轴封端盖复合模具设计毕业设计论文.docx
《轴封端盖复合模具设计毕业设计论文.docx》由会员分享,可在线阅读,更多相关《轴封端盖复合模具设计毕业设计论文.docx(40页珍藏版)》请在冰豆网上搜索。
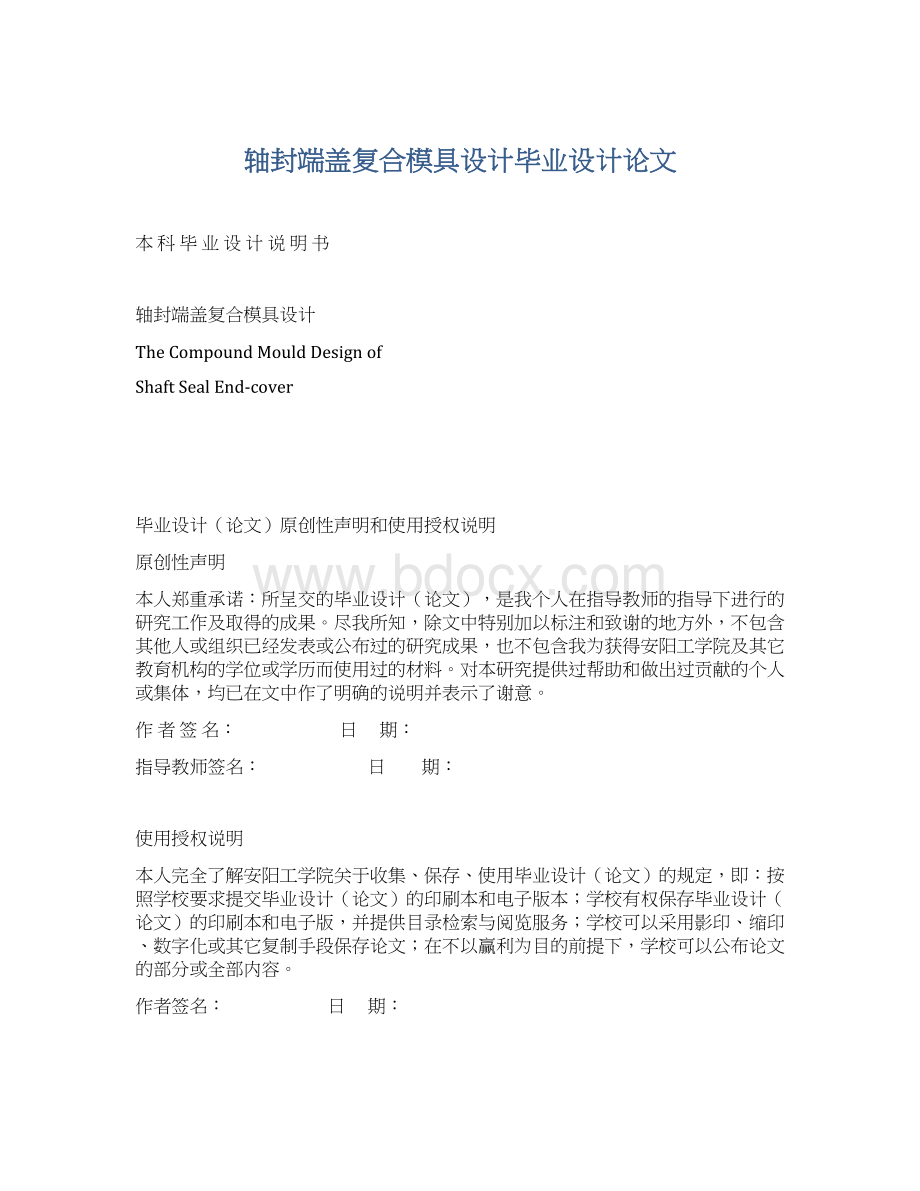
轴封端盖复合模具设计毕业设计论文
本科毕业设计说明书
轴封端盖复合模具设计
TheCompoundMouldDesignof
ShaftSealEnd-cover
毕业设计(论文)原创性声明和使用授权说明
原创性声明
本人郑重承诺:
所呈交的毕业设计(论文),是我个人在指导教师的指导下进行的研究工作及取得的成果。
尽我所知,除文中特别加以标注和致谢的地方外,不包含其他人或组织已经发表或公布过的研究成果,也不包含我为获得安阳工学院及其它教育机构的学位或学历而使用过的材料。
对本研究提供过帮助和做出过贡献的个人或集体,均已在文中作了明确的说明并表示了谢意。
作者签名:
日 期:
指导教师签名:
日 期:
使用授权说明
本人完全了解安阳工学院关于收集、保存、使用毕业设计(论文)的规定,即:
按照学校要求提交毕业设计(论文)的印刷本和电子版本;学校有权保存毕业设计(论文)的印刷本和电子版,并提供目录检索与阅览服务;学校可以采用影印、缩印、数字化或其它复制手段保存论文;在不以赢利为目的前提下,学校可以公布论文的部分或全部内容。
作者签名:
日 期:
轴封端盖复合模具设计
摘要:
本文主要阐述了轴封端盖复合模的设计过程。
首先通过对制件工艺性的分析,对比不同的生产方式以确定设计方案,再通过计算出总压力以选出压力机。
根据制件的尺寸要求计算出各工作部分的尺寸,并设计各主要零件的外形及固定方式,尤其是凹模周界尺寸的计算。
轴封端盖复合模具设计是以满足大批量生产的要求为前提,采用镶块式结构以避免修模。
本套模具提高了生产效率,降低了工人劳动强度,降低了生产成本,具有普遍适用性。
关键词:
工艺性;总压力;凹模周界尺寸;镶块式;修模
TheCompoundMouldDesignofShaftSealEnd-cover
Abstract:
Thispapermainlyexpoundstheshaftendcoversealingcompositemolddesignprocess.Firstofall,throughtheanalysisofthestampingmanufacturability,comparisonofdifferentproductionmethodsinordertodeterminethedesignscheme,andbycalculatingthetotalpressureinordertochoosethepress.Accordingtotherequirementsofthepartssizeiscalculatedforeachworksectionsize,anddesignthemainpartsoftheshapeandfixed.ShaftendcoversealingcompounddiedesignisbasedonthepremiseofmeettherequirementsofmassproductionandUSESthesetpieceofstructureinordertoavoidrepairingthemould.Thissetofmouldtoimprovetheproductionefficiency,reducestheworkerlaborintensity,reducetheproductioncost,hasgeneralapplicability.
