改性酚醛树脂基体对摩擦材料摩擦磨损性能的影响.docx
《改性酚醛树脂基体对摩擦材料摩擦磨损性能的影响.docx》由会员分享,可在线阅读,更多相关《改性酚醛树脂基体对摩擦材料摩擦磨损性能的影响.docx(20页珍藏版)》请在冰豆网上搜索。
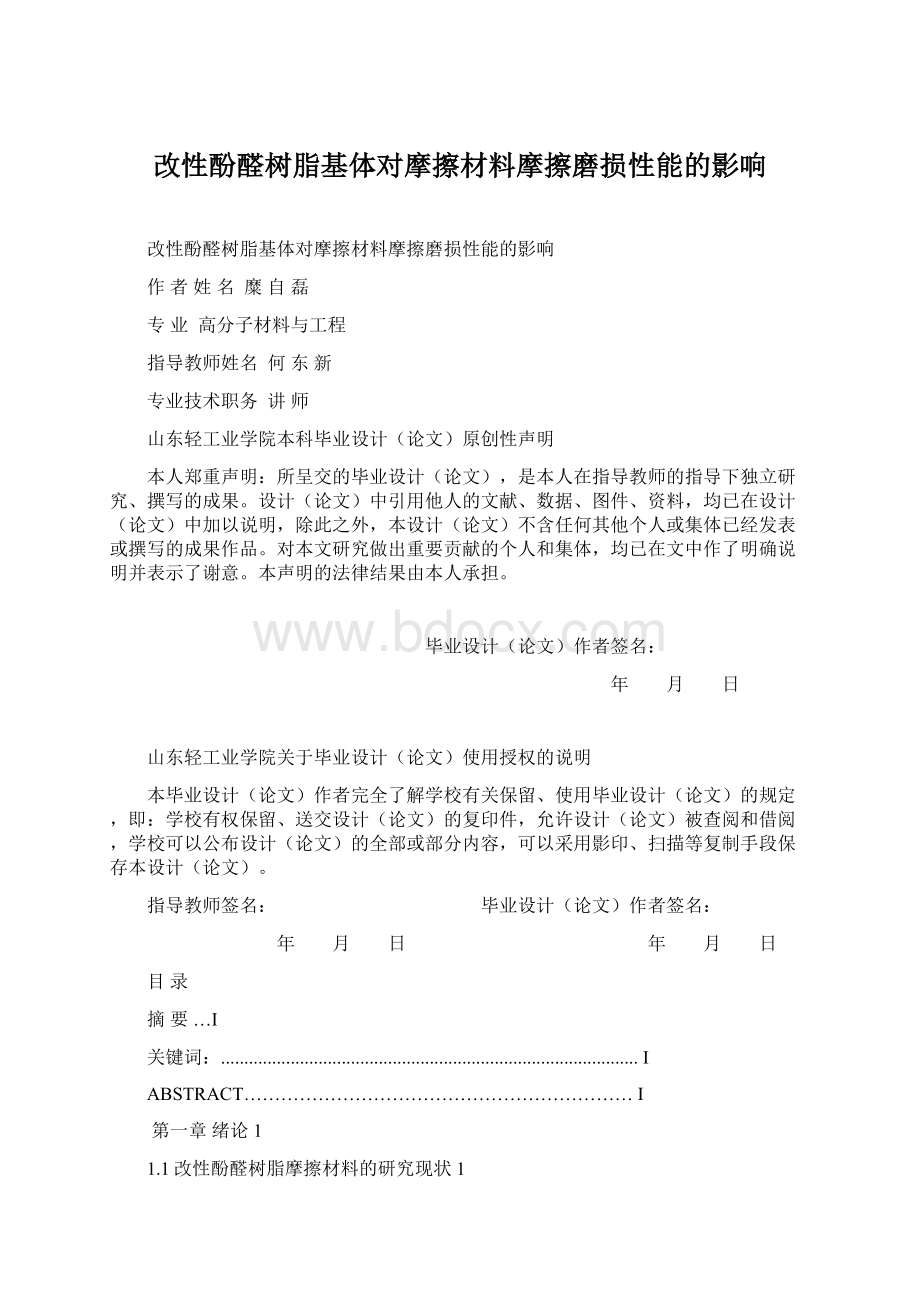
改性酚醛树脂基体对摩擦材料摩擦磨损性能的影响
改性酚醛树脂基体对摩擦材料摩擦磨损性能的影响
作者姓名糜自磊
专业高分子材料与工程
指导教师姓名何东新
专业技术职务讲师
山东轻工业学院本科毕业设计(论文)原创性声明
本人郑重声明:
所呈交的毕业设计(论文),是本人在指导教师的指导下独立研究、撰写的成果。
设计(论文)中引用他人的文献、数据、图件、资料,均已在设计(论文)中加以说明,除此之外,本设计(论文)不含任何其他个人或集体已经发表或撰写的成果作品。
对本文研究做出重要贡献的个人和集体,均已在文中作了明确说明并表示了谢意。
本声明的法律结果由本人承担。
毕业设计(论文)作者签名:
年 月 日
山东轻工业学院关于毕业设计(论文)使用授权的说明
本毕业设计(论文)作者完全了解学校有关保留、使用毕业设计(论文)的规定,即:
学校有权保留、送交设计(论文)的复印件,允许设计(论文)被查阅和借阅,学校可以公布设计(论文)的全部或部分内容,可以采用影印、扫描等复制手段保存本设计(论文)。
指导教师签名:
毕业设计(论文)作者签名:
年 月 日 年 月 日
目录
摘要…Ⅰ
关键词:
..........................................................................................Ⅰ
ABSTRACT………………………………………………………Ⅰ
第一章绪论1
1.1改性酚醛树脂摩擦材料的研究现状1
1.2改性酚醛树脂的改性方法1
1.2.1化学改性的酚醛树脂1
1.2.2物理改性的酚醛树脂3
1.3树脂基摩擦材料的组成4
1.4摩擦材料的摩擦磨损机理6
1.5本文的研究内容与目的6
第二章实验7
2.1试验设备及原料7
2.1.1试验设备7
2.1.2实验原料7
2.2样品制备7
2.2.1配料7
2.2.2混料8
2.2.3模压制备样品8
2.3摩擦试验方法及数据处理8
2.3.1摩擦试验方法8
2.3.2数据处理9
