原料磨系统管理及操作规程.docx
《原料磨系统管理及操作规程.docx》由会员分享,可在线阅读,更多相关《原料磨系统管理及操作规程.docx(9页珍藏版)》请在冰豆网上搜索。
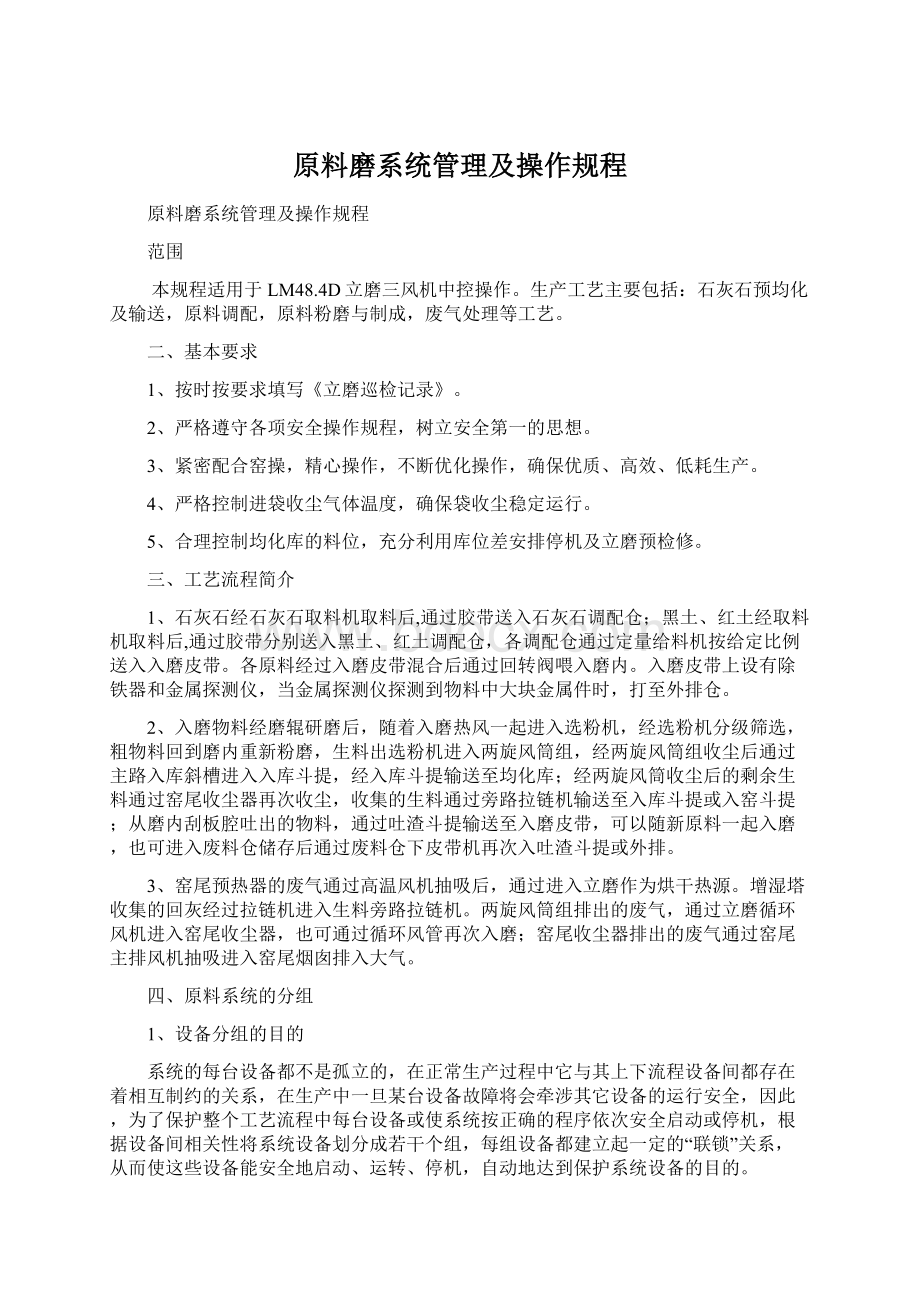
原料磨系统管理及操作规程
原料磨系统管理及操作规程
范围
本规程适用于LM48.4D立磨三风机中控操作。
生产工艺主要包括:
石灰石预均化及输送,原料调配,原料粉磨与制成,废气处理等工艺。
二、基本要求
1、按时按要求填写《立磨巡检记录》。
2、严格遵守各项安全操作规程,树立安全第一的思想。
3、紧密配合窑操,精心操作,不断优化操作,确保优质、高效、低耗生产。
4、严格控制进袋收尘气体温度,确保袋收尘稳定运行。
5、合理控制均化库的料位,充分利用库位差安排停机及立磨预检修。
三、工艺流程简介
1、石灰石经石灰石取料机取料后,通过胶带送入石灰石调配仓;黑土、红土经取料机取料后,通过胶带分别送入黑土、红土调配仓,各调配仓通过定量给料机按给定比例送入入磨皮带。
各原料经过入磨皮带混合后通过回转阀喂入磨内。
入磨皮带上设有除铁器和金属探测仪,当金属探测仪探测到物料中大块金属件时,打至外排仓。
2、入磨物料经磨辊研磨后,随着入磨热风一起进入选粉机,经选粉机分级筛选,粗物料回到磨内重新粉磨,生料出选粉机进入两旋风筒组,经两旋风筒组收尘后通过主路入库斜槽进入入库斗提,经入库斗提输送至均化库;经两旋风筒收尘后的剩余生料通过窑尾收尘器再次收尘,收集的生料通过旁路拉链机输送至入库斗提或入窑斗提;从磨内刮板腔吐出的物料,通过吐渣斗提输送至入磨皮带,可以随新原料一起入磨,也可进入废料仓储存后通过废料仓下皮带机再次入吐渣斗提或外排。
3、窑尾预热器的废气通过高温风机抽吸后,通过进入立磨作为烘干热源。
增湿塔收集的回灰经过拉链机进入生料旁路拉链机。
两旋风筒组排出的废气,通过立磨循环风机进入窑尾收尘器,也可通过循环风管再次入磨;窑尾收尘器排出的废气通过窑尾主排风机抽吸进入窑尾烟囱排入大气。
四、原料系统的分组
1、设备分组的目的
系统的每台设备都不是孤立的,在正常生产过程中它与其上下流程设备间都存在着相互制约的关系,在生产中一旦某台设备故障将会牵涉其它设备的运行安全,因此,为了保护整个工艺流程中每台设备或使系统按正确的程序依次安全启动或停机,根据设备间相关性将系统设备划分成若干个组,每组设备都建立起一定的“联锁”关系,从而使这些设备能安全地启动、运转、停机,自动地达到保护系统设备的目的。
2、设备联锁
联锁是系统设备保护的一种有效工具,根据联锁的功能不同,将其划分为安全联锁、启动联锁、运转联锁、保护联锁。
在工艺流程中设有启动和运转两种类型的联锁。
启动联锁:
⑴目的:
为了使工艺流程不中断,并能从下部流程的设备开始顺序地启动,工艺流程内的设备都被联锁着。
⑵联锁的功能:
只在工艺流程内的设备启动时起作用,当不符合启动条件时进行联锁使设备不能启动,满足了所有的启动联锁条件的设备方可启动,启动后,即使出现不满足启动联锁的条件,此时设备仍继续运行。
⑶启动操作:
