新型ATF定量加油机改造及问题分析.docx
《新型ATF定量加油机改造及问题分析.docx》由会员分享,可在线阅读,更多相关《新型ATF定量加油机改造及问题分析.docx(13页珍藏版)》请在冰豆网上搜索。
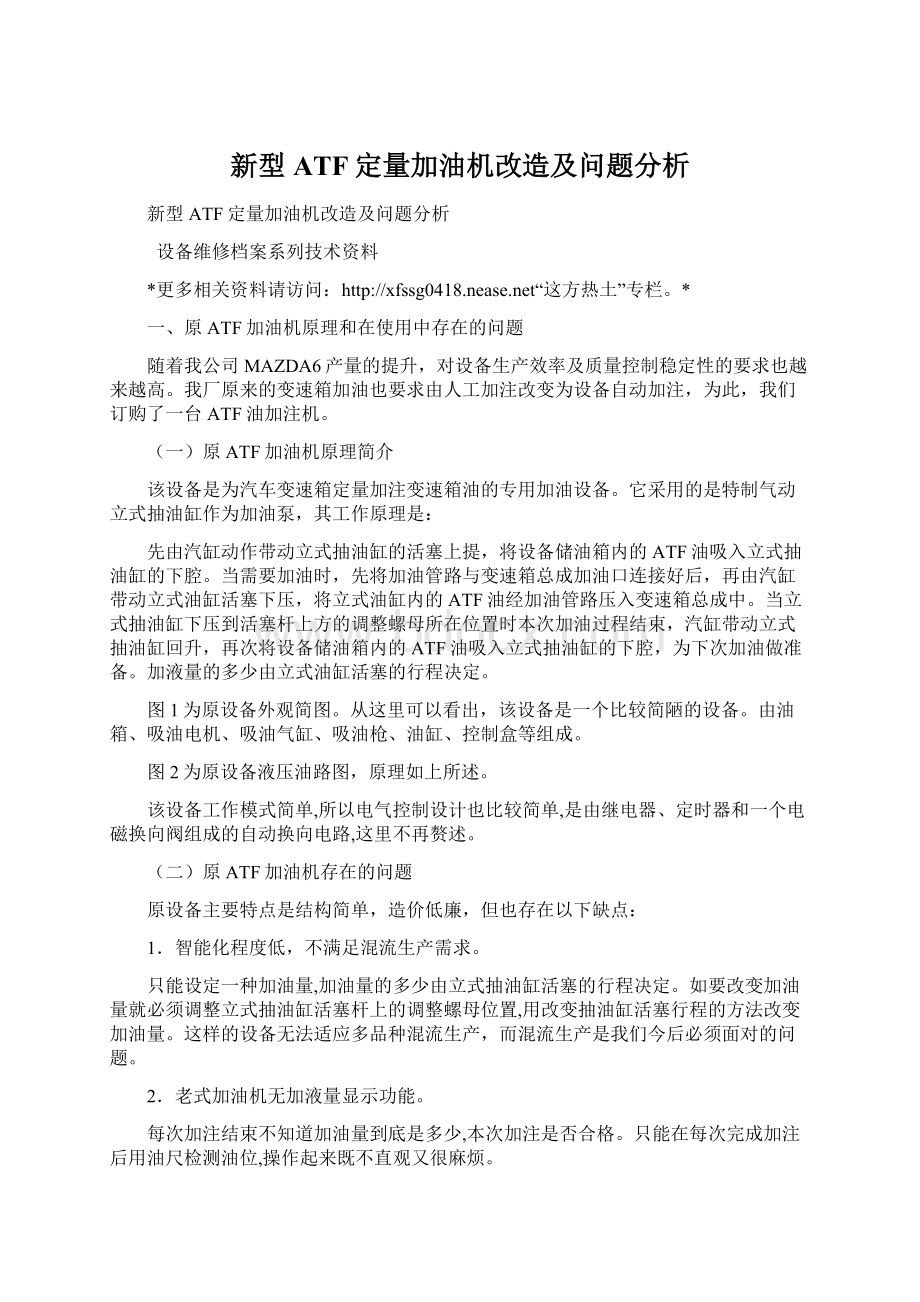
新型ATF定量加油机改造及问题分析
新型ATF定量加油机改造及问题分析
设备维修档案系列技术资料
*更多相关资料请访问:
“这方热土”专栏。
*
一、原ATF加油机原理和在使用中存在的问题
随着我公司MAZDA6产量的提升,对设备生产效率及质量控制稳定性的要求也越来越高。
我厂原来的变速箱加油也要求由人工加注改变为设备自动加注,为此,我们订购了一台ATF油加注机。
(一)原ATF加油机原理简介
该设备是为汽车变速箱定量加注变速箱油的专用加油设备。
它采用的是特制气动立式抽油缸作为加油泵,其工作原理是:
先由汽缸动作带动立式抽油缸的活塞上提,将设备储油箱内的ATF油吸入立式抽油缸的下腔。
当需要加油时,先将加油管路与变速箱总成加油口连接好后,再由汽缸带动立式油缸活塞下压,将立式油缸内的ATF油经加油管路压入变速箱总成中。
当立式抽油缸下压到活塞杆上方的调整螺母所在位置时本次加油过程结束,汽缸带动立式抽油缸回升,再次将设备储油箱内的ATF油吸入立式抽油缸的下腔,为下次加油做准备。
加液量的多少由立式油缸活塞的行程决定。
图1为原设备外观简图。
从这里可以看出,该设备是一个比较简陋的设备。
由油箱、吸油电机、吸油气缸、吸油枪、油缸、控制盒等组成。
图2为原设备液压油路图,原理如上所述。
该设备工作模式简单,所以电气控制设计也比较简单,是由继电器、定时器和一个电磁换向阀组成的自动换向电路,这里不再赘述。
(二)原ATF加油机存在的问题
原设备主要特点是结构简单,造价低廉,但也存在以下缺点:
1.智能化程度低,不满足混流生产需求。
只能设定一种加油量,加油量的多少由立式抽油缸活塞的行程决定。
如要改变加油量就必须调整立式抽油缸活塞杆上的调整螺母位置,用改变抽油缸活塞行程的方法改变加油量。
这样的设备无法适应多品种混流生产,而混流生产是我们今后必须面对的问题。
2.老式加油机无加液量显示功能。
每次加注结束不知道加油量到底是多少,本次加注是否合格。
只能在每次完成加注后用油尺检测油位,操作起来既不直观又很麻烦。
3.漏油严重。
因为原设计的立式抽油缸直径和长度都比较大,所以密封圈的密封面积也较大,且这种频繁往复工作的抽油缸对密封圈的密封性要求很高,国产密封圈在材料和加工工艺方面比较落后,抽油缸漏油的问题始终不能很好的解决。
另外原设备在加注枪头处没有设计控制阀,只是在加油完成后简单的将加注头向上悬挂,从加注头处漏油的情况就很严重,导致工作现场的环境比较恶劣。
4.工作节拍长。
立式抽油缸的往复速度与压缩空气的压力、立式抽油缸直径、加油管路出口直径和ATF油的粘度都有关系。
由于多方面条件因素的限制,这种加注机工作速度不能太快,不能适应3分钟以内节拍的生产线。
5.加注量不准确,重复精度低。
●由于加注头处没有控制阀,设备管路在非加注状态下没有完全密封,在管路中的这部分加注介质无法控制,造成了加注量不准。
