利用Teamcenter实现三维工艺设计技术.docx
《利用Teamcenter实现三维工艺设计技术.docx》由会员分享,可在线阅读,更多相关《利用Teamcenter实现三维工艺设计技术.docx(7页珍藏版)》请在冰豆网上搜索。
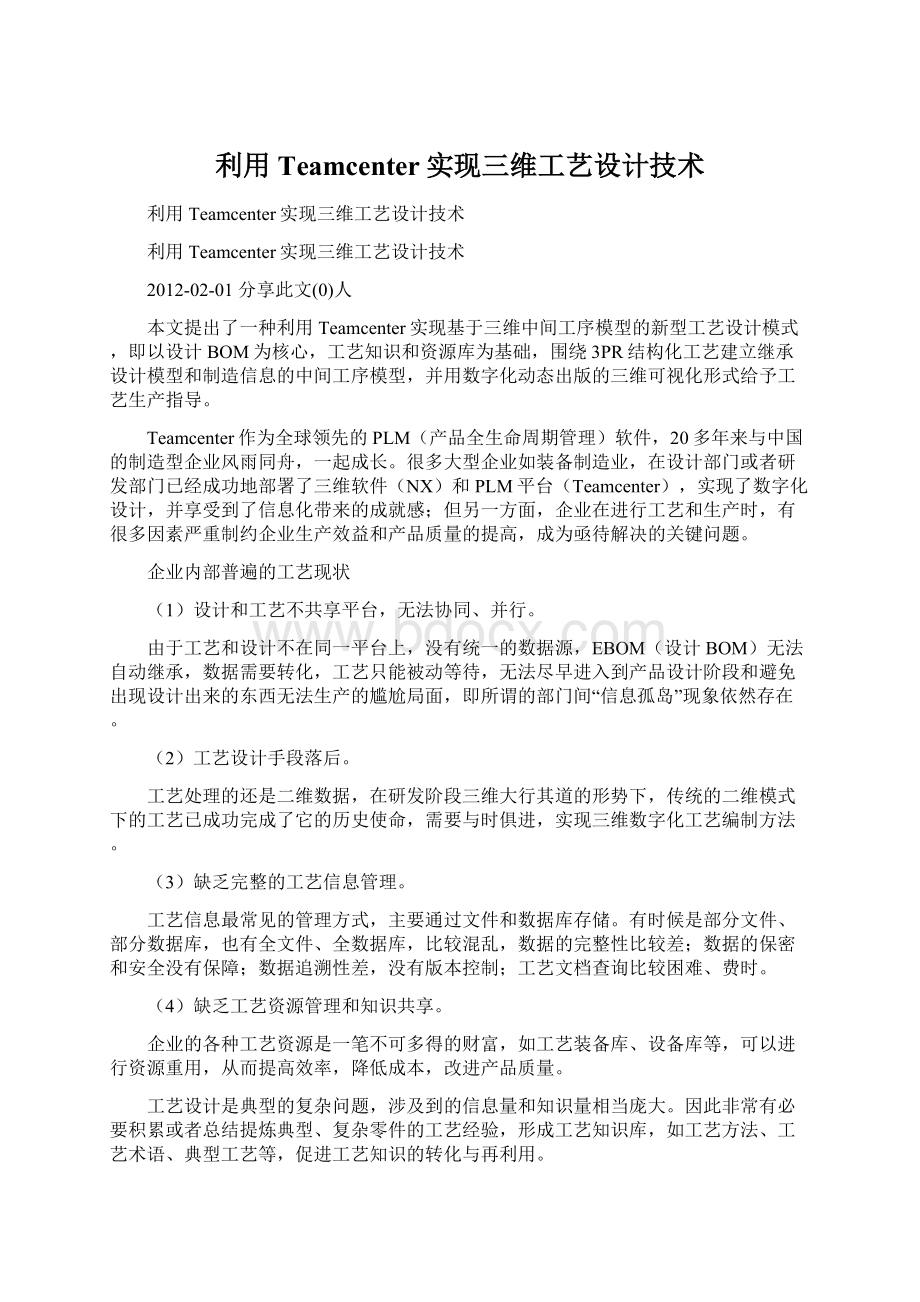
利用Teamcenter实现三维工艺设计技术
利用Teamcenter实现三维工艺设计技术
利用Teamcenter实现三维工艺设计技术
2012-02-01分享此文(0)人
本文提出了一种利用Teamcenter实现基于三维中间工序模型的新型工艺设计模式,即以设计BOM为核心,工艺知识和资源库为基础,围绕3PR结构化工艺建立继承设计模型和制造信息的中间工序模型,并用数字化动态出版的三维可视化形式给予工艺生产指导。
Teamcenter作为全球领先的PLM(产品全生命周期管理)软件,20多年来与中国的制造型企业风雨同舟,一起成长。
很多大型企业如装备制造业,在设计部门或者研发部门已经成功地部署了三维软件(NX)和PLM平台(Teamcenter),实现了数字化设计,并享受到了信息化带来的成就感;但另一方面,企业在进行工艺和生产时,有很多因素严重制约企业生产效益和产品质量的提高,成为亟待解决的关键问题。
企业内部普遍的工艺现状
(1)设计和工艺不共享平台,无法协同、并行。
由于工艺和设计不在同一平台上,没有统一的数据源,EBOM(设计BOM)无法自动继承,数据需要转化,工艺只能被动等待,无法尽早进入到产品设计阶段和避免出现设计出来的东西无法生产的尴尬局面,即所谓的部门间“信息孤岛”现象依然存在。
(2)工艺设计手段落后。
工艺处理的还是二维数据,在研发阶段三维大行其道的形势下,传统的二维模式下的工艺已成功完成了它的历史使命,需要与时俱进,实现三维数字化工艺编制方法。
(3)缺乏完整的工艺信息管理。
工艺信息最常见的管理方式,主要通过文件和数据库存储。
有时候是部分文件、部分数据库,也有全文件、全数据库,比较混乱,数据的完整性比较差;数据的保密和安全没有保障;数据追溯性差,没有版本控制;工艺文档查询比较困难、费时。
(4)缺乏工艺资源管理和知识共享。
企业的各种工艺资源是一笔不可多得的财富,如工艺装备库、设备库等,可以进行资源重用,从而提高效率,降低成本,改进产品质量。
工艺设计是典型的复杂问题,涉及到的信息量和知识量相当庞大。
因此非常有必要积累或者总结提炼典型、复杂零件的工艺经验,形成工艺知识库,如工艺方法、工艺术语、典型工艺等,促进工艺知识的转化与再利用。
针对以上现状与问题(当然不止这些),在实施中结合Teamcenter制造功能进行拓展和开发,着重从企业设计到工艺再到生产的大局观抓起,最终实现统一设计和工艺平台,帮助企业应用部门理通、理顺数据,实现正确的数据,在正确的时间,以正确的方式传递给正确的人。
Teamcenter概述
Teamcenter是SIEMENS公司针对制造业提供的产品生命周期管理的解决方案,旨在建立一个数字化生产环境,并管理产品制造所需的相关数据。
