新型陶瓷材料缩.docx
《新型陶瓷材料缩.docx》由会员分享,可在线阅读,更多相关《新型陶瓷材料缩.docx(14页珍藏版)》请在冰豆网上搜索。
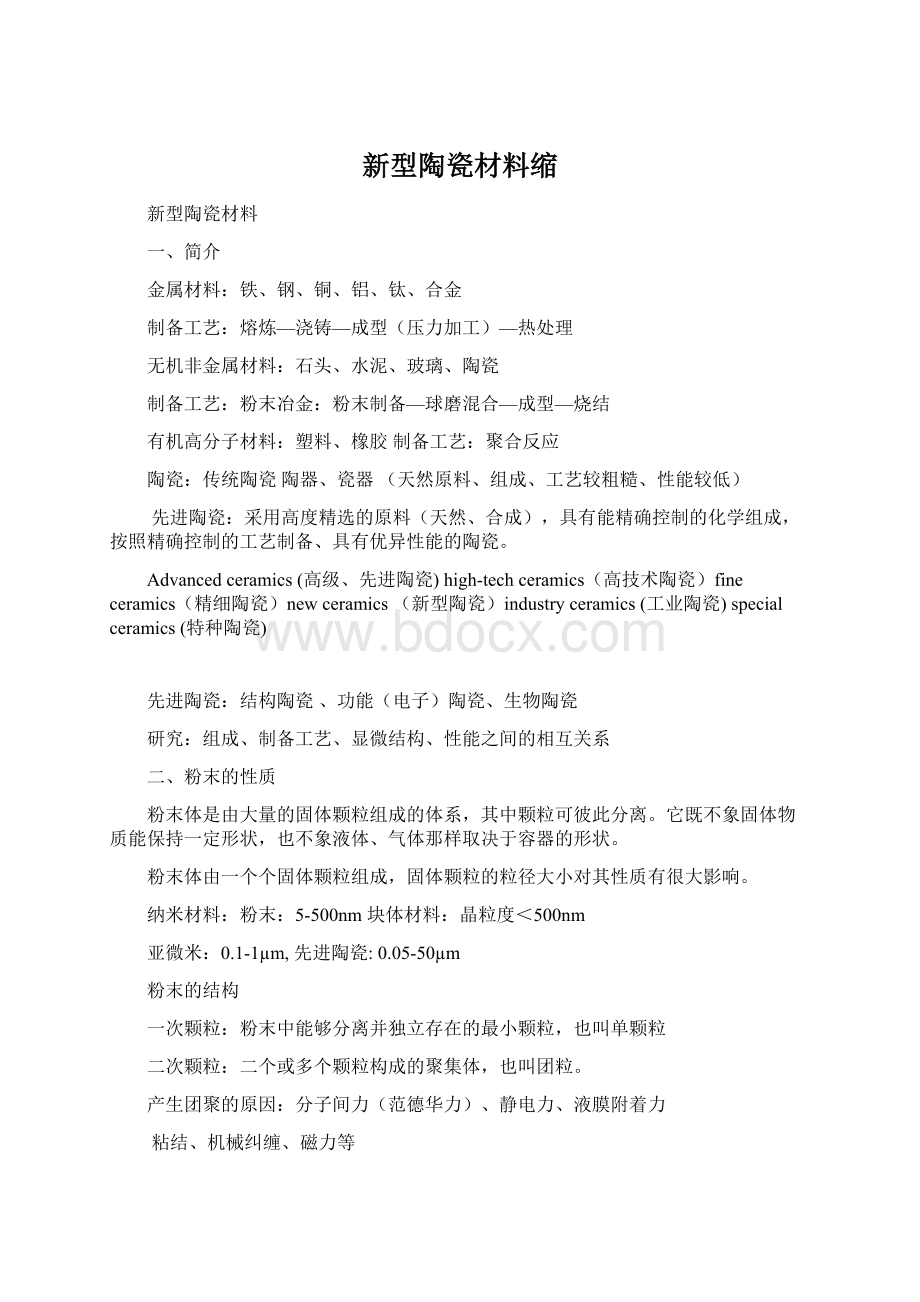
新型陶瓷材料缩
新型陶瓷材料
一、简介
金属材料:
铁、钢、铜、铝、钛、合金
制备工艺:
熔炼—浇铸—成型(压力加工)—热处理
无机非金属材料:
石头、水泥、玻璃、陶瓷
制备工艺:
粉末冶金:
粉末制备—球磨混合—成型—烧结
有机高分子材料:
塑料、橡胶制备工艺:
聚合反应
陶瓷:
传统陶瓷陶器、瓷器(天然原料、组成、工艺较粗糙、性能较低)
先进陶瓷:
采用高度精选的原料(天然、合成),具有能精确控制的化学组成,按照精确控制的工艺制备、具有优异性能的陶瓷。
Advancedceramics(高级、先进陶瓷)high-techceramics(高技术陶瓷)fineceramics(精细陶瓷)newceramics(新型陶瓷)industryceramics(工业陶瓷)specialceramics(特种陶瓷)
先进陶瓷:
结构陶瓷、功能(电子)陶瓷、生物陶瓷
研究:
组成、制备工艺、显微结构、性能之间的相互关系
二、粉末的性质
粉末体是由大量的固体颗粒组成的体系,其中颗粒可彼此分离。
它既不象固体物质能保持一定形状,也不象液体、气体那样取决于容器的形状。
粉末体由一个个固体颗粒组成,固体颗粒的粒径大小对其性质有很大影响。
纳米材料:
粉末:
5-500nm块体材料:
晶粒度<500nm
亚微米:
0.1-1µm,先进陶瓷:
0.05-50µm
粉末的结构
一次颗粒:
粉末中能够分离并独立存在的最小颗粒,也叫单颗粒
二次颗粒:
二个或多个颗粒构成的聚集体,也叫团粒。
产生团聚的原因:
分子间力(范德华力)、静电力、液膜附着力
粘结、机械纠缠、磁力等
硬团聚、软团聚
粉末的形状:
球状、片状、树枝状、柱状、不规则状等
粉末体的粒度与粒度分布
单个粉末颗粒的大小称为粒度。
由于实际上不存在同一粒度的粉末,实际粉末体所含颗粒的粒度大都有一个分布范围,按一定的粒度范围可将粉末分成很多级,各级粉末的百分含量就叫粉末的粒度分布,通常粉末的粒度是指粉末的平均粒度。
粉末粒度的测定
筛分析法:
目数或网目数是一英寸长度内的筛孔数m=25.4/(a+d)a:
网孔尺寸d:
丝径
泰勒标准筛:
100目0.147mm200目0.074mm400目0.038mm
显微镜分析法:
分散、观测、统计分析(图象仪)
费歇尔粒度测量法:
原理:
空气通过粉末粉末试样后,产生压力降,其大小与试样厚度、孔隙度及粉末形状有关。
测试时,控制试样厚度、孔隙度,粉末越细,空气透过时的阻力越大,产生的压力降越大。
d∝(F/(P-F))1/2
d:
:
粉末平均粒度
P:
空气通过粉末试样前的压力,F:
空气通过粉末粉末试样后产生的压力降;
氮吸附法:
根据粉末表面吸附氮气的量,来计算出粉末的比表面值。
粉末越细,比表面积越大,吸附的氮气越多。
费歇尔粒度反映的是粉末的外比表面,代表单颗粒和二次颗粒的粒度,如果与氮吸附法(反映外表面和一次颗粒的大小)联合使用,就能判断粉末聚集程度和二次颗粒的数量。
粉末的表面特性
粉末的比表面积:
单位重量粉末的表面积(平方米/克)。
粉末越细,比表面积越大。
粉末颗粒的表面能
物体内部的原子在周围原子的均等作用下处于能量平衡的状态,而表面原子则只是一侧受到内部原子的引力,另一侧则处于一种“过剩能量”的状态。
这种“过剩能量”就称为表面能。
粉末颗粒表面的“过剩能量”就称为粉末颗粒的表面能。
当物体被粉碎成细小颗粒时,会增加大量的新表面,并且新表面的量值随粒度变小而迅速增加,粉末越细,其表面能则越大。
粉末的工艺性质:
粉末的松装密度:
粉末自由松装时,单位体积的质量叫做粉末的松装密度。
粉末的流动性:
50克粉末从标准的流速漏斗流出所要的时间,单位为秒/50克。
粉末的压制性:
压紧性:
在一定压力下粉末的压缩程度,可用压缩比a表示a=h松/h压=d压/d松
h松:
粉末松装高度h压:
压块高度d松:
粉末松装密度d压:
压块密度
成形性:
粉末压制后,压块保持一定形状的能力。
三、粉末的制备
粉末的制备一般有二种方法:
机械法和合成法
机械法是利用外力的机械作用,将物料粉碎为化学成分基本不变的方法,在制粉过程中只发生物理变化。
如:
球磨、振动球磨、锤式破碎、喷雾法和气流粉碎等。
一般很难制备1微米以下的细粉,
气流粉碎:
喷射气流粉碎机(气流磨)能粉碎到亚微米级(0.1-0.5微米),粉末在高速喷射气流中互相碰撞进行粉碎。
合成法是通过化学反应将物料变成化学成分与原料不同的粉末的方法。
通常包括:
固相法、液相法和气相法。
合成法比机械法更通用,因为它可利用廉价的氧化物盐类作为原料,成本低,制备的粉末纯度高,粒度细,均匀性好。
许多难熔金属和化合物粉末只能用合成法生产。
固相法制备粉末
化合反应法
BaCO3+TiO2→BaTiO2+CO2(1100-1150C)(钛酸钡)
Al2O3+MgO→MgAl2O4(尖晶石)
3Al2O3+2SiO2→3Al2O3`SiO2(莫来石)
热分解反应
H2WO4→WO3+H2O
还原法
SIO2+C→SiC+CO
SIO2+C+N2→Si3N4+CO
液相法制备粉末
(1)沉淀法:
直接沉淀法Na2WO4(l)+CaCl2(l)→CaWO4(↓)+NaCl(l)
共沉淀法:
在混合的金属盐溶液中添加沉淀剂,可得到各种成分混合均匀的沉淀,然后进行热分解。
与固相法相比,能制得化学均匀性好且易烧结的粉料。
BaCl2和TiCl4的混合水溶液中,滴入草酸可沉淀出原子尺度混合的BaTiO(C2O4)24H2O
