地铁门槛毕业设计.docx
《地铁门槛毕业设计.docx》由会员分享,可在线阅读,更多相关《地铁门槛毕业设计.docx(30页珍藏版)》请在冰豆网上搜索。
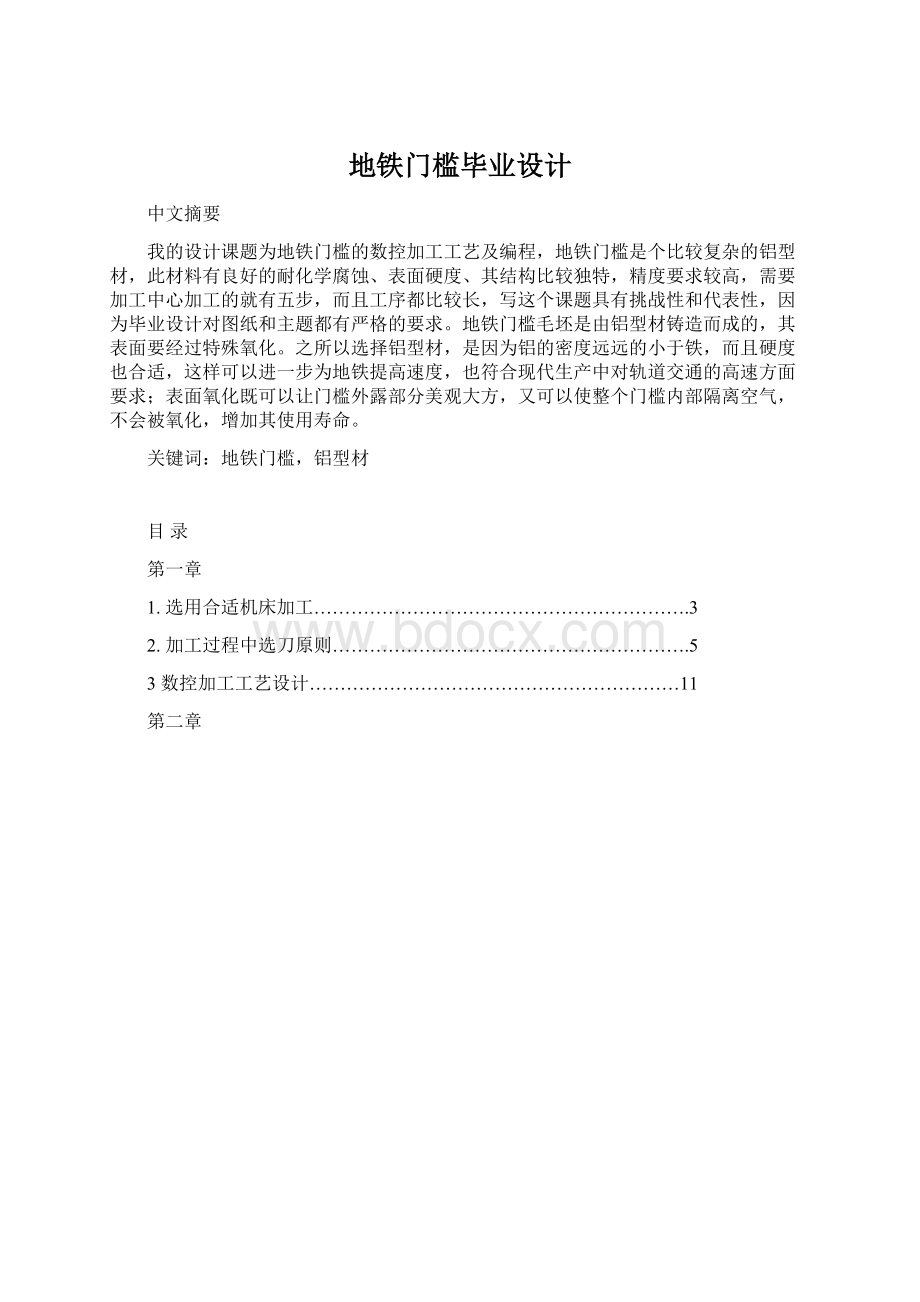
地铁门槛毕业设计
中文摘要
我的设计课题为地铁门槛的数控加工工艺及编程,地铁门槛是个比较复杂的铝型材,此材料有良好的耐化学腐蚀、表面硬度、其结构比较独特,精度要求较高,需要加工中心加工的就有五步,而且工序都比较长,写这个课题具有挑战性和代表性,因为毕业设计对图纸和主题都有严格的要求。
地铁门槛毛坯是由铝型材铸造而成的,其表面要经过特殊氧化。
之所以选择铝型材,是因为铝的密度远远的小于铁,而且硬度也合适,这样可以进一步为地铁提高速度,也符合现代生产中对轨道交通的高速方面要求;表面氧化既可以让门槛外露部分美观大方,又可以使整个门槛内部隔离空气,不会被氧化,增加其使用寿命。
关键词:
地铁门槛,铝型材
目录
第一章
1.选用合适机床加工…………………………………………………….3
2.加工过程中选刀原则………………………………………………….5
3数控加工工艺设计……………………………………………………11
第二章
4.
