模锻成型.docx
《模锻成型.docx》由会员分享,可在线阅读,更多相关《模锻成型.docx(16页珍藏版)》请在冰豆网上搜索。
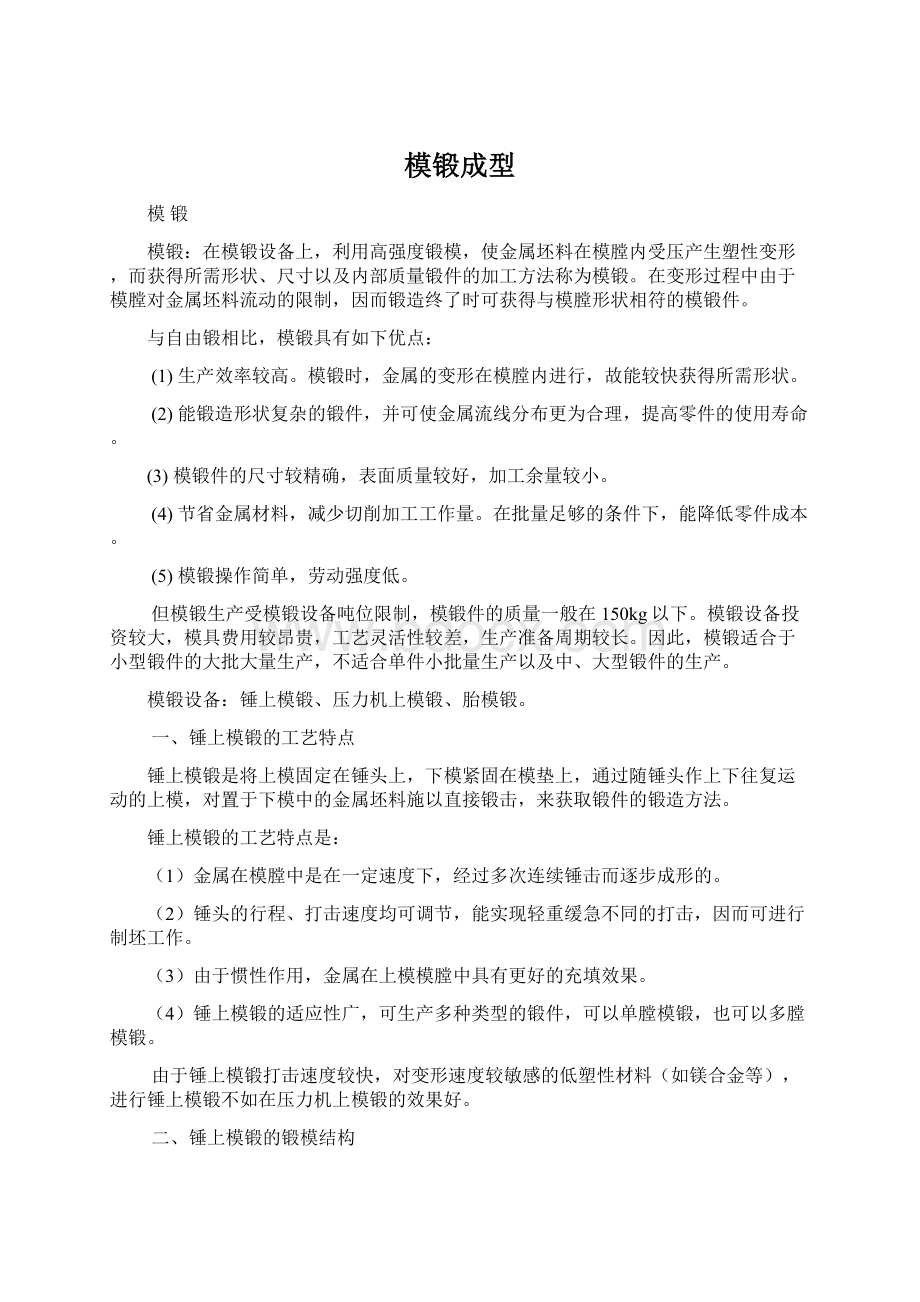
模锻成型
模锻
模锻:
在模锻设备上,利用高强度锻模,使金属坯料在模膛内受压产生塑性变形,而获得所需形状、尺寸以及内部质量锻件的加工方法称为模锻。
在变形过程中由于模膛对金属坯料流动的限制,因而锻造终了时可获得与模膛形状相符的模锻件。
与自由锻相比,模锻具有如下优点:
(1)生产效率较高。
模锻时,金属的变形在模膛内进行,故能较快获得所需形状。
(2)能锻造形状复杂的锻件,并可使金属流线分布更为合理,提高零件的使用寿命。
(3)模锻件的尺寸较精确,表面质量较好,加工余量较小。
(4)节省金属材料,减少切削加工工作量。
在批量足够的条件下,能降低零件成本。
(5)模锻操作简单,劳动强度低。
但模锻生产受模锻设备吨位限制,模锻件的质量一般在150kg以下。
模锻设备投资较大,模具费用较昂贵,工艺灵活性较差,生产准备周期较长。
因此,模锻适合于小型锻件的大批大量生产,不适合单件小批量生产以及中、大型锻件的生产。
模锻设备:
锤上模锻、压力机上模锻、胎模锻。
一、锤上模锻的工艺特点
锤上模锻是将上模固定在锤头上,下模紧固在模垫上,通过随锤头作上下往复运动的上模,对置于下模中的金属坯料施以直接锻击,来获取锻件的锻造方法。
锤上模锻的工艺特点是:
(1)金属在模膛中是在一定速度下,经过多次连续锤击而逐步成形的。
(2)锤头的行程、打击速度均可调节,能实现轻重缓急不同的打击,因而可进行制坯工作。
(3)由于惯性作用,金属在上模模膛中具有更好的充填效果。
(4)锤上模锻的适应性广,可生产多种类型的锻件,可以单膛模锻,也可以多膛模锻。
由于锤上模锻打击速度较快,对变形速度较敏感的低塑性材料(如镁合金等),进行锤上模锻不如在压力机上模锻的效果好。
二、锤上模锻的锻模结构
锻模结构:
如图2-18所示,锤上模锻用的锻模由带燕尾的上模2和下模4两部分组成,上下模通过燕尾和楔铁分别紧固在锤头和模垫上,上、下模合在一起在内部形成完整的模膛。
图2-18锤上锻模
1-锤头2-上模3-飞边槽4-下模5-模垫
6、7、10-紧固楔铁8-分模面9-模膛
模锻模膛:
制坯模膛和模锻模膛。
(一)制坯模膛
对于形状复杂的模锻件,为了使坯料基本接近模锻件的形状,以便模锻时金属能合理分布,并很好地充满模膛,必须预先在制坯模膛内制坯。
制坯模膛有以下几种:
1.拔长模膛减小坯料某部分的横截面积,以增加其长度。
如图2-19所示。
图2-19拔长模膛
a)开式b)闭式
2.滚挤模膛减小坯料某部分的横截面积,以增大另一部分的横截面积。
主要是使金属坯料能够按模锻件的形状来分布。
滚挤模膛也分为开式和闭式两种,如图2-20所示。
图2-20滚挤模膛
