换热器工艺设计.docx
《换热器工艺设计.docx》由会员分享,可在线阅读,更多相关《换热器工艺设计.docx(17页珍藏版)》请在冰豆网上搜索。
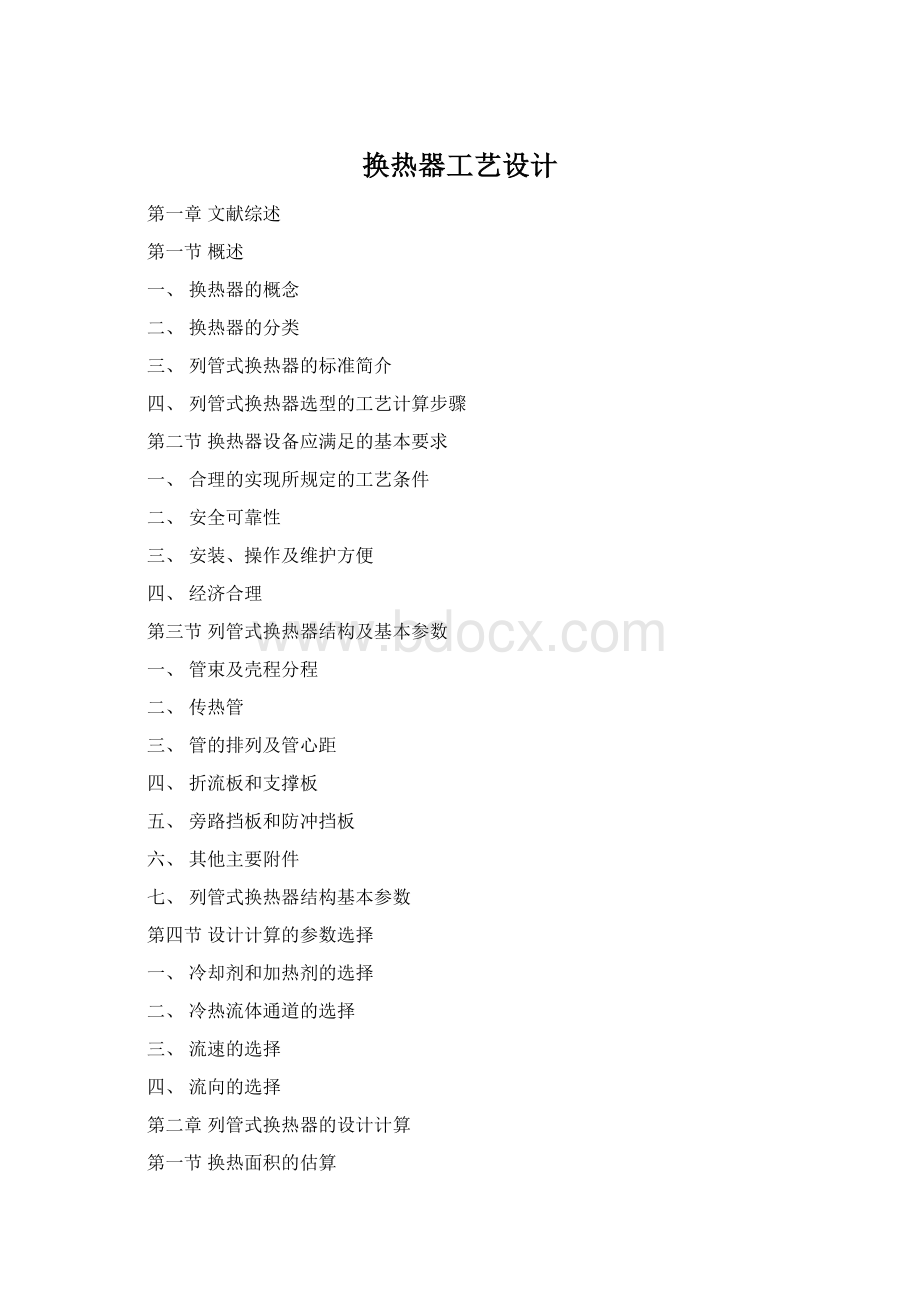
换热器工艺设计
第一章文献综述
第一节概述
一、换热器的概念
二、换热器的分类
三、列管式换热器的标准简介
四、列管式换热器选型的工艺计算步骤
第二节换热器设备应满足的基本要求
一、合理的实现所规定的工艺条件
二、安全可靠性
三、安装、操作及维护方便
四、经济合理
第三节列管式换热器结构及基本参数
一、管束及壳程分程
二、传热管
三、管的排列及管心距
四、折流板和支撑板
五、旁路挡板和防冲挡板
六、其他主要附件
七、列管式换热器结构基本参数
第四节设计计算的参数选择
一、冷却剂和加热剂的选择
二、冷热流体通道的选择
三、流速的选择
四、流向的选择
第二章列管式换热器的设计计算
第一节换热面积的估算
一、计算热负荷
二、估算传热面积
第二节换热器及主要附件的试选
一、试选管型号
二、换热器结构一些基本参数的选择
第三节换热器校核
一、核算总传热系数
二、核算压强降
第四节设计结果一览表
第五节设计总结及感想
一、设计总结
二、感想
参考文献
第一章文献综述(略)
第二章列管式换热器的设计计算
第一节换热面积的估算
一、计算热负荷(不考虑热损失)
由于设计条件所给为无相变过程。
由设计任务书可知热负荷为
Q=w原油Cp原油(t2-t1)=(50000/3600)×2.20×1000×(110-70)=1222222W.
由热量守恒可计算柴油出口温度T2
Q=w柴油Cp柴油(T1-T2)=(38000/3600)×2.48×1000×(175-T2)=1222222W
