提钒转炉供氧制度的设计本科 大学毕业设计.docx
《提钒转炉供氧制度的设计本科 大学毕业设计.docx》由会员分享,可在线阅读,更多相关《提钒转炉供氧制度的设计本科 大学毕业设计.docx(36页珍藏版)》请在冰豆网上搜索。
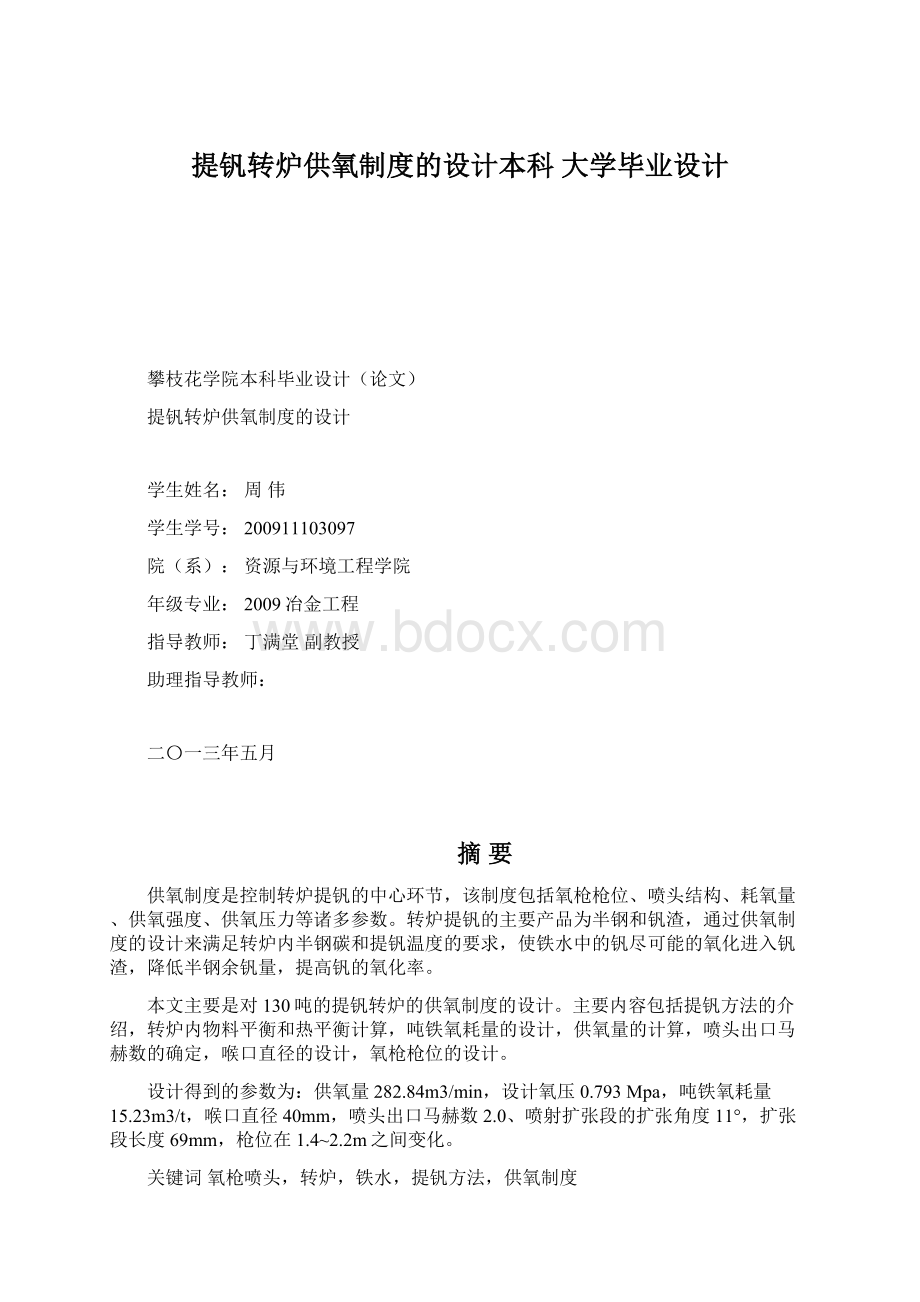
提钒转炉供氧制度的设计本科大学毕业设计
攀枝花学院本科毕业设计(论文)
提钒转炉供氧制度的设计
学生姓名:
周伟
学生学号:
200911103097
院(系):
资源与环境工程学院
年级专业:
2009冶金工程
指导教师:
丁满堂副教授
助理指导教师:
二〇一三年五月
摘要
供氧制度是控制转炉提钒的中心环节,该制度包括氧枪枪位、喷头结构、耗氧量、供氧强度、供氧压力等诸多参数。
转炉提钒的主要产品为半钢和钒渣,通过供氧制度的设计来满足转炉内半钢碳和提钒温度的要求,使铁水中的钒尽可能的氧化进入钒渣,降低半钢余钒量,提高钒的氧化率。
本文主要是对130吨的提钒转炉的供氧制度的设计。
主要内容包括提钒方法的介绍,转炉内物料平衡和热平衡计算,吨铁氧耗量的设计,供氧量的计算,喷头出口马赫数的确定,喉口直径的设计,氧枪枪位的设计。
设计得到的参数为:
供氧量282.84m3/min,设计氧压0.793Mpa,吨铁氧耗量15.23m3/t,喉口直径40mm,喷头出口马赫数2.0、喷射扩张段的扩张角度11°,扩张段长度69mm,枪位在1.4~2.2m之间变化。
关键词氧枪喷头,转炉,铁水,提钒方法,供氧制度
ABSTRACT
Oxygensupplysystemisthecentrallinktocontroltheconverterofvanadiumextraction,thesystemincludesthelanceposition,thenozzlestructure,oxygenconsumption,oxygensupplyintensity,oxygenpressureandotherparameters.Themainproductsoftheconverterofvanadiumextractionaresteelandvanadiumslag,throughthedesignofoxygensupplysystemtomeettherequirementsofthecarboncontentofthesteelandthetemperatureofvanadiumextractionintheconverter,thevanadiumisoxidizedintothevanadiumslagasmuchaspossibleforincreasingvanadiumoxidationrate.Atthesametime,reducingthevanadiumcontentwhichexistinthesemisteel,.
Themaincontentofthispaperistodesigntheoxygensupplysystemof130tonsofvanadiumextractionconverter.Themaincontentsincludeanalysingtheperformanceofthevanadiumslag,thecalculationofmaterialbalanceandheatbalanceintheconverter,designtheoxygenconsumptionofpertonhotmetal,thecalculationofthetotaloxygensupply,selectingthefigureofMahernumberinthenozzleexit,thedesignofthethroatdiameter,thedesignaboutthepositionoftheoxygenlance.
Thedesignparameters:
theamountofoxygenis282.84m3,thedesignoxygenpressureis0.793MPa,theoxygenconsumptionofpertonhotmetalis15.23m3/t,throatdiameter40mm,thenozzleexitMachnumberis2.0,thejetexpansionsegmentoftheexpansionangleis11°,theexpansionofthelengthis69mm,thepositionofthelancechangesbetween1.4to2.0m.