第三章试验结果及分析11
3.1试样摩擦系数实验结果的分析11
3.2试样磨损率实验结果的分析13
第四章结论16
参考文献:
17
摘要
酚醛树脂是摩擦材料中最重要的基体材料,但是纯酚醛树脂存在脆性大、耐热性不足等缺陷,因此要用做摩擦材料就必须要对酚醛树脂进行改性以提高其韧性和耐热性。
本试验就是用改性的酚醛树脂做粘结剂,用“干法”热压成型制备出标准摩擦片。
利用D-MS摩擦试验机研究了改性酚醛树脂含量对摩擦材料摩擦磨损性能的影响。
改性酚醛树脂基体对摩擦材料的摩擦磨损性能影响显著。
随着树脂基体含量的增加,摩擦系数逐渐减小,磨损率逐渐增大。
关键词:
摩擦材料酚醛树脂摩擦系数磨损率含量
ABSTRACT
Phenoficresinisoneofthemostimportantmatrixmaterialsforfictionmaterials,butpurephenolicresinhassomedefectssuchasbigbrittleness,lackofheat—resistance.Soitisnecessaryforphenolicresintobemodifiedtoimproveitstoughnessandbeat.resistancewhenitisusedforamatrixof~ictionmaterials.Inthepaper,themodifiedphenolicresinisusedasabinder.Thenormalfrictionalsampleswerepreparedbymoldingpressuremethod.TheeffectsofthemodifiedphenolicresincontentwerestudiedbyD—MSfrictiontesteronthefrictionandwearpropeaiesoffrictionmaterial.Itisshowedthatthemodifiedphenolicresinmatrixhassignificantinfluenceontribologicalpropertyofthefrictionmaterial.Thefrictioncoefficientisreduced.andthewearrateisincreasedwhentheresincontentisincreased.