a)开式b)闭式
3.弯曲模膛使坯料弯曲,如图2-21所示。
图2-21弯曲模膛
4.切断模膛在上模与下模的角部组成一对刃口,用来切断金属,如图2-22所示。
可用于从坯料上切下锻件或从锻件上切钳口,也可用于多件锻造后分离成单个锻件。
图2-22切断模膛
此外,还有成形模膛、镦粗台及击扁面等制坯模膛。
(二)模锻模膛
模锻模膛包括预锻模膛和终锻模膛。
所有模锻件都要使用终锻模膛,预锻模膛则要根据实际情况决定是否采用。
1.终锻模膛使金属坯料最终变形到所要求的形状与尺寸,如图2-18所示。
由于模锻需要加热后进行,锻件冷却后尺寸会有所缩减,所以终锻模膛的尺寸应比实际锻件尺寸放大一个收缩量,对于钢锻件收缩量可取1.5%。
飞边槽:
如图2-18所示。
飞边槽用以增加金属从模膛中流出的阻力,促使金属充满整个模膛,同时容纳多余的金属,还可以起到缓冲作用,减弱对上下模的打击,防止锻模开裂。
飞边槽的常见形式如图2-23所示,图2-23a为最常用的飞边槽形式,图2-23b用于不对称锻件,切边时须将锻件翻转180°,图2-23c用于锻件形状复杂,坯料体积偏大的情况,图2-23d设有阻力沟,用于锻件难以充满的局部位置。
飞边槽在锻后利用压力机上的切边模去除。
图2-23飞边槽形式
图2-24为带有飞边槽与冲孔连皮的模锻件。
2.预锻模膛用于预锻的模膛称为预锻模膛。
终锻时常见的缺陷有折迭和充不满等,工字型截面锻件的折迭如图2-25所示。
这些缺陷都是由于终锻时金属不合理的变形流动或变形阻力太大引起的。
为此,对于外形较为复杂的锻件,常采用预锻工步,使坯料先变形到接近锻件的外形与尺寸,以便合理分配坯料各部分的体积,避免折迭的产生,并有利于金属的流动,易于充满模膛,同时可减小终锻模膛的磨损,延长锻模的寿命。
预锻模膛和终锻模膛的主要区别是前者的圆角和模锻斜度较大,高度较大,一般不设飞边槽。
只有当锻件形状复杂、成形困难,且批量较大的情况下,设置预锻模膛才是合理的。
图2-24带有飞边槽与冲孔连皮的模锻件
1—冲孔连皮2—锻件3—飞边4—分模面
图2-25工字型截面锻件的折迭
根据模锻件的复杂程度不同,所需的模膛数量不等,可将锻模设计成单膛锻模或多膛锻模。
弯曲连杆模锻件所用多膛锻模如图2-26所示。
图2-26弯曲连杆锻模(下模)与模锻工序
1—拔长模膛2—滚挤模膛3—终锻模膛4—预锻模膛5—弯曲模膛
三、锤上模锻工艺规程的制定
锤上模锻工艺规程的制定主要包括绘制模锻件图、计算坯料尺寸、确定模锻工步、选择锻造设备、确定锻造温度范围等。
(一)绘制模锻件图
模锻件图是设计和制造锻模、计算坯料以及检验模锻件的依据。
根据零件图绘制模锻件图时,应考虑以下几个问题。
1.分模面上下锻模的分界面。
分模面的选择应按以下原则进行。
(1)要保证模锻件能从模膛中顺利取出,并使锻件形状尽可能与零件形状相同,一般分模面应选在模锻件最大水平投影尺寸的截面上。