KeywordsOxygenlancenozzle,Converter,Hotmetal,Vanadiumextractionmethod,Oxygensupplysystem
前言
钒属贵重金属,应用范围广,经济价值高,是一种极为重要的工业原料,可广泛应用于钢铁、化工、航空航天、电子工业、生物和农业等领域。
钒在自然界中的分布很广,约占地壳质量的0.02%;但分布极为分散,一般共生在其它金属矿中,因此钒通常作为副产品来回收。
目前钒钛磁铁矿是钒的主要矿物资源,该矿物的主要元素是铁、钒和钛,先将矿石冶炼成铁水后,再对铁水氧化吹炼得到钒渣,钒渣是生产钒及其产品的主要原料。
国内生产钒渣的工厂主要有承德新新钒钛股份有限公司和攀枝花钢铁集团股份有限公司。
本文主要是对130吨的提钒转炉的供氧制度的设计。
主要内容包括钒渣性能的分析,转炉内物料平衡和热平衡计算,吨铁氧耗量的设计,喷头供氧量的计算、喷头出口马赫数的确定、喉口直径的设计,氧枪枪位的设计。
1钒的生产概述
1.1钒的提取方法
1.1.1含钒磁铁矿直接提钒
从含钒磁铁矿石中直接提取钒的方法也称为湿法提钒。
矿石中V2O5含量为1~2%,芒硝与破碎精选的精矿粉混合后制成球,在1200℃的高温下焙烧,钒转化为可溶性钒酸钠。
加入硫酸后,钒酸钠反应转化成不溶于水的V2O5。
经过沉淀过滤后,所得的产物即为提钒产品。
1.1.2钒渣提钒
钒渣提钒是将钒钛磁铁矿经过高炉或电炉冶炼后得到含钒铁水,含钒铁水装入转炉、摇包或铁水包内,并向其中通入氧化性气体,使铁水中的钒氧化后得到钒渣。
钒渣提钒也称火法提钒,提取钒渣后的铁水称为半钢,半钢还可进一步冶炼成钢产品[1]。
1.1.3其他提钒方法
钾钒铀矿中提钒,这种矿石主要是生产金属铀,副产品为V2O5。
石油及其加工的产物、碳质页岩中都含有钒,重油、石油焦及其燃烧灰渣可使钒得到富集,也可直接从石油或石油加工产物中提钒[9],其中V2O5的质量分数为5~35%。
含钒的磷酸盐矿、含钒的粘土矿中也可以提钒。
而最近几十年中还发现可以从石煤中提钒,我国石煤资源丰富,可开采量大,但石煤中钒的品味相差较大,一般为0.13~1.00%,品味低于0.5%的占60%,提钒难度较大[21]。
1.2含钒铁水吹炼提钒
对
为0.4~0.6%的含钒铁水,要尽可能的将铁水中的钒氧化进入炉渣,铁的损耗要降至最低,即半钢的收得率要高,以降低钒渣生产成本,并且提钒后的半钢碳含量要尽量高,以满足下一步炼钢的要求[3]。
1.2.1转炉提钒的原理
转炉提钒是利用选择性氧化的原理,通过氧枪喷射出的高速氧射流对转炉中的含钒铁水进行搅拌,把铁水中的钒氧化成稳定的钒氧化物,以制取钒渣的一种物理化学反应过程。
在反应过程中,通过加入冷却剂控制熔池温度在碳钒转化温度以下,达到“去钒保碳”的目的[2]。
向转炉中供氧后,铁水中的Fe被大量氧化,Si、Mn、V和少量的C也同时被氧化。
钒可以氧化成V2O、VO、V2O3、V2O4、V2O5等化合物,其中V2O3和V2O5最稳定。
反应式为:
2[V]+3/2{O2}=(V2O3)式(1.1)
2[V]+3(FeO)=(V2O3)+3[Fe]式(1.2)
2[V]+5{O2}=(V2O5)式(1.3)
2[V]+5(FeO)=(V2O5)+5[Fe]式(1.4)
为得到高品位的钒渣,要最大限度的将铁水中的钒氧化进入炉渣,提钒后铁水中的钒的含量要尽量的低。
