢的控制达到以下水平:
(1)钢中T[O]
铸坯T[O]均小于30×10-6,平均达到14.69×10-6,T[O]的分布情况见图3.1。
图3.1钢中T[O]的分布情况
(2)非金属夹杂物
夹杂分布形态见图3.2。
图3.2夹杂分布形态金相照片
由图3.2看出,夹杂物基本以点球状、弥散地分布在钢中。
(3)钢中[S]
通过采取铁水深脱硫,控制转炉回硫,LF炉精炼脱硫后,使成品硫得到有效控制。
精炼过程的脱硫情况见表3.2。
表3.2LF炉精炼脱硫情况(%)
名称
转炉终点[S]/%
成品[S]/%
脱硫率/%
范围
0.008~0.021
0.005~0.011
25.0~64.3
平均
0.013
0.007
46.2
虽然LF精炼工艺在渣—钢精炼方面较其它精炼方法具有优势,但也存在精炼周期长、渣量大、能耗高等问题。
近年来,国内外高水平钢厂炉外精炼采用LF工艺呈现减少趋势,如韩国浦项钢铁公司和国内宝钢、马钢,只有在生产[S]低于0.002~0.003%的厚板钢种时才采用LF精炼方法,而大量钢种则采用成本较低的钢包吹氩加顶渣或直接采用RH精炼工艺。
3.3RH精炼
RH精炼又称真空循环脱气法。
其基本工艺原理是利用气泡将钢水不断地提升到真空室内进行脱气、脱碳等反应,然后回流到钢包中。
和其它各种真空处理工艺相比,RH技术的优点是:
(1)反应速度快,处理周期短,生产效率高,常与转炉配套使用;
(2)反应效率高,钢水直接在真空室内进行反应,可生产[H]≤0.5×10-6,[C]≤10×10-6的超纯净钢;
(3)可进行吹氧脱碳和二次燃烧进行热补偿,减少处理温降;
(4)可进行喷粉脱硫,生产[S]≤5×10-6的超低硫钢。
为了进一步提高RH的精炼效率,扩大处理能力,近几年国内外RH精炼技术的发展趋势是:
(1)提高真空泵的抽气能力,使RH达到极限真空度(66.7Pa)的抽气时间缩短到2min。
(2)进一步提高钢水的循环流量。
钢水循环流量决定于下降管内径,真空室内钢水深度和吹Ar的气体流量。
扩大RH下降管直径,提高氩气的供气强度以及提高真空室真空度,均有利于提高RH的循环流量。
(3)向RH内吹入纯氧,可以提高RH在高碳低氧区内的脱碳速度,因而有利于提高RH的初始含碳量。
当RH内钢水碳氧比[C]/[O]≤0.66时,RH脱碳速度的限制环节是钢中碳的扩散;当钢水碳氧比[C]/[O]≥0.6时,熔池内氧的传质速度决定了脱碳速度。
攀钢目前拥有3套130tRH真空装置,具有钢水脱气,去除夹杂,成分微调功能,年处理钢水400万吨能力的水平。
表3.3列出了攀钢RH工艺参数。
表3.3攀钢RH工艺参数
序号
项目
参数
1
处理装置型式
双室平移下动式
2
平均钢包容量/t
131.5
3
年处理能力/万t
140
4
平均处理周期/min
24-36
5
钢水循环量/t.min-1
50~70
6
抽真空时间/min
4
7
极限真空度/Pa
30
攀钢把RH作为高速重轨、高级别石油管坯钢生产的主要精炼设备。
攀钢冶炼高级别石油管坯钢的工艺技术路线为:
铁水预处理-转炉冶炼-出钢渣洗-LF炉精炼-RH处理-钙处理-连铸。
通过各工序的控制,攀钢管坯钢的控制达到以下水平:
(1)钢中[S]
通过铁水预处理深脱硫、转炉控制回硫、LF炉精炼脱硫、RH钙处理,成品硫处于较低范围。
全过程精炼脱硫情况见表3.4。
表3.4全过程精炼脱硫情况(%)
名称
转炉终点[S]/%
LF炉精炼[S]/%
RH钙处理[S]/%
范围
0.002~0.006
0.001~0.004
0.001~0.004
平均
0.0041
0.0026