●立式抽油缸内部密封不好,在加油时抽油缸内部蹿油的现象较为明显。
●因压缩空气压力的变化、ATF温度变换导致的ATF油粘度的变化,对抽油缸下压速度有明显的影响,而经试验证明抽油缸下压速度的变化对加注量的影响非常明显。
二、新型ATF定量加油机的改进方案
因为旧设备在设计和使用方面存在着较为明显的缺陷,根据新生产线的工艺、节拍等要求,老式定量加油机明显不能满足生产需要。
因此,我们根据存在的问题,提出了改进的要求和具体方案。
1.机床结构重新规划,设计更合理的加油控制油路,改变加油方式,变活塞式吸油加注为加油泵通过管路对变速箱直接加注。
2.用流量泵进行流量计数,进行加油量的控制。
3.为能合理控制储液罐液位,实现自动从油桶向储液罐补液,设置液位传感器及XST系列液位控制仪表。
4.由于油温对加注量有比较明显的影响,为解决该问题,在储液罐内增加加热器,并设置Pt100热电阻温度传感器及CH402过程仪表进行温度控制。
5.考虑设备的混流生产需要,增加多车型的柔性加注量选择,利用条码扫描,或手工选择加注量的方法,快速变更加注量。
实施中,鉴于我们没有自行制造能力,我们提出具体方案要求后,协调厂家(北京东昆科技公司)进行了机床本体设计和制造工作。
我们则承担了全部电气系统的控制柜配制、现场安装配线、部分油路安装、最终现场调试及后期程序改进等工作。
成为我单位和厂家联合解决重要设备问题的典型实例之一。
三.新型ATF加油机原理简介
(一)加注过程描述
新型ATF加油机的工作过程是:
ATF油存储在加油机内的储液罐内,加油机通过补液泵从两个55加仑油桶向加油机内的储液罐补充油液。
当定量加油机的加注头与变速箱总成连接好后,按加注头上的加注按钮,储液罐中的ATF油液经主液泵、设备管路、减压阀、流量传感器、控制阀和加油枪加注到生产线上的变速箱中。
整个设备由PLC来进行控制,加注量由计量泵来控制。
(二)加注系统的机械结构及改进
机械部分在原系统基础上有如下改进:
●新型加油机采用Ingersoll-Rand高速气动泵作为加液主泵,这样大大缩短了加注时间。
●由于采用了小直径、短行程、高速往复气动泵和进口密封件,漏油现象基本解决。
●在加注头处安装了结构紧凑的控制阀密封加油管路,使加液设备内部管路无控制盲点。
图3是新设备的液压原理图。
它分加注系统、补液系统、气动系统三个部分。
加注系统完成向车辆变速箱的加注,补液系统负责对储液罐的补液,气动系统实现对气动泵、阀、加注枪等驱动控制。
原理非常明了,不再赘述。
(三)电气控制原理
新型ATF加油机在电气设计方面也都有很大的改进:
在新型ATF定量加油机中安装了西门子S7-226PLC,按照“二”预定的方案进行了新设备的电气设计。
控制上,本设备除逻辑控制由PLC完成外,还使用了OP07进行工作方式选择及参数设置,用CH402过程仪表及加热装置进行油温控制,用XST仪表及液位传感器进行储液罐的液位控制,用ARO计量泵及PLC高速计数单元进行加注量控制等。
功能方面,改造后的设备集自动循环定量加注、ATF油恒温控制、加油量显示、生产线车型自动选择和设备储油箱自动补液等功能为一体。