铁水中元素的氧化放出大量的热量使炉温升高,而炉温升高不利于钒的氧化。
因此要求转化温度越低,半钢中残余钒含量就越低,才能得到高品位的钒渣。
1.3氧气顶吹转炉吹炼提钒
氧气顶吹转炉吹炼提钒是从转炉顶部吹入氧射流,使铁水中的钒被氧化提钒的方法。
氧气顶吹转炉吹炼提钒可分为同炉单渣法、同炉双渣法与转炉-转炉双联法三种方法。
(1)同炉单渣法是在一座转炉内,加入造渣剂后,吹炼含钒铁水,获得高氧化钙低品位的钒渣。
(2)同炉双渣法是在同一座转炉内,不加入碱性造渣材料,而仅加入冷却剂进行吹炼,当硅锰钒等元素氧化结束,碳焰刚露头时立刻停氧,倒出钒渣,然后再向该炉内加入造渣材料造渣、降碳去磷硫继续吹炼成钢。
一般前期称提钒期,而后期称炼钢期。
(3)转炉-转炉双联法是用两座转炉吹炼,一座为提钒炉仅加冷却剂提钒,获得钒渣和含碳的半成品半钢,再将半钢兑入另一座炼钢转炉内,加入造渣材料等降碳去磷去硫吹炼成钢。
1.3.1铁水成分的影响
(1)铁水中钒含量的高低,对钒渣中
含量有直接影响。
如吹炼
=0.20%的铁水,渣中
只有10%;而吹炼
=0.40%的铁水,渣中
为16%~20%。
(2)铁水中的Si、Mn、Ti等元素的氧化如图1.1所示,这些元素的氧化会放出大量的热量使熔池的温度升高,为碳的快速氧化提供了条件。
而碳的氧化降低了钒的氧化率,使半钢中的余钒含量增加,不利于提钒[5]。
(3)铁水中硅含量高会抑制钒的氧化[8]。
反应式如下:
[Si]+O2=(SiO2)ΔGθ=-946350+197.64T式(1.5)
[V]+3/4O2=1/2(V2O3)ΔGθ=-601450+118.76T式(1.6)
由以上两个反应式可知,[Si]与氧的亲合力比[V]与氧的亲合力强。
[Si]被氧化成(SiO2)对钒渣有“稀释”作用,而[Si]氧化放热使提钒所需的低温熔池环境时间缩短。
并且铁水[Si]含量大于0.15%时,使炉渣过稀,出钢过程中钒渣的收得率降低。
因此,铁水[Si]含量较高时,将抑制[V]的氧化,所以要严格控制铁水中[Si]的含量。
(4)铁水中含钛时,会使炉渣粘度增大,使转炉炉衬和氧枪粘结,影响设备的运行和使用寿命。
因此,要控制好提钒铁水中的钛含量[6]。
(5)而铁水中的硫也是对提钒和炼钢影响较大的元素,因而高炉铁水或经过与脱硫处理的铁水,在转入转炉前要进行扒渣或撇渣操作,使铁水中的渣量不超过0.5%。
图1.1铁水中元素氧化的ΔGθ-T
1.3.2钒渣成分的影响
(1)钒渣中氧化钙的影响
钒渣在后续焙烧工序过程中,渣中的CaO和V2O5会发生反应,生成不溶于水的CaO·V2O5,影响钒的回收。
根据一些研究者的研究表明,渣中CaO含量每增加1%,V2O5就会损失4.7%~9.0;因此
/
越高,对钒的回收影响越小。
而钒渣中的CaO主要来源于铁水带入的渣,所以铁水在加入转炉前必须将渣尽量除尽[10]。
(2)钒渣中二氧化硅的影响
钒渣中SiO2含量较高时,焙烧过程中会发生如下反应,
NaCO3+SiO2=Na2SiO3+CO2式(1.7)
Na2SiO3水解过程中析出SiO2胶质沉淀,影响V2O5浸出液的澄清,最终影响钒的回收。
钒渣中的SiO2主要来源于铁水,冷却剂的加入也会带来一些。
(3)钒渣中铁的影响
钒渣中铁有两种形态存在,金属铁和氧化铁。
金属铁含量过高会使钒渣的后续处理变困难,氧化铁的存在会使钒溶解于Fe203中,进而产生钒的流失,降低钒的收得率。
钒渣中氧化铁的含量用
表示,钒渣中