Keywords:
manufacturability;totalpressure;dieperimetersize;panelboardtype;repairingthemould
引言
冲压是通过模具对板材施加压力或拉力,使板材塑性成形,有时对板材施加剪切力而使板材分离,从而获得一定尺寸、形状和性能的一种零件加工方法。
由于冲压加工经常在材料冷状态下进行,因此也称冷冲压。
冲压加工的原材料一般为板材或带材,故也称板材冲压。
冲压加工需要研究冲压工艺与模具设计两个方面的问题。
冲压工艺可以分为分离工序和成形工序。
分离工序有落料、冲孔、切断、切边、剖切等;成型工序包括卷圆、扭曲、拉深、变薄拉深、翻孔、翻边、拉弯、胀形、起伏、扩口、缩口、旋压、校形等。
冲压加工作为一个行业,在国民经济的加工业中占有重要的地位。
根据统计,冲压件在各个行业中均占相当大的比重,尤其在汽车、电机、仪表、军工、家用电器等方面所占的比重更大。
冲压加工的应用范围极广,从精细的电子元件、仪表指针到重型汽车的覆盖件和大梁、高压容器封头以及航天器的蒙皮、机身等均需冲压加工。
冲压加工是一种高生产率的加工方法,如汽车等大型零件每分钟可生产几件,而小零件的高速冲压则每分钟可生产千件以上。
由于冲压加工的毛坯是板材或卷材,一般又在冷状态下加工,因此轻易实现机械化和自动化,比较适宜配置机械人而实现无人化生产。
特别是适用于定型产品的中大批生产。
“冲压要发展,模具是关键”,提高模具的效率需从冲模设计和制造开始。
冲压加工的材料利用率较高,一般可达70%-85%,冲压加工的能耗低,由于冲压生产具有节材、节能和高生产率等特点,所以冲压件呈批量生产时,其成本比较低,经济效益较高。
当然,冲压加工与其他加工方法一样,也有其自身的局限性,例如,冲模的结构比较复杂,模具价格偏高。
因此,对小批量、多品种生产时采用昂贵的冲模,经济上不合算,目前为了解决这方面的问题,正在努力发展某些简易冲模,如聚氨脂橡胶冲模、低合金冲模以及采用通用组合冲模、钢皮模等,同时也在进行冲压加工中心等新型设备与工艺的研究。
第1章轴封端盖工艺性分析
1.1零件材料的分析
考虑到产品成本和零件的使用性能,选用常用钢08F,是一种优质碳素结构钢,其屈服强度为180MPa,抗拉强度为280~390MPa,抗剪强度为200~310MPa,延伸率32%,适宜冲压选择。
1.2轴封端盖的工艺性分析
轴封端盖是轴对称件,见图1.1,其工艺过程为落料、冲孔、拉深、翻边,工件结构较为简单,厚度仅为1.5mm,冲裁性能较好,工艺性容易满足。
图1.1轴封端盖零件图
一般情况下,圆孔翻边时的孔缘在单向拉应力作用下,切向伸长变形引起的厚度减薄最大,最容易破裂,由于材料性质不均匀,孔缘各处允许的切向延伸率不一样,一旦孔缘某处的伸长变形超过了该处延允许的材料伸率,该处就会因厚度减薄过大而破裂。
翻边时的变形区基本上限制在凹模圆角区之内,凸模底部材料为直角变形区,处于切向、径向受拉伸的应力状态,切向应力在孔边缘最大,径向应力在孔边缘为零。
圆孔翻边时的变形程度用翻边系数K表示:
(1-1)
式中,d——毛坯上圆孔的初始直径;
D——翻边后竖边的中径。
(1)影响圆孔翻边成形极限的因素如下:
①材料伸长率和硬化指数n大,K小,成形极限大。
②孔缘如无毛刺和无冷作硬化时,K较小,成形极限较大。
为了改善孔缘状况,可采用钻孔代替冲孔,或在冲孔后进行整修,有时还可在冲孔后退火,以消除孔缘表面的硬化。
③用球形、锥形和抛物线凸模翻边时,变形条件比平底凸模优越,K较小。
在平底凸模中,其相对圆角半径
越大,极限翻边系数可越小。
④板材相对厚度越大,K越小,成形极限越大。
(2)毛坯尺寸的计算:
①毛坯翻边预制孔直径
,由参考手册可得:
(1-2)
