单十字式万向联轴器的加工.docx
《单十字式万向联轴器的加工.docx》由会员分享,可在线阅读,更多相关《单十字式万向联轴器的加工.docx(28页珍藏版)》请在冰豆网上搜索。
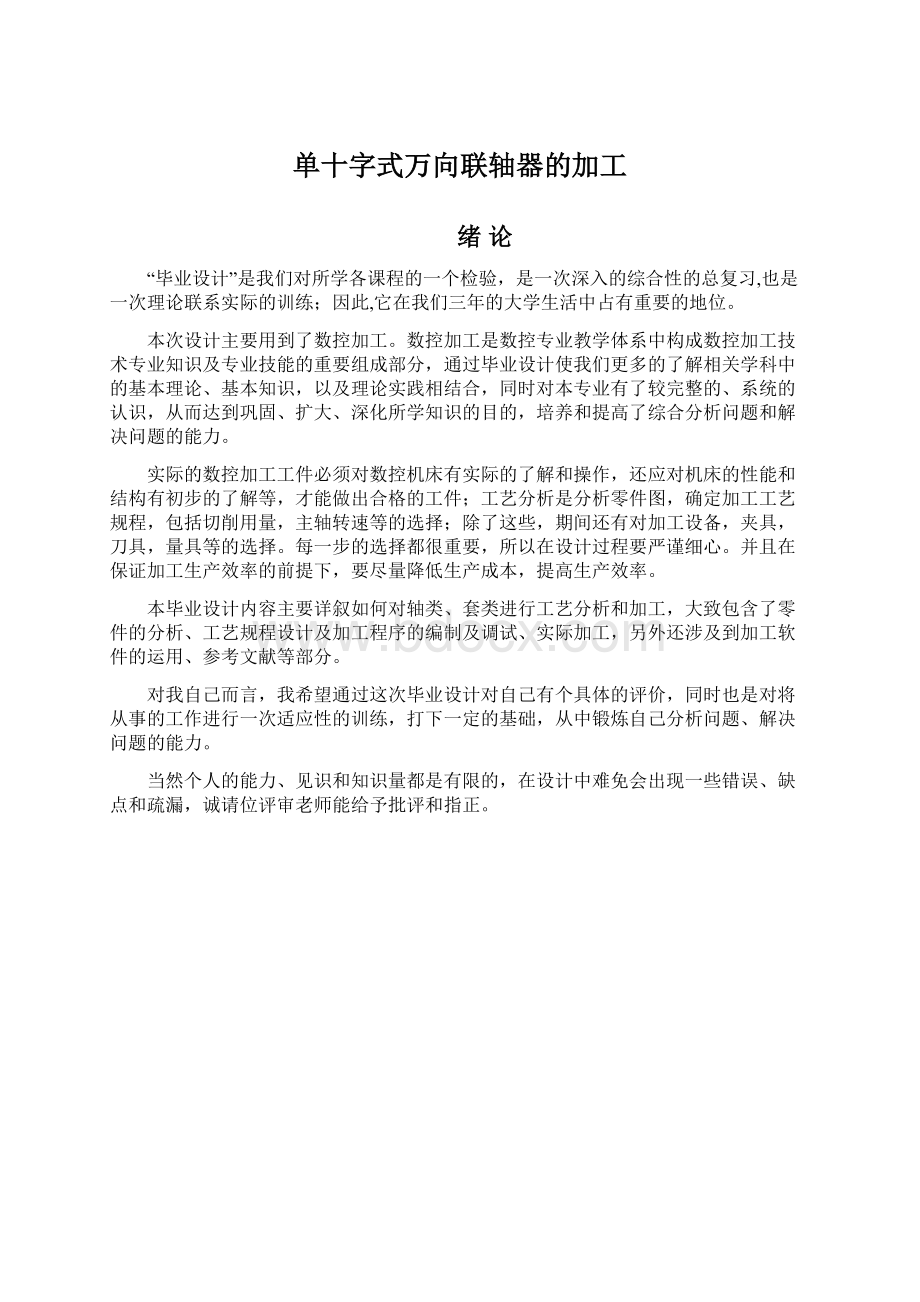
单十字式万向联轴器的加工
绪论
“毕业设计”是我们对所学各课程的一个检验,是一次深入的综合性的总复习,也是一次理论联系实际的训练;因此,它在我们三年的大学生活中占有重要的地位。
本次设计主要用到了数控加工。
数控加工是数控专业教学体系中构成数控加工技术专业知识及专业技能的重要组成部分,通过毕业设计使我们更多的了解相关学科中的基本理论、基本知识,以及理论实践相结合,同时对本专业有了较完整的、系统的认识,从而达到巩固、扩大、深化所学知识的目的,培养和提高了综合分析问题和解决问题的能力。
实际的数控加工工件必须对数控机床有实际的了解和操作,还应对机床的性能和结构有初步的了解等,才能做出合格的工件;工艺分析是分析零件图,确定加工工艺规程,包括切削用量,主轴转速等的选择;除了这些,期间还有对加工设备,夹具,刀具,量具等的选择。
每一步的选择都很重要,所以在设计过程要严谨细心。
并且在保证加工生产效率的前提下,要尽量降低生产成本,提高生产效率。
本毕业设计内容主要详叙如何对轴类、套类进行工艺分析和加工,大致包含了零件的分析、工艺规程设计及加工程序的编制及调试、实际加工,另外还涉及到加工软件的运用、参考文献等部分。
对我自己而言,我希望通过这次毕业设计对自己有个具体的评价,同时也是对将从事的工作进行一次适应性的训练,打下一定的基础,从中锻炼自己分析问题、解决问题的能力。
当然个人的能力、见识和知识量都是有限的,在设计中难免会出现一些错误、缺点和疏漏,诚请位评审老师能给予批评和指正。
第1章单十字式万向联轴器的工艺分析
1.1联轴器的图样分析
图1-1联轴器零件(单叉及套筒)
图1-1联轴器零件(销钉)
如图1-1及附图4所示,单十字式万向联轴器是由单叉(两副),圆柱销,销钉,套筒(两根)十字块构成:
从外形看,销钉,套筒圆柱销机构简单,但单叉结构复杂,工序较多,需要车床,铣床,以及线切割的综合加工。
1.2零件的形状及加工表面的尺寸分析
1.2.1零件的形位公差分析
(1)单叉的形位公差分析
参看附图1,可知单叉的外形设计尺寸为
120mm×85mm,左端要加工圆弧,内孔孔径为
mm,双耳上的孔为
mm,键槽为120mm×12.5mm,公差为0.1。
(2)套筒的形位公差
参看附图2,可知套筒的外形设计尺寸为36
mm,长为20mm、
;倒角1×45°内孔为
mm,长度为10mm;
(3)销钉的形位公差分析
参看附图3,可知销钉有台阶,第一个台阶设计尺寸为83mm×10mm,公差为0.1,
mm,,第二个台阶设计尺寸为
20mm×4mm。
1.2.2零件表面粗糙度的分析
表面粗糙度是保证零件表面微观精度的重要要求,也是合理选择数控机床、刀具及确定切削用量的依据。
从零件图样可知:
单叉内孔直径粗糙度Ra1.6um,其余粗糙度Ra6.3um,见附图1。
1.2.3零件的设计基准