经热分解后,可得到具有化学计量组成且烧结性能良好的BaTiO3粉末。
溶胶—凝胶法(Sol-gel)
(2)溶剂蒸发法
喷雾干燥法:
将溶液分散成小液滴喷入热风中,使之迅速干燥的方法。
喷雾干燥是一种广泛使用造粒方法。
喷雾热解法:
将金属盐溶液喷入高温气氛中,立即引起溶剂的蒸发和金属盐的热分解,从而直接合成出粉料。
偏钨酸氨水溶液→WO3+NH3+H2O(喷雾热解)
气相法制备粉末
物理气相沉积(PVD)和化学气相沉积(CVD)
物理气相沉积:
蒸发---凝聚,将原料加热至高温(电弧或离子流加热)使之气化,再冷却凝聚成细小粉末颗粒,整个过程中系统中不发生化学反应。
可制备纳米粉末(5-100nm)
化学气相沉积是挥发性金属化合物的蒸气通过化学反应合成所需物质的方法。
气相化学反应可分为二类,一类为单一化合物的热分解A(g)→B(s)+C(g)CH3SiCl3→SiC+HCL
另一类为二种以上化合物之间的气相反应A(g)+B(g)→C(s)+D(g)TiCl4+CH4→TiC+HCl
从气相析出的固体有下列几种形态:
在固体表面形成薄膜、晶须和晶粒、在气体中现成粉末颗粒。
气相中,颗粒的生成包括形成核和核生长二个过程,为了获得颗粒,首先要在气相中形成很多核,为此,必须达到高的过饱和度。
而在固体表面上生长薄膜,并不希望在气相中形成颗粒,因此要在低的过饱和度条件下进行。
四、球磨及混合料的制备
球磨是机械法制备粉末的基本方法。
有二个作用:
一是将粉末进一步磨细,二是将二种以上不同的粉末充分混合均匀。
球磨分干磨(不加入液体介质)和湿磨(加入液体介质)
湿磨介质:
主要作用是使粉末团粒分散,有利于混合均匀,另外它有可能被吸附在粉末颗粒的缺陷处,使粉末颗粒的强度降低,从而有利于破碎。
效率高于干磨。
不与物料发生化学反应,易挥发去除,表面张力小,不使粉末结团、安全等。
酒精、丙酮、水等
滚动球磨原理:
球磨机由一筒和球组成,其工作原理是:
当筒体转动时,装在筒内的研磨体(球)和被研磨体(物料)在摩擦力和离心力的作用下随筒体旋转至一高度,然后自动落下,对筒内物料产生冲击和磨削作用而将物料磨碎。
此外,球的搅拌作用还将物料混合均匀。
球磨筒转速:
转速太低,球发生滑动状态,球磨和混合效率低;转速高于某一速度时(临界转速)时,球在离心力的作用下,一直紧贴筒壁不能自由跌落,此时物料既不被搅拌,也不被破碎,球磨和混合效率极低。
当转速较高且低于临界转速时,球在离心力的作用下,形成抛落式并发生滚动研磨,此时既有翻动作用,也有球体与物料间的相互摩擦作用(磨碎作用),球磨和混合效率较高。
临界转速计算:
mg=mv2/rv=3.14dn
n临界=42.4/d1/2(d:
球磨筒直径:
米n:
转速转/分)
一般实际转速为临界转速的70-90%
装球量:
装球体积约为磨筒容积的40-50%
充填系数:
装球体积与磨筒容积之比
装料量:
球料比2:
1—10:
1(球料比越大,研磨效率越高,但生产效率越低)
液固比(毫升/公斤)WC-Co200-500毫升/公斤
实验室:
刚盖过固相面。
时间:
时间长,混合更均匀,粒度变细(一般球磨极限:
1微米,增加时间,不会更细)
通常:
12-96小时
球磨料的制备:
1)配料及湿磨
湿磨介质通常为酒精,若不怕氧化,也可用蒸馏水。
2)干燥:
使湿磨介质从浆中蒸发出来。
(800-120度)
电烘箱或蒸汽干燥柜,真空干燥箱。
冷冻干燥
3)过筛:
目的是除去料浆干燥时可能发生的结块,并使混合料松散,易于散热。
60-120目筛(振动筛)
混合料的制备:
在球磨料中加入成形剂,干燥制粒后成混合料,供压制成形用。
成形剂:
传统的陶瓷生产一般不需要加成形剂,因为坯料中含有一定的可塑性粘土成分,只要加入一定量的水,经过一定的工艺处理,就会具有良好的成形性能。
先进陶瓷几乎都采用化工原料,没有可塑成形性,因此要加入成形剂,使其具有良好的成形性能。
成形剂的选择原则:
1有较好的粘性,以保证压块有一定的强度;2有一定的润滑性能,以减少粉末压制过程中的内外摩擦力,保证压块密度均匀;3熔点较低,最好在常温下为液态,或能溶解于易挥发溶剂中,以便与物料混合均匀;4工艺性能好,可明显改善物料的塑性,便于挤压和机械加工6蒸发温度低,在低温烧结阶段易被排除,否则会明显增碳;7纯度高,不含其它杂质。
常用的成形剂:
石腊、合成橡胶、聚乙烯醇(PVA)、聚乙二醇(PEG)、甘油等
加入方法:
石腊、合成橡胶汽油溶液(加入到球磨料中),干燥,过筛
PEG水溶液(用水球磨时加入),干燥,过筛。
制粒:
使物料成为具有一定尺寸和适当流动性的团粒。
制粒可使物料具有较高和教稳定的松装密度,使其流动性提高,并能充满压模模腔,保证用容量法称料的压块单重一致。
制粒方法:
滚动制粒、喷雾制粒。
滚动制粒:
将物料置于滚筒中,以教慢的速度转动。
物料在筒中沿筒壁不断滚动,使粒子不断趋于球形,另一方面细粒子沾附在大粒子上,使后者长大。
滚筒直径:
150-300毫米,容积15-25升,转速30转/分,装料量15-40公斤,
制粒时间5-20分
喷雾制粒:
将物料与塑化成形剂混合好(一般用水)形成料浆,料浆通过喷嘴向上喷出雾化,由于料浆表面张力的作用,便形成了球状的细小液滴,其与向下流动的热氮气流接触,使液滴中的液体迅速蒸发,干燥而变成颗粒。
适用与工业化生产。
五、成形
压制原理
压制过程:
在压模中填装粉末,再在压力机下加压(0.5-10t/cm2),脱模后即可得到所需形状和尺寸的压坯。
压制全过程:
可粗约分为三个阶段:
第一阶段:
压块密度随压力增加而迅速增大,这是因为粉末的拱桥现象在不大的压力作用下迅速消除,粉末颗粒移动距离较大,使空隙急剧减少。
第二阶段:
压块密度缓慢增加。
