赖氨酸可行性研究报告.docx
《赖氨酸可行性研究报告.docx》由会员分享,可在线阅读,更多相关《赖氨酸可行性研究报告.docx(13页珍藏版)》请在冰豆网上搜索。
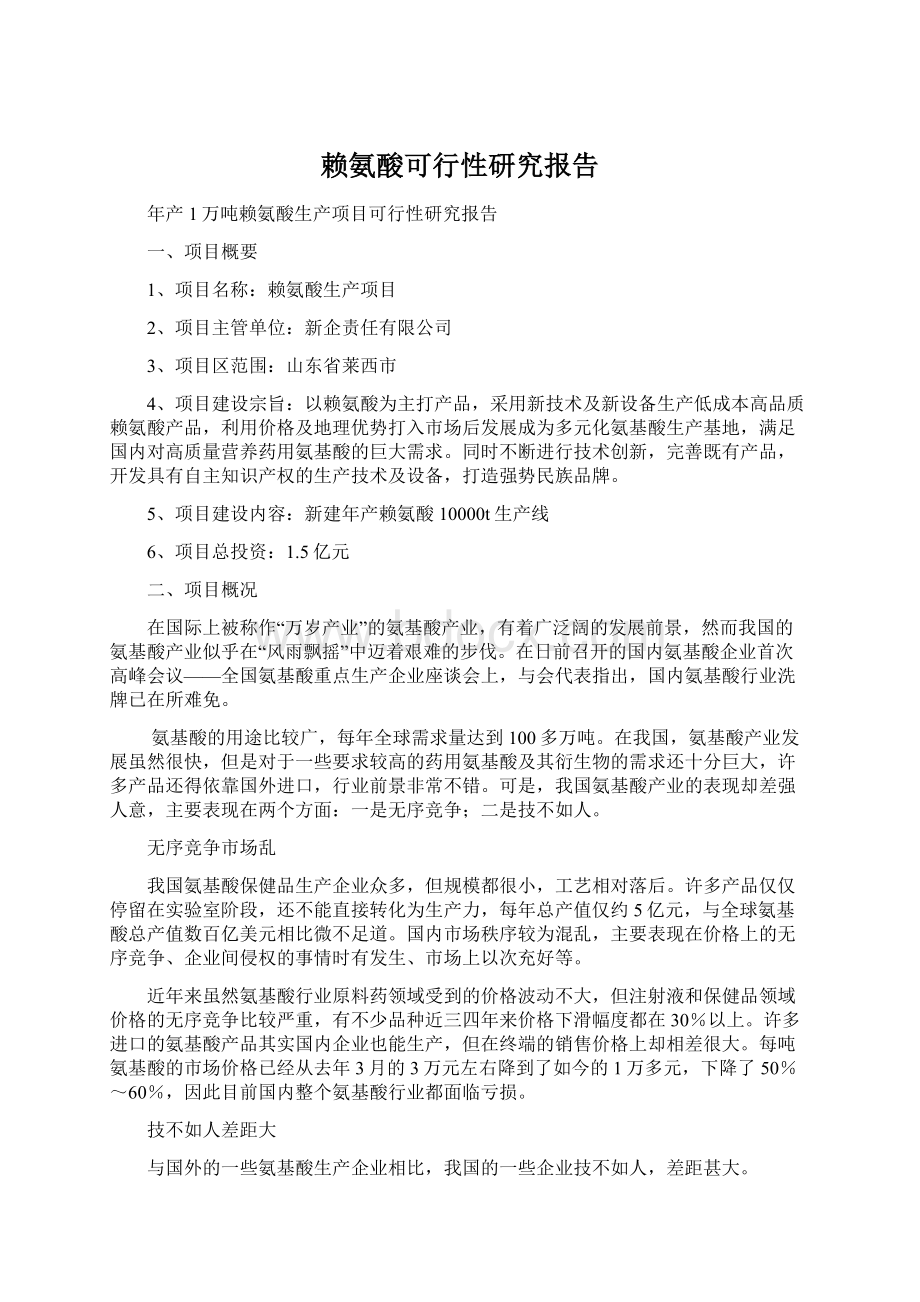
赖氨酸可行性研究报告
年产1万吨赖氨酸生产项目可行性研究报告
一、项目概要
1、项目名称:
赖氨酸生产项目
2、项目主管单位:
新企责任有限公司
3、项目区范围:
山东省莱西市
4、项目建设宗旨:
以赖氨酸为主打产品,采用新技术及新设备生产低成本高品质赖氨酸产品,利用价格及地理优势打入市场后发展成为多元化氨基酸生产基地,满足国内对高质量营养药用氨基酸的巨大需求。
同时不断进行技术创新,完善既有产品,开发具有自主知识产权的生产技术及设备,打造强势民族品牌。
5、项目建设内容:
新建年产赖氨酸10000t生产线
6、项目总投资:
1.5亿元
二、项目概况
在国际上被称作“万岁产业”的氨基酸产业,有着广泛阔的发展前景,然而我国的氨基酸产业似乎在“风雨飘摇”中迈着艰难的步伐。
在日前召开的国内氨基酸企业首次高峰会议——全国氨基酸重点生产企业座谈会上,与会代表指出,国内氨基酸行业洗牌已在所难免。
氨基酸的用途比较广,每年全球需求量达到100多万吨。
在我国,氨基酸产业发展虽然很快,但是对于一些要求较高的药用氨基酸及其衍生物的需求还十分巨大,许多产品还得依靠国外进口,行业前景非常不错。
可是,我国氨基酸产业的表现却差强人意,主要表现在两个方面:
一是无序竞争;二是技不如人。
无序竞争市场乱
我国氨基酸保健品生产企业众多,但规模都很小,工艺相对落后。
许多产品仅仅停留在实验室阶段,还不能直接转化为生产力,每年总产值仅约5亿元,与全球氨基酸总产值数百亿美元相比微不足道。
国内市场秩序较为混乱,主要表现在价格上的无序竞争、企业间侵权的事情时有发生、市场上以次充好等。
近年来虽然氨基酸行业原料药领域受到的价格波动不大,但注射液和保健品领域价格的无序竞争比较严重,有不少品种近三四年来价格下滑幅度都在30%以上。
许多进口的氨基酸产品其实国内企业也能生产,但在终端的销售价格上却相差很大。
每吨氨基酸的市场价格已经从去年3月的3万元左右降到了如今的1万多元,下降了50%~60%,因此目前国内整个氨基酸行业都面临亏损。
技不如人差距大
与国外的一些氨基酸生产企业相比,我国的一些企业技不如人,差距甚大。
由于我国氨基酸行业在技术上面临着较大问题,有些产品只有少部分企业可以生产,而且只能少量生产,即使是我国的氨基酸行业龙头企业技术也无法与跨国企业相比。
比如赖氨酸,目前国外的产品已经达到第三代,而我国还在第一代产品上停滞不前。
况且我国的氨基酸产品多数还仅用作附加值低的饲料,而对纯度要求较高的医药用氨基酸普遍缺乏生产能力。
同时,国产氨基酸原料药的质量不及进口原料药。
日本虽是一个缺乏原料、能源和劳力的国家,却成为了世界上氨基酸生产大国。
他们依赖技术优势,以技术上的领先抵消其他方面的不足。
控制着全球氨基酸市场60%份额的日本味之素公司等已经进入我国市场,在我国设立了10余家企业,目前有10个医药类氨基酸在我国市场上销售。
德国第三大化工企业德固赛集团在进入中国17年后拥有了18家独资或合资企业,每年氨基酸等产品在中国实现的销售收入达到数亿欧元。