如图2-27所示,若选a-a面为分模面,则无法从模膛中取出锻件。
图2-27分模面选择比较
(2)按选定的分模面制成锻模后,应使上下模沿分模面的模膛轮廓一致,以便在安装锻模和生产中容易发现错模现象。
如图2-27所示,若选c-c面为分模面,就不符合此原则。
(3)最好使分模面为一个平面,并使上下锻模的模膛深度基本一致,差别不宜过大,以便于均匀充型。
(4)选定的分模面应使零件上所加的敷料最少。
如图2-27所示,若将b-b面选作分模面,零件中间的孔不能锻出,其敷料最多,既浪费金属,降低了材料的利用率,又增加了切削加工工作量,所以该面不宜选作分模面。
(5)最好把分模面选取在能使模膛深度最浅处,这样可使金属很容易充满模膛,便于取出锻件,如图2-27所示的b-b面就不适合做分模面。
按上述原则综合分析,选用如图2-27所示的d-d面为分模面最合理。
2.加工余量和锻件公差为了达到零件尺寸精度及表面粗糙度的要求,锻件上需切削加工而去除的金属层,称为锻件的加工余量。
模锻件水平方向尺寸公差见表2-6。
模锻件内、外表面的加工余量见表2-7。
表2-6锤上模锻水平方向尺寸公差(mm)
模锻件长(宽)度
<50
50~120
120~260
260~500
500~800
800~1200
公差
+1.0
+1.5
+2.0
+2.5
+3.0
+3.5
-0.5
-0.7
-1.0
-1.5
-2.0
-2.5
表2-7内、外表面的加工余量Z1(单面)(mm)
加工表面最大
宽度或直径
加工表面的最大长度或最大高度
≤63
>63~160
>160~250
>250~400
>400~1000
>1000~2500
大于
至
加工余量Z1
—
25
1.5
1.5
1.5
1.5
2.0
2.5
25
40
1.5
1.5
1.5
1.5
2.0
2.5
40
63
1.5
1.5
1.5
2.0
2.5
3.0
63
100
1.5
1.5
2.0
2.5
3.0
3.5
3.模锻斜度为便于从模膛中取出锻件,模锻件上平行于锤击方向的表面必须具有斜度,称为模锻斜度,一般为5°~15°之间。
模锻斜度与模膛深度和宽度有关,通常模膛深度与宽度的比值(h/b)较大时,模锻斜度取较大值。
此外,模锻斜度还分为外壁斜度α与内壁斜度β,如图2-28所示。
外壁指锻件冷却时锻件与模壁离开的表面;内壁指当锻件冷却时锻件与模壁夹紧的表面。
内壁斜度值一般比外壁斜度大2°~5°。
生产中常用金属材料的模锻斜度范围见表2-8。
图2-28模锻斜度
表2-8各种金属锻件常用的模锻斜度
锻件材料
外壁斜度
内壁斜度
铝、镁合金
钢、钛、耐热合金
3°~5°
5°~7°
5°~7°
7°、10°、12°
4.模锻圆角半径模锻件上所有两平面转接处均需圆弧过渡,此过渡处称为锻件的圆角,如图2-29所示。
