塑胶模设计.docx
《塑胶模设计.docx》由会员分享,可在线阅读,更多相关《塑胶模设计.docx(13页珍藏版)》请在冰豆网上搜索。
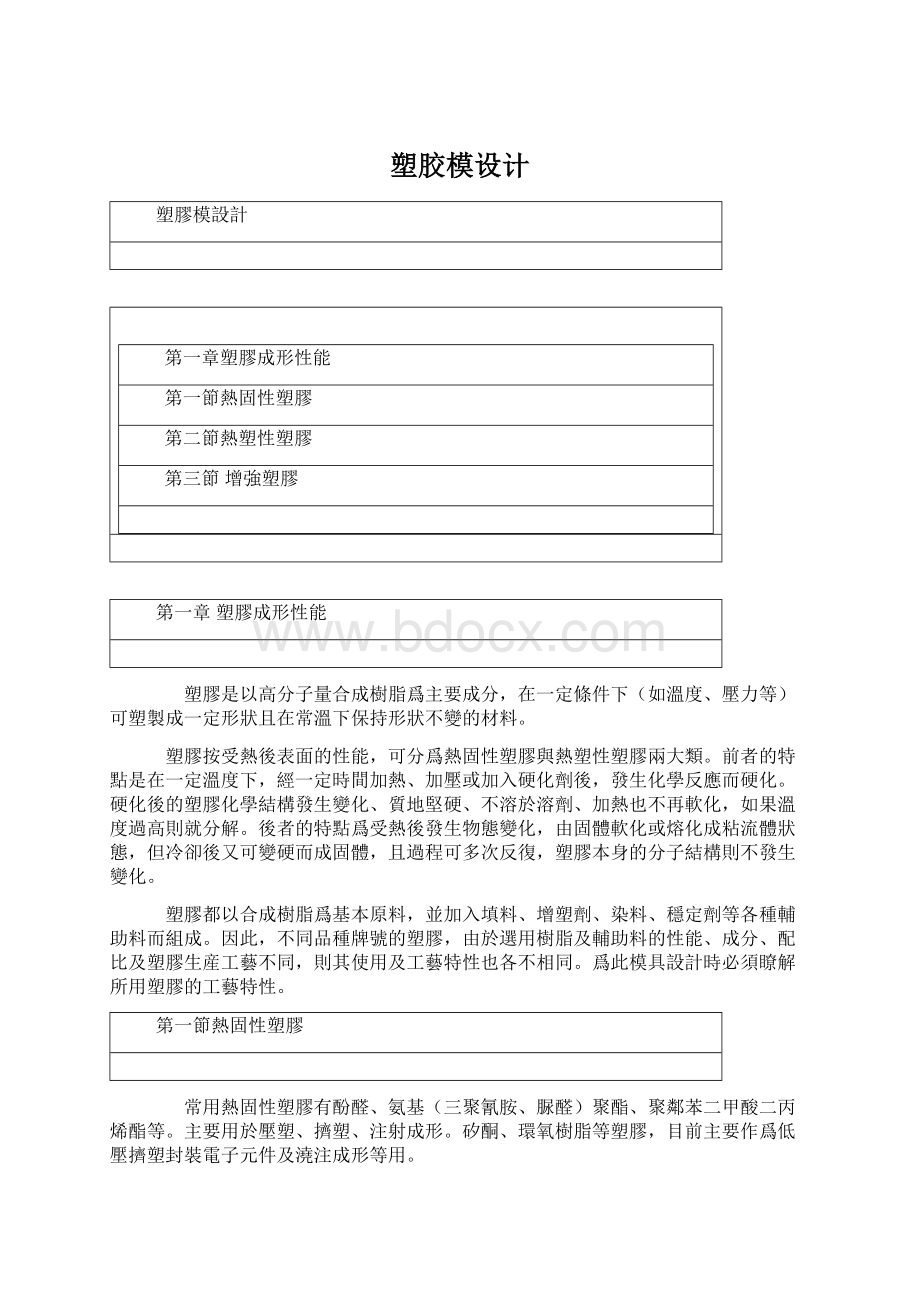
塑胶模设计
塑膠模設計
第一章塑膠成形性能
第一節熱固性塑膠
第二節熱塑性塑膠
第三節增強塑膠
第一章塑膠成形性能
塑膠是以高分子量合成樹脂爲主要成分,在一定條件下(如溫度、壓力等)可塑製成一定形狀且在常溫下保持形狀不變的材料。
塑膠按受熱後表面的性能,可分爲熱固性塑膠與熱塑性塑膠兩大類。
前者的特點是在一定溫度下,經一定時間加熱、加壓或加入硬化劑後,發生化學反應而硬化。
硬化後的塑膠化學結構發生變化、質地堅硬、不溶於溶劑、加熱也不再軟化,如果溫度過高則就分解。
後者的特點爲受熱後發生物態變化,由固體軟化或熔化成粘流體狀態,但冷卻後又可變硬而成固體,且過程可多次反復,塑膠本身的分子結構則不發生變化。
塑膠都以合成樹脂爲基本原料,並加入填料、增塑劑、染料、穩定劑等各種輔助料而組成。
因此,不同品種牌號的塑膠,由於選用樹脂及輔助料的性能、成分、配比及塑膠生産工藝不同,則其使用及工藝特性也各不相同。
爲此模具設計時必須瞭解所用塑膠的工藝特性。
第一節熱固性塑膠
常用熱固性塑膠有酚醛、氨基(三聚氰胺、脲醛)聚酯、聚鄰苯二甲酸二丙烯酯等。
主要用於壓塑、擠塑、注射成形。
矽酮、環氧樹脂等塑膠,目前主要作爲低壓擠塑封裝電子元件及澆注成形等用。
一、工藝特性
(一)收縮率
塑件自模具中取出冷卻到室溫後,發生尺寸收縮這種性能稱爲收縮性。
由於收縮不僅是樹脂本身的熱脹冷縮,而且還與各成形因素有關,所以成形後塑件的收縮應稱爲成形收縮。
1.成形收縮的形式成形收縮主要表現在下列幾方面:
(1)塑件的線尺寸收縮由於熱脹冷縮,塑件脫模時的彈性恢復、塑性變形等原因導致塑件脫模冷卻到室溫後其尺寸縮小,爲此型腔設計時必須考慮予以補償。
(2)收縮方向性成形時分子按方向排列,使塑件呈現各向異性,沿料流方向(即平行方向)則收縮大、強度高,與料流直角方向(即垂直方向)則收縮小、強度低。
另外,成形時由於塑件各部位密度及填料分佈不勻,故使收縮也不勻。
産生收縮差使塑件易發生翹曲、變形、裂紋,尤其在擠塑及注射成形時則方向性更爲明顯。
因此,模具設計時應考慮收縮方向性按塑件形狀、流料方向選取收縮率爲宜。
(3)後收縮塑件成形時,由於受成形壓力、剪切應力、各向異性、密度不勻、填料分佈不勻、模溫不勻、硬化不勻、塑性變形等因素的影響,引起一系列應力的作用,在粘流態時不能全部消失,故塑件在應力狀態下成形時存在殘餘應力。
當脫模後由於應力趨向平衡及貯存條件的影響,使殘餘應力發生變化而使塑件發生再收縮稱爲後收縮。
一般塑件在脫模後10小時內變化最大,24小時後基本定型,但最後穩定要經30~60天。
通常熱塑性塑膠的後收縮比熱固性大,擠塑及注射成形的比壓塑成形的大。