0.0028
(2)钢中[P]
转炉冶炼采用双渣法脱磷,前期炉渣碱度2.6~2.8,终点磷都控制在0.007%以内,最低达到0.004%,脱磷率达到92%以上,出钢前进行渣态调整,减少出钢下渣量,回磷量控制在0.001~0.002%。
(3)钢中[H]
经RH真空处理后,[H]含量控制在1.3×10-6以内,平均1.14×10-6。
(4)T[O]及夹杂控制
钢包渣氧化性随着冶炼工序的变化情况见图3.3。
图3.3钢包渣(FeO+MnO)变化情况
随着精炼的进行,钢包渣的氧化性不断降低,有利于钢中T[O]的降低和[S]的去除,成品圆钢T[O]控制在0.0011%以内,非金属夹杂(A、B、C、D)评级≤1.0级。
近年来,低碳铝镇静钢采用RH“轻处理”是RH用于普通钢种的一种趋势。
该工艺是日本钢铁企业在上世纪80年代开发成功的。
采用传统工艺生产低碳铝镇静钢,转炉炼钢终点钢水[C]要控制至0.04%左右,钢液溶解[O]含量在0.065%左右,此部分溶解[O]在随后精炼过程要通过加入铝进行脱氧,既要消耗大量铝,又增加了去除钢液中夹杂物(脱氧产物Al2O3)难度。
而采用RH“轻处理”工艺,转炉终点钢水[C]含量可提高至0.08~0.10%(对转炉而言,有缩短吹炼时间,降低渣中FeO,减少炉衬侵蚀等好处),相应的钢液溶解[O]含量约为0.02~0.035%左右。
转炉出钢过程不进行铝脱氧,随后利用RH在较低真空度下将[C]脱除至0.04%左右,钢液[O]含量在0.02%以下,然后进行脱氧和去除夹杂物操作,从而可以显著降低脱氧用铝量和非金属夹杂物生成量,既降低了生产成本,又提高了产品质量,目前已为高水平钢厂大量采用。
4存在的主要问题
近几年来,攀钢虽然在炉外精炼工艺技术、新品种开发等方面取得了较大进步,但与国内外先进企业相比还存在相当的差距,主要表现在以下方面:
4.1炉外精炼功能与产品结构优化的要求尚不协调
连铸发展与产品优化的要求是推动炉外精炼技术发展的两个根本原因。
攀钢连铸比已达到100%,但炉外精炼比目前只达到60~70%,LF炉主要用于钢水加热,RH只处理少量的钢种,炉外精炼工序的能力与功能,与国内外先进钢铁企业相比还存在差距。
日本连铸比超过90%以上,精炼比就>80%,现在已几乎为100%。
而真空精炼比1989年就达到54.6%,现已超过74%,有的厂达到80~100%。
宝钢、武钢等RH、VD精炼比达到60~75%。
这从总体上影响了攀钢连铸的水平和高档次产品的质量。
4.2对精炼的功能解析、理解与合理利用还不够深透
对精炼工序与产品选择的关系理解不深,平面布置的位置不合适,影响使用效率。
精炼工艺的系统性、适应性的研究还有差距。
这对企业生产工艺、产品质量的稳定有很大影响。
4.3对炉外精炼技术的经济性认识不够深入
认为炉外精炼只是增加投人、没有效益,还停留在必须用才用的观点。
应该在保证炉外精炼生产线高作业率的条件下,不断降低成本,建立高效、经济的洁净钢生产平台。
4.4精炼相关技术还有待提高
5改进思路
随着炼钢技术的进一步发展,炉外精炼作为最重要的炼钢生产工序,将会得到进一步的发展。
针对攀钢的现状,提出以下改进思路:
5.1进一步提高钢水真空精炼比
随着钢材纯净度的日益提高,要求真空处理的钢种逐渐增多,真空精炼技术的应用将更加普遍,因此,要提高真空精炼装置的作业率,充分发挥生产潜能。
5.2进一步提高炉外精炼工艺技术,实现高效化
目前,转炉和连铸工艺的发展均以高速化为目标。
炉外精炼处在转炉-连铸中间的位置,时间节奏的衔接十分重要,往往成为炼钢生产流程中的“瓶颈”,特别是LF炉工艺,受升温速度的限制,生产节奏已很难适应高效转炉和高速连铸的要求。