另外还预留了条码枪接口和工业以太网接口,为今后的全生产线联网奠定基础。
下面是全系统的电气控制结构框图,详细图纸可参见本文后附录资料。
图4:
系统电气原理框图
很明显,新系统比老设备功能完善得多,能够适应MAZDA6生产发展及产品混流的需要。
四.改造中主要技术难点的实现及探讨
在改造中,有几个问题有别于常规的PLC可编程逻辑控制器的设计,有一定的技术难度。
这里分别予以探讨:
(一)加注量的精确控制
因为设备采用了高精度计量泵(最小单位0.186ml)将所记录的加油量以高速脉冲的形式实时传递给PLC的高速记数器HSC0,PLC采用4倍速A/B相正交高速记数的方式工作,保证了在高速记数的过程中不丢记数脉冲,从而使加油量得到的准确控制。
如图5,表述了PLC高速计数器的数据转换过程。
1.系统通过OP07设置加注系数SLOW-K和加注量SFLOW,分别储存于数据寄存器VD110、VD24。
2.这两个数据进行乘积后,转换成加注控制当量,通过PLC内部进行数据整数转换等,用于加注控制的设定值。
3.加注量由计量泵进行测量,以高速脉冲的形式送高速计数端口HSC0。
4.HSC0的计数值送数据寄存器VD8,并通过除加注系数SLOW-K的方法,得到实际加注量,存VD16。
5.VD16的加注量和设定加注量SFLOW比较,如果大于设定值,则停止加注。
6.实际加注量VD16通过VD44(标签CFOW)送OP07进行实际加注量显示。
图5:
高速计数器用于加注量控制的软件计算流程图
这个基于高速计数器端口的控制过程,基本满足了目前生产准确加注的定量控制需要。
(二)油箱温度控制
之所以要控制温度,主要原因是为防止不同季节中,厂房温度发生较大变化时,保证相对恒定的油温,以避免变速箱油的黏度变化对加注量产生影响。
1.控制方法:
我们采用的方法是典型的温度过程控制方法——用Pt100热电阻、温度过程仪表CH402、加热器构成温度检测控制系统。
系统框图见图6所示。
图6:
温度过程控制系统框图
为了解决单点温度控制的频繁切换,而导致继电器触点烧蚀问题,我们使用了固态继电器。
2.外部接线:
CH402是典型的温度过程仪表。
该仪表有12个接线点,其外部接线方法为:
1:
220VAC火线L,2:
220VAC零线N。
3:
闲置。
4:
控制输出公共线。
5:
控制常开点输出(4、5)。
6:
控制常闭点输出(4、6)。
7:
闲置。
8、9:
报警输出AL1(触点)。
10、11、12:
传感器。
当用热电阻(RTD):
11、12短接,热电阻接到10-11、12。
当用热电偶(TC):
11接TC+,12接TC-,10闲置。
3.参数设置:
该仪表参数说明如下:
1).SV:
设定值。
温度控制目标值。
出厂值:
0度。
我们实际控制油温为26度。
2).AL1:
报警偏差。
范围:
-1999-+9999℃或者-199.9-+999.9℃。
超过该偏差AL1报警输出。
出厂值:
50。
3).LBA:
控制环中断报警。
范围:
0.1-200min(分)。
超过该值时,系统给出报警。