按规定好的分组顺序,选择好要启动的组,并做好启动联锁条件准备,在条件具备的前提下依次完成启动操作,不按规定的顺序进行启动前的选择,或启动的联锁条件不具备,包括前组设备没有选择或没有完成启动时,即使进行启动操作,组设备启动是不会实现的。
运转联锁:
⑴目的:
为保护流程的系统功能和流程内的设备(电动机),一旦某台设备故障停机则该工艺流程的上部流程中,对该设备的运转能产生影响的所有设备的电动机均随之停机。
⑵功能:
运转联锁系统在设备启动或运转过程检测到异常时,便使运转的设备(电动机)及由该设备的运转所能产生影响的所有设备)均停止运转(或给出相应的报警信号)。
⑶操作:
运转联锁兼有启动联锁功能。
在工艺流程中,不在下部流程的设备启动后,就不能启动上部流程的设备,因而要参照联锁程序与上述启动操作顺序,按规定的顺序启动各设备。
3、原料系统设备分组
⑴石灰石(黑土、红土)入库组
⑵原料调配组
⑶立磨喂料组
入磨皮带、除铁器、气动分料阀、回转下料器
⑷生料库顶组
库顶袋收尘、收尘风机、分配器风机、分配器备用风机、库顶斜槽风机、库顶斜槽备用风机
⑸生料输送组
入库斗提、斜槽袋收尘、备用风机、2#斜槽风机、备用风机、1#斜槽风机、回转下料器
⑹回灰输送组
绞刀、外排翻板阀)、翻板阀、可逆绞刀。
⑺立磨排渣组
排渣胶带机提升机
五、开磨前准备
1、通知巡检工对系统设备进行检查确认,填好开磨OK表。
2、检查配料站各仓的料位是否正常,通知行岗位工、取料机工根据仓位组织进料。
3、通知电工、巡检工进行挡板“三对一”工作。
4、检查各测点的温度、压力、流量显示是否正常。
5、检查窑尾袋收尘器压差、进出口温度是否正常。
6、通知化验室设定原料配比,确定各入磨物料的比例。
7、通知总降、调度准备开磨。
六、正常开磨
1、启动均化库顶组;
2、启动生料输送组;
3、通知巡检工检查密封风机,启动密封风机,观察压力是否正常;
4、启动磨辊稀油站,观察压力、温度、流量是否正常;
5、启动主减稀油站,观察压力、温度、流量是否正常;
6、启动液压张紧站,观察压力、温度、流量是否正常;
7、将立磨选粉机转速设定为800rpm,启动选粉机;待运行平稳后,逐步调整其转速;
8、关闭立磨循环风机入口挡板,启动风机,待风机运行平稳后,逐步调整其入口挡板、出口挡板开度,保持磨出口适当负压,根据磨出口温度,逐步打开入磨热风挡板,保持磨入口负压,按照磨机升温曲线进行烘磨;
9、启动磨机喂料组;观察各设备的起动电流是否在合理的范围内,如有异常,及时要求现场进行确认。
10、启动立磨吐渣组;
11、通知公司调度、总降、电工、磨巡检工,现场检查磨辊是否升起,启动磨主电机;
12、当磨机出口温度大于90℃,启动原料喂料组,按照化验室的要求设定配料比例;
13、增加立磨循环风机的抽风量,加大磨内通风量,同时调整入磨热风挡板开度,和循环风挡板开度,保持入磨负压小于1600Pa。
同步调整窑尾系统风机挡板开度,确保立磨循环风机出口负压在正常范围;
14、设定研磨压力等于60-80bar,当磨机差压大于4500Pa时,进行降辊研磨;若差压达到5500Pa,可适当加大研磨压力。