T2=128.31℃
二、计算平均温度差:
Δt1=175-110=65℃
Δt2=128.31-70=58.31℃
逆流温度差
℃
三.确定流体走向
由于原油温度低于柴油,为减少热损失和充分利用柴油的热量,选择原油走壳程,柴油走管程。
四.换热面积估算
由《化工原理课程设计》的表4-6,取K估=200W/(m2·℃).
先假设换热器为单管程、单壳程的,且冷热流体逆流接触。
则
A估=Q/(K估×Δtm逆)=1222222/(200×61.6)=99.2m2.
预先估算传热面积为99.2m2。
五、选柴油的流速为u1=1m/s
取换热管的规格为Φ25×2.5mm碳素钢管(8.3kg/6m)。
估算单管程的管子根数
=
=47.02≈47根。
根据传热面积A估计算管子的长度L’,有
式中:
d1----换热管的内径,为0.02m
d0----换热管的外径,为0.025m
五、管程数Nt的确定
由于L’数值太大,换热器不可使用单管程的形式,必须用多管程。
我们选择管程的长度为6m,则Nt=L’/6=27/6=4.5≈4.(管程数通常选择偶数)
六、校正温度差
R=(T1-T2)/(t2-t1)=(175-128.31)/(110-70)=1.167
P=(t2-t1)/(T1-t1)=(110-70)/(175-70)=0.381
根据R,P的值,查化工原理教材中图4-25(a),得温度校正系数
φ=0.91>0.9,说明换热器采用单壳程,四管程的结构是合适的。
Δtm=φ×Δtm逆=0.91*61.6=56.06℃。
七、求实际换热面积A实际
换热管数为n’×Nt=47×4=188根。
A实际=L×(π×d0)×n’=6×(3.14×0.025)×188=88.55m2.
实际换热面积为88.55m2.