而我国仅是依靠能源及较低的生产成本优势,因此难以与日本和德国等氨基酸生产大国竞争。
专家认为,随着环保问题日益受到重视和能源消耗受到控制,我国氨基酸生产企业的生产成本优势将会削弱,前景更加不容乐观。
洗牌难免谋自律
据了解,这次国内氨基酸企业首次高峰会议主题是“扩大共识,公平竞争,加强自律,共谋发展”。
鉴于国内氨基酸企业停产、倒闭与投资、开工轮番上演,不少专家认为,氨基酸行业洗牌难免。
一方面国内氨基酸企业举步维艰,另一方面市场存在很大的成长空间。
因此,在一部分企业面临停产、倒闭的同时,一些精明的投资商却纷纷把目光投向了氨基酸行业。
今年以来,华南地区规模最大的氨基酸生产企业星湖科技投资3.5亿元建成年产3万吨赖氨酸的生产线,苏北最大的氨基酸企业连云港顺德生物工程有限公司亦投资兴建预计年产氨基酸1500吨的生产线。
因此,在风起云涌的投资热潮中,难免有一些规模较小、技术落后的企业在洗牌中出局。
三、项目建设的必要性和可行性
1、氨基酸生产建设的必要性
氨基酸是体内合成蛋白质的基本单元,人体合成蛋白质需要的氨基酸有20种,其中12种氨基酸人体可以利用其他物质合成,另外的8种是必须氨基酸,也就是说这些氨基酸人体不能自身合成,必须从食物中获得。
蛋白质在人体中执行非常重要的功能,比如免疫功能,组成人体的结构物质等。
如果缺乏氨基酸,尤其是缺乏必须氨基酸人体就可能出现不适。
目前,国外非常重视利用氨基酸的营养与生理功能方面的研究。
在产品开发方面,氨基酸保健食品属于人体机能紧急要求时或消化吸收能力降低时必须补充的营养产品,以及肝功能患者的营养补充和应用于降血压的制剂和抗病毒制剂等。
产品形式主要有氨基酸营养输液、运动饮料、能量饮料、美容食品等,具有吸收利用率高和使用方便等优点。
在氨基酸保健食品研发方面,日本和美国处于领先地位。
最近日本企业研发出了一种含有8种必需氨基酸加谷氨酸、脯氨酸、精氨酸、维生素、矿物质配合的粉末食品——氨基酸丝肽。
经食用8周试验后,发现其有改善现代女性睡眠不足,解除疲劳,增强食欲,增强皮肤弹性,增强精力、活力,改善腰痛、肌肉痛、缓和应激等效果。
老年人服用两个月,还能使其血清蛋白值上升,营养改善,肝功能提高,减少皮肤角质剥离。
美国也有很多此类产品面市,在健身房、运动场所用量很大。
有的公司还推出经改进后的新产品“氨基酸生命饮料”,含氨基酸2200毫克,具有提高人体爆发力、高速反应的效果。
该产品在配入亮氨酸、缬氨酸、异亮氨酸、谷氨酸、精氨酸的基础上调制而成。
目前我国已成为全球最大的氨基酸原料药产销国和出口国,基本上所有21种氨基酸原料药国内企业都能生产。
目前国内年产氨基酸总量数百万吨,其中谷氨酸、蛋氨酸和赖氨酸约占全部氨基酸原料药总产量的90%。
与发达国家相比,我国氨基酸下游产品市场深度开发相对滞后。
尤其在具有抗病防病作用的保健型氨基酸产品开发方面与国外差距较大,国内市场上至今很少有这类产品销售,而美国保健型氨基酸产品年销售额高达几亿美元。
我国除医院用氨基酸大输液或少量氨基酸复合胶囊外,在市场上很少看到抗病防病用的保健型氨基酸产品。
业内人士分析,随着生活水平的提高和生活节奏的加快,人们需要从食品中获得更多的氨基酸,氨基酸保健食品满足了这样的市场需求,具有广阔的市场空间。
2、氨基酸生产的可行性
市场需求