14、启动磨机喷水装置,对磨内物料进行喷水,首喷设定为2t/h,可根据磨机出口温度调整磨内喷水量;
15、监视磨机振动值和磨机料层厚度,随时准备升辊;
16、当料层厚度超过100mm,增加研磨压力,但每次增压不准超过5bar/次;磨机振动稳定后,应先排空吐渣仓,在排吐渣之前可适当减产,并与现场保持联系,控制合理的下料速度(通过循环斗提的电流判断),避免磨况不稳。
17、当吐渣斗提电流下降,且料层厚度变薄时,可适当加产,每次加产不应超过10吨,时间间隔应大于10min;当吐渣斗提电流变大时,应增加磨内通风,增加立磨循环风机挡板开度,应同步增加选粉机转速;
18、当研磨压力达到75bar时,每增加研压不应超过2bar/次,且增压间隔必须大于15分钟,不论何时,研压不准超过85bar;
19、正常运行时,选粉机转速不准超过1300rpm。
七、停磨
1、通知巡检工,做好拉空石灰石仓、黑土仓、红土仓的准备;
2、通知窑、发电操作员做好相应准备,通知巡检工、化验室、总降、调度准备停磨;
3、停磨前2.5小时停止石灰石入库组;
4、停磨前2小时,通知联合储库行车工控制各调配仓料位,确保2小时后仓空;
5、待各仓下料出现不畅时,通知巡检工进行放仓工作,拉空后,停止原料调配组;(密切关注入磨皮带上物料、磨盘料层厚度、磨机振动情况,提前进行提辊操作,防止立磨出现异常振动);
6、为了控制好立磨振动,先减产运行,待立磨吐渣量下降时,减少磨内抽风,降低选粉机的转速,当出磨温度较高时,可先关小入磨热风挡板,控制好入磨风温。
当磨盘料层厚度逐步变小时,可降低研压。
当磨盘物料厚度小于50mm,可降压,升辊,将吐渣排至吐渣仓;
7、待入磨皮带上物料送完后,停止原料磨主电机;同时将入磨热风挡板关闭,打开旁路挡板,关闭循环风挡板。
关闭立磨循环风机入口挡板、出口挡板,停止循环风机;同时停止选粉机,当磨出口温度低于60℃时,同时办好停电手续并确认停电后,方可打开磨门,同控制磨内负压;
8、停磨后关风要尽量保证高温风机出口压力稳定,同时保证入窑尾收尘器气体温度,当入窑尾收尘器温度超过150℃,可适当打开入电收尘冷风挡板;
9、通知巡检工检查主斜槽物料输送情况,待彻底输送干净时,通知窑操,将回灰打至入窑后,同时1分钟后停止生料输送组;
10、停止生料库顶组;
11、在磨主电机停机2小时后,停止张紧液压站,将磨辊放至磨盘上。
在磨主电机停机超
过4小时以上时,可停止立磨磨辊润滑、主减稀油站;
12、在磨内停止通风4小时后方可停止密封风机。
4小时以上停磨:
1、通知现场适时停止向配料站各仓进料;
2、停止喂料组,停止磨内喷水组,升辊后,将三通阀挡板打入吐渣仓;
3、停磨主电机,打开旁路挡板、冷风挡板,逐渐减小热风挡板。
4、停止吐渣料循环组。
升辊大于15分钟,主电机停机小于4小时:
1、通知窑、发电操作员做好相应准备,通知巡检工、化验室、总降、调度准备停磨;
2、适时停止各仓进料。
3、止料、停喷水、升辊,停选粉机。
4、保持各稀油站、润滑站、液压站、密封风机及生料输送组及入库组的运行,可现场降辊。