由于该联轴器的零件外形结构,很多部分都需要在数控车床上加工,包括两套单叉的外圆及内孔,所以各零件的中心线就是零件的设计基准。
1.2.4毛坯材料的选择
根据该配合件零件外形形状分析,大多是套类、轴类的零件,所以毛坯一般选择型材(型材是具有一定的几何形状断面的轧制材料,型材按其截面形状分类有圆形、方形、角形、线材以及各种异型等,这些材料按一定的长度切断即可成为零件的毛坯)。
根据教学需要,由于设计加工的是一组教具,所以要求的力学性能较低,切削性能好,轻巧便于携带,而且经济、实用,故材料选择铝合金(LY12)的最为合适。
1.2.5毛坯尺寸及形状选择
选择毛坯形状和尺寸总的要求是:
外形要符合图纸要求,实现少屑或无屑加工,减少机械加工的劳动量。
根据零件图纸设计,在采用数控加工时其加工表面应有较充分的余量,所以选择如下:
(1)单叉毛坯尺寸的选择
单叉毛坯尺寸选
90mm×130mm(两根);
(2)销钉毛坯尺寸的选择
销钉为
25mm×85mm;
(3)套筒毛坯尺寸的选择
套筒为
25mm×40mm(两根)。
1.3设备的选用
对附图1至3的分析,虽然零件结构简单,但加工工序烦琐;零件的加工的外形由孔、边倒角和圆柱几部分组成;但单叉长度达120mm,销钉长度长达83mm且销钉直径相对较小,所以不宜加工,在加工过程中有可能变形。
因此,在加工过程中不仅要合理地选择切削参数,而且在刀具的选择上也要注意。
再者该零件有倒圆角的要求,而且该零件在装夹的时候不同于普通的工件的装夹,单叉必须在车床上把孔以及外形做到位,再采用四轴的加工中心,最后联轴器的两个单叉的键槽还要用到线切割的加工才能将零件完整的加工出来,所以在装夹时要尽量提高装夹精度,以保证在公差范围内。
该零件的材料为LY12,强度和硬度相对于合金钢要差一些,因此切削性能好。
1.3.1选择设备
纵观零件图,联轴器的套筒、销钉以及单叉的部分要在车床上才能加工出来,故选用CK6140卧式数控车床;单叉大部分在铣床上加工,故选用华中四轴加工中心。
1.3.2夹具的选择
数控加工所用的夹具,首先要保证夹具的坐标方向与机床的坐标方向相对固定;其次要能协调零件与机床坐标系的尺寸关系;
根据联轴器零件(圆柱销、销钉、套筒等)的毛坯为铝合金圆形棒料的特点,所以在车床上加工时,以工件一个端面作为定位基准,采用三爪自定心卡盘夹紧工件(夹具如图1-2所示);
图1-2三爪卡盘图1-3平口虎钳
根据工件的特点,单叉以及圆柱销的一部分工序要在铣床上完成,在铣床上加工时,采用平口虎钳装夹,夹持时工件的上表面至少要高出虎钳10mm~15mm,保证加工时的安全性,使刀具不会铣削到虎钳;工件的下面用垫块垫起(如图1-3所示)。
1.4确定加工顺序及走刀路线
整个联轴器零件的加工顺序按照基面先行、先粗后精、先面后孔的原则确定;分析附图可以确定套筒、单叉都是以外圆柱为基准,所以先加工零件的外圆柱部分,再加工零件的内孔部分。
由于单叉的毛坯必须在数控车床上去除,所以加工该零件时先车圆柱的尺寸再钻孔;在车销钉时尽减小径向的力防止小直径的销钉弯曲,由零件图可以分析出套筒与销钉需要配合,所以精度要求较高且要完成配合,而一般钻孔的表面粗糙度Ra值只能达到R6.3~12.5um,所以在加工这几个孔时需要先钻孔,扩孔,最后镗孔,以达到其精度要求。