该值一般设置为积分时间的2倍。
当ATU作用激活时,LBA失效。
另外,PID调节必须结束后,延迟LBA时间,保护起作用。
4).LBD:
LBA死区设置。
范围0-9999℃。
出厂值:
0。
5).ATU:
自动调节(AT)。
0:
在结束点或悬挂点,即无调节过程。
1:
在起点。
出厂值:
0。
该功能可以在调节过程中自动计算PID和LBA参数,实现系统自动调节作用。
此时,LCK不能锁定。
6).STU:
自调节(ST)。
0:
在悬挂点。
1:
在起点。
出厂值:
0。
此时,人为设置的PID起作用。
但当AT激活时,ST不起作用。
注意,ST激活时,无法修改PID、ARW数据。
如果系统出现波纹,建议关断ST作用。
7).P:
比例区间。
1-9999℃或者0.1-999.9℃。
设为0无比例作用。
出厂值:
30。
8).I:
积分时间。
1-3600秒。
设置为0时为PD控制。
出厂值:
240。
9).D:
微分时间。
1-3600秒。
设置为0时为PI控制。
出厂值:
60。
10).Ar:
防静差(Arw)。
比例区间的1-100%,设置为0时,积分取消。
出厂值:
100。
11).T:
比例循环。
1-100秒。
设定控制输出循环。
出厂值:
20。
12).Pb:
PV补偿。
-1999到9999℃或-199.9到999.9℃。
传感器误差校正值。
13).LCK:
设定数据锁存。
可以设置参数修改允许/禁止。
0000——SV和参数可以修改。
0001——仅仅可以修改SV、AL1。
0010——仅可以修改AL1以外的数据。
0011——仅可以修改SV。
0100——仅可以修改SV以外的数据。
0101——仅可以修改AL1。
0110——仅可以修改AL1、SV以外的数据。
0111——全部不能修改。
(三)液位控制
液位控制系统设计的目的,是为了实现从油桶到储油罐的自动补液操作。
我们使用了两个油桶,也分别设置了液位控制,一个油桶抽完后,自动切换到另一个油桶。
这里主要说明储油罐的液位控制。
该罐由于有油温控制,为安全起见,液位控制同样需要安全可靠。
同时,也是为了及时补油,以免对生产产生影响。
下面是液位控制系统的框图:
图7:
液位控制系统控制框图
液位传感器使用的是SAILOR公司的HTQ01,这是一个模拟传感器,直接接到XST仪表的13、14脚。
XST过程仪表功能相对比较强,可以进行温度、液位及其它基于标准变送器的过程控制。
其特点是:
1.输入控制信号可以是热电阻、热电偶、0-10mA、0-20mA、4-20mA电流、0-5V、1-5V电压、电位器等类型,适用面比较广泛,可以用于一般常规过程控制。
2.可以设定八个控制点,并分别有对应输出,控制相对灵活,可以控制比较复杂的过程。
3.具有外部RS232、RS485接口,便于实现外部通讯,提供数据采集通道。
我们实际使用了四个控制点,分别是超下、下、上、超上,设定值为:
80、100、320、340。
该器件原理上与CH402是基本相同的,只是功能更强大,限于篇幅,加上我们仅仅用来做液位控制,这里不介绍其接线及参数设置。
五、设备常见故障及处理方法