1998年末,我国已能生产18种基本氨基酸中的绝大部分品种,目前仅有少数几个品种尚无法自主生产,仍需依赖进口。
统计资料表明,目前我国药用氨基酸生产厂家已达近百家。
全国药用氨基酸总产量已逾4000吨,比20世纪80年代末净增8倍,因此,在一定程度上说,药用氨基酸作为发展中的产业,市场潜力很大,前景十分诱人。
目前,国产氨基酸原料药存在的主要问题是:
国产原料药的质量不及进口原料药:
且价格偏高;我国许多氨基酸研制仅停留在实验室阶段,有的品种只停留在公斤级;由于国内氨基酸工业发展不平衡,部分产品重复投产导致某些氨基酸产品供大于求(其中包括赖氨酸、苏氨酸、亮氨酸、异亮氨酸、胱氨酸和半胱氨酸等)。
氨基酸市场仍以进口产品为主
1999年底世界蛋氨酸的生产能力达到了72万吨,实际产量为48.9万吨,总体供大于求。
从销量来看,诺伟思公司占世界销量的44%,安万特公司占世界销量的24%,迪高沙公司占世界销量的25.6%,曹达公司占世界销量的4.5%。
我国天津蛋氨酸产量不足1%。
按1999年我国饲料生产来看,我国蛋氨酸的市场需求约为4万吨,而只有安万特(天津)公司一家生产,设计生产能力为1万吨,每年产量在4000吨左右。
近期由于环保问题及生产能力提高等需要,该公司正处于停产改造阶段。
由于国内蛋氨酸绝大部分需要靠进口,国内市场价格的起伏主要取决于世界上蛋氨酸生产企业的价格定位。
国内赖氨酸生产企业的生产能力已超过2万吨,目前又有两个企业正在筹建中,如果如期投产,我国赖氨酸的生产能力将超过6万吨。
近期国内饲料市场赖氨酸的需求量稳定在4万吨左右。
由于所赖氨酸进口量达3.2万吨,加之国内1.6万吨左右的生产量,总量已达4.8万吨。
货源充足,以致今年上半年赖氨酸的市场价格比较平稳。
今年下半年,由于世界范围内供大于求,加之国外、国内企业产品价格的竞争,赖氨酸的整体价格会相对平衡。
随着饲料生产形势的好转,国内赖氨酸价格会小幅上扬。
L-苯丙氨酸、L-蛋氨酸及其它氨基酸的生产状况及差距
1.L-苯丙氨酸生产状况及差距
生产厂家有平顶山易元制药公司、浙江稽山企业集团公司、浙江亚美生物化工股份有限公司、中日合资湖北峰江氨基酸有限公司、鹰潭市生物化学制药厂、连云港极美生化食品总公司。
目前我国食品级L-苯丙氨酸的生产能力为1500吨/年,药用级只有100吨/年左右。
而国际上1999年产量为20000吨/年,一般是采用酶法生产技术,产品供不应求,发展有前景。
而国内唯有南京化工大学在江西设点使用酶法生产,生产能力为100吨/年,产品质量符合药用级标准。
至今我国医药行业每年对L-苯丙氨酸需求量为200吨左右,大部分依赖进口。
国内大部分企业都从国外进口关键原料L-苯丙氨酸,并且数量受到限制,开工不足。
由干L-苯丙氨酸是合成甜味剂阿斯巴甜的主要原料,该甜味剂逐步从国外流行到国内,国内生产销售刚进入成长期,需求量逐渐增加,前景看好。
但目前市场竞争的焦点主要在于其生产成本,国内生产成本为10万-12万元/吨,而国际市场销售价为1.0万-1.2万美元/吨,仍有不小差距,今年形势尤为严峻。
2.L-蛋氨酸与其它氨基酸的生产状况及差距
八峰药化股份有限公司采用氨基酸酰化酶技术制取L-蛋氨酸,该技术已获得国家发明专利,该公司准备再投资1.1亿元,将目前100吨/年药用L-蛋氨酸的生产能力扩大到500吨/年。