在数控加工中,刀具相对于运动轨迹的方向称为加工路线。
加工路线的确定首先必须保证被加工表面零件的尺寸精度和表面质量。
其次考虑数值计算简单,走刀路线短,效率高。
为了保证表面质量和提高生产率,切削方式和切削方向应如下确定。
结合分析,单叉的加工方式:
以在数控车床上加工的部分(单叉)做为基准,粗加工时先用立铣刀对单叉并选择跟随周边开粗,精加工时应选择配置文件的方式再用球头刀对单叉进行精加工。
1.5刀具的选择
合理选择数控加工用的刀具是工艺处理工作中的重要内容。
在数控加工中,产品的加工质量和劳动生产率在很大程度上将受到刀具、夹具的制约,虽然大多数刀具、夹具与普通加工中所用相差不大,但实际的具有较高要求的加工必须或需做进一步特殊处理,或者选用适合本次加工的刀具,以满足零件加工的需要。
选刀具时,要使刀具的尺寸与被加工工件的表面尺寸和形状相适应。
在选择数控加工刀具时,还应考虑以下几个方面:
(1)切削性能好;
(2)精度高;
(3)可靠性高;
(4)耐用度高;
(5)切削及排削性能好。
故而根据零件结构特点,车刀选择刀具如下:
表1-1数控加工刀具卡片
产品名称或代号
零件名称
单十字式万向联轴器的加工
零件图号
01
序号
刀具编号
刀具规格名称
数量
加工表面
备注
1
T01
95º外圆车刀
1
粗、精加工销钉、套筒、单叉
2
T02
Φ16立铣刀
1
粗加工单双耳
3
T03
内孔镗刀
1
粗、精加工内孔
4
T04
宽4mm的切槽刀
1
切断
5
T05
A3中心钻
1
打预钻孔
6
T06
Φ30钻头
1
钻孔
7
T07
Φ9.8
1
钻孔
8
8
T08
Φ10立铣刀
1
精铣单叉双耳
7
铣削单叉(即双耳部分)时,受单叉轮廓尺寸的限制,同时考虑硬铝属于一般材料,加工性能较好,所以加工都选用三刃硬质合金立铣刀。
用Ф16的硬质合金立铣刀对单叉双耳粗加工,再选用Ф10的硬质合金立铣刀进精加工见表1-1所示。
1.6切削参数的选择
当进行数控编程时,编程人员必须确定每道工序的切削用量。
并以指令的形式输入程序中。
切削用量包括:
主轴转速,背吃刀量及进给速度等。
对于不同的加工方法需要选用不同的切削用量。
1.6.1主轴转速的确定
主轴转速n(r/min)要根据允许的切削速度Vc(m/min)来确定。
n=1000Vc/πD
公式中:
D—铣刀直径单位(mm)
Vc切削速度单位(m/min)
查“切削用量手册”可知当工件材料为铝合金,铣刀材料为硬质合金钢时Vc=(240~460)m/min。
当D=16时,n=1000Vc/πD=1000×240/3.14×16=4777r/min。
通过上面的计算和考虑机床的性能选定,直径为16mm的立铣刀的转速n=1600r/min。
1.6.2进给速度的确定
进给速度(
)是数控机床切削用量中的重要参数。
主要根据零件的加工精度和表面粗糙度要求以及刀具工件的材料性能选取。
进给速度受机床刚度和进给系统的性能限制。
式中:
z为所选刀具的齿数
n为主轴转速单位(r/min)
为进给量单位(mm/z)
查“切削用量手册”可知当工件材料为铝合金,铣刀材料为硬质合金时