门槛编程及工艺分析
(一)…………………………………………14
5.
门槛编程及工艺分析
(二)…………………………………………16
6.
门槛编程及工艺分析(三)…………………………………………17
7.
门槛编程及工艺分析(四)…………………………………………19
8.
门槛编程及工艺分析(五)…………………………………………21
第三章
9.总结……………………………………………………………………22
10.参考文献…………………………………………………………………23.
第一章
1.选用合适机床加工
首先,需要了解一下数控机床的加工特点:
数控机床是使用程序来控制机床实现自动加工的,与普通机床相比,数控机床具有以下特点:
①适应性强,高柔性。
数控机床加工零件改变时,只需改变相应的加工程序,不需要新制造或更换工装、调整设备,机床就可以迅速地转换为另一工件界面。
②高效率、高精度。
数控机床具有很高的控制精度和制造精度,另外,数控机床的自动加工方式还可以消除操作者的人为误差,加工的一致性好,质量比较稳定。
尤其在批量加工时,数控加工能够有效减少零件切削时间和辅助工作时问,提高生产效率。
③劳动强度低。
数控机床自动化较高,操作者不需要进行繁重的手工操作,劳动强度明显降低。
④易于建立计算机网络,实现先进的管理模式。
由于数控机床使用的是数字控制,易于实现CAD/CAM一体化,易于实现DNC控制。
⑤自适性差。
数控机床不能像普通机床加工时可以根据加工中出现的实际问题自由地进行人为调整。
另外,数控加工还有技术复杂、加工成本相对高、机床维修和编程技术要求较高等许多不利条件。
其次,数控机床的使用,使用好数控机床是一个综合因素,需要具有工艺员的工艺分析能力,又要有操作者的操作技能。
①工艺方面
(a)合理制定工艺方案。
作为一个合格的工艺员必须了解数控加工的适应性,了解各数控机床的加工特性及加工范围,针对加工对象合理选择数控机床及数控系统。
(b)严谨、细致的工艺文件。
工艺文件是指导工人操作的具体规范,对于数控加工来说,它要求工艺内容十分具体。
在传统加工中,许多具体的工艺问题,如:
工步的划分,走刀路线的确定,刀具、切削用量的选择等在很大程度上都是由操作者根据自己的经验和习惯决定的,无需在工艺中过多的规定。
在数控加工中,这些问题工艺员必须事先设计和安排,做出正确的选择编人工艺文件中。
另外,由于数控机床自适性差,所以,在工艺设计中要考虑全面,注意加工中每一个细节。
因此,一定要有一套严谨的编制思路。
(c)根据产品结构、加工部位、零件材料、刀具等确定合理的切削参数,尽量采用等材料切削,避免加工过程切削速度剧变、去除量不一致的现象。
(d)编程时不仅要考虑加工路线,还要考虑压板、螺钉、夹具等辅具的位置、高度,选择合理的走刀路线,防止碰撞现象。
(e)对加工程序进行试切和验证。
对首次使用的数控程序,应严格执行首件鉴定和程序验证过程,合格才能进行正式产品的批量加工。
(f)不断创新,挖掘数控机床的潜力,提高机床运转率。
与国外制造企业相比,国内的数控机床进给量、切削速度均存在安全系数过大的问题,因此应充分利用数控设备功能,用足用巧数控设备,不断的提高数控机床的工作效率。
拓宽加工范围,确保生产任务饱满。
(g)优化数控工艺,提高生产效率。
通过先进CAD/CAM软件的应用,进一步优化数控工艺,在对工件进行数字化建模和工艺分析基础上,优化走刀轨迹、合理选择刀具,简化和优化数控程序,从而有效地缩短切削时间,提高加工效率。