含量随氧化铁含量的增加而降低,当
=10%时,
为53.2%;当
=40%时,
为20.4%。
但
含量过低时,不利于铁水中元素的氧化,因此
要保持适当的含量[7]。
(4)钒渣中磷的影响
钒渣中的磷的是因铁水带入。
钒渣中的磷盐与钠盐经过焙烧,生成的磷酸盐溶于水,进而会影响钒的沉淀,也会对产品的性能和质量有较大的影响。
1.3.3留渣操作
留渣操作是将上一炉冶炼的终渣在出钢后留一部分或全部在转炉内,在下一炉冶炼时当作部分初渣使用。
转炉终渣一般具有较高的碱度和∑(FeO)含量,并且熔点不高,还含有大量的热理热[16]。
将这种炉渣留在炉内,可加速下一炉炉渣的形成,从而提高转炉的热效率。
攀钢转炉采用留渣操作不仅加速了初期渣的形成,而且也缓解了冶炼过程中温度不足的矛盾。
留渣操作试验结果见表1.1。
表1.1不同出钒渣操作对半钢和钒渣质量的影响
由表1.1可知:
留渣操作与未留渣操作相比,留渣操作的(TFe)降低了4.1%,(V2O5)含量提高了3.3%;留渣操作与未留渣操作的半钢[C]、[V]含量及温度相差不大。
;
1.3.4铁水温度的影响
在转炉吹炼提钒过程中,吹炼前期钒的氧化速率要大于中期和后期。
这是因为吹炼前期,转炉中的渣还未造好,脱碳速度较慢;而中期和后期渣的氧化性较强,脱碳反应激烈,脱碳量大,并且脱碳放出大量的热量,使炉温升温较快。
由攀钢的生产实践数据可知,当炉温低于1400℃时,对钒的氧化基本无影响;当温度高于1400℃时,半钢中的余钒量有所增加。
所以在吹炼前期是钒的主要氧化阶段,大量的钒被氧化进入渣中,氧化量占总量的70%左右。
为达到“脱碳保钒”的目的,要将炉温控制在钒、碳氧化的转换温度以下,吹炼钒渣的终点温度应控制在1340~1400℃之间,才能得到品位较高的钒渣和合格的半钢。
1.3.5供氧制度的影响
供氧制度是在氧枪喷头结构一定的条件下使氧气流股最合理地供给熔池,创造良好的物理化学反应条件。
供氧制度包括氧枪枪位、供氧强度、耗氧量、喷头结构、供氧压力等诸多参数,该制度是控制吹钒过程的中心环节。
1.4其他提钒方法
除了氧气顶吹转炉吹炼提钒以外,还有空气底吹转炉提钒、雾化法提钒和摇包提钒等方法。
1.4.1雾化提钒法
雾化提钒法是攀钢1978~1995年采用的从铁水吹炼钒渣的方法。
炼铁厂输送来的铁水倾翻机将铁水倒入中间罐,铁水进行撇渣和整流,然后进入雾化器。
雾化器中的高速富氧流股将铁水击碎成雾状,雾状铁水和富氧空气强烈混合,使铁水和氧的反应界面急剧增大,氧化反应迅速进行。
并且压缩空气可对反应区进行非常有效的冷却,使反应温度限制在对钒氧化有利的范围内。
雾化后的铁水在反应过程中汇集到雾化室底部通过半钢出钢槽进入半钢罐,钒渣漂浮于半钢表面形成渣层,最后将半钢与钒渣分离[11~12]。
1.4.2空气底吹转炉提钒法
空气底吹转炉提钒法是从转炉底部吹入空气将铁水中的钒氧化成钒渣。
采用该法生产钒渣的主要是俄罗斯丘索夫冶金工厂,该冶金工厂有三座转炉,装料量为18~22t/炉。
空气底吹转炉提钒法的特点是生产效率高,吹炼平稳、搅拌强度大、热利用率高。
建设投资少,不需要喷枪、料仓等设置。
1.4.3顶底复吹转炉提钒法
顶底复吹转炉提钒法是将顶吹法和底吹法综合在一起的提钒方法,顶底复吹的方法的目的是为了加强熔池搅拌,改善元素反应的动力学条件,以提高钒氧化率,改善钒渣成分,降低铁损。
该工艺适合于含钒较低的铁水。