=0.1mm/z;
当z=3,n=1600r/min时,
=3×1600×0.1=480mm/min;
通过上面的计算和实际加工的情况选定,直径为16mm的立铣刀的进给速度
=500mm/min。
1.6.3背吃刀量的确定
为了保证加工表面质量,可留少量精加工余量一般留0.1~0.3mm。
选择零件的切削用量必须根据零件的材料,刀具的材料,机床设备的加工精度等来确定。
下表是加工单叉的工艺卡片:
数控工艺卡片
零件名称
单叉
材料牌号
硬质合金LY12
工序号
1
设备名称
数控铣床
设备编号
文件号
1
零件图号
DC-1
材料硬度
工序名称
粗铣双耳精铣双耳
设备型号
关重工序
第2版
第1页
一、作业准备
1
按《设备操作作业指导书》《设备点检表》要求进行开机。
作业参数
车外圆
主轴转速
1500
进给量
300mm/min
车端面
主轴转速
1600
进给量
200mm/min
2
按照《工装点检表》的要求进行日点检并记录
工艺装备
工艺装备
工艺装备
种类
名称
规格及编号
数量
种类
名称
规格及编号
数量
种类
名称
规格及编号
数量
刀具
立铣刀
16X50X75
1
夹具
三爪卡盘
K11250C/D8
1
辅具
游标卡尺
0—150/0.02
1
立铣刀
16X30X50R3
1
千分尺
25—50
1
立铣刀
10X30X60
1
千分尺
25—50
3
按照《计量器具(设备)点检表》的要求进行日点检并记录。
4
加工首件并按首件三检执行,(当人员、设备工装、材料、工艺、环境变更要进行首件检查)
二、作业过程
作业工步
特性
规范/公差
重要度
评价/测量手段
1
清扫三爪卡盘,确认无异物或碰伤
长度
120mm
游标卡尺0—150/0.02
外径
Ф85mm
游标卡尺0—150/0.02
2
装夹毛坯右端,并使毛坯在转动过程
中无较大抖动,粗铣双耳
宽度
46mm
游标卡尺0—150/0.02
粗糙度
Ra3.2
粗糙度对比块
3
精铣双耳
外径
60mm
游标卡尺0—150/0.02
6
取零件,去毛刺
三作业终:
停机取料,并把工件整齐放入盛具内,不合格品做好标记分类摆放,并作好相关记录。
四反应计划:
对可疑产品作标记分类摆放。
1.7零件的装夹和定位
在机械加工中,必须使机床、夹具、刀具和工件之间保持正确的相互位置,才能加工出合格的零件。
这种正确的相互位置关系,是通过工件在夹具中的定位,夹具在机床上的安装,刀具相对于夹具的调整来实现的。
因此在实际的装夹中零件的夹紧力要合理,防止没有夹紧而甩出或是夹坏已加工表面,定位时要注意刀架和卡盘的相对位置。
第2章单十字式万向联轴器的程序编制
2.1单叉的程序编制
由于单叉零件的特征,需要用到车床和铣床。
2.1.1车床加工部分
首先编制单叉在车床上的程序;由于工件长120mm所以需要掉头加工,首先夹持左端加工右端(如图2-1),当然当单叉外圆柱达到要求时,必须手动打中打中心孔,以便钻内孔到20mm,然后再镗孔。
右端也是如此。
图2-1单叉零件图
程序如下:
(毛料为φ90mm
130mm)
%0062(程序名)
T0101(调用1号刀具、1号刀补,建立工件坐标系)