药用L-色氨酸的生产能力为150吨/年,并且还承担用生物酶法制备L-丝氨酸的科研项目。
由日本味之素公司、上海医药总公司和松江经济技术开发建设总公司共同投资2000万美元,兴建世界上最大的多种药用氨基酸精制厂——上海味之素氨基酸有限公司已于2001年3月峻工投产。
该公司一期工程投入运行后,可生产10种药用氨基酸产品,年产量达830吨,从而改变了长期以来我国药用氨基酸依赖进口的局面。
由上海天厨味精厂与日本协和发酵公司合资组成上海天厨氨基酸公司,其中引进日本全套先进发酵技术,拟生产精氨酸,组氨酸、环丝氨酸等国内奇缺产品,以解决氨基酸工业生产中的“瓶颈”。
届时上海将成为中国最大药用氨基酸工业基地。
由无锡晶石氨基酸公司生产药用异亮氨酸,年产120吨。
山东威海百奥生物工程联合公司生产药用L-丙氨酸、天门冬氨酸,年产500吨。
安徽临泉生化厂生产药用胱氨酸,年产达400吨。
湖北宜昌三峡制药厂生产药用L-缬氨酸,年产360吨。
而目前全世界以1999年为基准L-蛋氨酸产量为57万吨/年,并有逐年扩大趋势,尤其Degussa公司发现蛋氨酸市场需求强劲,预测是推动氨基酸市场发展的主导产品,放加紧新建蛋氨酸工厂,并在下属分公司以现有生产装置进一步扩产,到2005年生产能力将从目前18万吨/年增至38万吨/年。
其最终目的是使其生产成本有利于市场竞争。
另外,L-色氨酸世界消耗量每年约4000吨左右。
绝大部分用于饲料添加剂,特别是用于猪饲料添加剂。
而利用顺酐和富马酸等为原料经化学法生产天门各氨酸转化率仅为85%左右,而采用酶法生产,其转化率可达99%以上,故当今世界大部分用酶法生产氨基酸。
国内生产现状
由于氨基酸的用途比较广,每年全球需求量达到100多万吨。
目前我国的氨基酸产业发展虽然很快,但是对于一些要求较高的药用氨基酸及其衍生物的需求还十分巨大,而我国的氨基酸产业许多还仅仅停留在实验室阶段,还不能直接转化为生产力,因此许多产品还得依靠国外进口,所以行业前景事实上是非常不错的,可以说是“万岁产业”。
我国氨基酸保健品生产企业众多,但规模都很小,每年总产值大概只是5亿元,也没有品牌企业,许多企业都不愿意来投入开发这一市场,因此有着较广阔的发展空间。
我国氨基酸原料药内销加上出口,每年也将超过上百亿元。
要在我国实现每年氨基酸注射液100亿元的销售额并不难。
目前生产氨基酸注射液的企业有20多家,仅八峰药化每年可以做到1亿~2亿元以上销售额。
目前氨基酸注射液的国内年销售额(不算进口)大约是50亿~60亿元,因此还有较大的成长空间。
生产工艺--直接发酵法
直接发酵法发酵法包括一步法和经由二氨基庚二酸的二步法。
通常以废糖蜜,淀粉(或直接用木薯片粉碎至8O目)为原料,采用双酶法,使淀粉先经液化、糖化而转化为葡萄糖,然后再以糖类为发酵原料,日本多采用短杆菌诱发株为菌种,以通用的碳水化合物及其他营养为培养基,经过发酵、过滤、中和、精制、干燥而得成品,必要时进行重结晶。
成品对糖总得率为35%,每吨成品耗糖蜜8吨(或淀粉4.4吨),成本约1万元(折人民币)。
L一赖氨酸的生产工艺与味精(谷氨酸钠)类似,工艺较简单,日本的技术经济指标较先进。
微生物发酵法为生产L一赖氨酸的最主要技术,反应所用碳源为玉米、甘蔗等淀粉质或葡萄糖母液、甘蔗糖蜜等废料,所用高产菌种有BrevibacteriumSP。