(h)快速工装的使用。
在数控设备上使用快速工装可以有效地缩短工装准备、工件定位夹紧时间和机床调整时间。
设计快速夹具,采用标准定位法,使工人可以实现快速定位,无须对每个工件进行找正;对于一些小零件,可以在标准定位的基础上,一次装夹多个工件同时加工;采用柔性、模块化夹具,减少夹具数量。
②数控机床的操作方面为了更高的发挥数控机床价值,必须正确地掌握数控机床操作原则。
(a)按机床安全操作规程正确操作机床,对出现的故障及时汇报,并保持好现场。
(b)按工艺及程序的要求加工零件。
(c)加工前应协调零件、刀具、压板等尺寸,避免机床、零件、刀具、辅具之间的干涉、碰撞。
(d)提高操作者的技术素质,减少装刀、找正、对刀、测量等机床的非加工操作、调整时间。
(e)正确地管理刀柄、刀具、工装等辅具,并进行必要的维护和保养,保证辅具的精度。
轨道交通具有快速、运量大、低噪音、舒适安全、节能环保等诸多优点,自问世后便以其特有的优势在各种交通形式中一领风骚,成为世界各国发展城市公共交通系统、解决日益严重的城市交通问题的首选,地铁是一个大城市的命脉,作为轨道交通,地铁的优点很多:
运载量多,安全系数大,快速便捷。
相对于地面交通的频频堵车,日常上下班、出行的人们愈发感受到轨道交通所带来的便利任何事物都有其特点与发展条件,人们掌握后才能加速其发展。
数控机床的发展条件主要包括:
它是机、电、液、气、光多学科各种高科技的综合性组合,特别是以电子、计算机等现代先进技术为基石,必须具有巩固的技术基础,互相配套,缺一不可。
如不齐备,则数控机床难以顺利发展;
数控机床是由主机、各种元部件(功能部件)和数控系统三大部分组成,还需先进的自动化刀具配合,才能实现加工,各个环节在技术上、质量上必须切实过关,确保工作可靠、稳定,才能保数控机床工作的精度、效率和自动化,否则,难以在生产实际中使用;
它是社会需求、科技水平和人员素质三者的结合,缺一不成。
如果人员素质差、科技水平达不到,则难以满足社会需求。
人是一切活动的主体,需要各种精通业务的专家、人才和熟练技术工人,互相配合,共同完成。
否则,数控机床难以顺利发展。
数控机床的操作是一项艰巨的任务,为了适合我国的经济水平,提高教育水平和生产水平是解决数控机床操作的关键。
2.加工过程中选刀原则
地铁门槛车辆采用铝合金材料、模块化的设计制造技术不仅解决了车体结构轻量化的问题,可以顺利提速,而且大大简化了车辆制造工艺,可根据用户的不同要求进行车辆结构的优化组合,缩短了车辆设计、制造周期,具有显著的经济效益.在不同的加工环境中选用不同的立铣刀,所以加工过程中需要合理选择一些立铣刀,这样可以很好的提高数控机床的利用效率,也满足了工件表面光滑度的要求。
以下介绍立铣刀的选用原则。
(1)铣刀的刃齿数立铣刀刃齿一般有2齿、4齿、6齿;6齿用的较少,最近又增加有3齿的。
一般刃齿数愈多,容屑槽减小,心部实体直径增大,刚性更高。
但排屑性渐差,故一般刃齿数少用于粗加工、切槽。
刃齿数多用于半精加工、精加工、切浅槽(图19)。
最近各大刀具公司推出3齿立铣刀,互相展开竞争。
图19不同刃齿数的立铣刀
3齿立铣刀的推出,这是因为
生产效率提高50%
若切削长度一定(L=1000mm),同样的每齿进给量,3齿立铣刀的每齿切削次数减少了,即循环疲劳负荷减少了,寿命当然可高出许多。