G00X100Z150(确定起刀点)
M03S800
G00X95Z10
G01X92Z5F100(刀具到循环起点位置)
G71U1R1.5P10Q20X0.4Z0.2F100(粗切循环,粗切量1,精车量X0.4Z0.2)
S1500
N10G01X0F80(精加工起始行,到轴心延长线上)
G01Z0(到端面中心)
X84
X85Z-0.5(倒角0.5)
Z-62
N20X95(精加工程序结束行,退出加工端面)
G00X100
GOOZ150
M30(程序结束并返回起始行)
掉头以已加工的端面为基准加工。
程序如下:
%0063(程序名)
T0101(调用1号刀具、1号刀补,建立工件坐标系)
G00X100Z150(确定起刀点)
M03S800
G00X95Z140
G01X92Z5F100(刀具到循环起点位置)
G71U1R1.5P5Q6X0.4Z0.2F100(粗切循环,粗切量1,精车量X0.4Z0.2)
S1500
N5G01X0F80(精加工起始行,到轴心延长线上)
G01Z120(到端面中心)
X84
X85Z-129.5(倒角0.5)
Z60
N6X95(精加工程序结束行,退出加工端面)
G00X100
GOOZ150
M30(程序结束并返回起始行)
加工内孔的程序,内孔已经钻到20mm:
%0064(程序名)
T0303(调用3号刀具、3号刀补,建立工件坐标系)
G00X15Z150(确定起刀点)
M03S800
G00X10Z10
G01X5Z5F100(刀具到循环起点位置)
G71U1R1.5P5Q6X-0.4Z0.2F100(粗切循环,粗切量1,精车量X0.4Z0.2)
S1500
N5G01X40F80(精加工起始行,到轴心延长线上)
G01Z0(到端面中心)
X45
X46Z-0.5(倒角0.5)
Z-62
N6X5(精加工程序结束行,退出加工端面)
G00Z100
GOOX150
M30(程序结束并返回起始行)
掉头加工内孔,以已加工端面为基准:
%0065(程序名)
T0303(调用3号刀具、3号刀补,建立工件坐标系)
G00X15Z150(确定起刀点)
M03S800
G00X10Z140
G01X5Z125F100(刀具到循环起点位置)
G71U1R1.5P5Q6X-0.4Z0.2F100(粗切循环,粗切量1,精车量X0.4Z0.2)
S1500
N5G01X40F80(精加工起始行,到轴心延长线上)
G01Z120(到端面中心)
X45
X46Z119.5(倒角0.5)
Z60
N6X5(精加工程序结束行,退出加工端面)
G00Z150
GOOX150
M30(程序结束并返回起始行)
2.1.2铣床加工部分的程序编制与调试
由于单叉双耳部分架构复杂,因此采用UG软件自动编程,具体的操作如下:
(1)单叉加工工件坐标系的建立
双击UG4.0,打开已建好的单叉模型,首先在建模状态下画R42.5的圆并拉伸长度为60mm,以便定义工件毛料时使用。
在加工状态下锁定锁定操作导航器,i空白处单击右键插入几何视图双击MCS_MILL坐标,如图2-2,移动坐标到如图所示,并旋转坐标,使XC在长端,在间隙里打上勾,并指定安全平面为100,将装夹偏置改为“1”,如图2-3所示,然后确定。