成熟的CAD/PDM和ERP/MES系统已经在设计和生产中得到了验证,但是在CAD/PDM和ERP/MES之间缺少一个完整的解决方案来实现有效的衔接,Teamcenter制造工艺管理就是基于产品全生命周期Teamcenter主干在这二者之间的一个有效解决方案,是一座坚实而有力的桥梁。
Teamcenter造工艺管理解决方案不是将一些零散的应用程序进行简单的罗列,而是基于一个有效的核心,针对数字模型进行集中管理、协同和互操作,即以产品数据管理Teamcenter为平台将产品、工艺、工厂和资源进行有效的关联,同时保证了数据的一致、有效和重用。
这个集成的数据结构保证了快速、准确而安全地存取制造信息,同时可对制造工艺进行可视化、分析和优化,使生产企业各个部门和工作岗位间的信息流动能够顺利得到管理。
Teamcenter方案企业实施总体框架
基于笔者实施的企业设计部门采用三维NX设计软件,并成功应用Teamcenter作为产品数据管理平台,考虑到从产品设计到工艺规划再到产品制造过程的密切相关和数据流、信息流的传承与统一,提出以下总体框架(图1)。
在整个总体架构中必须考虑设计与工艺之间数据的继承,与ERP、MES的集成,在工艺规程的编制和工艺文件的格式输出等方面采用TeamcenterPublish输出3D工艺。
具体要点如下:
·工艺从Teamcenter中继承和提取设计产品结构EBOM和产品零组件属性,创建工艺结构,编制工艺规程,设定或关联与工艺/工序相关的工装、设备、车间、产品等信息;
·依据EBOM派生出相关联的制造BOM(MBOM),定义承制单位、协作单位、入库关系,生成工艺路线报表;
·利用TeamcenterPublish数字化动态发布、出版3D工艺相关文件;
·将制造BOM(MBOM)信息中含有的工艺路线、材料定额传递给ERP系统;
·MES系统在接到ERP的生产计划后,从Teamcenter中获得相关的工艺规程数据。
Teamcenter三维工艺设计关键技术实现
1结构化工艺设计
针对所实施企业统一Teamcenter平台下的设计产品BOM,利用其核心3PR(Product产品、
Process工艺、Plant工厂、Resource资源)理念,经过业务需求分析,分别需要不同的工艺类型来描述对象,用总工艺类型来管理所有的子工艺类型结构,通过BOMView反映这个零件所完成的工艺规程,子工艺类型有:
毛坯工艺、零件加工工艺、热处理工艺、表面处理工艺、注塑工艺、焊接工艺、冲压工艺等,子工艺下包含工序,工序又分下料工序、通用加工工序、数控工序和检验工序等。
在总工艺节点下创建子工艺节点,然后在子工艺节点下按需求创建加工工序节点,这些工艺和工序节点构建出工艺的BOP(BillofProcess,BOP)结构。
具体有2种操作方法,可以按照产品或者零件的特性手动逐步创建工艺结构,也可以从工艺资源库中选择某类型产品或零件的典型工艺作为模板自动创建出当前对象的工艺BOP结构,然后再做个别调整。
根据实施企业的工厂布局,可以将工厂、车间和设备模型定义出来,通过与工厂隶属管理,将设备与工厂布局关联,为设备赋予工厂布局属性,这样工厂结构就可以在工艺设计过程中被使用。