(4)後處理收縮有時塑件按性能及工藝要求,成形後需進行熱處理,處理後也會導致塑件尺寸發生變化。
故模具設計時對高精度塑件則應考慮後收縮及後處理收縮的誤差並予以補償。
2.收縮率計算塑件成形收縮可用收縮率來表示,如公式(1-1)及公式(1-2)所示。
Q實=(a-b)/b×100(1-1)
Q計=(c-b)/b×100(1-2)
式中:
Q實—實際收縮率(%);
Q計—計算收縮率(%);
a—塑件在成形溫度時單向尺寸(毫米);
b—塑件在室溫下單向尺寸(毫米);
c—模具在室溫下單向尺寸(毫米)。
實際收縮率爲表示塑件實際所發生的收縮,因其值與計算收縮相差很小,所以模具設計時以Q計爲設計參數來計算型腔及型芯尺寸。
3.影響收縮率變化的因素在實際成形時不僅不同品種塑膠其收縮率各不相同,而且不同批的同品種塑膠或同一塑件的不同部位其收縮值也經常不同,影響收縮率變化的主要因素有如下幾個方面。
1)塑膠品種各種塑膠都有其各自的收縮範圍,同種類塑膠由於填料、分子量及配比等不同,則其收縮率及各向異性也不同。
(2)塑件特性塑件的形狀、尺寸、壁厚、有無嵌件,嵌件數量及佈局對收縮率大小也有很大影響。
(3)模具結構模具的分型面及加壓方向,澆注系統的形式,佈局及尺寸對收縮率及方向性影響也較大,尤其在擠塑及注射成形時更爲明顯。
(4)成形工藝擠塑、注射成形工藝一般收縮率較大,方向性明顯。
預熱情況、成形溫度、成形壓力、保持時間、填裝料形式及硬化均勻性對收縮率及方向性都有影響。
如上所述模具設計時應根據各種塑膠的說明書中所提供的收縮率範圍,並按塑件形狀、尺寸、壁厚、有無嵌件情況、分型面及加壓成形方向、模具結構及進料口形式尺寸和位置、成形工藝等諸因素綜合地來考慮選取收縮率值。
對擠塑或注射成形時,則常需按塑件各部位的形狀、尺寸、壁厚等特點選取不同的收縮率。
另外,成形收縮還受到各成形因素的影響,但主要決定於塑膠品種、塑件形狀及尺寸。
所以成形時調整各項成形條件也能夠適當地改變塑件的收縮情況。
常用塑膠計算收縮率詳見表1-1。
模具設計時選取收縮率的規則詳見第三章所述。
(二)流動性
塑膠在一定溫度與壓力下填充型腔的能力稱爲流動性。
這是模具設計時必須考慮的一個重要工藝參數。
流動性大易造成溢料過多,填充型腔不密實,塑件組織疏鬆,樹脂、填料分頭聚積,易粘模、脫模及清理困難,硬化過早等弊病。
但流動性小則填充不足,不易成形,成形壓力大。
所以選用塑膠的流動性必須與塑件要求、成形工藝及成形條件相適應。
模具設計時應根據流動性能來考慮澆注系統、分型面及進料方向等等。
熱固性塑膠流動性通常以拉西格流動性(以毫米計)來表示。
數值大則流動性好,每一品種的塑膠通常分三個不同等級的流動性,以供不同塑件及成形工藝選用。
一般塑件面積大、嵌件多、型芯及嵌件細弱,有狹窄深槽及薄壁的複雜形狀對填充不利時,應採用流動性較好的塑膠。