为便于维修,我们归纳了新设备常见故障、原因及其处理方法,如下表:
故障
原因
解决办法
加注量不准确
流量传感器变动
标定流量传感器
储液罐内油液液位低
补充油液,检查液位控制器上下限并设定值
压缩空气停
气源过滤器堵塞
清洗/更换虑芯
气源开关未打开
修理/更换开关
供液故障排除:
故障
原因
解决办法
储液罐空或液位低
补液过滤器堵塞
更换虑芯
补液泵故障
维修/更换补液泵
55加仑ATF油桶中没油
换桶
储液罐内用于控制液位的传感器失效
维修/更换液位传感器
加注量不准或根本不加注
供液泵故障
维修/更换供液泵
供液泵入口过滤器堵塞
清洗过滤器
加注枪故障
维修/清理加注枪
截止阀故障
修理/更换截止阀
流量传感器故障
清洗/修理/更换
加注按钮/条码开关故障
联机检修线路/开关
OP07操作面板故障
检查通讯线路/更换操作面板
加注头滴油
压缩空气气压故障
检查气源和管路
加注枪内密封件老化
更换密封件
六、运行期间发现问题及继续改善
(一)软件问题
原软件设计是由北京公司做的,使用中发现流程结构过于复杂,明显地象在做复杂的数学逻辑,很多编程习惯受高级语言结构化编程的影响。
当然,也许这是一个好的编程习惯,但对于一个不是很庞大,很复杂的过程来说,这种编程方法,直接影响了程序的可读性。
这给对要求快速反应的生产维修来说,带来了许多的不便。
为此,我重新考虑和自行修改了设备控制程序。
修改后的程序,有如下特点:
1.结构更简单,可读性明显加强。
2.指令代码大量减少,思路变得更清晰易懂。
目前,修改设计后的程序已经下载到设备,运行情况良好。
论文后面附录中,给出了修改后的部分程序。
(二)固态继电器设计引发的事故及其处理
原来的温度控制系统中,我们直接使用了固态继电器控制加热器进行加热。
电路结构如图:
图8:
加热器控制图
即:
当温度仪表通知PLC,应该进行加热时,PLC通过Q0.0驱动继电器KA1,KA1的触点给加热器送电。
这个电路的问题是:
固态继电器的“触点”J1,实际上是可控硅的AK极。
如果可控硅击穿,加热器将连续加热而失去控制,温度过程仪表即使控制关断,对固态继电器也将不再起作用。
我们实际使用中,就发生一起这样的事故,整箱油被蒸发,部分器件造成损坏。
为此我们采取了如下改善措施:
1.在系统中增加了一个接触器KM2,把KM2常开触点串联到J1前。
KM2也由温度仪表通过PLC控制。
2.为了消除控制点附近的抖动,我们设计了3秒的滤波程序,使得KM2不发生抖动而达到稳定控制。
这样做以后,由于KM2不存在所谓触点“击穿”问题,加上两个器件同时故障的可能性大大降低,杜绝了同样隐患的再发生。
(三)高速计数设计缺陷分析
1.高速计数器的常规设计方法及设计存在问题
由于西门子S7-200系列PLC属于低端小型产品,没有单独的智能高速记数模块。
在使用高速记数功能时是用PLC的CPU模块内部集成的高速记数器HSC0~HSC5。
本设备用的高速计数器HSC0所使用的高速输入口是I0.1和I0.1。
常规做法是:
先给高速计数器预置一个设定值PV,当其当前值CV等于设定值PV时就触发一个中断事件,并转而调用相关中断服务程序完成所需任务。