KEYWORDS:
Frictionmaterial;Phenolicresin;Frictioncoefficient;Wearrate;Content
第一章绪论
1.1改性酚醛树脂摩擦材料的研究现状
酚醛树脂(PF)是世界上最早实现工业化的合成树脂,迄今已有近百午的历史。
由于其原料易得,价格低廉,生产工艺和设备简单,具有优异的机械性、耐寒性、电绝缘性、尺寸稳定性、成型加工性、阻燃性及烟雾性,因此,它已成为工业部门不可缺少的材料,具有一定的用途。
但是,PF结构上的薄弱环节是酚羟基和亚甲基容易氧化,使其耐热性受到影响。
随着工业的不断发展,特别是各种车辆和机械使用条件及航空、航天和其他国防尖端技术的发展,对高性能摩擦材料提出了新的要求,如较高的热分解温度、良好的热恢复性能、足够的摩擦系数、较好的耐磨性能及较低的噪音等。
纯的PF作为摩擦材料用于高级轿车、摩托车刹车片和离合器片的基材,均不能满足要求。
传统未改性的PF脆性大,韧性差,耐热性不足,限制了许多工业的开发。
因此,对PF进行改性,提高其韧性及耐热性是高性能PF的发展方向[1]。
1.2改性酚醛树脂的改性方法
树脂基摩擦材料主要由树脂基体、纤维增强材料、摩擦性能调节剂及填料4大类组元混合后经热压而成。
树脂基体是摩擦材料中的一个重要组元,同时也是摩擦材料中化学性能、热稳定性最差的组元,它的性能直接影响摩擦材料的热衰退性能、恢复性能、摩擦性能和机械性能[2]。
随着各种车辆和机械使用状况条件的提高,对摩擦材料的热性能和制动力矩的稳定性要求不断提高,从而对树脂基体提出了新的要求。
因此树脂必须有合适的模量,以保证在摩擦时有较大的接触面积,从而使摩擦副对偶在工作时稳定而不易产生振动;树脂必须有一定的耐热性以保证次摩擦层有足够的强度;树脂分解后的残留物必须有一定的摩擦性
能,以保证稳定的摩擦系数;树脂固化后必须有较低的硬度,以防止制动噪音[3]。
由于酚醛树脂具有良好的耐热性能和机械性能以及原料易得,价格便宜,工艺及生产设备简单等优点,因而一直是生产摩擦材料的最基本树脂成分,应用于摩擦材料业有70余年的历史[4]。
但是,纯酚醛树脂使摩擦材料硬度过高,脆性大,耐热极限温度约为2500℃。
当超过3000℃时,热分解现象相当严重,导致摩擦性能显著下降。
因此,对酚醛树脂进行改性,提高其耐热性和韧性一直是人们研究的重要课题.改性包括化学改性和物理改性[5]。
1.2.1化学改性的酚醛树脂
酚醛树脂的化学结构式为:
造成酚醛树脂性能不足的主要原因是:
①树脂中的苯酚含有次甲基,这个基团是刚性结构,导致树脂硬而脆、冲击强度降低。
②在酚醛的分子结构上缺乏粘结力极强的基团,使树脂的枯结性差。
③树脂分子中酚羟基是一个强极性基团,极易吸水,导致制品性脆、强度降低,同时由于酚羟基是弱键连接,在受热或紫外光作用下,易生成醌或其它结构,其耐热性差[6]。
酚醛树脂的化学改性主要是指除苯酚、甲醛外,还加入能参与缩聚反应的组分,或者加入能与酚醛树脂大分子进行化学反应的组分。
从缩聚机理及酚醛树脂的反应机理来看,改性途径有两个:
①封锁酚羟基。
树脂分子中留下的酚羟基容易吸水,且耐热性也不好,因而封锁
酚羟基可改善酚醛树脂的耐热性能。
②引进其它组分。
通过其它组分分隔包围酚羟基,从而达到改变固化速度、降低吸水性、提高性能的目的[7]。
一般来说,若改性组分有较柔软的长链结构,往往具有增韧改性效果;若能形成稳定的环状结构或引入高键能结构,以及减小易氧化的酚羟基、亚甲基的比例,则往往起到提高耐热性的效果:
而某些极性基团的引入,可改善粘结性。
通过化学改性,在酚醛树脂分子结构中引人其它成分,改进酚醛树脂的力学性能、耐高温性、耐磨性、韧性等,可使其比传统酚醛树脂更适用于作摩擦材料[8]。
(1)聚乙烯醇缩醛改性酚醛树脂
传统酚醛树脂中含有酚羟基,这种基团容易吸水,是造成树脂强度不高、耐热性较差的主要原因,通过聚乙烯醇缩醛的改性,分割和包围了酚羟基,从而使其力学性能提高,韧性增加,但其耐热性下降,只在早期的摩擦材料中使用过。
(2)环氧改性酚醛树脂
环氧改性的酚醛树脂曾被试用于石棉摩擦材料,它使材料的强度提高很多。
可以用作摩擦材料基体树脂,适用于车速不是很高的轻型车。
(3)油改性酚醛树脂
酚醛树脂中加入豆油、亚麻油、蓖麻油和桐油等可制成油改性酚醛树脂,据日本文献介绍,它最适用于旅行车用的制动片[9]。
(4)腰果壳油改性酚醛树脂
腰果壳油改性酚醛树脂具有如下特点:
①高温下有优良的柔性:
②与橡胶的相容性较好;③侧链的影响使之具有优越的耐酸、耐碱性。
用这种改性树脂制成的摩擦材料,具有较好的摩擦特性,摩擦系数稳定,磨损小。
美国、英国、前苏联均广泛采用腰果壳油改性酚醛树脂。
由于我国腰果壳资源有限,所以对这种改性树脂使用较少。
(5)二甲苯改性酚醛树脂
将二甲苯与甲醛在催化剂作用下的反应产物与苯酚、甲醛反应,生成二甲苯改性的酚醛树脂。
由于二甲苯的加入,分隔了酚羟基,使树脂的耐热性提高,其热分解温度在350℃以上,40℃以前的热伸长率小于10%,比不改性的树脂具有更稳定摩擦系数,国外曾报道,这种树脂是用于摩擦材料的主要品种之一。
目前国内已有该种树脂生产,但用于摩擦材料的报道还不多。
(6)尼龙改性酚醛树脂
将尼龙66在甲酸中溶解后,加人甲醛生成羟甲基尼龙,再与苯酚、甲醛在催化剂的作用下,最终生成尼龙改性酚醛树脂。
用作摩擦材料基体树脂时可以使摩擦材料有较高的强度,且摩擦特性保持较长,但其价格也较高。
(7)硼改性酚醛树脂
用苯酚、双酚A与硼酸或硼砂及甲醛,于氢氧化钠催化下制得硼改性酚醛树脂。
由于B—0键键能很高,树脂的耐热性,特别是瞬间耐高温性大为提高,双酚A硼酚醛树脂在250℃时失重率4.2%,300℃为4.6%。
用双酚A合成的硼改性酚醛树脂的耐水性比用苯酚合成的有所改善。
硼改性酚醛树脂降解时碳化率高,生成的碳化硼呈蜂窝状,有利于热的扩散,故表现出较好的热稳定性,适合于摩擦材料对基体树脂的要求,温度从150℃升高到300℃,摩擦系数从0.35变化到O.37,极值为0.40(250℃时)[10-11]。
但由于这种材料价格高,在我国还未实用。