擠塑成形時應選用拉西格流動性150毫米以上的塑膠,注射成形時應用拉西格流動性200毫米以上的塑膠。
爲了保證每批塑膠都有相同的流動性,在實際中常用並批方法來調節,即將同一品種而流動性有差異的塑膠加以配用,使各批塑膠流動性互相補償,以保證塑件質量。
常用塑膠的拉西格流動性值詳見表1-1,但必須指出塑膠的注動性除了決定於塑膠品種外,在填充型腔時還常受各種因素的影響而使塑膠實際填充型腔的能力發生變化。
如粒度細勻(尤其是圓狀粒料),濕度大、含水分及揮發物多,預熱及成形條件適當,模具表面光潔度好,模具結構適當等則都有利於改善流動性。
反之,預熱或成形條件不良、模具結構不良流動阻力大或塑膠貯存期過長、超期、貯存溫度高(尤其對氨基塑膠)等則都會導致塑膠填充型腔時實際的流動性能下降而造成填充不良。
(三)比容及壓縮率
比容爲每一克塑膠所佔有的體積(以釐米3/克計)。
壓縮率爲塑粉與塑件兩者體積或比容之比值(其值恒大於1)。
它們都可被用來確定壓模裝料室的大小。
其數值大即要求裝料室體積要大,同時又說明塑粉內充氣多,排氣困難,成形周期長,生産率低。
比容小則反之,而且有利於壓錠,壓制。
各種塑膠的比容詳見表1-1。
但比容值也常因塑膠的粒度大小及顆粒不均勻度而有誤差。
(四)硬化特性
熱固性塑膠在成形過程中在加熱受壓下轉變成可塑性粘流狀態,隨之流動性增大填充型腔,與此同時發生縮合反應,交聯密度不斷增加,流動性迅速下降,融料逐漸固化。
模具設計時對硬化速度快,保持流動狀態短的料則應注意便於裝料,裝卸嵌件及選擇合理的成形條件和操作等以免過早硬經或硬化不足,導致塑件成形不良。
硬化速度一般可從表1-1的保持時間來分析,它與塑膠品種、壁厚、塑件形狀、模溫有關。
但還受其他因素而變化,尤其與預熱狀態有關,適當的預熱應保持使塑膠能發揮出最大流動性的條件下,儘量提高其硬化速度,一般預熱溫度高,時間長(在允許範圍內)則硬化速度加快,尤其預壓錠坯料經高頻預熱的則硬化速度顯著加快。
另外,成形溫度高、加壓時間長則硬化速度也隨之增加。
因此,硬化速度也可調節預熱或成形條件予以適當控制。
硬化速度還應適合成形方法要求,例注射、擠塑成型時應要求在塑化、填充時化學反應慢、硬化慢,應保持較長時間的流動狀態,但當充滿型腔後在高溫、高壓下應快速硬化。
(五)水分及揮發物含量
各種塑膠中含有不同程度的水分、揮發物含量,過多時流動性增大、易溢料、保持時間長、收縮增大,易發生波紋、翹曲等弊病,影響塑件機電性能。
但當塑膠過於乾燥時也會導致流動性不良成形困難,所以不同塑膠應按要求進行預熱乾燥,對吸濕性強的料,尤其在潮濕季節即使對預熱後的料也應防止再吸濕。
由於各種塑膠中含有不同成分的水分及揮發物,同時在縮合反應時要發生縮合水分,這些成分都需在成形時變成氣體排出模外,有的氣體對模具有腐蝕作用,對人體也有刺激作用。
爲此在模具設計時應對各種塑膠此類特性有所瞭解,並採取相應措施,如預熱、模具鍍鉻,開排氣槽或成形時設排氣工序。