八、选择换热器壳体尺寸
选择换热管为三角形排列,换热管的中心距为t=32mm。
横过管束中心线的管数:
最外层换热管中心线距壳体内壁距离:
b'=(1——1.5)d0,此处b’取一倍d0,即b'=0.025m
壳体内径:
圆整后,换热器壳体圆筒内径为D=550mm,壳体厚度选择8mm。
长度定为5996mm。
壳体的标记:
筒体DN550δ=8L=5910。
筒体材料选择为Q235-A,单位长度的筒体重110kg/m,壳体总重为110*(5.910-0.156)=632.94kg。
(波形膨胀节的轴向长度为0.156m,见本设计设备图)
九、确定折流挡板形状和尺寸
选择折流挡板为有弓形缺口的圆形板,直径为540mm,厚度为6mm。
缺口弓形高度为圆形板直径的约1/4,本设计圆整为120mm。
折流挡板上换热管孔直径为25.6mm,共有188-22-13/2=159.5个;拉杆管孔直径为16.6mm,每个折流挡板上有4个。
折流挡板上的总开孔面积=159.5*514.7185+4*216.4243=82963.2972mm2。
折流挡板的实际面积=191126.3264-82963.2972=108163.0292mm2,重量为5.1kg。
选择折流挡板间距h=400mm。
折流挡板数NB=L/h-1=6000/400-1=14块.换热管排列的横截面如下图所示:
图中圆环形的剖切面表示换热器壳体的剖面.换热管分为四个管程,每个管程47根换热管(图中各个小菱形的顶点表示换热管横截面的中心).图中8个”十”字形表示拉杆的开孔,拉杆直径为16mm.
十、波形膨胀节
冷流体原油为黏度较高的流体,其定性温度为(110*0.4+70*0.6)=86℃;热流体柴油的定性温度为(175*0.5+128.31*0.5)=87.5+64.155=151.66℃.冷热流体的定性温度差=151.66-86=65.66℃>50℃,所以换热器壳体上要安装波形膨胀节。
波形膨胀节的壁厚与壳体相同,为8mm。
根据换热器壳体的公称直径550mm,可知波形膨胀节的公称直径也是550mm,根据公称直径,查《化工设备机械基础》(化学工业出版社,2008)书中表16-9的对应条目,获得波形膨胀节的具体尺寸(见换热器设备图)。
单个波形膨胀节的质量=4579586.3154mm3×7.8×10-3×10-3kg·mm-3=35.721kg。
十一、传热系数K的计算
1.管程对流传热系数αi
换热管内柴油流速:
雷诺数
,
普兰德数
,
柴油的黏度小于常温水黏度的两倍,是低黏度液体,且是被冷却,所以
w/(m2·℃)
2.壳程对流传热系数αo
壳程流通截面积:
m2
壳程流速:
换热管为三角形排列,壳程的当量直径为
雷诺数
,
普兰德数
,
原油被加热,所以
w/(m2·℃)
3.污垢热阻
根据设计任务书,两侧的污垢热阻Rso=Rsi=1.72×10-4m2·℃/W。
4.总传热系数Ko
;取管壁λw=45w/(m·℃)
=287.2w/(m2·℃)
A需要=Q/(Ko×Δtm)=1222222/(287.2×56.06)=75.91m2.