PI—B等,在优选菌种配方中含有HPP/KHPO、乙酸钠等组分,在添加2%硫酸铵后可获得高产菌种。
将适宜的配方组分注人500ml的三角烧瓶内于120C加热15min加压灭菌后,在通氧下培养出菌种在高峰期内接人种子培养液在常温常压下发酵,再用膜分离法或化学法分离。
制备L一赖氨酸在14L的发酵器中进行。
通过菌种培养,生长菌体和发酵工艺生产赖氨酸,筛选出的FHI28高产菌株,遗传性能稳定,是一株适合工业化生产的优良菌种,在20ml发酵罐中产L一赖氨酸8.5~9.2%,发酵周期59~67h。
工艺的关键技术在于培养和优选最适宜的菌种,采用不同的原料其结果会大不相同,甚至同一原料也会因原料产地和产出时间的差使结果有很大差别。
国内的发酵法工艺提取率为80%~85%,糖转化率40%一43%,产品收率大于90%。
在发酵和菌种培养中,必须有专人负责,在经过对菌种培养和溶变处理,培养出变异菌种,经筛选和最优化选择出最佳菌种,在培养高峰期加入碳源内,经调整pH后,在发酵期内灭菌处理,在接人种子培养物使其发酵后,按照规定处理方法经分离后得精品L一赖氨酸。
微生物发酵法是利用微生物合成其自身所需的各种氨基酸的能力,通过菌株的溶变等处理,选育出各种营养缺陷型及抗性的变异菌种,以解除代谢调节中的反馈与阻遏,达到过量合成某种氨基酸的一种方法。
发酵法生产赖氨酸通常以淀粉、甘蔗或甜菜制糖后的废糖蜜为原料,其工艺过程为:
淀粉在酸或酶的作用下水解成淀粉糖,假如营养盐调PH值后,进入发酵罐进行灭菌处理,然后接人种子培养物使其发酵,经过微生物发酵后的浓缩液冷冻结晶、离心分离、烘干提纯后即得产品。
四、项目规模、计划销售量、销售方向及设备参数
项目规模、计划销量及销售方向
为满足国内氨基酸的需求,拟建年产赖氨酸10000吨的生产线一条,其他种类氨基酸生产线在后期工程中逐步建设。
销售面向全国各地,因广东、上海、北京地区经济水平相对较高,氨基酸保健品需求量较大,因此销售重点面向该地区。
主要生产设备及参数
设计压力(设备内)0.3MPa(半圆管及加热挡板)0.3MPa
设计温度142。
C主要材料0Cr18Ni9316L321Q235-B
公称容积m3
50
100
200
350
直径DN,mm
3000
3800
4600
5600
直筒高度H,mm
7000
8800
12000
13340
H/DN
2.33
2.32
2.32
2.3
全容积m3
57.5
115
230
402
冷却(加热)F,m2
加热档板半圆管
24(6组)
36(6)组
36(8组)
36(16组)
60
120
240
420(地区有差异)
设计压力(设备内)0.3MPa(半圆管及加热挡板)0.3MPa
设计温度142。
C主要材料0Cr18Ni9316L321Q235-B
功率kw
55,75
75,95
165,180
280,320
转速nr/min
100~190
100~190
100~190
100~150(具体根据工艺而定)
搅拌器直径MM
950-1000
1000-1100
1200-1250
1300-1400
公称容积m3
内筒体直径Dg
筒体高度H
换热面积m2
搅拌轴转速r.p.m
搅拌轴功率kw
10