二、成形特性
在模具設計必須掌握所用塑膠的成形特性及成形時的工藝特性。
1.工藝特性常用熱固性塑膠工藝特性見表1-1
2.成形特性常用熱固性塑膠成形特性見表1-2。
各種塑膠成形特性與各塑膠品種有關外,還與所含有填料品種和粒度及顆粒均勻度有關。
細料流動性好,但預熱不易均勻,充入空氣多不易排出、傳熱不良、成形時間長。
粗料塑件不光澤,易發生表面不均勻。
過粗、過細還直接影響比容及壓縮率、模具加料室容積。
顆粒不均勻的則成形性不好、硬化不勻,同時不宜採用容量法加料。
填料品種對成形特性的影響見表1-3
第二節熱塑性塑膠
熱塑性塑膠品種極多,即使同一品種也由於樹脂分子及附加物配比不同而使其使用及工藝特性也有所不同。
另外,爲了改變原有品種的特性,常用共聚、交鏈等各種化學聚合方法在原有的樹脂結構中導入一定百分比量的異種單體或高分子相等樹脂,以改變原有樹脂的結構成爲具有新的使用及工藝特性的改性品種。
例如,ABS即爲在聚苯乙烯分子中導入了丙烯腈、丁二烯等異種單體後成爲改性共聚物,也可稱爲改性聚苯乙烯,具有比聚苯乙烯優越的使用,工藝特性。
由於熱塑性塑膠品種多、性能複雜,即使同一類的塑膠也有僅供注射用或擠出用之分,故本章節主要介紹各種注射用的熱塑性塑膠。
一、工藝特性
(一)收縮率
熱塑性塑膠成形收縮的形式及計算如前所述,影響熱塑性塑膠成形收縮的因素如下
1.塑膠品種熱塑性塑膠成形過程中由於還存在結晶化形起的體積變化,內應力強,凍結在塑件內的殘餘應力大,分子取向性強等因素,因此與熱固性塑膠相比則收縮率較大,收縮率範圍寬、方向性明顯,另外成形後的收縮、退火或調濕處理後的收縮一般也都比熱固性塑膠大。
2.塑件特性成形時融料與型腔表面接觸外層立即冷卻形成低密度的固態外殼。
由於塑膠的導熱性差,使塑件內層緩慢冷卻而形成收縮大的高密度固態層。
所以壁厚、冷卻慢、高密度層厚的則收縮大。
另外,有無嵌件及嵌件佈局、數量都直接影響料流方向,密度分佈及收縮阻力大小等,所以塑件的特性對收縮大小,方向性影響較大。
3.進料口形式、尺寸、分佈這些因素直接影響料流方向、密度分佈、保壓補縮作用及成形時間。
直接進料口、進料口截面大(尤其截面較厚的)則收縮小但方向性大,進料口寬及長度短的則方向性小。
距進料口近的或與料流方向平行的則收縮大。
4.成形條件模具溫度高,融料冷卻慢、密度高、收縮大,尤其對結晶料則因結晶度高,體積變化大,故收縮更大。
模溫分佈與塑件內外冷卻及密度均勻性也有關,直接影響到各部分收縮量大小及方向性。
另外,保持壓力及時間對收縮也影響較大,壓力大、時間長的則收縮小但方向性大。
注射壓力高,融料粘度差小,層間剪切應力小,脫模後彈性回跳大,故收縮也可適量的減小,料溫高、收縮大,但方向性小。
因此在成形時調整模溫、壓力、注射速度及冷卻時間等諸因素也可適當改變塑件收縮情況。