(8)芳烷基醚酚醛树脂
以二甲氧基对二甲苯与苯酚、甲醛为原料,可制得芳烷基醚酚醛树脂。
这种芳烃改性的酚醛树脂具有酚醛树脂易于加工的特点。
由于封锁了酚羟基,使树脂的耐热性和耐氧化性更为稳定,用这种树脂制成的玻璃钢在275℃暴露1000h或300℃暴露300h后弯曲强度仍保留50%上[12]我国曾将该种树脂用于摩擦材料,试验效果良好,但价格较高。
(9)芳醇改性酚醛树脂
芳醇改性酚醛树脂是由中国兵器工业第五三研究所最新研制成功的新型酚醛树脂,其突出的特点是耐热性好,热分解温度可达450℃,400℃失重率为5.2%。
470℃失重率为4.4%。
这种树脂游离酚含量低,试验室产品小于1%。
工业化产品小于2%,可有效避免制品热膨胀现象的发生[13]。
制成的离音器摩擦片性能指标全部高于国家规定的指标,超速破坏强度达到1320r/rain,在国内处于较高水平:
制成的盘式制动片摩擦系数稳定。
磨损率小,黏结强度高,制动时无噪音。
另外,该树脂还具有良好的成型工艺性:
目前这种树脂已在多种车型的制动片上应用。
(10)其它化学改性酚醛树脂
还有一些化合物可以通过化学反应对酚醛树脂进行改性。
据报道,前苏联曾用含松香30%改性酚醛树脂制成摩擦材料,用于重载荷工作场合,摩擦系数稳定可经受1000℃的摩擦温度。
还有用三聚氰氨改性酚醛树脂制成摩擦材料,它具有高的摩擦系数和良好的耐磨性。
此外还有苯胺改性酚醛树脂,甲酚、二甲酚改性酚醛树脂。
1.2.2物理改性的酚醛树脂
酚醛树脂的物理改性是指用某些聚合物与酚醛树脂共混。
改性效果受两组分化学结构、分子量及其分布、聚合物之间相容性、共混物形态结构、共混比例以及操作工艺等多方面因素的影响。
若掺入酚醛树脂的聚合物具有卓越的韧性、良好的耐热性并且能与酚醛树脂有适中的热力学相容性,使共混物呈亚微观的均匀分散形态,则该种共混改性的酚醛树脂才能用于摩擦材料,获得理想的摩擦性能。
以适量柔软的橡胶与刚性硬质的树脂进行共混改性,构成所谓“高分子合金",是解决摩擦材料基体兼有高耐热性、优异耐磨性和较低弹性模量的有效手段[14]。
适合与树脂共混的橡胶主要有丁腈橡胶、丁苯橡胶、丁二烯橡胶和氯丁橡胶等,尤其以丁腈橡胶、丁苯橡胶最为常见。
丁腈橡胶的溶解度参数(9.3—9.9)与酚醛树脂的溶解度参数(10.5)相近,两者共混,有较好的相容性,可起到增韧效果,同时还能显著提高耐热性。
丁腈橡胶有块状固体、液体和粉末3种形态,均可用作酚醛树脂改性剂。
块状固体丁腈橡胶增韧酚醛树脂用密炼法进行共混,可克服开炼法工艺的缺点和不足。
在密炼机中,物料受强烈的捏合、挤压和剪切作用,摩擦产生的大量热量使丁腈橡胶和酚醛树脂很快软化、熔融,达到均匀分散和塑化。
液体丁腈橡胶可在酚醛树脂缩聚反应过程中加入,大大简化了共混的工艺。
通过电镜观察,得知该共混体系形态结构为海岛结构,即酚醛树脂构成连续相,而丁腈橡胶形成分散相,这种形态
结构保证材料的抗冲强度有显著提高,硬度下降,且可使摩擦材料的整体耐热性大幅度提高[15]。