(2)刃切削接触次数=1000/2+0.1=5000(次/min)3刃切削接触次数=1000/3+0.1=3333(次/min)在加工斜倾角较大的型面,若转速以5000r/min,f=l000mm/min,切削条件加工:
2刃时,f=1000/2/5000=0.1(mm/min)。
刀刃发生缺损,故需降低每齿进给量。
但若使用了3刃立铣刀,L=1000/3/5000=0.067(m而:
),保证了生产率,又可能不损伤刀刃完成加工。
另外从降低加工表面粗糙度值方面来看,3刃比2刃也要好,若每分钟进给量、转速一定。
理论加工粗糙度高度计算式。
(·为刀尖圆角半径)
理论加工粗糙度高度计算式
(·为刀尖圆角半径)
另外在低速加工时(即机床功能较差,刀具伸出长度较长时),此时,刀具转速若降低为3000r/min,f=0.1mm/min。
2刃时,f=0.1x2xl000=200(mm/min)3刃时,f=Olx3xl000=300(mm/min)3刃生产效率提高1.5倍,保证要求的生产周期。
但3齿较2齿立铣刀在粗加工切槽时,由于同时接触刃齿数量多而较2齿切削阻力大,中心部切屑排出性能也比2齿差,球头立铣刀磨损时,3齿比2齿的中心刃重磨难。
以L3齿的优点与缺点在使用4齿立铣刀中当然更进一步表现出来,一定的每齿进给量4齿生产效率更高,一定的切削长度刀齿寿命更长,一定的每齿进给量表面粗糙度值更低等当然由于同时参与,齿数多切削阻力更大。
球头立铣刀时,4刃立铣刀的中心刃处排屑更难,各大公司亦有4刃立铣刀中心刃设计制造为2刃,设计特殊形状的螺旋槽等来改进。
2.立铣刀的螺旋角立铣刀的螺旋角0=0o时,为直刃立铣刀。
夕尹0c时,为螺旋刃立铣刀。
图20直刃与螺旋刃立铣刀
直刃加工时,切削刃全部同时切人工件,同时离开工件,这样反复作用加工。
易引起振动缺损,加工表面质量不佳。
作用在刀刃上的切削力作用在同一方向上,使刀具弯曲,故壁面加工精度差。
螺旋刃加工切人工件时,刀刃上某点其受力位置随刀具回转而变化。
结构仁难以引起振动,作用在刀刃上的切削力垂直于螺旋角方向,并分解为垂直分力与进给分力,使刀具弯曲的进给分力减小了,故壁面加工精度好。
图21螺旋角大小与受力情况
螺旋角的选择,螺旋角与切削振动、磨损、加工精度有关,一般螺旋角大好。
其理由是螺旋角越大参与切削长度越长、切削力在长切刃L被分散之故(图21)。
但是螺旋角也不是越天越好。
螺旋角大垂直于刀具分力就大,就不适合加工刚性差的工件。
还有切屑排出性也变差了。
碳素钢、合金钢、预硬钢、不锈钢、铸铁、铝合金、纯铜和塑料等加工第1推荐用45。
螺旋角,第2推荐300螺旋角。
钦合金、镍合金、不锈钢等难切削材料和高硬度钢等加工推荐用60。
螺旋角。
图22为螺旋角与立铣刀磨损影响关系及其试验条件。
图22螺旋角与立铣刀磨损被切削材料:
S50C(248HB);使用工具:
拓mm、4刃、硬质合金;切削条件:
30r/min、1600r/min、25m/min、轴向的背吃刀量90mm、6mm;顺铣切削油剂:
化学溶剂20倍水溶液
为对切削振动影响关系及其试验条件。
图24为螺旋角大小对轴向、进给方向加工表面粗糙度、壁面斜倾度影响关系及试验条件。
图24螺旋角大小对表面粗糙度壁面倾斜量影响被切削材料:
S50C(248HB);使用工具:
势6mm、4刃、硬质合金;切削条件:
30m/min、1600r/min、f=004mm/z、f=25mm/min、轴向的背吃刀量9.omm、径向的侧吃刀量O.6mm、顺铣;切削油剂:
化学溶剂20倍水溶液。
图25为螺旋角大小对加工精度影响关系及其试验条件。
由图22、23、24、25可知螺旋角大,加工表面粗糙度、壁面倾斜量、壁面垂直度、刀具磨损、切削振动均有改善。
为进一步减振防振,尚可选用双螺旋角,即不等导程立铣刀(图26)。
图25螺旋角与加工精度(壁面垂直度)
被切削材料:
$50c(248HB);使用工具:
一般用2刃立铣刀≠6mm,SED2060S(螺旋角30~),SEE2060S(螺旋角45~);切削条件:
切削速度F=60m/rain、转速n=3.183r/min、每刃进给量r。
=0.04mm/z、工作台进给量:
255ram/rain、轴向背吃刀量:
9.Omm、侧吃刀量:
O.6mm、顺铣、切削长度=0.2m;湿式切削(水溶性切削液)。
图26不等导程立铣刀
具有多个螺旋角的立铣刀因使产生振动的节拍改变故可防振。
特别在铝合金切削时防振效果明显。
对螺旋角全面归纳,合理选用可参考表4螺旋角选用表。
螺旋角对刀具寿命、加工精度等有较大影响。
3.按粗、精加工对立铣刀分类
以上几种从不同刀具材料、不同的头形精度、不同的刀齿数、不同的螺旋角对立铣刀分类。
都实际联系到了不同的选择可加工出不同的精度,反过来按精度要求可选择以上各参数。
如选刚度高,耐磨性好,适宜高速加工的刀具材料,达到±0.01~±0.005mm的R精度,直径精度高,形状精度高,刀齿数多,螺旋角大的立铣刀,适宜精加工、半精加工。
反之,则用在粗加工。
但这里特别介绍一种高效的粗加工立铣刀亦称苞米铣刀或分屑式立铣刀如图27。
表4
螺旋角
项目
标准螺
旋角300
不等升角
38。
.34。
强螺旋
角45。
超强螺
旋角600
切削力
进给抗力
主切削力
o
◎
◎
◎
背向力
o
◎
◎
表面粗糙度
o
◎
◎
◎
加工精度
波度
o
o
o
壁面垂直度
◎
◎
◎
o
后刀面磨损
o
o
◎
◎
寿命
折损
◎
◎
◎
◎
侧面加工
o
◎
◎
◎
壁面精加工
◎
◎
◎
加工形态
深槽
o
o
o
浅槽
o
◎
◎
孔、沉孔
◎
o
碳素钢/合金钢
179~380HB
◎
◎
◎
o
预硬钢
35—45HRC
o
◎
◎
o
被切削
淬火钢
45~60HRC
o
◎
材料
不锈钢
◎
◎
铸铁
◎
◎
◎
铝合金
◎
◎
纯铜·钢合金
◎
◎
石墨
◎
◎
注:
◎非常好。
良好
螺旋角
前角
节距
外观
20。
细节距
20。
约6。
细节距
30。
特殊形状
30。
细节距
~。
~一_隧
一’■…;q—
图27几种带分屑槽粗加工立铣刀
一(每个刃齿峰位不同)、
带有分屑槽的粗加工立铣刀,由于切屑被碎断,切削力很低,通常切削力比较如下:
可转位刀片立铣刀>通用整体立铣刀>大螺旋角立铣刀>分屑粗加工立铣刀。
这种刀具可以用高速钢、硬质合金等制造,可以加各种涂层。
它通常是4~6槽,螺旋角一般200~30。
,分屑节距有粗有细,还有特殊形状的,前角一般为6。
,为提高粗加工切削效率可选用它。
这种刀具特别适用于工件刚性差(薄壁),不能承受大夹紧力工件的加工,适用于机床刚性差,转数不能高,但想加大背吃刀量提高效率时,也适用铝、铜等材料的高效粗加工。
有AlTiN等涂层的尚可加工难加工材料与高硬度材料。
3.数控加工工艺设计
4.