圆弧过渡有利于金属的变形流动,锻造时使金属易于充满模膛,提高锻件质量,并且可以避免在锻模上的内角处产生裂纹,减缓锻模外角处的磨损,提高锻模使用寿命。
图2-29模锻圆角半径
图2-30模锻件常用冲孔连皮
钢的模锻件外圆角半径(r)一般取1.5mm~12mm,内圆角半径(R)比外圆角半径大2~3倍。
模膛深度越深,圆角半径值越大。
为了便于制模和锻件检测,圆角半径尺寸已经形成系列,其标准是1、1.5、2、2.5、3、4、5、6、8、10、12、15、20、25和30等,单位为mm。
5.冲孔连皮由于锤上模锻时不能靠上、下模的突起部分把金属完全排挤掉,因此不能锻出通孔,终锻后,孔内留有金属薄层,称为冲孔连皮(图2-24),锻后利用压力机上的切边模将其去除。
常用的连皮形式是平底连皮,如图2-30所示,连皮的厚度t通常在4~8mm范围内,可按下式计算:
t=0.45(d—0.25h—5)0.5+0.6h0.5(mm)
式中d——锻件内孔直径,单位为mm;
h——锻件内孔深度,单位为mm。
连皮上的圆角半径R1,可按下式确定:
R1=R+0.1h+2(mm)
孔径d<25mm或冲孔深度大于冲头直径的3倍时,只在冲孔处压出凹穴。
上述各参数确定后,便可绘制锻件图。
图2-31所示为齿轮坯模锻件图。
图中双点划线为零件轮廓外形,分模面选在锻件高度方向的中部。
由于零件轮辐部分不加工,故无加工余量。
图中内孔中部的两条直线为冲孔连皮切掉后的痕迹。
图2-31齿轮坯模锻件图
(二)计算坯料质量与尺寸
坯料质量包括锻件、飞边、连皮、钳口料头以及氧化皮等的质量。
通常,氧化皮约占锻件和飞边总和质量分数的2.5%~4%。
(三)确定模锻工序
模锻工序主要根据锻件的形状与尺寸来确定。
根据已确定的工序即可设计出制坯模膛、预锻模膛及终锻模膛。
模锻件按形状可分为两类:
长轴类零件与盘类零件,如图2-32所示。
长轴类零件的长度与宽度之比较大,例如台阶轴、曲轴、连杆、弯曲摇臂等;盘类零件在分模面上的投影多为圆形或近于矩形,例如齿轮、法兰盘等。
图2-32模锻零件
a)长轴类零件b)盘类零件
1.长轴类模锻件基本工序常用的工序有拔长、滚挤、弯曲、预锻和终锻等。
拔长和滚挤时,坯料沿轴线方向流动,金属体积重新分配,使坯料的各横截面积与锻件相应的横截面积近似相等。
坯料的横截面积大于锻件最大横截面积时,可只选用拔长工序;当坯料的横截面积小于锻件最大横截面积时,应采用拔长和滚挤工序。
锻件的轴线为曲线时,还应选用弯曲工序。
对于小型长轴类锻件,为了减少钳口料和提高生产率,常采用一根棒料上同时锻造数个锻件的锻造方法,因此应增设切断工序,将锻好的工件分离。
当大批量生产形状复杂、终锻成形困难的锻件时,还需选用预锻工序,最后在终锻模膛中模锻成形。
某些锻件选用周期轧制材料作为坯料时,如图2-33所示,可省去拔长、滚挤等工序,以简化锻模,提高生产率。
图2-33轧制坯料模锻