由于大量空隙已在第一阶段消除,继续增大压力的结果主要是使颗粒发生弹性变形。
在这个阶段,粉末颗粒移动距离很小,甚至只在颗粒大小的范围内滑动或转动。
第三阶段:
压力的增加可能达到粉末材料的屈服极限和强度极限,粉末颗粒在此压力下产生朔性变形或脆性断裂。
变形方向或断裂碎块填入空隙,从而使压块密度增加。
对于朔性粉末来说,第二阶段不明显,它迅速由第一阶段过渡到第三阶段,但对陶瓷粉末,第二阶段相当明显,而且压制过程一般只能进行到这个阶段的初期
金属粉末压力:
2-10t/cm2,陶瓷粉末:
0.5-2t/cm2
侧压力:
模压成形时,在压制压力的作用下,粉末对模壁产生的压力叫侧压力,一般为正压力的1/3-1/4。
压制过程的压力分布:
模压成形时,由于粉末颗粒间的相互摩擦和粉末颗粒与模壁间的摩擦,使得施加于冲头上的压力(压制压力)并不按帕斯卡原理进行传递,因此压坯各点上所受到的压力是不相同的。
一般来说,离压头越远的地方所受到的压力越小,这种压力损失叫压力降。
粉末颗粒越细,形状越复杂,离加压冲头越远,压力降也越大。
加压方式:
单向加压、双向加压
压坯密度分布:
与压力分别相似。
由于粉末颗粒与模壁间的摩擦损失对压坯中心部分的影响较小,因此加压面的密度形成四周大,中间小;另外,纵向看,离加压冲头越远,压力降也越大,密度也就越小。
压块强度的本质:
对于一般粉末冶金模压成形的压块来说,压块强度是由颗粒间的机械啮合和原子间力共同作用的结果,成形剂的粘合作用也十分重要。
压块强度随成形剂用量的增加而提高,渗腊压坯可以进行机械加工。
压块强度与压制压力的关系:
压块强度随成形压力的增加而提高,与压块密度随压力增加而提高的情况相似。
这是由于空隙度下降,粉末接触表面增加的缘故。
当压力足够大时,更高的压力已不能提高压块强度,相反由于粉末体的局部加工硬化和应力集中,会导致压块出现裂纹和分层。
压块的弹性后效
弹性内应力:
在压块的粉末颗粒内部和颗粒间的接触表面上,会产生一个与粉末颗粒受力方向相反,并力求阻止粉末颗粒变形,以便达到与压制压力平衡的作用力,这个力就称为弹性内应力。
弹性后效:
在去除压制压力和将压块脱模后,由于弹性内应力的松弛作用而引起压块体积膨胀的现象,称为弹性后效。
脱模瞬间是弹性后效最显著的时刻,也是压块最容易出现裂纹和分层的时刻。
压制工艺:
压模设计的基本参数
压缩比:
粉末松装高度与压坯高度之比(2.5-4)
线收缩系数:
压坯尺寸与烧结坯相应尺寸之比K(1.15-1.3)
线收缩率:
(压坯尺寸-烧结坯相应尺寸)/压坯尺寸
单位压制压力:
0.5-2吨/平方厘米(陶瓷材料)
压模内腔尺寸的确定
1.压模内腔直径D=KD1D1烧结坯尺寸
压制工艺:
1.单重的计算
W=VdkW:
压坯单重V:
烧结致密后的体积d:
烧结致密体密度k损失系数:
1.02-1.05