5.
2.旋转体类零件
常用数控车床或磨床加工j
(1)考虑加工效率:
住车床七加工时,通常加工余量大,必须合理安排粗加工路线,以提高加工效率。
实际编程时,一般不宜采用循环指令(否则,以工作进给速度的空刀行程太大)。
比较好的方法是用粗车尽快去除材料,再精车。
(2)考虑刀尖强度:
图5
数控车床上经常用到低强度刀具加工细小凹槽采用斜向进刀,不易崩刀,图5a则易崩刀。
3.平面轮廓零件常用数控铣床加工。
应注意:
(l)切入与切出方向控制:
图6(a)的径向切入,工件表面留有凹坑;图6(b)切向切入、切出,工件表面光滑。
所以在加工轮廓时要注意从切向切入、切出,才可以保证工件加工出来的表面光滑度。
(2)一次逼近方法选择:
只具有直线和圆弧插补功能的数控机床在加工不规则曲线轮廓时,需要用微小直线段或圆弧段去逼近被加工轮廓(其误差称一次逼近误差),逼近时,应该使工件误差在合格范围,同时程序段的数量少为佳。
可以减少加工时间,提高机床工作效率。
4.立体轮廓零件
(l)考虑工件强度及表面质量:
图7(b),该形状的工件受力后,强度较图7(a)差,图7(c)的表面质量最好。
(2)考虑机床的插补功能:
加工飞机大梁直纹扭曲面时,若加工机床三轴联动,只好用效率低的球头铣刀;若机床为四轴联动,则可以选用效率较高的圆柱铣刀铣削(图8)。
第二章
4.门槛编程及工艺分析
(一)
门槛毛坯截面如下图,长度为1980mm,
门槛毛坯立体图
加工门槛的第一步是1面铣孔槽及缺口,如图1
图1
1.工序准备:
因为门槛大致为三棱柱,所以加工时需要特定的工装即门槛数铣台(两个)。
以便于门槛在加工过程中不会因为受力太大而晃动,导致工件报废或精度不够。
压板四组,用于门槛两端加固作用。
直径为16和8的铣刀数把,最小精度为0.02mm的游标卡尺一个,2米的卷尺一个,
2.工艺分析:
门槛是经过表面氧化的,所以在加工过程中要轻上轻卸,不能大力敲击。
为了保证槽和孔的表面光滑度,在铣削过程中要开切削液,并且要时刻注意不要出现粘刀现象。
在铣孔时应选直径为8的立铣刀,而铣槽时应选择直径为16的立铣刀,主轴转速设为1500转/分,进给为400,这样既可以提高效率,加工出来的工件表面光滑度也会更好。
门槛
(一)调试中要注意点:
门槛数铣台的放置,要把坐标直线拉直,这样做出的孔和槽误差不会太大;工件坐标系位置,用中心棒对刀,转速为400r/min,X轴是门槛的横向中点,Y轴是门槛的最底边,Z设在工件的上表面;压板应该压在工件的两端,且稍留位置,用于确定两端端面的位置;
3.用mastercam编程得:
%
O0000
(门槛1)
N102G0G17G40G49G80G90
N104T2M6
N106G0G90G54X-1611.Y-13.746A0.S1500M3
N108G43H2Z100.