a)周期轧制材料b)模锻后形状
2.盘类模锻件基本工序常选用镦粗、终锻等工序。
对于形状简单的盘类零件,可只选用终锻工序成形。
对于形状复杂,有深孔或有高肋的锻件,则应增加镦粗、预锻等工序。
3.修整工序坯料在锻模内制成模锻件后,还须经过一系列修整工序,以保证和提高锻件质量。
修整工序包括以下内容。
(1)切边与冲孔模锻件一般都带有飞边及连皮,须在压力机上进行切除。
切边模如图2-34a所示,由活动凸模和固定凹模组成。
凹模的通孔形状与锻件在分模面上的轮廓一致,凸模工作面的形状与锻件上部外形相符。
冲孔模如图2-34b所示,凹模作为锻件的支座,冲孔连皮从凹模孔中落下。
图2-34切边模及冲孔模
a)切边模b)冲孔模
1—凸模2—凹模
(2)校正在切边及其它工序中都可能引起锻件的变形,许多锻件,特别是形状复杂的锻件在切边冲孔后还应该进行校正。
校正可在终锻模膛或专门的校正模内进行。
(3)热处理目的是消除模锻件的过热组织或加工硬化组织,以达到所需的力学性能。
常用的热处理方式为正火或退火。
(4)清理为了提高模锻件的表面质量,改善模锻件的切削加工性能,模锻件需要进行表面清理,去除在生产中产生的氧化皮、所沾油污及其它表面缺陷等。
(5)精压对于要求尺寸精度高和表面粗糙度小的模锻件,还应在压力机上进行精压。
精压分为平面精压和体积精压两种。
平面精压如图2-35a所示,用来获得模锻件某些平行平面间的精确尺寸。
体积精压如图2-35b所示,主要用来提高锻件所有尺寸的精度、减小模锻件的质量差别。
精压模锻件的尺寸精度偏差可达±(0.1~0.25)mm,表面粗糙度Rα可达0.8~0.4μm。
图2-35精压
a)平面精压b)体积精压
弯曲连杆模锻工序如图2-26所示,坯料经过拔长、滚挤、弯曲三个工序后,形状接近于锻件,然后经预锻及终锻两个模膛制成有飞边的锻件,最后切边,得到弯曲连杆模锻件。
(四)选择锻造设备
锤上模锻的设备:
蒸汽-空气锤、无砧座锤、高速锤等。
(五)确定锻造温度范围
模锻件的生产也在一定温度范围内进行,与自由锻生产相似。
四、锤上模锻件的结构工艺性
设计模锻零件时,应根据模锻特点和工艺要求,使其结构符合下列原则:
1.模锻零件应具有合理的分模面,以使金属易于充满模膛,模锻件易于从锻模中取出,且敷料最少,锻模容易制造。
2.模锻零件上,除与其它零件配合的表面外,均应设计为非加工表面。
模锻件的非加工表面之间形成的角应设计模锻圆角,与分模面垂直的非加工表面,应设计出模锻斜度。
3.零件的外形应力求简单、平直、对称,避免零件截面间差别过大,或具有薄壁、高肋、等不良结构。
一般说来,零件的最小截面与最大截面之比不要小于0.5,如图2-36a所示零件的凸缘太薄、太高,中间下凹太深,金属不易充型。
如图2-36b所示零件过于扁薄,薄壁部分金属模锻时容易冷却,不易锻出,对保护设备和锻模也不利。