图2-2坐标系的移动
图2-3安全高度的指定
(2)创建几何体
单击工具栏中的创建几何体按钮,弹出创建几何体对话框(如图2-4),选击工件对话框中的毛坯,选择,弹出毛坯几何体对话框,选择工件的毛坯,单击确定(如图2-5),,即完成了毛料的选择;再单击工件对话框中的部件,选择,弹出工件几何体对话框,选择工件(如图2-6),单击确定即完成了几何体的创建。
图2-4毛坯的选择图2-5毛坯的确定图2-6部件的选择
(3)选择加工方式
创建几何体中已经把加工坐标系,安全平面以及装夹偏置处理完成了,接下来就是选择加工的方式,进入右边的操作导航器,在WORKPIECE右击进入后找到插入,将鼠标指向插入将会弹出一个对话框点击操作就显示如图2-7所示的创建操作对话框。
在如图的类型栏里边找到型腔铣(mill_contour)也就是现在所显示的子类型第一个。
图2-7加工方式的选择
由于部件和毛料在创建几何体时就定义了,所以此时不需要在选择。
将切削方式选择为“跟随工件”,将第一刀的全局深度改为“1”在根据图2-7中所示的进行更改,点击切削层,进去显示如图2-8所示的对话框,将范围深度改为顶层,范围深度为22.5,每一刀的局部深度改为“1”。
值得说明的一点是切削层的作用是控制刀路高低的,设置好以后然后点击确定即可。
图2-8切屑层的设定
(4)创建刀具
单击工具栏中的创建刀具按钮,弹出创建刀具对话框如图2-9所示,单击新建,弹出选择子类型为mill-contour,选择铣削平底刀,取刀具名为D8,单击确定,弹出如图2-10所示的对话框,设置刀具直径为,单击确定。
图2-9刀具的建立图2-10选择刀具种类
如图2-10所示对话框中将刀具名称设置好以后,单击确定,弹出如图2-11所示的一个对话框,将第一项的直径值改为之前设置好的数字“8”单击确定这样开粗要用的刀具就设置好了。
图2-11修改刀具直径
(5)刀路的生成
刀具设置好以后,这时可以将刀路先生成,先看一下是否正确;刀路生成,正确后才开始设置其它相关的参数,单击如图2-12所示把方框中的勾去掉,确定;这时刀路生成,如图2-13所示:
图2-12刀路的生成
将图2-12所示中的“显示参数中的緑色钩全部去掉单击确定这样刀路就完全生成,如图2-13所示:
图2-13刀路显示
认真检查后无误,然后开始设置参数如图2-14:
图2-14设置刀路参数
在如图2-14中,单击方法,把进退刀中的竖直改为5,传送方式为“先前的平面”,确定。
单击切削,修改切削参数,方框中打上勾,把部件侧边余量改为“0.3”如图2-15;单击机床,勾上刀具号、补偿寄存器,并分别输入“1,如图2-16;单击进给率,勾上主轴转速,输入“800”如图2-17;在进给上的第一刀输入“100”,剪切中输入“200”,如图2-18.这些都设置好后,单击确定再次生成刀路。
图2-15余量的留取
图2-16设置刀具寄存器图2-17给定主轴转速图2-18进给的给定
(6)刀路的变换
由于单叉直径大,所以一次性不能做完,还得用到变换,具体操作如下:
右键第一刀生成的刀路,选择对象→变换,如图2-19所示;选择与平面成镜像,即与XY平面做镜像(如图2-20),然后确定→复制→接受→确定,如图2-21所示,当然这些实际的加工是要在四周的铣床上才能做到的,实际的加工是刀具不动,工件旋转一定角度即可,最后是工件的精加工。
图2-19刀路的变化图2-20变换平面
图2-21镜像后的刀路
(7)两个孔的加工
首先是中心钻打预钻孔,其作用是导向和定位;然后扩孔,其余操作和双耳的操作大同小异,也需要变换,所不同的是选择平面铣对孔进行精加工,最终如图2-22。
图2-22铣孔刀路
确定无误后进行2D的仿真,确认无误后借助后处理生出加工刀路,利用在线加工对单叉进行加工。
2.2套筒的程序编制
套筒4共两根,工序有车外形,钻中心孔、钻孔、切断以及铰孔;
程序如下:
(毛料为φ25mm
40mm)
%0065(程序名)
T0101(调用1号刀具、1号刀补,建立工件坐标系)
G00X100Z150(确定起刀点)
M03S800
G00X45Z10
G01X27Z5F100(刀具到循环起点位置)
G71U1R1.5P10Q20X0.4Z0.2F100(粗切循环,粗切量1,精车量X0.4Z0.2)
S1500
N10G01X0F80(精加工起始行,到轴心延长线上)
G01Z0(到端面中心)
X19
X20Z-0.5(倒角0.5)
Z-40
N20X27(精加工程序结束行,退出加工端面)
G00X100
GOOZ150
M30(程序结束并返回起始行)
2.3销钉的程序编制
由于销钉长度长,在加工时必须用到顶尖,防止在销钉的加工是甩动,加工完后切断,倒角,去毛刺,(毛料为φ25mm
90)程序如下:
%0066(程序名)
T0101(调用1号刀具、1号刀补,建立工件坐标系)
G00X100Z150(确定起刀点)
M03S800
G00X27Z10
G01X27Z5F100(刀具到循环起点位置)
G71U1R1.5P10Q20X0.4Z0.2F100(粗切循环,粗切量1,精车量X0.4Z0.2)
S1500
N10G01X8F80(精加工起始行)
G01Z0(到端面中心)
X19
X20Z-0.5(倒角0.5)
Z-83
X19
X20Z-83.5
N20X27(精加工程序结束行,退出加工端面)
G00X100
GOOZ150
M30(程序结束并返回起始行)
第3章单十字式万向联轴器的加工
3.1机床夹具的安装与校正夹具
以数控铣削加工中使用较为广泛的平口钳作为对象,介绍其安装与校正方法。
3.1.1平口钳的安装
在安装平口钳之前,需将机床工作台面、平口钳底面擦拭干净,若一次装安装之后使用时间较长,应将工作台面上放置平口钳的位置及平口钳底面涂上润滑油,以防生锈。
①将平口钳轻放在机床工作台面上,使钳口大致与X轴方向平行。
若只安装一台平口钳,一般将其放在工作台的中间位置;
②将固定螺栓放入相应的位置,轻度旋紧以初步固定平口钳的位置(螺母不能旋得太紧,以方便校正平口钳);
3.1.2平口钳的校正
平口钳的校正即是通过某种方法使平口钳的固定钳口(钳口平面)与机床坐标X轴或Y轴平行(通常将钳口平面与X轴平行),一般采用打表的方法进行校正,所使用的工具是百分表及磁性表座(如图3-1所示)。