N110Z0.
N112G1Y10.254F400.
N114X-1617.
N116Y4.254
N118X-1843.
N120Y10.254
N122X-1849.
N124Y-13.746
N126G0Z100.
…………………….
…………………
5.门槛编程及工艺分析
(二)
加工门槛的第二步是(在面3)铣中间的七个槽,如图2.
图2
1准备工序:
压板四组,用于门槛两端加固作用。
直径为16和8的铣刀数把,最小精度为0.02mm的游标卡尺一个,2米的卷尺一个,
2.工艺分析:
在加工过程中要轻上轻卸,不能大力敲击。
为了保证槽和孔的表面光滑度,在铣削过程中要开切削液,并且要时刻注意不要出现粘刀现象。
在铣孔时应选直径为12的立铣刀,主轴转速设为1500转/分,进给为400,这样既可以提高效率,加工出来的工件表面光滑度也会更好。
门槛
(二)调试中要注意点:
加工过程中不需要门槛数铣台,但要把门槛坐标直线拉直,这样做出的孔和槽误差不会太大;工件坐标系位置,用中心棒对刀,转速为400r/min,X轴是门槛的左端,Y轴是门槛的最里边,Z设在工件的上表面;压板的压法,要把门槛下端突出的筋插在加工中心工作台的沟槽里,并且与里面靠紧,在其正面两端的2/3处分别压上一块压板,压板一定压紧。
3用mastercam编程得
O0000
(门槛2)
N102G0G17G40G49G80G90
N104T1M6
N106G0G90G54X116.Y8.A0.S1500M3
N108G43H1Z100.112G1Y-21.617F500.
N114Y-141.585Z100.
N110Z0.
N
N116Y-148.5
N118G3X154.R19.
N120G1Y-141.585
N122Y-21.617Z0.
N124Y7.
N126X148.
N128Y-4.
N130X122.
N132Y-10.
N134X148.
N136G0Z100.
…………………………
....................
6.门槛编程与工艺分析(三)
加工门槛的第三步是(在面2)铣两端缺口。
如图3:
图3
1.工序准备:
压板四组,用于门槛两端加固作用。
直径为16和8的铣刀数把,最小精度为0.02mm的游标卡尺一个,2米的卷尺一个,
2.工艺分析:
在加工过程中要轻上轻卸,不能大力敲击。
为了保证槽和孔的表面光滑度,在铣削过程中要开切削液,并且要时刻注意不要出现粘刀现象。
在铣孔时应选直径为12的立铣刀,主轴转速设为1500转/分,进给为400,这样既可以提高效率,加工出来的工件表面光滑度也会更好。
门槛(三)调试中要注意点:
加工过程中需要门槛数铣台,要把门槛坐标直线拉直,这样做出的孔和槽误差不会太大;工件坐标系位置,用中心棒对刀,转速为400r/min,X轴是门槛的横向中点,Y轴是门槛的最底边,Z设在工件的上表面;压板应该压在工件的两端,压板一定压紧。
3用mastercam编程得
%
O0000
(门槛3)
N102G0G17G40G49G80G90
N104T1M6
N106G0G90G54X-10.Y118.A0.S1500M3
N108G43H1Z100.
N110Z-12.
N112G1X13.5F400.
N114G3X23.5Y128.R10.
N116G1Y142.
N118G2X28.5Y147.R5.
N120G1X133.5
N122Y68.
N124G3X143.5Y58.R10.
N126G1X205.
N128Y-10.
N130G0Z100.
N132X-10.Y120.
N134Z-12.
N136G1X13.5
N138G3X21.5Y128.R8.
N140G1Y142.
N142G2X28.5Y149.R7.
N144G1X133.5
N146G2X135.5Y147.R2.
N148G1Y68.
N150G3X143.5Y60.R8.
N152G1X207.
N154Y-10.
N156G0Z100.
N158X-10.Y118.
N160Z-27.
N162G1X13.5
N164G3X23.5Y128.R10.
N166G1Y142.
N168G2X28.5Y147.