因此,要进一步提高炉外精炼技术,重视工艺技术的分解和综合集成的研究,缩短精炼周期,以适应转炉和连铸高效发展的要求,同时只有进一步高效化才能减少温降、物料、能源的消耗,才能降低成本。
5.3重视具有重要功能的吹氩、喂线、合成渣洗精炼技术规范与优化
吹氩、喂线、合成渣洗是具有良好冶金功能的炉外精炼技术,大量用于普通棒线材和一些优质钢种的生产,尤其吹氩和喂线常常与其它各种精炼工艺组合应用。
但攀钢对吹氩、喂线认识不足,操作不规范,计量不够精确,影响了应用和效果。
我们必须从气压、气量控制、透气元件结构优化提高、芯线质量、喂入速度控制等基本工艺优化和规范化入手,切实发挥应有的冶金效果,提高效率、降低消耗,减轻其它精炼方法的冶金负荷,实现整个精炼工艺的最优化。
5.4实现炉外精炼工艺的自动控制
主要内容包括:
准确预报钢水精炼的终点成分与温度,选择最佳的精炼工艺并利用计算机控制精炼过程中吹O2、搅拌、加料、合金调整与钢水加热和温度控制等操作。
5.5重视专线化生产的推广应用
专线化生产是宝钢首先总结提出的一种优化流程模式,武钢等厂也已有实例,这种方式有装备利用率高、工艺稳定、冶金功能充分发挥等一系列优点。
攀钢应重视专线化生产的研究,合理、充分发挥各种精炼设备的生产效能,实现高效化生产。
5.6重视中间包冶金技术的开发
中间包冶金是在炉外精炼基础上的延伸,是保证最终钢水质量的重要环节,应给予更多的关注。
主要包括防止二次氧化的上、下全密封浇注技术;中间包恒温浇铸的保温、加热技术;进一步净化钢水的流场结构优化、提高覆盖剂保温和吸附夹杂物功能;耐火材料优化技术等方面。
参考文献
[1]王雅贞.氧气顶吹转炉炼钢工艺与设备.北京:
冶金工业出版社2003
[2]李士奇.现代电炉炼钢.北京:
冶金工业出版社1995
[3]周剑南.钢铁生产工艺装备新技术.北京:
冶金工业出版社1999
[4]高泽平.炉外精炼.北京:
冶~金工业出版社2005
[5]王永忠.电炉除尘技术.北京:
冶金工业出版社2003
[6]陈家祥.钢铁冶金学.北京:
冶金工业出版社1990
[7]刘根来.炼钢原理与工艺.北京:
冶金工业出版社2004
[8]朱苗永.现代冶金学.北京:
冶金工业出版社2005
目录
第一章总论1
第一节项目背景1
第二节项目概况2
第三节可研报告编制依据及研究范围4
第二章项目建设的必要性6
第三章外部和内部环境分析8
第一节外部环境分析8
第二节xx镇社会经济环境分析11
第三节xx镇发展的机遇与挑战分析14
第四节xx镇发展的优势与劣势分析16
第五节项目风险分析18
第四章建设条件20
第一节项目选址20
第二节场址条件20
第五章发展战略和总体规划22
第一节发展战略目标22
第二节战略实施措施22
第三节规划原则23
第四节总体规划24
第六章基础设施建设内容30
第七章环境保护32
第一节项目场址现状32
第二节项目建设与运营对环境的影响32
第三节环境保护措施33
第四节环境评价结论36
第八章组织机构和项目实施进度37
第一节组织机构37
第二节人力资源配置38
第三节项目实施进度39
第九章投资估算及资金筹措41
第一节投资估算41
第二节投资使用计划与资金筹措45
第十章财务评价47
第一节财务评价基础数据与参数选取47
第二节经营收入估算47
第三节成本费用估算50
第四节财务评价51
第五节财务评价结论55
第十一章社会评价56
第一节项目对社会的影响分析56
第二节项目与所在地互适性分析57
第三节社会评价结论58
第十二章结论与建议59
第一节结论59
第二节建议59