将子工艺节点关联工厂的车间区域,并在子工艺节点下的相关工序节点上指定工作中心或者工段上的设备(图2)。
以上描述的工艺、工序、工厂结构模型,都有各自对应的属性表,用来描述其自身的信息。
通过以上设计和工艺的3PR关联,二者之间会建立某种引用关系,无论对于设计人员还是工艺人员,都可以通过这种关系快速、有效、准确地定位到需要的对象。
2中间工序模型
结构化工艺创建出来之后,如何有效利用设计的3D模型才是真正的关键所在。
为此实施中提出了中间工序模型的概念。
之所以将中间工序模型单独列出来,主要原因是其对工艺模式的创新有直接意义。
中间工序模型是指产品从原材料形态到最终成品的加工过程中某个工序对应的模型。
对传统的工艺方式,工序面对的都是二维化图纸,无论是加工还是审阅理解都浪费大量的时间,另一方面,工序对应模型的不同状态,通常是由不同的设备和人员完成的,当一个零件从一个工作中心到另一个工作中心时,需要显示这种形态的变化,其对应的NC加工程序也是不相同的,因此利用中间工序模型来描述不同工序上零件的工序基准、加工内容、加工要求等生产现场方面,计量内容、计量要求等计量方面,检验内容方面,加工刀路仿真结果及数控加工程序的执行都起到事半功倍的作用。
图3描述了不同工序对应的形态及具体尺寸。
零件的加工将根据实际的需求分多步工序进行,每一工序具有其对应的模型状态。
零件加工各工序模型都应与零件模型相关,以实现零件模型的更新能自动传递到各加工工序模型。
同时各上下工序之间模型也应保持关联,以符合实际加工过程中毛坯模型在各工序之间的状态转换。
在形成的工序模型上,下一步需要进行的是产品制造信息(ProductManufactureInformation,PMI)的标注,用来指导生产。
当然在实际的工程应用中,设计部门的PMI标注需要传递给工艺部门,让工艺部门的技术人员可以重新利用和继承这些已经标注好的PMI,减少工艺编制的工作量。
设计模型的PMI被传递到了工序模型后,由工艺人员进行参考和新标注工艺信息,φ50.6是工艺人员在工序模型上标注的尺寸,(146.3±0.05)mm是设计模型PMI传递过来的尺寸。
所有的紫红色尺寸,工艺人员可以根据需要选择是否显示,但是不能对该尺寸进行修改(图4)。
3数字化出版发布
形象、鲜明的中间工序模型,如果能够出版发布,并且能够随着产品设计模型的变化,与其相关的文档可以动态自动更新,势必大大提高日常对工程文档生成、维护的效率。
利用Teamcenter的Publish可以将设计的3D模型以不同的表现形式体现出来。
因此在实施中,着重从以下几方面将动态的3D模型形象地描述出来。
(1)带有PMI标注(如尺寸公差等)的三维中间工序模型、爆炸图、标注和符号、导引线、剖面等;
(2)可以将出版的文件输出到不同格式(如XML/SGML)的编辑器中(例如FrameMaker、ArbortextEditor、XMLSpy);
(3)最终将出版物打包,供网页发布浏览。