丁苯橡胶的溶解度参数为8.48,与酚醛树脂的溶解度参数相差很大,两者相容性不良。
当用一定量的丙烯酸参与共聚,所得的羧基丁苯胶乳,其极性明显增加,与酚醛树脂共混时的相容性提高。
为使胶乳中的橡胶微粒高度分散在树脂中,达到橡胶与树脂充分共混,必须在酚醛树脂缩聚反应期间,在严格控制反应条件下,加入合成胶乳,以使之不破乳[16]。
用此种改性酚醛树脂作为摩擦材料粘合剂,可降低其摩擦制品的硬度,改善与对偶的贴合性,增大有效接触面积,降低了由于振动产生的制动噪音,摩擦性能也很稳定。
近代研究表明,橡胶增韧作用和银纹化有关。
正是橡胶的引入,引发并控制了银纹的增长,从而达到均衡载荷的作用。
因为橡胶粒子起着应力集中体的作用,促使银纹产生,吸收大量冲击能量。
银纹的产生,要求橡胶玻璃化的温度尽可能低,同时,为阻止银纹增长并发展成裂纹,还要求橡胶分散相粒子有一定的大小。
合适的橡胶粒子应在0.2—1×10-6之间[17]。
综上所述,摩擦材料用酚醛树脂主要通过化学改性和物理改性两种途径来改善其耐热性和韧性。
提高耐热性主要是提高树脂结构中芳杂环含量或引入其它聚合物的结构单元:
提高韧性主要是外加柔韧性聚合物或在树脂结构中引入柔性结构单元[18-19]。
显然,提高耐热性和提高韧性所采取的方法是相互矛盾的,在提高耐热的同时,韧性会受到影响,反之亦然。
因此,在摩擦材料中选用高耐热性的改性酚醛树脂,同时与橡胶共混以提高韧性将是今后的发展方[20]。
1.3树脂基摩擦材料的组成
摩擦材料主要由树脂基体、纤维增强材料、摩擦性能调节剂及填料四大类原材料混合后经热压而成。
(1)树脂基体
树脂基体在摩擦材料中起着最关键的作用。
树脂基体在摩擦材料起粘结剂作用,是摩擦材料中化学性能、热稳定性能最差的组元,其性能直接影响摩擦材料的热衰退性能、恢复性能和机械性能16I,树脂不仅要在很大的温度范围内保持对纤维和各种填料的黏结力,稳定摩擦系数和磨损量,防止材料崩溃,而且其受热分解炭化的产物也要其有一定的强度和摩擦性能,这样当制动功率较高导致摩擦表面树脂出现降解时,制动片的摩擦特性不会出现太大的衰退。
若单从耐热性考虑,有许多高耐热性树脂可供选择,如聚酰亚胺、聚醚砜、聚醚砜酮等,但它们的成型温度太高(300℃以上),价格也较贵,因此,从耐热性、成本、工艺性等方面综合考虑,本试验中确定树脂基体选用酚醛树脂。
酚醛树脂以其较好的耐热性能被最早作为汽车制动片的基体树脂用于摩擦材料。
随着汽车车速的提高,汽车制动片单位面积吸收的能量成倍增加,要求在较小的踏板制动力条件下获得更为稳定的制动效应,从而促使汽车制动系统向前盘后鼓的结构格局发展。
由于盘式结构制动片的表面积为鼓式片的1/6~1/4,单位面积吸收功相应为鼓式片的4~6倍[21],表面温度可达400℃以上[22]。
传统酚醛树脂的耐高温性能不能满足要求,而且还存在伸长率低、脆性大、制成的摩擦材料硬度高、冲击强度低、易生成硬而脆的摩擦残留表面、产生热衰退、摩擦性能不稳定、以及摩擦材料本身的界面已产生应力开裂和界面裂缝等问题。