模具設計時根據各種塑膠的收縮範圍,塑件壁厚、形狀,進料口形式尺寸及分佈情況,按經驗確定塑件各部位的收縮率,再來計算型腔尺寸。
對高精度塑件及難以掌握收縮率時,一般宜用如下方法設計模具:
(1)對塑件外徑取較小收縮率,內徑取較大收縮率,以留有試模後修正的餘地。
(2)試模確定澆注系統形式、尺寸及成形條件。
(3)要後處理的塑件經後處理確定尺寸變化情況(測量時必須在脫模後24小時以後)。
(4)按實際收縮情況修正模具。
(5)再試模並可適當地改變工藝條件略微修正收縮值以滿足塑件要求。
(二)流動性
1.熱塑性塑膠流動性大小,一般可從分子量大小、熔融指數、阿基米德螺旋線長度、表現粘度及流動比(流程長度/塑件壁厚)等一系列指數進行分析。
分子量小,分子量分佈寬,分子結構規整性差,熔融指數高、螺旋線長度長、表現粘度小,流動比大的則流動性就好,對同一品名的塑膠必須檢查其說明書判斷其流動性是否適用于注射成形。
按模具設計要求我們大致可將常用塑膠的流動性分爲三類:
(1)流動性好尼龍、聚乙烯、聚苯乙烯、聚丙烯、醋酸纖維素、聚(4)甲基戍烯;
(2)流動性中等改性聚苯乙烯(例ABS·AS)、有機玻璃、聚甲醛、聚氯醚;
(3)流動性差聚碳酸酯、硬聚氯乙烯、聚苯醚、聚碸、聚芳碸、氟塑料。
2.各種塑膠的流動性也因各成形因素而變,主要影響的因素有如下幾點:
(1)溫度料溫高則流動性增大,但不同塑膠也各有差異,聚苯乙烯(尤其耐衝擊型及MI值較高的)、聚丙烯尼龍、有機玻璃、改性聚苯乙烯(例ABS·AS)、聚碳酸酯、醋酸纖維等塑膠的流動性隨溫度變化較大。
對聚乙烯、聚甲醛、則溫度增減對其流動性影響較小。
所以前者在成形時宜調節溫度來控制流動性。
(2)壓力注射壓力增大則融料受剪切作用大,流動性也增大,特別是聚乙烯、聚甲醛較爲敏感,所以成形時宜調節注射壓力來控制流動性。
(3)模具結構澆注系統的形式,尺寸,佈置,冷卻系統設計,融料流動阻力(如型面光潔度,料道截面厚度,型腔形狀,排氣系統)等因素都直接影響到融料在型腔內的實際流動性,凡促使融料降低溫度,增加流動性阻力的則流動性就降低。
模具設計時應根據所用塑膠的流動性,選用合理的結構。
成形時則也可控制料溫,模溫及注射壓力、注射速度等因素來適當地調節填充情況以滿足成形需要。
(三)結晶性
熱塑性塑膠按其冷凝時無出現結晶現象可劃分爲結晶形塑膠與非結晶形(又稱無定形)塑膠兩大類。
所謂結晶現象即爲塑膠由熔融狀態到冷凝時,分子由獨立移動,完全處於無次序狀態,變成分子停止自由運動,按略微固定的位置,並有一個使分子排列成爲正規模型的傾向的一種現象。
作爲判別這兩類塑膠的外觀標準可視塑膠的厚壁塑件的透明性而定,一般結晶性料爲不透明或半透明(如聚甲醛等),無定形料爲透明(如有機玻璃等)。
但也有例外情況,如聚(4)甲基戍烯爲結晶性料卻有高透明性,ABS爲無定形料但卻並不透明。
在模具設計及選擇注射機時應注意對結晶料有下列要求:
(1)料溫上升到成形溫度所需的熱量多,要用塑化能力大的設備。