面积裕量:
〉15%
符合换热器设计规范的要求。
十二、压强降的计算
1.管程压强降
已知管程直管的绝对粗糙度ε=0.1mm,则ε/d1=0.1/20=0.005,雷诺准数
,查摩擦系数图1-28,得到λ=0.035,所以,每程直管的压降:
.75Pa;
柴油在每管程中局部阻力导致的压强降按经验公式计算如下:
Pa;
一般地,流体流经换热器进出口导致的压强降可以忽略。
对于Φ25×2.5的换热管,结垢校正系数Ft=1.4;因为是单壳程、四管程的换热器,所以Ns=1,Np=4;
Pa<30000Pa,
符合任务书的要求。
2.壳程压强降
流体横过管束的压强降:
管子排列方法对压强降的校正因数F=0.5(正三角形排列);
壳程流体的摩擦系数fo,当Re2〉500时,fo=5.0×Re2-0.228=5.0×1943-0.228=0.89;
横过管束中心线的管子数nc=15;
折流板数NB=14;
壳程流速u2=0.354m/s;
ρ原油=815kg/m3
=5113Pa;
流体通过折流板缺口的压强降:
折流板间距h=400mm=0.400m;
壳体内径D=550mm=0.550m
=1462Pa
一般地,流体流经换热器进出口导致的压强降可以忽略。
壳程总压降:
对于液体壳程压强降的结垢校正系数Fs=1.15;
壳程数Ns=1
=7561Pa<30000Pa.符合任务书的要求。
十三、主要附件的选择
1.接管及法兰的选型
1)管口A
管口A为柴油出口。
①接管管径的确定:
流量为38000kg/h,密度为715kg/m3,相当于q=38000/715/3600=0.01476m3/s。
柴油为低粘度流体,在接管中的合理流速u=1——2m/s。
本设计取u=1m/s。
则接管的内径=
=0.1371m=137mm。
接管的外径选择为159mm,壁厚选择为4.5mm,材质为20钢,每米管子的重量17.14kg(GB-T17395-1998无缝钢管尺寸、外形、重量及允许偏差)。
②接管长度的选择:
接管的长度L选择150mm,则重量为2.6kg。
接管的标记:
接管Φ159×4.5L=150
③接管法兰的选择:
查《大学工程制图》(华东理工大学出版社,2005)表14-5,接管外径dH=159mm的板式平焊钢制管法兰的公称通径DN=150mm。
选择公称压力PN=0.6MPa的突面法兰,材料为Q235-A,标记为:
HG20592法兰PL150(B)-0.6RFQ235-A。
重量为5.14kg。
该法兰有8个均布在外周的螺孔,使用8个M16螺栓、螺母、垫片与工艺管道连接。
2)管口B
管口B为原油出口。
原油的流量为50000kg/h,密度为815kg/m3,相当于q=50000/815/3600=0.01704m3/s。
原油在接管中的合理流速u=1——2m/s。
本设计取u=1m/s。
则接管的内径=
=0.147m=147mm。
选择接管的外径、壁厚、材质、长度和接管法兰都与管口A的相同。
3)管口C
管口C为排气口。
①接管管径的确定:
接管的外径选择32mm,壁厚选择为3.5mm,材质为20钢,每米管子的重量2.46kg(GB-T17395-1998无缝钢管尺寸、外形、重量及允许偏差)。
②接管长度的选择:
接管的长度L选择150mm,则重量为0.369kg。
接管的标记:
接管Φ32×3.5L=150
③接管法兰的选择:
查《大学工程制图》(华东理工大学出版社,2005)表14-5,接管外径dH=32mm的板式平焊钢制管法兰的公称通径DN=25mm。
选择公称压力PN=0.6MPa的突面法兰,材料为Q235-A,标记为:
HG20592法兰PL25(B)-0.6RFQ235-A。
该法兰有4个均布在外周的螺孔,使用4个M10螺栓、螺母、垫片与配套的法兰盖装配。
4)管口D
管口D为原油进口。
接管、法兰与管口A和B的完全相同。
5)管口E
管口E为排污口。
①接管管径的确定:
接管的外径选择57mm,壁厚选择为3.5mm,材质为20钢,每米管子的重量4.62kg。
②接管长度的选择:
接管的长度L选择150mm,则重量为0.693kg。
接管的标记:
接管Φ57×3.5L=150
③接管法兰的选择:
查《大学工程制图》(华东理工大学出版社,2005)表14-5,接管外径dH=57mm的板式平焊钢制管法兰的公称通径DN=50mm。
选择公称压力PN=0.6MPa的突面法兰,材料为Q235-A,标记为:
HG20592法兰PL50(B)-0.6RFQ235-A。
重量为1.51kg。
该法兰有4个均布在外周的螺孔,使用4个M12螺栓