为了解决这些问题,所以人们对酚醛树脂进行改性,并且取得了很大的进展,上面关于改性已详细介绍。
(2)增强纤维
增强纤维在摩擦材料中起骨架作用。
选择增强纤维的依据是:
耐热性高,力学性能好,高温下不熔融,价格低,来源广。
尽管石棉具有许多优异特性,国内外对石棉的危害性也存在着许多争议,但一方面为了符合国家政策,另一方面由于石棉是含结晶水的硅酸盐矿物,在较高的制动功率下当摩擦面温度达到使石棉脱去结晶水的温度时,石棉将失去增强效果,脱除的水气还会破坏闸片的强度和摩擦性能,所以本论文所研究的摩擦材料中不添加石棉。
而一些耐热性很高的高科技有机纤维,如聚苯并咪唑纤维、聚问苯二甲酰间苯二胺纤维等,国内尚未能大规模生产,价格高,来源困难,因此在本论文中不采用。
碳纤维是一种高科技纤维,其含碳量在95%以上,高温下不熔不融,具有优异韵耐热链,很高的拉伸强度和拉伸模量,储热能力大,特别是在高温下具有比低温下更优越的力学性能和摩擦特性。
碳纤维作为制动摩擦材料的重要缝分,在国外已有成功应用的先例,因此本论文中选择碳纤维作为增强纤维。
长期以来,限制碳纤维在民用领域应用的关键问题是其昂贵的价格,近几年由于国内外几大炭纤维生产厂的生产规模迅速扩大,技术日趋成熟,特别是我国自己也拥有生产能力,使得国内碳纤维的价格急剧下降,为碳纤维在民用领域的应用扫清了障碍。
但是,在摩擦材料中单纯使用碳纤维作为增强材料还存在几个问题:
一是与其他原材料相比,碳纤维的相对价格仍然较高,导致摩擦材料的生产成本增加,二是碳纤维与铸铁材料配副的摩擦系数较低,三是若碳纤维用量太大则混料时易结团,导致混料均,所以碳纤维的用量不宜过多,但用量太少又不能保证纤维的增强作用,所以,为了在摩擦材料中有足够比例的纤维以形成适当的骨架结构,以及优化性能、降低成本,需要加入其它种类的纤维以提高摩擦材料的摩擦系数和改善工艺性,即利溺多种纤维混杂的混杂效应[23]。
通过对比各种纤维的特点,本次设计选择了钢纤维与碳纤维一起作为增强纤维。
钢纤维具有优良的耐热性和导热性,韧性好,经表面处理后与树脂的结合良好,混料时易分散,硬度较高,可提高摩擦系数并且价格较低,其缺点是比重大,易生锈,加入量过多时易产生制动火花和啸叫;并具有适中的摩擦系数,但其韧性、导热性较差。
通过将这两种纤维合理搭配,在材料中混杂形成无规交叉网络,发挥炭纤维减摩质轻,金属纤维高强导热的特点,可达到扬长避短、互为补充的效果,可以从亚微观结构上保证研制的材料有良好的机械性能和耐热性能。
各种纤维的相对比例和总用梁量则要通过工艺试验、力学性能试验和摩擦性能试验来确定。
(3)填料
填料是摩擦材料中不可缺少的组分,包括多种摩擦性能调节剂和配合剂。
其主要作用是调节摩擦材料的摩擦磨损性能,以更好地满足各种工况条件下制动和传动功能的要求。
此外,还常常通过添加不同的填料来控制、调节摩擦材料制品的硬度和结构密实度,以改善制动噪音、降低制品成本等[24]。
填料的加入对聚合物基复合材料的宏观摩擦学性能影响很大,填料的加入会不同程度地改善摩擦学性能。
用于填料的种类很多,如金属粉末、矿物质、氧化物、云母、石墨、固体润滑物以及盐类等。