2.压坯高度的控制:
H=hK(烧结致密后的高度,K:
线收缩系数)
压力控制,限高器控制
压制废品
分层、裂纹、未压好
其它成形方法
模压成形只能生产形状较简单、高度尺寸较小的产品。
其它成形方法
冷等静压成形
利用高压液体的静压力直接作用于装在弹性模具内的物料,使压块在各个方向同时均匀受压的一种成形方法。
液体介质可以是水、油,弹性模具材料应选用弹性好、抗油性好的橡胶或塑料。
(压力范围:
500-3000公斤/平方厘米)
特点:
1使用范围广,可生产一般方法不能生产的形状复杂、大件及细长的产品。
2成形质量高,可少用或不用成形剂,生坯密度高且均匀、烧结收缩小、不易变形。
生坯可直接进行机加工,可批量生产。
3模具制造方便而且成本低。
4生产效率较低,生坯精度和光洁度教差、往往要辅以机加工。
冷等静压工艺:
弹性模具制造—粉末装模密封—装入冷等静压机—加压—卸压脱模
粉末装模:
应尽可能均匀一致,反复捣打、振动装模可使粉末分布均匀,装好料的模具,为防止液体介质流入模腔,装料端应密封,一般用塑料塞子塞住,并用金属丝扎紧。
注射成形:
在一定温度下,将增塑处理的混合料浆通过压力注入到模腔中,料浆在模腔中冷却成形,然后脱模,取出坯体。
其特点是可制备复杂形状制品。
挤压成形、注浆成形、热压铸成形、流延成形
脱成形剂(脱蜡)
烧结前,将成形剂完全排出,否则,余下的成形剂在后来的烧结过程中会转变成炭,不利于烧结致密化。
脱除方法:
真空脱蜡、氢气脱蜡:
在真空或氢气气氛中加热,使石蜡气化随真空抽出或随氢气一起燃烧掉。
设备:
真空脱蜡炉、氢气脱蜡炉
工艺:
缓慢升温(2~5度/分钟),450度/1~10小时然后520~550度/1-5小时。
烧结
烧结过程:
将粉末生坯加热到一定温度,并保持一定时间,然后冷却,从而得到所需要的微观结构和性能的材料或制品,这种特殊的热处理工艺叫烧结。
通过高温下物质的传递,烧结使得从压坯中粉末颗粒间的机械结合变成晶粒间的化学键结合,晶粒长大,空隙和晶界减少,体积收缩,密度增加,最后成为坚固的具有的多晶烧结体,其强度比压坯的强度要大的多。
烧结的驱动力:
粉末的表面能降低。
与块状物体相比,粉末体处于能量不稳定状态。
任何系统都有向最低能量状态发展的趋势。
因此,粉末体的过剩表面能就成为烧结的动力。
烧结是一个不可逆过程,烧结后,系统将转变成为热力学更稳定的状态。
粉末体的表面能一般小于5000J/mol,与化学反应过程可达几到几十万J/mol相比,这个烧结推动力不大,因此在常温下烧结不能自动进行,必须对粉末体加高稳,才能使之转变成烧结体。
烧结过程中物质的传递
1蒸发和凝结、2扩散、3粘滞流动和塑性流动、4溶解和析出
液相烧结机理:
物质通过液相传递,效率高于固相和气相。
(1)颗粒重排,液相充填空隙
(2)溶解-析出
(3)晶粒长大,液相冷却后通常留在晶界。