式中,D—翻边直径32(按中线计)(mm);
H—翻边高度(mm),H=7mm;
r—竖边与凸缘的圆角半径(mm),r=3.5mm;
t—料厚(mm),t=1.5mm。
则:
预制孔直径为23mm。
②毛坯的直径
当零件的弯曲角为
时,则毛坯的展开长度为
(1-3)
已知,
mm。
第2章冲压工艺方案的确定及各部分工艺力的计算
2.1冲压方案的拟定
考虑到需落料、冲孔、拉深、翻边成形四道工序,可以有以下种方案:
方案一:
先落料冲孔,后拉深翻边成形,采用单工序生产。
方案二:
落料-冲孔-翻边-拉深复合模,采用复合模生产。
方案三:
落料-冲孔-翻边-拉深级进模,采用级进模生产。
方案一结构简单,但需两道工序、两副模具才能完成,效率较低,且精度不易保证。
如此浪费了人力,物力,财力。
从经济角度考虑不妥当,难以满足大批量生产要求。
方案二只需一副模具即可成形,该工艺特点首先进行落料,再冲孔,翻边,拉深成形。
采用这种方法加工的工件外观平整、毛刺小、产品质量高,而且大大的提高了生产效率,也解决了操作者将手放入模具内的不安全因素,复合模能在压力机的一次行程内,完成落料、冲孔、及拉深、翻边数道工序。
在完成这些工序的过程中,冲件材料无须进给移动。
方案三:
级进模是在压力机一次行程中完成多个工序的模具,它具有操作安全的显著特点,模具强度较高,寿命较长。
使用级进模便于冲压生产自动化,可以采用高速压力机生产,也只需要一副模具,制造精度较高,先落料后冲孔,再进行拉深翻边成形,但是级进模较难保证内、外相对位置的一致性,相对生产周期长,其模具结构复杂,成本高,板料的定位与送进是级进模设计中的关键问题。
通过上述三种方案的分析比较,该工件的冲压生产采用方案二为佳。
2.2排样设计
冲裁件在板、条等材料上的布置方法称为排样。
排样的合理与否,影响到材料的经济利用率,还会影响到模具结构、生产率、制件质量、生产操作方便与安全等,因此,排样是冲裁工艺与模具设计中一项很重要的工作。
冲压件大批量生产成本中,毛坯材料费用占60%以上,排样的目的就在于合理利用原材料。
衡量排样经济性、合理性的指标是材料利用率。
要提高材料利用率,就必须减少废料面积,冲裁过程中所产生的废料,可分为两种情况。
(1)结构废料
(2)工艺废料
根据材料的利用情况,排样的方法可以有三种,如图2.1。
(a)有废料排样(b)少废料排样(c)无废料排样
图2.1排样方式
有废料的排样法材料利用率较低,但制件的质量和冲模寿命较高,常用于工件形状复杂、尺寸精度要求较高的排样。
少、无废料排样法的材料利用率较高,但是,少、无废料排样的应用范围有一定的局限性,受到工件形状结构的限制,且由于条料本身的宽度公差,条料导向与定位所产生的误差,会直接影响工件尺寸而使工件的精度降低。
在几个工件的汇合点容易产生毛刺。
由于采用单边剪切,也会加快模具磨损而降低冲模寿命,并直接影响工件的断面质量,所以少、无废料排样常用于精度要求不高的工件排样。
考虑到造作方便及模具结构简单,故采用单排排样设计。
搭边值要合理确定,搭边值过大,材料利用率低。
搭边值小,材料利用率虽高,但过小时就不能发挥搭边的作用,在冲裁过程中会被拉断,造成送料困难,使工件产生毛刺,有时候还会被拉入凸模和凹模间隙,损坏模具刃口,降低模具寿命。
搭边值过小,会使作用在凸模侧表面上的法向应力沿着落料毛坯周长的分布不均匀,引起模具刃口的磨损。
(3)搭边值的选取
综合考虑影响搭边值的因素,由参考手册查得搭边值
=1.2mm,
=1.0mm。
条料送进步距h=87.1+1.0=88.1mm
有以上数据,排样设计如图2.2。
图2.2排样图
2.3材料利用率的计算
一个步距内的材料利用率
(2-1)
式中,A—冲裁件面积(包括冲出的小孔在内)(
);
n—个步距内的冲件