攀钢从2001年已开始复合吹钒实验,2005年开始进行大规模实验,到2008年1月全面推广复吹提钒方法,取得了很好的效果。
顶底复吹转炉提钒法中顶部吹氧气,底部吹惰性气体。
采用底吹惰性气体强化搅拌时,可有效地改善金属和钒渣的氧化效果,渣中的FeO能有效地参与铁水中元素的氧化反应,钒进入渣中的速度、钒氧化率、钒回收率及渣中(V2O5)品位都得到提高,同时渣中铁含量相应降低。
反应如下:
3(FeO)+2[V]=(V2O3)+[Fe]式(1.8)
(FeO)+2[C]=[Fe]+CO(g)式(1.9)
[C]+[O]=CO(g)式(1.10)
1.4.4摇包提钒
摇包结构与钢包相似,摇包上口带有出铁口,它装在振动台架上,呈水平方向摇动,从摇包上口伸入水冷氧枪,进而供氧吹炼提钒。
南非海威尔德钢钒公司曾经采用摇包法提钒,该厂的生产流程为:
回转窑直接还原得到金属化球团装入电炉炼铁,得到的铁水再装入摇包内提钒,提钒后的半钢倒入转炉内炼钢[4]。
摇包提钒优点是不占用炼钢设备,使用寿命长,设备简单,渣铁分离较好,钒、铁回收率高,钒氧化率高。
但提钒处理时间长,产量低,耗氧高。
1.4.5铁水包提钒
铁水包提钒有两支枪,一支为氧枪,其位置在铁水包中心,喷咀距熔池表面500mm。
另一支为氮枪,吹氮气搅拌熔池,其位置在铁水包中心和边缘之间,枪插入铁水中,距离铁水包底部500mm。
铁水包包盖上有三个孔,分别为氧枪孔、氮枪孔和冷却剂加入孔。
冷却剂是用氧化铁制成的颗粒。
吹炼过程图1.3所示:
图1.3铁水包提钒吹炼过程
2提钒转炉内物料平衡和热平衡计算
2.1原始数据
2.1.1金属料成分及温度
金属料成分及温度如表2.1所示:
表2.1金属料成分及温度
种类
C/%
Si/%
Mn/%
P/%
S/%
Ti/%
V/%
温度/℃
铁水
4.5
0.16
0.08
0.070
0.013
0.23
0.30
1290
含钒生铁块
4.31
0.10
0.12
0.059
0.05
0.28
0.324
25
2.1.2原料成分
渣料和炉渣成分如表2.2所示:
表2.2渣料和炉渣成分
种类
CaO/%
SiO2/%
MgO/%
Al2O3/%
S/%
P/%
CaF2/%
TiO2/%
Fe2O3/%
C/%
石英砂
0.3
95.96
1.54
1.42
0.02
0.02
0
0
1.5
0
镁质炉衬
1.5
0.5
78.6
1.0
0
0
0
0
0
18.4
2.1.3假设条件
(1)转炉铁水130吨,含钒生铁块为金属料装入量的5%,铁水为金属料装入量的95%。
(2)金属中碳总量的75%氧化成CO,25%的碳氧化成CO2。
(3)渣中铁珠量为渣量的8%。
(4)喷溅量极少,因此可以忽略。
(5)炉气平均温度为1450℃自由氧含量为0.5%。
(6)烟尘量为1.16%,其中FeO=70%,Fe2O3=20%。
(7)氧气纯度为99.6%,0.4%的氮气。
(8)进入炉渣的耐火材料量为金属量0.05%,其中炉衬侵蚀量为0.03%,补炉料为0.02。
(9)每100kg金属料加入石英砂1.20kg,铁水带入渣量为0.52kg,
(10)氧气利用率为75%,吹炼时间为7min。
2.2物料平衡计算
2.2.1元素氧化量
金属料氧化量如表2.3所示:
表2.3金属料氧化量
种类
C/%
Si/%
Mn/%
P/%
S/%
Ti/%
V/%
铁水/95%
4.5×95
0.16×95
0.08×95
0.070×95