(2)冷凝時放出熱量大,要充分冷卻。
(3)熔態與固態的比重差大,成形收縮大,易發生縮孔、氣孔。
(4)冷卻快結晶度低,收縮小,透明度高。
結晶度與塑件壁厚有關,壁厚冷卻慢結晶度高,收縮大,物性好。
所以結晶性料應按要求必須控制模溫。
(5)各向異性顯著,內應力大。
脫模後未結晶化的分子有繼續結晶化傾向,處於能量不平衡狀態,易發生變形,翹曲。
(6)結晶熔點範圍窄,易發生未熔粉末注入模具或堵塞進料口。
(四)熱敏性及水敏性
1.熱敏性塑膠系指某些塑膠對熱較爲敏感,在高溫下受熱時間較長或進料口截面過小,剪切作用大時,料溫增高易發生變色、降聚,分解的傾向,具有這種特性的塑膠稱爲熱敏性塑膠。
如硬聚氯乙烯、聚偏氯乙烯、醋酸乙烯共聚物,聚甲醛,聚三氟氯乙烯等。
熱敏性塑膠在分解時産生單體、氣體、固體等副産物,特別是有的分解氣體對人體、設備、模具都有刺激、腐蝕作用或毒性。
因此,模具設計、選擇注射機及成形時都應注意,應選用螺杆式注射機,澆注系統截面宜大,模具和料筒應鍍鉻,不得有死角滯料,必須嚴格控制成形溫度、塑膠中加入穩定劑,減弱熱敏性能。
2.有的塑膠(如聚碳酸酯)即使含有少量水分,但在高溫、高壓下也會發生分解,這種性能稱爲水敏性,對此必須預先加熱乾燥。
(五)應力開裂及熔融破裂
1.有的塑膠對應力敏感,成形時易産生內應力並質脆易裂,塑件在外力作用下或在溶劑作用下即發生開裂現象。
爲此,除了在原料內加入附加劑提高抗裂性外,對原料應注意乾燥,合理的選擇成形條件,以減少內應力和增加抗裂性。
並應選擇合理的塑件形狀,不宜設置嵌件等儘量減少應力集中。
模具設計時應增大脫模斜度,選用合理的進料口及頂出機構,成形時應適當的調節料溫、模溫、注射壓力及冷卻時間,儘量避免塑件過於冷脆時脫模,成形後塑件還宜進行後處理提高抗裂性,消除內應力並禁止與溶劑接觸。
2.當一定融熔指數的聚合物熔體,在恒溫下通過噴嘴孔時其流速超過某值後,熔體表面發生明顯橫向裂紋稱爲熔融破裂,有損塑件外觀及物性。
故在選用熔融指數高的聚合物等,應增大噴嘴、澆道、進料口截面,減少注射速度,提高料溫。
(六)熱性能及冷卻速度
1.各種塑膠有不同比熱、熱傳導率、熱變形溫度等熱性能。
比熱高的塑化時需要熱量大,應選用塑化能力大的注射機。
熱變形溫度高的冷卻時間可短,脫模早,但脫模後要防止冷卻變形。
熱傳導率低的冷卻速度慢(如離子聚合物等冷卻速度極慢)必須充分冷卻,要加強模具冷卻效果。
熱澆道模具適用於比熱低,熱傳導率高的塑膠。
比熱大、熱傳導率低,熱變形溫度低、冷卻速度慢的塑膠則不利於高速成形,必須用適當的注射機及加強模具冷卻。
2.各種塑膠按其品種特性及塑件形狀,要求必須保持適當的冷卻速度。
所以模具必須按成形要求設置加熱和冷卻系統,以保持一定模溫。
當料溫使模溫升高時應予冷卻,以防止塑件脫模後變形,縮短成形周期,降低結晶度。