通过捕捉数字化出版3D模型的不同状态或标注,所有的几何信息会被临时放在剪贴板上(实际上在Teamcenter是一种独立类型的数据集),在电子手册创建时可以分别填充到3D模型和爆炸图显示区,当双击3D模型区时,可以调用Teamcenter浏览器进行旋转,调整到合适位置退出时,电子手册上反映的就是最终调整的状态。
4工艺资源库
建立3D工艺处处离不开工艺资源,工艺资源库的积累是企业不可多得的财富。
在实施中,工艺资源主要指两部分,一部分是工艺知识库,如典型工艺、工艺参数库、切削参数库等,另一部分是底层制造资源,如设备、工装,包括通用的和专用的。
利用Teamcenter的In-Class分类管理功能,可以提供一个高度集成化的、易于掌握和使用的软件系统,使得工艺设计人员可以在计算机辅助技术的帮助下对制造资源与工艺知识进行有效管理,从而减少工艺设计时间、增加工艺设计准确性、提高设计效率。
分别从以下几点实现。
(1)分类的层级结构管理。
针对企业要管理的资源对象,根据企业零部件、工艺资源的分类标准(比如用于产品设计的零部件标准)进行管理,或用于工艺设计的工装夹具标准。
通过收集整理,提炼出企业的零部件、工艺资源分类标准,有以下几类:
制造资源库、辅助材料库、标准件库、典型工艺库和工艺知识库,当然每个大类下又有子类,对某个大类根据某个或几个特性进行细分。
(2)定义每一个类别的属性、属性的格式及属性的值列表。
针对每一个类别,定义其属性、属性格式以及属性的值列表,然后进行汇总,生成分类的属性字典。
在企业实施属性定义时,根据企业各种资源的类别细则,抽象出共同的属性,作为父类的属性,子类会继承父类,避免重复。
(3)绘制每一个类别的简图。
为了形象地描述每一个类的零部件、工艺资源的特征,针对每一个类别绘制了其类别简图,通过可以管理这些简图,方便以后进行查询。
(4)定义权限,包括分类的权限和分类标准的权限控制。
对于分类,为了避免由多人操作引起的混乱,实施时为实例分类和层级结构的定义设定了权限,以方便对分类管理的操作进行控制。
(5)制定分类层级结构和实例的维护规范。
分类的维护规范主要是用来规范零部件分类库的增加、减少和变更的行为,以实现专人管理避免引起混乱。
最终形成的样例见图5。
结束语
通过以上三维工艺设计的分析,本文提出了一种利用Teamcenter实现基于三维中间工序模型的新型工艺设计模式,即以设计BOM为核心,工艺知识和资源库为基础,围绕3PR结构化工艺建立继承设计模型和制造信息的中间工序模型,并用数字化动态出版的三维可视化形式给予工艺生产指导。
在吸收传统工艺设计方式优点的基础上,充分发挥工艺信息从产生、接受、维护、发送到再运用的组合功效,满足不同使用者对工艺信息和数据的共享、共用,从根本上为实现产品全生命周期内数字化设计、数字化制造、数字化检测和数字化装配提供了有效的方式。
在将工艺模型实现三维化之后,随着应用的不断深入,三维工艺装配仿真将成为继工艺设计之后需要研究的重点。
通过计算机仿真的技术手段模拟和预测产品的整个生产制造过程,从而验证设计和制造方案的可行性,尽早发现并解决潜在的问题。
这对于缩短新产品开发周期、提高产品质量、降低开发和生产成本,降低决策风险都是非常重要的。