之后再利用中断程序装入一个新预设值,为下一次中断响应做准备。
因为中断事件的响应是即时的,其响应速率远远高于程序扫描方法的响应速率,因而高速计数器可以实现精确的高速控制。
利用此种方法时高速计数器的工作频率可达到10~30KHZ。
但该设备在使用高速计数器时没有编制相关的中断程序。
原来的做法是:
先将HSC0设定成4倍速A/B相正交输入的高速记数方式,并把其当前值用MOV指令不断的传送到PLC的数据字VD8中,经一系列转换和相关算法后把得到的数据放入VD16中去,然后去比较VD16(当前值)和数据字VD24(预设值),当VD16>VD24时停止加油。
图9:
原设计程序高速计数器处理过程流程图
具体转换过程如图9所示。
该过程是在每个扫描周期访问到对应数据字时,才去查询高速计数的结果,这样就失去了高速计数器即时响应的意义。
2.原设计对加注精度影响的估算
经本人粗略对其过程估算,得出结果如下:
S7-226PLC常规循环扫描时间约在1~100ms之间。
本设备使用的S7-226PLC的时钟频率是33MHZ,执行一条布尔指令的时间是0.37us。
因本设备约有400条左右的PLC指令,并考虑到使用了大量MOV等多周期指令的因素,估算循环扫描时间应大于3ms。
而现在设备加注1.8L油时需要记数17460次(1.8升×加注系数9700),经现场记时,在标准加注压力下加注1.8升ATF油用时12秒,反算出高速计数器的输入周期在0.69ms左右。
虽然高速计数器的允许频率远高于0.69ms的对应速度,但原程序是将高速计数器的当前值用一系列普通“低速指令”(MOV、COMPARE、DI—R)进行运算处理,这种做法在理论上有2.3ms以上的失控区间(按当前加油记数速度来算会在高速记数到位的最后时刻多加注3个脉冲量)。
一旦今后对此设备其它相关功能的程序进行补充时,如条码枪扫描输入、车型自动选择和加油数据网络采集等(因工艺原因暂未落实),PLC的程序会更大、循环扫描时间会更长,高速记数的失控脉冲也会相应增多。
另外如高速计数器相关程序不用中断来做,PLC在运行程序时会首先响应其他中断事件(如PLC通讯端口接受条码引发的中断事件)。
而ATF定量加油机的首要任务是保证高速计数器工作的即时性,应给它以高级别的中断优先权,这在程序编制上是十分重要的。
用高速计数器触发中断事件来控制相关程序是正确的方法,可以保证控制的即时性,进而保证加注精度。
3.改进的方法
我针对以上问题,编制了一小段程序(用高速记数器的中断事件号调用中断程序),如图10所示。
这个程序解决了上述问题。
七.改进的效果及意义
以上的改造过程及后期改善,使得变速箱高效精确加油的生产需要得到良好的解决,并为今后的多品种混流生产创造了条件。
改造前,变速箱加油效率及加注量不稳定的问题,一直成为总装生产一个长期存在设备问题。
项目实施后,设备使用效果一直稳定良好,加注精度完全满足工艺需要。
图10:
改进后的高速计数器处理程序
由于时间和本人技术水平等原因,所阐述的问题一定存在不妥之处,敬请各位评审老师批评指正。
此致
工友(GuQ)2005/11/03