0.013×95
0.23×95
0.30×95
含钒生铁块/5%
4.31×5
0.10×5
0.12×5
0.059×5
0.05×5
0.28×5
0.324×5
半钢
3.85
0.02
痕迹
0.068
0.014
痕迹
0.04
氧化量/%
0.641
0.137
0.082
0.001
0.001
0.233
0.261
2.2.2各元素反应产物及数量
各元素反应产物及数量如表2.4所示:
表2.4各元素反应产物及数量
元素
产物
氧化量/kg
氧耗量/kg
氧化产物量/kg
C
CO
0.641×75%=0.481
0.481×
=0.641
0.481×
=1.122
CO2
0.641×25%=0.160
0.160×
=0.427
0.160×
=0.587
Si
SiO2
0.137
0.137×
=0.157
0.137×
=0.294
Mn
MnO
0.082
0.082×
=0.024
0.082×
=0.106
P
P2O5
0.001
0.001×
=1.290×10-3
0.001×
=2.290×10-3
S
SO2
0.001×
=
3.33×10-4
3.33×10-4×
=
3.33×10-4
3.33×10-4×
=
6.66×10-4
CaS
0.001-3.33×10-4=
6.67×10-4
0
6.67×10-4×
=
1.501×10-3
Ti
TiO2
0.223
0.223×
=0.149
0.223×
=0.372
V
V2O5
0.261
0.261×
=0.205
0.261×
=0.466
Fe
FeO
0.218
0.218×
=0.060
0.280
Fe2O3
0.065
0.065×
=0.028
0.093
合计
1.639
1.691
注:
气化脱硫占总脱硫量的
,FeO和Fe2O3由渣量反算
炉渣的重量及成分如表2.5所示:
表2.5炉渣的重量及成分
项目
氧化产物量/kg
石英砂/kg
镁质炉衬/kg
合计/kg
CaO
0
1.20×0.3%=0.004
0.05×1.5%=0.001
0.005
MgO
0
1.20×1.54%=0.018
0.05×78.6%=0.039
0.057
SiO2
0.294
1.20×95.96%=1.152
微量
1.446
P2O5
2.290×10-3
0
0
0.002
MnO
0.106
0
0
0.106
Al2O3
1.20×1.42%=0.017
0
0.017
CaF2
0
0
0
CaS
0.002
0
0
0.002
S
微量
0
0
P
微量
0
0
V2O5
0.446
0
0
0.446
TiO2
0.372
0
0
0.372
Fe2O3
0.084
1.20×1.5%=0.018
0
0.102
FeO
0.252
0
0
0.252
C
0
0.05×18.4%=0.009
0.009
由表4和表5可知除了FeO和Fe2O3以外的熔渣量为:
+
+
+
+
+
+
+
+
+
=
1.446+0.005+0+0.106+0.057+0.002+0.017+0.002+0.446+0.372=2.453
又知终点渣成分中
+
=9%+3%=12%
则其他成分占百分比为(100%-12%)=88%
熔渣量为
=2.788kg
总渣量=熔渣量+铁水带入的渣量=2.788+0.52=3.308kg
其中:
FeO量