热压、气压烧结、热等静压
先进结构陶瓷
氮化硅陶瓷密度3.2硬度90HRA,韧性5-7
α氮化硅β氮化硅(更稳定,因为α氮化硅的内部应变更大)
六方晶系α氮化硅小于1400度高于1400度α→β
a7.75a7.61
c5.62c2.91
粉末制备:
硅粉氮化:
Si+N2→Si3N4(1400C)
SiO2还原氮化SiO2+c+N2→Si3N4+CO
化学气相沉积(CVD)SiCl4+NH3→Si3N4NH4Cl
SiH4+NH3→Si3N4H2
氮化硅粉末:
高α相大于90%,高氮含量大于38%,细小于1微米(5.8m2/g)
氮化硅块体材料制备
⏹反应烧结⏹常压烧结⏹气压烧结⏹热压
烧结原理:
氮化硅是强共价键,扩散迁移率很低,并且在1600度开始明显挥发,因此很难烧结致密化。
通常加入MgO,CeO2Y2O3等稀土氧化物作为烧结助剂,它们将与氮化硅粉末表面的二氧化硅反应,在1400~1450度形成硅酸盐液相,形成液相烧结。
液相冷却后通常转变成玻璃相留在晶界。
性能
反应烧结常压烧结气压烧结热压
抗弯强度(MPa)200-300600-1000700-1200700-1300
应用:
⏹高温结构件⏹耐磨耐腐蚀件⏹轴承⏹刀具
氧化铝陶瓷
氧化铝有多种同素异形体。
但主要有三种:
α氧化铝:
三方晶系,在自然界只存在α氧化铝,如天然刚玉、红宝石、蓝宝石等。
α氧化铝结构最紧密、高温稳定,是三种形态中最稳定的晶型,具有优异的机电性能。
β氧化铝:
一种氧化铝含量很高的多铝酸盐矿物。
其化学组成可近似用RO·6Al2O3和
R2O·11Al2O3来表示(RO指碱土金属氧化物,R2O指碱金属氧化物)
γ氧化铝:
属尖晶石(立方)结构,氧原子呈立方密堆积,铝原子填充在间隙中。
它的密度小,且高温不稳定,机电性能差,在自然界中不存在。
由于是松散结构,因此可利用它来制造多孔特殊用途的材料。
氧化铝粉末制备
1拜尔法(湿化学法)由铝矾土(Al2O3·3H2O)和硬水铝石为原料
量大不太纯3000-8000元/吨
2热分解法高纯(99.99%以上)、超细8万~35万/吨
硫酸铝铵分解
Al2(NH4)2(SO4)3·24H2O→Al2(SO4)3(NH4)2SO4·H2O+23H2O↑(100~200C)
Al2(SO4)3(NH4)2SO4·H2O→Al2(SO4)3+2NH3↑+SO3↑+2H2O↑(500~600C)
Al2(SO4)3→Al2O3+3SO3↑(800~900C)
3电熔刚玉由铝矾土(Al2O3·3H2O)和硬水铝石为原料加碳在电弧炉内于2000~2400熔融制得,也称人造刚玉
氧化铝陶瓷的性质
莫氏硬度9,密度3.9,韧性3-5抗弯强度250-900Mpa,膨胀系数6-8×10-6/C,(与金属差不多)介电常数9-10,比电阻≥1013Ω·cm,导热系数25-30W/m·k