如图2-36c所示零件有一个高而薄的凸缘,使锻模的制造和锻件的取出都很困难。
改成如图2-36d所示形状则较易锻造成形。
图2-36模锻件结构工艺性
4.在零件结构允许的条件下,应尽量避免有深孔或多孔结构。
孔径小于30mm或孔深大于直径两倍时,锻造困难。
如图2-37所示齿轮零件,为保证纤维组织的连贯性以及更好的力学性能,常采用模锻方法生产,但齿轮上的四个Φ20mm的孔不方便锻造,只能采用机加工成形。
图2-37模锻齿轮零件
5.对复杂锻件,为减少敷料,简化模锻工艺,在可能条件下,应采用锻造—焊接或锻造—机械联接组合工艺,如图2-38所示。
图2-38锻焊结构模锻零件
a)模锻件b)焊合件
五、其它模锻方法
除了锤上模锻外,压力机上模锻和胎模锻等模锻方法也有着较为广泛的应用。
(一)压力机上模锻
用于模锻生产的压力机有摩擦压力机、平锻机、水压机、曲柄压力机等,其工艺特点的比较见表2-9。
表2-9压力机上模锻方法的工艺特点比较
锻造方法
设备类型
工艺特点
应用
结构
构造特点
摩擦压力机上模锻
摩擦压力机
滑块行程可控,速度为(0.5~1.0)m/s,带有顶料装置,机架受力,形成封闭力系,每分钟行程次数少,传动效率低
特别适合于锻造低塑性合金钢和非铁金属;简化了模具设计与制造,同时可锻造更复杂的锻件;承受偏心载荷能力差;可实现轻、重打,能进行多次锻打,还可进行弯曲、精压、切飞边、冲连皮、校正等工序
中、小型锻件的小批和中批生产
曲柄压力机上模锻
曲柄压力机
工作时,滑块行程固定,无震动,噪音小,合模准确,有顶杆装置,设备刚度好
金属在模膛中一次成形,氧化皮不易除掉,终锻前常采用预成形及预锻工步,不宜拔长、滚挤,可进行局部镦粗,锻件精度较高,模锻斜度小,生产率高,适合短轴类锻件
大批大量生产
平锻机上模锻
平锻机
滑块水平运动,行程固定,具有互相垂直的两组分模面,无顶出装置,合模准确,设备刚度好
扩大了模锻适用范围,金属在模膛中一次成形,锻件精度较高,生产率高,材料利用率高,适合锻造带头的杆类和有孔的各种合金锻件,对非回转体及中心不对称的锻件较难锻造
大批大量生产
水压机上模锻
水压机
行程不固定,工作速度为(0.1~0.3)m/s,无震动,有顶杆装置
模锻时一次压成,不宜多膛模锻,适合于锻造镁铝合金大锻件,深孔锻件,不太适合于锻造小尺寸锻件
大批大量生产
(二)胎模锻
胎模是一种不固定在锻造设备上的模具,结构较简单,制造容易,如图2-39所示。
胎模锻是在自由锻设备上用胎模生产模锻件的工艺方法,因此胎模锻兼有自由锻和模锻的特点。
胎模锻适合于中、小批量生产小型多品种的锻件,特别适合于没有模锻设备的工厂。
图2-39胎模示意图
胎模锻工艺过程包括制订工艺规程、制造胎模、备料、加热、胎模锻及后续加工工序等。
在工艺规程制订中,分模面的选取可灵活一些,分模面的数量不限于一个,而且在不同工序中可选取不同的分模面,以便于制造胎模和使锻件成形。