當塑膠餘熱不足以使模具保持一定溫度時,則模具應設有加熱系統,使模具保持在一定溫度,以控制冷卻速度,保證流動性,改善填充條件或用以控制塑件使其緩慢冷卻,防止厚壁塑件內外冷卻不勻及提高結晶度等。
對流動性好,成形面積大、料溫不勻的則按塑件成形情況有時需加熱或冷卻交替使用或局部加熱與冷卻並用。
爲此模具應設有相應的冷卻或加熱系統。
各種塑膠成形時要求的模溫及熱性能見表1-4及表1-5。
(七)吸濕性
塑膠中因有各種添加劑,使其對水分各有不同的親疏程度,所以塑膠大致可分爲吸濕、粘附水分及不吸水也不易粘附水分的兩種,料中含水量必須控制在允許範圍內,不然在高溫、高壓下水分變成氣體或發生水解作用,使樹脂起泡、流動性下降、外觀及機電性能不良。
所以吸濕性塑膠必須按要求採用適當的加熱方法及規範進行預熱,在使用時還需用紅外線照射以防止再吸濕。
二、成形特性
常用熱塑性塑膠成形特性及成形條件見表1-4及表1-5。
第三節增強塑膠
爲了進一步改善熱固及熱塑性塑膠的機電性能。
常在塑膠中加入玻璃纖維填料(簡稱玻纖),作爲增強材料,以樹脂爲粘結劑而組成新型複合材料,通稱爲增強塑膠(熱固性塑膠的增強塑膠又稱爲玻璃鋼)。
由於塑膠配方的玻璃纖維的品種、長度、含量等不同,其工藝性及使用特性也各不相同。
本節主要介紹模壓用的熱固性增強塑膠及注射用的熱塑性增強塑膠。
一、熱固性增強塑膠
熱固性增強塑膠是以樹脂、增強材料、輔助劑等組成。
其中樹脂作爲粘結劑,它要求有良好的流動性、適宜的固化速度、副産物少,易調節粘度和良好的互溶性,並需滿足塑件及成形要求。
增強材料起骨架作用,其品種規格繁多主要用玻璃纖維,一般含量爲60%、長度爲15~20毫米。
輔助劑包括調節粘度的稀釋劑(用以改進玻纖與樹脂的粘結)、用以調節樹脂-纖維介面狀態的玻纖表面處理劑、用以改進流動性,降低收縮,提高光澤度及耐磨性等用的填料和著色顔料等。
由於選用的樹脂,玻纖的品種規格(長度、直徑,無堿或含堿,支數,股數,加撚或無撚),表面處理劑,玻纖與樹脂混制工藝(預混法或預浸法,塑膠配比等不同則其性能也各不相同。
(一)工藝特性
1.流動性增強料的流動性比一般壓塑膠差,流動性過大時易産生樹脂流失與玻纖分頭聚積。
過小則成形壓力及溫度將顯著提高。
影響流動性的因素很多,要評定某種料的流動性,必須按組成作具體分析。
影響流動性的因素見表1-6。
2.收縮率增強塑膠的收縮率比一般壓塑膠小,它主要由熱收縮及化學結構收縮組成。
影響收縮的因素首先是塑膠品種。
一般酚醛料比環氧、環氧酚醛、不飽和聚酯等料要大,其中不飽和聚酯料收縮最小。
其他影響收縮的因素是塑件形狀及壁厚,厚壁則收縮大,塑膠中所含填料及玻纖量大則收縮小,揮發物含量大則收縮也大,成形壓力大,裝料量大則收縮小,熱脫模比冷脫模的收縮大,固化不足收縮大,當加壓時機及成形溫度適當,固化充分而均勻時則收縮小。
同一塑件其不同部位的收縮也各不相同,尤其對薄壁塑件更爲突出。