本次实验选用的填料为轻质碳酸钙、高岭土、硅灰石、重晶石和石墨。
轻质碳酸钙和重晶石在摩擦材料中作为增量性填料,其作用主要是降低成本、稳定摩擦系数,要求它们的硬度适中,以与钢铁相近为宣,化学性质稳定,在制动过程所能达到的温度范围内不发生分解、脱水等可能导致材料破坏的反应。
选择摩擦性能调节剂的主要依据是硬度和化学稳定性。
对增摩性摩擦性能调节剂,选用一些高硬度的无机粉末,硅灰石具备这些性能,而且价格也很便宜,但用量要少粒径要细,以免造成严重磨损。
石墨在摩擦材料中是作为减摩性摩擦性能调节剂使用,具有润滑、改善热衰退、减少制动噪声的效果。
高岭土在摩擦材料中作为低成本填料使用[25]。
1.4摩擦材料的摩擦磨损机理
关于制动摩擦副的摩擦磨损机理研究很多,但由于摩擦材料中成分和组织以及材料性能的复杂性,迄今为止还没有一个公认的理论能解释摩擦过程中摩擦磨损现象的机理。
例如在低负荷和低温下,主要磨损机理既有认为是磨料磨损的,也有认为是粘着磨损或疲劳磨损的。
但对用高分子树脂作为粘合剂的摩擦材料,在摩擦过程界面转移膜(摩擦转移膜)的形成及其在摩擦过程中的减磨作用和高温下的有机物分解造成热磨损方面的认识是比较一致的。
对于摩擦界面转移膜的形成,一般认为,新制动摩擦副在初始阶段的跑合过程中,粗糙表面的微凸峰相互接触发生塑性变形和断裂,断裂形成的磨屑在界面压力和摩擦力作用下,由于有机成分较多而相互粘结,并粘结于两摩擦副表面。
因为界面膜自身内部的粘结力大于其与两表面的粘结力,在摩擦作用下会沿其中部面剪开而粘结在两摩擦体表面,形成摩擦转移膜,转移膜的成分以有机物和填料及金属元素组成。
随着转移膜的不断形成,两摩擦表面的粗糙度降低直到形成稳定的转移膜。
在这一过程中摩擦系数变化较大,而磨损率由大到小。
一般认为,这段过程的磨损机理为磨料磨损。
在随后的过程中,转移膜的形成、剪切处于动态平衡,在温度不太高的情形下,摩擦系数和磨损都处于相对稳定的状态。
随着温度的增高,有机物发生降解从而使摩擦材料表面的无机填料成分增加,转移膜与摩擦材料的粘结程度降低,转移膜破裂丽引起严重的热磨损[26]。
对于一些纤维增强的摩擦材料,有人认为纤维的加入有利于转移膜的形成并增加其稳定性,从而起到减磨作用。
而对铝基复合材料制动盘,转移膜在其上形成的可能性和稳定性较铸铁高,故有人认为铝基复合材料中的硬颗粒起到了机械夹挤的用。
摩擦材料的表层成分、性质和结构对其摩擦磨损起着决定性作用。
目前关于表面结构主要有两种模型,它们都是由表至里地将表层划分为五层,对三、四、五(即靠近基体的三层)的认识相同,分别为裂纹形成层、应变层和基体。
而对一、二层的认识不同,一种认为一层是由分解和部分碳化且包含有微裂纹的树脂组成,二层是树脂的降解层;另一种模型认为一层是吸附层,二层是金属化层,这可能是由于材质和试验条件的不同所致。
也有人将摩擦表层划分为四层,即表面工作层、疏松层、变形强纯层和基体。
由于对磨损机理的认识不尽相同,且各种磨损机理都未能完全地解释各种材质和工况下的摩