氧化铝陶瓷生产工艺
原料煅烧—磨细—配方—加成形剂—成形—素烧—修坯—烧结—表面处理
原料煅烧:
目的:
使γ氧化铝全部转变成α氧化铝,减少烧成收缩。
此外,还可排除氧化铝原料中的Na2O,提高原料的纯度。
磨细:
5微米的颗粒大于10%时,对烧结有明显的防碍作用。
球磨
配方:
纯氧化铝很难烧结且温度很高。
加入添加剂以降低烧结温度,促进烧结。
添加剂类型:
二大类:
一是与氧化铝形成固溶体(TiO2,Cr2O3、Fe2O3、MnO2等)
二是能形成液相(高岭土、SiO2、CaO、MgO等)
烧结:
1400~1800度/2~4小时
应用:
利用其机械强度和绝缘电阻大的性能,可作为真空器件、电路基板、可控硅和固体电
路外壳、火花塞绝缘体等;利用其强度和硬度较大的性能,可作为磨料磨具、纺织瓷件、刀具等、利用其良好的化学稳定性、可作为化工和生物陶瓷、人工关节等。
ZrO2陶瓷
含锆的矿石,自然界主要有二种:
斜锆石(ZrO2)和锆石英(ZrO2·SiO2)
二氧化锆有三种同素异形体。
立方、单斜和四方晶系
1170C2370C2715C
其相变转化如下:
单斜(m)———四方(t)———立方©———液相
密度5.656.106.27
单斜与四方晶系的转化,伴随7%左右的体积变化。
加热时由单斜转变为四方晶系,体积收缩;冷却时由四方转变为单斜,体积膨胀。
二氧化锆陶瓷的制造工艺、性质和用途
由于晶形转变,发生体积变化,单纯的二氧化锆陶瓷很容易开裂。
后发现加入适量的氧化物(Y2O3、CaO、MgO等),可使二氧化锆变成无异常膨胀、收缩的四方晶型的稳定的二氧化锆。
利用稳定的或部分稳定的二氧化锆,能获得性能良好的二氧化锆陶瓷。
Y2O3-PSZ(Y2O3部分稳定ZrO2)是将原来稳定ZrO2所需的Y2O3量从8mol%以上减少到3~4mol%,能明显提高ZrO2陶瓷的强度。
Mg—PSZ制备工艺:
成分为ZrO2-10mol%MgO的混合料在1700度烧结后快冷得到单相立方ZrO2,之后在1400度热处理,在立方ZrO2基体中析出细的四方ZrO2。
性能
抗弯强度韧性硬度
完全稳定ZrO21000-13007-1090-92
部分稳定ZrO2300-4003-487-90
烧结温度1650~1800度,保温2~4小时。
应用:
耐火度高、比热和导热系数小、是理想的耐火材料和高温绝缘材料,强度高、韧性好、硬度高可作为耐磨材料(球阀)。
ZrO2增韧陶瓷
韧性:
材料抵抗主裂纹失稳扩展的能力。
在大多数情况下,陶瓷内部存在有裂纹(包括表面裂纹、工艺缺陷等),当受到外力,或存在应力集中时,裂纹会迅速扩展,导致陶瓷体破坏。
因此防止裂纹扩展,消除应力集中,是提高韧性的关键。
ZrO2增韧原理:
利用ZrO2增韧陶瓷,是通过四方相(t-ZrO2)转变为单斜相(m-ZrO2)马氏体相变来实现