一般收縮率爲0~0.3%,而0.1~0.2%的則居多,收縮大小還與模具結構有關,總之選擇收縮時應綜合考慮。
3.壓縮比增強料的比容,壓縮比都較一般壓塑膠大,預混料則更大,因此在模具設計時需取較大的裝料室,同時向模內裝料也較困難,尤其預混料更爲不便,但如採用料坯預成形工藝則壓縮比就可顯著減小。
裝料量一般可預先估算,經試壓後再作調整。
估算裝料量的方法可由如下四種:
(1)計算法裝料量可按公式(1-3)計算:
A=V×G(1+3~5%)(1-3)
式中A——裝料量(克);
V——塑件體積(釐米3);
G——所用塑膠比重(克/釐米3);
3~5%——物料按發物、毛刺等損耗量補償值。
(2)形狀簡化計算法將複雜形狀塑件簡化成由若干個簡單形狀組成,同時將尺寸也相應變更再按簡化形狀進行計算,如圖1-1所示。
(3)比重比較法當按金屬或其他材料的零件仿製塑件時,則可將原零件的材料比重及重量與所選用的增強塑膠比重之比求得裝料量。
(4)注型比較法用樹脂或石蠟等澆注型材料注入模具型腔成形後再以此零件按比重比較法求得裝料量。
4.物料狀態增強料按其玻纖與樹脂混合製成原料的方式可分爲如下三種狀態。
(1)預混料是將長達15~30毫米的玻纖與樹脂混合烘乾而成,它比容大,流動性比預浸料好,成形時纖維易受損傷,質量均勻性差,裝料困難,勞動條件差。
適用於壓制中小型、複雜形狀塑膠及大量生産時,不宜用於壓制要求高強度的塑件。
使用預混料時要防止料“結”使流動性迅速下降。
該料互溶性不良,樹脂與玻纖易分頭聚積。
(2)預浸料是將整束玻纖浸入樹脂,烘乾切短而成。
它流動性比預混料差,料束間相溶性差,比容小,玻纖強度損失小,物料質量均勻性良好,裝模時易按塑件形狀受力狀態進行合理輔料,適用於壓制形狀複雜的高強度塑膠。
(3)浸氈料是將切短的纖維均勻地鋪在玻璃布上浸漬樹脂而成的氈狀料,其性能介於上述兩者之間。
適用壓制形狀簡單,厚度變化不大的薄壁大型塑件。
5.硬化速度及貯存性增強塑膠按其硬化速度可分爲快速和慢速兩種。
快速料固化快,裝料模溫高,爲適用於壓塑小型塑件及大量生産時常用原料。
慢速料適用於壓制大型塑件,形狀複雜或有特殊性能要求及小批量生産時,慢速料必須慎重選擇升溫速度,過快易發生內應力,硬化不勻,填充不良。
過慢則降低生産效率。
所以模具設計時應預先瞭解所用料的要求。
各種料都有其允許貯存期及貯存條件。
凡超期或貯存條件不良者都會導致塑膠變質,影響流動性及塑件質量,故試模及生産時都應注意。
(二)成形條件
熱固性增強塑膠的成形條件見表1-7。
(三)塑件及模具設計注意事項
1.塑件設計時應注意下列事項。
(1)塑件光潔度可達7~9,精度一般宜取3~5級,但沿壓制方向精度不易保證,宜取自由公差。
(2)不易脫模,宜取較大脫模斜度。
若不允許取較大脫模斜度時,則塑件徑向公差宜取大。
(3)塑件宜取回轉體對稱外形,不宜過高。
(4)壁應厚而均勻,避免尖角、缺口、窄槽等形