1800
3800
14
160-200
17-22
15
2000
4800
18
160-200
22-30
20
2200
5000
22
160-200
30-37
30
2400
6600
34
150-200
45-55
40
2600
7500
45
120-200
55-75
50
2800
8000
58
120-200
55-90
60
3000
8300
65
120-250
65-115
75
3200
8800
84
120-240
90-145
100
3600
9400
114
120-220
80-110
150
4200
10800
165
120-200
105-180
200
4600
11500
280
120-200
95-180
300
5200
12300
456
125-180
115-250
500
6800
17000
700
100-180
250-350
800
8000
18500
1000
100-180
400-600
主要优点在于如下几点:
(1)、系列的完整性,功率与转速能适应不同发酵工艺需要,拓宽了工艺选择余地。
必要时加配变频器,可无级调速,以适应发酵过程中菌丝浓度的变化,提高产量。
(2)、加热(冷却)盘管改用罐外半圆管,有利于罐内消毒、清理,当需增加换热面积时,可将原有一般挡板改为加热挡板。
这样加热效果非常直接和有效。
既降低了能耗,又节约了成本。
(3)、采用三分式联轴器,方便密封部件的检修及拆换,缩短维修时间,提高检修质量。
(4)、取消底轴承、中间轴承(或不设中间轴承),以减少污染,延长检修周期。
(5)上、下两层采用不同形式的搅拌器,增设稳定器,可提高搅拌效果,减少对罐体的震荡。
降低轴在运转中所产生的挠度,保证轴的稳定运转。
(6)、改变传动形式,由原来的三角皮带改为立式齿轮传动,体积小,运转平稳。
(7)、有利于操作,不需经常检修,维护方便。
根据生产量计算,每年生产10000t赖氨酸,除去各种辅助时间预计每年进行生产的天数为300天,则每天生产10000/300=33.3t,假设每吨发酵液占用体积为34.68m3,所需反应器总体积为33.3X34.68m3=1156m3。
选用200m3的发酵罐,则所需发酵罐的数目约为六个。
五、原材料及动力供应
常用的原料为甘蔗或甜菜制糖后的废糖蜜、淀粉水解液等廉价糖质原料。
此外,醋酸、乙醇等也是可供选用的原料。
直接发酵法生产赖氨酸的主要微生物有谷氨酸棒状杆菌、黄色短杆菌、乳糖发酵短杆菌的突变株等3种。
这种方法是在50年代后期开发的。
70年代以来,由于育种技术的进展,选育出一些具有多重遗传标记的突变株,使工艺日趋成熟,赖氨酸的产量也得到成倍增长。
工业生产中最高产酸率已提高到每升发酵液100~120g,提取率达到80~90%左右。
山东省玉米作物丰富,可作为提取生产赖氨酸所需淀粉,工业用地价格相对低廉。
赖氨酸生产所需能源主要为电能,可由当地提供,所需的水蒸气也可得到满足。
因此可将生产基地建于山东。
六、经济效益分析
赖氨酸的主要生产成本大约8000~11000元每吨,平均生产每吨赖氨酸所耗玉米淀粉2.1~2.8吨、豆粕500~700公斤,电耗1200度,蒸汽14吨。
全年赖氨酸产量:
10000吨
所需玉米淀粉:
2.8X10000=28000吨
豆粕:
700/1000X10000=7000吨
电耗:
1200X10000=12000000度
蒸汽:
14X10000=140000吨
原料
单价/(元/吨)
年产10000吨价(元)
玉米淀粉
2800
78400000
豆粕
3350
23450000
电耗
0.463元/度
5556000
蒸汽
150
21000000
合计:
128406000
氨基酸参考销售价格如下:
2010年12月1日全国氨基酸价格
品种
含量
规格
产地
价格(元/公斤)
赖氨酸
98.50%
25公斤/件
国产
15-15.3
98.50%
25公斤/件
进口
17.5
65%
25公斤/件
国产
9-9.3
蛋氨酸
99%
25公斤/件
进口
40-41.5
88%
250公斤/桶
进口
34
苏氨酸
99%
25公斤/件
国产
16.5-17.5
99%
25公斤/件
进口
17.5-18.5
色氨酸
99%
25公斤/件
国产
160-165
99%
25公斤/件
进口
200-210
赖氨酸定价为15元/公斤,也即15000元/吨。
则年利润为:
15000X10000—128406000=21594000(元)
假设生产的10000吨赖氨酸全部售出,则总获利2159.4万元/年。
七、副产物及废液处理:
传统的赖氨酸生产工艺,一般是发酵液先酸化后,进入树脂柱中进行离交提取,用氨水进行解析后的赖氨酸(解析液)进行薄膜蒸发浓缩,经结晶分离后精制成品。
赖氨酸发酵液不进行过滤直接上柱提取(混液吸附),即树脂吸附后进行洗涤,含大量的菌体、蛋白、胶体的废水将被洗涤下来形成难以治理的废水。
发酵液放罐后直接经Ultra-flo超滤系统过滤,能使真正收率达到99%以上,滤渣中含有大量的蛋白质及菌丝等营养物质,烘干后作饲料,可进行包装销售。
整个工艺过程除了最终产品赖氨酸和副产品饲料、硫酸铵外,无多余废水排放。
特点:
1)酵液超滤过滤无须任何预处理,节约成本。
菌渣可直接做饲料,完全消除废液污染。
滤液不含蛋白质量高,保证连续离交进料要求。
过滤收率可达98-99%。
2)由于减少了蛋白对树脂的污染,可增加树脂的吸附容量10%以上,并有效延长树脂寿命。
3)减少悬浮物在连续离交树脂罐内的沉积,减少反冲次数,减少树脂破碎。
4)纳滤低成本的预浓缩,降低能耗。
部分无机盐透过纳滤膜,减少产品灰份。
纳滤透析水回用顶洗,闭路循环提高收率减低成本。
(根据实践表明纳滤浓缩平均成本为20元/吨水)
5)纳滤废水处理系统能将硫酸铵废水处理成回用水,并且回收硫酸铵做肥料。
膜系统适应性强,能随时跟上今后用户对处理后的污水排放水质进一步提高的要求。
6)本工艺膜系统运行平稳,维修容易。
膜系统可分性强,可根据料液流量大小随时切换膜的运行数量,其余可进行清洗、保护或更换等操作,故膜系统无传统工艺的每年大修要求,在40℃~45℃左右用低压力大流量对膜进行清洗,只需清洗一小时左右即能使膜通量恢复,而不用拆卸设备,可实现全自动运行与清洗。
7)工艺占地面积大大缩小。
由于膜设备都是由膜元件叠加起来的,使膜设备占地极小。
膜系统为全封闭系统,无物料和气体的泄漏,噪音小,并容易实现全自动化运行。
发酵液放罐后直接经Ultra-flo超滤系统过滤,去除蛋白质、菌