5、若不入磨检查,关闭各入磨及出磨挡板进行保温(若须紧急入磨检查,先汇报分厂领导及生产调度),可关闭各入磨热风挡板,打开入磨冷风挡板及磨出口挡板,进行冷磨。
但入磨时必须关闭所有的进出口热风挡板。
15分钟以内升辊:
停原料调配组;
停磨内喷水;
关小循环风机入口挡板,控制磨内温度;
升辊超过15分钟,停磨主电机。
八、磨机操作控制量
1、出磨生料成分
通过改变原材料的配比来控制出磨生料成分。
2、磨喂料控制
磨机喂料量根据磨机差压控制。
根据变化的总喂料量、差压维护在相应的设定值水平。
当放吐渣仓内物料前,相应减少喂料量。
3、磨气流量控制
磨机气流量通过调整循环风机入口挡板的大小来进行控制。
4、磨出口温度
通过调整喷水量来保持磨出口温度恒定。
5、磨入口负压
通过调整循环风门的大小来保持磨机进口负压稳定。
九、磨机正常运行时调整参数范围
1、喂料量:
220t-300t/h2、选粉机转速:
1000~1300r/min
3、磨机入口负压:
500~1000Pa4、磨机入口温度:
180~240℃
5、磨机出口温度:
80~90℃6、磨机差压:
<6000Pa
7、磨主电机电流:
110A8、磨机振动:
5mm/s±2
9、收尘器入口温度:
90~180℃
十、应急处理
1、主减稀油站回油温度接近高高报时,可暂时升辊以降温,及时通知现场开启冷却器并观察冷却情况,减少喂料量,降低研磨压力,或停磨。
2、定量给料机载荷达到120%时,应减少板喂机给定值,超过5min时,可停止板喂机,待皮带秤载荷下降后再开启。
3、增湿塔大面积塌料时,应迅速升辊,可开大冷风阀补风,暂时降低选粉机转速。
4、磨出口温度过低或下降过快时,易引发磨内塌料,若磨内差压急剧上升时,应迅速升辊,防止振动跳停,同时升辊的时间不宜过长,待差压停止增长后即可降辊。
5、密切关注窑况,窑况有大的波动时,及时调整增湿塔的喷水量,防止湿底。
6、当黑土、红土断料5min以上应通知质检部门,10min以上应停磨处理。
7、磨内差压突然降低,应密切关注各参数的变化情况,尤其是循环斗提电流,若其值上升过快,可大致判断为下料口堵,通知巡检工去现场确认,应停磨处理。
8、磨主电机跳停:
迅速打开旁路挡板,关小热风挡板,适当打开冷风风机挡板,保证磨入口微负压,检查原因。
9、回转阀跳停:
喂料组、主电机连锁跳停,迅速打冷风风机环挡板,关闭热风挡板,调节循环风挡板、冷风挡板控制温度。
10、系统掉电:
现场关闭热风挡板,循环风机出口挡板,开冷风挡板,来电后及时启动密封风机,磨辊润滑站及各稀油站。
1、原料磨开机升温要求:
℃
100
90
80
投料
70
60
50
40
30
20
10
0
10
20
30
40
50
60
70
80
90
min
原料磨升温曲线
开机升温速率出磨温度每分钟不得超过1OC进出口温差不大于20OC
2、停机降温要求:
℃
100
80
60
50℃
开磨门
40
20
0
60
120
180
240
300
min
严格按降温曲线操作,磨机停机后出口稳定平缓降温
冷却到50℃以下时方可开启磨门(期间不得开启大气进气阀及排气阀)
开磨门时磨机内外温差不得超过30℃
降温速率每小时不得超过10℃